Subjects:
- Introduction to hydraulics
- Hydraulic Schematics
Introduction hydraulics:
By hydraulics we mean the transfer of energy (forces and movements) by means of a liquid. The word “hydraulics” comes from Greek (hydro = water, aulos = pipe). Hydraulics is a drive, control and regulation technology that we encounter in motor vehicle technology, mechanical engineering, drive and control technology, aircraft and agriculture. We can distinguish hydraulics in hydrokinetic and hydrostatic drive:
- Hydrokinetic: high fluid velocities and relatively low pressures, such as the torque converter in the automatic transmission;
- Hydrostatic: Low fluid velocities and high pressures, as we find in power steering.
In practice, in addition to hydraulics, we also find pneumatics, electronics and mechanical drive technology. Each technique has its own advantages and disadvantages for the application for which it is used. The advantages and disadvantages of hydraulics compared to the other techniques are:
Benefits:
- High power density; large forces and torques can be transferred with small component sizes;
- Infinitely adjustable speed, power and torque;
- Hydraulic energy can be stored and reused;
- High accuracy and constant positioning is possible.
Cons:
- Relatively expensive technique;
- Sensitive to dirt;
- Possibility of leakage (both internal and external).
In a hydraulic system, a movement of fluid takes place. The liquid flow can be set in motion by means of a pump or a piston. All hydraulic systems are based on Pascal's law:
“pressure exerted on a fluid at rest propagate uniformly in all directions in a closed vessel.”
We see this principle in the following figure, where a force (F1) is exerted on the piston surface with a piston. The force creates a pressure in the liquid-filled (closed) system, pushing the piston upwards with the force F2.
The pressure depends on the force and surface area of the piston. On the page "pressure in the hydraulic systemThis is made clear by means of animations and calculations.
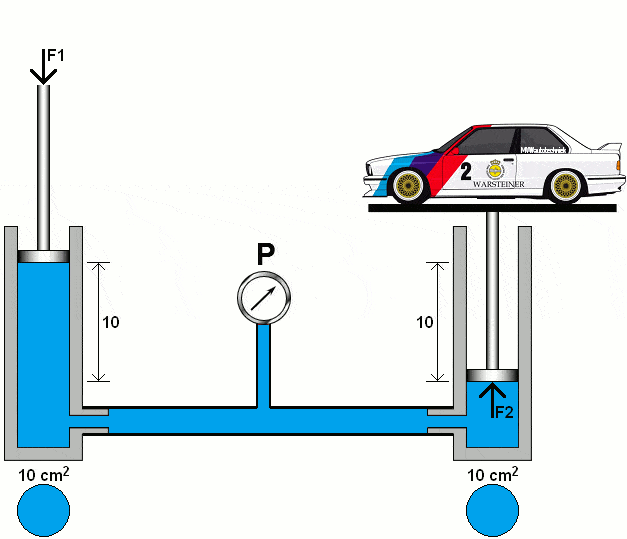
Hydraulic schemes:
The hydraulic diagrams made up of symbols are compiled by the manufacturer in order to be able to read how components are connected during maintenance and/or repair work. The flowchart also tells what types of components are in the system. An overview of the symbols can be found on the page with the hydraulic symbol list.
The following image shows the most commonly used components in a hydraulic system. The components are shown with a color and number.
An electric motor drives the hydraulic pump (1), which moves the hydraulic oil to the control slide (4).
The pressure relief valve (2) protects the system against excessive pressures. The system pressure can be read from the manometer (3).
The manually operable control slide has four connections:
P (pump), T (tank), and connections A and B for the cylinder.
The control slide can be set in three positions:
- at rest (current position);
- to the right;
- to the left.
Depending on the position of the control slide, the cylinder is supplied with hydraulic oil and the piston will move.
The following images show the different positions of the control slide with which the cylinder can be moved.
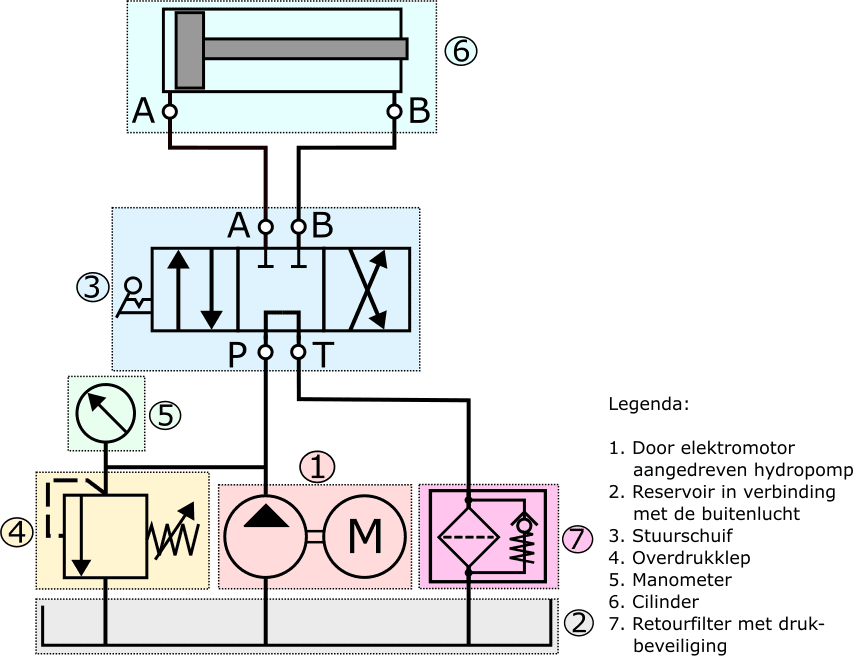
1. Control slide in neutral position:
The hydropump in the following diagram is again driven by an electric motor. The pump draws the hydraulic oil from the reservoir and supplies the oil under increased pressure to the pressure relief valve, pressure gauge and control valve.
The control slide is in the middle position, so that the connections P and T are interconnected and the hydraulic oil enters the control slide via P and leaves via T.
From connection T, the hydraulic oil flows through the return filter to the reservoir. In the housing of the return filter there is a pressure protection, which opens against the spring force when the liquid pressure increases.
The pressure increase can occur when the filter becomes clogged by dirt particles.
Because the hydraulic oil circulates in this position of the control slide, there is hardly any pressure build-up. There is only a limited amount of resistance that the oil encounters in the control valve, the pipes and the return filter. However, this resistance is so low that the oil is pumped around without pressure.
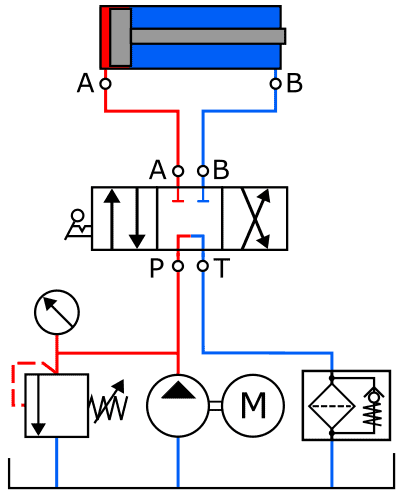
2. Control slide in left position:
The control slide is moved to the left position. The connections P and A, as well as T and B are in communication with each other in this position. The hydraulic oil moves through the pipes to the left side of the cylinder. The pressure build-up on the left side of the piston begins and is now sent out.
Because the return (B) of the cylinder is now connected to the T-connection of the control slide, the oil on the right side in the cylinder can flow – via the return filter – to the reservoir.
The cylinder makes an outward movement until the end stop is reached. We see this in the following situation.
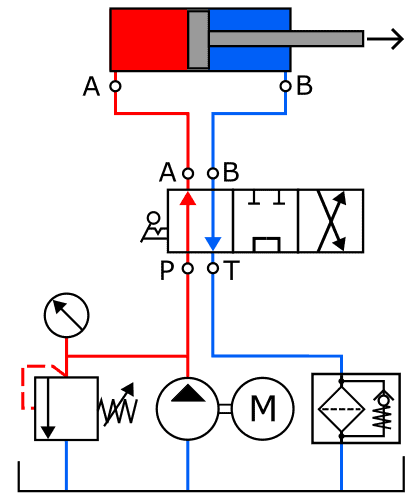
3. Piston in extreme position:
The piston is in this situation maximally extended, so the end stop has been reached. The overpressure protection prevents the pressure from rising too high. Without this protection, the pressure would rise uncontrollably, resulting in breakdowns.
The pressure control valve (shown to the left of the hydraulic pump in the figure) opens when the preset pressure is reached. The pressure relief valve connects the supply line from the hydropump to the return. A constant circulation now takes place via this pressure relief valve, until the pressure decreases.
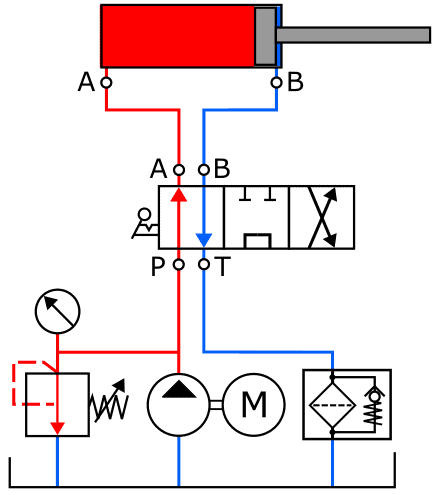
4. Control slider in the right position:
The control slide is now actuated in the right (opposite) position. Compared to situation 2, the pipes are connected to each other cross-left: the P is now connected to B, so that the pressure build-up on the right-hand side of the piston. Terminal A is connected to T (return). The piston moves from the control slide to the left in this position.
When the end stop of the piston is reached, the pressure build-up will rise again to the pressure at which the pressure relief valve opens. The control slide must then be returned to the middle position.
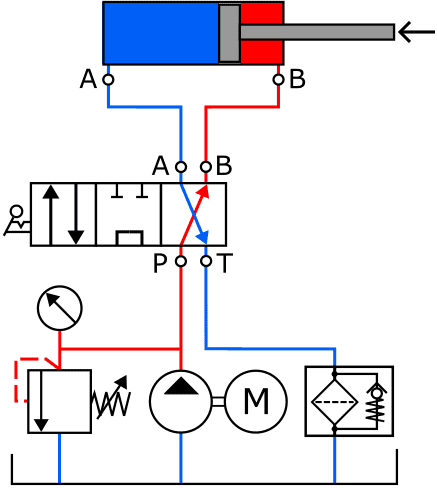
Related page: