Przedmioty:
- Wtrysk pośredni i bezpośredni
- Kontrola ciśnienia paliwa z wtryskiem pośrednim
- Strategia wtrysku wtrysk wielopunktowy
- Wtryskiwacz elektromagnetyczny (MPI)
- Wtryskiwacz piezoelektryczny (DI)
- Strategie wtrysku wtrysk bezpośredni
- Podwójny wtrysk
- Pomiar charakterystyki napięciowej i prądowej na wtryskiwaczu wielopunktowym
- Czas wtrysku w zależności od położenia wału korbowego
- Ograniczenie prądu ECU
- Określenie wymaganej ilości paliwa
- Tabela VE
- Tabela AFR
Wtrysk pośredni i bezpośredni:
Rodzaje układów wtryskowych silnika benzynowego dzielą się na wtrysk pośredni do przepustnicy, wtrysk pośredni na cylinder i bezpośredni wtrysk wysokociśnieniowy. Akapity na tej stronie wyjaśniają te różne systemy wtrysku.
Wtrysk pośredni:
Przed przepustnicą znajduje się wtryskiwacz. Paliwo wtryskiwane jest na przepustnicę, gdzie miesza się z przepływającym powietrzem. Główną wadą jest brak dokładnego dawkowania paliwa na cylinder; jeden cylinder zawsze dostaje trochę więcej lub mniej niż drugi. W związku z tym systemu nie można regulować i dlatego nie jest on już stosowany ze względu na wymogi ochrony środowiska. System ten nazywany jest także wtryskiem centralnym (Monopoint).
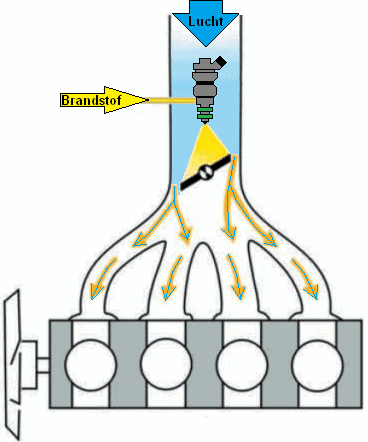
Wtrysk pośredni:
Każdy cylinder ma swój własny wtryskiwacz. Wtryskiwacz wtryskuje paliwo do zaworu dolotowego. Przepływające powietrze zapewnia także wymieszanie się w tym układzie zanim mieszanka paliwowo-powietrzna trafi do komory spalania. Zaletą w porównaniu z wtryskiem pośrednim jest to, że ilość paliwa można kontrolować znacznie dokładniej. System ten nazywany jest także MPI (wtrysk wielopunktowy) lub PFI (wtrysk paliwa do portu).
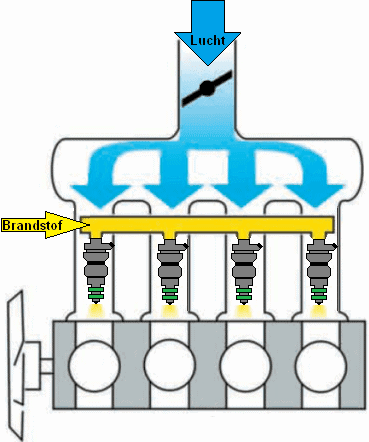
Wtrysk bezpośredni:
Wtryskiwacze DI (wtrysk bezpośredni) lub DISI (zapłon iskrowy z bezpośrednim wtryskiem) znajdują się obok świecy zapłonowej, w górnej części komory spalania. Przez ten wtryskiwacz wtryskiwane jest paliwo pod wysokim ciśnieniem około 200 barów podczas suwu ssania. Do głównych zalet tego układu należy jeszcze dokładniejsza regulacja ilości paliwa, możliwość kilkukrotnego wtrysku podczas suwu ssania oraz chłodniejsza mieszanka paliwowo-powietrzna. Umożliwia to producentom zwiększenie stopnia sprężania silnika. Wtryskiwacz może być wykonany jako wtryskiwacz piezoelektryczny lub z cewką magnetyczną.
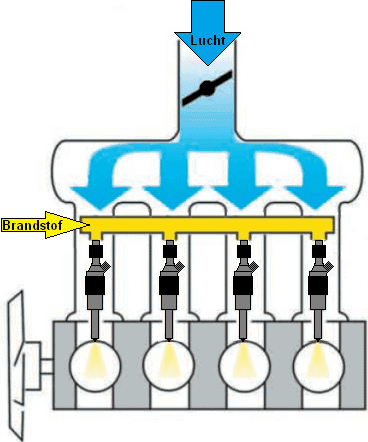
DI wymaga wyższych ciśnień wtrysku niż MPI/PFI, ponieważ wtrysk odbywa się podczas suwu sprężania; paliwo musi być wystarczająco rozpylone, podczas gdy powietrze w cylindrze jest sprężone. Dlatego DI ma osobną pompę wysokociśnieniową. Pompa wysokociśnieniowa zwiększa ciśnienie paliwa w kanale paliwowym. Wtryskiwacze są przymocowane do tej galerii paliwa za pomocą rurek. Gdy tylko sterownik silnika wyśle sygnał do wtryskiwacza, otworzy się on i zamknie w żądanym czasie.
