Onderwerpen:
- Actuatoren voor het motormanagementsysteem bepalen en aanbrengen
- Brandstofinjectoren
- Het kiezen van geschikte injectoren
- Montage van de injectoren in het inlaatspruitstuk
- Ontsteking
- Het voorbereiden met de conventionele ontsteking
- Bobine voor het motormanagementsysteem
- Stroomopbouw in de primaire spoel
- Ontstekingsvervroeging
- Gasklephuis
- Testopstelling van de stappenmotor met simulator
- Instellingen voor de stappenmotor
- Brandstofpompcircuit
- Afronden van de mechanische werkzaamheden
Actuatoren voor het motormanagementsysteem bepalen en aanbrengen:
De actuatoren die met de MegaSquirt zullen worden aangestuurd, zijn de injectoren, bobine, brandstofpomp en de stappenmotor voor het stationaire toerental. Dit hoofdstuk beschrijft het proces waarin de actuatoren zijn getest en op het motorblok zijn aangebracht, en welke keuze daarvoor zijn gemaakt.
Brandstofinjectoren:
De MegaSquirt stuurt de injectoren aan. De injectoren zijn massa geschakeld. Bij een massa geschakeld component is er een voedingsspanning aanwezig, maar loopt er pas stroom wanneer de massa wordt ingeschakeld. In dit geval zal de injector pas inspuiten wanneer de MegaSquirt ECU de massa schakelt. Zodra de bekrachtiging wordt beëindigd, stopt de injector met inspuiten. De hoeveelheid in te spuiten brandstof wordt bepaald aan de hand van de VE-tabel en AFR-tabel.
Een MOS-FET schakelt de injector in- en uit waardoor de brandstof wordt ingespoten. De hoeveelheid brandstof welke door de MegaSquirt wordt bepaald, hangt van verschillende factoren af:
- De ideale gaswet die de hoeveelheid lucht relateert aan zijn druk, volume en temperatuur;
- Gemeten waarden door de sensoren in het motorblok: druk in het inlaatspruitstuk (MAP-sensor), koelvloeistof- en inlaatluchttemperatuur, krukastoerental en de gegevens van de gaskleppositiesensor;
• Afstelparameters: benodigde brandstofhoeveelheid, vullingsgraad (VE), openingstijd van de injector en verrijking onder bepaalde omstandigheden.
De injectietijd moet zo lang mogelijk zijn tijdens het stationair draaien van de motor om een goede brandstofdosering te verkrijgen. Daarom kan niet zomaar iedere willekeurige injector kan worden toegepast op de motor. De eigenschappen van verschillende soorten injectoren dienen vergeleken te worden en berekeningen moeten inzicht verschaffen in de benodigde brandstofhoeveelheid voor de betreffende motor. Er was ook nog een keuze mogelijk tussen hoog- en laag impedante injectoren. Laag-impedante injectoren zijn geschikt voor motoren waarbij een zeer snelle opening van de injectornaald benodigd is. De typische weerstand bedraagt 4 Ohm. Het nadeel van deze injectoren is de hoge stroomsterkte. De warmteontwikkeling die hierdoor in de MegaSquirt ontstaat is onwenselijk. Het is wel mogelijk om laag-impedante injectoren toe te passen door speciale IGBT’s op een warmtegeleidende plaat op de MegaSquirt-behuizing te monteren. Er is gekozen om hoog-impedante injectoren toe te passen. Hierbij is er minder sprake van warmteontwikkeling en worden deze IGBT’s niet gebruikt.
De doorlaatgrootte (flow) van groot belang om de juiste inspuithoeveelheid, en daarmee dus de aansturing te bepalen. Bij de keuze voor te grote injectoren, zal de inspuittijd bij een stationair toerental dusdanig kort zijn, dat de motor wellicht onregelmatig zal gaan draaien. De injectiehoeveelheid moet voldoende zijn om alle brandstof te kunnen injecteren in de beschikbare tijd. De injectiehoeveelheid wordt aangegeven als injectietijd in milliseconden. Uitgegaan wordt van een hoge belasting bij een hoog motortoerental. Dit is bij een MAP van 100 kPa. Aan de hand van de motoreigenschappen kan de benodigde injectorflow berekend worden. De injectorflow geeft aan hoeveel milliliter brandstof er per minuut wordt ingespoten.
Het kiezen van de geschikte injectoren:
Voor het project zijn injectoren van drie verschillende types beschikbaar gesteld. Onderzoek wees uit welk type injector het meest geschikt was om in dit project toe te passen.
Elk type injector heeft een andere flow; de opbrengst na een minuut lang inspuiten verschilt per type. Voordat de injectoren werden getest, ondergingen ze een reinigingsbeurt in een ultrasoonbad. Met deze reinigingsmethode wordt de injector van binnen en van buiten door middel van ultrasone trillingen en een speciale testvloeistof gereinigd, zodat eventuele oude vuilresten geen invloed kunnen uitoefenen op de flowmeting of het inspuitbeeld. Tijdens de ultrasoonreiniging werden de injectoren continu geopend en gesloten en is het inspuitbeeld van elke injector bekeken; dit was een mooie nevel. Bij het sluiten waren er geen afwijkingen te zien, zoals druppelvorming of een afwijkende straal. Na het ultrasoon reinigen en het testen zijn de O-ringen vervangen, zodat er een goede afdichting gegarandeerd kan worden bij montage in het inlaatspruitstuk.
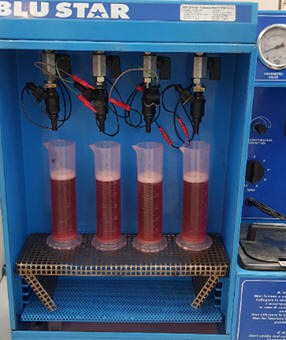
Middels een testopstelling (zie bovenstaande afbeelding) kunnen de injectoren in meerdere maatbekers inspuiten, zodat de ingespoten hoeveelheid brandstof na een bepaalde tijd kan worden afgelezen. Met het aansturen van de injectoren onder een werkdruk van 3 bar kan de hoeveelheid ingespoten brandstof worden gecontroleerd. De brandstofdruk op toevoerleiding (de rail) moet 3 bar bedragen en de injectornaald moet gedurende 30 of 60 seconden met een duty cycle van 100% worden aangestuurd. Nadat de injectoren gedurende 30 seconden waren aangestuurd, konden de volgende gegevens worden ingevuld:
Type 1: 120 ml
Type 2: 200 ml
Type 3: 250 ml
Slechts één type injector zal worden gebruikt. Middels de onderstaande formule wordt de injectorgrootte bepaald:

De injectorgrootte wordt bepaald aan de hand van het effectieve vermogen (Pe) dat bij een bepaald toerental wordt geleverd, de Break Specific Fuel Consumption (BSFC), het aantal injectoren (n injectoren) en de maximale duty cycle waarmee de injectoren worden aangestuurd. Het geheel wordt met 10.5 vermenigvuldigd om van pund per hour (lb/hr) naar ml/min om te rekenen.
