Themen:
- Allgemeines
- Gesundheitliche Vorteile
- Pumpe-Düse austauschen und einstellen
- Kraftstoffförderpumpe
- Benutzerdefinierte Verteilung
- Kraftstoffkühler
Gesamt:
An moderne Dieselmotoren werden immer höhere Anforderungen gestellt. Verbraucher fordern immer mehr Komfort und Leistung, während Regierung und andere Behörden immer strengere Umweltauflagen stellen. Autohersteller sind gezwungen, sauberere und sparsamere Motoren zu entwickeln, die gleichzeitig mehr Leistung erbringen müssen. Beispiele hierfür sind das Common-Rail-System und das Unit-Injektor-Kraftstoffeinspritzsystem. Das Pumpe-Düse-Einspritzsystem wurde von Volkswagen entwickelt.
Volkswagen nutzte die Pumpe-Düse-Technologie für:
- 1.2 TDI,
- 1.4 TDI,
- 1.9SDI,
- 1,9 TDI 105, 110, 115, 130 und 150 PS,
- 2.0 TDI,
- 2.0SDI,
- 2.5 R5 TDI,
- 5.0 V10 TDI.
Aufgrund der Emissionsvorschriften werden in Neuwagen nicht mehr Pumpe-Düse-Einspritzventile, sondern Common-Rail-Einspritzventile eingesetzt.
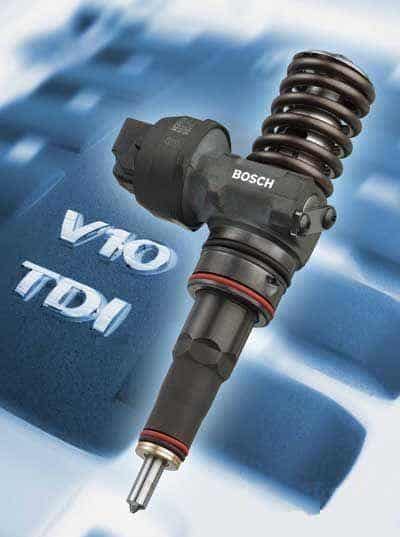
Operation:
Das Unit-Injektor-Einspritzsystem ist eine Kraftstoffdirekteinspritzung. Eine elektronische Kraftstoffpumpe pumpt den Dieselkraftstoff mit einem Druck von ca. 7,5 bar vom Tank zur Kraftstoffversorgung der Pumpe-Düse-Einheiten. Mit diesem Druck wird das Pumpenelement gefüllt. Das Pumpenelement der Pumpe-Düse-Einheit wird über einen Kipphebel von der Nockenwelle betätigt. Der Druckaufbau im Pumpenelement beginnt in dem Moment, in dem der Kipphebel die Einspritznadel nach unten drückt. Die eingespritzte Kraftstoffmenge wird durch das Magnetventil gesteuert; Je länger das Steuergerät das Magnetventil ansteuert, desto mehr wird gespritzt.
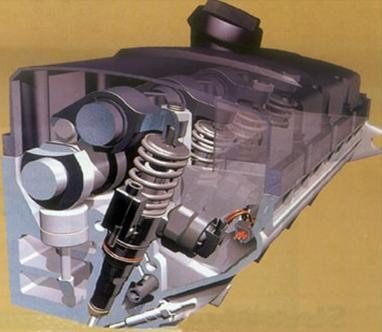
Der Pumpinjektor ermöglicht mehrere Injektionen nacheinander werden Erledigt:
- Voreinspritzung: Das Magnetventil beginnt zu arbeiten. Durch den Einsatz der Voreinspritzung wird die Verbrennung sanfter gestartet, was das Dieselklopfen reduziert. Die Höhe der Einspritznadel während der Voreinspritzung beträgt 1/3 der maximalen Höhe. Der Öffnungsdruck der Injektoren beträgt dann 180 bar.
- Haupteinspritzung: Der Öffnungsdruck des Injektors für die Haupteinspritzung kann ca. 2000 bar erreichen. Dieser Druck wird erreicht, wenn der Motor seine maximale Leistung abgibt. Die Haupteinspritzung endet, wenn das Magnetventil nicht mehr betätigt wird.
Die Kipphebel, die die Kolben in den Pumpe-Düse-Einheiten betätigen, werden von der Nockenwelle angetrieben. Während des Pumpenhubs wird im Hochdruckraum ein hoher Kraftstoffdruck aufgebaut. Der Druck oben und unten an der Zerstäubernadel ist gleich. Die Zerstäubernadel bleibt daher geschlossen.
