Przedmioty:
- Początek projektu
- Silnik
- Skrzynia biegów
- Sprawdź, wymień i wyreguluj części silnika
- Zamontuj silnik na ruchomej ramie
- Chłodzenie
- Deska rozdzielcza i instalacja elektryczna
- Pompa paliwa i zbiornik
- Uruchom silnik w klasycznej konfiguracji
Początek projektu:
Po podjęciu decyzji o wyposażeniu silnika w system zarządzania silnikiem MegaSquirt rozważano wybór odpowiedniego typu silnika. Standardowe pakiety konwersji z instrukcjami nie były interesujące. Celem było zastosowanie silnika spełniającego następujące warunki:
- nie powinny być znane żadne wcześniejsze projekty konwersji tego silnika;
- czterocylindrowy silnik benzynowy;
- jeszcze nie wyposażony we wtrysk i elektroniczny układ zapłonowy;
- możliwość obciążenia silnika.
Silnik:
Poszukiwania doprowadziły do silnika pochodzącego z Land Rovera (seria 2A) z początku lat 70-tych. Ten czterocylindrowy silnik benzynowy o pojemności 2,25 litra, z trzema łożyskami głównymi, był oryginalnie wyposażony w gaźnik i mechaniczny rozdzielacz zapłonu. O wyborze zadecydowało połączenie tego silnika Land Rovera i oryginalnej skrzyni biegów; Hamulec skrzyni biegów jest przymocowany do wału wyjściowego skrzyni biegów. Hamulec skrzyni biegów, który faktycznie służy jako hamulec postojowy, umożliwia zaciągnięcie hamulca silnika podczas pracy.
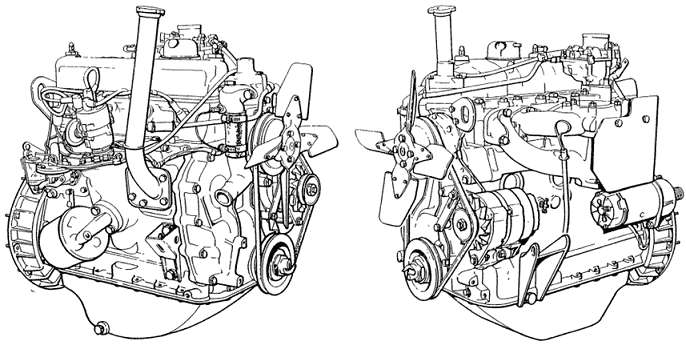
Silnik prawdopodobnie nie działał od dziesięcioleci. Oczywiście musi być na tyle niezawodny, aby działał w systemie zarządzania silnikiem. Należało więc najpierw dokładnie sprawdzić i przetestować silnik. Postawiono następujące cele:
- Sprawdź, wymień i wyreguluj części silnika;
- Zamontuj silnik na ruchomej ramie;
- Pozwól silnikowi działać w klasycznej konfiguracji;
- Instalowanie komponentów systemu zarządzania silnikiem;
- Zmontuj i przygotuj ECU MegaSquirt;
- Pozwól silnikowi działać w systemie zarządzania silnikiem.
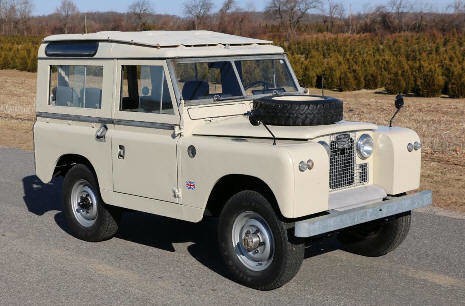
Skrzynia biegów:
Skrzynia biegów pochodzi z wojskowego Land Rovera. Zielony kolor faktycznie to zdradza.Aby w późniejszym etapie stworzyć jak najbardziej oryginalną całość z silnikiem, zielony lakier został usunięty. Na zdjęciu nie ma jeszcze hamulca skrzyni biegów; został on później zamontowany na wale wyjściowym zgodnie z instrukcjami fabrycznymi.
