Subjects:
- Crankshaft Position Sensor (CPS)
- Oxygen sensor
- Coolant Temperature Sensor (CLT)
- Intake air temperature sensor
- Throttle Position Sensor (TPS)
Crankshaft Position Sensor (CPS):
The crankshaft position sensor is mounted on the front of the engine above the sprocket of the crankshaft pulley on the BMW engine. The ECU can determine the following from the signal from this sensor:
- the crankshaft speed: is determined by the speed at which the teeth move past the sensor.
- the crankshaft position determined from the sprocket reference point. One or more ground teeth serve as the reference point.
The crankshaft pulley is of the “60-2” type. The disc contains 60 teeth, two of which have been ground away. The ground teeth serve as a reference point. The actual TDC of the piston of cylinder 1 occurs 16 teeth later.
The number of degrees between the reference point and the actual TDC can be determined with a simple calculation:
Every time a tooth moves past the sensor, the crankshaft (360 / 60) = 6 degrees is turned.
If the reference point and the actual TDC are 18 notches apart, that is (6 * 16) = 96 degrees.
This fact is very important for the engine management system. After the reference point has been registered, the ECU can determine when to inject or ignite by counting the teeth. In the situation where the ignition has to be brought forward by 30 degrees, the ECU must ensure that 5 teeth before the actual TDC (5 teeth * 6 degrees = 30), ie 13 teeth after the reference point, sparks the spark plug. This does not take into account the charging time of the primary coil in the ignition coil, which also takes time, so in reality the ECU starts charging the primary coil a few crankshaft degrees earlier. We will come back to this in the section on the ignition coil in the chapter on actuators.
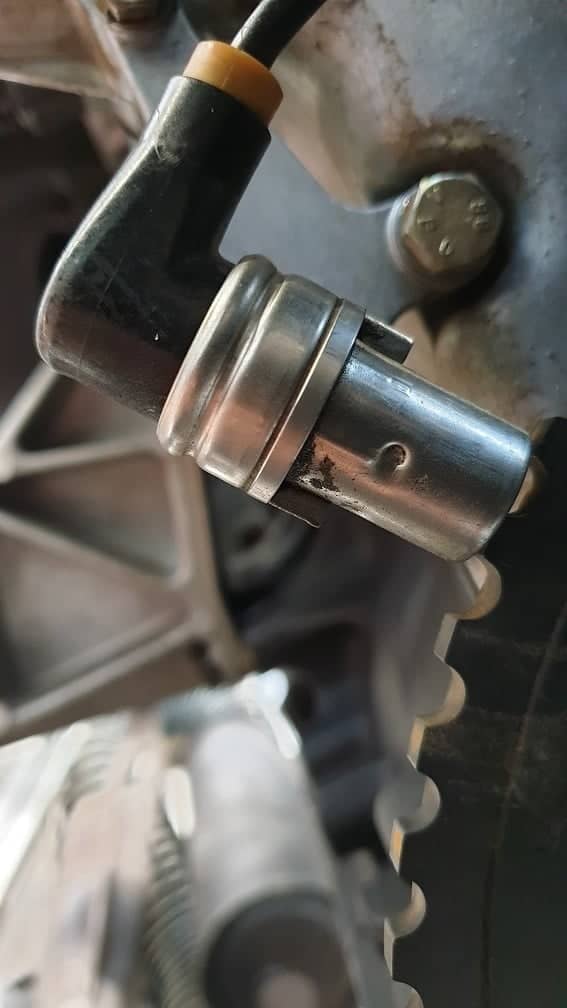
Lambda probe:
The oxygen sensor has been replaced by a Bosch LSU 4.2 5-wire wideand sensor. The sensor is connected to the Innovate LC-2 digital lambda controller. This controller converts the signal from the oxygen sensor into a digital signal and forwards it to the MegaSquirt ECU.
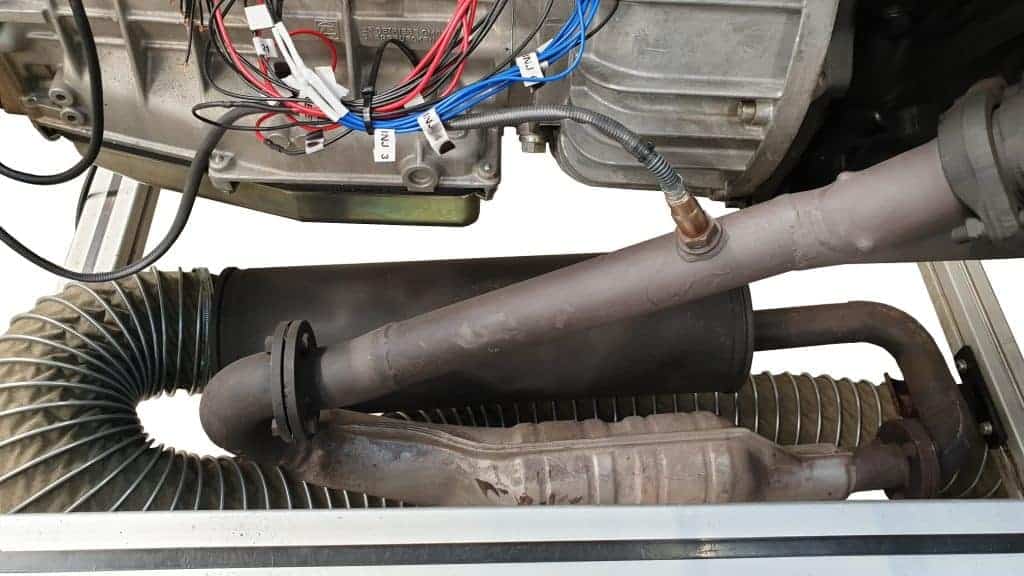
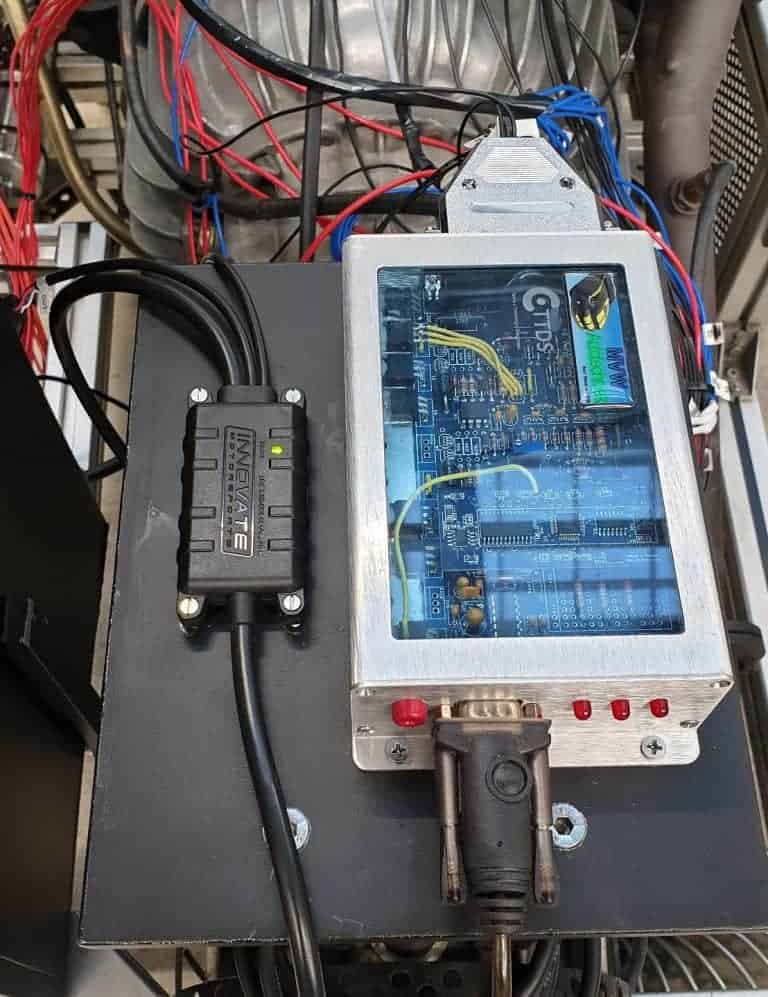
Specifications Innovate LC-2 O2 Controller:
Power | |
Operating Voltage | 9.8V to 16V DC |
Input Current, O² heater initial warm-up | 2.0A nominal, 3A max |
Input Current, O² normal operation | 0.8A nominal, 1.1A max |
Environmental | |
operating ambient temperature | 0° to 140° F (−17.78° to 60° C) |
Storage ambient temperature | −40° to 185°F (−40° to 85°C) |
Water resistance | Splash resistant, non-submersible |
Sensors | |
Compatible Types | Bosch™ LSU4.2 & Bosch™ LSU4.9 |
Bosch™ Heater Control | Digital PID via pump cell impedance |
measurements | |
Lambda | .5 to 8.0 |
Air/Fuel Ratio | 7.35 to 117 (gasoline), Fuel Type Programmable |
Accuracy | |
For Lambda | Accurate to +/- .007 (.1 AFR) |
Response Time | |
Free Air to Lambda | < 100 mS ( < 25 mS typical) |
Inputs | |
Serial | 1, Innovative MTS Compatible |
outputs | |
Analog | 2-0VDC, 5 bit resolution, programmable |
Serial | 1, Innovative MTS Compatible |
Communication | |
Serial | MTS (Innovate Modular Tuning System) compatible |
Coolant Temperature Sensor (CLT):
The engine was originally equipped with two sensors that both measure the coolant temperature. The image below shows the thermostat housing with two coolant temperature sensors and a thermal switch for the cooling fan. We do not use the left sensor. The middle one is connected to the MegaSquirt ECU. The reason we only use one sensor is explained below. We also do not use the thermal switch; we currently turn the cooling fan on or off with a manual switch. Later, the control will also be provided by the MegaSquirt.
