Subjects:
- Determining and installing actuators for the engine management system
- Fuel Injectors
- Choosing suitable injectors
- Installing the injectors in the intake manifold
- Ignition
- Preparing with the conventional ignition
- Ignition coil for the engine management system
- Current build-up in the primary coil
- ignition advance
- Throttle body
- Test setup of the stepper motor with simulator
- Stepper Motor Settings
- Fuel Pump Circuit
- Completion of the mechanical work
Determining and installing actuators for the engine management system:
The actuators that will be controlled by the MegaSquirt are the injectors, ignition coil, fuel pump and the stepper motor for the idle speed. This chapter describes the process in which the actuators are tested and mounted on the engine block, and which choice has been made.
Fuel Injectors:
The MegaSquirt controls the injectors. The injectors are grounded. With a ground-switched component, a supply voltage is present, but current only flows when the ground is switched on. In this case the injector will only inject when the MegaSquirt ECU switches the mass. Once the actuation is terminated, the injector will stop injecting. The amount of fuel to be injected is determined on the basis of the VE table and AFR table.
A MOS-FET switches the injector on and off causing the fuel to be injected. The amount of fuel determined by the MegaSquirt depends on several factors:
- The ideal gas law relating the amount of air to its pressure, volume and temperature;
- Measured values by the sensors in the engine block: intake manifold pressure (MAP sensor), coolant and intake air temperature, crankshaft speed and the data from the throttle position sensor;
• Adjustment parameters: required amount of fuel, degree of filling (VE), opening time of the injector and enrichment under certain conditions.
The injection time should be as long as possible while the engine is idling in order to obtain a good fuel dosage. Therefore, not just any random injector can be applied to the engine. The properties of different types of injectors must be compared and calculations must provide insight into the required amount of fuel for the engine in question. There was also a choice between high and low impedance injectors. Low impedance injectors are suitable for engines where a very fast opening of the injector needle is required. The typical resistance is 4 Ohms. The disadvantage of these injectors is the high current. The heat development that arises in the MegaSquirt as a result is undesirable. It is possible to use low-impedance injectors by mounting special IGBTs on a heat-conducting plate on the MegaSquirt housing. It was decided to use high-impedance injectors. There is less heat development and these IGBTs are not used.
The passage size (flow) is of great importance to determine the correct injection quantity, and thus the control. If the injectors are too large, the injection time at idle speed will be so short that the engine may start to run irregularly. The injection quantity must be sufficient to inject all the fuel in the time available. The injection amount is indicated as injection time in milliseconds. A high load at a high engine speed is assumed. This is at a MAP of 100 kPa. The required injector flow can be calculated on the basis of the engine properties. The injector flow indicates how many milliliters of fuel are injected per minute.
Choosing the appropriate injectors:
Injectors of three different types have been made available for the project. Research showed which type of injector was most suitable for use in this project.
Each type of injector has a different flow; the yield after a one minute injection differs per type. Before testing, the injectors were cleaned in an ultrasonic bath. With this cleaning method, the injector is cleaned inside and out by means of ultrasonic vibrations and a special test liquid, so that any old dirt residues cannot influence the flow measurement or the injection pattern. During the ultrasonic cleaning, the injectors were continuously opened and closed and the injection pattern of each injector was examined; this was a nice mist. When closing, no abnormalities could be seen, such as drop formation or a deviating radius. After the ultrasonic cleaning and testing, the O-rings were replaced, so that a good seal can be guaranteed when mounted in the intake manifold.
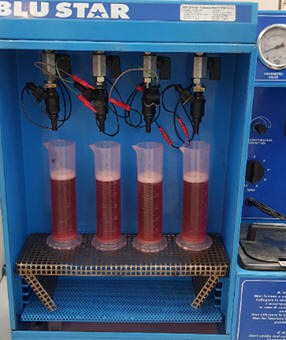
By means of a test set-up (see image above), the injectors can inject into several measuring cups, so that the amount of fuel injected can be read after a certain time. By controlling the injectors under a working pressure of 3 bar, the amount of injected fuel can be checked. The fuel pressure on the supply line (the rail) must be 3 bar and the injector needle must be actuated for 30 or 60 seconds with a duty cycle of 100%. After the injectors had been activated for 30 seconds, the following data could be entered:
Type 1: 120ml
Type 2: 200ml
Type 3: 250ml
Only one type of injector will be used. The injector size is determined using the formula below:

The injector size is determined by the effective power (Pe) delivered at a certain speed, the Break Specific Fuel Consumption (BSFC), the number of injectors (n injectors) and the maximum duty cycle with which the injectors are controlled. The whole is multiplied by 10.5 to convert from pound per hour (lb/hr) to ml/min.
