Themen:
- Gesundheitliche Vorteile
- Unterschiede zwischen dem konventionellen Einspritzsystem und dem Common Rail
- Niederdruckabschnitt
- Hochdruckabschnitt
- Spannung und Strom am elektromagnetischen Injektor messen
- Motorelektronik
Operation:
Common Rail ist ein Einspritzsystem, das seit 1997 bei Dieselmotoren eingesetzt wird. Die Ansteuerung der Einspritzdüsen erfolgt über das Motorsteuergerät. Sowohl das Öffnen und Schließen des Injektors (die Einspritzzeit) als auch die Anzahl der Einspritzungen pro Verbrennungszyklus werden vom Motorsteuergerät bestimmt. Das Motorsteuergerät berechnet die Einspritzzeit anhand verschiedener Faktoren wie Drehzahl, Last, Außenluft- und Motortemperatur usw.
Die Hochdruckpumpe versorgt den Kraftstoffkanal mit Kraftstoffdruck. Im Kraftstoffkanal herrscht immer ein konstanter Druck. Alle Einspritzdüsen sind direkt mit dem Kraftstoffkanal verbunden. Der Kraftstoffdruck liegt somit auch direkt an der Versorgungsleitung jedes Injektors an. Erst sobald der Injektor ein Öffnungssignal vom Motorsteuergerät erhält, öffnet er. Der Druck aus dem Kraftstoffkanal gelangt nun über die Einspritzdüse in den Zylinder. Die Einspritzung stoppt, sobald das Motorsteuergerät das Signal beendet.
Die grüne Linie zeigt die Niederdruck-Kraftstoffversorgungsleitung.
Die elektronische Kraftstoffpumpe (11) fördert den Kraftstoff mit einem Druck von max. 5 bar über das Filterelement (9) zur Hochdruckpumpe (1). Eine Hochdruckleitung (rot) verläuft von der Hochdruckpumpe zum Kraftstoffverteiler. Im Kraftstoffverteiler herrscht ein Kraftstoffdruck, der von der Drehzahl der Hochdruckpumpe abhängt. Der Raildrucksensor erfasst diesen Wert und übermittelt ständig den aktuellen Kraftstoffdruck an das Motorsteuergerät.
Die Hochdruckleitungen aller Einspritzventile sind mit dem Kraftstoffverteiler verbunden, wie auf dem Kraftstoffverteiler mit der Nummer 8 und dem Einspritzventil mit der Nummer 16 dargestellt. Die Rücklaufleitung (blau) sorgt dafür, dass der gesamte überschüssige Kraftstoff von der Einspritzdüse, dem Kraftstoffverteiler und der Hochdruckpumpe zum Tank zurückgeführt wird. Zur Kühlung der Komponenten, die sich oft im Motorraum befinden, findet eine ständige Kraftstoffzirkulation statt.
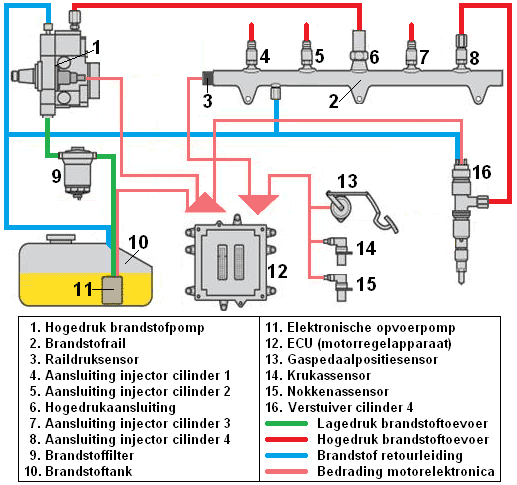
Unterschiede zwischen konventionellem Einspritzsystem und Common Rail:
Für (konventionelle) Dieselmotoren ohne Common-Rail-Einspritzung (also mit a Hochdruck-Leitungspumpe, Rotationsverteilerpumpe oder elektronisch gesteuerte Verteilpumpe) Die Einspritzdüsen werden durch den Druck des Kraftstoffs selbst geöffnet.
Die Kraftstoffpumpe dreht sich mit der Drehzahl der Nockenwelle und baut zum richtigen Zeitpunkt Druck auf. Der Druckaufbau und die Einspritzung hängen daher von der Steuerzeit der Kraftstoffpumpe im Verhältnis zur Nockenwelle ab. Deshalb muss beim Zahnriemenwechsel immer die Kraftstoffpumpe blockiert werden.
Bei Common-Rail-Motoren wird der Kraftstoff eingespritzt, wenn das Motorsteuergerät ein Signal gibt. Bei der ersten Generation der Common-Rail-Motoren spielte die Position der Pumpe daher keine Rolle. Dieser kann beim Einbau des Zahnriemens in jede beliebige Position gedreht werden. Die Pumpe versorgt die Einspritzschiene mit einem konstanten Kraftstoffdruck.