Zalety DI w porównaniu do PFI obejmują:
- Dokładniejszy wtrysk;
- Możliwe wielokrotne zastrzyki;
- Czas wtrysku można regulować;
- Możliwe wyższe ciśnienie efektywne nad tłokiem (umożliwiając w ten sposób downsizing przy wyższym stopniu sprężania);
- Niższe zużycie paliwa, niższa emisja CO2.
Wady obejmują:
- Wyższe koszty systemu ze względu na wysokociśnieniową pompę paliwa, zaawansowane wtryskiwacze, bardziej złożoną głowicę cylindrów;
- Zwiększona emisja sadzy (emisje PM);
- Bezpośredni wtrysk do komory spalania zapewnia chłodzenie zamiast ciepła potrzebnego do odparowania paliwa.
Silnik z podwójnym wtryskiem wykorzystuje zalety obu systemów. Wtrysk bezpośredni i pośredni można przełączać w zależności od warunków pracy. Działanie i zastosowanie podwójnego wtrysku opisano w akapicie o tej samej nazwie na tej stronie.
Kontrola ciśnienia paliwa z wtryskiem pośrednim:
Stałe ciśnienie paliwa jest warunkiem dokładnej kontroli wtrysku paliwa. Ciśnienie paliwa (ciśnienie w szynie) znajduje się u góry wtryskiwacza, a ciśnienie w kolektorze dolotowym na dole. Ciśnienie w kolektorze dolotowym zmienia się w zależności od obciążenia silnika i bez regulatora ciśnienia będzie miało wpływ na różnicę ciśnień paliwa, a tym samym na ilość wtrysku. Z tego powodu stosujemy regulator ciśnienia paliwa. W tym rozdziale zagłębimy się w działanie i przeznaczenie tego sterownika.
Poniższy rysunek przedstawia elementy silnika benzynowego z wtryskiem pośrednim i wtryskiem wielopunktowym. Przyglądamy się przepływowi paliwa od pompy w zbiorniku do wtryskiwacza.
Gdy ECU steruje przekaźnikiem pompy paliwa, pompa działa. Pompa zasysa paliwo z najniższej możliwej części zbiornika paliwa i wymusza przepływ paliwa w stronę filtra paliwa. Cząsteczki zanieczyszczeń w paliwie pozostają w materiale filtra. Przefiltrowane paliwo dociera następnie do galerii paliwa. W większości przypadków galeria paliwowa montowana jest bezpośrednio na wlocie wtryskiwacza.
W kolektorze paliwowym panuje stałe ciśnienie: dopiero gdy wtryskiwacz jest sterowany elektrycznie przez ECU (patrz niebieski przewód), wtryskiwacz otwiera się i paliwo wtryskiwane jest do kolektora dolotowego na otwarty zawór dolotowy. Ilość wtryskiwanego paliwa zależy od:
- czas wtrysku (określany przez ECU poprzez wydłużenie lub skrócenie sygnału wtrysku);
- ciśnienie paliwa (przy czasie wtrysku wynoszącym 2 milisekundy wtryskiwacz wstrzyknie więcej niż obliczył ECU, jeśli ciśnienie paliwa będzie za wysokie).
Ciśnienie paliwa w zbiorniku paliwa (zwane także ciśnieniem szyny) jest regulowane w oparciu o obciążenie silnika. Omówimy to bardziej szczegółowo w następnej sekcji.
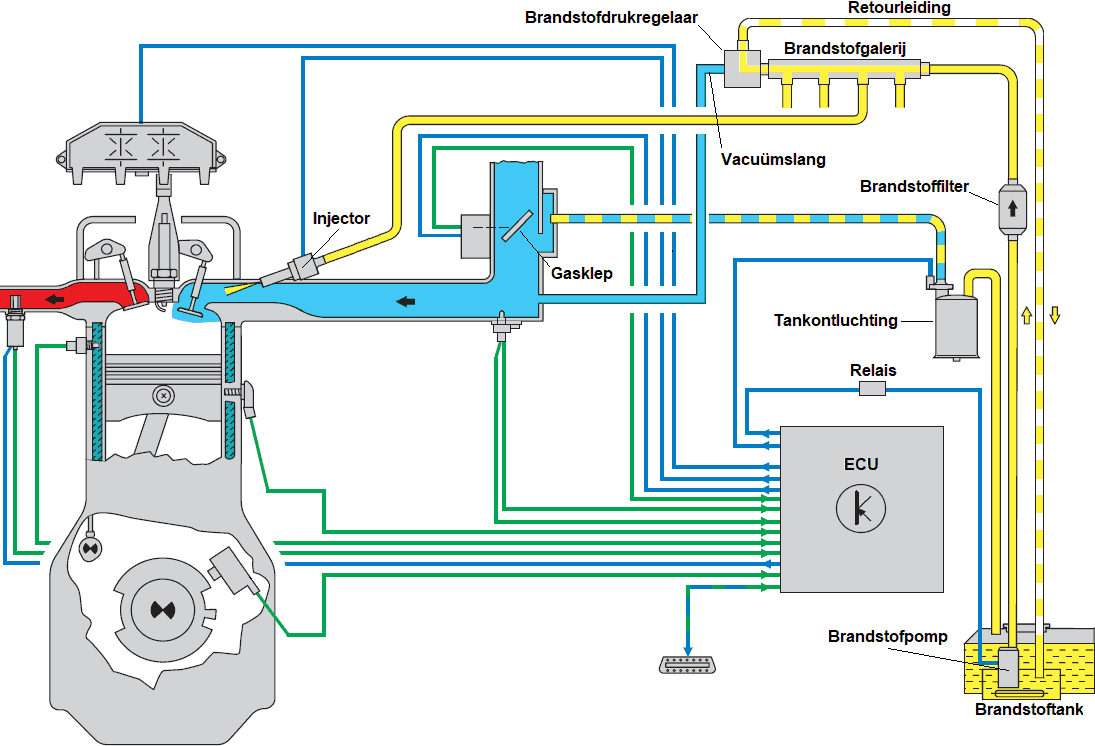
Bez użycia regulatora ciśnienia powstają następujące sytuacje:
- Na biegu jałowym wyższe podciśnienie (tj. niskie ciśnienie powietrza) w kolektorze dolotowym będzie powodować niepożądane wyższe ciśnienie paliwa;
- Podczas przyspieszania podciśnienie jest mniejsze lub w ogóle nie występuje (pełne obciążenie), a ciśnienie paliwa spada, choć pożądane jest wyższe ciśnienie paliwa.