Wenn das Magnetventil aktiviert wird, verschwindet der Druck an der Unterseite der Zerstäubernadel. Der Druck oben ist größer und drückt die Kolbennadel nach unten.
Der dem Injektor zugeführte, aber nicht zur Einspritzung verwendete Kraftstoff wird über den Rücklaufkanal zum Tank zurückgeführt.
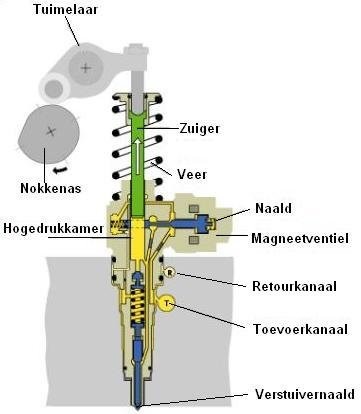
Pumpe-Düse austauschen und einstellen:
Nach der Demontage oder dem Austausch einer Pumpe-Düse-Einheit muss diese eingestellt werden. Dies erfolgt auf Basis zweier Messungen.
- Die erste Messung besteht darin, die Pumpe-Düse-Einheit direkt in den Zylinderkopf einzubauen. Hierzu dient der Messschieber.
- Die zweite Messung besteht darin, den maximalen Hub einzustellen, den der Kolben in der Pumpe-Düse macht.
1. Kipphebelwelle demontieren.
Zum Austausch einer Pumpe-Düse-Einheit muss eine der beiden Kipphebelwellen demontiert werden. In diesem Fall wurde die Kipphebelwelle der Pumpe-Düse-Zylinder 3 und 4 entfernt.
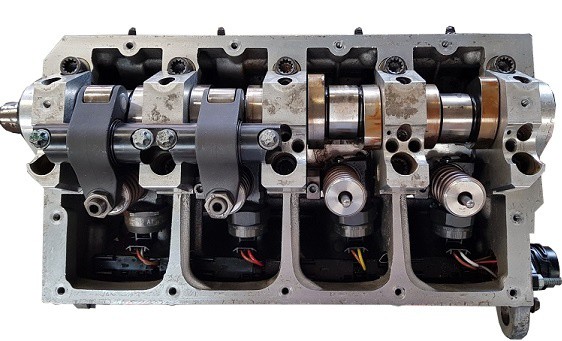
2. Klemmblock entfernen.
Um den Spannblock zu demontieren, muss die Schraube (gekennzeichnet durch einen roten Pfeil) gelöst werden. Der Spannblock ist am Verdampfer eingehängt und muss herausgezogen werden.
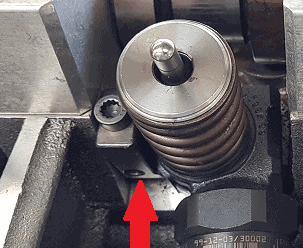
3. Pumpe-Düse demontieren und einbauen.
Ziehen Sie die Pumpe-Düse-Einheit mit dem Abzieher vom Zylinderkopf ab. Haken Sie den hervorstehenden Teil des Abziehers in den Teil ein, an dem der Spannblock in die Pumpe-Düse einhakt.
Installieren Sie neue O-Ringe um den Injektor, bevor Sie ihn austauschen. Anschließend den Injektor vorsichtig in den Zylinderkopf drücken und den Spannblock montieren. Ziehen Sie die Schraube noch nicht fest, da dies verhindert, dass sich der Injektor zur Einstellung dreht.
Im Bild wurde der Injektor von Zylinder 3 ausgetauscht (der linke). Das ist sichtlich schief. Die Anpassung erfolgt in Schritt 4.
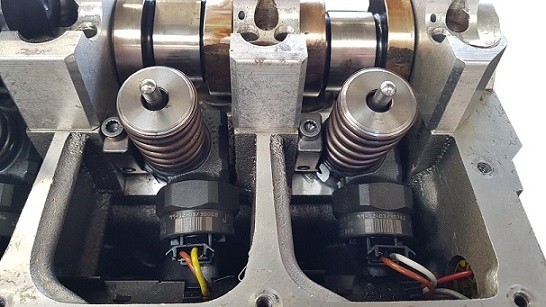
4. Passen Sie die Position der Pumpe-Düse an.
Mit dem Bremssattel Es muss der Abstand zwischen der Ausbuchtung des Einspritzventils und der Außenseite des Zylinderkopfs gemessen werden. Dies ist im Bild zu sehen.
Entspricht der gemessene Wert nicht dem vom Hersteller angegebenen Wert, muss der Injektor gedreht werden. Die Ausbuchtung des Injektors wird daher einen anderen Abstand zur Außenseite des Zylinderkopfes haben.
Der vorgeschriebene Wert dieses Abstandes beträgt: 151,3 mm ± 0,9 mm. Dies bedeutet, dass im Idealfall die Größe 151,3 mm betragen sollte, diese jedoch um 0,9 mm abweichen kann. Das Bild unten zeigt die Messung und das nächste Bild zeigt eine Vergrößerung des Messwerts auf dem Lineal.
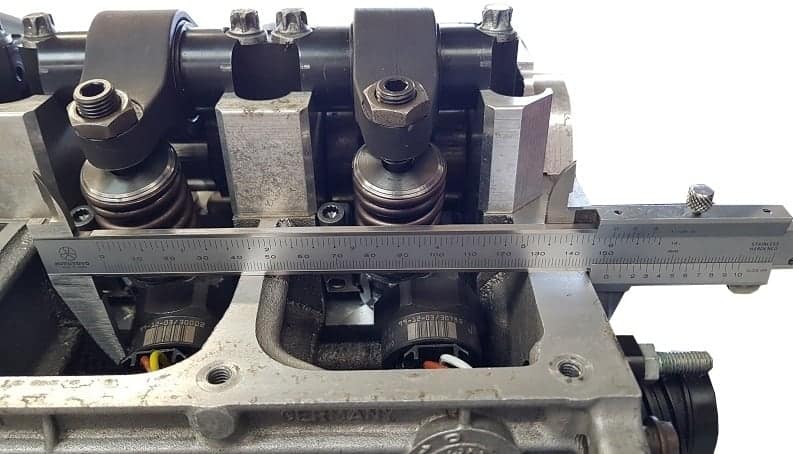
Das Bild zeigt eine Vergrößerung des Lineals während der Messung in Schritt 4. Die angegebene Größe beträgt 151,3 mm. Dies ist der vom Hersteller vorgeschriebene Wert. Der Bolzen des Spannblocks kann werden verschärft.
Bei der Messung anderer Pumpe-Düse-Einspritzventile muss die rechte Messbacke des Messschiebers am Zylinderkopf gehalten werden. Die Einstellwerte der anderen Injektoren werden daher alle unterschiedlich sein. Um die Messung am Injektor von Zylinder 1 (Verteilerseite) durchführen zu können, muss der Bremssattel einen Messbereich von 400 mm haben.
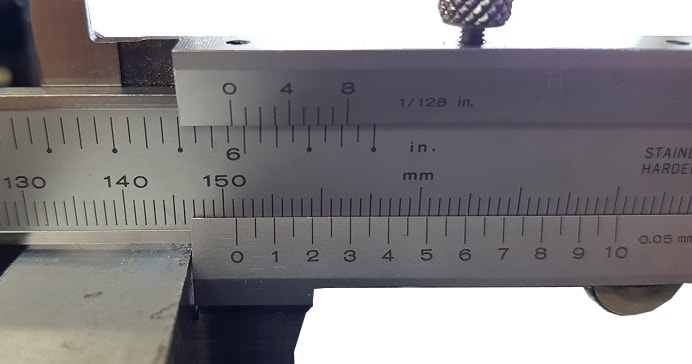
5. Installieren Sie die Messuhr.
Montieren Sie die Messuhr am ausgewechselten Injektor. Legen Sie die Messuhr auf die Seite des Kipphebels, die sich beim Betrieb der Pumpe-Düse-Einheit absenkt.
Da der Zeiger der Messuhr in jedem Fall den Kipphebel berühren soll, muss die Messuhr mit Vorspannung auf den Kipphebel gedrückt werden. Bei der Auf- und Abbewegung berührt die Nadel immer den Kipphebel. Achten Sie darauf, dass die Vorspannung mindestens 3 mm beträgt.
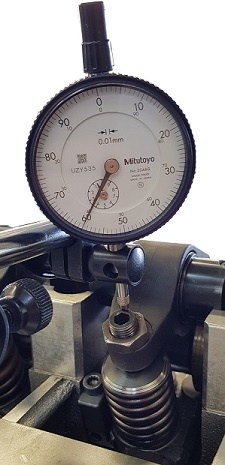
6. Drehen Sie die Kurbelwelle, bis der Kipphebel seinen tiefsten Punkt erreicht.
Der Zweck dieser Messung besteht darin, den tiefsten Punkt des Kipphebels zu messen. Die folgenden Messungen werden an der Pumpe-Düse-Einheit von Zylinder 2 durchgeführt.
Beim Drehen der Kurbelwelle senkt sich der Kipphebel, sodass der Wert auf der Messuhr abnimmt. Der Zeiger bewegt sich gegen den Uhrzeigersinn zurück.
Wenn der niedrigste Punkt erreicht ist, stoppt der Zeiger. Bei weiterer Drehung der Kurbelwelle steigt der Zeiger wieder an. An dem Punkt dazwischen, an dem der Zeiger stehen bleibt, hat der Kipphebel seinen tiefsten Punkt erreicht und der Einstellvorgang muss befolgt werden.
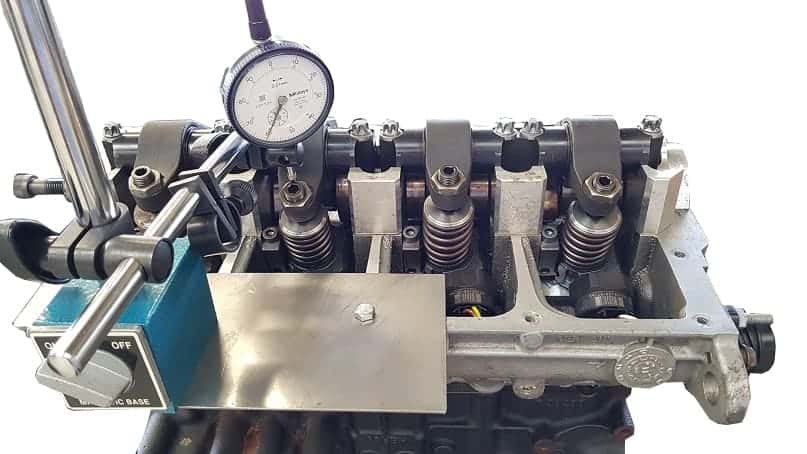
7. Einstellen der Pumpe-Düse (1).
Lösen Sie die Sicherungsmutter und drehen Sie dann die Einstellschraube ganz nach oben, bis der Kipphebel den oberen Ring der Pumpe-Düse berührt.
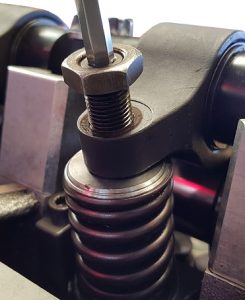
8. Einstellen der Pumpe-Düse (2).
Drehen Sie die Einstellschraube bis zum Anschlag in den Kipphebel hinein. Dadurch wird die Feder der Pumpe-Düse-Einheit komprimiert. Das Wenden kann schwierig sein. Hören Sie auf zu drehen, wenn ein großer Widerstand spürbar ist, da in diesem Moment der Kolben in der Pumpe-Düse den Boden der Hochdruckkammer berührt.
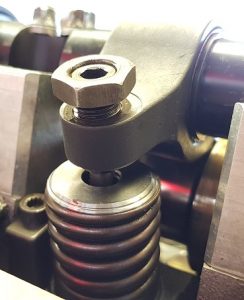
9. Drehen Sie die Einstellschraube um 180° zurück.
Nachdem die Einstellschraube vollständig bis zum Anschlag angezogen wurde, muss sie um eine halbe Umdrehung zurückgedreht werden. Dadurch wird verhindert, dass der Kolben in der Pumpe-Düse-Einheit jedes Mal, wenn die Nockenwelle die Pumpe-Düse-Einheit betätigt, auf den Boden der Hochdruckkammer trifft.
Wurden mehrere Pumpe-Düse ausgetauscht, muss diese Messung für jeden Injektor wiederholt werden. Bitte beachten Sie, dass die Einstellanweisungen je nach Motorcode oder Baujahr unterschiedlich sein können!
Aus den oben genannten Anweisungen und Bildern können keine Rechte abgeleitet werden.
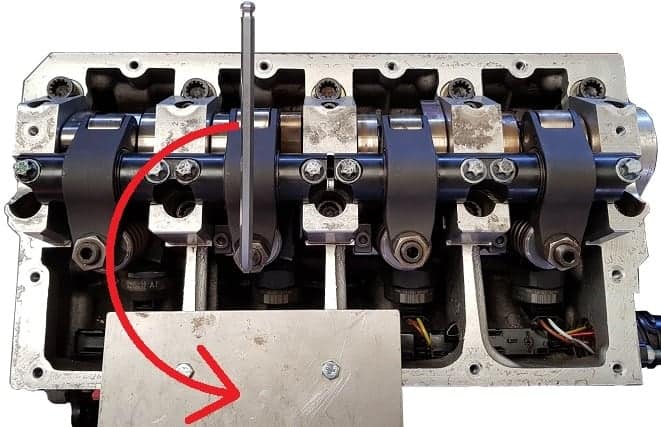
Kraftstoffförderpumpe:
Die Kraftstoffförderpumpe ist eine Flügelzellenpumpe mit Federtellern. Dieser wird dazwischen gelegt Kraftstofffilter und die Zerstäuber. Der Antrieb der Pumpe erfolgt über die Nockenwelle. Die Pumpe verfügt über ein Druckbegrenzungsventil, das den Druck in der Zuleitung auf 7,5 bar begrenzt. In der Pumpe ist ein Ventil eingebaut, das den Druck in der Rücklaufleitung der Pumpe-Düse-Einheiten konstant bei ca. 1 bar hält.
Benutzerdefinierte Verteilung:
Da der Druck in den Pumpe-Düse-Einspritzventilen auf ca. 2000 bar ansteigen kann, wird die Verteilung des Motors zusätzlich belastet. Um zu verhindern, dass der Riemen reißt, wurden verschiedene Maßnahmen ergriffen:
- Das Kurbelwellenrad weist an zwei Stellen etwas größere Zahnlücken auf. Sobald die Pumpe-Düse einen hohen Druck aufbaut, wird der Zahnriemen gedehnt. Dadurch wird die Zahnteilung etwas vergrößert. Dies wird dadurch ausgeglichen, dass die Zahnhöhlen an zwei Stellen etwas vergrößert werden.
- Der Zahnriemen wurde breiter gemacht und ist dadurch stärker.
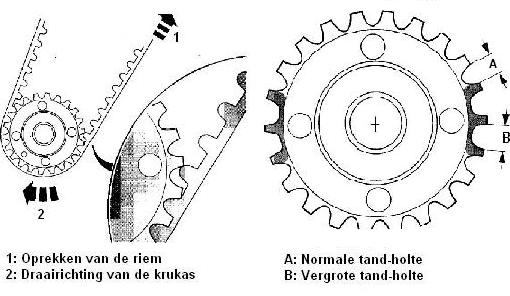
Kraftstoffkühler:
Die Funktion des Kraftstoffkühlers besteht, wie der Name schon sagt, darin, den Kraftstoff zu kühlen. Der Kraftstoffkühler befindet sich in der Nähe des Kühlers oder unter dem Auto. Im gesamten System herrscht ein kontinuierlicher Kraftstofffluss. Der in den Tank zurückfließende Kraftstoff wird durch den Zylinderkopf des Motors erheblich erhitzt. Der Kraftstoffkühler kühlt den zum Tank zurückfließenden Kraftstoff.
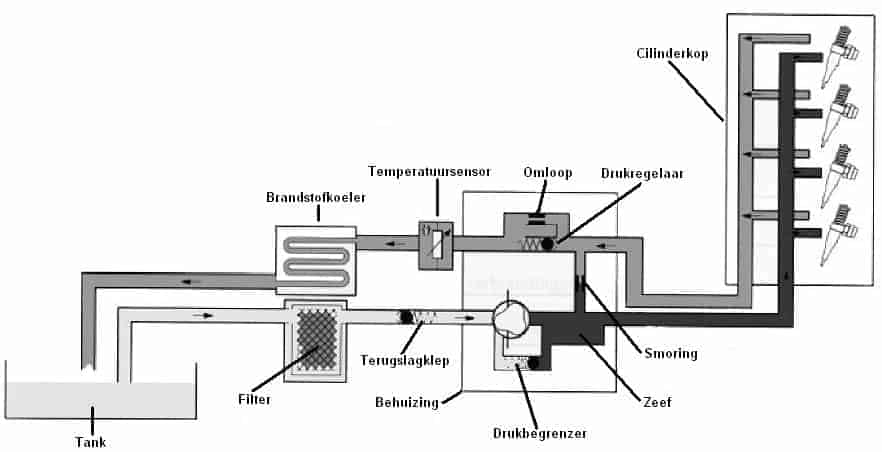
Verwandte Seiten: