Przedmioty:
- Zarys ogólny
- Suwmiarka z noniuszem
- Wskaźnik śrubowy
- Wskaźnik zegarowy
- Szczelinomierz
- Plastiż
Ogólne:
Narzędzia pomiarowe są często stosowane w technice samochodowej, na przykład podczas kontroli silnika. Ale narzędzia pomiarowe służą również do pomiaru grubości okładzin hamulcowych lub tarczy hamulcowej. Aby dokonać pomiaru, ważna jest znajomość dokładności pomiarowej, z jaką zaprojektowano narzędzie. Średnicę cylindra można zmierzyć wewnętrznymi szczękami pomiarowymi suwmiarki, ale nie jest to wystarczająco dokładne (1/20 mm). Czujnik zegarowy jest znacznie dokładniejszy (1/100 mm).
Najpopularniejsze narzędzia pomiarowe w warsztacie i ich dokładność to:
- Suwmiarka z noniuszem (0,05 mm, co odpowiada 1/20 mm).
- Rozmiar śruby (0,01 mm lub 1/100 mm.)
- Wskaźnik zegarowy (0,01 mm.)
- Szczelinomierz (0,05 mm.)
- Plastige (dokładność w zależności od wersji).
Na tej stronie wyjaśniono, jak ustawić, odczytać i w razie potrzeby skalibrować wspomniane wcześniej narzędzia pomiarowe oraz przedstawiono przykłady pomiarów.
Suwmiarka z noniuszem:
Suwmiarka jest szeroko stosowanym narzędziem pomiarowym w technice samochodowej. Za pomocą suwmiarki można zmierzyć wymiary wewnętrzne, zewnętrzne i głębokość elementu z dokładnością do dwudziestego milimetra.
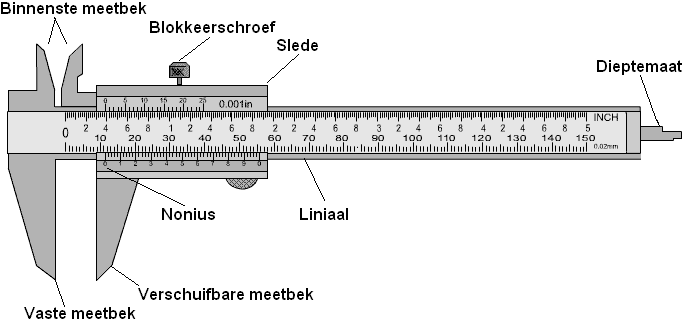
Pomiar za pomocą stałej szczęki pomiarowej:
Rozmiar można odczytać poprzez zaciśnięcie elementu w nieruchomej szczęce pomiarowej. Linijka wskazuje teraz 20 mm. Jest to średnica zewnętrzna pierścienia.
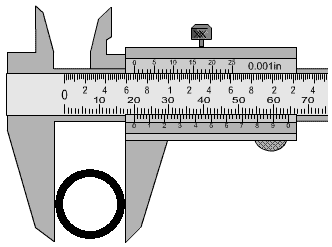
Pomiar za pomocą wewnętrznej szczęki pomiarowej:
Średnicę wewnętrzną można odczytać zaciskając szczękę pomiarową wewnątrz pierścienia. To jest 18mm. Oznacza to, że pierścień ma grubość (20-18) = 2 mm.
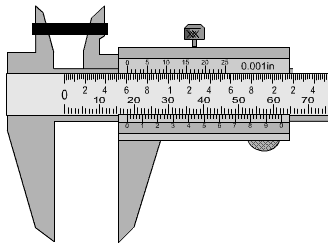
Pomiar za pomocą głębokościomierza:
Na przykład w przypadku obiektów, których nie można usunąć z powierzchni lub cylindrów z dnem, wysokość można zmierzyć za pomocą głębokościomierza. Umieszczając koniec głębokościomierza na powierzchni i grubszą część zacisku na elemencie, można określić jego wysokość. W tym przypadku wysokość czarnego bloku określa się:
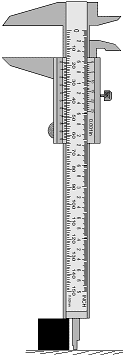
Aby odczytać suwmiarkę, należy również spojrzeć na dziesiąte części milimetra. Miejsce, w którym kolejna kreska noniusza pokrywa się dokładnie z linią linijki, oznacza pomiar w dziesiątych częściach milimetra (liczba po przecinku). Na obrazku 0 noniusza wynosi 1,1 cm, czyli 11 mm od linijki. Linia cyfry 10 na noniuszu pokrywa się z linią na linijce. Oznacza to, że jest dokładnie 11,0 mm wordt wymierzony.
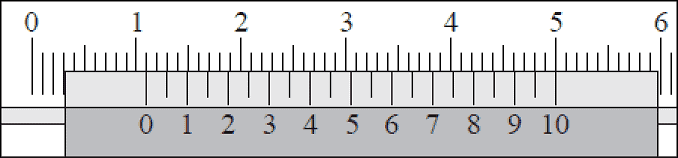
Podczas kolejnego pomiaru noniusz przesunął się nieco w lewo i mamy do czynienia z liczbą po przecinku. Patrzymy na miejsce, w którym kolejna linia noniusza pokrywa się dokładnie z linią linijki. Na obrazku 0 noniusza wynosi 1,1 cm, a więc 11 (całych) milimetrów. Linia cyfry 9 na noniuszu pokrywa się z linią na linijce. Oznacza to, że mierzy się dokładnie 10,9 mm.
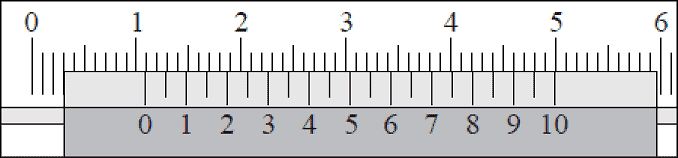
Pomiar na obrazie opiera się na tej samej zasadzie. W tym przypadku 0 noniusza znajduje się w połowie odległości między 15 a 16 mm linijki. Zatem już w zasadzie wiesz, że liczba dziesiętna powinna wynosić około 4, 5 lub 6. Linie linijki i noniusza odpowiadają liczbie 5; więc teraz mierzone jest (15+0,5) = 15,5 mm.
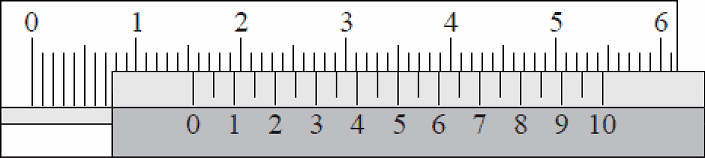
Pomiędzy liczbami na noniuszu znajdują się również małe linie. Wskazują one pięć setnych milimetra. Linia pomiędzy 0 a 1 na noniuszu odpowiada linii na linijce. Na rysunku (10 + 0,05) = 10,05 mm. Odczytanie pięciusetnych wymaga wprawnego oka.
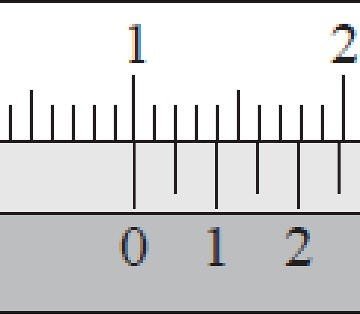
W tej animacji odczyt noniusza jest wyjaśniony czerwonymi strzałkami.

Suwmiarkę można również wykonać cyfrowo, jak pokazano na obrazku. Wymiary mierzonego elementu można odczytać na wyświetlaczu cyfrowym. Często można to ustawić zarówno na cale, jak i milimetry.
Istnieją również zaciski z analogowym czujnikiem zegarowym, w którym wyświetlacz cyfrowy znajduje się na powyższym obrazku. Suwmiarka ta nie jest zbyt często używana, ale zależy to od tego, czego użytkownik woli używać.
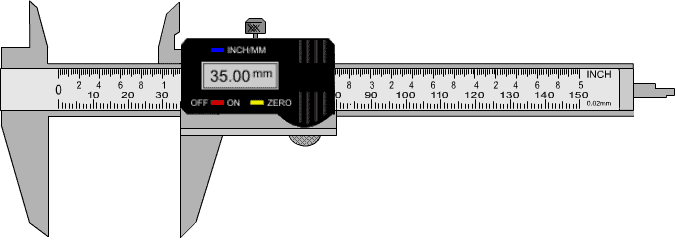
Rozmiar śruby:
Można zastosować miernik śrubowy (zwany także mikrometrem lub mikrometrem wspornikowym). Worden służy do pomiaru elementów o wielkości do 25 mm z dokładnością do jednej setnej milimetra (0,01 mm). Przy jednym obrocie bębna pomiarowego wrzeciono pomiarowe przesuwa się o 0,5 mm.
Mikrometr należy zawsze trzymać za izolowany uchwyt, ponieważ ciepło rąk wpływa na wynik pomiaru. Miejscowe ogrzewanie w mikrometrze może spowodować nieznaczne rozszerzenie materiału. Zwłaszcza w przypadku pomiaru, w którym wynik musi być mierzony z dokładnością do setnych, ważne jest przestrzeganie przepisów.
Element przeznaczony do pomiaru należy umieścić pomiędzy kowadłem a wrzecionem pomiarowym. Obracając bęben pomiarowy, wrzeciono pomiarowe porusza się do przodu i do tyłu. Zanim wrzeciono pomiarowe dotknie elementu, należy dokręcić ostatnią odległość śrubą czułości. Śruba sensoryczna zawiera mechanizm zatrzaskowy, który po przyłożeniu określonej siły wytwarza dźwięk „klikania”. W tym momencie wiesz, że nie możesz dalej kręcić licznikiem. Zbyt mocne dokręcenie mikrometru może spowodować nieprawidłowe wyniki pomiarów. Bęben pomiarowy można zablokować przed dalszym obrotem za pomocą dźwigni blokującej.
Poniżej znajduje się obraz mikrometru, na którym wielkość łożyska kulkowego (obiektu pomiaru) wordt wymierzony.
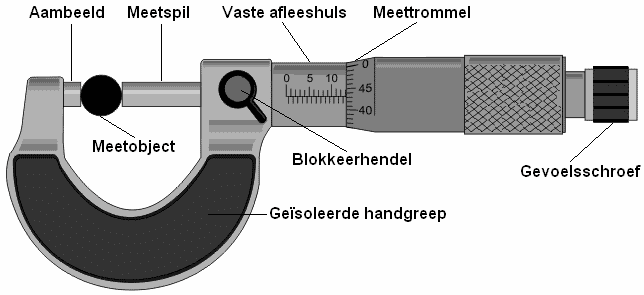
Na powyższym obrazku łożysko kulkowe ma grubość 13,43 mm. Na górnej skali widzisz 10, obok której znajdują się 3 linie. Każda linia ma jeden milimetr, więc 10+3=13 mm. Liczbę po przecinku odczytuje się na bębnie pomiarowym. Oto liczby 40 i 45. Jeśli przyjrzysz się uważnie, zobaczysz, że linia skali wynosi 43. Razem daje to 13,43 mm.
Bęben pomiarowy posiada skalę od 0,0 do 0,49 mm. Dzieje się tak dlatego, że skala z pełnymi milimetrami (na lewo od bębna pomiarowego) zawiera również pół milimetra; dolne linie wskazują pół milimetra. Poniżej podano szereg przykładów.
Całe milimetry są wyświetlane na linii poziomej. W tym przypadku jest to 13mm. Linia 16 mm na bębnie pomiarowym jest równa poziomej linii na tulei odczytowej. Rozmiar wskazany na tym obrazku to (13 + 0,16) = 13,16 mm.
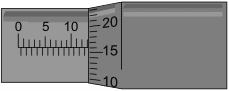
Na obrazku widoczna jest linia poniżej linii skali tulei odczytowej. Ta linia poniżej linii poziomej wskazuje, że jest to pół milimetra. Według skali wynosi co najmniej 5,5 milimetra (bez uwzględnienia bębna pomiarowego). Skala na bębnie pomiarowym wskazuje 36. Obecnie wskazany rozmiar wynosi łącznie (5,5 + 0,36) = 5,86 mm.
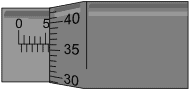
Na tym zdjęciu linia na dole skali jest ponownie najbliżej bębna pomiarowego. Czyli znowu co najmniej 12,5 mm według skali poziomej. Następnie dodajemy wskazaną wartość bębna pomiarowego; wartość ta wynosi 0,35 mm. Następnie dodajemy do siebie 12,5 i 0,35.
Razem jest to (12,5 + 0,35) = 12,85 mm.
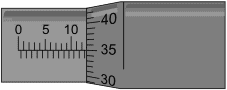
Na tym obrazku wskazany rozmiar to (16 + 0,355) = 16,355 mm.
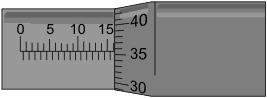
Zdjęcie pokazuje rozmiar śruby o wartości 75,235 mm. Skala na bębnie pomiarowym wynosi od 23 do 24 mm. Ponieważ kaliber wynosi 75 mm, rozmiar śruby różni się o 0,235 mm. Każdy pomiar, który zostanie wykonany, będzie zatem zbyt wysoki. Tuleję odczytową należy obrócić względem rękojeści za pomocą odpowiedniego widelca regulacyjnego. Widełki regulacyjne widać na powyższym obrazku.
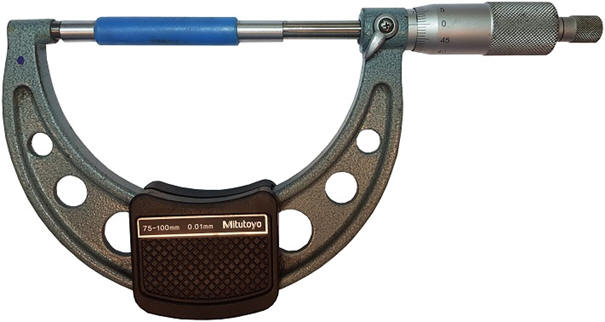
Przed pomiarem mikrometrem należy go najpierw skalibrować. Nieprawidłowa kalibracja prowadzi do błędów pomiaru! Rozmiar śruby kalibruje się przy użyciu odpowiedniego kalibru. Kaliber na poniższym obrazku wynosi dokładnie 75,00 mm. Oznacza to, że gdy miernik śrubowy mierzy kaliber, miernik śrubowy musi dokładnie wskazywać tę liczbę. Jeśli zmierzona wartość jest błędna, należy najpierw skalibrować rozmiar śruby, obracając bęben wewnętrzny widelcem.
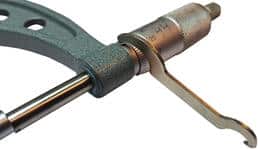
Wskaźnik zegarowy:
Bardzo dokładny pomiar głębokości można przeprowadzić za pomocą czujnika zegarowego. Mała wskazówka po wewnętrznej stronie wskazuje całe milimetry, a duża wskazówka wskazuje liczbę po przecinku. Kiedy czujnik zegarowy jest umieszczony na prostej powierzchni, powinien wskazywać 0,00 mm, jak pokazano na poniższym rysunku. Pierścień zewnętrzny można obracać, aby umożliwić kalibrację. Jeśli po umieszczeniu na płaskiej powierzchni zmierzone zostanie 0,3 mm, pierścień zewnętrzny należy obrócić tak, aby duża wskazówka wskazywała 0.
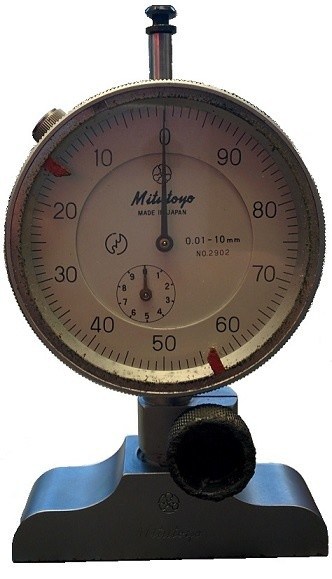
Wskaźnik zegarowy na zdjęciu wskazuje 5,00 mm. Mała wskazówka wynosi 5, a duża wskazówka wynosi 0. Jeśli duża wskazówka byłaby na poziomie 81, a mała wskazówka mieściłaby się w przedziale od 5 do 6, licznik wskazywałby wartość 5,81 mm. Im bardziej trzpień pomiarowy zostanie wciśnięty w górę w dół, tym mniejsza będzie odczytana wartość.
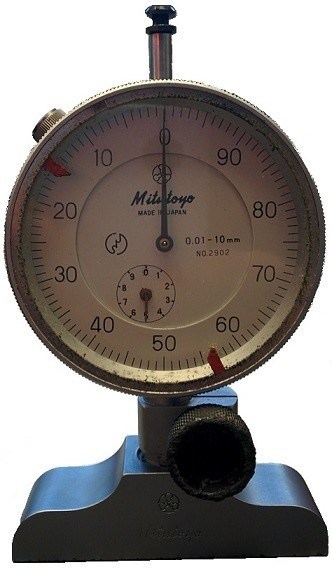
Tarcza mikrometru wskazuje: 0.01 – 10 mm. Oznacza to, że mikrometr może wskazywać wartość od 0.01 do 10 mm. Nie da się zatem dokonać pomiaru głębokości przy głębokości 12 mm, ponieważ trzpień pomiarowy jest na to za krótki i wskazówki nie są w stanie tego wskazać. Aby móc mierzyć wartości większe niż 10 mm, wraz z mikrometrem dostarczane są różne przedłużki. Przykład tego można zobaczyć na obrazku. Rozciągnięcie mierzy się tutaj za pomocą mikrometru. Oznacza to wartość 10,0 mm.
