Przedmioty:
- Wprowadzenie
- Pomiar bez zakłóceń
- Błąd 1 – Przerwany przewód sygnałowy
- Błąd 2 – Przerwany przewód zasilający
- Błąd 3 – Przerwany przewód uziemiający
- Błąd 4 – Opór przejścia
- Błąd 5 – Zwarcie pomiędzy przewodem zasilającym i sygnałowym
- Błąd 6 – Zwarcie pomiędzy przewodem zasilającym i uziemiającym
- Błąd 7 – Zwarcie w czujniku C
- Błąd 8 – Brak napięcia zasilania z powodu uszkodzonego ECU
- Błąd 9 – Przerwany przewód sygnałowy PWM
- Naprawa przerwanego przewodu dodatniego
Przedmowa:
Jeśli podejrzewamy, że doszło do awarii, w pierwszej kolejności skanujemy samochód. The Kod błędu daje nam kierunek dalszych poszukiwań. Jeśli w pamięci błędów nie są zapisane żadne kody błędów, sprawdzamy, czy możemy rozpoznać odchylenia w danych bieżących. Zobacz stronę Diagnostyka Pokładowa.
Jeśli kod błędu dotyczy czujnika, nie oznacza to, że czujnik jest uszkodzony. Aby wykluczyć problem w okablowaniu i/lub połączeniach wtykowych, użyj: schematy elektryczne i sprzęt pomiarowy wykluczają pewne rzeczy. Na tej stronie omówiono szereg możliwych sytuacji i pokazano, że opis kodu błędu może różnić się od rzeczywistej przyczyny.
Pomiar bez zakłóceń:
Poniższy rysunek przedstawia pomiar napięcia zasilania i masy aktywnego czujnika.
Aktywny czujnik otrzymuje przez niego plus (5 woltów) i masę urządzenie sterujące. W tym przypadku zasilacz jest OK. Drugi pomiar możemy wykonać na przewodzie masowym (pin 3 czujnika i/lub pin 4 w ECU). Sygnał musi mieścić się w przedziale od 0,5 do 4,5 V.
Oprócz czujników aktywnych zajmujemy się również czujnikami pasywnymi i inteligentnymi. Więcej na ten temat przeczytasz na stronie: typy czujników i sygnały.
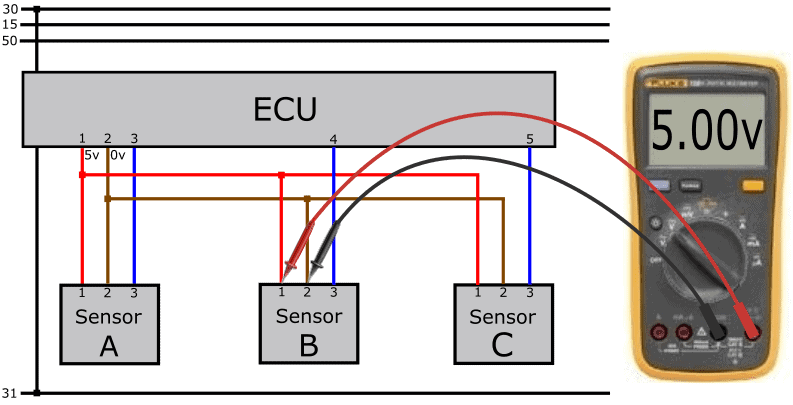
Do wytworzenia sygnału czujnik wykorzystuje napięcie zasilania 5 V. Sygnał musi mieścić się w przedziale od 0,5 do 4,5 V. ECU odczytuje poziom napięcia (lub w innych przypadkach częstotliwość) i przekłada go na wartość. Może to być na przykład wartość elementu czujnik ciśnienia ładowania są następujące: przy ciśnieniu turbo wynoszącym 1,5 bara czujnik wysyła do ECU napięcie 3,25 V.
Podczas tego pomiaru napięcie sygnału jest mierzone względem masy i jest prawidłowe.
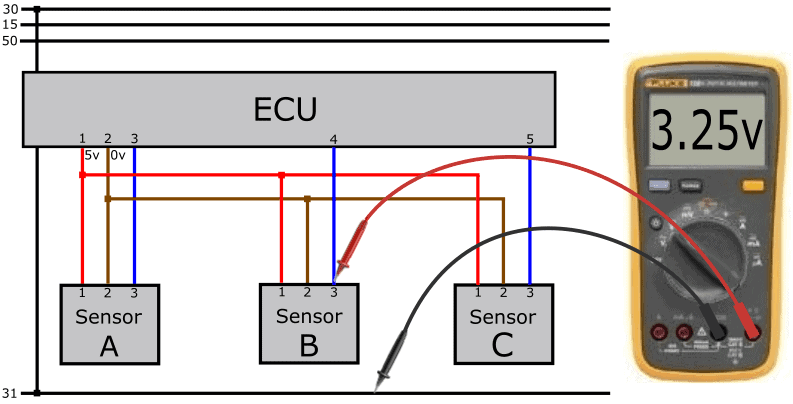
Korzystanie z pudełko ucieczki możemy zmierzyć we wtyczce ECU. Wiemy wtedy, jakie napięcia wysyła i odbiera ECU.
W następnym pomiarze ponownie mierzymy 3,25 V, ale wtedy na wejściu ECU. Oznacza to, że przewód sygnałowy jest w porządku: napięcie jest przesyłane w stosunku 1:1 z czujnika do ECU.
