Przedmioty:
- Określ i zainstaluj siłowniki dla układu zarządzania silnikiem
- Wtryskiwacze paliwa
- Wybór odpowiednich wtryskiwaczy
- Montaż wtryskiwaczy w kolektorze dolotowym
- Zapalenie
- Przygotowanie przy użyciu konwencjonalnego zapłonu
- Cewka zapłonowa układu sterowania silnikiem
- Nagromadzenie prądu w cewce pierwotnej
- Wyprzedzenie zapłonu
- korpus przepustnicy
- Konfiguracja testowa silnika krokowego z symulatorem
- Ustawienia silnika krokowego
- Obwód pompy paliwa
- Zakończenie prac mechanicznych
Określanie i instalowanie siłowników dla układu zarządzania silnikiem:
Elementy wykonawcze, które będą sterowane za pomocą MegaSquirt, to wtryskiwacze, cewka zapłonowa, pompa paliwa i silnik krokowy odpowiedzialny za prędkość biegu jałowego. W tym rozdziale opisano proces testowania i montażu siłowników na bloku silnika oraz dokonany wybór.
Wtryskiwacze paliwa:
MegaSquirt steruje wtryskiwaczami. Wtryskiwacze są podłączone do masy. W przypadku elementu podłączonego do uziemienia występuje napięcie zasilania, ale prąd płynie tylko wtedy, gdy masa jest włączona. W takim przypadku wtryskiwacz będzie wstrzykiwał tylko wtedy, gdy ECU MegaSquirt zostanie przełączone na masę. Gdy tylko aktywacja zostanie zatrzymana, wtryskiwacz przestaje wstrzykiwać. Ilość wtryskiwanego paliwa określa się na podstawie tabeli VE i tabeli AFR.
MOS FET włącza i wyłącza wtryskiwacz, powodując wtrysk paliwa. Ilość paliwa określona przez MegaSquirt zależy od kilku czynników:
- Prawo gazu doskonałego, które wiąże ilość powietrza z jego ciśnieniem, objętością i temperaturą;
- Wartości mierzone przez czujniki w bloku silnika: ciśnienie w kolektorze dolotowym (MAP sensor), temperatura płynu chłodzącego i powietrza dolotowego, prędkość obrotowa wału korbowego oraz dane z czujnika położenia przepustnicy;
• Parametry regulacji: wymagana ilość paliwa, stopień napełnienia (VE), czas otwarcia wtryskiwaczy oraz wzbogacenie w określonych warunkach.
Czas wtrysku powinien być jak najdłuższy na biegu jałowym silnika, aby uzyskać odpowiednią dawkę paliwa. Dlatego w silniku można zastosować nie byle jaki wtryskiwacz. Należy porównać właściwości różnych typów wtryskiwaczy i obliczenia muszą dać wgląd w wymaganą ilość paliwa dla danego silnika. Do wyboru były także wtryskiwacze o wysokiej i niskiej impedancji. Wtryskiwacze niskoomowe nadają się do silników gdzie wymagane jest bardzo szybkie otwarcie iglicy wtryskiwacza. Typowa rezystancja wynosi 4 omy. Wadą tych wtryskiwaczy jest duży prąd. Wytwarzanie ciepła w MegaSquirt jest niepożądane. Istnieje możliwość zastosowania wtryskiwaczy o niskiej impedancji poprzez zamontowanie specjalnych tranzystorów IGBT na płycie przewodzącej ciepło na obudowie MegaSquirt. Zdecydowano się na zastosowanie wtryskiwaczy o wysokiej impedancji. Wytwarza się mniej ciepła i te IGBT nie są używane.
Rozmiar przejścia (przepływ) jest bardzo ważny dla określenia prawidłowej ilości wtrysku, a tym samym kontroli. Jeśli dobierzemy zbyt duże wtryskiwacze, czas wtrysku na biegu jałowym będzie na tyle krótki, że silnik może pracować nieregularnie. Ilość wtrysku musi być wystarczająca do wtryskiwania całego paliwa w dostępnym czasie. Ilość wtrysku jest wskazywana jako czas wtrysku w milisekundach. Przy wysokich obrotach silnika zakłada się duże obciążenie. Dzieje się tak przy MAP wynoszącym 100 kPa. Wymagany przepływ wtryskiwaczy można obliczyć na podstawie właściwości silnika. Przepływ wtryskiwacza wskazuje, ile mililitrów paliwa jest wtryskiwanych na minutę.
Wybór odpowiednich wtryskiwaczy:
W ramach projektu udostępniono wtryskiwacze trzech różnych typów. Badania wykazały, który typ wtryskiwacza był najodpowiedniejszy do zastosowania w tym projekcie.
Każdy typ wtryskiwacza ma inny przepływ; wydajność po jednej minucie wtrysku różni się w zależności od rodzaju. Przed badaniem wtryskiwacze zostały poddane czyszczeniu w kąpieli ultradźwiękowej. Dzięki tej metodzie czyszczenia wtryskiwacz jest czyszczony od wewnątrz i na zewnątrz za pomocą wibracji ultradźwiękowych i specjalnego płynu testowego, tak aby wszelkie pozostałości starego brudu nie miały wpływu na pomiar przepływu ani wzór wtrysku. Podczas czyszczenia ultradźwiękowego wtryskiwacze były w sposób ciągły otwierane i zamykane oraz sprawdzano wzór wtrysku każdego wtryskiwacza; to była piękna mgła. Podczas zamykania nie zaobserwowano żadnych nieprawidłowości, takich jak tworzenie się kropli lub odchylony strumień. Po czyszczeniu ultradźwiękowym i testowaniu oringi zostały wymienione, aby zapewnić dobre uszczelnienie po zamontowaniu w kolektorze dolotowym.
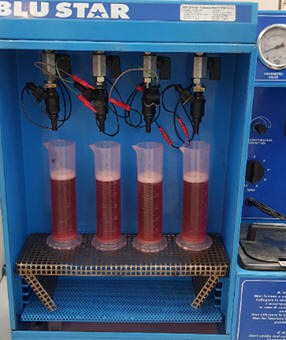
Korzystając z układu testowego (patrz zdjęcie powyżej), wtryskiwacze mogą wtryskiwać do wielu miarki, dzięki czemu po określonym czasie można odczytać ilość wtryskiwanego paliwa. Sterowanie wtryskiwaczami przy ciśnieniu roboczym 3 bar pozwala kontrolować ilość wtryskiwanego paliwa. Ciśnienie paliwa na przewodzie zasilającym (szynie) musi wynosić 3 bary, a igła wtryskiwacza musi być uruchomiona na 30 lub 60 sekund przy cyklu pracy 100%. Po włączeniu wtryskiwaczy na 30 sekund można było wprowadzić następujące dane:
Typ 1: 120 ml
Typ 2: 200 ml
Typ 3: 250 ml
Stosowany będzie tylko jeden typ wtryskiwacza. Wielkość wtryskiwacza określa się za pomocą poniższego wzoru:

Rozmiar wtryskiwacza określa się na podstawie mocy efektywnej (Pe) dostarczanej przy określonej prędkości, zużycia paliwa podczas przerwy (BSFC), liczby wtryskiwaczy (n wtryskiwaczy) i maksymalnego cyklu pracy, z jakim sterowane są wtryskiwacze. Całość mnoży się przez 10.5, aby przeliczyć funty na godzinę (lb/h) na ml/min.
Odpowiedź na obliczenia wskazuje, który wtryskiwacz jest odpowiedni dla tej konfiguracji silnika. Nie stanowi to problemu, jeśli odchylenie od obliczonej wartości jest mniejsze niż 20 ml. Różnica ta jest kompensowana poprzez dostosowanie oprogramowania w MegaSquirt. Poniższa tabela zawiera przegląd danych używanych we wzorach:
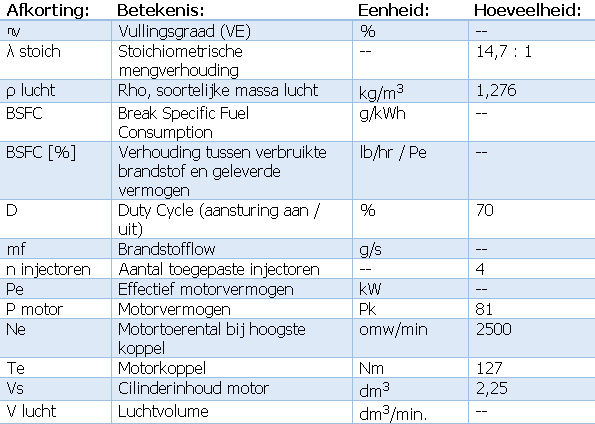
Pierwszym krokiem jest określenie dawki paliwa wtryskiwanego przy danym momencie obrotowym. Na każde dwa obroty wału korbowego zasysana jest pewna ilość powietrza. Stopień napełnienia jest najwyższy przy prędkości obrotowej. Ze względu na właściwości silnika (m.in. na zachodzenie zaworów) przy tej prędkości obrotowej silnik najlepiej się wypełnia, a jego sprawność jest najwyższa. Szacuje się, że stopień wypełnienia będzie wynosić około 70%. Formuła 4 oblicza objętość powietrza znajdującego się w danym momencie w silniku.
We wzorze 5 ilość wtryskiwanego paliwa obliczana jest na podstawie objętości znajdującego się w nim powietrza. Moc silnika osiągniętą przy prędkości obrotowej momentu obrotowego oblicza się ze wzoru 6. Stosunek ilości wtryskiwanego paliwa do mocy wskazuje BSFC we wzorach 7 i 8.
Rzeczywisty BSFC mnoży się przez 6 we wzorze 3600 w celu przeliczenia na kWh. BSFC silnika benzynowego często mieści się w przedziale od 250 do 345 g/kWh. Im niższa wartość, tym bardziej wydajny jest silnik. Wzór 8 wskazuje zależność pomiędzy przepływem paliwa w funtach/godzinę i efektywną mocą silnika. Procent ten jest zawarty we wzorze 9.



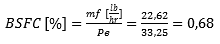

Odpowiedź na wzór 9 wyjaśniła, że do zastosowania w silniku nadają się wtryskiwacze o przepływie 200 ml/min. Różnica 7 ml jest pomijalna, ponieważ jest ona kompensowana w oprogramowaniu podczas wypełniania tabeli VE.
Montaż wtryskiwaczy w kolektorze dolotowym:
Elektronicznie sterowany układ wtryskowy umożliwia demontaż gaźnika, który jest częścią klasycznej konfiguracji. W związku z tym gaźnik zostaje zastąpiony korpusem przepustnicy (do zasilania powietrzem) i czterema oddzielnymi wtryskiwaczami paliwa. Kolektor dolotowy został zachowany i zmodyfikowany, aby umożliwić konwersję na system zarządzania silnikiem. Wtrysk paliwa odbywa się w kolektorze dolotowym. Zdecydowano o zamontowaniu wtryskiwaczy jak najbliżej zaworu dolotowego. W większości przypadków producenci silników samochodowych decydują się na montaż zaworu dolotowego pod kątem w kolektorze dolotowym. Paliwo jest wtryskiwane na zawór wlotowy. Jednak dla obecnego projektu wybrano układ, w którym wtryskiwacze są umieszczone pod kątem 45 stopni w stosunku do kanałów powietrznych w kolektorze.
Kolektor dolotowy wykonany jest z odlewu aluminiowego. Zdecydowano się na zamontowanie aluminiowych tulei do kolektora. Ręczna obróbka do odpowiedniego rozmiaru nie wchodziła w grę, ponieważ tuleje musiały mieć inne wymiary niż standardowy rozmiar wiertła. Oznaczało to, że outsourcing samochodów dostawczych musiał zostać zlecony firmie dysponującej odpowiednim sprzętem. Tuleje można następnie przymocować do kolektora za pomocą spawania TIG. Zdecydowano się na montaż wtryskiwaczy w pozycji pionowej, a nie pod kątem, z następujących powodów:
- Proces montażu: Łatwiej jest ustawić samochody dostawcze w prostym, poziomym układzie. Spawanie vanów z kolektorem jest łatwiejsze, bo teraz łatwiej jest spawać dookoła niż w sytuacji, gdy van stoi pod kątem.
- Obróbka końcowa: Podczas spawania tuleje stają się nieco owalne. Odkształcenie jest spowodowane ciepłem wydzielającym się podczas procesu spawania. Uwzględniono to, zmniejszając wewnętrzną średnicę tulei niż zewnętrzną średnicę wtryskiwaczy. Wykańczanie (rozwiercanie) jest mniej ryzykowne: gdy tulejki zostaną zaokrąglone od wewnątrz, średnica jest optymalna dla wtryskiwaczy i zapewniona jest szczelność dzięki oringom. Wysokość samochodów dostawczych jest ważna; wtryskiwacz nie może być umieszczony zbyt głęboko w kolektorze. Końcówka wtryskiwacza nie może utrudniać przepływu powietrza. Z informacji ze źródła: (Banish, Engine Management, zaawansowany tuning, 2007) zdecydowano się zamontować wtryskiwacze tak głęboko w kolektorze, aby końcówki znalazły się dokładnie w otworach kolektora; przepływ powietrza nie jest utrudniony.
- Wtrysk paliwa: Ponieważ wymieszanie mgły paliwowej z powietrzem jest optymalne przed otwarciem zaworu dolotowego, nie ma większego znaczenia, czy wtryskiwacz wtryskuje dokładnie przy zaworze dolotowym, czy tuż przed nim w kolektorze dolotowym.
Przy wtrysku jednoczesnym, wtrysk następuje przy każdym obrocie wału korbowego (360°). Cztery wtryskiwacze wtryskują jednocześnie. Oznacza to, że paliwo wtryskiwane jest do układu dolotowego również wtedy, gdy zawór dolotowy nie jest otwarty. Po pewnym czasie zawór wlotowy otwiera się, a paliwo nadal dostaje się do cylindra.
Tuleje są specjalnie przycinane na wymiar na tokarce. Średnica wewnętrzna jest nieco mniejsza niż średnica zewnętrzna wtryskiwacza; Ponieważ odkształcenie ma miejsce podczas procesu spawania, musi istnieć możliwość usunięcia materiału podczas obróbki końcowej za pomocą rozwiercania. Oznacza to, że średnica nieznacznie wzrasta, ponieważ materiał jest szlifowany. Średnica nie powinna być zbyt duża, gdyż wtedy istnieje ryzyko, że gumowy oring na wtryskiwaczu nie będzie już w stanie wystarczająco dobrze uszczelnić. Dobra pieczęć jest bardzo ważna; wyciek powietrza obok wtryskiwacza skutkuje niższym podciśnieniem w kolektorze dolotowym.
Zmierzone podciśnienie nie odpowiada już obliczonemu podciśnieniu. Ma to wpływ na wtrysk, który ustala się na podstawie tabeli VE. Podciśnienie odgrywa w tym główną rolę. Funkcje i ustawienia tabeli VE opisano w następnym rozdziale.
Na spodzie tulei wykonano skośną krawędź, dzięki czemu kształty odpowiadają kształtom kolektora dolotowego. Furgonetka musi być wówczas ustawiona możliwie pionowo. Zdjęcie poniżej przedstawia kolektor dolotowy wraz z pochłaniaczem w trakcie montażu. Tuleja jest klejona z jednej strony, dzięki czemu wyraźnie widać wpływ zgrzewania na materiał. Nie było jasne, czy aluminium kolektora zawierało zbyt duże zanieczyszczenia, które utrudniałyby spawanie. To okazało się być w porządku. Aby zapobiec przesuwaniu się tulei podczas spawania, w kolektorze wywiercono wcześniej otwory, a tuleje utrzymywano we właściwej pozycji za pomocą specjalnie wykonanego szablonu. W ten sposób cztery tuleje są zespawane dookoła. Końcowa kontrola wykazała, że połączenia pomiędzy tulejami i kolektorem są szczelne.
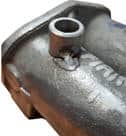
Połączenie pomiędzy wtryskiwaczami jest zwykle utworzone przez solidną szynę wtryskiwaczy. Ta rura z przyłączami, często wykonana ze stopu aluminium, jest wykonywana na wymiar przez producenta. Wykorzystany w projekcie silnik Land Rovera ma dwa wtryskiwacze tuż obok siebie, jednak odstęp pomiędzy parami wtryskiwaczy jest dość duży. Wymiary szyny paliwowej i przestrzeń pomiędzy kanałami powietrza w kolektorze dolotowym nie pasowały. Dlatego szyna wymagała regulacji.
Skracanie niektórych części i wydłużanie innych poprzez lutowanie jest bardzo trudne; zanieczyszczenie starym paliwem, które jest bardzo trudne do usunięcia z wnętrza szyny, może spowodować pogorszenie przyczepności. Ponieważ dotyczy to paliwa, wybrano najbezpieczniejszą metodę; części, na których mocowane są wtryskiwacze, połączone są wysokiej jakości wężem paliwowym. Na wszystkich końcach zamontowano zszyte krawędzie i zastosowano solidne opaski zaciskowe, aby zapobiec przesuwaniu się węży po zszytych krawędziach.
Zdjęcie poniżej przedstawia kolektor dolotowy w momencie obróbki. Przewód zasilający (oznaczony numerem 1) jest podłączony do wyjścia pompy paliwa. Paliwo podawane jest na wejście czterech wtryskiwaczy pod ciśnieniem 3 barów. Regulator ciśnienia (3) reguluje ciśnienie w zależności od ciśnienia w kolektorze dolotowym, ponieważ różnica ciśnień pomiędzy ciśnieniem paliwa a podciśnieniem w kolektorze dolotowym musi wynosić 3 bary. Paliwo wraca do zbiornika przewodem powrotnym (2). Istnieje ciągły obieg paliwa. Wtrysk następuje tylko wtedy, gdy wtryskiwaczami steruje sterownik MegaSquirt.
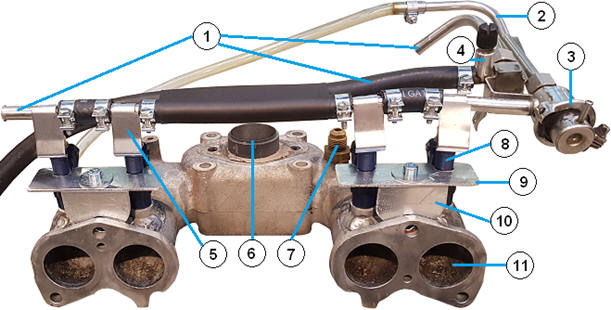
- linia zaopatrzenia
- linia powrotna
- regulator ciśnienia
- Kontrola ciśnienia
- osłona termiczna
- Podłączenie zaworu gazowego
- Podłączenie podciśnienia
- Wtryskiwacz cylindra 1
- Wspornik wtryskiwacza A
- Wspornik wtryskiwacza B
- Cylinder kanału dolotowego 1
W istniejących samochodach osobowych listwa wtryskowa mocowana jest do kolektora dolotowego za pomocą opasek lub oczek. Listwa wtryskiwaczy zaciska wtryskiwacze w kolektorze. Ponieważ do tego projektu jako listwę wtryskową wybrano elastyczny przewód paliwowy, powyższe nie jest możliwe. Zdecydowano się zatem na zamocowanie wtryskiwaczy w kolektorze dolotowym za pomocą robionego na zamówienie wspornika. Wsporniki składają się z dwóch części: części górnej (wspornik A) i części dolnej (wspornik B).
Wspornik A zawiera dwa wycięcia, które można nasunąć na wtryskiwacze. Umożliwia to wciśnięcie wtryskiwaczy w kolektor za pomocą płaskich boków. Obydwa wsporniki A posiadają szczelinowe otwory, umożliwiające regulację odległości wtryskiwaczy od szczelinowych otworów. Wsporniki A i B są ze sobą skręcone: wspornik B jest przymocowany do tej samej śruby dwustronnej, która mocuje kolektor do silnika. Szczelinowy otwór umożliwia regulację wspornika w kierunku pionowym. Im bardziej wspornik jest przesunięty w dół, tym mocniej jest zaciśnięty wtryskiwacz.
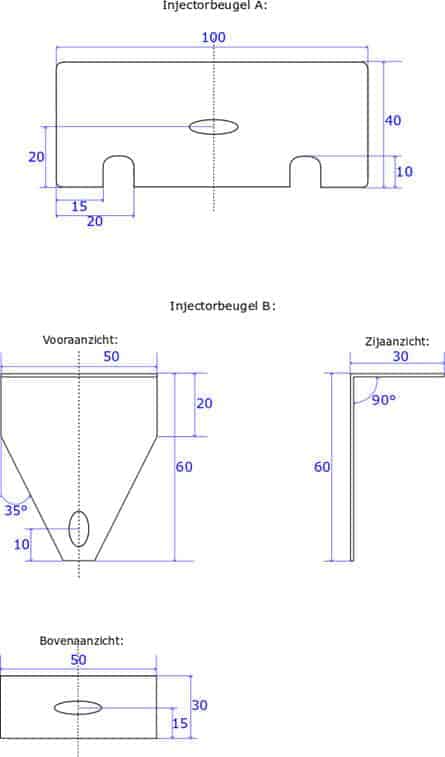
Zapłon:
Konwencjonalny zapłon został zastąpiony elektronicznie sterowanym układem zapłonowym z cewką zapłonową sterowaną przez MegaSquirt. Aby silnik mógł w pełni funkcjonować przy oryginalnych technikach, należy najpierw podłączyć konwencjonalny układ z punktami styku. Dopiero po kilku godzinach pracy można stwierdzić, że silnik pracuje prawidłowo, po czym można przystąpić do montażu i regulacji m.in. elektronicznie sterowanego zapłonu.
