Subjects:
- History of the diesel engine
- Operation
- Advantages & Disadvantages of the diesel engine
- Duty Cycle Of The Four Stroke Diesel Engine
- Direct & Indirect Injection
- Low & high pressure section
- Injection process
- diesel knock
History of the diesel engine:
The diesel engine is named after its inventor Rudolf Diesel (1858-1913). The first diesel engine according to Diesel's theory became a reality on February 17, 1894. This engine worked on the principle of spontaneous combustion and ran for 1 minute long 88 rpm. Robert Bosch developed the high-pressure injection pump that allowed the diesel engine to start its worldwide conquest.
The first passenger car with a diesel engine was the 170 Mercedes-Benz 1935D.
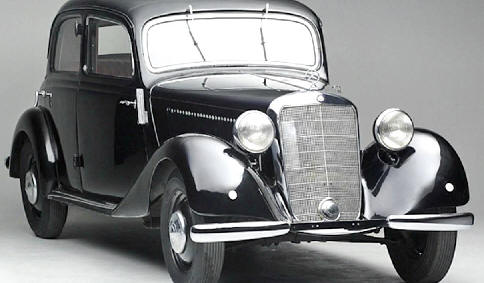
Operation:
A diesel engine gets air in the cylinders. No mixture, as is often the case with petrol engines. There the fuel is often already mixed with the air (the mixture). The air in a diesel engine is sometimes drawn in by the engine itself (without turbo) usually supplied under pressure by a turbo. This is called pressure filling. The supercharging allows a greater amount of air to enter, which can be ignited with additional fuel. More information about pressure filling can be found on the page turbo. The diesel engine is supplied with as much air as possible, which is not regulated by quantity as with a petrol engine. The unlimited air supply is called an “air surplus”.
In the diesel engine, the fuel is not ignited by the aid of a component (like the spark plug ignites the gasoline fuel in a gasoline engine). In a diesel engine, combustion is achieved by injecting the diesel fuel. This gives the diesel engine the name "self-igniter". The high pressure fuel pump provides the required fuel pressure.
A lot of heat is needed for this combustion. This heat is generated by the high compression pressure created by the piston during compression. By compressing the air (it is put under a very high pressure) a lot of heat is created. This heat is needed for combustion.
De atomizer injects a certain amount of diesel fuel just before the piston is at TDC. Usually this is done in several steps, with a pre-, main and post-injection. Because the diesel fuel is mixed with the warm air (due to the high compression final pressure), this fuel ignites by itself. This is called the labor stroke. (More on the four-stroke process later).
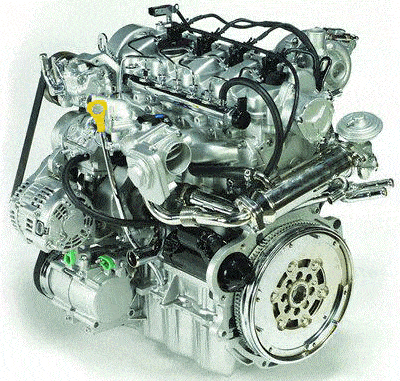
The diesel engine therefore needs heat to start combustion. This heat (of at least 250 degrees) is not yet present when the engine is started. The compression final pressure often does not give the correct temperature in the combustion chamber. To solve this, there are glow plugs mounted in the cylinder head. These glow plugs activate when the engine is started and ensure that the air in the combustion chamber has the correct temperature for the diesel fuel to ignite.
Advantages & Disadvantages of the diesel engine
- Advantages of a diesel engine compared to a petrol engine:
Due to the higher compression ratio and the course of combustion, a diesel engine is more economical than a petrol engine. A diesel engine generally also has a longer lifespan (depending on the way of use). - Disadvantages of a diesel engine compared to a petrol engine:
A diesel engine is noisier, has a lower power compared to a petrol engine with the same displacement (without the use of a turbo and intercooler) and it is a more expensive, more heavily constructed engine. The pre-heating of the engine is no longer a disadvantage, because a direct injection diesel engine can start without pre-heating. Even at temperatures around freezing point, it will still start after a little longer starting.
Today, diesel engines are getting quieter, making it more and more difficult to tell the gasoline and diesel engines apart.
Duty cycle of the four stroke diesel engine:
A diesel engine duty cycle consists of four strokes; the intake stroke, the compression stroke, the power stroke and the exhaust stroke. During these strokes, the piston has moved down and up twice. As a result, the crankshaft has been rotated twice.
During each stroke, all kinds of things happen; air is drawn in, fuel is injected, the air and fuel are burned and the remaining gases are expelled from the cylinder. Below is described what exactly happens in which stroke:
- Intake Stroke:
The inlet valve is open, the exhaust valve is closed. The piston moves from TDC to ODP.
– Without turbo: Air is sucked in due to the negative pressure that is created.
– With turbo: The inlet air is fed from the turbo into the cylinder space with overpressure.There is no regulating valve in the intake path, such as the gas valve of the petrol engine. With a diesel engine, the amount of air that is sucked in is therefore not adjustable. The throttle valve located in the intake system (the throttle valve) serves only to shut off the engine. By closing this valve and thereby stopping the air supply, the engine will stall quietly.
Compression Stroke:
The inlet and outlet valves are closed. The piston moves from ODP to TDC. The air is compressed. As a result, the temperature of the air rises and, depending on the compression ratio, can reach a temperature of about 550 degrees. With a petrol engine, the temperature is about 400 degrees. When starting from cold, the engine is first warmed up by the glow plugs to reach the temperature at which the mixture can ignite.Labor stroke:
The inlet and outlet valves are closed and the piston has compressed the air under very high pressure. A few degrees before TDC, fuel is injected through the injector, which ignites due to the high compression final pressure. The pressure from the ignition pushes the piston from TDC to ODP.exhaust stroke:
The inlet valve is closed, the exhaust valve is open. The piston moves from ODP to TDC and expels the exhaust gas. The loop process is described on the Seiliger process page.
