Subjects:
- Determining and Installing Engine Management System Sensors
- Crankshaft Position Sens.
- pulse wheel
- Map sensor
- Coolant temperature sensor
- Oxygen sensor
Determining and installing sensors for the engine management system:
The engine management system requires a number of sensors. Sensors serve as the “input” of the system. Sensors convert a physical quantity into an electrical signal, which can be processed by a computer, in this case the MegaSquirt.
In the assembly process of the MegaSquirt, the components to be mounted on the motor must be taken into account, because the construction of the MegaSquirt can differ.
The figure shows the different sensor circuits that these components are in. The input signals shown in the figure come from the lambda sensor, the throttle position sensor, the coolant temperature sensor and the air temperature sensor.
In addition to the sensors, the schematic also contains a number of resistors and capacitors. The composition of these components forms filters; these filters serve to absorb interference signals and noise. When the sensor signal is distorted by noise, this can have major consequences for the control of the actuators, and therefore also for the functioning of the motor.
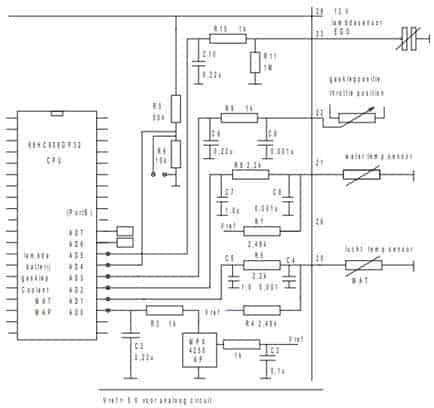
Crankshaft Position Sensor:
An important input for the engine management system is the crankshaft speed.
The crankshaft speed is measured using a crankshaft position sensor and a pulse wheel. The crankshaft position sensor has two important functions:
- The crankshaft speed can be determined on the basis of the frequency of the signal;
- The missing tooth in the pulse wheel indicates the crankshaft position in which the pistons of cylinders 1 and 4 are a few degrees before TDC.
The engine speed influences the control of the injectors and the ignition. The missing tooth in the 36-1 pulse wheel is important to determine the ignition and injection times. It has been decided to use a Hall sensor and not the induction encoder as the speed sensor. An inductive sensor generates an alternating voltage that must be converted into a direct voltage in the MegaSquirt controller. A Hall sensor generates a square-wave voltage, which is amplified to a voltage of 5 or 12 volts with an internal or external pull-up resistor. This makes the Hall sensor more suitable for forming a reliable signal. Before assembling the MegaSquirt, that choice must be made in advance; both sensors require a different circuit layout.
Pulse wheel:
The crankshaft position sensor measures a change in the air gap of a pulse wheel mounted on the engine. On the Land Rover engine, however, there is no crankshaft position sensor and therefore no pulse wheel. The pulse wheel therefore had to be retrofitted. Much thought has gone into the location and position of the pulse wheel. Possibilities were:
- A 36-tooth disc that is attached to the outside of the crankshaft pulley by a clamp or bolt connection.
- Adjusting the current crankshaft pulley by milling teeth out of the pulley.
It is common to use a 36-1 or a 60-2 pulse wheel. The pulse wheel with 60 teeth is mainly used for larger diameters. The 36-1 is suitable for use because of the tooth width. It is very important that the pulse wheel has as little height stroke as possible. An altitude stroke means a change in the magnetic field between the sensor and the teeth of the pulse wheel. This can adversely affect the running of the engine. This should of course be prevented. It was therefore preferable to adapt the current crankshaft pulley. The outer edge of the existing crankshaft pulley is machined on a milling machine. Notches have been created by removing material. The remaining 36 teeth are used to allow the sensor to measure the changes in the magnetic fields. A tooth has been ground away in front of the reference point. The image below shows the machined crankshaft pulley.
At the top of the pulse wheel, right below the sensor, the ground tooth is visible. When the crankshaft is in this position it does not mean that the pistons of cylinders 1 and 4 are at TDC, but that these pistons are 90 degrees before TDC, which corresponds to 9 teeth (360/36). As soon as the missing tooth passes, the MegaSquirt receives the signal that the ignition must take place soon. From that point on, it is calculated when the ignition coil should be controlled. In the event of varying operating conditions, the pre-ignition time is also determined on the basis of this reference point.
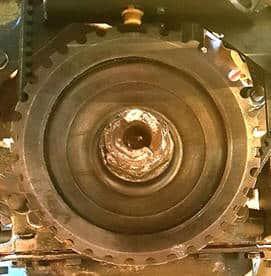
The image of the oscilloscope (see illustration) shows the crankshaft signal (top) in relation to the ignition coil drive signal (bottom). At the eighth tooth after the missing one, the drive pulse to the ignition coil is formed. When the engine is idling, the ignition is advanced 10 degrees, because it comes down to 1 tooth. That corresponds to the 90 degrees (9 teeth) between the removed tooth and the actual top dead center.
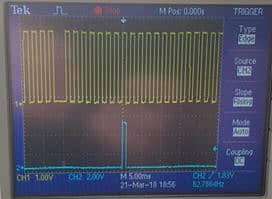
To assemble the Hall sensor circuit in the MegaSquirt, it is necessary to install capacitor C11, resistors R12 and R13, diode D2 and opto-coupler U3 (see figure below). The signal from the Hall sensor enters the diagram in figure 105 at “Opto in”. The signal arrives at the so-called opto-coupler via the diode and resistor. This component is indicated by a broken broken line. The opto-coupler is a small integrated circuit in which the LED on the left side makes the phototransistor on the right side conductive when lit. The opto-coupler can be seen as a switch with no mechanical or electrical connections between the control and switching part.
When the transistor in the opto-coupler is conductive, a small current can flow from Vcc to ground. At that moment there is a voltage of 0 volts on “Opto Out”. If the transistor is not conductive, there is no current and therefore no voltage drop across resistor R13. The voltage on “Opto out” is then 5 volts.
By using an opto-coupler, a galvanic separation is made between the diode and the phototransistor. Dangerous interference voltages are thus kept outside the microcontroller circuit, as the breakdown voltage is usually greater than 5 kV.
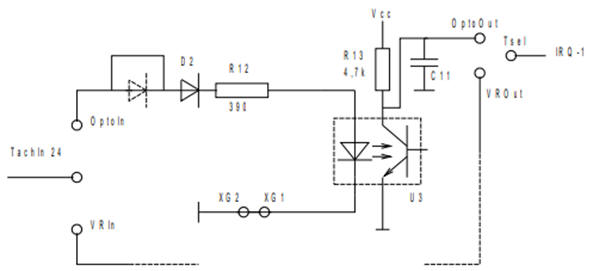
MAP sensor:
A Manifold Absolute Pressure sensor (MAP) measures the pressure in the intake manifold. The MegaSquirt uses this pressure, the engine speed and the inlet temperature to calculate the amount of air entering the engine. With the Land Rover engine, an absolute pressure (the outside air pressure) or negative pressure will be measured. It is a naturally aspirated engine that sucks in its air itself. Engines equipped with a turbo have to do with overpressure in the intake manifold. The measuring range of a MAP sensor is usually between 0,2 and 1.1 bar.
The pressure in the intake manifold, along with the throttle opening angle (which is measured by the throttle position sensor) and engine speed, can determine engine load. Due to the lack of a MAF (Manifold Air Flow) sensor, the amount of air drawn in is calculated on the basis of the engine data and the negative pressure prevailing in the intake manifold. It was decided not to use a MAF sensor, because the signal is less reliable because it is not designed for the engine. Matching the settings to the intake manifold characteristics is complex. This requires many correction factors.
The applied MPX4250AP MAP sensor is shown in the figure. The MegaSquirt printed circuit board is standard equipped with connection options for this type of MAP sensor. This sensor is also included as standard in the kit. The amount of fuel injected depends, among other things, on the amount of air present, because an attempt is made to achieve a stoichiometric mixing ratio (14,68 kg of air to 1 kg of fuel). There was an option to not use both the MAF and MAP sensors. The amount of air drawn in would then be determined according to a so-called Alpha-N regulation. This involves looking at the position of the gas valve, which determines the amount of air present. However, this is less accurate than a MAP sensor, so this has not been chosen. In this project the throttle position sensor is only used for the acceleration enrichment.
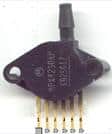
Coolant temperature sensor:
There are no temperature sensors on the engine in the classic arrangement. The engine is standard equipped with a bimetal, which has the function to illuminate the dashboard light when the coolant temperature is too high. Because the engine management system does take the temperature of the coolant and the intake air into account, it was decided to install NTC resistors afterwards. An NTC resistor has a negative temperature coefficient. That is, the resistance value decreases as the temperature increases. As the coolant temperature sensor, a sensor has been chosen that has a resistance value of 2,5 kilo-ohms at 25⁰ Celsius. Here, the resistance change is greatest in the most important temperature range. The properties of the NTC resistance must be mapped out to calculate a correct temperature.
The resistance change is greatest with a change in the temperature range between 0⁰C and 60⁰C. This can be seen from the course of the characteristic; in the mentioned temperature range there is a decrease in resistance of about 5kΩ, while at T 60⁰C the resistance hardly decreases. In some cases it is desirable to also measure temperatures above 60°C. To make this possible, at a certain temperature the internal bias resistor can be switched to a bias resistor of a different value. This produces two NTC characteristics. However, in this project the coolant temperature is only used for the cold start enrichment, which is hardly used above 60°C.
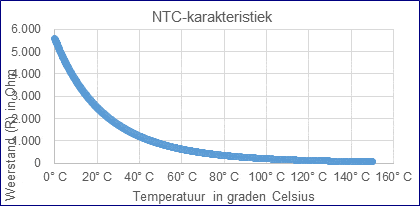
The low temperatures are also the most interesting; cold start enrichment will take place here; the injector is actuated longer when the engine is cold. When the engine has warmed up sufficiently (T 60⁰C), there is less and less enrichment. From a T = 90⁰C, the injection strategy follows the values set in the reference field. The reference field is a standard entered value. External factors, such as a cold start enrichment at a low temperature, form a correction factor on this standard value. The MegaSquirt no longer takes the coolant temperature into account.
Lambda probe:
A lambda probe (sensor) is mounted in the exhaust that measures the air/fuel ratio in the exhaust gases. The lambda sensor has an important task to “tune” the engine management at a later stage by filling in the AFR and VE tables. In order to understand the ideal mixing ratio and the usefulness and necessity of enrichment or depletion, the stoichiometric mixing ratio, enrichment and depletion are first defined.
The stoichiometric mixing ratio indicates the ratio of air to fuel using all the oxygen from the air. This is the case with the ratio 14,68:1 (rounded off as 14,7 kg of air to 1 kg of petrol). We then speak of λ = 1.
The lambda value can vary under different operating conditions:
- Enrich: λ < 1;
- Impoverish: λ > 1.

Enriching to λ = 0,8 means that a mixing ratio of 11,76 kg of air to 1 kg of gasoline applies. So there is less air available to burn 1 kg of fuel. The enrichment or depletion of the mixture must always remain within the explosive limits. Enrichment occurs when the engine has to deliver more power. A richer mixture also provides cooling. A lean mixture, on the other hand, gives better fuel consumption. The image below shows two graphs showing maximum power and lowest fuel consumption.
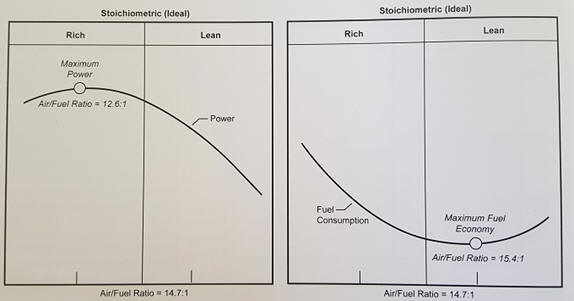
The lambda value affects not only power and fuel consumption, but also exhaust emissions. A richer mixture ensures a lower NOx content, but also higher CO and HC emissions. With a leaner mixture, the fuel particles are further apart, so that the combustion is no longer optimal; As a result, HC emissions also rise. The figure below shows the emissions related to the lambda value. When using a catalytic converter, it is desirable to have the injection run continuously, alternately rich and lean. With a rich mixture, CO is formed as a result of an oxygen deficiency, with which the catalyst reduces the NOx. A lean mixture contains a surplus of oxygen, with which CO and HC are oxidized.
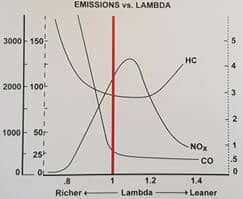
There are two types of lambda sensors; the jump sensor and the broadband sensor. The MegaSquirt supports both types. However, when setting the VE table, a jump sensor is unsuitable and the choice was therefore made to use the broadband sensor. The VE table is set by adapting the VE values to the measured AFR. Although the VE values can in principle be filled in by means of calculations and largely on the basis of the torque profile, the AFR is soon beyond the range of the jump sensor. A broadband sensor offers a solution due to its large measuring range; it can measure an AFR between 8,0 and 1,4. The mixture composition will in almost all cases be in this measuring range with the engine running, so the broadband sensor is suitable for setting the VE table. Tuning without the broadband sensor is practically impossible.
The MegaSquirt does not have an internal lambda controller. When the properties of the broadband sensor are known, they can be entered in a table in the TunerStudio program. In other cases, a broadband sensor with external controller is required. The output voltage is linearized by the external controller. The output voltage from the controller to the MegaSquirt is between 0 and 5 volts, with the ratio between the lambda value and the voltage having a linear progression. The voltage value is converted into a lambda value in the MegaSquirt. The image shows the graph with the linear gradient.
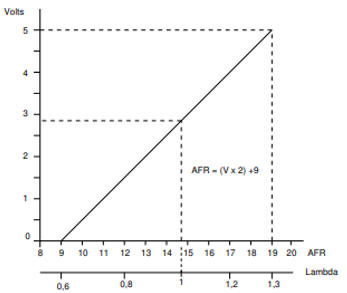
Next: Actuators.