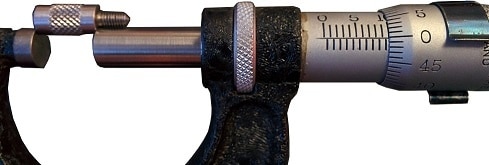
Mierzona jest tylko część w kształcie beczki, a nie gwint śruby. Dzięki zamontowaniu tego przedłużenia na mikrometrze pręt pomiarowy nie jest już za krótki. Można teraz nadal zmierzyć wartość na przykład 12 mm. Należy teraz upewnić się, że do zmierzonej wartości dodano wielkość przedłużenia. Oto przykład: gdy mikrometr wskazuje wartość 5,19 mm, rzeczywistym rozmiarem jest zmierzona wartość + długość trzpienia pomiarowego, więc 5,19 + 10,00 = 15,19mm.
Pomiary są wykonywane za pomocą czujnika zegarowego na tych stronach:
Szczelinomierz:
Szczelinomierz służy do pomiaru odstępu pomiędzy dwiema częściami. Szczelinomierz składa się z szeregu metalowych pasków, z których każdy ma inną grubość. Grubość podana jest na metalowym pasku. Dolny pasek szczelinomierza na poniższym obrazku ma oznaczenie „30”. Oznacza to, że metalowy pasek ma grubość 0,30 mm.
Aby zmierzyć odstęp między dwiema częściami, należy rozłożyć dowolny metalowy pasek i wsunąć pomiędzy częściami. Jeżeli pasek można przesuwać bardzo łatwo lub nawet bez oporu, wówczas przestrzeń jest większa niż grubość paska. Trzeba więc rozłożyć grubszy metalowy pasek. Jeśli pasek już nie pasuje, oznacza to, że jest za gruby. Jeśli pasek można wsunąć pomiędzy częściami z pewnym oporem, to jest to właściwy rozmiar.
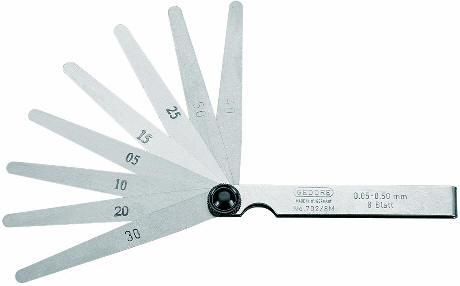
Poniższy rysunek mierzy luz końcowy pierścienia tłokowego.
Pomiarów dokonuje się szczelinomierzami na poniższych stronach:
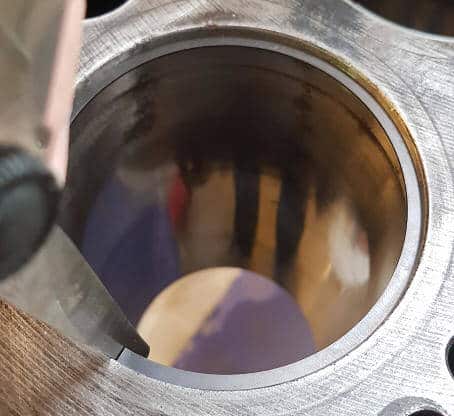
Plastygacja:
Do sprawdzenia luzów pomiędzy łożyskami ślizgowymi można zastosować Plastige. Plastige to specjalny drut z tworzywa sztucznego, który należy nałożyć na część, pomiędzy którą należy zmierzyć luz. Następnie należy zabezpieczyć pokrywę łożyska tak, aby plastigage został dociśnięty płasko. Miarą luzu jest odkształcenie plastigage.
Istnieją różne kolory plastigage. Każdy kolor reprezentuje inny rozmiar.
- Zielony: dla luzu łożyskowego od 0,025 do 0,076 mm.
- Czerwony: 0,050 – 0,150 mm.
- Niebieski: 0,102 – 0,229 mm.
- Żółty: 0,23 – 0,51 mm.
Na tej stronie wykonywany jest pomiar plastyką:
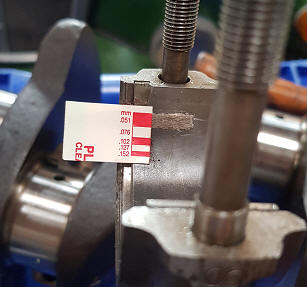
Powiązane strony: