Subjects:
- Torque converter operation
Torque converter operation:
The torque converter is mounted between the engine and automatic gearbox and consists of 3 basic parts; the pump wheel, the stator and the turbine wheel. In a torque converter, the force exerted by the engine is transferred to the driving wheels by means of a fluid flow. The pump wheel will turn. The liquid is thrown out by the centrifugal force. The liquid flows along the curved blades of the turbine wheel. The goal is that when the pressure increases, i.e. when more oil is pumped into the blades of the turbine wheel, the turbine will rotate with it.
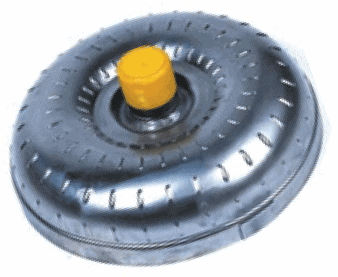
When the engine speed is low, the centrifugal force of the fluid will still be too low to rotate the turbine wheel. At an increasing engine speed, the centrifugal force will become so great that the turbine wheel is taken along and the vehicle will start to move. The speed of the turbine wheel will increase until almost the speed of the engine is reached. The pump speed and the turbine speed will never be completely equal in normal driving, because there are always certain losses, such as when the oil hits the side of the vanes. There is always a certain amount of slip. That is also the reason why cars with automatic gearboxes always use slightly more fuel than cars with manual gearboxes.
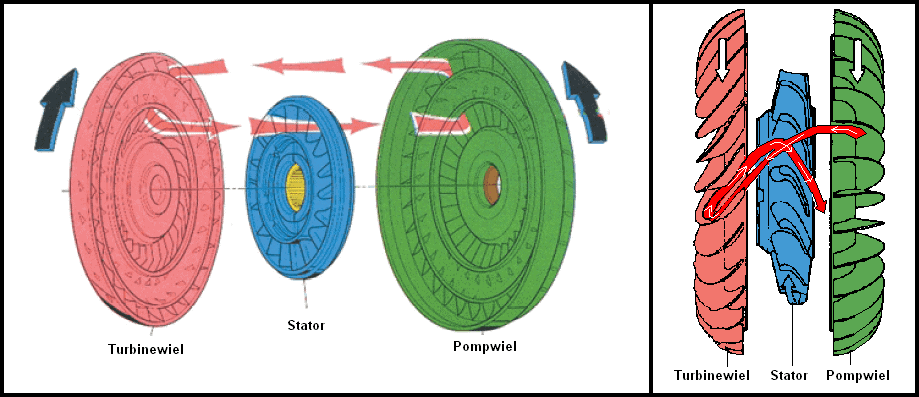
The stator is a ring-shaped part that rotates with the speed of the turbine. The stator ensures that the turbine is driven more powerfully. The stator has a freewheel function, and can only rotate in one direction. The oil that flows back from the turbine can thus settle against the stator, creating a little more pressure in the turbine (see the picture).
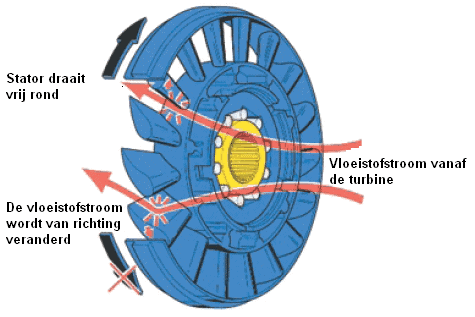