The answer to the calculation indicates which injector is suitable for this engine configuration. It is not a problem if there is less than 20 ml deviation from the calculated value. This difference is compensated for by adjusting the software in the MegaSquirt. The following table summarizes the data used in the formulas:
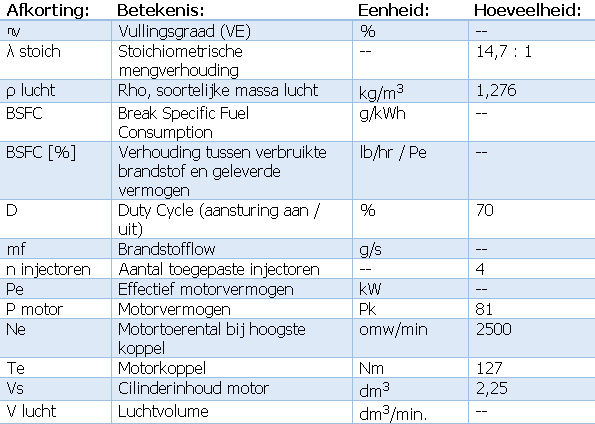
The first step is to determine the fuel injected at the torque speed. A certain amount of air is drawn in for every two revolutions of the crankshaft. The degree of filling is highest at the torque speed. Due to the engine characteristics (including the valve overlap), the engine fills best at this speed and the efficiency is highest. It is estimated that the filling level will be around 70%. Formula 4 calculates the volume of air that is present in the engine at that moment.
In formula 5, the amount of fuel injected is calculated on the basis of the air volume present. The engine power achieved at the torque speed is calculated in Formula 6. The ratio between the amount of fuel injected and the power indicates the BSFC in formulas 7 and 8.
The actual BSFC is multiplied by 6 in Formula 3600 to convert to kWh. The BSFC of a petrol engine is often between 250 and 345 g/kWh. The lower the value, the more efficient the motor is. Formula 8 specifies the ratio between fuel flow in pounds/hour and effective engine power. This percentage is adopted in formula 9.



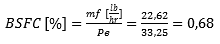

With the answer to formula 9, it has become clear that the injectors with a flow of 200 ml/min are suitable for use on the engine. The difference of 7 ml is negligible as it is compensated for in the software when filling in the VE table.
Installing the injectors in the intake manifold:
The electronically controlled injection system allows the carburettor, which is part of the classic setup, to be removed. The carburettor is thus replaced by a throttle body (for the air supply) and four separate fuel injectors. The intake manifold was retained and modified to allow conversion to the engine management system. The fuel injection takes place in the intake manifold. It was decided to mount the injectors as close as possible to the inlet valve. In most cases, car engine manufacturers choose to mount the intake valve at an angle in the intake manifold. The fuel is injected against the inlet valve. In the current project, however, an arrangement was chosen in which the injectors are placed at an angle of 45 degrees with respect to the air ducts in the manifold.
The intake manifold is made of die-cast aluminum. The choice was made to attach aluminum buses to the manifold. Manually machining to a good size was not an option, because the bushes had to have different dimensions than a standard size of a drill. This meant that the outsourcing of the vans had to be outsourced to a company with suitable equipment. The vans could then be attached to the manifold by means of TIG welding. The choice to mount the injectors upright instead of at an angle was made for the following reason:
- The assembly process: it is easier to set up the canisters in a straight, horizontal arrangement. Welding the vans to the manifold is easier because it is now easier to weld around than in the situation where the van is at an angle.
- The post-processing: During the welding the bushes become a bit oval. The deformation is caused by the heat released during the welding process. This has been taken into account by making the inner diameter of the canisters smaller than the outer diameter of the injectors. Finishing (clearing) is less risky: when the canisters are rounded on the inside, the diameter is optimal for the injectors, while the seal is guaranteed by the O-rings. The height of the vans is important; the injector should not be fitted too far into the manifold. The end of the injector should not obstruct the airflow. From the information from source: (Banish, Engine Management, advanced tuning, 2007) it has been decided to mount the injectors so deep in the manifold, that the ends are exactly in the holes of the manifold; the airflow is not obstructed.
- Fuel Injection: Because the mixing of the fuel mist with the air is optimal before the intake valve opens, it does not matter whether the injector injects exactly on the intake valve, or just before that in the intake manifold.
With simultaneous injection, the injection takes place every crankshaft rotation (360°). The four injectors inject simultaneously. This means that fuel is also injected into the intake tract when the intake valve is not open. Some time later, the inlet valve opens and the fuel still enters the cylinder.
The bushes are specially cut to size on a lathe. The inner diameter is slightly smaller than the outer diameter of the injector; because there is deformation during the welding process, there must still be a possibility in the post-processing to remove material by means of reaming. This means that the diameter becomes slightly larger because material is being ground away. The diameter should not be too large, because then there is a risk that the rubber O-ring on the injector can no longer seal well enough. A good seal is very important; air leakage past the injector results in a lower underpressure in the intake manifold.
The measured negative pressure then no longer corresponds to the calculated negative pressure. This affects the injection, which is determined on the basis of the VE table. The underpressure plays a major role in this. The features and settings of the VE table are described in a subsequent chapter.
A bevel has been filed on the underside of the vans, so that the shapes match those of the inlet manifold. This means that the van must stand upright as much as possible. The image below shows the intake manifold with a canister during the assembly process. The canister is attached on one side, so that it can be clearly seen what influence the welding has on the material. It was unclear whether the aluminum of the manifold did not contain too much contamination, which would make welding more difficult. This turned out to be okay. To prevent the bushes from shifting during welding, holes were drilled in the manifold beforehand and the bushes were held in the correct position with a specially tailored jig. In this way, the four buses are welded all around. A final check showed that the connections between the vans and the manifold were airtight.
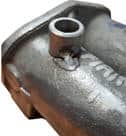
The connection between the injectors is normally formed by a solid injector rail. This tube with connections, usually made of aluminum alloy, has been precisely custom-made by a structural engineer. On the Land Rover engine used for the project, there are two injectors right next to each other, but the space between the pairs of injectors is quite large. The dimensions of the fuel rail and the space between the intake manifold air ducts did not match. The rail therefore had to be adapted.
Shortening some parts and lengthening the other parts is very difficult by means of soldering; the contamination by old fuel, which is very difficult to remove from the inside of the rail, can cause a deteriorated adhesion. Because it concerns fuel, the safest way has been chosen; the parts on which the injectors are attached are connected to each other by means of a high-quality fuel hose. Seamed edges have been fitted at all ends and sturdy hose clamps have been applied to prevent the hoses from sliding over the seams.
The image below shows the intake manifold at the time of processing. The supply line (marked number 1) is connected to the outlet of the fuel pump. Under a pressure of 3 bar, the fuel is fed to the inlet of the four injectors. The pressure regulator (3) regulates the pressure depending on the inlet manifold pressure, because the pressure difference between the fuel pressure and the underpressure in the inlet manifold must remain 3 bar. The fuel flows back to the tank via the return line (2). There is a continuous circulation of fuel. An injection takes place only when the injectors are controlled by the MegaSquirt ECU.
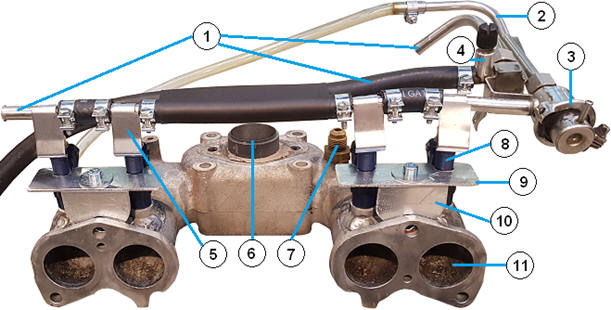
- supply line
- return line
- Pressure regulator
- Pressure Control
- heat shield
- Throttle connection
- Negative pressure connection
- Injector cylinder 1
- Injector bracket A
- Injector bracket B
- Inlet channel cylinder 1
On existing passenger cars, the injector rail is attached to the intake manifold using clamps or eyelets. The injector rail clamps the injectors in the manifold. Because a flexible fuel hose as the injector rail was chosen for this project, the aforementioned is not possible. That is why it was decided to clamp the injectors in the intake manifold with a custom-made bracket. The brackets consist of two parts: the upper part (bracket A) and the lower part (bracket B).
Bracket A contains two notches that can be slid over the injectors. This allows the injectors to be pressed into the manifold by means of the flat sides. There are slotted holes in both brackets A, so that the distance in which the injectors are located in the slotted holes can be adjusted. Brackets A and B are screwed together: bracket B is attached to the same stud as the manifold is mounted to the engine. A slotted hole makes it possible to adjust the bracket in vertical direction. The more the bracket is moved downwards, the more firmly the injector clamps.
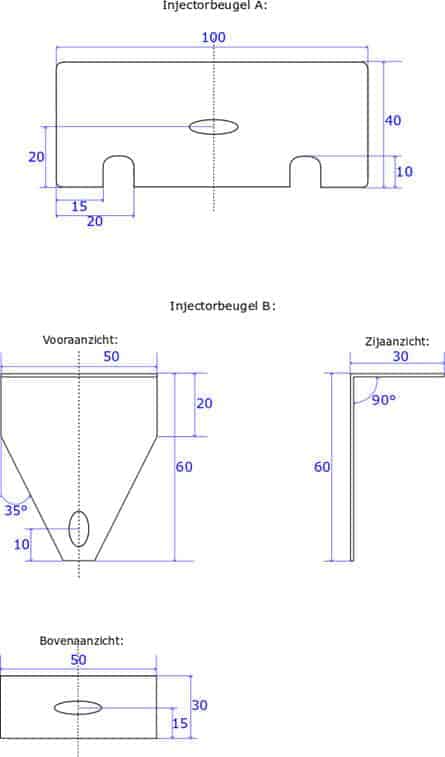
Ignition:
The conventional ignition has been replaced by an electronically controlled ignition system with ignition coil controlled by the MegaSquirt. In order for the motor to function fully on the original techniques, the conventional system with contact points must first be connected. Only after a number of operating hours can it be established that the engine is functioning properly, after which it is possible to start assembling and adjusting, among other things, the electronically controlled ignition.
Preparing with the conventional ignition:
The Land Rover engine was originally equipped with a contact point ignition system, which is now also referred to as a conventional ignition system. The picture shows this type of ignition system.
With closed contacts, the build-up of the primary current begins. The current is limited to 3 to 4 Ampere by the resistance of the primary winding. When a current flows through the primary coil of the ignition coil, a magnetic field will be built up. Both the primary (3) and the secondary coil (4) are in this magnetic field. When the current through the contacts (10) is interrupted by the breaker cam (9) on the distributor shaft, a voltage is generated in both coils. About 250 volts is created in the primary coil. The difference in windings will create an induction voltage of 10 to 15 kV in the secondary coil. The spark plug spark is created when the tips are opened.
