Przedmioty:
- Silnik BMW
- Wstępne prace nad projektem
- Sprawdzanie pompy olejowej
- Usuń od dystrybutora
- Układ rozruchu i ładowania
- Rama z monitorami i komputerem
- Deska rozdzielcza z instalacją elektryczną
- Chłodzenie
- Zbiornik paliwa
- Rura wlotu powietrza, filtr powietrza, węże odpowietrzające skrzynię korbową
Silnik BMW
Szybko podjęto decyzję o zastosowaniu tego silnika BMW w tym projekcie konwersji; było zbyt wiele defektów, przy których uczniowie mogli majstrować, ale wciąż było wystarczająco dobrych, aby je naprawić. Silnik pochodzi z BMW serii 5 E34. Poniższa tabela przedstawia dane silnika.
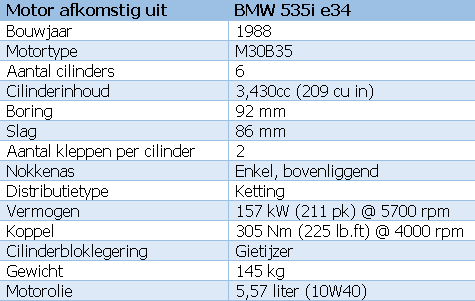
Pierwsze działania projektu:
Jak wskazano wcześniej, silnik BMW jest w dobrym stanie. Wysoce zmotywowany uczeń natychmiast zaczął usuwać załączniki. Wiązka przewodów, oryginalny ECU i wtyczka diagnostyczna ODB1 zostały trwale usunięte. Inne części takie jak pokrywa zaworów, kolektory łącznie z wydechem, rama z chłodnicą są sprawdzane, czyszczone, a następnie ponownie instalowane z nowymi uszczelkami, o-ringami i obejmami węży. Zawory są wyregulowane, pompa płynu chłodzącego wymieniana profilaktycznie ze względu na wiek i rdzę.
Oczywiście olej jest wymieniany, a układ chłodzenia czyszczony. W późniejszym etapie, gdy silnik pracuje co najmniej godzinę, następuje ponowna wymiana płynów i wymiana filtrów.
Zdjęcia poniżej przedstawiają początek projektu demontażu osprzętu i regulacji luzów zaworowych. Kliknij na zdjęcia, aby otworzyć je w pełnym rozmiarze.
Sprawdzanie pompy olejowej:
Podczas sterowania rozrusznikiem zwrócono uwagę na obieg oleju w głowicy cylindrów. Podczas rozruchu nie było widać dopływu oleju do wałka rozrządu itp. Nie było wiadomo czy pompa oleju i filtr ssący są sprawne; W końcu silnik był używany w przeszłości do zadań praktycznych. Być może czegoś brakowało w dostawie ropy. Podjęto więc decyzję o rozebraniu miski olejowej i sprawdzeniu pompy oleju oraz filtra siatkowego.
Po demontażu i sprawdzeniu stwierdziliśmy, że pompa olejowa i akcesoria są w porządku. Części zostały ponownie zmontowane i uzupełniono olej.