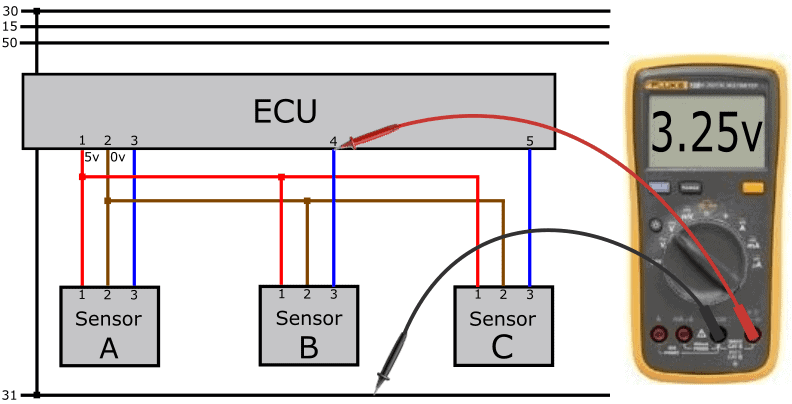
Sygnał czujnika nigdy nie będzie wynosił 0,0 lub 5,0 V. Zawsze zostaje zachowany pewien zakres. Często wynosi ono od 0,5 do 4,5 V. Czujnik nie będzie generował napięć niższych niż 0,5 lub wyższych niż 4,5 V. W przypadku usterek czujników lub okablowania, ECU rozpoznaje na podstawie poziomu napięcia, czy wartość mieści się w zakresie pomiarowym, czy poza nim:
- napięcia niższe niż 0,5 V: ECU generuje kod błędu z opisem: „czujnik
- w przypadku napięć wyższych niż 4,5 V w opisie kodu błędu wskazany jest „obwód dodatni”.
Aktywne czujniki mogą również wysyłać sygnał cyfrowy. Czujniki te często nie są zasilane przez ECU, ale poprzez zacisk 15. W większości przypadków mamy do czynienia z sygnałem PWM.
Poniższy obraz przedstawia część schematu, w której aktywny czujnik ma zewnętrzne zasilanie, a przewód sygnałowy jest podłączony poprzez styk 3 czujnika do styku 4 ECU. Profil napięcia czujnika w porównaniu do połączenia z masą mierzony jest za pomocą oscyloskopu.
Zakres jest ustawiony na 2 wolty i 5 milisekund na działkę. Cykl pracy wynosi 50%.
W akapicie: Błąd 9 – Przerwany przewód sygnałowy PWM omawiamy kroki prowadzące do postawienia właściwej diagnozy.
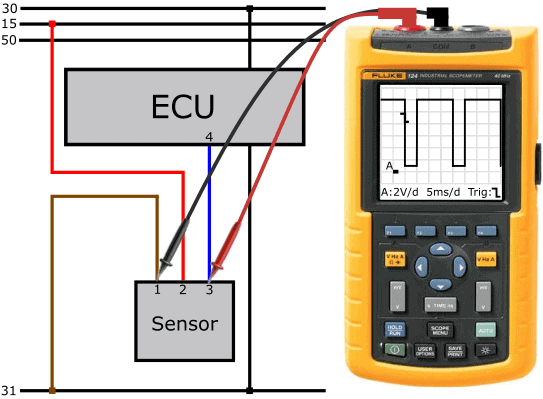
Diagnozowanie okablowania czujnika:
Przed przystąpieniem do diagnozowania czujników musimy zdawać sobie sprawę z rodzaju czujnika (pasywny, aktywny, inteligentny) oraz sposobu, w jaki czujnik wysyła swój sygnał do urządzenia sterującego (analogowy lub cyfrowy, w postaci AM (modulacja amplitudy) lub FM (Modulacja częstotliwości) Po zapoznaniu się ze schematem elektrycznym możemy oszacować, jakie napięcia będziemy mierzyć na okablowaniu.
W poniższych akapitach omówiono możliwe usterki, które mogą wystąpić w praktyce. Zamiast zaczynać od „reklamacji klienta”, od razu podaje się przyczynę; np.: przerwany przewód, zwarcie itp. Chodzi o zapoznanie się z technikami pomiarowymi. Bo jak postępować w przypadku awarii? A jakich pomiarów używasz, żeby znaleźć przyczynę?
Opanujesz techniki pomiarowe i ciekawi Cię obudowa? Następnie odwiedź stronę: Przypadek: awaria czujnika ciśnienia paliwa, zwarcie z plusem.
Błąd 1 – Przerwany przewód sygnałowy:
Jeśli przewód sygnałowy zostanie przerwany, napięcie sygnałowe z czujnika nie może dotrzeć do ECU. W tym dziale możesz przeczytać co mierzysz w tej sytuacji na połączeniach zarówno czujnika jak i ECU.
Wykonujemy następujące pomiary na aktywnym czujniku i uzyskujemy następujące odczyty:
- przewód zasilający (pin 1) względem masy czujnika (pin 2). 5 V;
- napięcie sygnałowe do masy 2,9 V.
Zasilanie i wygenerowany sygnał czujnika są prawidłowe. Jednak sygnał czujnika nie dociera do ECU z powodu przerwy.
Aby zmierzyć napięcie na wejściu ECU, używamy skrzynki zaciskowej.
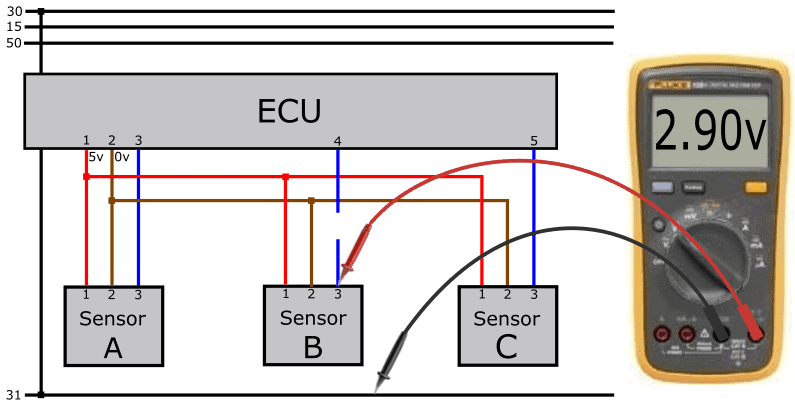
Za pomocą breakout boxa wykonujemy pomiar na pinie 4 ECU w porównaniu z masą (lub pinem 2 czujnika). Mierzymy napięcie 4,98 wolta.
Napięcie po stronie ECU jest zatem wyższe niż napięcie wysyłane przez czujnik. Obwód w ECU odpowiada za napięcie wyjściowe 4,98 wolta. Z jednej strony ma to związek ze sposobem przetwarzania sygnału, ale także z rozpoznawaniem zakłóceń.
ECU mierzy teraz własne napięcie wyjściowe i rozpoznaje je jako obwód dodatni ze względu na napięcie zasilania 4,98 V.
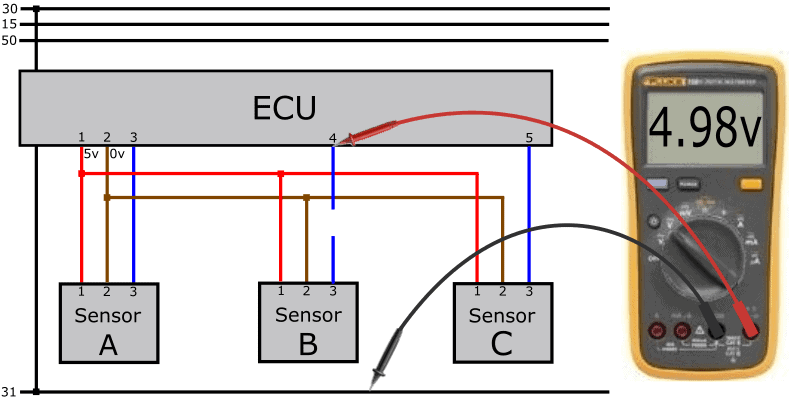
Następnie mierzymy różnicę napięcia na przewodzie między ECU a czujnikiem. W sytuacji bezproblemowej różnica napięć musi wynosić prawie 0 V.
W tym przypadku mierzymy różnicę napięcia 2,08 wolta; mianowicie 2,9 V (czujnik) w porównaniu do 4,98 V (ECU).
Napięcia mogą sprowadzić Cię na złą drogę.
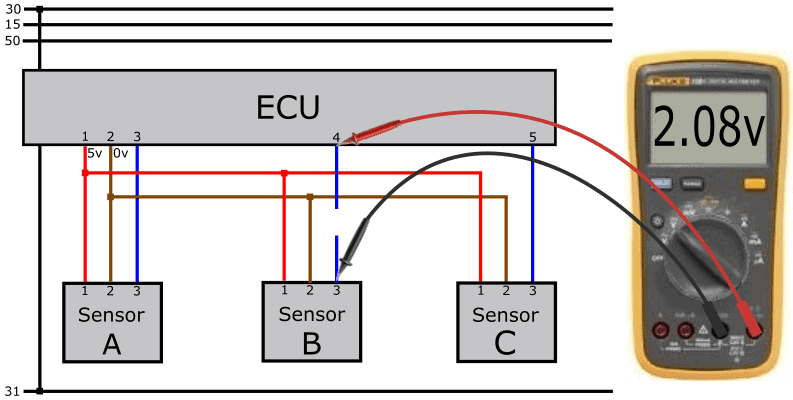
Wyjmij wtyczkę z czujnika. Gdyby nie było przerwy w przewodzie, zmierzylibyśmy 4,98 V z ECU na wyjętej wtyczce. Teraz mierzymy 4 V na pinie 4,98 ECU, ale 0 V na wyjętej wtyczce.
W tym przypadku możemy już stwierdzić, że przewód sygnałowy jest przerwany.
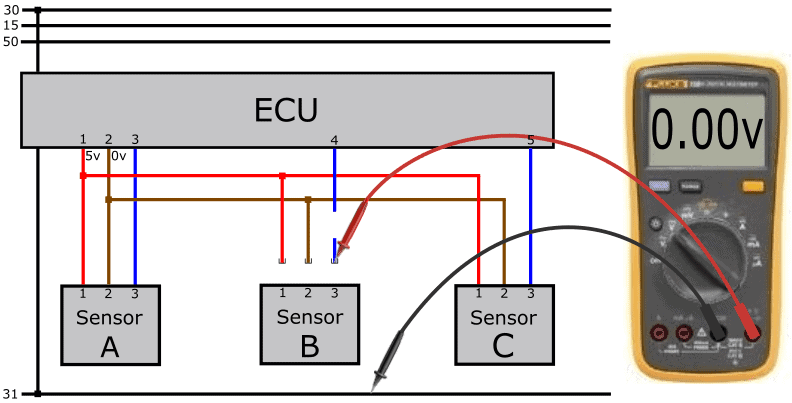
W przypadku przerwanego przewodu sygnałowego napięcie na wejściu sygnałowym ECU wynosi około 5.0 V. Na stronie: typy czujników i sygnały, w dziale: „zasilanie i przetwarzanie sygnału” można przeczytać, w jaki sposób ECU przetwarza sygnał z aktywnego czujnika. Dzięki tej wiedzy możesz lepiej zrozumieć, jak możemy sobie poradzić z zakłóceniami, takimi jak przerwany przewód sygnałowy.
W ECU generowane jest napięcie 4,98 V. Pomiędzy przewodem dodatnim (z 78L05) a przetwornikiem ADC znajduje się pewna liczba rezystorów, które podnoszą napięcie sygnałowe do 5 woltów, gdy przez złącze sygnałowe nie dochodzi napięcie. ADC mierzy to napięcie i przetwarza je na sygnał cyfrowy. ECU otrzymuje zatem sygnał o napięciu poza zakresem i generuje kod błędu.
Uwaga: przy podobnej usterce napięcie nie zawsze wynosi dokładnie 4,98 lub 5,0 woltów!
Na stronie: Przypadek: usterka czujnika ciśnienia paliwa – zwarcie z plusem usterka jest opisana w przypadku odchylenia tej wartości napięcia.
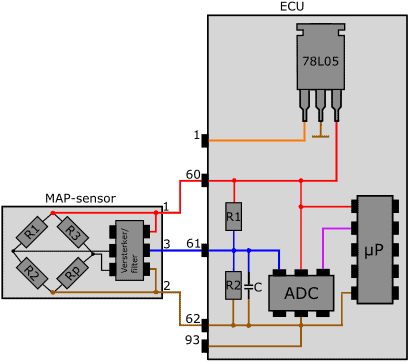
Błąd 2 – Przerwany przewód zasilający:
Pomiędzy złączem przewodu dodatniego pomiędzy trzema czujnikami a wtyczką czujnika występuje przerwa. Napięcie zasilania 5 V nie może teraz dotrzeć do czujnika. Czujnik nie może funkcjonować bez napięcia zasilania i masy.