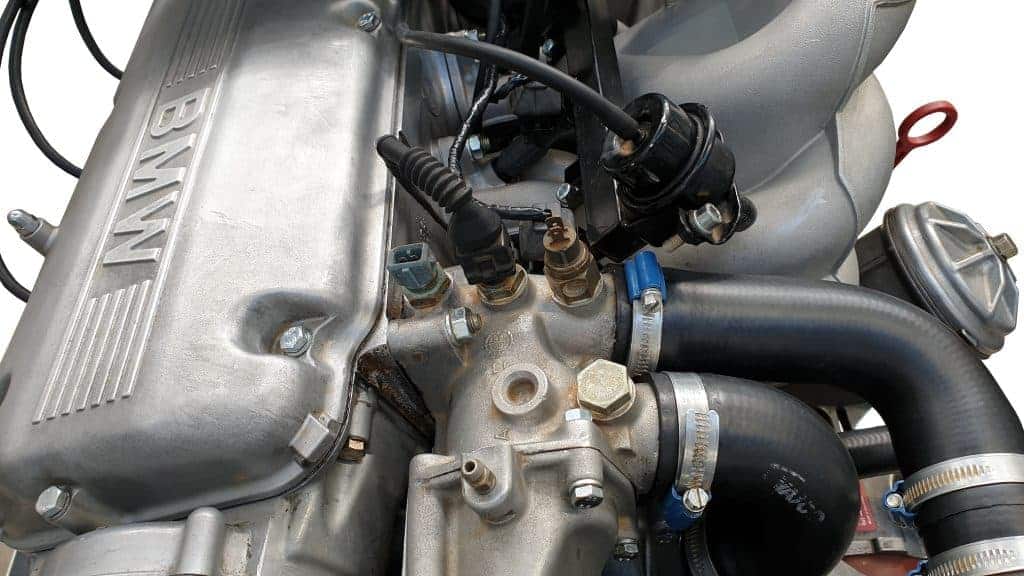
Why two coolant temperature sensors? And why do we only use one?
An NTC sensor has a logarithmic course. The resistance decreases with increasing temperature. The blue characteristic in the picture shows the greatest resistance change between 0 and 40 degrees Celsius. With increasing temperature, the resistance decreases less quickly.
The red characteristic also decreases with increasing temperature, but here the largest change can be seen between 40 and 80 degrees.
We are mainly interested in the temperature up to 60 degrees Celsius in connection with the cold start settings. Think of the fuel enrichment and the air circulation via the idle adjustment motor. Above 60 degrees Celsius, it is no longer necessary to fortify.
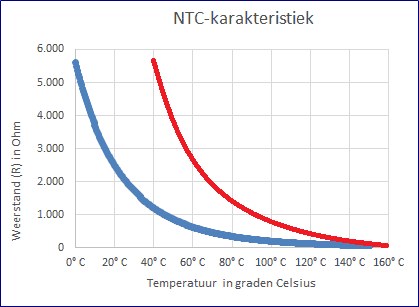
Intake air temperature sensor:
The original sensor is built into the air flow meter. However, this air flow meter has been removed. This means that a temperature sensor must be installed elsewhere.
We use a universal NTC sensor. The brand and origin are unknown. The important thing is that we measure the resistance values at a temperature change, and then enter them into the TunerStudio program.
The temperature sensor is mounted in the air intake pipe near the idle control actuator. The sensor is clicked into the hose. The measuring element is located in the air intake pipe and measures the temperature of the passing air.
Since there was no plug with the sensor, the wires were soldered to the contacts and protected with heat shrink tubing.
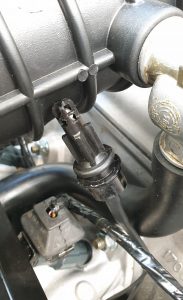
Throttle Position Sensor (TPS):
Information will follow later…