Regulator ciśnienia paliwa zwiększa lub zmniejsza ciśnienie benzyny w zbiorniku paliwa w oparciu o ciśnienie powietrza w kolektorze dolotowym. Regulator ciśnienia paliwa możemy uznać za zawór dynamiczny, który umożliwia otwarcie przewodu zasilającego pompy paliwa i przewodu powrotnego.
Po prawej stronie widzimy wykres ciśnienia paliwa, na którym względna różnica ciśnień we wszystkich warunkach (na biegu jałowym, przy częściowym obciążeniu i przy pełnym obciążeniu) wynosi 4 bary dzięki regulatorowi ciśnienia.
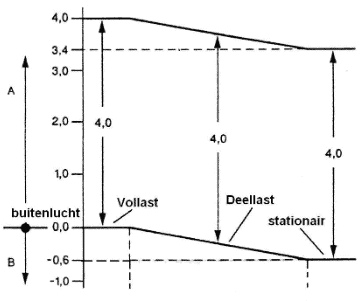
Poniższe wyjaśnienie odnosi się do zdjęć przedstawiających regulator ciśnienia w sytuacji bez i z podciśnieniem. Po prawej stronie znajduje się regulator ciśnienia paliwa firmy Bosch, z którego korzysta kilku producentów samochodów.
Bez podciśnienia (po lewej):
W stanie spoczynku regulator ciśnienia jest zamknięty: sprężyna dociska membranę do zamknięcia, uniemożliwiając przedostanie się dostarczanego paliwa do przewodu powrotnego.
Z próżnią (w środku):
Gdy ciśnienie nad membraną zostanie zmniejszone, ciśnienie paliwa po stronie zasilania wypycha membranę do góry, pokonując siłę sprężyny. Tworzy się otwór, przez który dostarczane paliwo jest spuszczane przewodem powrotnym do zbiornika paliwa.
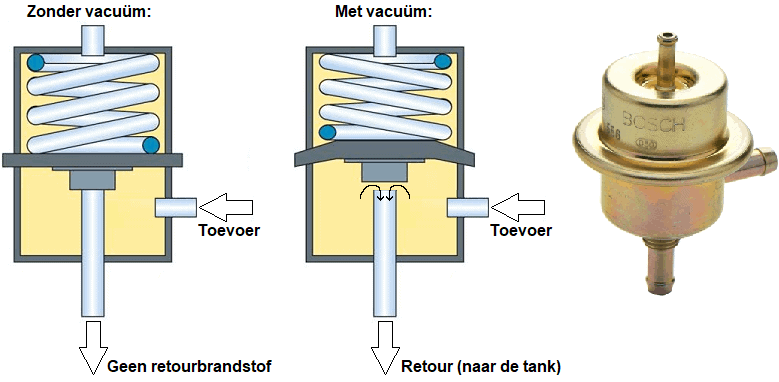
Strategia wtrysku wtrysk wielopunktowy:
W przypadku (pośredniego) wtrysku wielopunktowego stosowane są trzy różne metody wtrysku:
- Jednoczesny: wtrysk odbywa się jednocześnie na wszystkich cylindrach.
- Grupa: iniekcja odbywa się na grupę; istnieje rozróżnienie pomiędzy jedną lub większą liczbą grup.
- Sekwencyjny: każdy wtryskiwacz jest sterowany osobno i dlatego ma swój własny moment wtrysku.
Układ zarządzania silnikiem na poniższym rysunku ilustruje wtrysk grupowy. Wtryskiwacze cylindrów 1 i 2 mają wspólne zasilanie (czerwony) i oba są jednocześnie połączone z masą (zielony). Wtryskiwacze cylindrów 3 i 4 są takie same, ale sterowane są oddzielnie od cylindrów 1 i 2.
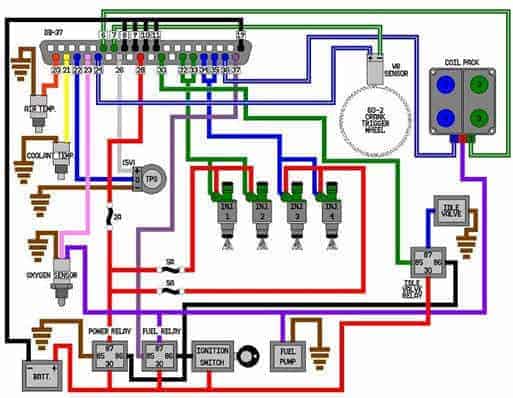
Wtryskiwacz elektromagnetyczny (MPI):
Wtryskiwacz elektromagnetyczny jest stosowany w wielu silnikach benzynowych, które nie korzystają z (bezpośredniego) wtrysku wysokociśnieniowego z oddzielną pompą wysokociśnieniową. Na wlocie wtryskiwacza paliwo znajduje się pod stałym ciśnieniem 1 bar. Ciśnienie paliwa zapewnia pompa paliwa znajdująca się w zbiorniku. Przy wtrysku wielopunktowym (opisanym w dalszej części strony) każdy cylinder ma swój własny wtryskiwacz. Wtryskiwacz ten montowany jest w kolektorze dolotowym i wtryskuje paliwo pod ciśnieniem do 6 barów przed otwarciem zaworu. Paliwo ma wówczas wystarczająco dużo czasu, gdy zawór wlotowy zaczyna się otwierać, aby zmieszać się z całym tlenem (zaznaczonym na rysunku ciemnoniebieską strzałką) wpływającym do cylindra.
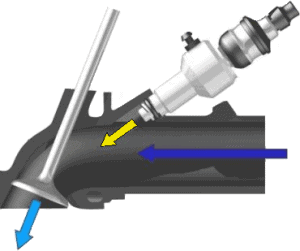
Jednostka sterująca silnika sprawdza położenie wału korbowego w celu regulacji czasu wtrysku i zapłonu. Na podstawie kilku czynników (temperatura silnika i otoczenia, obciążenie, prędkość itp., da sygnał do wtryskiwacza w odpowiednim momencie do otwarcia. Wtyczka tego wtryskiwacza zawiera dwie żyły. Jeden przewód ma stały plus około 14 V. Drugi przewód jest podłączony do masy przez ECU, aby umożliwić przepływ prądu przez cewkę wtryskiwacza. Gdy cewka jest wystarczająco naładowana, igła wtryskiwacza otwiera się wbrew sile sprężyny. Kiedy sterowanie zatrzymuje się, sprężyna ściska igłę wtryskiwacza z powrotem Następnie zostaje odcięty dopływ paliwa. Po zatrzymaniu sterowania cewka jest nadal naładowana elektrycznie. Energia w cewce tworzy szczyt indukcyjny, który można zaobserwować na oscyloskopie. Napięcie indukcyjne wynosi przez krótki czas około 60 woltów.
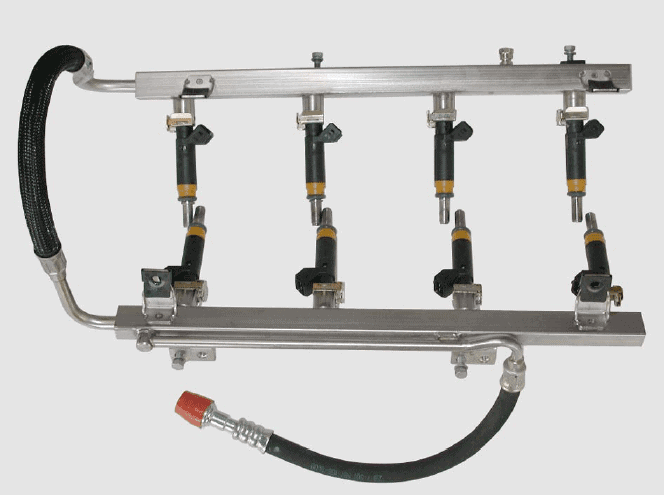
Wtryskiwacze te są zasilane paliwem przez szynę paliwową (zwaną także galerią paliwową). Pompa wspomagająca w zbiorniku paliwa zapewnia ciśnienie w szynie paliwowej. Ciśnienie paliwa w listwie jest stałe (ok. 4 bar). Ponieważ ciśnienie jest tak niskie, wtryskiwacze są mocowane za pomocą zacisku blokującego i pierścienia uszczelniającego typu O-ring. Zwłaszcza w starszych samochodach, gdzie układ jest demontowany, warto przed montażem wymienić oringi.
Obudowa wtryskiwacza jest zwykle wykonana z tworzywa sztucznego. W górnej części obudowy znajduje się złącze wtykowe, które jest wewnętrznie połączone z cewką. U góry znajduje się gumowy O-ring, po którym przesuwa się galeria paliwa. Na dole znajdują się oringi lub teflonowe pierścienie uszczelniające. O-ring stosowany jest głównie we wtryskiwaczach MPI z wtryskiem niskociśnieniowym, natomiast pierścienie teflonowe można spotkać w silnikach z wtryskiem wysokociśnieniowym, np. silniku FSI.
Cewka jest nawinięta wokół rdzenia wtryskiwacza. Na załączonym obrazku cewka jest zaznaczona na czerwono. W środku wtryskiwacza, również wewnątrz cewki, znajduje się tłok. Tłok ten posiada mechaniczne połączenie z igłą. Nad tłokiem znajduje się sprężyna, która utrzymuje tłok, a tym samym igłę w gnieździe, zamykając otwór do wstrzykiwania.
W stanie spoczynku napięcie na obu zaciskach cewki wynosi około 14 woltów w stosunku do masy. Aby zalać wtryskiwacz, ECU silnika zasila jedną stronę cewki masą, podczas gdy druga strona otrzymuje napięcie dodatnie. W tym momencie przez cewkę zaczyna płynąć prąd, co powoduje powstanie pola magnetycznego. To pole magnetyczne ciągnie tłok, a tym samym igłę do wstrzykiwań, do góry.
Gdy konieczne jest zatrzymanie wtrysku, ECU odłącza masę, powodując zanik pola magnetycznego. Sprężyna popycha tłok z powrotem w dół, powodując, że igła odcina dopływ paliwa do komory spalania.
Wtryskiwacz ma zwykle wiele otworów. Otwory te są bardzo małe, dzięki czemu paliwo wtryskiwane jest z wtryskiwacza do komory spalania w postaci mgły. Im drobniejsza mgła, tym łatwiej odparowuje.
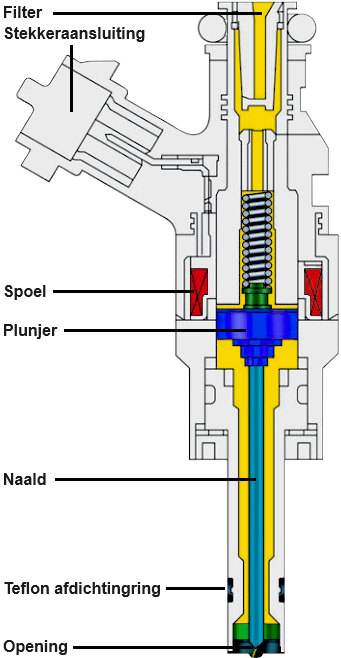
Wtryskiwacz piezoelektryczny (DI):
Wtryskiwacze piezoelektryczne można stosować zarówno w silnikach benzynowych, jak i wysokoprężnych. BMW było pierwszą marką, która zastosowała technologię piezoelektryczną w silnikach benzynowych, ale zaprzestała tego w nowszych silnikach.
Wtryskiwacz piezoelektryczny jest częścią wtrysku wysokociśnieniowego. Oddzielna pompa wysokociśnieniowa zapewnia ciśnienie do szyny paliwowej. Ta szyna paliwowa rozprowadza paliwo do wszystkich wtryskiwaczy (patrz zdjęcie). Ze względu na bardzo wysokie ciśnienia stosuje się rury aluminiowe z dławnicami. Dławnice (nakręcane na rurę i wtryskiwacze) należy zawsze dokręcać z odpowiednią siłą. Jest to określone w instrukcji naprawy odpowiedniego silnika.
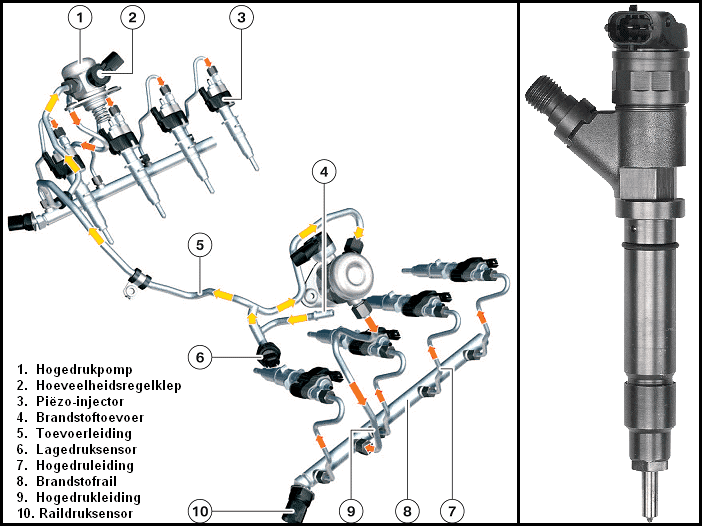
Element piezoelektryczny we wtryskiwaczu ma właściwość zmiany długości po podłączeniu do niego napięcia dodatniego lub ujemnego. Jest to używane z wtryskiwaczem. Gdy tylko jednostka sterująca silnika dostarczy napięcie sterujące o wartości od około 100 do 150 woltów, element piezoelektryczny rozszerza się o około 0,03 mm. Ta zmiana długości wystarczy, aby ustanowić połączenie pomiędzy komorą wysokiego i niskiego ciśnienia. Wstrzyknięcie rozpoczyna się natychmiast. Element piezoelektryczny może włączać się i wyłączać w ciągu jednej tysięcznej sekundy. W połączeniu z bardzo wysokim ciśnieniem wtrysku, sięgającym 2000 barów, zapewnia to bardzo szybkie i dokładne wtryskiwanie. Prędkości te umożliwiają także wykonanie wielu wtrysków jeden po drugim.
