Onderwerpen:
- Het begin van het project
- Motor
- Versnellingsbak
- Motoronderdelen inspecteren, vervangen en afstellen
- Motor op verrijdbaar frame monteren
- Koeling
- Dashboard en elektrische installatie
- Brandstofpomp en tank
- Motor in klassieke opstelling laten functioneren
Het begin van het project:
Nadat er was besloten om een motor te voorzien van een MegaSquirt motormanagementsysteem, is er nagedacht over een geschikt motortype. Standaard ombouwpakketten met handleidingen waren niet interessant. De doelstelling was om een motor te gebruiken die aan de volgende voorwaarden voldeet:
- er moeten geen eerdere ombouwprojecten van deze motor bekend zijn;
- viercilinder benzinemotor;
- nog niet voorzien een injectie- en elektronisch ontstekingssysteem;
- de mogelijkheid om de motor te belasten.
Motor:
De zoektocht kwam uit bij een motor van een Land Rover (series 2A) uit begin jaren ’70. Deze 2,25 liter viercilinder benzinemotor met drie hoofdlagers was van origine voorzien van een carburateur en mechanische verdelerontsteking. De combinatie van deze Land Rover motor en de originele versnellingsbak was doorslaggevend voor de keuze; op de uitgaande as van de versnellingsbak is een transmissierem bevestigd. De transmissierem, die eigenlijk als parkeerrem dient, geeft de mogelijkheid om de motor tijdens het draaien de belasten door deze rem aan te trekken.
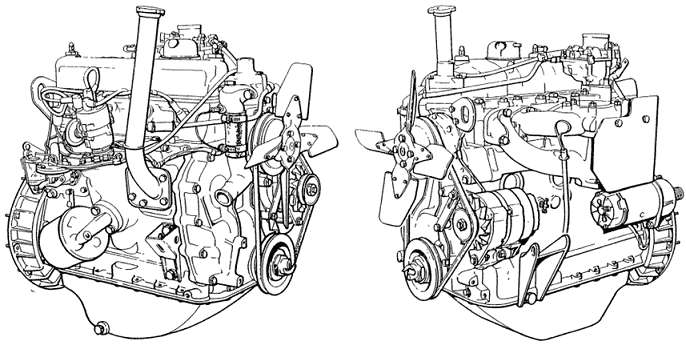
De motor had waarschijnlijk al tientallen jaren niet meer gefunctioneerd. Uiteraard moet hij betrouwbaar genoeg zijn om op het motormanagementsysteem te kunnen draaien. Het was daarom noodzakelijk om de motor eerst grondig te inspecteren en te testen. Hierbij waren de volgende doelstellingen gemaakt:
- Motoronderdelen inspecteren, vervangen en afstellen;
- Motor op een verrijdbaar frame monteren;
- Motor laten functioneren in de klassieke opstelling;
- Componenten voor het motormanagementsysteem aanbrengen;
- MegaSquirt ECU in elkaar zetten en gereedmaken;
- Motor op het motormanagementsysteem laten functioneren.
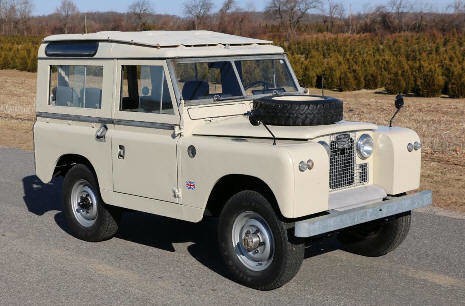
Versnellingsbak:
De versnellingsbak is afkomstig vanuit een uit het leger afkomstige Land Rover. De groene kleur verraad het eigenlijk al. Om in een later stadium een – zo origineel mogelijk – geheel te vormen met de motor, is de groene verf verwijderd. De transmissierem is op de foto nog niet aanwezig; deze is later, volgens de fabrieksvoorschriften, aan de uitgaande as gemonteerd.
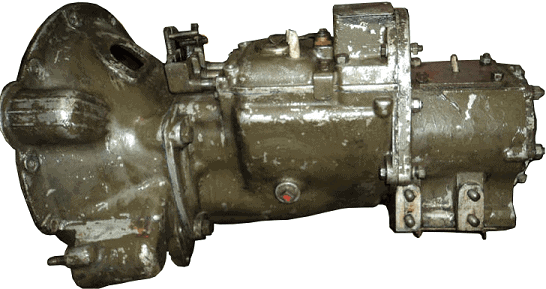
Motoronderdelen inspecteren, vervangen en afstellen:
Aan het begin van het project was het onduidelijk of de beschikbaar gestelde motor geschikt was om te gebruiken. Van het motorblok was namelijk weinig bekend, alleen dat de motor jarenlang had stilgestaan. Onduidelijk was of er interne onderdelen beschadigd of zelfs – mogelijk onherstelbaar – defect waren. In dit laatste geval was het vervangen de motor door een ander exemplaar de enige mogelijkheid om het project te hervatten.
Om niet in een later stadium tot de conclusie te komen dat de motor onbruikbaar zou zijn, is besloten de motor uit elkaar te halen en te reviseren. Van de onderdelen werden slijtagepatronen gecontroleerd en vergeleken met de fabrieksspecificaties. Onderdelen waarbij de metingen zich binnen deze toleranties bevonden zijn weer teruggeplaatst. Onderdelen die waren afgekeurd, zijn vervangen. Er is rekening gehouden met het doel waarvoor de motor gebruikt zal worden; de motor dient met zo min mogelijk kosten te worden opgebouwd om voldoende betrouwbaar te zijn voor de uitvoering van het project en het gebruik als onderwijsleermiddel.
De motor is op de ophangpunten van het versnellingsbakhuis aan de montagebok bevestigd. De motor kan in verschillende posities verdraaid worden. Daarmee zijn zowel de cilinderkop als de carterpan optimaal bereikbaar voor demontagewerkzaamheden. Voor het juist functioneren van de motor is het belangrijk om voorzorgsmaatregelen te nemen om voor een goede compressie-einddruk te zorgen. Bij een te lage druk van één of meerdere cilinders resulteert dit in een slecht werkende, haperende motor. In dat geval is het afstellen met de nieuw aan te brengen ontsteking en het injectiesysteem lastig, al dan niet onmogelijk.
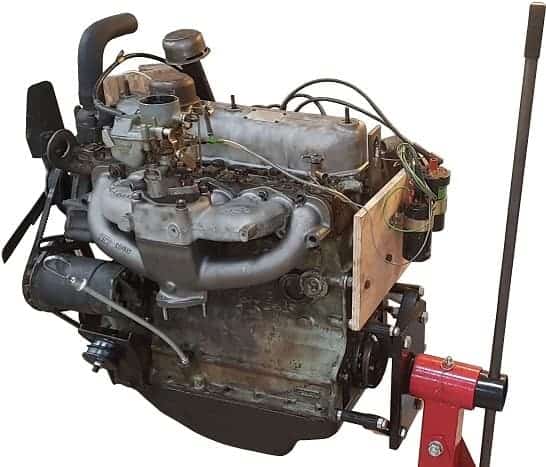
Eén van de eerste controlepunten zijn de zuigers en cilinderwanden. Om een goede controle uit te oefenen, dienden de zuigers uit het motorblok gedemonteerd te worden. Na demontage van de cilinderkop en de carterpan konden de zuigers er worden uitgenomen. De zuigers zijn gecontroleerd op ovaliteit en zichtbare slijtagesporen. Tevens zijn de zuigerveren op slijtage gecontroleerd. Versleten zuigerveren kunnen namelijk compressieverlies en olieverbruik veroorzaken; beide gevolgen dienen door deze controle voorkomen te worden. Behalve een optische controle, werd ook de speling tussen de zuigerveergroeven en de zuigerveer gemeten.
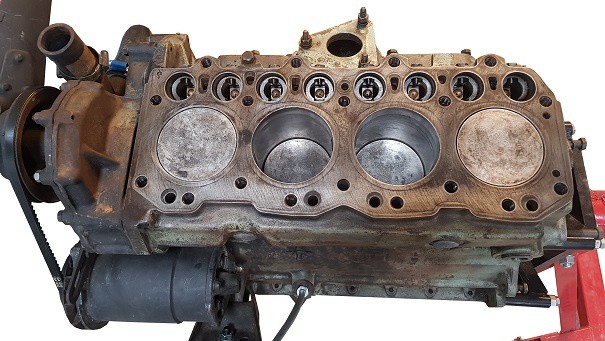
De onderstaande afbeelding laat een meting zien waarbij de zuiger wordt gemeten met een schroefmaat. Behalve de ovaliteit, kan ook de afstand tussen de zuiger en de cilinderwand worden bepaald. Een te grote afstand betekent dat er sprake is van overmatige slijtage. Voor het project zou dit betekenen dat er mogelijk andere overmaat zuigers geplaatst moeten worden. Nadat de vier zuigers optisch en meetkundig waren beoordeeld, kon worden vastgesteld dat er geen sprake was van overmatige slijtage.
Na vervanging van zuigerveren moet de slotspeling worden gemeten en eventueel worden aangepast om enerzijds te voorkomen dat de zuigerveer breekt (als gevolg van te kleine of te grote speling) en anderzijds om compressieverlies tegen te gaan (lekverliezen door een te grote speling). De zuigerveer wordt in de cilinder geplaatst waar de diameter het kleinst is. De slotspeling wordt met een voelermaat gemeten. Deze meting wordt in de afbeelding weergeven. De zuigerveren van cilinder 1 zijn vanwege hun slechte toestand vervangen en moesten een millimeter kleiner worden gevijld; in de gemonteerde toestand raakten de uiteinden elkaar.
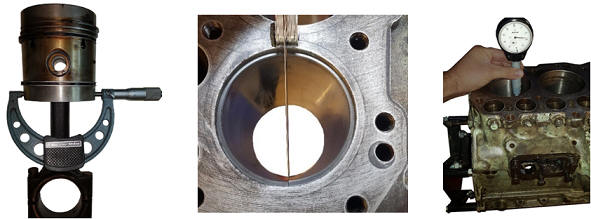
Het meten van de slijtage van de cilinderbussen wordt met een daarvoor geschikt meetobject uitgevoerd. De uitslag van de wijzer toont de mate van de slijtage. In de afbeelding is de cilindermeting van cilinder 4 te zien. Vooral aan de zijde waar de lijbaankracht optreedt, zal de cilinderdiameter zijn toegenomen. De cilinderwanden mogen enige slijtage vertonen, echter dient de slijtage wel binnen de toleranties te vallen. De meetresultaten toonden dat er een toelaatbare slijtage aan de cilinderwanden aanwezig was. Een optische controle van de cilinderbussen wees uit dat een aantal delen van de wanden glad waren. De hoongroeven waren niet of nauwelijks meer aanwezig.
De hoongroeven, een soort kleine krasjes, zorgen ervoor dat er ten alle tijden een kleine oliefilm tussen de zuigerveer en de cilinderwand aanwezig is. Deze oliefilm heeft als hoofdtaak smering, maar dient ook als afdichting en helpt dus mee aan het behalen van de compressie-einddruk. Met een daarvoor bestemde hoonsteen zijn in alle vier de cilinderbussen nieuwe hoongroeven aangebracht. De afbeelding toont deze bewerking. Er is getracht de hoongroeven zoveel mogelijk kruislings, onder een hoek van 45 graden aan te brengen.
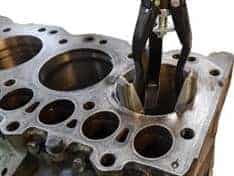
De kleppen dichten de verbrandingsruimte boven de zuiger af. Bij lekkage langs de klepzitting ontstaat er compressieverlies; iets wat voorkomen dient te worden. Om de toestand van de kleppen en de klepzitting te kunnen controleren, dienen in eerste instantie alle kleppen uit de cilinderkop verwijderd te worden. De afbeelding toont een gedemonteerde klepveer van de inlaatklep van cilinder 1. De klepschotels van de kleppen van cilinder 1 waren dusdanig aangetast dat er besloten werd om beiden te vervangen.
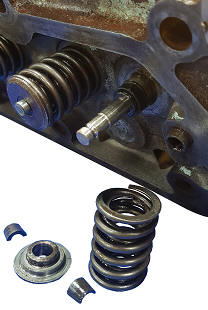
Na de demontage bleken een aantal klepzittingen te zijn ingevreten / aangetast. De onderstaande afbeelding toont de klepzittingen van cilinder 1. Met een grote mate van waarschijnlijkheid zou de motor niet goed hebben gefunctioneerd wanneer hier geen controle op was uitgevoerd. Enkel het opnieuw inschuren van de nieuwe kleppen zou onvoldoende zijn, dus werd besloten om de klepzittingen te frezen.
Met een klepzitting frees wordt er een kleine hoeveelheid materiaal verwijderd, zodat de klepzitting weer glad is. De steel van de frees wordt in de klepgeleider geschoven (zie onderstaande afbeelding). Hiermee is men er zeker van dat de frees recht op de zitting geplaatst kan worden. Tijdens het bewerkingsproces is rekening gehouden met twee verschillende hoeken waarin gefreesd moet worden. De kleppen van cilinder 1 en 2 waren het meest aangetast. Voor de volledigheid zijn alle acht klepzittingen bewerkt. Na het frezen zijn de kleppen met een speciaal schuurmiddel ingeschuurd om voor een zo goed mogelijke afdichting te zorgen.
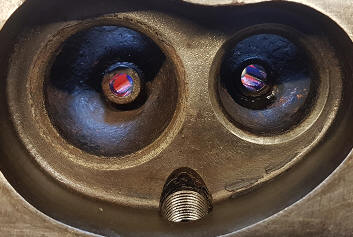
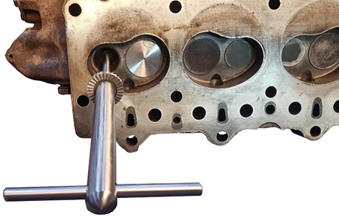
Met een meetklok wordt de axiale krukasspeling van de krukas met drie hoofdlagers en twee axiaallagers gemeten. Bij teveel axiale speling kan er, indien er geen sprake is van een mechanisch defect, een axiaallager van een groter formaat worden gemonteerd. De meting die in de afbeelding te zien is, toonde aan dat de axiaalspeling in orde was.
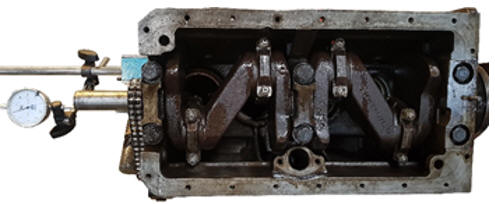
De ruimte tussen de glijlagers van de krukas en drijfstang, met andere woorden: de radiale krukasspeling, wordt gemeten met plastigage (zie afbeelding). Plastigage is een speciale kunststofdraad dat blijvend vervormt na het samenpersen. Na montage van de lagerkap of drijfstang zal de plastigage een afdruk achterlaten. De breedte van de afdruk geeft aan hoeveel speling zich tussen het glijlager en de krukas bevindt.
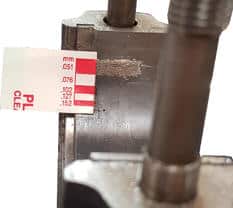
De distributieketting brengt de beweging van de krukas over naar de nokkenas. Na de montage van de zuigers, krukas en cilinderkop, dient de distributieketting na het bevestigen opnieuw afgesteld te worden. Vanwege het ontbreken van afstel- en merktekens, diende de afstelling bepaald te worden aan de hand van het asymmetrische kleppendiagram. Met behulp van een gradenschijf op de krukas kan worden bepaald onder welke hoek de inlaat- en uitlaatkleppen openen en sluiten (zie afbeelding). De distributie-onderdelen zoals de tandwielen, ketting, geleider en spanner zijn gecontroleerd op optische slijtage. Dit was in orde.
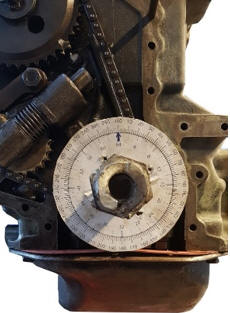
Alle onderdelen zijn volgens de voorgeschreven aanhaalmomenten vastgezet. Omdat de motor uit elkaar is gehaald, dienen na een aantal gereden kilometers controles te worden uitgevoerd. Echter, dit is niet mogelijk omdat de motor niet in een voertuig wordt ingebouwd. Daarom is besloten om na 24 draaiuren de door Land Rover voorgeschreven controles uit te voeren.