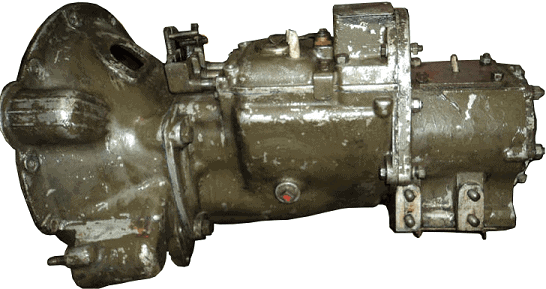
Sprawdź, wymień i wyreguluj części silnika:
Na początku projektu nie było jasne, czy udostępniony silnik nadawał się do użytku. Niewiele wiedziano o bloku silnika, poza tym, że silnik stał nieruchomo przez lata. Nie było jasne, czy jakiekolwiek części wewnętrzne zostały uszkodzone lub nawet – prawdopodobnie nieodwracalne – wadliwe. W tym drugim przypadku jedyną możliwością wznowienia projektu była wymiana silnika na inny.
Aby na późniejszym etapie nie dojść do wniosku, że silnik będzie bezużyteczny, zdecydowano się na rozebranie i remont silnika. Sprawdzono wzorce zużycia części i porównano je ze specyfikacjami fabrycznymi. Części, których pomiary mieściły się w podanych tolerancjach, zostały wymienione. Części odrzucone zostały wymienione. Uwzględniono cel, w jakim silnik będzie używany; silnik musi być zbudowany jak najmniejszym kosztem, aby był wystarczająco niezawodny do realizacji projektu i służył jako narzędzie dydaktyczno-uczące się.
Silnik mocowany jest do wspornika montażowego w punktach mocowania obudowy skrzyni biegów. Silnik można obracać w różnych pozycjach. Dzięki temu zarówno głowica cylindrów, jak i miska olejowa są optymalnie dostępne podczas prac demontażowych. Dla prawidłowego funkcjonowania silnika ważne jest podjęcie środków ostrożności zapewniających dobre ciśnienie końcowe sprężania. Jeśli ciśnienie w jednym lub większej liczbie cylindrów jest zbyt niskie, skutkuje to źle funkcjonującym i słabnącym silnikiem. W takim przypadku regulacja przy nowo zamontowanym zapłonie i układzie wtryskowym będzie utrudniona, jeśli nie niemożliwa.
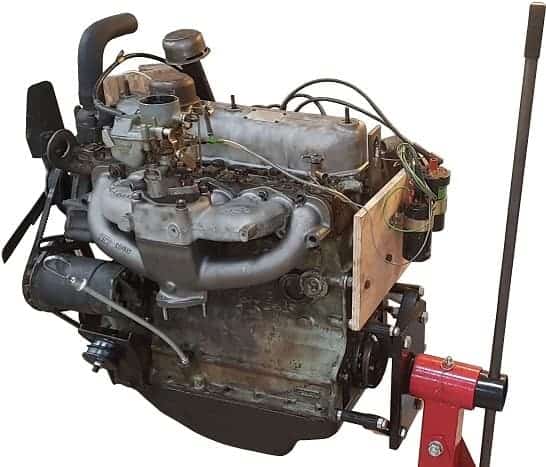
Jednym z pierwszych punktów kontrolnych są tłoki i ścianki cylindrów. Aby sprawować odpowiednią kontrolę, należało wymontować tłoki z bloku silnika. Po zdemontowaniu głowicy cylindrów i miski olejowej można było zdemontować tłoki. Tłoki zostały sprawdzone pod kątem owalności i widocznych oznak zużycia. Pierścienie tłokowe zostały również sprawdzone pod kątem zużycia. Zużyte pierścienie tłokowe mogą powodować utratę kompresji i zużycie oleju; Kontrola ta musi zapobiec obu konsekwencjom. Oprócz kontroli optycznej zmierzono również luz pomiędzy rowkami pierścieni tłokowych a pierścieniem tłokowym.
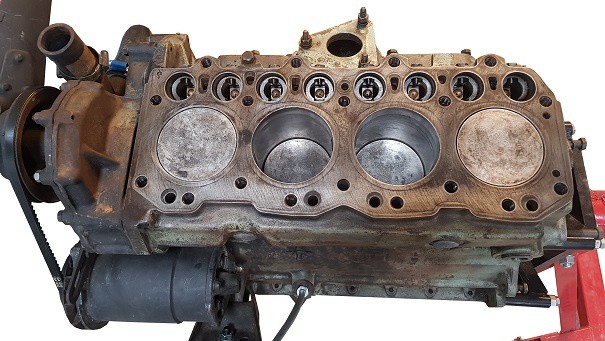
Poniższy rysunek przedstawia pomiar, podczas którego tłok jest mierzony za pomocą miernika śrubowego. Oprócz owalności można również określić odległość pomiędzy tłokiem a ścianką cylindra. Zbyt duży dystans oznacza nadmierne zużycie. W przypadku projektu oznaczałoby to konieczność zainstalowania innych nadmiarowych tłoków. Po ocenie wizualnej i geometrycznej czterech tłoków stwierdzono, że nie doszło do nadmiernego zużycia.
Po wymianie pierścieni tłokowych należy zmierzyć i w razie potrzeby wyregulować luz końcowy, aby zapobiec pęknięciu pierścienia tłokowego (na skutek zbyt małego lub zbyt dużego luzu) i zapobiec utracie kompresji (utratom wycieków na skutek zbyt dużego luzu ). Pierścień tłokowy umieszcza się w cylindrze, w którym średnica jest najmniejsza. Luz zamka mierzy się szczelinomierzem. Pomiar ten pokazano na rysunku. Pierścienie tłokowe pierwszego cylindra zostały wymienione ze względu na ich zły stan i musiały być piłowane o jeden milimetr mniejsze; po złożeniu końce stykały się ze sobą.
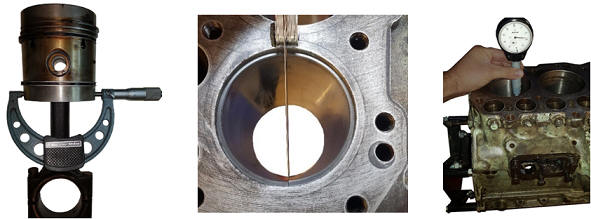
Pomiar zużycia tulei cylindrowych przeprowadza się za pomocą odpowiedniego obiektu pomiarowego. Odchylenie wskazówki pokazuje stopień zużycia. Zdjęcie pokazuje wymiar cylindra 4. Średnica cylindra wzrośnie, zwłaszcza po stronie, po której występuje siła ślizgowa. Ściany cylindra mogą wykazywać pewne zużycie, ale zużycie musi mieścić się w granicach tolerancji. Wyniki pomiarów wykazały akceptowalne zużycie ścianek cylindrów. Kontrola optyczna tulei cylindrów wykazała, że wiele części ścianek było gładkich. Rowki honujące już prawie nie występowały.
Rowki po honowaniu, czyli rodzaj drobnych zadrapań, sprawiają, że pomiędzy pierścieniem tłokowym a ścianką cylindra przez cały czas znajduje się niewielki film olejowy. Głównym zadaniem tego filmu olejowego jest smarowanie, ale pełni on również funkcję uszczelniającą i dlatego pomaga w osiągnięciu końcowego ciśnienia sprężania. We wszystkich czterech tulejach cylindrów wykonano nowe rowki honownicze przy użyciu odpowiedniego kamienia do honowania. Zdjęcie przedstawia tę operację. Podjęto próbę zastosowania rowków honujących możliwie najbardziej poprzecznie, pod kątem 45 stopni.
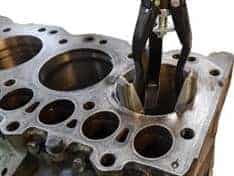
Zawory uszczelniają przestrzeń spalania nad tłokiem. Wyciek wzdłuż gniazda zaworu powoduje utratę kompresji; coś, czemu należy zapobiegać. Aby sprawdzić stan zaworów i gniazda zaworu, należy najpierw zdemontować wszystkie zawory z głowicy cylindrów. Na zdjęciu zdemontowana sprężyna zaworowa z zaworu dolotowego cylindra 1. Płytki zaworowe zaworów cylindra 1 zostały na tyle zniszczone, że podjęto decyzję o wymianie obu.
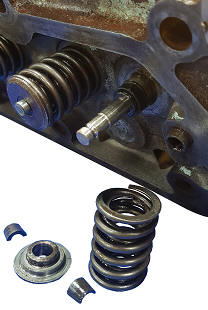
Po demontażu okazało się, że kilka gniazd zaworów zostało uszkodzonych/uszkodzonych. Zdjęcie poniżej przedstawia gniazda zaworowe pierwszego cylindra. Jest bardzo prawdopodobne, że gdyby nie zostało to sprawdzone, silnik nie pracowałby prawidłowo. Samo ponowne przeszlifowanie nowych zaworów nie byłoby wystarczające, dlatego zdecydowano się na frezowanie gniazd zaworów.
Za pomocą obcinaka do gniazd zaworów usuwa się niewielką ilość materiału, dzięki czemu gniazdo zaworu jest ponownie gładkie. Trzpień obcinaka wsuwa się w prowadnicę zaworu (patrz zdjęcie poniżej). Dzięki temu nóż można umieścić prosto na gnieździe. Podczas procesu obróbki uwzględniono dwa różne kąty, pod którymi należy wykonać frezowanie. Najbardziej ucierpiały zawory cylindrów 1 i 2. Aby zapewnić kompletność, wszystkie osiem gniazd zaworów zostało obrobionych maszynowo. Po frezowaniu zawory są szlifowane specjalnym materiałem ściernym, aby zapewnić jak najlepszą szczelność.
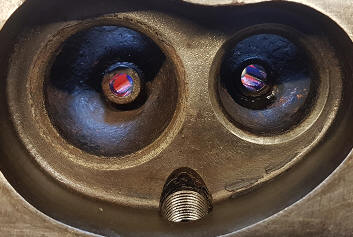
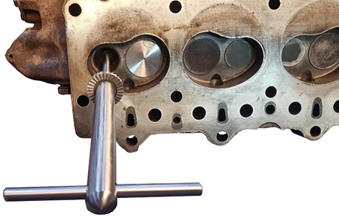
Luz osiowy wału korbowego z trzema łożyskami głównymi i dwoma łożyskami oporowymi mierzy się za pomocą czujnika zegarowego. Jeżeli luz osiowy jest zbyt duży, można zamontować większe łożysko osiowe, jeśli nie występuje usterka mechaniczna. Pomiar pokazany na obrazku wykazał, że luz osiowy był prawidłowy.
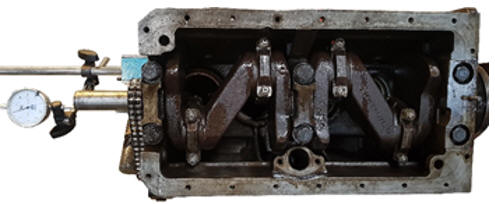
Przestrzeń pomiędzy łożyskami ślizgowymi wału korbowego a korbowodem, inaczej mówiąc: luz promieniowy wału korbowego, mierzy się plastyką (patrz rysunek). Plastige to specjalny drut z tworzywa sztucznego, który pod wpływem ściskania trwale odkształca się. Po zamontowaniu pokrywy łożyska lub korbowodu, plastigage pozostawi ślad. Szerokość nadruku wskazuje, jaki jest luz pomiędzy łożyskiem ślizgowym a wałem korbowym.
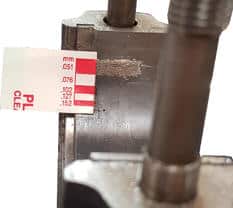
Łańcuch rozrządu przenosi ruch z wału korbowego na wałek rozrządu. Po zamontowaniu tłoków, wału korbowego i głowicy cylindrów należy po montażu ponownie wyregulować łańcuch rozrządu. Ze względu na brak regulacji i oznaczeń, regulację należało ustalić na podstawie schematu asymetrycznego zaworu. Za pomocą tarczy stopniowej na wale korbowym można określić kąt otwarcia i zamknięcia zaworów dolotowych i wydechowych (patrz zdjęcie). Części rozdzielcze, takie jak zębatki, łańcuch, prowadnica i napinacz, zostały sprawdzone pod kątem zużycia optycznego. To było w porządku.
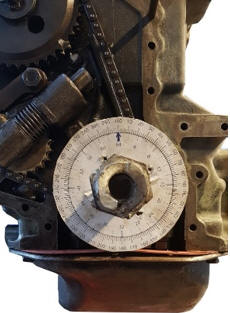
Wszystkie części są dokręcane zgodnie z zalecanymi momentami dokręcania. Ponieważ silnik został rozebrany, kontroli należy dokonać po przejechaniu kilku kilometrów. Nie jest to jednak możliwe, ponieważ silnik nie jest montowany w pojeździe. Dlatego też zdecydowano o przeprowadzeniu kontroli zalecanych przez firmę Land Rover po 24 godzinach pracy.
Montaż silnika na ramie mobilnej:
Celem było wykorzystanie silnika jako narzędzia dydaktycznego działającego w oparciu o system zarządzania silnikiem. Silnik nie jest montowany w samochodzie. Aby zapewnić bezpieczną i niezawodną konfigurację, zdecydowano się umieścić silnik na odpowiedniej ramie silnika. Zamierzono, aby silnik był przymocowany do ramy silnika w oryginalnych miejscach mocowania silnika. Ponieważ nie ma gotowych zestawów do konwersji, wsporniki musiały być wykonane na zamówienie.
Na etapie budowy należało dokonać wyboru, w jaki sposób powinien być zbudowany silnik. W przypadku zwiększonego obciążenia silnika należy dostosować układ sterowania silnikiem. Ponieważ oryginalna skrzynia biegów posiada hamulec skrzyni biegów, zdecydowano się zamontować skrzynię biegów również na ramie silnika. Uruchomienie tego hamulca skrzyni biegów umożliwia krótkotrwałą pracę silnika pod obciążeniem.
Edycja i adaptacja istniejących mocowań silnika umożliwiła niezawodne połączenie silnika z ramą. Rama silnika oferuje również możliwość zamocowania deski rozdzielczej, na której można między innymi realizować elementy sterujące. Zdjęcie przedstawia moment, w którym silnik wisi nad ramą i jest gotowy do zamocowania.
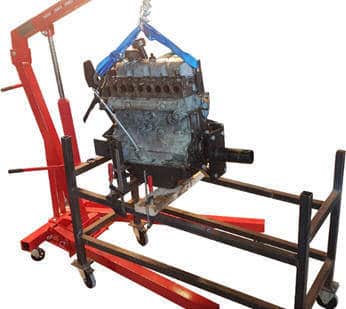
Poduszki silnika po stronie rozdzielczej wykonane są z rur stalowych i profili U. Tłumienie zapewnia guma motocyklowa. Dwie rury są zamontowane jedna na drugiej w dolnej części, aby zamontować blok silnika i skrzynię biegów możliwie poziomo na ramie. Wsporniki mocuje się do bloku silnika i ramy za pomocą prętów gwintowanych M8 i M12, śrub i nakrętek.
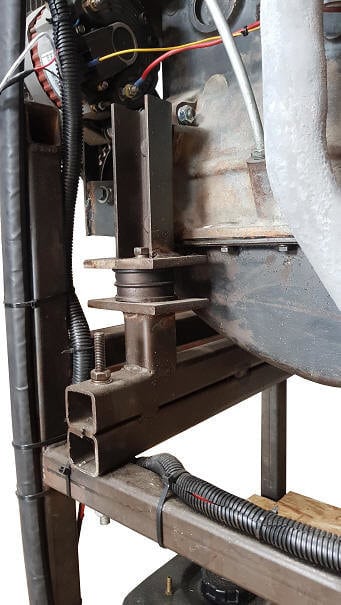
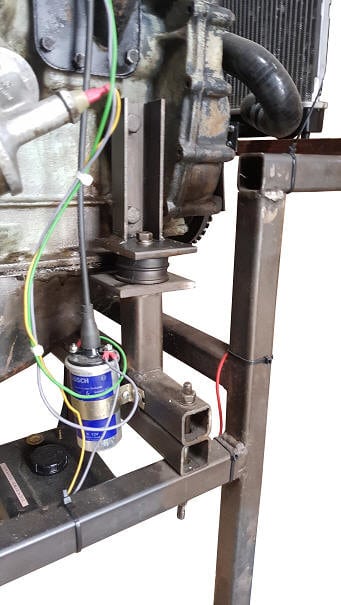
Takie podparcie skrzyni biegów zostało wykonane po obu stronach skrzyni biegów, z którą opiera się ona na ramie.
Po bezpiecznym i niezawodnym zamontowaniu silnika i skrzyni biegów do ramy można było wznowić montaż silnika. Po zamontowaniu regulowanych i regulowanych części, takich jak gaźnik i zapłon, zostały one wyregulowane zgodnie z wartościami fabrycznymi.
Na ramie zamontowane są również inne elementy umożliwiające pracę silnika, takie jak chłodnica, deska rozdzielcza ze sterownikami i zbiornik paliwa. Komponenty te opisano w poniższych akapitach.
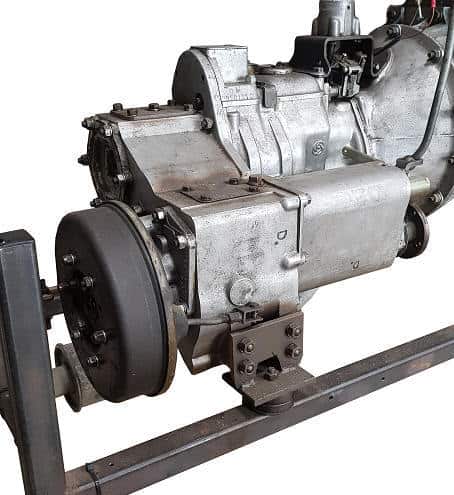
Chłodzenie:
W oryginalnym stanie chłodzenie zapewnia duży radiator i metalowy wentylator chłodzący zamontowany na pompie wody. Ponieważ silnik nie jest montowany w pojeździe, ale na ruchomej ramie, ważne jest, aby zastosować odpowiednie części zamienne. Metalowy wentylator chłodzący został zastąpiony zasilanym elektrycznie wentylatorem chłodzącym z plastikowymi łopatkami. Wersja plastikowa jest nie tylko znacznie bezpieczniejsza, ponieważ silnik jest przystosowany do celów edukacyjnych (dokonując pomiarów należy wziąć pod uwagę bezpieczeństwo osobiste), ale także lepiej nadaje się do szybszego nagrzewania chłodnicy i bloku silnika. Elektryczny wentylator chłodzący można włączać i wyłączać za pomocą przycisku na desce rozdzielczej. Umożliwia to szybkie rozgrzanie silnika, ponieważ istnieje niewielka możliwość obciążenia go mechanicznego. Kiedy silnik jest rozgrzany, bardziej prawdopodobne jest wystąpienie „zamkniętej pętli”, w której dane z sondy lambda wykorzystywane są do sterowania wtryskiem paliwa. Przykładowo, gdy silnik jest zimny – w „pętli otwartej” – następuje dodatkowe wzbogacenie: przy wtrysku większej ilości paliwa (λ < 1) korekta paliwa przez sondę lambda jest niepożądana.
Rysunek przedstawia przegląd elementów zainstalowanego układu chłodzenia. Oryginalnego grzejnika nie było. Ponieważ jego rozmiar i waga nie nadawały się do montażu na ramie motocykla, wybrano mniejszą chłodnicę z rynku wtórnego. Średnice przyłączy górnego i dolnego węża chłodnicy odpowiadają oryginalnym.
Górne i dolne węże chłodnicy są wykonane na zamówienie z silikonowych węży i złączy. Elektryczny wentylator chłodzący jest przymocowany do wspornika montażowego. Górny wąż chłodnicy zabezpiecza chłodnicę przed przewróceniem. Korek nadciśnieniowy (0,9 bar) chroni układ chłodzenia przed nadmiernym ciśnieniem. Gdy ciśnienie wzrośnie zbyt mocno, zawór w korku chłodnicy otwiera się pod wpływem siły i płyn chłodzący przepływa przez przelew do pojemnika zbiorczego.
Należało sprawdzić eksperymentalnie, czy chłodnica ma wystarczająco duży przepływ i czy wentylator chłodzący ma wystarczającą wydajność, aby odprowadzić ciepło. W pierwszej fazie testów stwierdzono, że system jest sprawny.
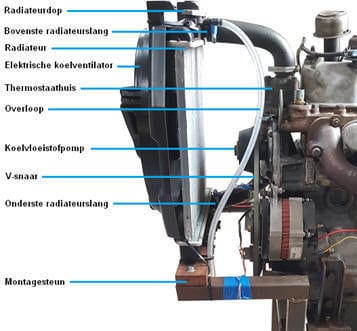
Deska rozdzielcza i instalacja elektryczna:
Do ramy przymocowana jest deska rozdzielcza, na której znajdują się kontrolki, przełączniki, sterownik MegaSquirt, różne przekaźniki i wiązki kablowe. Deska rozdzielcza służy do monitorowania i sterowania funkcjami silnika.
Na zdjęciu widać deskę rozdzielczą. Numer 1 na rysunku wskazuje lokalizację uziemnika; kluczyk odłącza akumulator od masy. Ponieważ nie ma potrzeby zasilania wyłączonego silnika, bezpieczniej jest odłączyć uziemienie, gdy silnik pozostaje bez nadzoru. Numer 2 oznacza przełącznik wentylatora chłodzącego. Numery 3 i 4 to kontrolki alternatora (D+), numer 5 to przycisk startu, a numer 6 to włącznik zapłonu (zacisk 15). Z tyłu deski rozdzielczej znajduje się skrzynka bezpieczników. MegaSquirt jest montowany na dolnym panelu i jest oznaczony numerem 7. Numer 8 wskazuje przekaźnik pompy paliwa. Na desce rozdzielczej istnieje również możliwość zamontowania skrzynki rozdzielczej, na której uczniowie mogą dokonywać pomiarów. Umożliwia to pomiar wartości czujników i elementów sterujących siłownikiem za pomocą oscyloskopu.
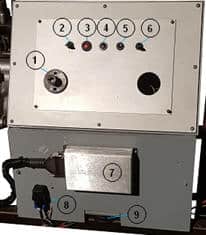
Oryginalny przekaźnik rozrusznika steruje rozrusznikiem; Za pomocą małego przycisku startu pin 86 jest podłączony do masy, powodując przepływ prądu sterującego. Prąd sterujący wytwarza pole magnetyczne, powodując przepływ prądu głównego pomiędzy zaciskami 30 i 87; rozrusznik jest zasilany tym prądem głównym do chwili zwolnienia przycisku startu.
Zmodernizowany alternator dostarcza napięcie i prąd ładowania do akumulatora. Lampka kontrolna informuje, czy alternator ładuje prawidłowo. Sonda lambda, wtryskiwacze i cewka zapłonowa otrzymują napięcie zasilające ze skrzynki bezpieczników. Przesyłanie informacji oraz polecenia włączania i wyłączania MegaSquirt są realizowane poprzez inne przewody sygnałowe i uziemiające.
Pompa paliwa i zbiornik.
Mechaniczna pompa paliwa w klasycznej konfiguracji nie jest już używana podczas montażu elementów układu sterowania silnikiem, ponieważ ciśnienie robocze jest zbyt niskie (200 mbar). Wymagane ciśnienie paliwa dla wtryskiwaczy MPI sterowanych przez ECU MegaSquirt wynosi 3 bary. Wystarczy standardowa elektroniczna pompka paliwa z samochodu osobowego. Ze względu na ograniczoną przestrzeń wybrano kompaktową jednostkę, w której zbiornik paliwa, pompa i filtr znajdują się w jednej obudowie. Metalowa rama umożliwia montaż urządzenia do ramy silnika. W dalszej fazie projektu zostaną zamontowane przewody paliwowe łączące pompę paliwa z wtryskiwaczami w kolektorze dolotowym.
Przewody zasilające od pompy paliwa biegną kanałem kablowym do tablicy rozdzielczej, sposób montażu został już opisany. Przewód dodatni pompy jest zasilany przez MegaSquirt poprzez przekaźnik.
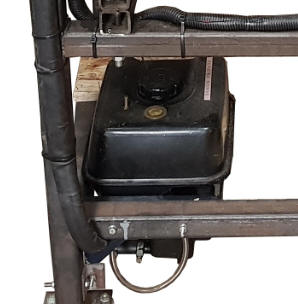
Uruchom silnik w klasycznej konfiguracji.
Przed zamontowaniem elementów układu sterującego silnikiem, silnik został początkowo przystosowany do pracy w klasycznej konfiguracji, tj. z zapłonem gaźnikowym i rozdzielaczem. W rozdziale 5.2 opisano prace jakie miały miejsce przy montażu silnika i podzespołów pomocniczych na ramie silnika. W pierwszej fazie testów, gdy silnik został uruchomiony w układzie klasycznym, można było przeprowadzić kontrole w następujących warunkach:
- Chłodny początek;
- na biegu jałowym;
- Zwiększona prędkość, zwiększone obciążenie;
- Długotrwała praca w temperaturze roboczej.
Podczas powyższych kontroli okazało się, że pozostało jeszcze do wykonania szereg napraw zanim silnik stał się na tyle niezawodny, że można go było poddać konwersji.
- Po pierwszym uruchomieniu silnika okazało się, że uszczelka w pompie płynu chłodzącego jest już niesprawna; wyciekł płyn chłodzący z bloku silnika wzdłuż łożyska. Wymiana pompy płynu chłodzącego wystarczyła, aby rozwiązać problem.
- Następnym problemem było zgaśnięcie, gdy silnik osiągnął temperaturę roboczą. Zapłon uległ awarii, co uniemożliwiło uruchomienie silnika. Problem tkwił w dystrybutorze i można go było łatwo rozwiązać.
- Z biegiem czasu pomiędzy silnikiem a skrzynią biegów powstał wyciek oleju. Wyciek prawdopodobnie pochodzi z uszczelniacza wału korbowego. Wyciek ten zostanie usunięty po zakończeniu inwestycji.
Po stwierdzeniu, że silnik jest w porządku w klasycznej konfiguracji, mogliśmy kontynuować prace nad elektroniką.
Volgende: czujniki.