Przygotowanie przy użyciu konwencjonalnego zapłonu:
Silnik Land Rovera był pierwotnie wyposażony w układ zapłonowy z punktami kontaktowymi, który obecnie nazywany jest również konwencjonalnym układem zapłonowym. Zdjęcie przedstawia ten typ układu zapłonowego.
Przy zamkniętych punktach styku rozpoczyna się gromadzenie prądu pierwotnego. Prąd jest ograniczony do 3 do 4 amperów przez rezystancję uzwojenia pierwotnego. Kiedy prąd przepływa przez uzwojenie pierwotne cewki zapłonowej, wytwarza się pole magnetyczne. Zarówno cewka pierwotna (3), jak i wtórna (4) znajdują się w tym polu magnetycznym. Gdy prąd płynący przez punkty styku (10) zostanie przerwany przez krzywkę wyłącznika (9) na wale rozdzielacza, w obu cewkach indukuje się napięcie. W cewce pierwotnej wytwarza się około 250 woltów. Różnica w uzwojeniach wytworzy w uzwojeniu wtórnym napięcie indukcyjne od 10 do 15 kV. Iskra świecy zapłonowej powstaje w momencie otwarcia punktów.
Napięcie indukcyjne można ograniczyć, umożliwiając przepływ prądu pierwotnego przez pewien czas po otwarciu punktów stykowych. Osiąga się to za pomocą kondensatora, który jest połączony równolegle w punktach styku. Kondensator jest elementem określającym czas, który w zależności od pojemności faktycznie reguluje poziom napięcia indukcyjnego. Zapobiega się również spaleniu punktów kontaktowych.
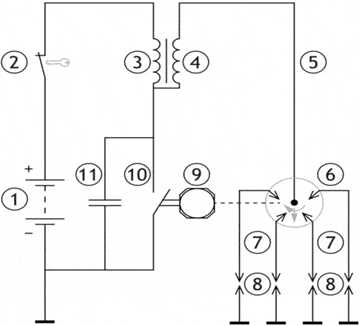
Cewka zapłonowa układu sterowania silnikiem:
System zarządzania silnikiem będzie sterował cewką zapłonową. Klasyczna cewka zapłonowa z rozdzielaczem pozostaje na silniku w celu przeprowadzenia testu, ale nie stanowi już części funkcjonowania silnika spalinowego. Wybrano bezrozdzielaczowy układ zapłonowy (cewka zapłonowa DIS), co w wolnym tłumaczeniu oznacza: „bezrozdzielaczowy układ zapłonowy”. Ten typ układu zapłonowego nie wykorzystuje dystrybutora. Inną opcją był wybór cewki zapłonowej Coil on plug (COP). Do każdej świecy zapłonowej podłączona jest osobna cewka zapłonowa. Cewka zapłonowa COP nazywana jest również cewką zapłonową z kołkiem. Wadą cewki zapłonowej COP jest to, że odprowadzanie ciepła jest słabsze niż w przypadku cewki zapłonowej DIS. W przypadku stosowania cewek zapłonowych COP wymagany jest również sygnał z czujnika wałka rozrządu, którego w obecnym silniku nie ma.
Brakujący ząb w kole pasowym wału korbowego służy jako punkt odniesienia, na podstawie którego określa się czas zapłonu. W przypadku cewki zapłonowej DIS w momencie zapłonu załączają się jednocześnie dwie świece zapłonowe. Cewka zapłonowa DIS to tak naprawdę zespół, w którym zamontowane są dwie cewki zapłonowe. Kiedy tłoki cylindrów 1 i 4 poruszają się w górę, jeden będzie zajęty suwem sprężania, a drugi suwem wydechu. Mimo to obie świece zapłonowe będą generować iskrę. Iskra wytworzona przez cylinder pracujący w suwie sprężania spowoduje zapłon mieszanki. Druga iskra, tak zwana „iskra zmarnowana”, pojawia się, gdy spaliny opuszczają komorę spalania. Iskra marnowana to iskra, która powstaje, gdy nie następuje zapłon żadnej mieszanki. Energia zapłonu jest niska; pomimo iskry straty energii są niewielkie. Nie jest to również szkodliwe.
Rysunek przedstawia schemat działania czterocylindrowego silnika benzynowego z cewką zapłonową DIS. Ten schemat pracy pokazuje dwa znaczniki zapłonu na moment zapłonu; 1 z nich wytwarza iskrę zapalającą mieszankę, drugi to iskra marnowana. Cewką zapłonową DIS można sterować za pomocą MegaSquirt za pomocą zaledwie dwóch impulsów.
Kiedy suw sprężania ma miejsce w cylindrze 1, a suw wydechu w cylindrze 4, MegaSquirt steruje cewką pierwotną A poprzez pin 36 w DB37 (patrz rysunek poniżej). Sterowanie to odbywa się w oparciu o punkt odniesienia wału korbowego (od 90 do 120 stopni przed GMP). MegaSquirt steruje cewką pierwotną B, która jest odpowiedzialna za wytwarzanie iskry cylindrów 2 i 3 i jest włączana o 180 stopni za cewką A. Nie ma punktu odniesienia dla cewki B, ale moment zapłonu można wyznaczyć po prostu licząc zęby na kole impulsowym 36-1.
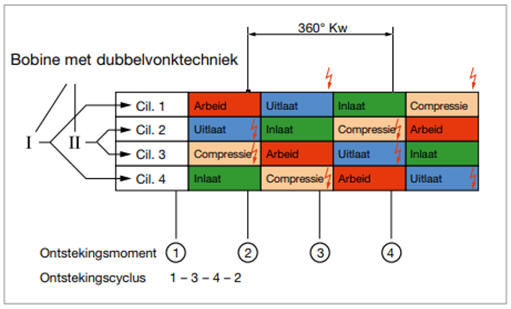
Pomiędzy cewką A cewki zapłonowej a stykiem 7 procesora pokazano rezystancję 330 omów. Rezystor ten ogranicza prąd i napięcie indukcyjne impulsu sterującego. Ponieważ rezystor ten nie jest standardem na płytce drukowanej MegaSquirt, należy go zamontować w późniejszym czasie. Na lewo od pionowej linii przerywanej na poniższym obrazku pokazano wewnętrzne obwody MegaSquirt. Pokazane komponenty (dwa rezystory 330 omów i diody LED) musiały zostać później przylutowane do płytki drukowanej.
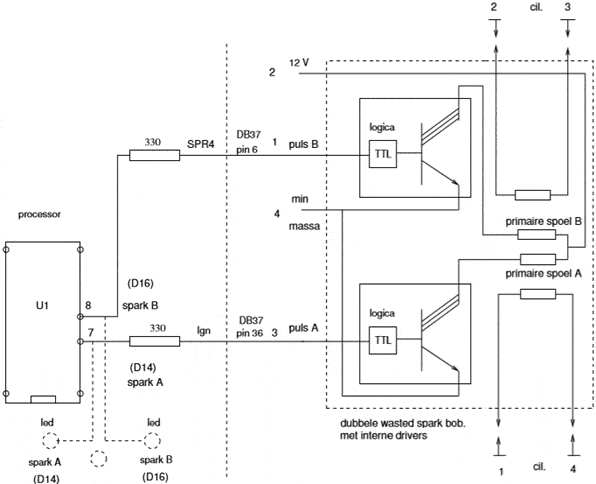
Nagromadzenie prądu w cewce pierwotnej:
Ważne jest, aby uzyskać wgląd w gromadzenie się prądu w cewce pierwotnej. Za jego pomocą można określić nie tylko natężenie prądu, ale także czas ładowania cewki zapłonowej. Czas ładowania zależy od wielu czynników, które MegaSquirt musi wziąć pod uwagę.
Współczynnik samoindukcji (wartość L) wybranej cewki zapłonowej wynosi 3,7 mH. Wraz z rezystancją omową R określa się maksymalny prąd pierwotny i czas narastania krzywej. Mała wartość L i rezystancja zapewniają szybki wzrost prądu po włączeniu. Znane dane cewki zapłonowej można wykorzystać do obliczenia sposobu wytwarzania prądu pierwotnego.
Poniższy wzór przedstawia ogólne rozwiązanie równania różniczkowego pierwszego rzędu, które oblicza prądy, czasy ładowania i rozładowywania, aby przedstawić zjawisko przełączania w postaci krzywej.
Równanie to:

gdzie stałą czasową (Tau) oblicza się w następujący sposób:

Zgodnie z prawem Ohma maksymalny prąd będzie wynosił 28 amperów:
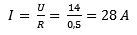
W rzeczywistości takie natężenie nie zostanie osiągnięte.
Cewka wyłącza się wcześniej. Powód wyjaśniono później. Wpisanie tej informacji do wzoru ogólnego daje:
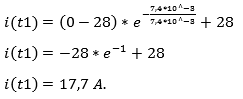
Rysunek przedstawia krzywą ładowania cewki pierwotnej. Od czasu T0 do 1 Tau cewka jest naładowana do 63,2%. Jest to stała wartość procentowa czasu ładowania cewki. Wynik wzoru 13 pokazuje, że cewka jest naładowana prądem 1 ampera przy 17,7 Tau. Przy t = 5 Tau wartość końcowa została praktycznie osiągnięta.
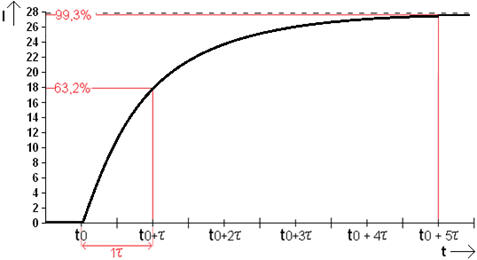
Według specyfikacji cewki zapłonowej prąd pierwotny cewki zapłonowej po naładowaniu wynosi 7,5 A. Prąd nie wzrasta. Czas potrzebny do osiągnięcia 7,5 A nazywany jest czasem oczekiwania. Czas oczekiwania zależy od napięcia akumulatora, które w tym przypadku wynosi 14 woltów. Jeżeli proces ładowania nie jest regulowany, prąd płynący przez cewkę wynosi maksymalnie 12 amperów, zgodnie ze wzorem 28.
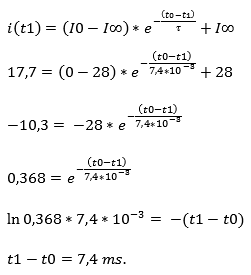
Cewkę według wzoru 14 ładuje się do 7,4 A w czasie t = 17,7 ms. Rzeczywisty czas ładowania jest krótszy, ponieważ cewka ładowana jest maksymalnie do 7,5 A. Wymagany czas można obliczyć wpisując znane dane we wzorze 15.
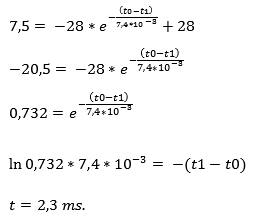
Narastanie prądu pierwotnego zostaje zatrzymane przy 7,5 A. Zapobiega to nadmiernemu i niepotrzebnemu nagrzewaniu się cewki zapłonowej. Najważniejsze jest to, aby cewka została optymalnie naładowana w jak największym stopniu w jak najkrótszym czasie. Na rysunku przedstawiono krzywą ładowania do t = 2,3 ms.
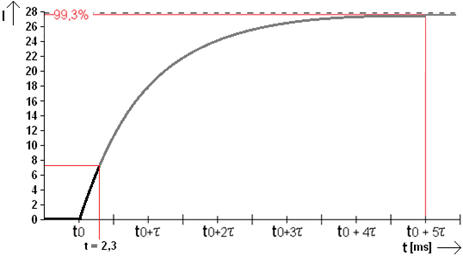
Kiedy napięcie akumulatora spada, na przykład podczas uruchamiania silnika, ma to wpływ na czas postoju. Następnie osiągnięcie wartości 2,3 A zajmuje więcej niż 7,5 ms. Nowy czas ładowania wyznaczany jest za pomocą znanego już wzoru. Maksymalny prąd określa się na podstawie napięcia akumulatora:
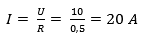
Czas ładowania do 7,5 A przy maksymalnie 20 A oblicza się ze wzoru 17:
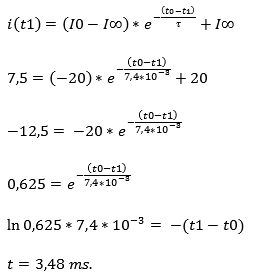
Na rysunku czarną linią pokazano czas ładowania przy napięciu 14 V, a kolorem zielonym czas ładowania przy napięciu 10 V. Linie spadają jednocześnie do 0; to jest moment zapłonu. Ponieważ niższe napięcie akumulatora wymaga więcej czasu na naładowanie cewki pierwotnej, MegaSquirt musi wcześniej włączyć zasilanie główne.
Czarne linie (rosnące i opadające) wskazują czas przebywania przy napięciu akumulatora 14 woltów. Zielona linia wskazuje zaawansowany czas ładowania przy niższym napięciu: daje to Δt. Rzeczywisty czas ładowania wynosi w tym przypadku Δt + 100%.
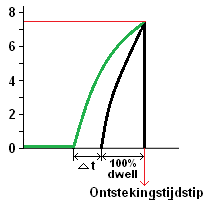
Zostanie to wyjaśnione w dalszej części tej sekcji na przykładzie i rysunku 36. Czas ładowania ulega wydłużeniu, a moment zapłonu pozostaje taki sam. Jeśli tak się nie stanie lub nie stanie się to w wystarczającym stopniu, będzie to miało konsekwencje dla energii uwalnianej podczas zapłonu. W takim przypadku prąd pierwotny zostanie wyłączony zbyt wcześnie, przez co nie zostanie osiągnięty prąd 7,5 A. Wydłużenie czasu ładowania cewki pierwotnej (czas przebywania) jest we wzorze funkcją napięcia akumulatora. Obliczanie czasu przebywania przy różnych napięciach daje inny maksymalny prąd w cewce.
Zakładając, że napięcie akumulatora może spaść do 6 woltów podczas rozruchu i wzrosnąć do 14,7 woltów podczas ładowania, można narysować krzywą, obliczając liczbę wartości pośrednich. Poniższy rysunek przedstawia korektę czasu przebywania dla zastosowanej cewki zapłonowej DIS. Dla każdego wzrostu napięcia o 2 wolty na wykresie umieszczany jest (czerwony) punkt. Ponieważ w programie TunerStudio wprowadzono wcześniej wprowadzony czas oczekiwania wynoszący 2,3 ms przy napięciu 14 V, na podstawie tego napięcia tworzony jest współczynnik korekcyjny. Napięcie 14 woltów wynosi zatem 100% (bez korekcji).
Teraz stało się jasne, że czas ładowania wzrasta nawet o 315% przy napięciu akumulatora 6 woltów.
W niesprzyjających warunkach napięcie akumulatora może spaść nawet o 6 woltów. Oznacza to osłabienie iskry zapłonowej. Wydłużenie czasu przebywania (czasu przepływu prądu pierwotnego) kompensuje to, dzięki czemu nawet przy tak niskim napięciu uzyskuje się wystarczającą energię zapłonu. Oznacza to, że Δt z rys. 36 jest trzykrotnie większe (2,3 ms * 315% = 7,26 ms) w porównaniu z czasem przebywania wynoszącym 100% (2,3 ms) wskazanym na czarno.
Współczynniki zaznaczone na czerwono na powyższym obrazku można skopiować bezpośrednio do programu TunerStudio.
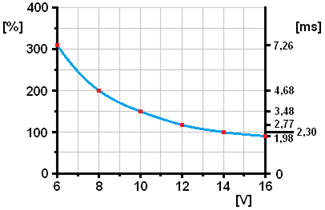
Jakiś czas po rozładowaniu cewki pierwotnej rozpoczyna się przygotowanie do następnego zapłonu. Im wyższa prędkość obrotowa silnika, tym szybciej ładuje się cewka. Rysunek 37 przedstawia dwie krzywe, w których prąd pierwotny wzrasta do 8,85 A. Czas zapłonu przypada na punkt, w którym linia spada do 0 A.
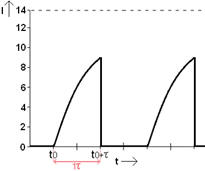
Określanie czasu zapłonu:
Sygnał zapłonu wyznaczany jest z punktu odniesienia wału korbowego.
W pierścieniu zębatym koła pasowego wału korbowego, 36 ząb z 1 zębów został wyfrezowany pod kątem 100 stopni przed górnym martwym punktem tłoka cylindra 1. Pomiędzy 100 a 0 stopni, a więc podczas suwu sprężania mikroprocesor MegaSquirt może określić czas zapłonu. Uwzględnia to zaliczkę.
Na obrazku przedstawiono obraz z oscyloskopu dwukanałowego, na którym górny obraz przedstawia punkt odniesienia wału korbowego, a dolny obraz przedstawia sygnał sterujący z MegaSquirt do cewki zapłonowej DIS. Sygnał sterujący ma napięcie 5 woltów (logiczna 1) i trwa około 1,5 ms.
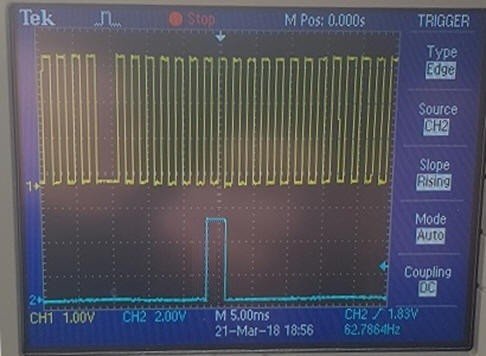
Wyprzedzenie zapłonu:
W tym projekcie nie zastosowano czujników spalania stukowego. Możliwe jest przetwarzanie informacji z czujników spalania stukowego, ale samo zainstalowanie czujnika spalania stukowego nie wystarczy. Przetwarzanie sygnałów jest złożone. Sygnał pukania należy najpierw przekształcić na sygnał tak/nie lub na sygnał analogowy wskazujący siłę detonacji.
Przetwarzanie wibracji silnika na sygnał stukowy odbywa się za pomocą obwodu interfejsu. Obwód ten nie występuje w MegaSquirt II. Dlatego zdecydowano się na bezpieczne ustawienie wyprzedzenia przy pełnym obciążeniu i częściowym obciążeniu, tak aby silnik nie znalazł się w strefie stuków. Ustawiona krzywa wyprzedzenia pełnego obciążenia musi być określona w granicach uderzeń. Dane wyprzedzenia odśrodkowego i podciśnienia w przypadku zapłonu konwencjonalnego są określane na podstawie danych fabrycznych z instrukcji silnika. Punkty można nanieść na wykres (przykład na obrazku poniżej).
Różowa linia wskazuje oryginalny, mechaniczny postęp. Jest to częściowo liniowe ze względu na mechaniczną konstrukcję odważników odśrodkowych. Czarna linia pokazuje kontrolę mapy w MegaSquirt; ta linia przebiega po krzywej. Ważne jest, aby trzymać się z dala od obszarów uderzeń przy częściowym i pełnym obciążeniu; dlatego też sterowanie mapą jest ograniczone przy częściowym obciążeniu (czerwona linia), a przesuw przy pełnym obciążeniu nie zwiększa się bardziej niż w przypadku mechanicznego przesuwu (czerwona linia). Rzeczywisty układ mapy jest zgodny z niebieską linią.
Najpierw należało wprowadzić krzywą wyprzedzenia pełnego obciążenia w tabeli wyprzedzenia iskry. Przy wyższych prędkościach i mniejszych obciążeniach wymagany będzie większy postęp. Przy częściowym obciążeniu zaliczka jest dodawana do zaliczki przy pełnym obciążeniu. Wypełnioną tabelę wyprzedzenia zapłonu i ustawień wyprzedzenia zapłonu, gdy silnik jest zimny, przedstawiono na stronie 7.
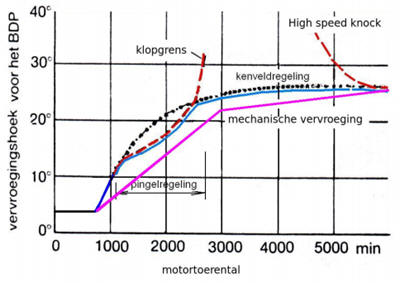
Korpus przepustnicy:
Dopływ powietrza/paliwa był kontrolowany przez gaźnik w oryginalnym stanie. W układzie sterowania silnikiem gaźnik zastępuje korpus przepustnicy i cztery wtryskiwacze zamontowane w kolektorze dolotowym. Zapewnia to bardziej precyzyjny i kontrolowany wtrysk niż w przypadku gaźnika, gdzie mieszanka paliwowo-powietrzna powstaje centralnie w kolektorze i jest podzielona na cztery kanały. Przepustnicę otwiera się za pomocą cięgna Bowdena obsługiwanego ręcznie z tablicy rozdzielczej.
W końcu MegaSquirt II nie obsługuje elektronicznie sterowanego korpusu przepustnicy. Dlatego jedyną opcją, którą można zastosować, jest sterowanie cięgnem Bowdena.
Pozycja przepustnicy przekazywana jest do MegaSquirt za pomocą napięcia. Wielkość napięcia zależy od kąta otwarcia przepustnicy. Czujnik położenia przepustnicy to potencjometr o napięciu zasilania 5 woltów (patrz zdjęcie). Niezbędne jest połączenie 3 i uziemienie 1. Pływak (pin 2) przyjmuje pozycję na oporze zależnym od położenia przepustnicy. Dlatego też prowadnica jest połączona z przepustnicą. Kiedy biegacz musi pokonać niewielki dystans ponad oporem (biegacz wskazuje w lewo), opór jest niski. Na zdjęciu prowadnica jest ustawiona po prawej stronie (od strony masy), co oznacza, że występuje duża rezystancja, a co za tym idzie, niskie napięcie sygnału.
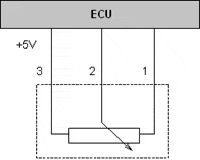
Przy zastosowaniu korpusu przepustnicy na prowadnicy występuje napięcie 600 mV przy zamkniętej przepustnicy i napięcie 3,9 V przy całkowicie otwartym zaworze. ECU odbiera napięcie i na jego podstawie oblicza kąt otwarcia przepustnicy. Gwałtowny wzrost kąta otwarcia oznacza, że następuje przyspieszenie; ECU reaguje na to krótkim wzbogaceniem. Nazywa się to wzbogacaniem przyspieszającym. Czujnik położenia przepustnicy nie służy do określenia wzbogacenia mieszanki w różnych warunkach pracy; Do tego celu służy czujnik MAP.
Konfiguracja testowa silnika krokowego z symulatorem:
Po dostosowaniu sprzętowym MegaSquirt można było wykorzystać skrzynkę rozdzielczą do sprawdzenia, czy odbierane jest sterowanie silnikiem krokowym. Świecenie dwukolorowych diod LED sygnalizuje, że odbywa się sterowanie. Poszczególne etapy sterowania silnikiem krokowym można śledzić obserwując zmianę kolorów. Kolory na przemian są czerwone i żółte. Dane silnika krokowego można wprowadzić w menu „Kontrola biegu jałowego” w programie TunerStudio. Oprócz typu (4 przewody) można również ustawić liczbę stopni. Obejmuje to również pozycję wyjściową, w której musi znajdować się silnik krokowy po uruchomieniu silnika. Ponadto można ustawić czas potrzebny na dostosowanie jednego kroku.
Liczba stopni zależy między innymi od temperatury płynu chłodzącego; niższa temperatura wymaga większego otwarcia silnika krokowego. Kroki w zależności od temperatury można ustawić na wykresie. Za pomocą symulatora można sprawdzić, czy silnik krokowy jest faktycznie prawidłowo sterowany. Ponieważ sprawdza się to najpierw na symulatorze, a nie na silniku, można zapobiec problemom podczas uruchamiania lub pracy silnika ze względu na możliwy problem ze sprzętem lub oprogramowaniem. Ponieważ na kąt otwarcia silnika krokowego największy wpływ ma temperatura płynu chłodzącego i prędkość obrotowa silnika, można sprawdzić poprawność sterowania kręcąc tymi potencjometrami. Miernik na desce rozdzielczej w TunerStudio wyświetli korektę liczby dostosowanych kroków.
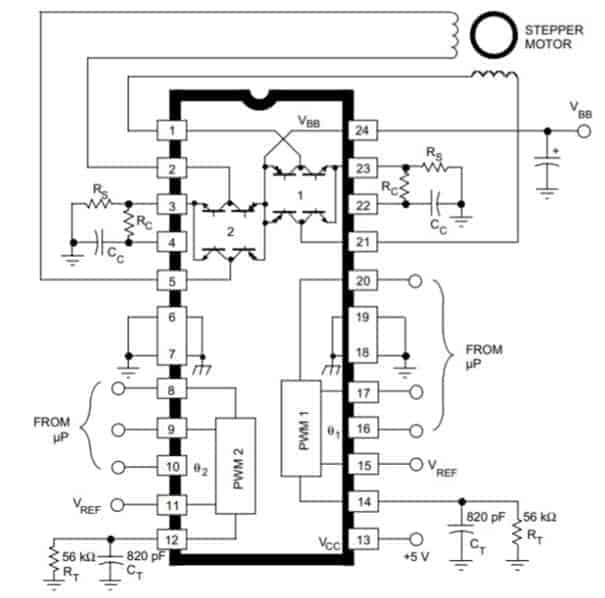
Ustawienia silnika krokowego:
Rysunek przedstawia ekran ustawień silnika krokowego wykorzystywanego do regulacji biegu jałowego (sterowanie biegiem jałowym).
Kroki regulacji silnika są ustalane z góry za pomocą Arduino. Aby przemieścić się do pozycji podstawowej (kroki bazowania), należy także wprowadzić liczbę kroków. Silnik krokowy jest aktywny w fazie nagrzewania (algorytm) i zasila cewki na postoju (podtrzymuje prąd pomiędzy krokami).
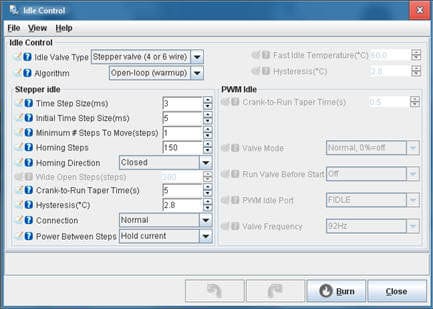
Położenie silnika krokowego zależy od temperatury płynu chłodzącego. Przy uruchamianiu zimnego silnika zawór powinien być otwarty nieco bardziej niż przy uruchamianiu rozgrzanego silnika. Poniższy obrazek przedstawia ekran ustawień umożliwiający ustawienie kroków (Kroki) w zależności od temperatury płynu chłodzącego (Chłodziwo). Gdy silnik jest zimny, silnik krokowy jest całkowicie otwarty, gdy silnik pracuje na biegu jałowym. W fazie nagrzewania silnik krokowy lekko się zamyka.
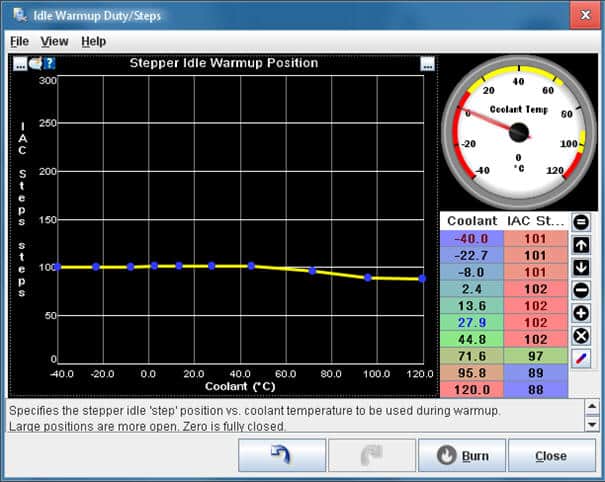
Możliwe jest również dostosowanie położenia silnika krokowego w zależności od temperatury płynu chłodzącego podczas uruchamiania silnika. Nazywa się to „pracą/krokami pracy na biegu jałowym”. Poniższy obrazek przedstawia ekran ustawień.
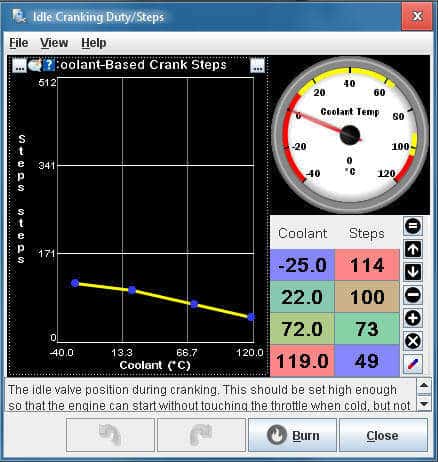
Obwód pompy paliwa:
MegaSquirt zapewnia włączanie i wyłączanie pompy paliwa. Tranzystor Q19 na poniższym rysunku chroni tranzystor Q2 przed nadmiernym prądem. Jeśli prąd jest zbyt wysoki, tranzystor może się przepalić. Gdy prąd płynący przez część kolektor-emiter tranzystorów Q2 i R40 wzrasta, osiągane jest napięcie nasycenia na bazie tranzystora Q19. Tranzystor Q19 włącza się, powodując spadek napięcia baza-emiter w Q2.
Połączenie FP-1 PTA0 jest kontrolowane wewnętrznie przez MegaSquirt. Do sterowania obwodem tranzystorowym wymagany jest sygnał wejściowy z czujnika położenia wału korbowego (czujnik Halla lub czujnik indukcyjny). W przypadku utraty sygnału, na przykład w przypadku niezamierzonego zgaśnięcia silnika, zasilanie pompy paliwowej zostaje natychmiast przerwane.
Wyjście obwodu tranzystorowego (FP1 OUT) jest podłączone do przekaźnika pompy paliwa. Pin 85 przekaźnika jest wyjściem prądu sterującego. W przypadku przekaźnika pod napięciem główna sekcja zasilania (piny 30 i 87) jest przełączana, dzięki czemu pompa paliwowa otrzymuje napięcie zasilania potrzebne do działania.
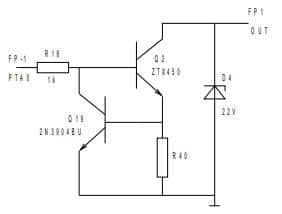
Zastosowano elektroniczną pompę paliwa o ciśnieniu roboczym 3 bary. Paliwo kierowane jest przez filtr paliwa do listwy paliwowej, gdzie panuje ciśnienie na wlocie wtryskiwaczy. Wtryskiwacz wstrzyknie wcześniej obliczoną ilość paliwa do kolektora dolotowego, gdy nadejdzie sygnał z MegaSquirt. Sterowanie MegaSquirtem określa nie tylko ilość wtryskiwanego paliwa, ale także ciśnienie paliwa w listwie.
Przy wyższym ciśnieniu w szynie, przy tej samej kontroli zostanie wtryśnięta większa ilość paliwa. Dlatego ciśnienie w szynie należy regulować w oparciu o podciśnienie w kolektorze dolotowym. Różnica ciśnień (∆P) musi przez cały czas wynosić 3 bary. Na rysunku przedstawiono schemat układu paliwowego. Linie różowe, żółte, pomarańczowe i czarne pokazują połączenia elektryczne. Linia czerwona wskazuje dopływ paliwa, a linia niebieska powrót paliwa.
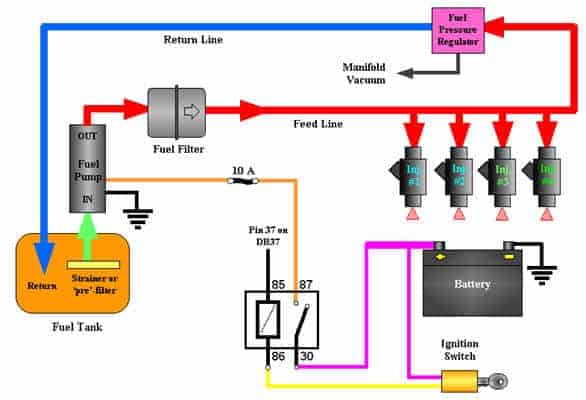
Zakończenie prac mechanicznych:
Kolejne trzy zdjęcia przedstawiają silnik w końcowej fazie modyfikacji mechanicznych.
Zdjęcie 1:
Jest to strona, z której widoczna jest większość zastosowanych części. Tutaj znajduje się również deska rozdzielcza elementów sterujących i ECU MegaSquirt. Pod zdjęciem znajduje się legenda z opisem numerów części. Zdjęcia można otworzyć w większym rozmiarze klikając na nie.
- Zawór dławiący;
- Przewód paliwowy do wtryskiwaczy;
- Rurka łącząca przepustnicę na kolektorze dolotowym;
- Wskaźnik ciśnienia paliwa;
- Kolektor dolotowy i wydechowy;
- Deska rozdzielcza z włącznikiem wentylatora chłodzącego, lampkami alternatora i ciśnienia oleju, wyłącznikiem zapłonu i uziemnikiem;
- Wąż podciśnieniowy do czujnika MAP;
- Sonda lambda;
- Węże paliwowe (zasilanie i powrót) razem w skrzynce termokurczliwej;
- Zespół pompy paliwa/zbiornika;
- Przekaźnik pompy paliwa;
- megatrysk;
- Tłumik wydechowy.
Zdjęcie 2:
Na zdjęciu widać drugą stronę silnika. Tutaj widać gaźnik (15) i konwencjonalny zapłon (17). Celem tego klasycznego zapłonu jest wywołanie iskry na świecach zapłonowych w układzie testowym (14). Nie ma to oczywiście żadnego wpływu na silnik, ale daje wgląd w działanie zapłonu, tak jak to miało miejsce w klasycznych samochodach.
Liczba 20 oznacza mechanizm hamulca skrzyni biegów. Drążek bębna hamulcowego można dokręcić za pomocą linki Bowdena, dzięki czemu wał wyjściowy skrzyni biegów zostanie wyhamowany. Hamulec skrzyni biegów jest włączany w celu krótkotrwałego obciążenia silnika po włączeniu biegu.
Zdjęcie 3:
Wyraźnie widać tutaj widok silnika z góry z układem testowym zapłonu i szyny paliwowej.
Zakończono regulacje mechaniczne. Nie można jeszcze uruchomić silnika, ponieważ należy najpierw wprowadzić pewne dane do MegaSquirt.
Volgende: Regulacja ECU MegaSquirt II.