The induction voltage can be limited by allowing the primary current to flow through for a while after opening the contact points. This is achieved with a capacitor connected in parallel across the contact points. The capacitor is a time-determining element which, depending on the capacitance, in fact regulates the level of the induction voltage. It also prevents the contact points from burning in.
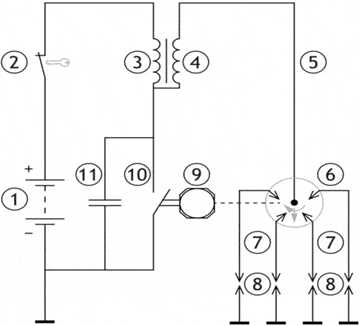
Ignition coil for the engine management system:
The engine management system will control the ignition coil. The classic ignition coil with distributor will remain on the engine to serve as a test set-up, but are no longer part of the functioning of the combustion engine. A Distributorless Ignition System (DIS coil) has been chosen, loosely translated as: “distributorless ignition system”. This type of ignition system does not use a distributor. Another option was to choose a Coil on Plug (COP) ignition coil. A separate ignition coil is connected to each spark plug. A COP coil is also called a pen coil. The disadvantage of a COP coil is that the heat dissipation is less good than that of a DIS coil. Also, when using COP ignition coils, a signal from a camshaft sensor is needed, which is not present on the current engine.
The missing tooth in the crankshaft pulley serves as the reference point for determining ignition timing. With the DIS coil, two spark plugs will be actuated simultaneously at an ignition moment. The DIS ignition coil is in fact a unit in which two ignition coils are mounted. When the pistons of cylinders 1 and 4 move upwards, one will be engaged in the compression stroke and the other in the exhaust stroke. Still, both spark plugs will generate a spark. The spark created by the cylinder that is engaged in the compression stroke will cause an igniting mixture. The other spark, the so-called “wasted spark”, sparks as the exhaust gas leaves the combustion chamber. The wasted spark is a spark that is formed when no mixture is ignited. The ignition energy is low; despite the spark, there is little energy loss. Nor is it harmful.
The figure shows the working diagram of a four-cylinder petrol engine with a DIS ignition coil. This work diagram shows two ignition marks per ignition moment; 1 of them generates the spark to ignite the mixture, the other is the wasted spark. A DIS coil can be controlled by the MegaSquirt with just two pulses.
When the compression stroke takes place in cylinder 1 and the exhaust stroke in cylinder 4, the MegaSquirt controls primary coil A via pin 36 on DB37 (see image below). This control is based on the crankshaft reference point (between 90 and 120 degrees BDC). The MegaSquirt controls the primary coil B, which is responsible for the sparking of cylinders 2 and 3, turns 180 degrees after coil A. There is no reference point for coil B, but the ignition timing can be determined simply by counting the teeth on the 36-1 pulse wheel.
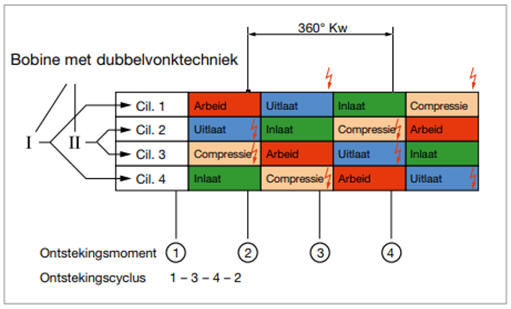
A 7 ohm resistor is shown between coil A of the ignition coil and pin 330 of the processor. This resistance limits the current and induced voltage of the drive pulse. Since this resistor is not standard on the MegaSquirt PCB, it must be retrofitted. The internal circuitry of the MegaSquirt is shown to the left of the vertical dashed line in the figure below. The components shown (the two 330 Ohm resistors and the LEDs) had to be soldered onto the printed circuit board afterwards.
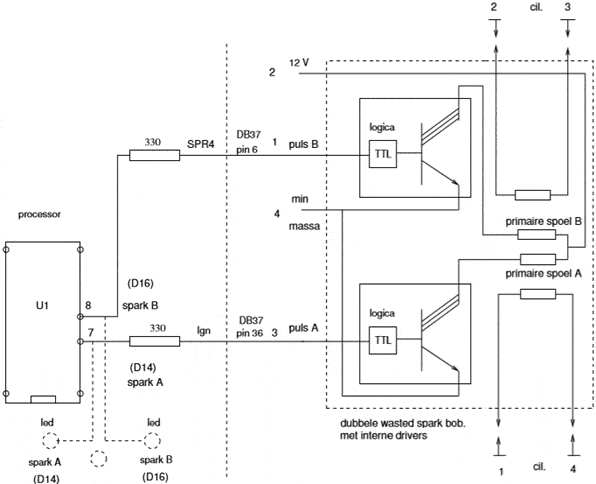
Current build-up in the primary coil:
It is important to gain insight into the current build-up in the primary coil. Not only the current strength, but also the charging time of the ignition coil can be determined with this. The loading time depends on a number of factors, which the MegaSquirt must take into account.
The self-induction coefficient (L-value) of the selected ignition coil is 3,7mH. Together with the ohmic resistance R, the maximum primary current and the rise time of the curve are determined. A small L value and resistance causes the current to rise rapidly after switching on. The known data from the ignition coil can be used to calculate how the primary current is built up.
The following formula shows the general solution of the 1st order differential equation, which calculates the currents, charge and discharge times to show the switching phenomenon by means of a curve.
The equation reads:

where the time constant (Tau) is calculated as follows:

According to Ohm's Law, the maximum current would be 28 Amps:
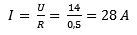
In reality, this amperage will not be achieved.
The coil is turned off earlier. The reason will be explained later. Filling this data into the general formula gives:
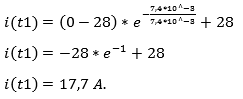
The figure shows the charge curve of the primary coil. From the time T0 to 1 Tau, the coil is charged at 63,2%. This is a fixed percentage for the charge time of a coil. The result of formula 13 shows that the coil is loaded with 1 Ampere at 17,7 Tau. At t = 5 Tau the final value is practically reached.
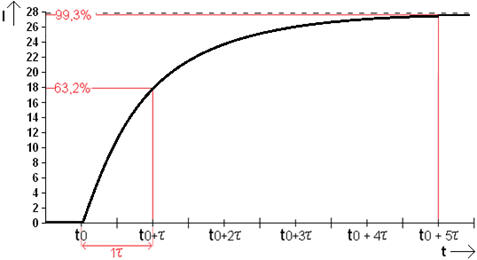
According to the specifications of the ignition coil, the primary current of the ignition coil is 7,5 A after charging. The current does not rise any higher. The time it takes to reach 7,5 A is called the dwell time. The dwell time depends on the battery voltage, which in this case is 14 volts. The current through the coil is, if the charging process is not regulated, a maximum of 12 Ampere according to formula 28.
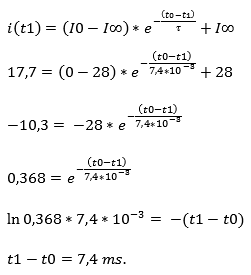
The coil of formula 14 is charged to 7,4 at t = 17,7 ms. The actual charging time is shorter, because the coil is charged to a maximum of 7,5 A. The time required can be calculated by filling in the known data in Formula 15.
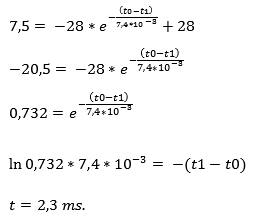
Primary current build-up is stopped at 7,5 A. This prevents the ignition coil from heating up excessively and unnecessarily. The most important thing is that the coil is charged as optimally as possible in the shortest possible time. The figure shows the charge curve up to t = 2,3 ms.
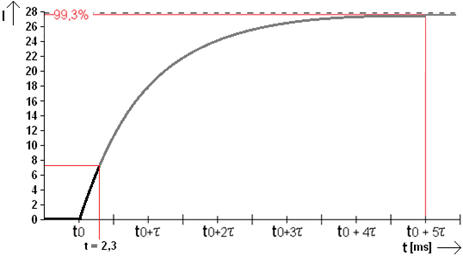
When the battery voltage drops, for example when starting the engine, this will affect the dwell time. It then takes longer than 2,3 ms before the 7,5 A is reached. The new loading time is determined with the now well-known formula. The maximum current is determined by the battery voltage:
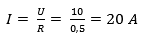
The charging time up to 7,5 A with a maximum of 20 A is calculated in formula 17:
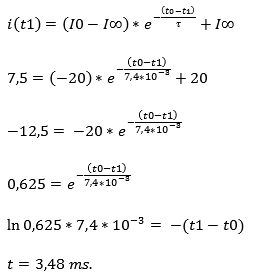
In the picture, the charging time at 14 volts is shown with the black line, and the charging time at 10 volts is shown in green. The lines drop to 0 at the same time; this is the ignition timing. Because a lower battery voltage takes longer to charge the primary coil, the MegaSquirt must turn on the primary power earlier.
The black lines (rising and falling) indicate the dwell time at a battery voltage of 14 volts. The green line indicates the advanced charging time at a lower voltage: this gives Δt. The actual loading time in that case is therefore Δt + 100%.
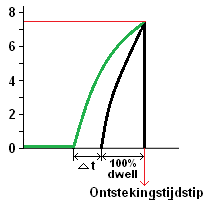
This is clarified later in this section with an example and figure 36. The charging time is extended and the ignition timing remains the same. If this is not done or insufficiently, this will have consequences for the energy released during the ignition. In that case, the primary current is switched off too early, so that the current of 7,5 A is not achieved. The extension of the primary coil charging time (dwell time) is in formula form a function of the battery voltage. Calculating the dwell time at different voltages gives a different maximum current in the coil.
By assuming that the battery voltage can drop to 6 volts during starting and rise to 14,7 volts during charging, a curve can be sketched by calculating a number of intermediate values. The image below shows the dwell time correction for the applied DIS coil. With every increase of 2 volts a (red) dot is placed in the graph. Since a previously entered dwell time of 2,3 ms at a voltage of 14 volts has been entered in the TunerStudio program, a correction factor is formed from this voltage. A voltage of 14 volts is therefore 100% (no correction).
It has now been made clear that the charging time increases by up to 315% at a battery voltage of 6 volts.
The battery voltage can drop by as much as 6 volts in unfavorable conditions. This means a weakening in the ignition spark. Increasing the dwell time (the time that the primary current flows) compensates for this, so that sufficient ignition energy is obtained even at this low voltage. This means that Δt from Figure 36 is tripled (2,3 ms * 315% = 7,26 ms) from the black marked dwell time of 100% (2,3 ms).
The coefficients marked in red in the image above can be copied directly into the TunerStudio program.
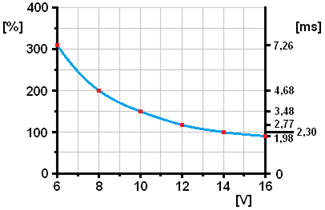
Some time after the primary coil is discharged, the build-up for the next ignition begins. The higher the engine speed, the faster the coil is recharged. Figure 37 shows two curves where the primary current increases to 8,85 A. The ignition timing is at the point where the line drops to 0 A.
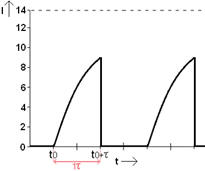
Determining the ignition time:
The ignition signal is determined from the crankshaft reference point.
In the sprocket of the crankshaft pulley, 36 of the 1 teeth has been milled out at 100 degrees before the top dead center of the piston of cylinder 1. Between 100 and 0 degrees, so during the compression stroke, the microprocessor of the MegaSquirt can determine the ignition timing . This takes into account the advance.
The image shows the two-channel oscilloscope image in which the top image shows the crankshaft reference point and the bottom image shows the drive signal from the MegaSquirt to the DIS coil. The control signal has a voltage of 5 volts (a logic 1) and lasts about 1,5 ms.
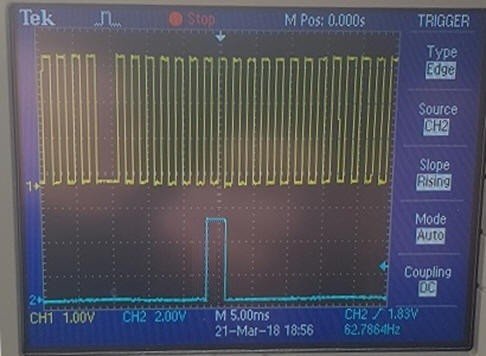
Ignition advance:
No knock sensors are used in this project. There is a possibility to process information from knock sensors, but mounting a knock sensor alone is not sufficient. The processing of the signals is complex. The knock signal must first be converted into a yes/no signal or into an analog signal that indicates the strength of the detonation.
The conversion of motor vibrations to a knock signal is done by an interface circuit. This circuit is not present in the MegaSquirt II. That is why it was decided to safely set the full-load and part-load advance, so that the motor cannot end up in the knock area. The full load advance curve to be set must be determined within the knock limits. The centrifugal and vacuum advance data of the conventional ignition is determined on the basis of the factory data from the engine manual. The points can be plotted in a graph (example in the image below).
The pink line indicates the original mechanical advance. This is partly linear due to the mechanical construction of the centrifugal weights. The black line represents the map control in the MegaSquirt; this line follows a curve. It is important to stay out of the part-load and full-load knockdown areas; that is why the map control in part load is limited (red line) and the advance at full load does not increase any further than in the situation with mechanical advance (red line). The actual map arrangement is according to the blue line.
First, the full load advance curve had to be entered in the spark advance table. At a higher speed and at a lower load, more advance will be required. In the case of part load, the advance is added to the full load advance. Page 7 shows the completed ignition advance table and cold advance settings.
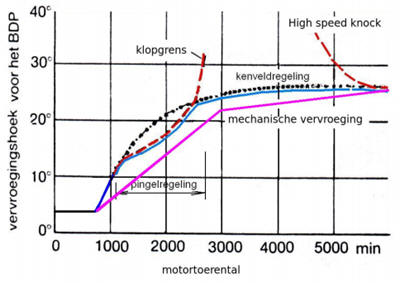
Throttle Body:
The air/fuel supply was controlled by the carburettor in its original condition. For the engine management system, the carburettor is replaced by a throttle body and four injectors that are mounted in the intake manifold. This provides a more precise and controlled injection than the carburettor, where an air/fuel mixture is formed centrally in the manifold and divided into four channels. The throttle is opened by a Bowden cable that is manually operated from the instrument panel.
After all, the MegaSquirt II does not support an electronically operated throttle body. Therefore, the Bowden cable control is the only option to use.
Throttle position is transmitted to the MegaSquirt by means of a voltage. The magnitude of the voltage depends on the opening angle of the throttle. The throttle position sensor is a potentiometer with a supply voltage of 5 volts (see picture). Connection 3 and a ground connection 1 are necessary. The runner (pin 2) takes a position on the resistance that depends on the throttle position. The runner is thus connected to the gas valve. When the bishop has to bridge a small distance over the resistance (the bishop points to the left) then the resistance is low. In the picture, the wiper is to the right (the ground side) which means that there is a high resistance and therefore a low signal voltage.
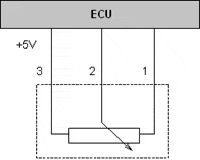
With the throttle body used, there is a voltage of 600mV on the wiper when the throttle is closed and a voltage of 3,9V when the valve is fully open. The ECU receives the voltage and calculates the opening angle of the throttle. A rapid increase in the opening angle means acceleration is taking place; the ECU responds to this by short-term enrichment. This is called the acceleration enrichment. The throttle position sensor is not used to determine mixture enrichment under various operating conditions; the MAP sensor is used for this.
Test setup of the stepper motor with simulator:
After the MegaSquirt had been modified in hardware, the breakout box could be used to check whether the control of the stepper motor is being received. The lighting of two-color LEDs indicates that an actuation is taking place. The steps in which the stepper motor is controlled can be followed by looking at the change of the colors. The colors alternate between red and yellow. Stepper motor data can be entered in the “Idle control” menu in the TunerStudio program. In addition to the type (4 wire), the number of steps can also be set. This also includes the starting position in which the stepper motor must be when the motor is started. Furthermore, the time can be set for how long it takes to adjust one step.
The number of steps depends, among other things, on the coolant temperature; a lower temperature requires a larger opening of the stepper motor. The steps relative to the temperature can be set in a graph. The simulator can be used to check whether the stepper motor is actually properly controlled. By checking it on the simulator first rather than on the engine, it can prevent problems starting or running the engine due to a possible hardware or software problem. Since mainly the coolant temperature and the motor speed influence the opening angle of the stepper motor, it is possible to check whether the control is correct by turning these potentiometers. The gauge on the dashboard in TunerStudio will show the adjustment in the number of adjusted steps.
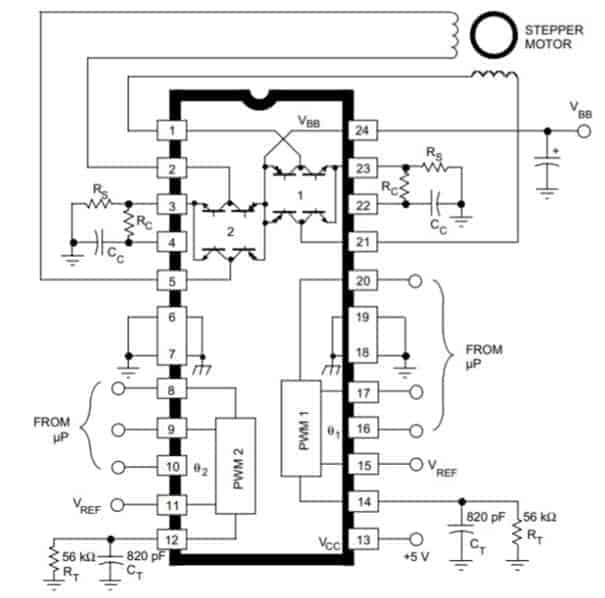
Stepper motor settings:
The illustration shows the setting screen for the stepper motor used for idle speed (idle control).
The steps in which the motor is adjusted are determined in advance with the help of an Arduino. Also, the number of steps must be entered to move to its base position (homing steps). The stepper motor is active in the warm-up phase (algorithm) and energizes the coils while stationary (hold current between steps).
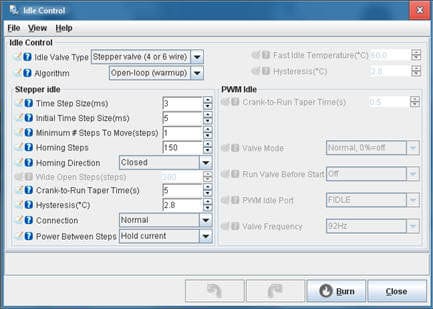
The position of the stepper motor depends on the coolant temperature. When starting a cold engine, the valve should be slightly more open than when the engine is warmed up. The image below shows the settings screen to set the steps (Steps) in relation to the coolant temperature (Coolant). When the engine is cold, the stepper motor is fully open when the engine is idling. During the warm-up phase, the stepper motor closes slightly.
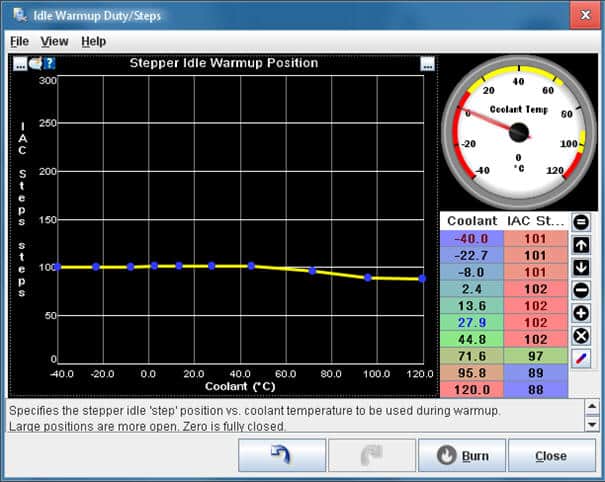
It is also possible to adjust the position of the stepper motor according to the coolant temperature during engine start-up. This is called the “Idle Cranking Duty/Steps”. The image below shows the settings screen.