Motor op verrijdbaar frame monteren:
Het doel was om de motor in te zetten als onderwijsleermiddel, waarbij deze draait op een motormanagementsysteem. De motor wordt niet in een auto geplaatst. Om te zorgen voor een veilige en betrouwbare opstelling, is besloten om de motor op een geschikt motorframe te plaatsen. Het is de bedoeling dat de motor op de originele plaatsen van de motorsteunen op het motorframe wordt bevestigd. Omdat er geen kant en klare ombouwsets zijn, moesten de steunen op maat worden gemaakt.
n de opbouwfase moest de keuze gemaakt worden hoe de motor opgebouwd zou moeten worden. De afstelling van het motormanagementsysteem moet onder verhoogde motorbelasting plaatsvinden. Omdat op de originele versnellingsbak een transmissierem aanwezig is, werd er gekozen om ook de versnellingsbak op het motorframe te monteren. Met het bedienen van deze transmissierem is het mogelijk om de motor kortstondig belast te laten draaien.
Het bewerken en aanpassen van de bestaande motorsteunen heeft het mogelijk gemaakt om een de motor op een betrouwbare manier met het frame te verbinden. Het motorframe biedt tevens de mogelijkheid om een dashboard te bevestigen, waar o.a. de bediening op gerealiseerd kan worden. De afbeelding toont het moment waarop de motor boven het frame hangt en klaar is om bevestigd te worden.
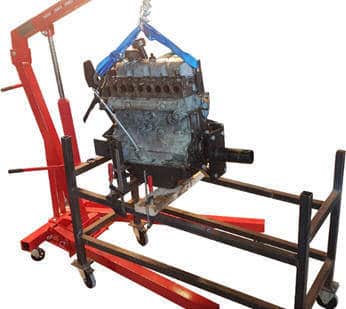
De motorsteunen aan de distributiezijde zijn vervaardigd uit stalen buizen en U-profielen. Een motorrubber zorgt voor de demping. Aan de onderzijde zijn twee buizen op elkaar gemonteerd om de combinatie van het motorblok en versnellingsbak zo horizontaal mogelijk op het frame te monteren. Door middel van M8 en M12 draadeinden, bouten en moeren zijn de steunen aan het motorblok en het frame bevestigd.
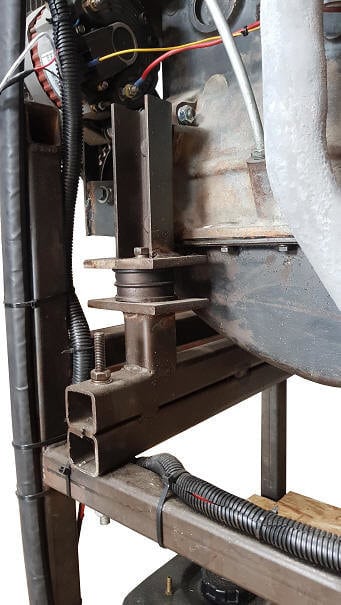
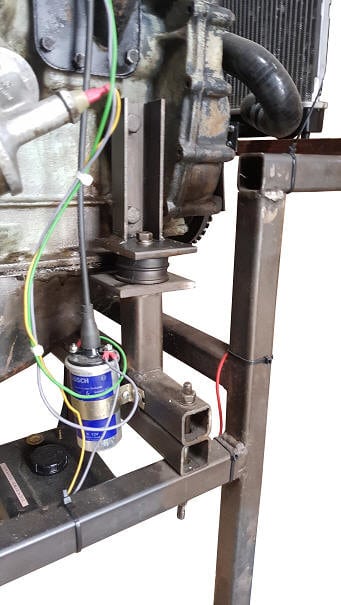
Aan beide zijden van de versnellingsbak is een dergelijke versnellingsbaksteun gemaakt waarmee deze op het frame rust.
Nadat de motor en versnellingsbak op een veilige en betrouwbare wijze op het frame waren gemonteerd, kon de opbouw van de motor worden hervat. Na de montage van instelbare en verstelbare onderdelen, denk daarbij aan de carburateur en de ontsteking, werden deze volgens de fabriekswaarden afgesteld.
Op het frame zijn ook andere componenten gemonteerd die het functioneren van de motor mogelijk maken, zoals de radiateur, het dashboard met bedieningsmogelijkheden en de brandstoftank. Deze componenten worden in de volgende paragrafen beschreven.
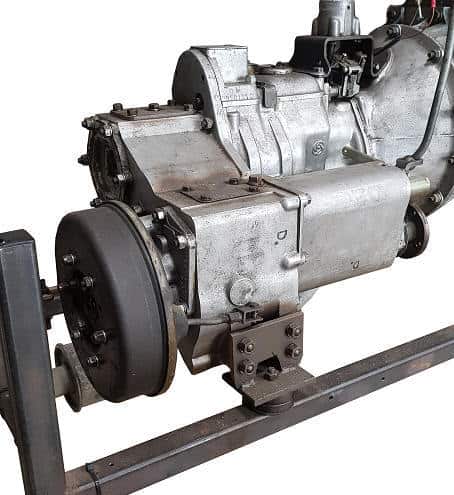
Koeling:
De koeling wordt in originele toestand gerealiseerd door een grote radiateur en een – op de waterpomp gemonteerde – metalen koelventilator. Omdat de motor niet in een voertuig wordt ingebouwd, maar op een verrijdbaar frame, is het van belang om geschikte aftermarket componenten te gebruiken. De metalen koelventilator werd vervangen door een elektrisch aangedreven koelventilator met plastic ventilatorbladen. Niet alleen is de plastic uitvoering een stuk veiliger daar de motor geschikt wordt gemaakt voor onderwijsdoeleinden (denk daarbij aan de persoonlijke veiligheid bij het verrichten van metingen) maar is ook meer geschikt voor het sneller opwarmen van de radiateur en het motorblok. De elektrische koelventilator is met een knop op het dashboard in en uit te schakelen. Dit geeft de mogelijkheid om de motor snel op te laten warmen, want er is immers weinig mogelijkheid om hem mechanisch te belasten. Bij een opgewarmde motor is er eerder sprake van een “closed loop” waarbij de gegevens van de lambdasonde worden gebruikt om de brandstofinspuiting te regelen. Bij koude motor – in “open loop” – wordt er bijvoorbeeld extra verrijkt: bij het inspuiten van een grotere hoeveelheid brandstof ( λ < 1) is de brandstofcorrectie door de lambdasonde ongewenst.
De afbeelding toont een overzicht van de componenten van het gemonteerde koelsysteem. De originele radiateur was niet aanwezig. Omdat het formaat en het gewicht hiervan niet geschikt waren om op het motorframe te monteren, is er gekozen voor een kleinere after-market radiateur. De diameters van de aansluitingen van de bovenste en onderste radiateurslangen komen overeen met de originele.
De bovenste en onderste radiateurslangen zijn op maat gemaakt met siliconen slangen en koppelstukken. De elektrische koelventilator is op een montagesteun vastgezet. De bovenste radiateurslang beschermt de radiateur tegen het kantelen. Met een overdrukdop (0,9 bar) wordt het koelsysteem beschermd tegen te hoge drukken. Wanneer de druk te hoog oploopt, wordt de klep in de radiateurdop tegen de kracht in geopend en stroomt er koelvloeistof door de overloop naar een opvangbak.
Proefondervindelijk moest worden vastgesteld of de radiateur een voldoende hoge doorstroommogelijk had en of de koelventilator voldoende capaciteit had om de warmte af te voeren. Tijdens de eerste testfase is het systeem in orde bevonden.
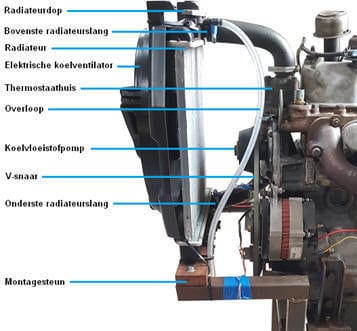
Dashboard en elektrische installatie:
Op het frame is een dashboard bevestigd waarop zich controlelampjes, schakelaars, de MegaSquirt ECU, diverse relais en kabelbundels bevinden. Het dashboard wordt gebruikt om de motorfuncties te controleren en te bedienen.
Op de afbeelding is het dashboard te zien. Nummer 1 in de figuur geeft de plek van de massa-schakelaar aan; een sleutel verbreekt de verbinding met de massa van de accu. Omdat het niet nodig is om de uitgeschakelde motor van spanning te voorzien, is het veiliger om de massa te onderbreken wanneer de motor onbeheerd wordt achtergelaten. Nummer 2 geeft de schakelaar voor de koelventilator aan. Nummer 3 en 4 de controlelampjes voor de dynamo (D+), nummer 5 de startknop en nummer 6 de contactschakelaar (klem 15). Aan de achterkant van het dashboard bevindt zich een zekeringenkast. De MegaSquirt is op het onderste paneel aangebracht en wordt met nummer 7 aangegeven. Nummer 8 geeft het brandstofpomprelais aan. Het dashboard biedt tevens de mogelijkheid om een breakout-box te monteren waarop studenten metingen kunnen verrichten. Hiermee wordt het mogelijk gemaakt om de sensorwaarden en actuatoraansturingen met de oscilloscoop te meten.
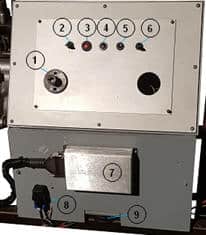
Het originele startrelais verzorgd de aansturing van de startmotor; met een kleine startknop wordt pin 86 aan massa gelegd, waardoor er een stuurstroom gaat lopen. De stuurstroom verzorgd een magnetisch veld, waardoor er een hoofdstroom gaat lopen tussen klem 30 en 87; de startmotor wordt voorzien van deze hoofdstroom tot dat de startknop wordt losgelaten.
De achteraf gemonteerde wisselstroomdynamo verzorgd de laadspanning en laadstroom naar de accu. Een controlelampje geeft een indicatie of de dynamo goed laadt. De lambdasonde, injectoren en bobine krijgen een voedingsspanning vanaf de zekeringenkast. Via andere signaal- en massadraden worden de informatieoverdracht en in- en uitschakelcommando’s van de MegaSquirt verzorgd.
Brandstofpomp en tank.
De mechanische brandstofpomp in de klassieke opstelling wordt bij het aanbrengen van de componenten van het motormanagementsysteem niet meer gebruikt, omdat de werkdruk te laag is (200mbar). De benodigde brandstofdruk voor MPI-injectoren die door de MegaSquirt ECU worden aangestuurd bedraagt 3 bar. Een standaard elektronische brandstofpomp uit een personenauto volstaat. Er is vanwege de beperkte ruimte gekozen voor een compacte unit, waarin de brandstoftank, pomp en filter in één behuizing zitten. Een metalen frame maakt het mogelijk om de unit aan het motorframe te monteren. In een later stadium van het project zullen de brandstofslangen worden geplaatst die de verbinding tussen de brandstofpomp en de injectoren in het inlaatspruitstuk vormen.
De voedingsdraden van de brandstofpomp zijn lopen via een kabelgoot naar het instrumentenpaneel waarvan de montage reeds is beschreven. De plusdraad van de pomp wordt via een relais door de MegaSquirt bekrachtigd.
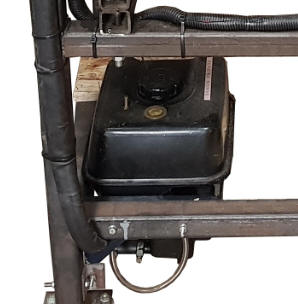
Motor in klassieke opstelling laten functioneren.
Voordat de componenten voor het motormanagementsysteem worden aangebracht, werd de motor in eerste instantie functioneel gemaakt in de klassieke opstelling, dus met carburateur en verdelerontsteking. In hoofdstuk 5.2 zijn de werkzaamheden beschreven die hebben plaatsgevonden om de motor en hulpcomponenten op het motorframe te monteren. In de eerste testfase, waarbij de motor in de klassieke opstelling gestart werd, konden er controles worden gedaan tijdens de volgende omstandigheden:
- Koude start;
- Stationair draaien;
- Verhoogd toerental, verhoogde belasting;
- Langdurig draaien op bedrijfstemperatuur.
Tijdens de bovenstaande controles bleek dat er nog een aantal reparaties plaats moesten vinden voordat de motor betrouwbaar genoeg was voor de ombouw.
- Na de eerste motorstart bleek dat de afdichting in de koelvloeistofpomp niet meer in orde was; de koelvloeistof lekte langs het lager uit het motorblok. Het vervangen van de koelvloeistofpomp was voldoende om het probleem op te lossen.
- Een volgend probleem was het afslaan wanneer de motor op bedrijfstemperatuur kwam. De ontsteking viel weg, waardoor de motor niet meer gestart kon worden. Het probleem bevond zich in de verdeler en kon makkelijk worden opgelost.
- Na verloop van tijd vormde zich een olielekkage tussen de motor en de versnellingsbak. De lekkage is vermoedelijk afkomstig van de krukaskeerring. Deze lekkage zal na het afronden van het project worden opgelost.
Nadat de motor in de klassieke opstelling in orde werd bevonden, kon er verder worden gegaan met de elektronica.
Volgende: Sensoren.