Direct & Indirect injection:
An engine can be equipped with direct injection or with indirect injection. The differences between the two systems are described below.
Direct injection:
The injection pressure is higher with direct injection than with indirect injection. The fuel is injected directly into the cylinder (or the piston bottom formed for it) at the end of the compression stroke. The mixing therefore takes place in the cylinder and not in the swirl chamber as with indirect injection. In order to improve the mixture formation, the inlet air is swirled. The vortex is created by the shape of the intake manifold and the shape of the piston bottom.
Compared to a diesel engine with indirect injection, a direct injection diesel engine has the advantage that it requires less combustion chamber wall surface. As a result, a direct injection diesel engine will have less loss of compression and combustion heat, resulting in higher efficiency and cleaner exhaust gases.
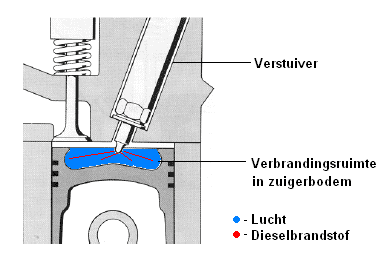
Indirect injection:
Indirect injection was most commonly used on older diesel engines. You hardly come across it these days.
In an indirect injection engine, the fuel is not injected above the piston, but injected, mixed and vaporized in the swirl chamber. The fuel is injected into the swirling air of the swirl chamber during the compression stroke. In this way a good mixture of fuel with air is created. The piston bottom in this case is flat (sometimes with recesses for the valves).
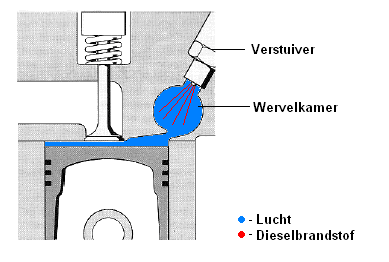
Low & high pressure section:
The fuel supply of a diesel engine is divided into 2 parts; the low-pressure section and the high-pressure section.
The low pressure section consists of the following parts:
- Fuel tank
- feed pump (mounted in the fuel tank, or one piece with the high pressure pump)
- Fuel filter (mounted under the car or under the hood, removes the contaminated particles and moisture from the diesel fuel)
- Low pressure fuel lines (the fuel is fed from the tank to the high pressure pump through these lines)
- Fuel return line (this drains the return and leak fuel from the injectors, high pressure pump and filter back to the fuel tank) This return/leak fuel is needed for cooling and lubrication of the affected parts. The heat is thus discharged to the tank.
The high-pressure section consists of the following parts:
- High pressure fuel lines (the fuel is fed from the high pressure pump to the injectors through these lines. The lines must all be the same length and thickness to avoid pressure differences)
- high pressure pump (the fuel pumped from the booster pump to the high pressure pump is pumped from here through the high pressure fuel lines to the injectors)
- Atomizer (injects the fuel into the cylinder when opening pressure is reached)
Injection Process:
The time between the injection of the fuel and the actual combustion is called the delay time. The small fuel droplets injected by the injector have to convert to gaseous form. This transition is possible due to the high temperature in the combustion chamber (which is reached by the compression ultimate pressure or the glow plug at start-up). This time should be as short as possible, otherwise it will affect the combustion. This also means that the engine will run worse and that less power will be available.
The image below shows the complete injection process.
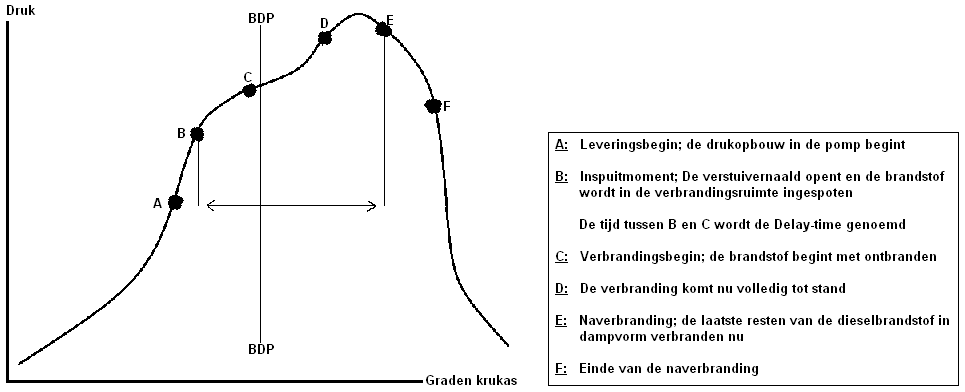
Diesel knock:
There are several milliseconds between the start of injection (see A in the figure above) and the start of combustion (C). The very small fuel droplets injected by the atomizer (the fuel mist) must first be brought up to temperature in order to be able to change into vapor form. The outside of the fuel drop will first turn into a gaseous state and then gradually burn. The remaining remains of the drop then spontaneously ignite and cause the recognizable engine noise; the diesel knock. This is an uncontrolled combustion and can take place at the wrong time.
The following things can cause a diesel knock:
- Defective atomizers (drip or a bad atomization with too large droplets)
- Defective injection pump (discharge valves or plungers defective)
- Fuel (water present, cetane number too low, air in fuel
- Engine (compression final pressure too low, glow plugs not working)
- Wrong timing of the fuel pump