Het antwoord op de berekening geeft aan welke injector voor deze motorconfiguratie geschikt is. Het is geen probleem wanneer er minder dan 20 ml wordt afgeweken van de berekende waarde. Met het aanpassen van de software in de MegaSquirt wordt dit verschil weer gecompenseerd. De volgende tabel weergeeft een overzicht van de gegevens die in de formules worden gebruikt:
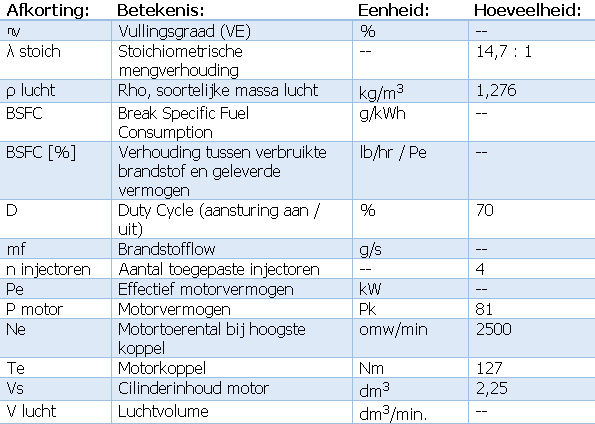
De eerste stap is het bepalen van de ingespoten brandstof bij het koppel-toerental. Per twee omwentelingen van de krukas wordt er een bepaalde hoeveelheid lucht aangezogen. Bij het koppel-toerental is de vullingsgraad het hoogst. Vanwege de motoreigenschappen (onder anderen de klepoverlap) vult de motor bij dit toerental het beste is het rendement het hoogst. Naar schatting zal de vullingsgraad rond de 70% bedragen. In formule 4 wordt het luchtvolume berekend dat op dat moment in de motor aanwezig is.
In formule 5 wordt de hoeveelheid ingespoten brandstof berekend aan de hand van het aanwezige luchtvolume. Het motorvermogen dat bij het koppeltoerental wordt bereikt wordt in formule 6 berekend. De verhouding tussen de hoeveelheid ingespoten brandstof en het vermogen geeft in formules 7 en 8 de BSFC aan.
De werkelijke BSFC wordt in formule 6 vermenigvuldigd met 3600 om naar kWh te rekenen. De BSFC van een benzinemotor bedraagt vaak tussen de 250 en 345 g/kWh. Hoe lager de waarde is, hoe efficiënter de motor is. Formule 8 geeft de verhouding tussen de brandstofflow aan in pound / hour en het effectieve motorvermogen. Dit percentage wordt in formule 9 overgenomen.



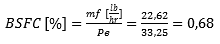

Met het antwoord op formule 9 is duidelijk geworden dat de injectoren met een flow van 200 ml/min geschikt zijn om toe te passen op de motor. Het verschil van 7 ml is verwaarloosbaar omdat dit in de software wordt gecompenseerd tijdens het invullen van de VE-tabel.
Montage van de injectoren in het inlaatspruitstuk:
Het elektronisch geregelde inspuitsysteem maakt het mogelijk dat de carburateur, die deel uitmaakt van de klassieke opstelling, kon worden verwijderd. De carburateur wordt dus vervangen door een gasklephuis (voor de luchttoevoer) en vier aparte brandstofinjectoren. Het inlaatspruitstuk bleef behouden en werd aangepast om de ombouw naar het motormanagementsysteem mogelijk te maken. De brandstofinspuiting vindt plaats in het inlaatspruitstuk. Er is gekozen om de injectoren zo dicht mogelijk bij de inlaatklep te monteren. Constructeurs van automotoren kiezen er in de meeste gevallen voor om de inlaatklep onder een hoek in het inlaatspruitstuk te bevestigen. De brandstof wordt daarbij tegen de inlaatklep gespoten. Bij het huidige project is echter gekozen voor een opstelling waarbij de injectoren onder een hoek van 45 graden ten opzichte van de luchtkanalen in het spruitstuk geplaatst worden.
Het inlaatspruitstuk is vervaardigd uit gegoten aluminium. Gekozen is om aluminium busjes op het spruitstuk te bevestigen. Handmatig tot een goede maat bewerken was geen optie, omdat de busjes afwijkende afmetingen moesten hebben dan een standaard maat van een boor. Dat betekende wel dat het uitbesteden van de busjes uitbesteed moest worden naar een bedrijf met geschikte apparatuur. De busjes konden daarna door middel van TIG-lassen aan het spruitstuk worden bevestigd. De keuze om de injectoren rechtop te monteren in plaats van onder een hoek, is gemaakt om de volgende reden:
- Het montageproces: het is makkelijker om de busjes in een rechte, horizontale opstelling op te stellen. Het lassen van de busjes op het spruitstuk is eenvoudiger doordat er nu makkelijker rondom gelast kan worden dan in de situatie waarbij het busje onder een hoek staat.
- De nabewerking: Tijdens het lassen worden de busjes een beetje ovaal. De vervorming ontstaat door de warmte die vrijkomt tijdens het lasproces. Hiermee is rekening gehouden door de binnendiameter van de busjes kleiner te maken dan de buitendiameter van de injectoren. Het nabewerken (het ruimen) is minder risicovol: wanneer de busjes van binnen weer zijn rondgemaakt is de diameter optimaal voor de injectoren, waarbij de afdichting door de O-ringen gewaarborgd is. De hoogte van de busjes is belangrijk; de injector mag niet te ver in het spruitstuk worden aangebracht. Het uiteinde van de injector mag de luchtstroming niet belemmeren. Uit de informatie van bron: (Banish, Engine Management, advanced tuning, 2007) is besloten de injectoren dusdanig diep in het spruitstuk te monteren, dat de uiteinden zich precies in de gaten van het spruitstuk bevinden; de luchtstroming wordt niet gehinderd.
- Brandstofinspuiting: Omdat de vermenging van de brandstofnevel met de lucht optimaal is voordat de inlaatklep opent, maakt het niet zoveel uit of de injector exact op de inlaatklep inspuit, of vlak daarvoor in het inlaatspruitstuk.
Bij simultane inspuiting vindt de inspuiting iedere krukasrotatie (360°) plaats. De vier injectoren spuiten tegelijk in. Dat betekent dat er ook brandstof in het inlaatkanaal wordt gespoten terwijl de inlaatklep niet geopend is. Enige tijd later opent de inlaatklep en komt de brandstof alsnog in de cilinder terecht.
De busjes zijn speciaal op maat op een draaibank geslepen. De binnendiameter is iets kleiner dan de buitendiameter van de injector; doordat er vervorming plaatsvindt tijdens het lasproces, moet er bij de nabewerking nog een mogelijkheid zijn om materiaal te verwijderen door middel van het ruimen. Dat betekent dat de diameter iets groter wordt omdat er materiaal weggeslepen wordt. De diameter mag niet te groot worden, omdat dan de kans bestaat dat de rubberen O-ring op de injector niet goed genoeg meer kan afdichten. Een goede afdichting is erg belangrijk; lucht-lekkage langs de injector resulteert in een lagere onderdruk in het inlaatspruitstuk.
De gemeten onderdruk komt dan niet meer overeen met de berekende onderdruk. Dit heeft invloed op de inspuiting die aan de hand van de VE-tabel wordt bepaald. De onderdruk speelt hierbij een grote rol. De kenmerken en de instellingen van het VE-tabel worden in een volgend hoofdstuk beschreven.
Aan de onderzijde van de busjes is een schuine kant gevijld, zodat de vormen overeenkomen met die van het inlaatspruitstuk. Het busje moet daarmee zo recht mogelijk overeind komen te staan. In de onderstaande afbeelding is het inlaatspruitstuk met een busje te zien tijdens het assemblageproces. Het busje is aan één zijde gehecht, zodat goed bekeken kan worden wat het lassen voor invloed heeft op het materiaal. Onduidelijk was of het aluminium van het spruitstuk niet teveel vervuiling bevatte waardoor het lassen bemoeilijkt zou worden. Dit bleek in orde. Om te voorkomen dat de busjes tijdens het lassen van hun plek zouden kunnen verschuiven, zijn van te voren gaten in het spruitstuk geboord en met een speciaal op maat gemaakte mal de busjes op de juiste positie gehouden. Op die manier zijn de vier busjes rondom vast gelast. Een laatste controle liet blijken dat de verbindingen tussen de busjes en het spruitstuk luchtdicht waren.
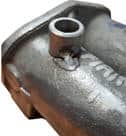
De verbinding tussen de injectoren wordt normaliter gevormd door een massieve injectorrail. Deze buis met aansluitingen, veelal van een aluminiumlegering, is door een constructeur precies op maat gemaakt. Bij de Land Rover motor die voor het project gebruikt wordt, zitten er twee injectoren vlak naast elkaar, maar is de ruimte tussen de tweetallen injectoren best groot. De afmetingen van de brandstofrail en de ruimte tussen de luchtkanalen van het inlaatspruitstuk kwamen niet overeen. De rail moest daarom worden aangepast.
Het op sommige stukken inkorten en de andere delen verlengen is door middel van solderen erg lastig; de vervuiling door oude brandstof, welke zeer lastig uit de binnenzijde van de rail te verwijderen is, kan zorgen voor een verslechterde hechting. Omdat het brandstof betreft, is er gekozen voor de meest veilige manier; de delen waarop de injectoren bevestigd worden, zijn door middel van een hoogwaardige brandstofslang met elkaar verbonden. Aan alle uiteinden zijn felsranden aangebracht en er zijn stevige slangklemmen toegepast die voorkomen dat de slangen over de felsranden glijden.
De onderstaande afbeelding toont het inlaatspruitstuk ten tijde van de bewerking zien. De toevoerleiding (aangegeven met nummer 1) is verbonden met de uitgang van de brandstofpomp. Onder een druk van 3 bar wordt de brandstof op de ingang van de vier injectoren gezet. De drukregelaar (3) regelt de druk afhankelijk van de inlaatspruitstukdruk af, omdat het drukverschil tussen de brandstofdruk en de onderdruk in het inlaatspruitstuk 3 bar moet blijven. Via de retourleiding (2) stroomt de brandstof weer naar de tank. Er vindt een continue circulatie van brandstof plaats. Pas wanneer de injectoren door de MegaSquirt ECU worden aangestuurd, vindt een inspuiting plaats.
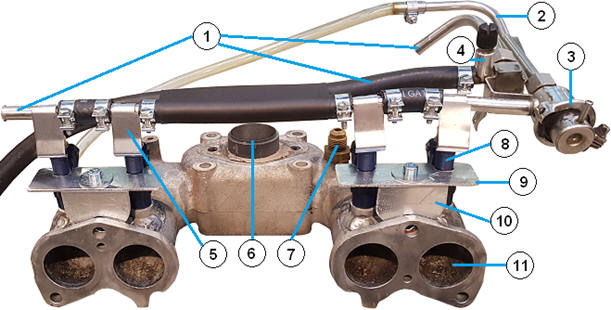
- Toevoerleiding
- Retourleiding
- Drukregelaar
- Drukcontrole
- Hitteschild
- Gasklepaansluiting
- Onderdrukaansluiting
- Injector cilinder 1
- Injectorbeugel A
- Injectorbeugel B
- Inlaatkanaal cilinder 1
Bij bestaande personenauto’s wordt de injectorrail met behulp van klemmen of oogjes aan het inlaatspruitstuk bevestigd. De injectorrail klemt daarbij de injectoren in het spruitstuk. Omdat er voor dit project is gekozen voor een flexibele brandstofslang als injectorrail, is eerder genoemde niet mogelijk. Daarom is er besloten om de injectoren met een op maat gemaakte beugel in het inlaatspruitstuk te klemmen. De beugels bestaan uit twee delen: bovenste deel (beugel A) en het onderste deel (beugel B).
Beugel A bevat twee inkepingen die over de injectoren geschoven kunnen worden. Hiermee kunnen de injectoren door middel van de platte kanten in het spruitstuk worden gedrukt. In beide beugels A zitten sleufgaten, zodat de afstand waarin de injectoren zich in de sleufgaten bevinden, kan worden afgesteld. Beugels A en B worden op elkaar geschroefd: beugel B wordt aan hetzelfde tapeind bevestigd als waarmee het spruitstuk op de motor gemonteerd zit. Een sleufgat maakt het mogelijk dat de beugel in verticale richting te verstellen is. Hoe meer de beugel naar onderen wordt bewogen, des te krachtiger de injector vastgeklemd.
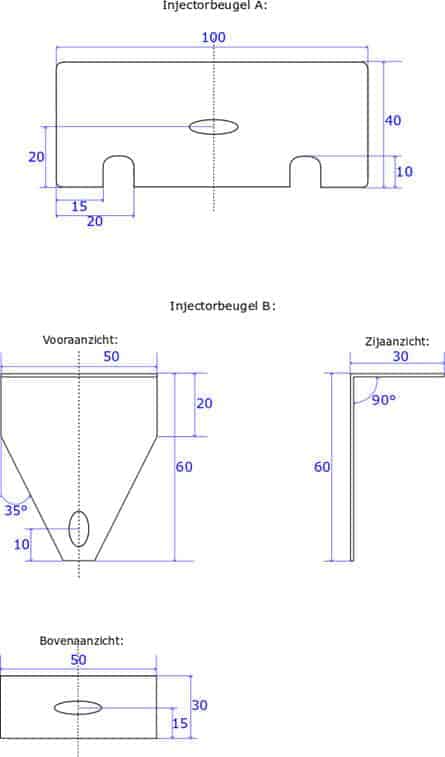
Ontsteking:
De conventionele ontsteking is vervangen door een elektronisch geregeld ontstekingssysteem met bobine die door de MegaSquirt wordt aangestuurd. Om de motor eerst volledig te laten functioneren op de originele technieken, dient in eerste instantie het conventionele systeem met contactpunten aangesloten te worden. Pas na een aantal draaiuren kan worden vastgesteld dat de motor goed functioneert, waarna begonnen kan worden aan het monteren en afstellen van o.a. de elektronisch aangestuurde ontsteking.
Het voorbereiden met de conventionele ontsteking:
De Land Rover motor is van origine uitgevoerd met een ontstekingssysteem met contactpunten, wat tegenwoordig ook wel een conventioneel ontstekingssysteem wordt genoemd. De afbeelding toont dit type ontstekingssysteem.
Bij gesloten contactpunten begint de opbouw van de primaire stroom. De stroomsterkte wordt beperkt tot 3 á 4 Ampère door de weerstand van de primaire wikkeling. Wanneer er een stroom door de primaire spoel van de bobine vloeit, zal een magnetisch veld worden opgebouwd. Zowel de primaire (3) als de secundaire spoel (4) bevinden zich in dit magnetische veld. Wanneer de stroom door de contactpunten (10) door de onderbrekernok (9) op de verdeleras worden onderbroken, wordt er in beide spoelen een spanning opgewekt. In de primaire spoel ontstaat ongeveer 250 volt. Het verschil in wikkelingen zal in de secundaire spoel een inductiespanning van 10 tot 15 kV ontstaan. Op het moment van openen van de punten ontstaat de bougievonk.
De inductiespanning kan worden beperkt door na het openen van de contactpunten de primaire stroom nog even door te laten vloeien. Dit wordt bereikt met een condensator, die parallel over de contactpunten is geschakeld. De condensator is hierbij een tijdbepalend element die, afhankelijk van de capaciteit, in feite de hoogte van de inductiespanning afregelt. Ook wordt voorkomen dat de contactpunten inbranden.
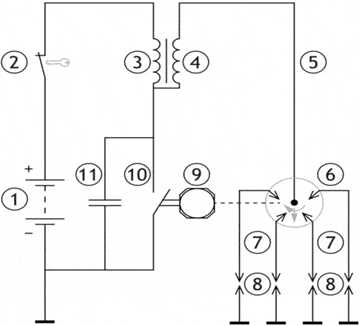
Bobine voor het motormanagementsysteem:
Het motormanagementsysteem zal de aansturing van de bobine verzorgen. De klassieke bobine met verdeler blijven wel op de motor aanwezig om te dienen als testopstelling, maar maken geen deel meer uit voor het functioneren van de verbrandingsmotor. Er is gekozen voor een Distributorless Ignition System (DIS-bobine), vrij vertaald als: “verdelerloos ontstekingssysteem”. Dit type ontstekingssysteem maakt geen gebruik van een verdeler. Een andere mogelijkheid was het kiezen voor een Coil on plug (COP) bobine. Daarbij wordt op elke bougie een aparte bobine aangesloten. Een COP-bobine wordt ook wel een penbobine genoemd. Het nadeel van een COP-bobine is dat de warmteafvoer minder goed is dan van een DIS-bobine. Ook is bij het toepassen van COP-bobines een signaal van een nokkenassensor nodig, wat op de huidige motor niet aanwezig is.
De ontbrekende tand in de krukaspoelie dient als het referentiepunt waarmee het ontstekingstijdstip wordt bepaald. Bij de DIS-bobine zullen op een ontstekingsmoment twee bougies tegelijk worden aangestuurd. De DIS-bobine is in feite een unit waar twee bobines in gemonteerd zitten. Wanneer de zuigers van cilinder 1 en 4 met naar boven bewegen, zal één met de compressieslag bezig zijn en de ander met de uitlaatslag. Toch zullen beide bougies een vonk genereren. De vonk die ontstaat bij de cilinder die bezig is met de compressieslag zal zorgen voor een ontbrandend mengsel. De andere vonk, de zogenaamde “wasted spark” vonkt terwijl het uitlaatgas de verbrandingsruimte verlaat. De wasted spark is een vonk die wordt gevormd wanneer er geen mengsel wordt ontbrandt. De ontstekingsenergie is laag; ondanks de vonk is er weinig energieverlies. Ook is het niet schadelijk.
In de afbeelding is het arbeidsdiagram van een viercilinder benzinemotor met een DIS-bobine te zien. In dit arbeidsdiagram staan twee ontstekingsmarkeringen per ontstekingsmoment; 1 daarvan genereert de vonk om het mengsel te ontsteken, de ander is de wasted spark. Een DIS-bobine kan met slechts twee pulsen door de MegaSquirt worden aangestuurd.
Wanneer in cilinder 1 de compressieslag en in cilinder 4 de uitlaatslag plaatsvinden, stuurt de MegaSquirt via pin 36 op DB37 (zie onderstaande afbeelding) de primaire spoel A aan. Deze aansturing vindt plaats aan de hand van het krukasreferentiepunt (tussen de 90 en 120 graden voor het BDP). De MegaSquirt stuurt de primaire spoel B, welke verantwoordelijk is voor de vonkvorming van cilinder 2 en 3, wordt 180 graden na spoel A aan. Voor spoel B is er geen referentiepunt aanwezig, maar het ontstekingstijdstip kan simpelweg door het tellen van de tanden op het 36-1 pulswiel worden bepaald.
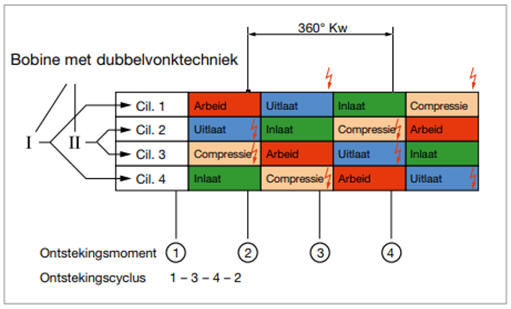
Tussen spoel A van de bobine en pin 7 van de processor is een weerstand van 330 ohm afgebeeld. Deze weerstand beperkt de stroom en inductiespanning van de aanstuurpuls. Omdat deze weerstand zich niet standaard op de MegaSquirt-printplaat bevindt, moet deze achteraf worden gemonteerd. Links van de verticale onderbroken streeplijn in de onderstaande afbeelding wordt het interne circuit van de MegaSquirt getoond. De getoonde componenten (de twee weerstanden van 330 Ohm en de LED’s) dienden achteraf op de printplaat gesoldeerd te worden.
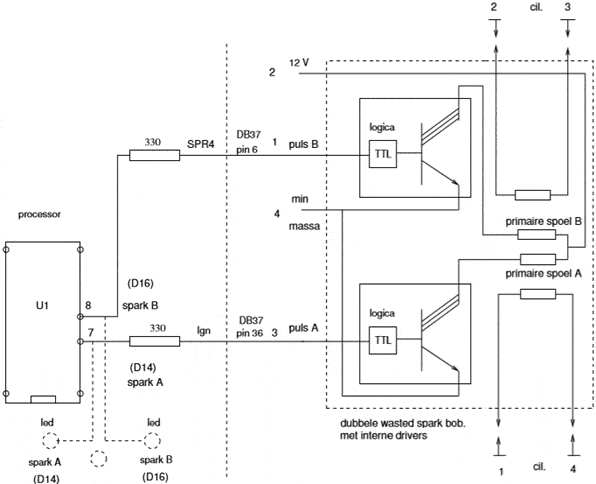
Stroomopbouw in de primaire spoel:
Het is belangrijk om inzicht te krijgen over de stroomopbouw in de primaire spoel. Niet alleen de stroomsterkte, maar ook de laadtijd van de bobine kan hiermee bepaald worden. De laadtijd is van een aantal factoren afhankelijk, waar de MegaSquirt rekening mee moet houden.
De zelfinductiecoëfficiënt (L-waarde) van de gekozen bobine bedraagt 3,7mH. Samen met de ohmse weerstand R wordt de maximale primaire stroom en de stijgtijd van de kromme bepaald. Een kleine L-waarde en weerstand zorgt ervoor dat de stroom na het inschakelen snel stijgt. Met de bekende gegevens van de bobine kan worden berekend hoe de primaire stroom wordt opgebouwd.
De volgende formule toont de algemene oplossing van de 1e orde differentiaalvergelijking, waarmee de stroomsterktes, laad- en ontlaadtijden worden berekend om het schakelverschijnsel middels een curve te tonen.
De vergelijking luidt:

waarbij de tijdsconstante (Tau) als volgt wordt berekend:

De maximale stroom zou volgens de Wet van Ohm 28 Ampère bedragen:
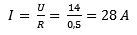
In werkelijkheid zal deze stroomsterkte niet worden behaald.
De spoel wordt eerder uitgeschakeld. De reden wordt verderop verklaard. Het invullen van deze gegevens in de algemene formule geeft:
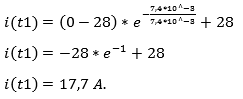
De afbeelding toont de ladingscurve van de primaire spoel. Vanaf het tijdstip T0 naar 1 Tau wordt de spoel voor 63,2% geladen. Dit is een vast percentage voor de ladingstijd van een spoel. De uitkomst van formule 13 toont aan dat de spoel bij 1 Tau met 17,7 Ampère geladen is. Op t = 5 Tau is de eindwaarde praktisch bereikt.
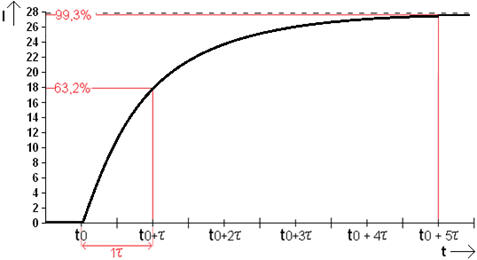
Volgens de specificaties van de bobine bedraagt de primaire stroom van de bobine na het opladen 7,5 A. De stroom loopt daarbij niet hoger op. De tijd die ervoor nodig is om de 7,5 A te bereiken, wordt de dwell-tijd genoemd. De dwell-tijd is afhankelijk van de accuspanning, welke in dit geval 14 volt bedraagt. De stroom door de spoel bedraagt, wanneer het laadproces niet wordt afgeregeld, volgens formule 12 maximaal 28 Ampère.
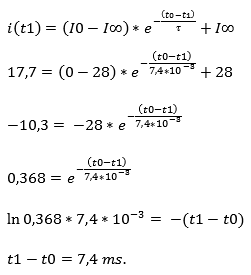
De spoel volgens formule 14 is bij t = 7,4 ms tot 17,7 A geladen. De daadwerkelijke laadtijd is korter, omdat de spoel tot maximaal 7,5 A wordt geladen. De benodigde tijd kan worden berekend door de bekende gegevens in formule 15 in te vullen.
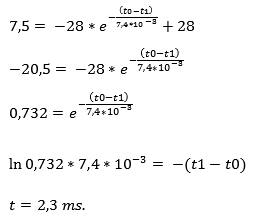
De primaire stroomopbouw wordt bij 7,5 A gestopt. Dit voorkomt het overmatig en onnodig warm worden van de bobine. Het belangrijkste is dat de spoel in een zo kort mogelijke tijd zoveel optimaal wordt opgeladen. De afbeelding weergeeft de laadcurve tot t = 2,3 ms.
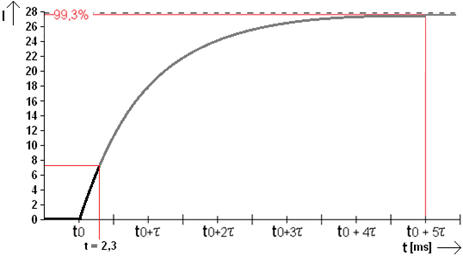
Wanneer de accuspanning daalt, bijvoorbeeld tijdens het starten van de motor, heeft dat invloed op de dwell-tijd. Het duurt dan langer dan 2,3 ms voordat de 7,5 A wordt bereikt. Met de inmiddels bekende formule wordt de nieuwe laadtijd bepaald. De maximale stroom wordt bepaald aan de hand van de accuspanning:
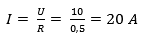
De laadtijd tot 7,5 A met een maximum van 20 A wordt in formule 17 berekend:
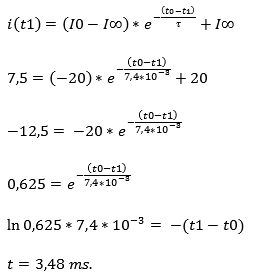
In de afbeelding is de laadtijd bij 14 volt met de zwarte lijn, en de laadtijd bij 10 volt met groen weergeven. De lijnen dalen op hetzelfde moment naar 0; dit is namelijk het ontstekingstijdstip. Omdat er bij een lagere accuspanning meer tijd nodig is om de primaire spoel te laden, moet de MegaSquirt de primaire stroom eerder inschakelen.
De zwarte lijnen (stijgend en dalend) geven de dwell-tijd aan bij een accuspanning van 14 volt. De groene lijn geeft de vervroegde laadtijd aan bij een lagere spanning: dit geeft Δt. De werkelijke laadtijd is in dat geval dus Δt + 100%.
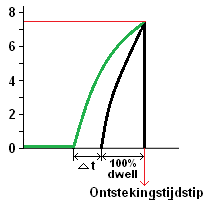
Later in deze paragraaf wordt dit met een voorbeeld en figuur 36 verduidelijkt. De laadtijd wordt verlengd en het ontstekingstijdstip blijft hetzelfde. Zou dat niet of onvoldoende gebeuren, dan heeft dat gevolgen voor de energie die bij de ontsteking vrijkomt. De primaire stroom wordt in dat geval te vroeg uitgeschakeld, waardoor de stroomsterkte van 7,5 A niet behaald wordt. De verlenging van de laadtijd van de primaire spoel (dwell-tijd) is in formulevorm een functie van de accuspanning. Het berekenen van de dwell-tijd bij verschillende spanningen geeft een andere maximale stroomsterkte in de spoel.
Door aan te nemen dat de accuspanning tijdens het starten kan zakken tot 6 volt en tijdens het laden kan stijgen tot 14,7 volt, kan door het berekenen van een aantal tussenliggende waarden een curve worden geschetst. De onderstaande afbeelding laat de dwell-tijd-correctie zien voor de toegepaste DIS-bobine. Bij elke toename van 2 volt is een (rode) punt in de grafiek geplaatst. Omdat een eerder ingevoerde dwell-tijd van 2,3 ms bij een spanning van 14 volt in het programma TunerStudio is ingevoerd, wordt vanaf deze spanning een correctiefactor gevormd. Een spanning van 14 volt is dus 100% (geen correctie).
Nu is inzichtelijk gemaakt dat de laadtijd tot maar liefst 315% toeneemt bij een accuspanning van 6 volt.
De accuspanning kan in ongunstige omstandigheden tot wel 6 volt zakken. Dit betekent een verzwakking in de ontstekingsvonk. Het verlengen van de dwell-tijd (de tijd dat de primaire stroom vloeit) compenseert dit, zodat ook bij deze lage spanning voldoende ontstekingsenergie wordt verkregen. Dat betekent dat Δt uit figuur 36 verdrievoudigd wordt (2,3 ms * 315% = 7,26 ms) ten opzichte van de met zwart aangegeven dwell-tijd van 100% (2,3 ms).
De met rood aangegeven coëfficiënten in de bovenstaande afbeelding kunnen rechtstreeks worden overgenomen in het programma TunerStudio.
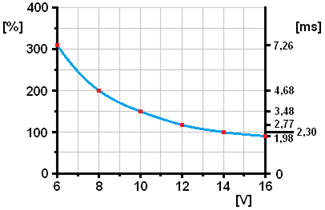
Enige tijd nadat de primaire spoel ontladen is, begint de opbouw voor de volgende ontsteking. Hoe hoger het motortoerental is, des te sneller de spoel weer wordt opgeladen. In figuur 37 zijn twee curves getoond waarbij de primaire stroom oploopt tot 8,85 A. Het ontstekingstijdstip bevindt zich op het punt waarbij de lijn naar 0 A daalt.
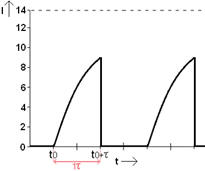
Bepalen van het ontstekingstijdstip:
Het ontstekingssignaal wordt bepaald aan de hand van het krukasreferentiepunt.
In de tandkrans van de krukaspoelie is van de 36 tanden 1 tand uitgefreesd op 100 graden voor het bovenste dode punt van de zuiger van cilinder 1. Tussen de 100 en 0 graden, dus tijdens de compressieslag, kan de microprocessor van de MegaSquirt het ontstekingstijdstip bepalen. Hierin wordt rekening gehouden met de vervroeging.
De afbeelding toont het tweekanaals oscilloscoopbeeld waarin het bovenste beeld het krukasreferentiepunt en het onderste beeld het aanstuursignaal van de MegaSquirt naar de DIS-bobine tonen. Het aanstuursignaal heeft een spanning van 5 volt (een logische 1) en duurt ongeveer 1,5 ms.
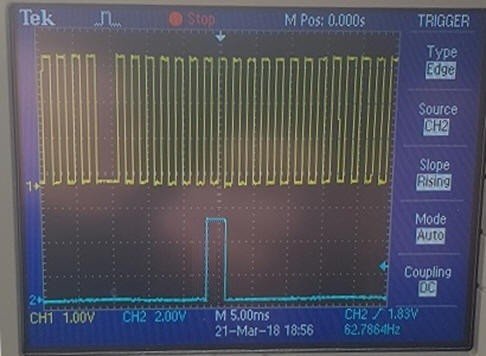
Ontstekingsvervroeging:
Er wordt in dit project geen gebruik gemaakt van pingelsensoren. Er bestaat wel een mogelijkheid om informatie van pingelsensoren te verwerken, maar volstaat enkel het monteren van een pingelsensor niet. De verwerking van de signalen is complex. Het pingelsignaal moet eerst worden omgezet in een ja/nee signaal of in een analoog signaal dat de sterkte van detonatie weergeeft.
De omzetting van motortrillingen naar een pingelsignaal geschiedt door een interfaceschakeling. Deze schakeling is niet in de MegaSquirt II aanwezig. Daarom is gekozen voor het veilig instellen van de vollast- en deellastvervroeging, zodat de motor niet in het pingelgebied terecht kan komen. De in te stellen vollastvervroegingscurve dient binnen de pingelgrenzen te worden vastgesteld. De centrifugaal- en vacuümvervroegingsgegevens van de conventionele ontsteking wordt aan de hand van de fabrieksgegevens uit de manual van de motor bepaald. De punten kunnen worden uitgezet in een grafiek (voorbeeld in de onderstaande afbeelding).
De roze lijn geeft de originele, mechanische vervroeging aan. Deze verloopt gedeeltelijk lineair vanwege de mechanische constructie van de centrifugaalgewichten. De zwarte lijn weergeeft de kenveldregeling in de MegaSquirt; deze lijn verloopt volgens een kromme. Belangrijk is om uit de deellast- en vollast-pingelgebieden te blijven; daarom wordt de kenveldregeling in deellast beperkt (rode lijn) en neemt de vervroeging in vollast niet verder toe dan in de situatie met mechanische vervroeging (rode lijn). De werkelijke kenveldregeling verloopt volgens de blauwe lijn.
Als eerste diende de vollast vervroegingskromme in de spark advance tabel te worden ingevuld. Bij een hoger toerental en bij een lagere belasting zal er meer vervroeging nodig zijn. Bij deellast wordt de vervroeging bij de vollast vervroeging opgeteld. Op pagina 7 worden de ingevulde ontstekingsvervroegingstabel en de vervroegingsinstellingen bij koude motor getoond.
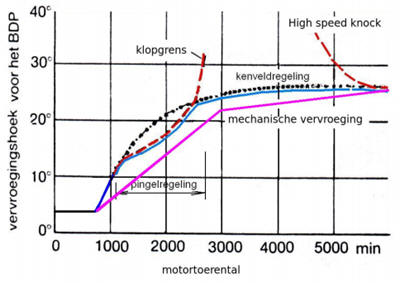
Gasklephuis:
De lucht-/ brandstoftoevoer werd in originele toestand door de carburateur geregeld. Voor het motormanagementsysteem wordt de carburateur vervangen door een gasklephuis en vier injectoren die in het inlaatspruitstuk bevestigd worden. Hiermee wordt een meer nauwkeurige en gecontroleerde inspuiting verkregen dan bij de carburateur, waar zich centraal in het spruitstuk een lucht- / brandstofmengsel wordt gevormd en zich verdeeld in vier kanalen. De gasklep wordt geopend door een bowdenkabel die vanaf het instrumentenpaneel handmatig bediend wordt.
De MegaSquirt II ondersteunt immers geen elektronisch bediend gasklephuis. Daarom is de bowdenkabel-bediening de enige mogelijkheid om toe te passen.
De gaskleppositie wordt door middel van een spanning doorgegeven aan de MegaSquirt . De grootte van de spanning is afhankelijk van de openingshoek van de gasklep. De gaskleppositiesensor is een potmeter met een voedingsspanning van 5 volt (zie afbeelding). Aansluiting 3 en een massa-aansluiting 1 zijn noodzakelijk. De loper (pin 2) neemt een plaats op de weerstand aan die afhankelijk is van de gasklepstand. De loper is dus met de gasklep verbonden. Wanneer de loper een kleine afstand over de weerstand moet overbruggen (de loper wijst naar links) dan is de weerstand laag. In de afbeelding staat de loper naar rechts (de massazijde) wat betekent dat er een hoge weerstand is en er dus sprake is van een lage signaalspanning.
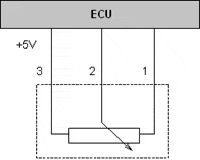
Bij het toegepaste gasklephuis staat er een spanning van 600mV op de loper wanneer de gasklep gesloten is en een spanning van 3,9V wanneer de klep volledig geopend is. De ECU ontvangt de spanning en berekent hiermee de openingshoek van de gasklep. Een snelle toename in de openingshoek betekent dat er geaccelereerd wordt; de ECU speelt hierop in door kortstondig te verrijken. Dit wordt de acceleratieverrijking genoemd. De gaskleppositiesensor wordt niet gebruikt om de verrijking van het mengsel te bepalen bij verschillende bedrijfsomstandigheden; hiervoor wordt gebruik gemaakt van de MAP-sensor.
Testopstelling van de stappenmotor met simulator:
Nadat de MegaSquirt hardwarematig was aangepast, kon met de breakout-box worden gecontroleerd of de aansturing van de stappenmotor wordt ontvangen. Het oplichten van twee-kleuren LED’s toont aan dat een aansturing plaatsvindt. De stappen waarin de stappenmotor aangestuurd wordt is te volgen door te kijken naar de verandering van de kleuren. De kleuren wisselen tussen rood en geel. In het menu “Idle control” in het programma TunerStudio kunnen de stappenmotorgegevens worden ingevoerd. Behalve het type (4 wire) kan ook het aantal stappen worden ingesteld. Hieronder valt ook de beginpositie waarin de stappenmotor moet staan als de motor gestart wordt. Verder kan de tijd ingesteld worden hoelang het verstellen van één stap duurt.
Het aantal stappen is onder anderen afhankelijk van de koelvloeistoftemperatuur; een lagere temperatuur vereist een grotere opening van de stappenmotor. In een grafiek kunnen de stappen ten opzichte van de temperatuur worden ingesteld. Met de simulator kan worden gecontroleerd of de stappenmotor daadwerkelijk goed wordt aangestuurd. Doordat het eerst op de simulator wordt gecontroleerd in plaats van op de motor, kan worden voorkomen dat er problemen tijdens het starten of het draaien van de motor ontstaan door een mogelijk hard- of softwarematig probleem. Omdat voornamelijk de koelvloeistoftemperatuur en het motortoerental invloed hebben op de openingshoek van de stappenmotor, kan door het verdraaien van deze potentiometers worden bekeken of de aansturing correct is. De meter op het dashboard in TunerStudio zal de verstelling weergeven in het aantal verstelde stappen.
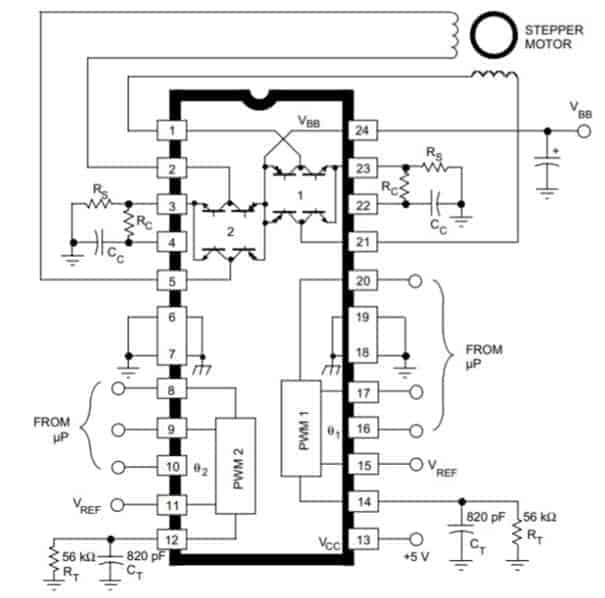
Instellingen voor de stappenmotor:
De afbeelding weergeeft het instellingenscherm voor de stappenmotor die gebruikt wordt voor het stationaire toerental (idle control).
De stappen waarin de motor versteld wordt zijn van te voren met behulp van een Arduino vastgesteld. Ook dienen de aantal stappen ingevoerd te worden om naar zijn basispositie te bewegen (homing steps). De stappenmotor is actief in de warmdraai-fase (algorithm) en bekrachtigd de spoelen in stilstand (hold current between steps).
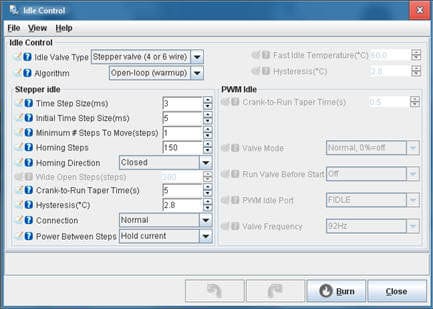
De stand van de stappenmotor hangt af van de koelvloeistoftemperatuur. Tijdens het starten van een koude motor dient de klep iets meer open te staan dan bij een opgewarmde motor. De onderstaande afbeelding toont het instellingenscherm om de stappen in te stellen (Steps) in relatie met de koelvloeistoftemperatuur (Coolant). Wanneer de motor koud is, staat de stappenmotor tijdens het stationair draaien van de motor volledig geopend. Tijdens de opwarmfase sluit de stappenmotor een beetje.
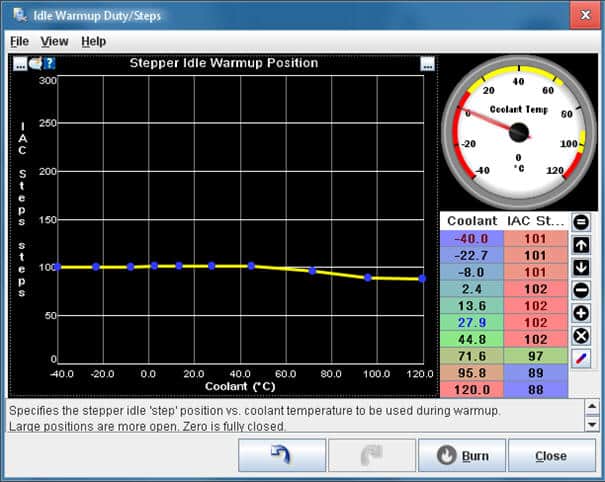
Het is ook mogelijk om tijdens het starten van de motor de positie van de stappenmotor aan de hand van de koelvloeistoftemperatuur in te stellen. Dit wordt de “Idle Cranking Duty/Steps” genoemd. In de onderstaande afbeelding is het instellingenscherm te zien.
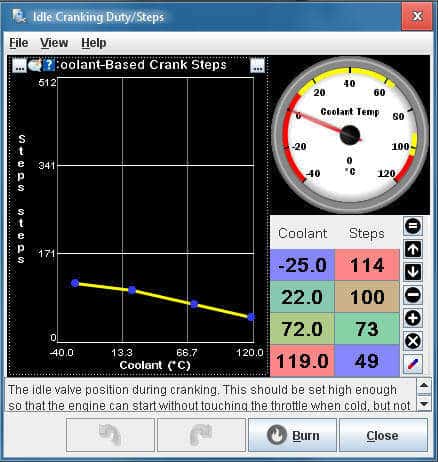
Brandstofpompcircuit:
De MegaSquirt zorgt voor het in- en uitschakelen van de brandstofpomp. Transistor Q19 in de onderstaande afbeelding beveiligd de transistor Q2 tegen te hoge stroomsterktes. Bij een te hoge stroom kan de transistor doorbranden. Wanneer de stroom door het collector-emittergedeelte van Q2 en R40 toeneemt, wordt de verzadigingsspanning aan de basis van Q19 bereikt. Transistor Q19 gaat in geleiding, waardoor de basis-emitterspanning bij Q2 lager wordt.
Aansluiting FP-1 PTA0 wordt intern door de MegaSquirt aangestuurd. Een ingangs-signaal van de krukaspositiesensor (een Hall-sensor of inductieve sensor) is nodig om de transistorschakeling aan te sturen. Bij het wegvallen van het signaal, bijvoorbeeld bij het onbedoeld afslaan van de motor, wordt de voeding van de brandstofpomp direct beëindigd.
De uitgang van de transistorschakeling (FP1 OUT) wordt aangesloten het brandstofpomprelais. Pin 85 van het relais is de uitgang van de stuurstroom. Bij een bekrachtigd relais wordt het hoofdstroomgedeelte (pin 30 en 87) geschakeld, zodat de brandstofpomp een voedingsspanning krijgt om te werken.
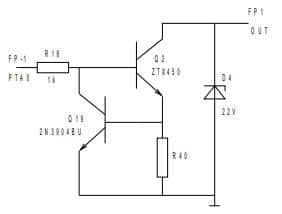
Er wordt gebruik gemaakt van een elektronische brandstofpomp met een werkdruk van 3 bar. De brandstof wordt door het brandstoffilter naar de brandstofrail geleidt, waar de druk op de ingang van de injectoren staat. De injector zal een vooraf berekende hoeveelheid brandstof in het inlaatspruitstuk injecteren op het moment dat er een signaal van de MegaSquirt komt. Niet alleen de aansturing van de MegaSquirt bepaalt de hoeveelheid ingespoten brandstof, maar ook de brandstofdruk in de rail.
Bij een hogere raildruk zal bij dezelfde aansturing een grotere hoeveelheid brandstof worden ingespoten. De raildruk moet dus worden afgeregeld aan de hand van de onderdruk in het inlaatspruitstuk. Het drukverschil (∆P) dient ten alle tijden 3 bar te blijven. In de afbeelding is het schema weergeven van het brandstofsysteem. De roze, gele, oranje en zwarte lijnen geven de elektrische verbindingen weer. De rode lijn geeft de brandstoftoevoer aan en de blauwe lijn de brandstofretour.
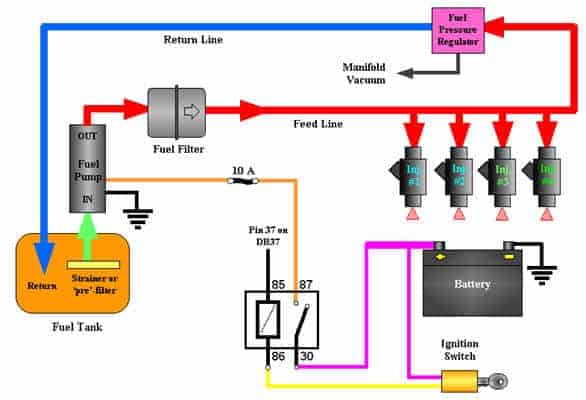
Afronden van de mechanische werkzaamheden:
De volgende drie foto’s tonen de motor in de eindfase van de mechanische aanpassingen.
Foto 1:
Dit is de zijde waar de meeste aangebrachte onderdelen zichtbaar zijn. Ook bevinden zich hier het dashboard voor de bediening en de MegaSquirt ECU. Onder de foto staat een legenda met de beschrijving van de nummers bij de onderdelen. U kunt de foto’s in een groter formaat openen door erop te klikken.
- Gasklep;
- Brandstofleiding voor de injectoren;
- Verbindingsbuis voor gasklep op inlaatspruitstuk;
- Brandstofdrukmeter;
- In- en uitlaatspruitstuk;
- Dashboard met schakelaar koelventilator, lampjes voor dynamo en oliedruk, contactschakelaar en massaschakelaar;
- Onderdrukslang voor MAP-sensor;
- Lambdasonde;
- Brandstofslangen (toevoer en retour) bij elkaar in een krimpkaus;
- Brandstofpomp- / tankunit;
- Brandstofpomprelais;
- MegaSquirt;
- Uitlaat einddemper.
Foto 2:
Op deze foto wordt de andere kant van de motor getoond. Hier zijn de carburateur (15) en de conventionele ontsteking (17) te zien. Deze klassieke ontsteking heeft als doel de bougies in de testopstelling (14) te laten vonken. Dit heeft voor de motor natuurlijk geen functie, maar het geeft wel inzicht in de werking van de ontsteking zoals deze in klassieke auto’s werkte.
Nummer 20 geeft het mechanisme van de transmissierem aan. Middels een bowdenkabel kan de stang van de remtrommel worden aangetrokken, zodat de uitgaande as van de versnellingsbak wordt afgeremd. De transmissierem wordt toegepast om de motor kortstondig te belasten wanneer er een versnelling is ingeschakeld.
Foto 3:
Het bovenaanzicht van de motor met de proefopstelling voor de ontsteking en de brandstofrail zijn hier duidelijk zichtbaar.
De mechanische aanpassingen zijn voltooid. De motor kan nog niet worden gestart, omdat eerst enkele gegevens in de MegaSquirt moeten worden ingevoerd.
Volgende: MegaSquirt II ECU aanpassen.