Heutzutage sind alle Motoren viel präziser abgestimmt. Auch die Pumpe muss oft blockiert werden. Dadurch sollen Vibrationen im Zusammenhang mit dem Druckaufbau der Pumpe verhindert werden. Die Pumpen sind nun so konstruiert, dass die Spitzen des Druckaufbaus gleichzeitig mit dem Kompressionstakt des Motors auftreten. Der Motor läuft ruhiger und der Zahnriemen wird weniger stark belastet.
Niederdruckabschnitt:
Der Niederdruckabschnitt umfasst den Kraftstofftank, die elektrische Kraftstoffpumpe, den Kraftstofffilter, die Niederdruck-Kraftstoffleitung und die Rücklaufleitung. Diese Komponenten werden im Folgenden beschrieben.
- Kraftstofftank: Hier wird der Kraftstoff gelagert. Das Tankvolumen kann bei leichteren und schwereren Luxus-Pkw zwischen 30 und 70 Litern variieren. Klicken Sie hier für weitere Informationen zum Kraftstofftank.
- Elektrische Förderpumpe: im Tank montiert. Diese Pumpe sorgt dafür, dass der Kraftstoff unter niedrigem Druck vom Tank zur Hochdruckpumpe (im Motorraum) gepumpt wird. Common-Rail-Dieselmotoren verfügen nicht immer über eine elektronische Druckerhöhungspumpe. Manchmal ist in die Hochdruckpumpe eine Zahnradpumpe eingebaut. Der Kraftstoff wird daher von der Hochdruckpumpe aus dem Tank angesaugt und ein Druck zum Kraftstoffverteiler aufgebaut. Klicken Sie hier für weitere Informationen zur Druckerhöhungspumpe.
- Kraftstofffilter: Kraftstoff kann verunreinigte Partikel enthalten. Diese Partikel bleiben im Filtermaterial hängen und können nicht in das Einspritzsystem gelangen. Der Kraftstofffilter dient auch als Wasserabscheider. Dieselkraftstoff enthält auch Feuchtigkeit. Diese Feuchtigkeit ist sehr schädlich für die Pumpe und die Einspritzdüsen/Leitungen. Dadurch kann es zu Korrosion im Inneren der Bauteile kommen. Um dies zu verhindern, wird zusätzlich das Wasser vom Kraftstoff getrennt und verbleibt im Filter. Dieser Filter muss regelmäßig entleert werden. ersetzen.
- Niederdruck-Kraftstoffleitung: Diese Kraftstoffleitung verläuft von der elektronischen Kraftstoffpumpe zur Hochdruckpumpe. Der Druck auf diesem Rohr beträgt ca. 5 bar.
- Kraftstoffrücklaufleitung: Der zu viel gepumpte Kraftstoff gelangt über die Rücklaufleitung zurück zum Tank. Der Rücklaufbrennstoff dient gleichzeitig der Kühlung, da er die Wärme abführt. Daher muss immer Rücklaufkraftstoff vorhanden sein. Beim Abbremsen (Motor wird abgebremst) wird kein Kraftstoff in den Brennraum eingespritzt. Zu diesem Zeitpunkt ist die Menge an Rücklaufkraftstoff am größten.
Anhand des Rücklaufkraftstoffs lässt sich auch erkennen, ob ein Injektor unbeabsichtigt offen bleibt. Die Ursache hierfür kann beispielsweise eine Verschmutzung oder ein Defekt des Injektors oder ein Fehler in der Ansteuerung des Motorsteuergeräts sein. Durch das Abtrennen der Rücklaufleitungen aller Einspritzventile und deren gleichzeitiges Sammeln kann der gegenseitige Unterschied betrachtet werden. Wenn bei einer Einspritzdüse merklich wenig Rücklaufkraftstoff vorhanden ist, kann es durchaus sein, dass die Einspritzdüse zu lange geöffnet bleibt. Es wird zu viel Kraftstoff eingespritzt. Dies ist im Bild unten zu sehen. Hier hat ein Einspritzventil keinen Rücklaufkraftstoff.
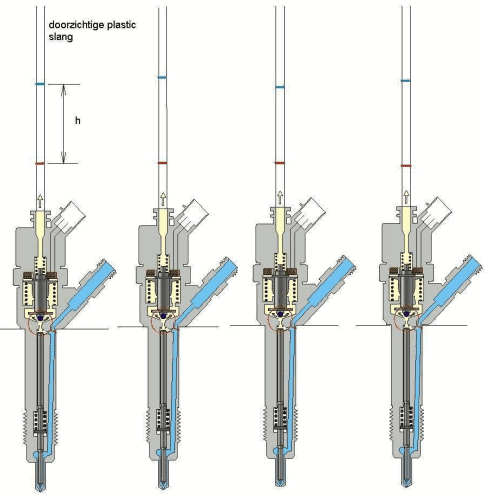
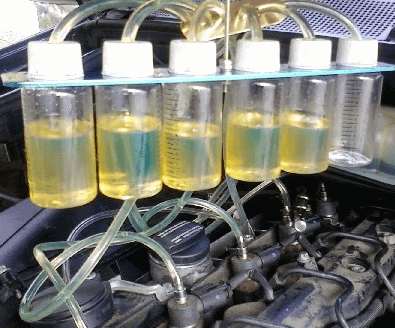
Hochdruckabschnitt:
Der Hochdruckteil umfasst die Hochdruckpumpe, den Kraftstoffkanal, die Hochdruckkraftstoffleitungen und die Einspritzdüsen.
- Hochdruckpumpe
Die Hochdruckpumpe ist als Plungerpumpe ausgeführt und sorgt dafür, dass der Kraftstoffdruck im Kraftstoffkanal (systemabhängig) auf einem konstanten Druck bleibt. Dieser beträgt 1300 bar bei der ersten Generation der Common-Rail-Motoren (ab 1997) und 2000 bar bei aktuellen Systemen. Je höher der Einspritzdruck, desto kleiner die Kraftstofftröpfchen und desto besser ist die Verbrennung und damit die Abgasemissionen. Die Kraftstoffmenge, die die Pumpe dem Kraftstoffkanal zuführt, ist begrenzt, da der Motor weniger benötigt. Der Druck bleibt dann in etwa gleich. Durch die Steuerung eines elektromagnetischen Überlaufs verstellt sich ein Steuerkolben aufgrund der Federspannung immer weiter. Der Raildruck nimmt dann ab. Auf der Seite Hochdruck-Kraftstoffpumpe wird die Funktionsweise verschiedener Arten von Hochdruckpumpen, einschließlich Common-Rail-Diesel, ausführlich erläutert.
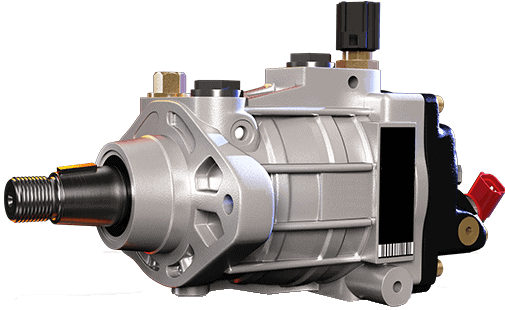
- Kraftstoffgalerie
Der Kraftstoff wird von der Hochdruckpumpe zum Kraftstoffkanal gepumpt. Im Kraftstoffkanal herrscht ein konstanter Kraftstoffdruck. Kraftstoffleitungen verlaufen vom Kraftstoffkanal zu den Einspritzdüsen. Der Raildrucksensor ist außerdem mit dem Kraftstoffkanal verbunden (bei zu hohem Raildruck sorgt das Motormanagement dafür, dass das Druckbegrenzungsventil öffnet) und es gibt eine Rücklaufleitung.
- Hochdruck-Kraftstoffleitungen
Da Hochdruck-Kraftstoffleitungen hohen Drücken standhalten müssen, müssen sie stark sein. Sie bestehen aus Metall und werden mit Überwurfmuttern sowohl mit der Pumpe als auch mit den Injektoren verbunden. Diese Hochdruck-Kraftstoffleitungen transportieren den Kraftstoff von der Hochdruckpumpe zum Kraftstoffverteiler und vom Kraftstoffverteiler zu den Einspritzventilen. Die Rohre zwischen dem Kraftstoffverteiler und den Einspritzdüsen haben alle die gleiche Länge und Dicke. Dies verhindert gegenseitige Einspritzunterschiede. Ist der Abstand zwischen Kraftstoffkanal und Zylinder 1 größer als zwischen Kraftstoffkanal und Zylinder 4, wird das Rohr von Zylinder 4 gebogen. Aufgrund dieser Biegung muss der Kraftstoff vom Zylinder 4 den gleichen Weg zurücklegen wie vom Zylinder 1. - Zerstäuber
Es gibt elektromagnetische oder Piezo-Injektoren angewandt. Mit diesen Injektoren können die Einspritzmenge, die Einspritzfolge und der Einspritzzeitpunkt gesteuert werden. Am Injektoreingang herrscht ein konstanter Kraftstoffdruck. Dies ist der gleiche Druck wie im Kraftstoffverteiler. Dieser Druck herrscht auch im Steuerraum, solange das Magnetventil geschlossen ist. Das Magnetventil wird von der ECU gesteuert.
Sobald das Magnetventil vom Motormanagement angesteuert wird, wird die Düsennadel angehoben und der Injektor spritzt eine bestimmte Menge Kraftstoff ein. Da der Raildruck und die Einspritzöffnungen immer konstant sind, weiß das Motormanagement genau, wie viel Kraftstoff in einer bestimmten Zeit eingespritzt wird. Da nach der Fertigung immer eine minimale Abweichung auftritt, muss diese Abweichung dem Motorsteuergerät mitgeteilt werden. Nach der Herstellung wird der Injektor getestet. Ein Code wird unter anderem anhand der Ergebnisse des Öffnungsdrucks und der Injektormenge ermittelt. Dieser Code ist auf dem Injektor eingraviert und kann vom Techniker gelesen werden (siehe Abbildung unten, der Code lautet 574-221). Diese Lernmethode ist für einen Benzinmotor und einen Dieselmotor gleich. - Spannung und Strom am elektromagnetischen Injektor messen:
Der Spannungs- und Stromverlauf am elektromagnetischen Injektor kann mit dem Oszilloskop gemessen werden. Damit lässt sich feststellen, ob der Injektor vom Steuergerät korrekt angesteuert wird.
Im Bild des Oszilloskops unten ist die rote Linie die Spannungskurve und die blaue Linie die Stromkurve. Das Bild oben zeigt zwei Injektionen. Links ist die Voreinspritzung und rechts die Haupteinspritzung. Bei anderen Motoren können bis zu drei Einspritzungen nacheinander erfolgen.
Der Injektor öffnet bei hoher Spannung und hohem Strom. Die Spannung beträgt ca. 80 Volt. Diese hohe Spannung kann durch einen Kondensator im Steuergerät erreicht werden. Diese hohe Spannung in Kombination mit einem niedrigen Spulenwiderstand sorgt für eine schnelle Reaktion des Injektors. Der Injektor verfügt daher über eine kurze Ein- und Ausschaltverzögerung. Da der Strom durch die Spule viel Wärme verursacht, muss diese begrenzt werden. Ohne Strombegrenzung läge der tatsächliche Strom bei bis zu 300 Ampere. Dieser Wert wird jedoch nie erreicht, da die Einspritzspule schon vor langer Zeit durchgebrannt sein wird.
Die Strombegrenzung ist daran zu erkennen, dass die Spannung ständig zwischen 4,6 und 5,1 ms ein- und ausgeschaltet wird. Während dieser Strombegrenzung sind Spannung (12 Volt) und Strom (12 Ampere) noch hoch genug, um die Einspritznadel offen zu halten.
Bei 5,1 ms wird die Steuerung gestoppt und die Einspritznadel schließt.
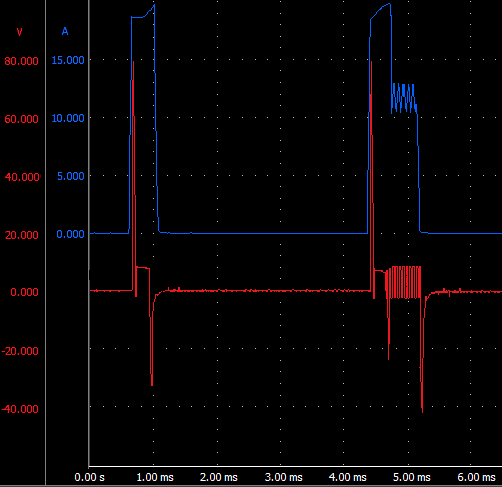
Motorelektronik:
Das Motormanagement (ECU) wird anhand von Daten von Sensoren (Gaspedalstellungssensor, Motortemperatur, Fahrgeschwindigkeit, Kurbelwellendrehzahl, Luftmenge) berechnet.Luftmassenmesser), Ansauglufttemperatur, Abgasqualität (NOx), die einzuspritzende Kraftstoffmenge und der Zeitpunkt, zu dem sie eingespritzt werden soll. Die Steuerung der Einspritzdüsen ist eine schwierige Aufgabe. Um in kurzer Zeit (max. 300 Millisekunden) einen Strom von mehr als 20 Ampere liefern zu können, ist eine Spannung von bis zu 80 Volt notwendig.
Dies wird mit der Ladung erreicht Kondensatoren und Leistungsverstärkerstufen.
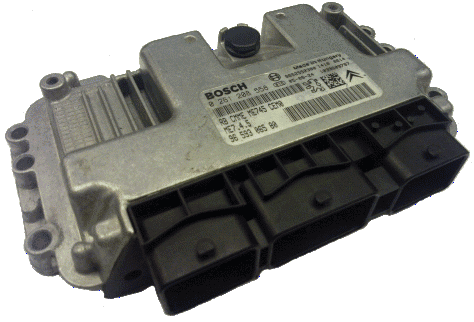