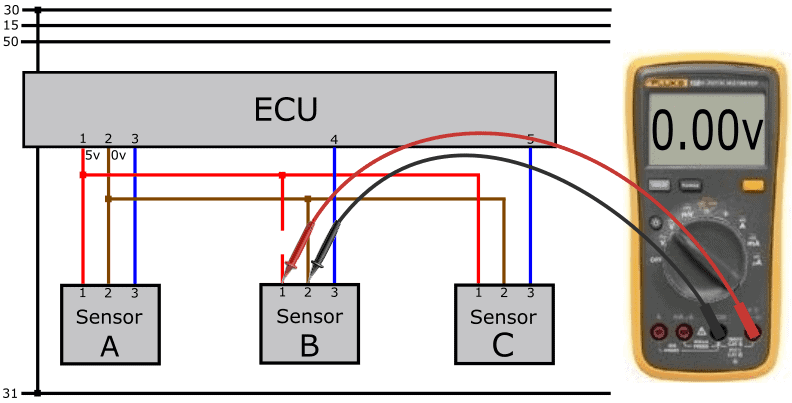
Ponieważ w poprzednim pomiarze zmierzyliśmy zasilanie i masę na wtyczce, pozostaje nam jeszcze wykluczyć, który z dwóch przewodów ma problem. Dlatego mierzymy plus na innym czujniku w tym samym obwodzie dodatnim. Można to oczywiście zrobić również w ECU, jeśli dostępna jest skrzynka rozdzielcza.
Mierzymy 1 woltów na pinie 5 czujnika A w porównaniu z masą czujnika B. Oznacza to, że masa czujnika B jest prawidłowa.
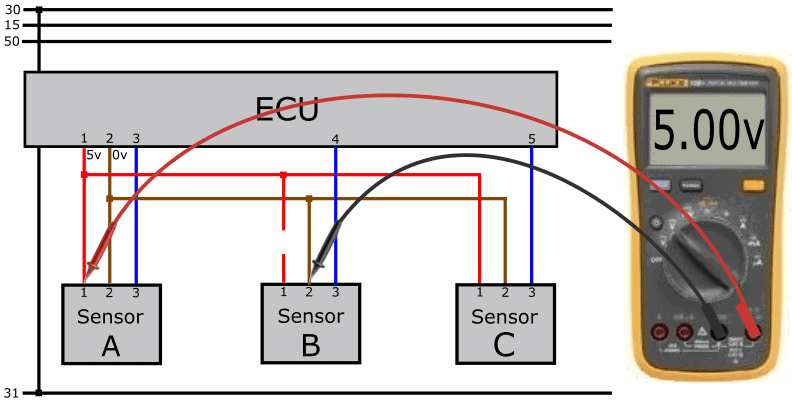
Gdy przez elektronikę aktywnego czujnika nie przepływa prąd z powodu przerwanego przewodu zasilającego, mierzymy napięcie na wejściu sygnałowym ECU wynoszące 4,98 V. Mamy podobną sytuację jak w przypadku przerwanego przewodu sygnałowego: wewnętrzne rezystory w ECU podnoszą napięcie sygnału: do 4,98 V. Ponieważ w tym przypadku przewód sygnałowy jest w porządku, mierzymy również napięcie na wtyczce czujnika wynoszące 4,98 V.
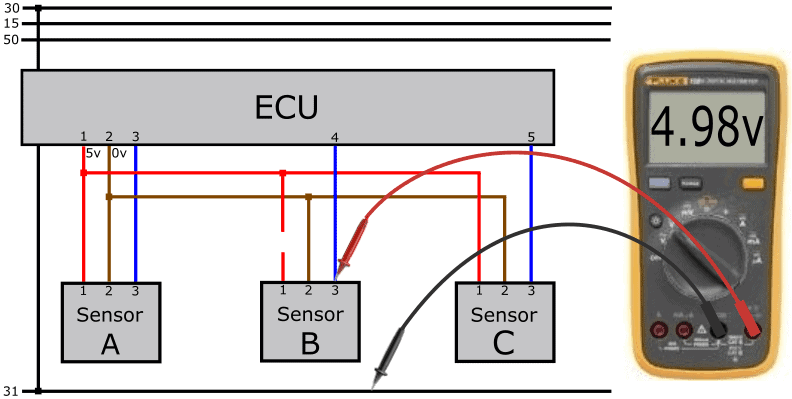
W przypadkach, gdy napięcie wynosi nieco powyżej 5,0 V, napięcie stabilizatora napięcia mogło wzrosnąć. Patrz akapit: „Zasilanie i przetwarzanie sygnałów” na stronie: „typy czujników i sygnały".
Błąd 3 – Przerwany przewód uziemiający:
W tym przypadku nie plus, ale przewód uziemiający jest przerwany. Do czujnika dostarczane jest napięcie zasilania 5 woltów, ale ponieważ dokonujemy pomiaru w przerwanym przewodzie, woltomierz nie ma napięcia odniesienia i wskazuje 0 woltów.
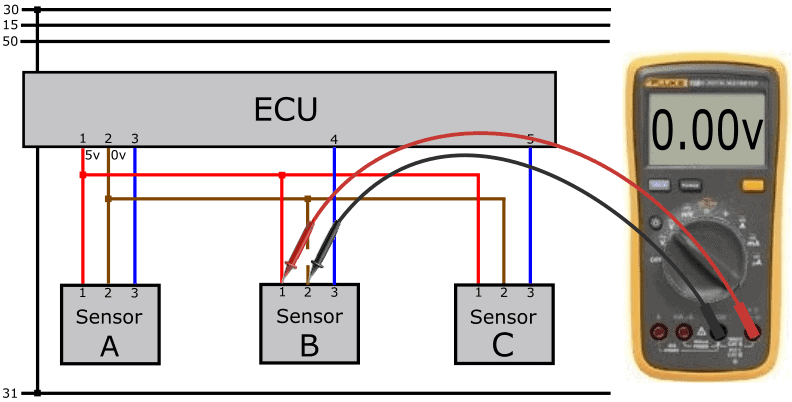
Po przesunięciu ujemnego trzpienia pomiarowego do masy nadwozia lub akumulatora woltomierz rzeczywiście wskazuje 5 woltów.
Kiedy podłączamy ujemny pin pomiarowy do złącza masy czujników A i C, musimy również zmierzyć różnicę 5 woltów. Gdybyśmy zmierzyli 2 V na pinie 5 czujnika A, ale nie 5 V na czujniku C, wówczas przerwa wystąpiłaby w przewodzie pomiędzy czujnikiem A i B, tj. pomiędzy dwoma pierwszymi węzłami.
Podobnie jak w przypadku przerwanego sygnału i przewodu dodatniego, teraz mierzymy napięcie na przewodzie sygnałowym wynoszące 4,98 V.
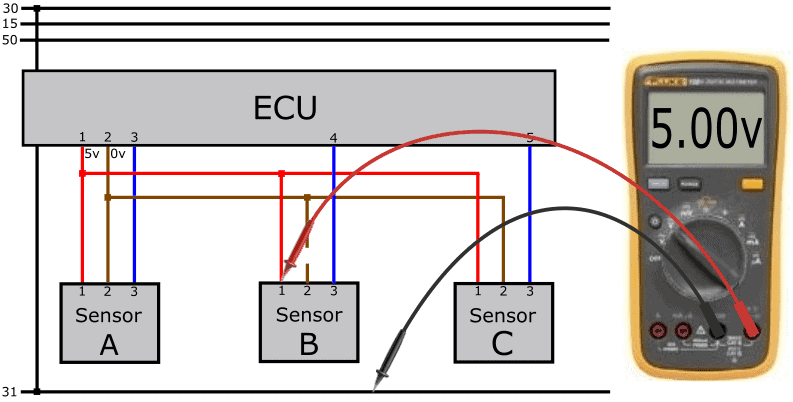
Błąd 4 – Opór przejścia:
W poprzednim akapicie omówiono już utratę napięcia spowodowaną rezystancją przejściową. Na następnym schemacie widzimy rezystor w przewodzie zasilającym. Kiedy prąd przepływa przez przewód zasilający, rezystancja przejściowa zapewnia (prawdopodobnie) zbyt niskie napięcie na pinie 1 wtyczki B. Mierzymy 4 wolty zamiast 5 woltów, które spodziewaliśmy się zmierzyć.
Zapisany opis DTC w tym przypadku może brzmieć: „przekroczenie dolnej wartości granicznej sygnału”.
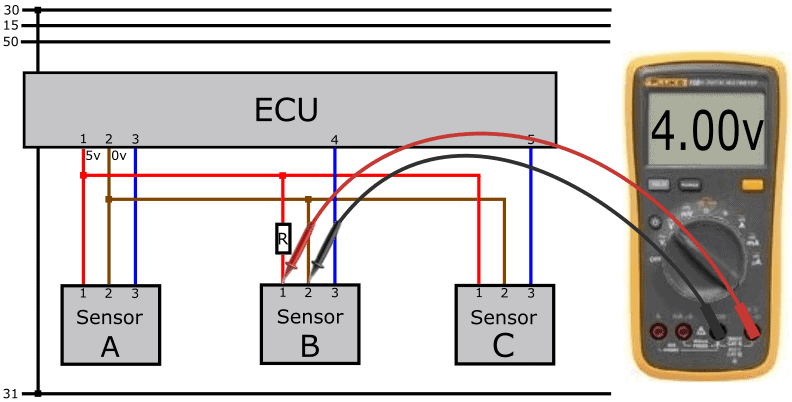
Jeśli zmierzymy styk 1 złącza B względem styku 1 złącza C, powinniśmy uzyskać różnicę (5-5) = 0 woltów. Teraz widzimy różnicę 1 wolta.
Ponieważ utrata napięcia występuje tylko w przewodzie czujnika B, a nie czujnika C, możemy założyć, że przewód pomiędzy złączem przewodu poziomego na schemacie a wtyczką jest niesprawny.
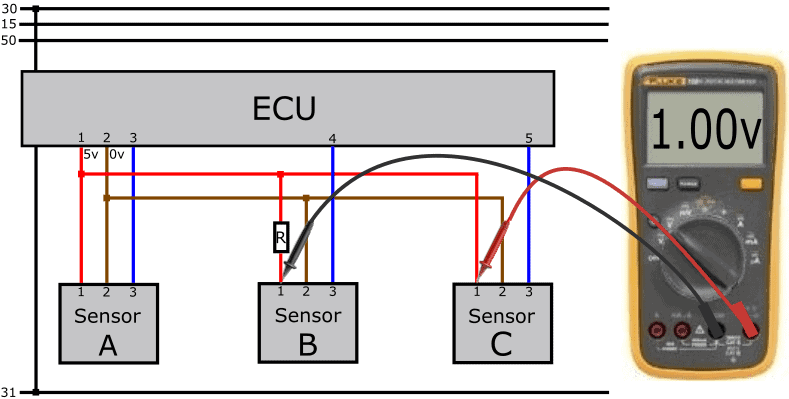
Błąd 5 – Zwarcie pomiędzy przewodem zasilającym i sygnałowym:
Możliwą usterką w okablowaniu jest zwarcie. Ze zwarciami spotykamy się w następujących sytuacjach:
- pomiędzy przewodem zasilającym a przewodem sygnałowym (zwarcie dodatnie);
- pomiędzy przewodem uziemiającym a przewodem sygnałowym (zwarcie do masy);
- pomiędzy jednym z trzech przewodów między sobą i/lub z karoserią (połączenie masy);
Na tym schemacie widzimy zwarcie pomiędzy przewodem sygnałowym a przewodem dodatnim (obwód dodatni). Mierzymy napięcie sygnału równe napięciu zasilania 5 woltów.
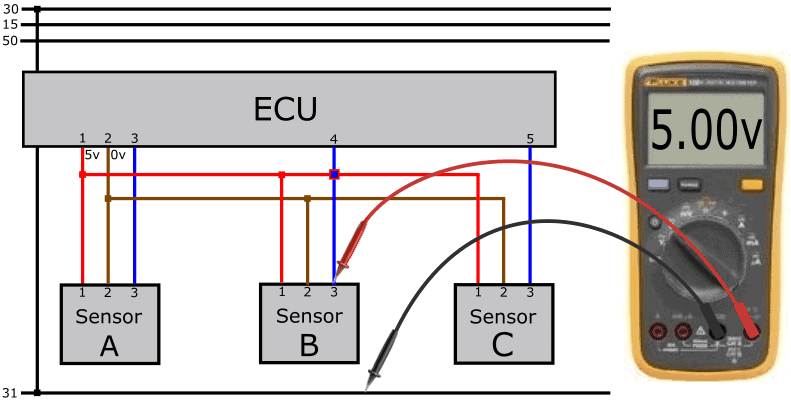
Podczas pomiaru napięcia 5 woltów na pinie 3 czujnika i pinie 4 ECU, problem może mieć podłoże wewnętrzne w czujniku. Aby to wykluczyć, sprawdzamy omomierzem, czy nie ma zwarcia w okablowaniu. Aby uzyskać bezpieczny i poprawny pomiar wyłączamy ECU, demontujemy wtyczkę ECU oraz demontujemy wtyczki czujników które są podłączone do węzłów. Ponieważ doszło do zwarcia, mierzymy połączenie omomierzem.
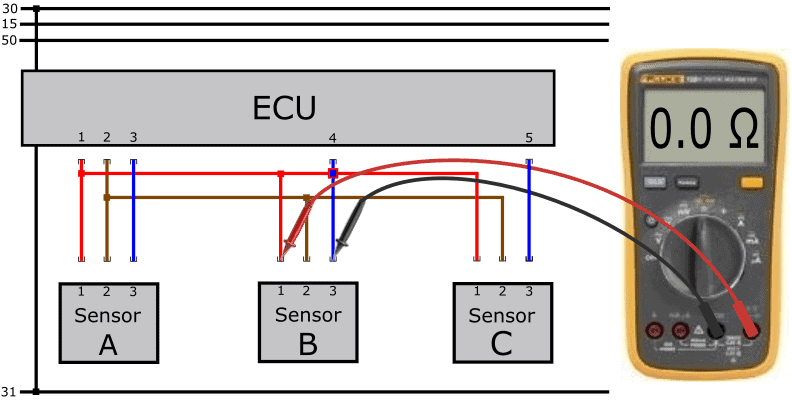
W tym przypadku jest to 0,0 oma, ponieważ przewody łączą się ze sobą. W rzeczywistości wartość ta może być o kilka omów wyższa. Gdy nie ma zwarcia, omomierz wskazuje OL lub 1. (nieskończenie wysoka rezystancja), ponieważ pomiędzy przewodami a sondami pomiarowymi nie ma połączenia elektrycznego.
Błąd 6 – Zwarcie pomiędzy przewodem zasilającym i uziemiającym:
W przypadku zwarcia pomiędzy przewodem zasilającym a masowym ECU wyłącza zasilanie pinu 1. Wszystkie czujniki zasilane przez pin 1 nie będą już działać. W związku z tym kody usterek będą zapisywane w wielu czujnikach.
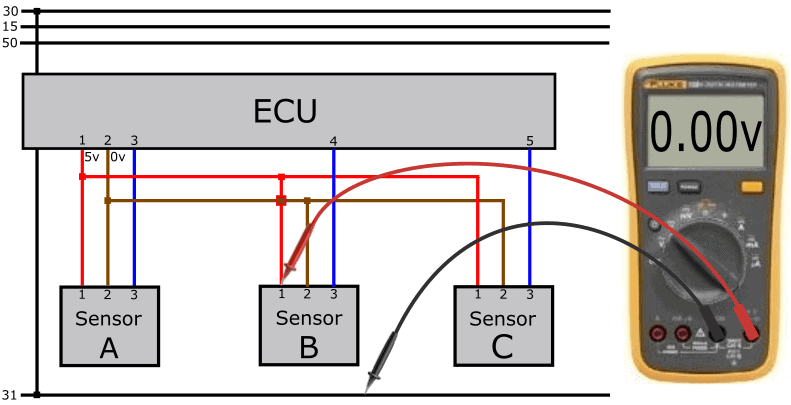
W tym przypadku mierzymy również napięcie 5,0 na przewodzie sygnałowym, które wychodzi z ECU.
Aby wykluczyć czy nie mamy do czynienia z zwarciem demontujemy złącza zarówno ECU jak i wszystkich czujników w danym obwodzie jak w poprzednim akapicie. Za pomocą omomierza zmierz rezystancję między przewodem czerwonym i brązowym.
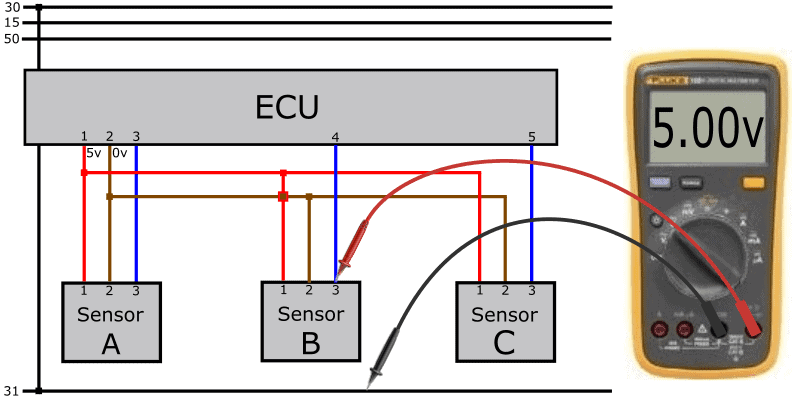
Błąd 7 – Zwarcie w czujniku C:
Mierząc napięcie zasilania względem masy, ponownie mierzymy 0 woltów. W poprzedniej usterce mieliśmy zwarcie w okablowaniu. W tym przypadku zwarcie ma miejsce wewnątrz czujnika.
Wyciągamy po kolei wtyczki czujników widocznych na schemacie. Po odłączeniu wtyczki od czujnika C nie mamy już zwarcia i ECU ponownie zasili przewód dodatni napięciem 5 V. W niektórych wersjach dzieje się to automatycznie, w innych wymagana jest wymiana zacisku.

Błąd 8 – Brak napięcia zasilania z powodu uszkodzonego ECU:
W niektórych przypadkach może się zdarzyć, że przyczyną braku napięcia zasilania jest ECU. Wewnętrznie obwód jest uszkodzony i napięcie 5 V nie jest dostarczane.
ECU jest często błędnie zgłaszane jako uszkodzone. W większości przypadków istnieje inna przyczyna. Dlatego w pierwszej kolejności należy sprawdzić możliwe przerwy i zwarcia w okablowaniu oraz podłączonych czujnikach. Aby wykluczyć, czy przyczyną jest wewnętrzna usterka ECU, sprawdzamy wszystkie połączenia masowe ECU.
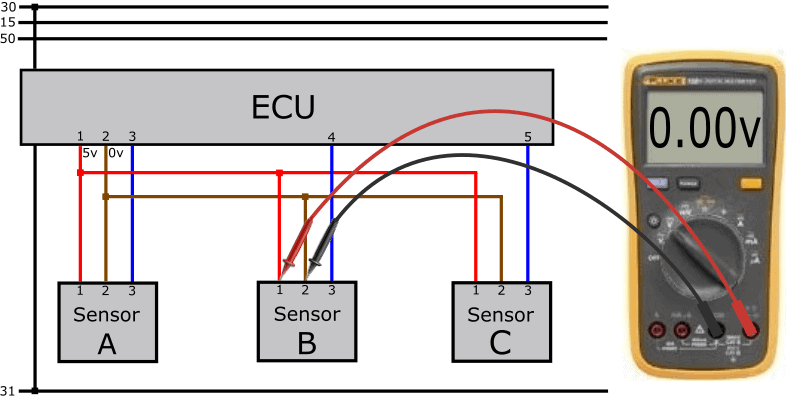
Dzięki rozbudowanemu systemowi zarządzania silnikiem widzimy wiele obwodów w ECU, każdy z własnym przewodem uziemiającym. Czasami w jednej wtyczce znajdujemy aż osiem przewodów uziemiających. W momencie, gdy jeden styk we wtyczce ma słaby styk lub jeden przewód uziemiający w wiązce przewodów ulegnie przerwaniu, obwód ten ulega awarii. Dlatego najlepiej pod obciążeniem zmierzyć próbnikiem (dodatni na akumulatorze, ujemny na każdym złączu masy we wtyczce ECU), czy masa jest OK. Próbnik musi palić się jednakowo jasno na każdym przewodzie uziemiającym. Czy lampa nie świeci przy jednym połączeniu z masą? Wtedy być może zidentyfikowałeś przyczynę i ECU nie jest uszkodzone.
Błąd 9 – Przerwany przewód sygnałowy PWM:
Do tej pory mówiliśmy o napięciach analogowych, które można zmierzyć za pomocą multimetru. Jeśli jest to sygnał cyfrowy, multimetr już nie wystarczy. Następnie korzystamy z oscyloskopu. Poniższy tekst dotyczy oscyloskopu przedstawionego na poniższych ilustracjach. Tutaj widzimy Fluke 124 ze zmodyfikowanym wyświetlaczem.
Powodem wykonania tego pomiaru jest opis usterki, który można przetłumaczyć z kodu usterki. W opisie czytamy: „Przerwany sygnał czujnika”.
Obraz oscyloskopu pokazuje linię stałego napięcia o wartości 0 woltów. Oznacza to, że pomiędzy sondami pomiarowymi nie ma różnicy napięć. Czy zmierzyłeś, czy przewody dodatni i uziemiający czujnika są dobre (pin 2 w porównaniu do 1), w tym przypadku około 13 V, coś jest nie tak z przewodem sygnałowym. Należy pamiętać, że czujnik może przesyłać informacje na dwa sposoby:
- Czujnik wysyła napięcie dodatnie do ECU (zwykle napięcie analogowe;
- ECU wysyła napięcie, które co pewien czas jest przykładane do masy przez czujnik (za pomocą PWM; sygnał cyfrowy).
W przykładzie napięcie sygnału po stronie czujnika wynosi 0 V, dlatego przyjmujemy metodę 2.
Ponieważ przewód sygnałowy jest przerwany, czujnik nie otrzymuje zasilania z ECU.
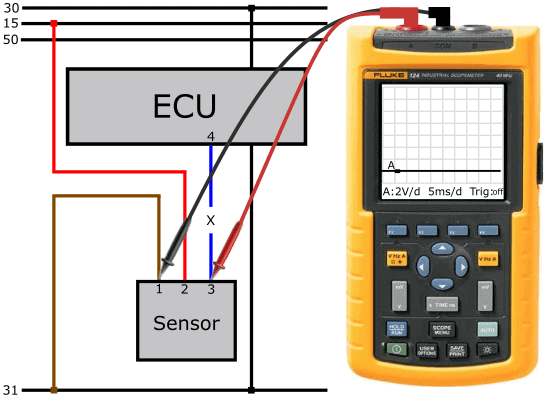
Mierzymy pin 4 ECU względem pinu 1 wtyczki. Napięcie wynosi 12 wolt. Na podstawie tych pomiarów ustaliliśmy, że wejście czujnika ECU jest prawidłowe.
ECU najwyraźniej wysyła stałe napięcie, ale nie dochodzi do czujnika. Dlatego czujnik nie ma napięcia, które można by połączyć z masą.
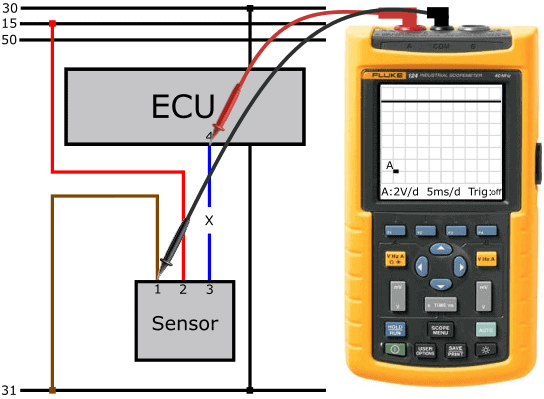
Podczas kolejnego pomiaru łączymy kołki pomiarowe po obu stronach przewodu sygnałowego. Dzięki temu określamy różnicę napięcia w stanie aktywnym na przewodzie. W sytuacji bezproblemowej napięcie musi wynosić 0 V. Jednak w aktywnej części napięcia bloku widzimy napięcie 12 woltów. Kiedy otrzymamy pełny Jeśli mierzymy napięcie zasilania w maksymalnej dodatniej części napięcia bloku, to w większości przypadków mamy do czynienia z przerwanym przewodem. Podobnie jest teraz: napięcie wyjściowe ECU (pin 4 w porównaniu do masy) wynosi 12 woltów.
Ponadto widzimy w dolnej części napięcie bloku odchylenie: dNapięcie na linii spada do około 5 woltów, pozostaje stałe przez 10 milisekund z tętnieniem, a następnie ponownie wzrasta do 12 woltów. Ponieważ oscyloskop jest teraz połączony szeregowo pomiędzy rezystorem podciągającym w ECU a rezystorem podciągającym w czujniku, tworzone jest połączenie szeregowe. Luneta posiada dużą rezystancję wewnętrzną, która wpływa na sygnał. Z tego powodu sygnał nie jest użyteczny.
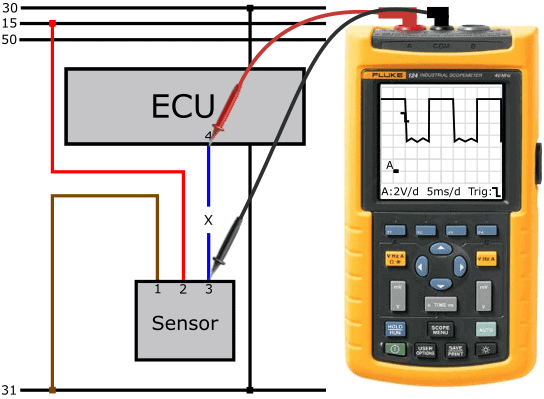
Chociaż pomiar napięcia pod obciążeniem jest wystarczający do postawienia dobrej diagnozy, nie zaszkodzi zastosować pomiar rezystancji, aby wykazać, że w przewodzie faktycznie występuje przerwa. W tym przypadku mierzymy nieskończenie dużą rezystancję (OL lub 1.)
Po naprawie przewodu sygnałowego ponownie mierzymy napięcie sygnału względem masy. Uwaga: mierzymy tutaj względem masy, więc „aktywna” część czujnika w sygnale PWM jest teraz odwrócona…
Na tym obrazie zakresu widzimy, że:
- napięcie wynosi maksymalnie 12 woltów. Tutaj czujnik nie jest aktywny: napięcie na przewodzie sygnałowym nie jest doprowadzone do masy.
- napięcie spada do 1 wolta. Tutaj czujnik jest aktywny: czujnik przykłada napięcie z ECU do masy poprzez elektronikę czujnika.
Czujnik zawiera obwód elektroniczny, który nadal zużywa 1 wolt. Napięcie to pozwala również ECU rozpoznać, że czujnik włącza się prawidłowo. ECU może określić na podstawie poziomów napięcia, czy czujnik działa prawidłowo:
- napięcie w dłuższym okresie czasu jest równe lub wyższe niż 12 woltów:
ECU rozpoznaje przerwę lub obwód dodatni; - napięcie niższe niż 1 V: ECU rozpoznaje zwarcie do masy.
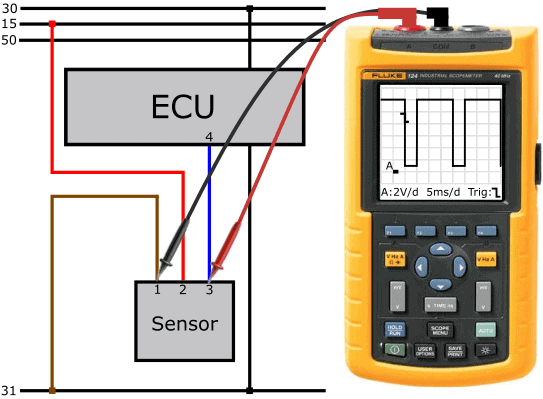
Naprawa przerwanego przewodu dodatniego:
Spośród pięciu usterek opisanych w poprzednich akapitach, w większości przypadków można je stosunkowo łatwo usunąć.
Przetnij przewód z oporem przerywającym lub przejściowym możliwie najkrótszym w wiązce przewodów.
Jeśli to konieczne, zastosuj izolację. Znajdź najbliższy czujnik podłączony do tego samego obwodu. W przypadku aktywnych czujników można to łatwo znaleźć na schemacie elektrycznym. Na schemacie najbliższy czujnik to C. Starannie przylutuj nowy przewód do przewodu dodatniego.
Zawsze pracuj z rurką termokurczliwą, aby zapobiec przyszłym problemom wynikającym z przenikania wilgoci. Jeśli zamkniesz to taśmą izolacyjną, w najbliższej przyszłości pojawią się nowe problemy!
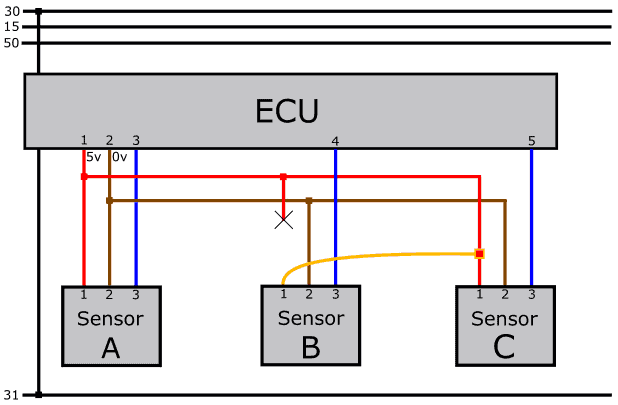