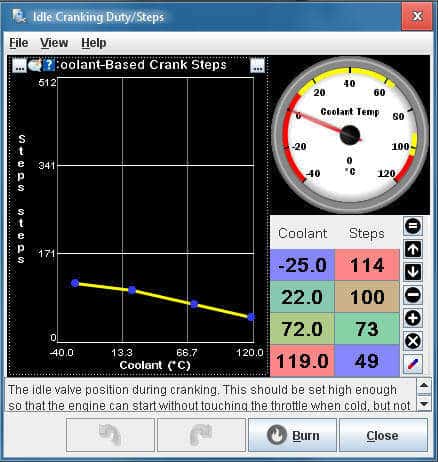
Fuel Pump Circuit:
The MegaSquirt takes care of switching the fuel pump on and off. Transistor Q19 in the figure below protects transistor Q2 against excessive currents. If the current is too high, the transistor may burn out. When the current through the collector-emitter portion of Q2 and R40 increases, the saturation voltage at the base of Q19 is reached. Transistor Q19 turns on, reducing the base-emitter voltage at Q2.
Connection FP-1 PTA0 is controlled internally by the MegaSquirt. An input signal from the crankshaft position sensor (a Hall sensor or inductive sensor) is needed to drive the transistor circuit. If the signal is lost, for example if the engine stops unintentionally, the supply to the fuel pump is immediately terminated.
The output of the transistor circuit (FP1 OUT) is connected to the fuel pump relay. Pin 85 of the relay is the output of the control current. With an energized relay, the main power portion (pins 30 and 87) is switched, providing the fuel pump with a supply voltage to operate.
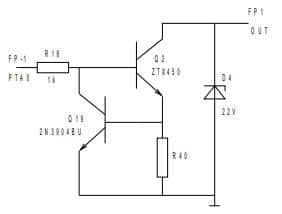
An electronic fuel pump with a working pressure of 3 bar is used. The fuel is directed through the fuel filter to the fuel rail, where the pressure is at the inlet of the injectors. The injector will inject a pre-calculated amount of fuel into the intake manifold when a signal comes from the MegaSquirt. Not only the control of the MegaSquirt determines the amount of fuel injected, but also the fuel pressure in the rail.
At a higher rail pressure, a larger amount of fuel will be injected with the same control. The rail pressure must therefore be adjusted on the basis of the underpressure in the inlet manifold. The pressure difference (∆P) must remain 3 bar at all times. The picture shows the schematic of the fuel system. The pink, yellow, orange and black lines indicate the electrical connections. The red line indicates the fuel supply and the blue line the fuel return.
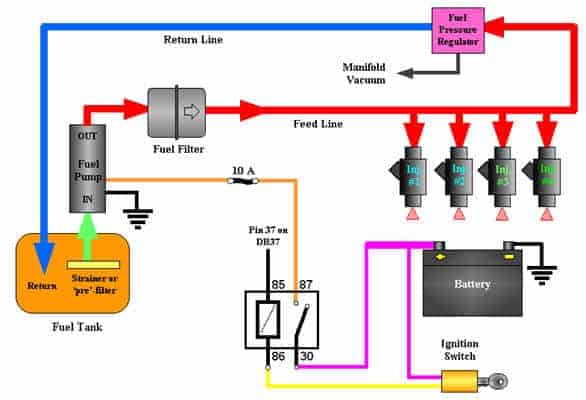
Completion of the mechanical work:
The next three photos show the engine in the final phase of the mechanical adjustments.
Photo 1:
This is the side where most of the applied parts are visible. The dashboard for the controls and the MegaSquirt ECU are also located here. Below the photo is a legend with the description of the numbers for the parts. You can open the photos in a larger size by clicking on them.
- throttle valve;
- Fuel line for the injectors;
- Connecting tube for throttle valve on intake manifold;
- fuel pressure gauge;
- Intake and exhaust manifold;
- Dashboard with cooling fan switch, lights for alternator and oil pressure, ignition switch and ground switch;
- Vacuum hose for MAP sensor;
- Lambda probe;
- Fuel hoses (supply and return) together in a shrink tube;
- Fuel pump / tank unit;
- fuel pump relay;
- Mega Squirt;
- Exhaust muffler.
Photo 2:
This photo shows the other side of the engine. Here you can see the carburettor (15) and the conventional ignition (17). The purpose of this classic ignition is to spark the spark plugs in the test rig (14). Of course this has no function for the engine, but it does provide insight into the operation of the ignition as it worked in classic cars.
Number 20 denotes the transmission brake mechanism. The rod of the brake drum can be tightened by means of a Bowden cable, so that the output shaft of the gearbox is braked. The transmission brake is applied to momentarily load the engine when a gear is engaged.
Photo 3:
The top view of the engine with the ignition test set-up and the fuel rail are clearly visible here.
The mechanical adjustments are complete. The engine cannot be started yet, as some data must first be entered into the MegaSquirt.