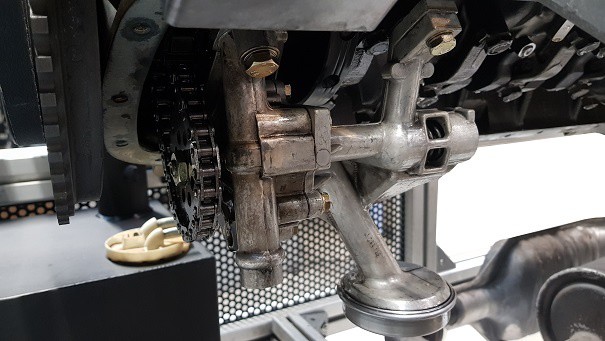
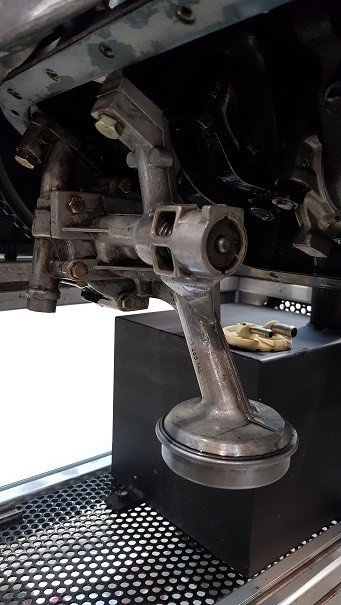
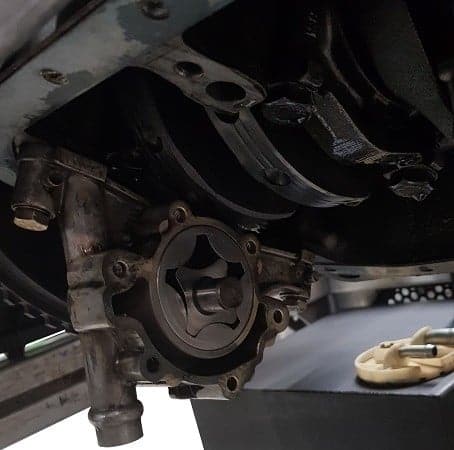
Aby usunąć dystrybutora:
Układ zapłonowy wyposażony jest w cewkę zapłonową DIS. Usuwamy oryginalną cewkę zapłonową i rozdzielacz. Po usunięciu dystrybutora pozostała odsłonięta dziura w głowicy cylindrów. Widoczny jest tutaj koniec wałka rozrządu i uszczelka wałka rozrządu. W późniejszym etapie można tu zamontować czujnik położenia wałka rozrządu w połączeniu z MegaSquirtem III (na razie używamy MS-II). Aby całość ładnie zakryć, w programie AutoCAD narysowano okładkę i utworzono ją na drukarce 3D. Zdjęcie zostało zrobione 10 minut po rozpoczęciu drukowania. Łącznie drukowanie trwało 3,5 godziny.
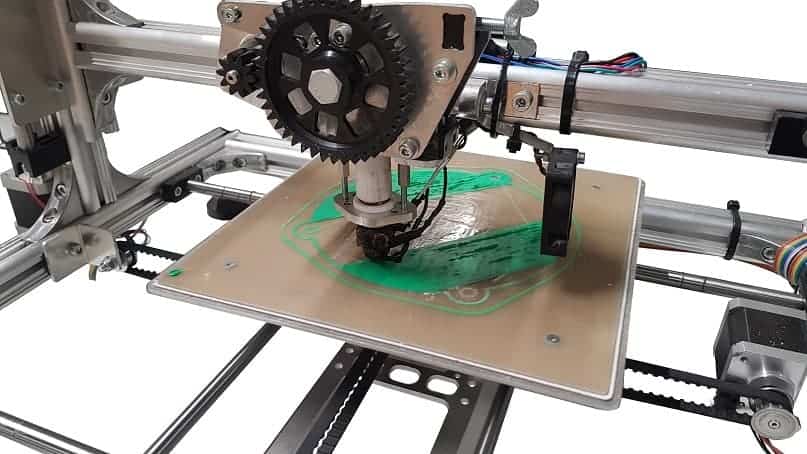
Układ rozruchu i ładowania:
Jedną z widocznych usterek był uszkodzony przekaźnik rozrusznika. Przynajmniej gwintowany koniec się ułamał. Naprawa przekaźnika rozrusznika wydawała się niemożliwa. Na szczęście koszty nie okazały się zbyt duże: lokalny specjalista od remontów dostarczył nowy przekaźnik rozrusznika za 25 euro. Zdjęcie przedstawia wadliwy (po lewej) i nowy (po prawej).
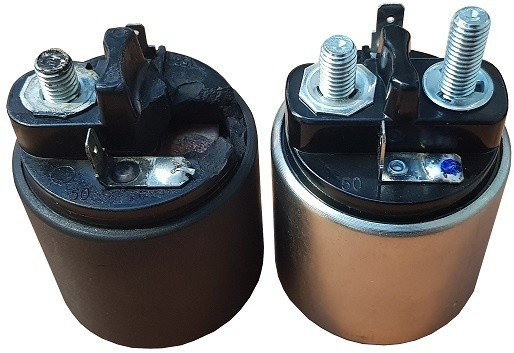
Mniej szczęścia mieliśmy z dynamem. Po podłączeniu przewodów dodatnich podczas podłączania przewodu uziemiającego odkryto, że gdzieś w układzie nastąpiło zwarcie. Po krótkich poszukiwaniach odnaleziono przyczynę; B+ alternatora zetknął się z obudową. Rezystancja pomiędzy zaciskiem B+ i obudową wynosiła 0,2 oma. Dynamo zostało natychmiast zdemontowane i otwarte. Co się okazało? Złącze D+ zetknęło się z obudową, ponieważ wnętrze obudowy nie było proste i plastikowa tulejka była pęknięta. Alternator nigdy nie działał w ten sposób; Prawdopodobnie jakiś student rozebrał alternator w ostatnich latach, gdy silnik przestał działać, i nie złożył go prawidłowo.
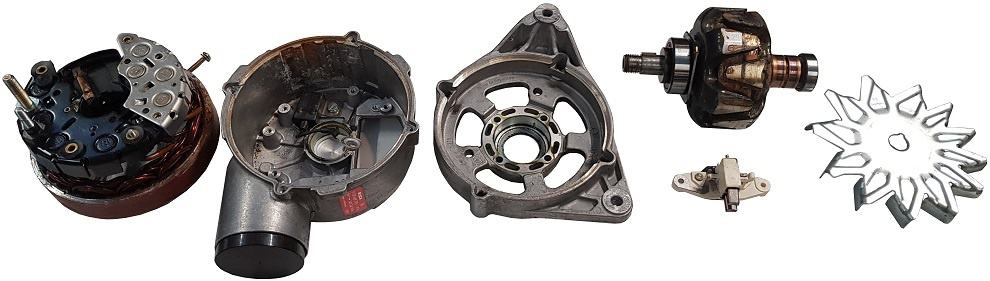
Po naprawie rozrusznika i alternatora przystąpiono do okablowania. Czerwone przewody widać na obrazku poniżej.
Przewód dodatni akumulatora jest podłączony do złącza B+ alternatora. Przewód dodatni do rozrusznika jest również zamontowany na tym samym kołku.
Przewód D+ alternatora jest podłączony do bezpiecznika (zacisk 15) poprzez lampkę kontrolną prądu ładowania na desce rozdzielczej. Przewód sterujący rozrusznika (zacisk 50) obsługiwany jest za pomocą przycisku start na desce rozdzielczej.
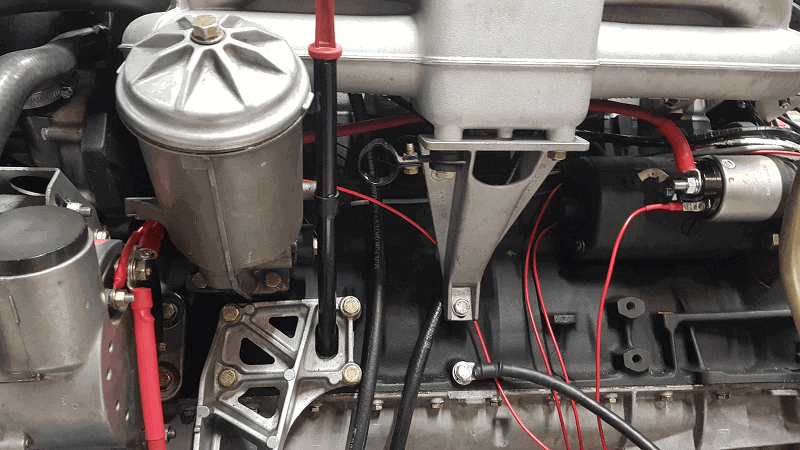
Rama z monitorami i komputerem:
Na ramie motocykla montowany jest komputer stacjonarny z dwoma ekranami. Na tych ekranach zostaną ostatecznie wyświetlone wskaźniki i mapy na desce rozdzielczej. Możliwe jest także zademonstrowanie pomiarów za pomocą oscyloskopu (pikoskopu) na ekranie.
Rama została zaprojektowana w taki sposób, aby oba ekrany można było zamontować jeden pod drugim. Ekrany są pochylone pod pewnym kątem, dzięki czemu można je wyraźnie odczytać stojąc przed motocyklem.
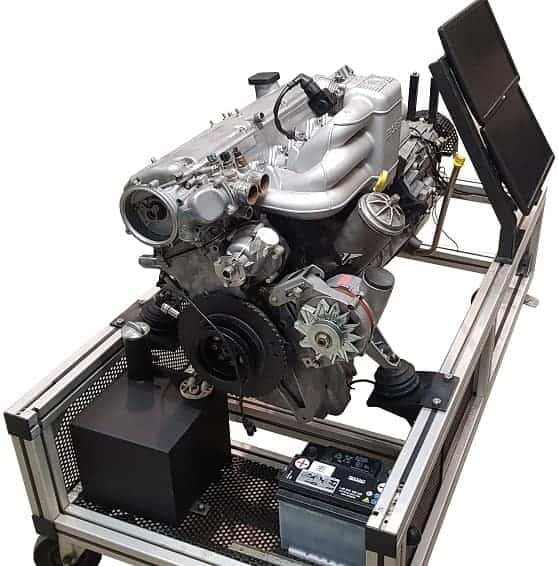
Komputer stacjonarny jest umieszczony za ekranami na ramie silnika. Komputer jest marki Dell i typu Optiplex XE (Core2Duo 2,6 GHz, 4 GB RAM). Ten typ komputera jest przeznaczony do pracy 24 godziny na dobę, 7 dni w tygodniu w ciężkich zastosowaniach biznesowych, na przykład w ciepłych i zakurzonych obszarach. Dlatego ten komputer PC idealnie nadaje się do montażu na ramie motocykla przy pracującym silniku. Standardowy dysk twardy został zastąpiony dyskiem SSD, aby ryzyko wystąpienia drgań było jak najmniejsze. Sponsorem komputera i monitorów jest firma Zenid.net.
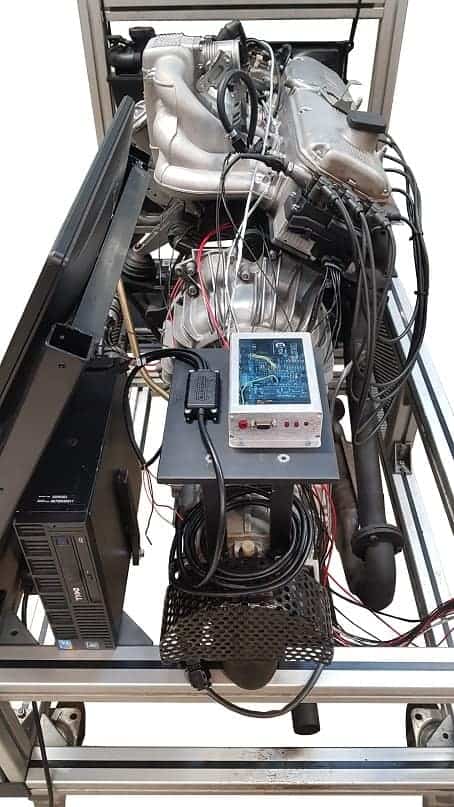
Deska rozdzielcza z instalacją elektryczną:
Pod ekranami umieszczono panel z wieloma elementami. Na zdjęciu widać tył panelu z okablowaniem.
Od lewej do prawej:
- Odłącznik uziemienia
- Wyłącznik zapłonu (zacisk 15) i przycisk startu (zacisk 50)
- Przełącznik wentylatora chłodzącego
- Zacisk lampy 15
- Lampka kontrolna prądu ładowania D+
- Skrzynka bezpieczników 1 (6x)
- Skrzynka bezpieczników 2 (6x)
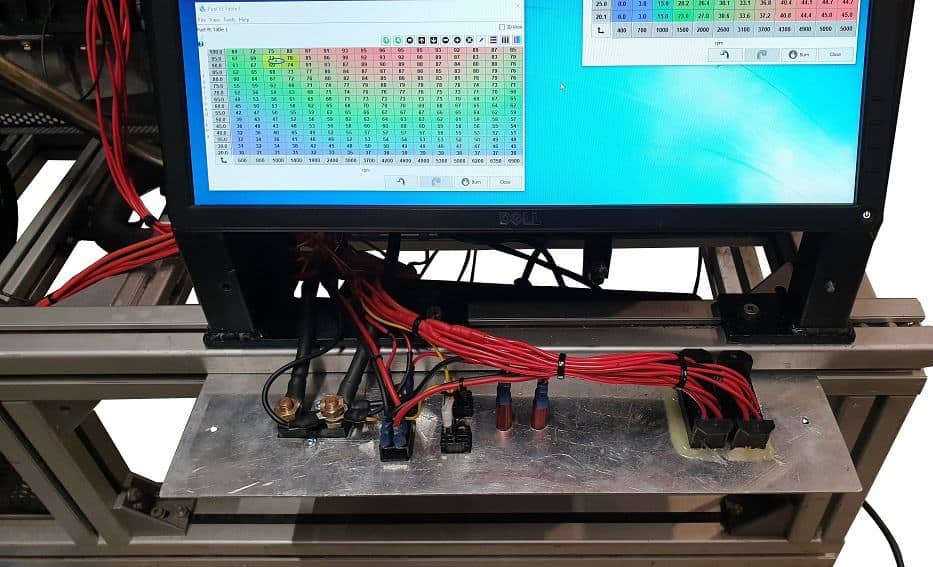
Schemat elektryczny został niedawno zmieniony. Nowa wersja zostanie wkrótce dodana do tej strony.
Chłodzenie:
Oryginalne elementy układu chłodzenia były niekompletne, brudne i/lub wadliwe. Oprócz nowej pompy płynu chłodzącego, która została wymieniona zapobiegawczo, zamontowano także następujące części:
- Kaloryfer;
- Zbiornik płynu chłodzącego;
- Sześć nowych węży chłodnicy;
- Wentylator chłodzący.
Te komponenty nie pochodzą z E34, ale E46 (seria 3). Rozmiar chłodnicy, średnica węży chłodzących i moc wentylatora chłodzącego są wystarczające, aby zapewnić dobre chłodzenie. Wentylator chłodzący ma moc nie mniejszą niż 390 W.
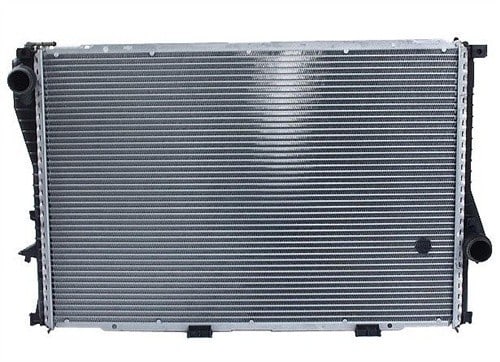
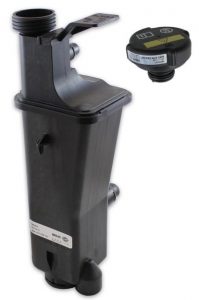
Powyższe zdjęcia przedstawiają chłodnicę i zbiornik wyrównawczy. Składniki te należą do siebie; zbiornik można przymocować do chłodnicy od góry i od dołu. Wymaga to specjalnej ramy, która znajduje się pomiędzy nimi. Ta ramka nie jest pokazana.
Zdjęcie poniżej przedstawia wentylator chłodzący. Wentylator jest również częścią chłodnicy i zbiornika; te trzy części są ze sobą połączone. Poniższy obrazek pokazuje również moment, w którym zawieszono w ramie elementy chłodzące, składające się z tych właśnie opisanych. W ten sposób można regulować wysokość i odległość pomiędzy obudową termostatu a rurką zbiornika. Docelowo wkłada się tu wąż chłodzący w kształcie litery S.
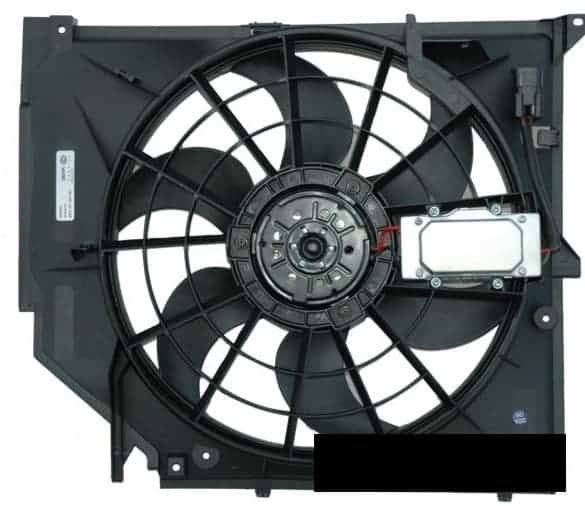
Grzejnik montuje się w następujący sposób:
- klocki gumowe umieszcza się pomiędzy chłodnicą a poziomą belką ramy silnika, tak aby chłodnica mogła na nich stanąć;
- dzięki żelaznym prętom po lewej i prawej stronie grzejnik jest zaciśnięty we wszystkich kierunkach;
- Żelazne pręty u góry zapewniają, że grzejnik nie może się przechylić.
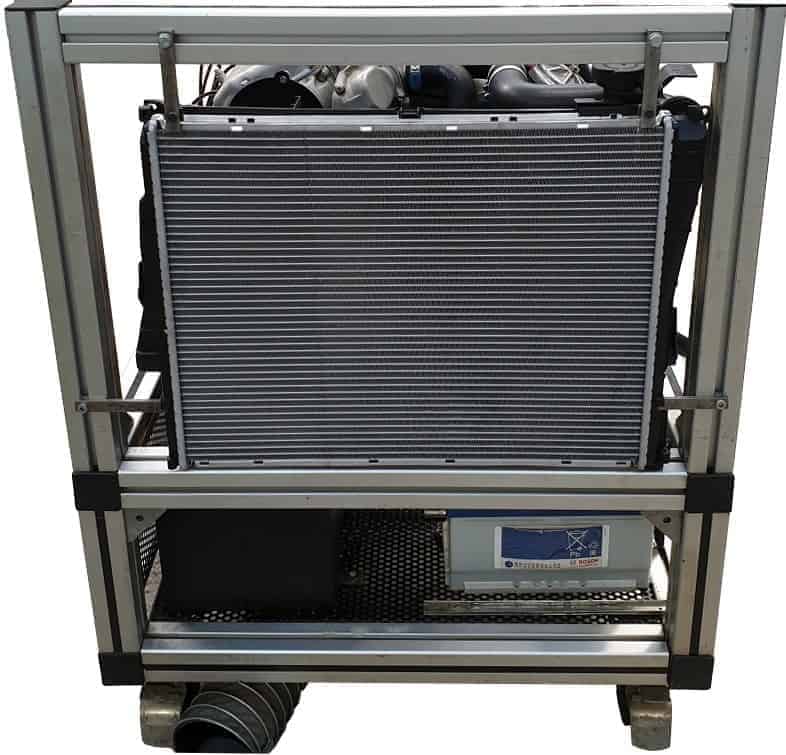
Wąż chłodzący o oryginalnych wymiarach montowany jest standardowo na kołnierzu, który jest zatrzaskiwany na górze chłodnicy. Zagięcia węża nie odpowiadają przestrzeni jaką dysponujemy w tym silniku. Dlatego też zdemontowano standardowy wąż chłodzący z kołnierza i zeszlifowano obkurczony wokół niego pierścień. Zamiast tego przycięto dwa węże o średnicy 38 mm (G4278-17033) i zamontowano je w kolanie w kształcie litery S.
Przez chwilę szukaliśmy dobrego mocowania dwóch węży. Plastikowa rura PCV okazała się zbyt miękka i odkształcała się pod wpływem ciepłego płynu chłodzącego, więc była nieodpowiednia. Sklep z częściami samochodowymi zaczął szukać i ostatecznie zaproponował mosiężną złączkę węża (WK 34305), która idealnie pasowała. Dzięki żebrowanej powierzchni zewnętrznej węże doskonale się zaciskają.
Poniższy rysunek przedstawia mosiężne złącze węża stanowiące połowę jednego węża chłodzącego. Drugi wąż chłodzący jest również zamontowany na złączce węża, a opaski zaciskowe są mocno dokręcone.
Ten sam typ złącza węża montowany jest również pomiędzy dwoma innymi wężami chłodzącymi na dole chłodnicy.
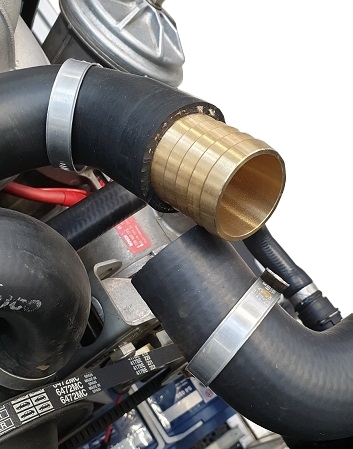
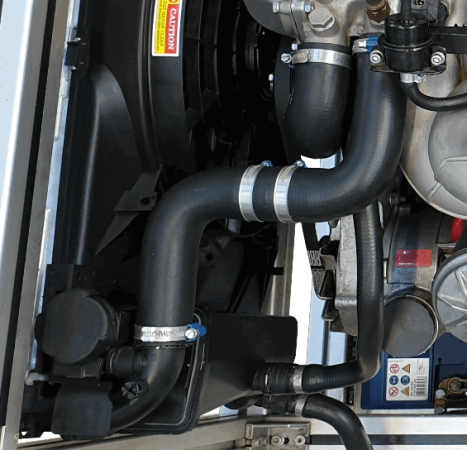
Zbiornik paliwa:
Zbiornik paliwa o pojemności 20 litrów stał już w tym samym miejscu w swoim dawnym stanie. Zbiornik mocowany jest do ramy silnika i znajduje się w rogu obok akumulatora, pod dolnym wężem chłodnicy. Zbiornik zamyka oryginalna chromowana nakrętka.
Poniższy rysunek przedstawia zbiornik paliwa i dwa przewody paliwowe. Jednym z nich jest podaż, a drugim powrót. Węże idą do listwy paliwowej, gdzie zamontowane są wtryskiwacze. Elementy te opisano w rozdziale „Siłowniki”.
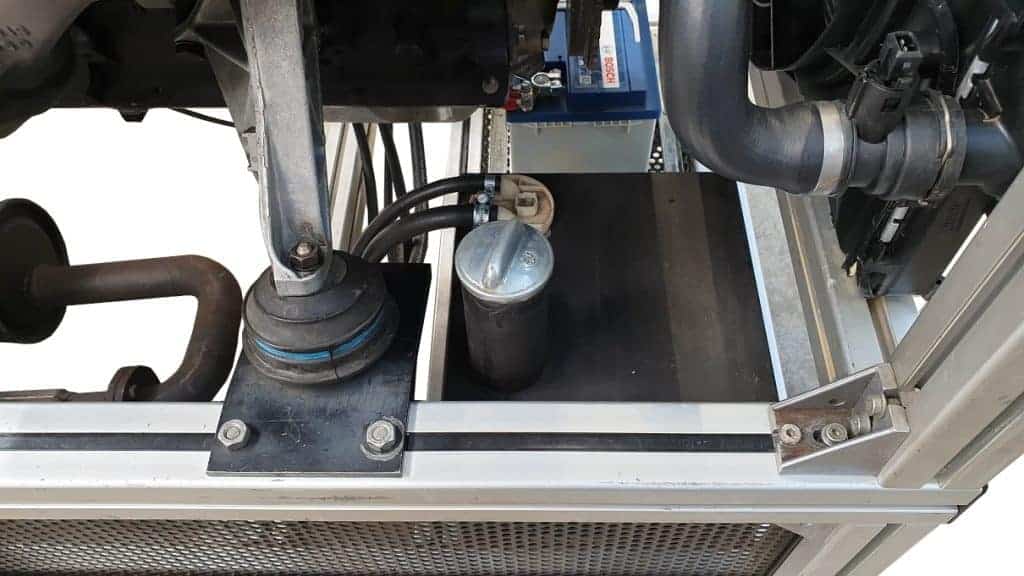
Rura wlotu powietrza, filtr powietrza, węże odpowietrzające skrzynię korbową:
Brakowało oryginalnej rury wlotu powietrza, przewodów odpowietrzających skrzynię korbową, zaworu sterującego biegiem jałowym PWM i obudowy filtra powietrza. Nawet jeśli było wiele części, istniało duże prawdopodobieństwo, że wystąpią pęknięcia ze względu na wiek i częsty demontaż/montaż. Części te poza zaworem sterującym PWM zostały zakupione jako nowe. Przewód wlotowy powietrza i węże odpowietrzające skrzynię korbową zostały zamówione u dealera BMW. Oryginalna obudowa filtra powietrza nie pasowała idealnie do ramy silnika, dlatego szybko podjęto decyzję o zamontowaniu filtra powietrza na świeżym powietrzu. Filtr powietrza (K&N, KNRC-3250) miał taką samą średnicę jak rurka dolotowa powietrza.
Korzystając z programu AutoCAD i drukarki 3D, zaprojektowano i wydrukowano przystawkę, którą można zamontować pomiędzy filtrem powietrza a rurą dolotową.
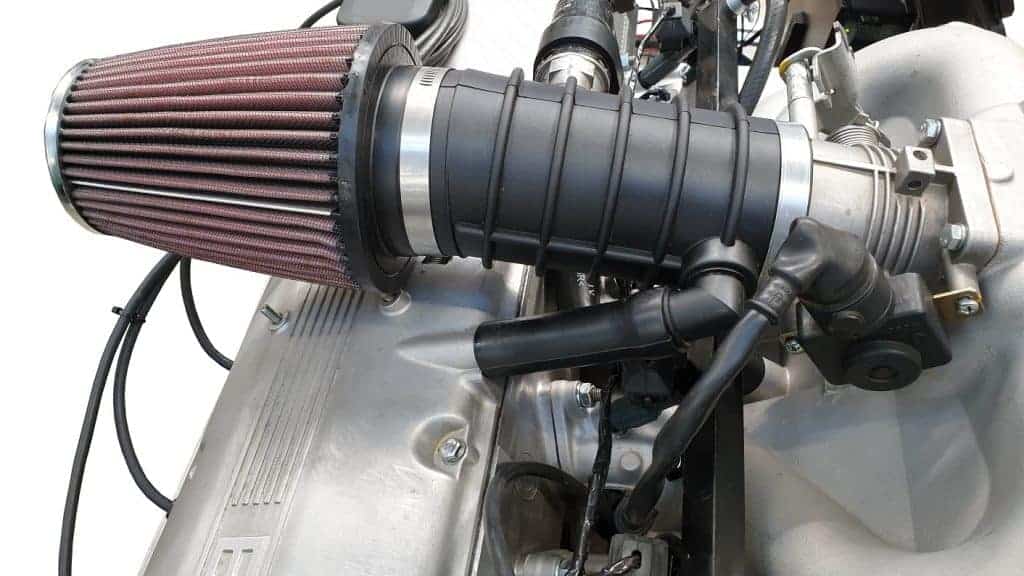