Zaletą wielokrotnych wtrysków podczas suwu ssania jest optymalne mieszanie powietrza z paliwem. Wysokie ciśnienie powoduje, że kropelki paliwa są bardzo drobno rozpylone, dzięki czemu jeszcze lepiej mieszają się z powietrzem. Podczas suwu ssania może nastąpić do 8 wstrzyknięć. Ma to pozytywne skutki w zakresie zużycia paliwa, mocy i emisji spalin.
Strategie wtrysku wtrysk bezpośredni:
Strategia wtrysku bezpośredniego ma różne warianty: przez ścianę, przez powietrze i przez strumień (patrz ilustracje poniżej). W takich sytuacjach zachodzi proces spalania warstwowego. Nie dotyczy to wszystkich warunków pracy.
- Prowadzenie po ścianie: Tłok kieruje chmurę paliwa do świecy zapłonowej. Odległość pomiędzy świecą zapłonową a wtryskiwaczem jest duża. Stosowany do silników GDI i HPI.
- Prowadzona powietrzem: Ruch powietrza przenosi chmurę paliwa do świecy zapłonowej. Odległość pomiędzy świecą zapłonową a wtryskiwaczem jest duża. Stosowany do silników FSI i JTS.
- Prowadzenie strumieniowe: Świeca zapłonowa znajduje się na krawędzi chmury paliwa. Odległość pomiędzy wtryskiwaczem a świecą zapłonową jest niewielka. Stosowany w silnikach BMW.
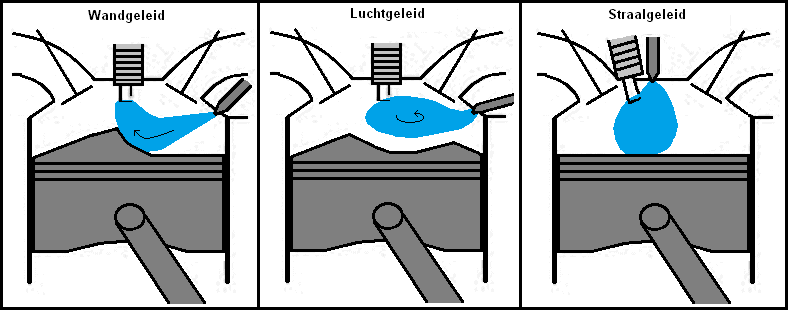
Jak już wskazano, silniki benzynowe z bezpośrednim wtryskiem paliwa nie mają spalania warstwowego we wszystkich warunkach pracy. Silniki z bezpośrednim wtryskiem strumieniowym mogą pracować fazowo przy częściowym obciążeniu. Warstwowy proces spalania oznacza, że w przestrzeni spalania znajdują się różne warstwy powietrza. W pobliżu świecy wartość lambda wynosi 1. Dalej wartość lambda staje się wyższa (mniejsza, więc więcej powietrza). Powietrze to tworzy izolującą warstwę powietrza. W procesie warstwowym czas wtrysku jest dłuższy niż w procesie jednorodnym. Za pomocą wtrysku warstwowego przepustnicę można całkowicie otworzyć, dzięki czemu mniej dławi powietrze. Ponieważ zasysane powietrze jest pozbawione masy, napotyka mniejszy opór i dzięki temu może być łatwiej zasysane. Ponieważ wartość lambda w przestrzeni spalania przy wtrysku warstwowym jest mniejsza od 1 ze względu na izolującą warstwę powietrza, nie powoduje to żadnych problemów ze spalaniem. Podczas procesu nakładania warstw zużycie paliwa maleje.
Przy jednorodnej mieszance wartość lambda wynosi wszędzie 1. Oznacza to, że w silniku benzynowym stosunek powietrza do paliwa wynosi 14,7:1 (14,7 kg powietrza na 1 kg paliwa). Każdy silnik może pracować równomiernie. Jeśli nastąpi wzbogacenie, wartość lambda spadnie, a jeśli mieszanka stanie się uboższa, wartość lambda wzrośnie:
<1 = Bogaty
>1 = Słabo
Aby katalizator działał prawidłowo, silnik zawsze będzie się wahać pomiędzy mieszanką bogatą i ubogą. The sonda lambda wysyła dane do systemu zarządzania silnikiem.
Przy pełnym obciążeniu silnik zawsze pracuje równomiernie. Daje to wyższy moment obrotowy niż w przypadku procesu warstwowego. Jeśli silnik pracuje równomiernie, paliwo wtryskiwane jest wcześniej. Silnik pracuje równomiernie również podczas ruszania z miejsca. Występuje wówczas wyższy moment rozruchowy, niż gdyby silnik pracował warstwowo.
Poniższa krzywa charakterystyczna przedstawia sytuacje robocze przy różnych prędkościach w porównaniu do ciśnienie spalania, z i bez użycia EGR.
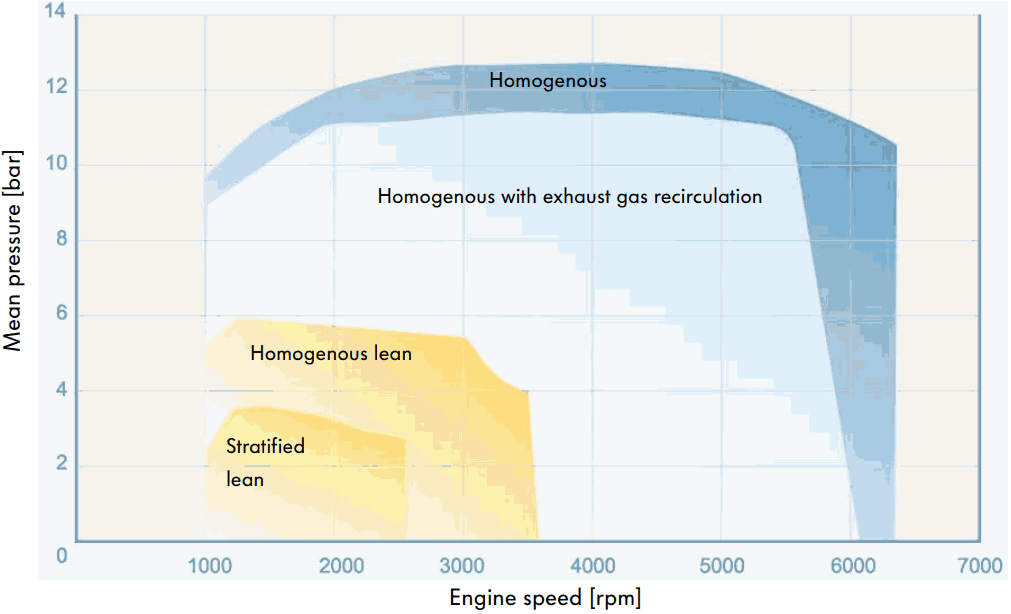
Podwójny wtrysk:
Grupa VAG wykorzystuje silniki benzynowe z podwójnym wtryskiem, aby spełniać aktualne normy emisji. W silnikach z podwójnym wtryskiem występują dwa układy wtrysku paliwa: układ niskociśnieniowy i układ wysokociśnieniowy.
- Układ niskociśnieniowy zawiera wtryskiwacze MPI, które są stosowane od dziesięcioleci. Wtryskiwacze MPI montowane są w kolektorze dolotowym i wtryskują do zaworu dolotowego pod ciśnieniem od 4 do 5 barów;
- Układ wysokociśnieniowy zawiera wtryskiwacze wysokociśnieniowe, które wtryskują bezpośrednio do komory spalania pod ciśnieniem wtrysku maksymalnie od 150 do 200 barów.
System zarządzania silnikiem określa, który wtryskiwacz jest sterowany.
Poniższe zdjęcie przedstawia przekrój głowicy cylindrów z dwoma układami paliwowymi.
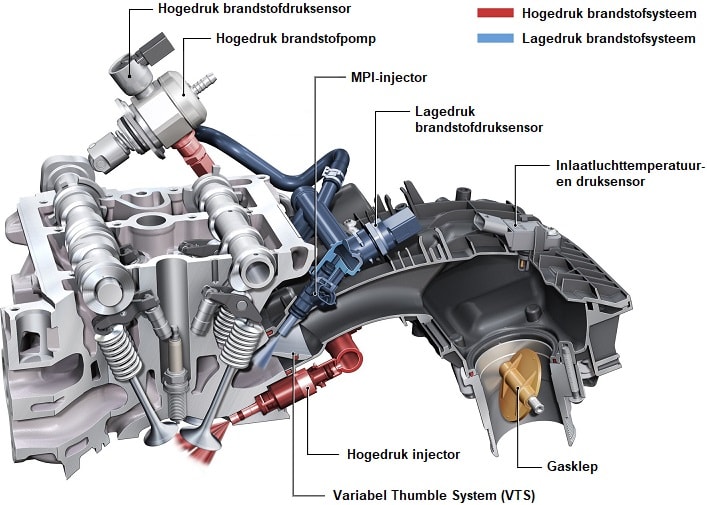
Wtrysk MPI zapewnia lepsze mieszanie powietrza i paliwa. Wtryskiwacze bezpośrednie pracują na biegu jałowym i przy pełnym obciążeniu. Dzięki wtryskowi bezpośredniemu uzyskuje się lepsze chłodzenie, co umożliwia wyższy stopień sprężania. Jednakże mieszanie powietrza i paliwa nie jest optymalne. Powoduje to większą emisję sadzy. Z tego powodu silniki z wtryskiem bezpośrednim są obecnie wyposażane w filtr cząstek stałych. Nie stanowi to problemu w przypadku podwójnego wtrysku. „System zmiennego kciuka”, w skrócie VTS, to wersja zmiennej kolektora dolotowego, która zapewnia lepszy przepływ powietrza. „Kciuk” to strumień powietrza, który tworzy wir na wejściu do cylindra. Zawirowanie powietrza jest niezbędne do prawidłowego wymieszania paliwa z wtryskiwacza MPI z powietrzem.
Podwójny wtrysk w połączeniu z VTS zapewnia lepszą emisję spalin. Dodatkową zaletą jest to, że zawór dolotowy czyszczony jest za pomocą wtryskiwacza MPI. Silniki z wtryskiem bezpośrednim często mają zanieczyszczony układ dolotowy (kolektor dolotowy i zawory dolotowe), co powoduje problemy, takie jak ograniczony dopływ powietrza. W skrajnym scenariuszu wlot zostaje tak zatkany, że zawór dolotowy nie może już prawidłowo zamykać się na głowicy cylindrów i ostatecznie ulega spaleniu, ponieważ nie jest w stanie dostatecznie odprowadzić ciepła.
Wiadomo, że te same silniki w USA wyposażane są wyłącznie w wtrysk bezpośredni, w przypadku silników VAG z podwójnym wtryskiem. Kolektor dolotowy jest zaślepiony. Dzieje się tak dlatego, że w chwili pisania tego tekstu wymagania środowiskowe w Europie są bardziej rygorystyczne niż w USA, a producent nie dostarcza silników na rynki, na których normy emisji są mniej rygorystyczne w przypadku tak drogich układów ze względu na koszty.
Pomiar charakterystyki napięciowej i prądowej na wtryskiwaczu wielopunktowym:
Oscyloskop może mierzyć tylko napięcie. Kable pomiarowe można podłączyć równolegle do elementów elektrycznych. Pomiar prądu szeregowo nie jest możliwy. Prąd można mierzyć za pomocą indukcyjnej cęgi prądowej. Czujniki Halla w cęgach prądowych mierzą pole magnetyczne i przekształcają je na napięcie. Napięcie można zmierzyć oscyloskopem. W tym przypadku współczynnik konwersji wynosi 10 mv na amper; Na każde 0,010 wolta przesyłane przez cęgi prądowe można to przeliczyć na 1 A.
Poniższy obraz zakresu przedstawia profil napięcia i prądu wtryskiwacza elektromagnetycznego.
- Czerwony: gradient napięcia;
- Żółty: przepływ prądu.
W spoczynku napięcie wynosi 14 woltów. Na wtyczce nie ma już różnicy napięcia, więc nie płynie prąd. ECU łączy jeden przewód z masą w celu sterowania wtryskiwaczem. Różnica napięć powoduje przepływ prądu przez cewkę wtryskiwacza.
Żółta linia wskazuje przepływ prądu: w momencie, gdy napięcie spadnie do 0 woltów, rozpoczyna się narastanie prądu. Ładowanie cewki wymaga czasu. Prąd nie wzrasta bardziej niż około 0,9 A. W połowie narastania prądu widzimy zagięcie linii: jest to moment, w którym wytworzył się wystarczający magnetyzm, aby podnieść igłę z jej gniazda. Wtryskiwacz rozpoczyna wstrzykiwanie.
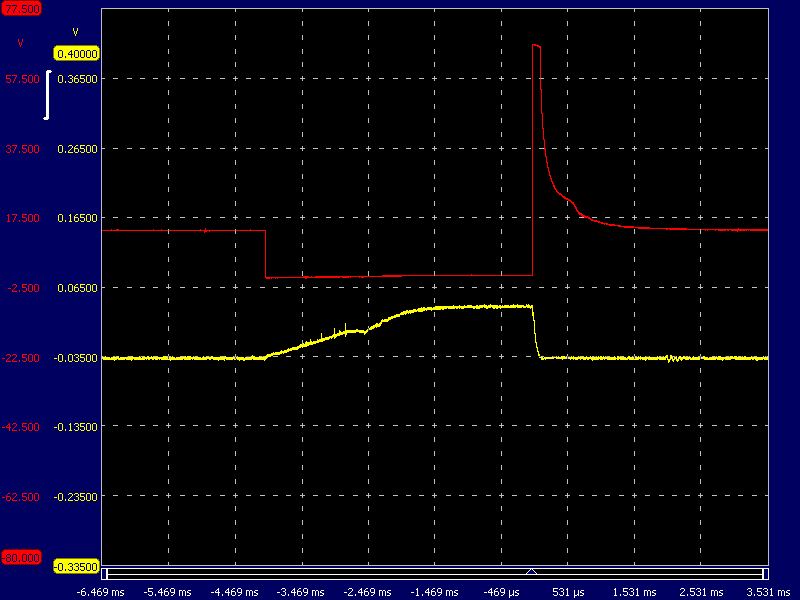
ECU przerywa połączenie z masą, aby zatrzymać sterowanie. Energia resztkowa w cewce zapewnia napięcie indukcyjne o wartości około 60 woltów. Wstrzykiwacz przestaje wstrzykiwać, ponieważ sprężyna wpycha igłę z powrotem w jej gniazdo. Można to zobaczyć na obrazie oscyloskopu po uderzeniu sygnału napięciowego.
Jeśli silnik pracuje nieregularnie i pojawiają się przerwy zapłonu w cylindrze, może to mieć kilka przyczyn:
- Brak iskry lub słaba iskra z powodu uszkodzonej świecy zapłonowej, kabla świecy zapłonowej lub cewki zapłonowej;
- Ograniczenie dopływu paliwa na skutek zatkanego filtra paliwa, uszkodzonego regulatora ciśnienia, problemu z pompą paliwa lub wtryskiwaczem;
- Utrata kompresji spowodowana problemem z pierścieniami tłokowymi, uszkodzoną uszczelką głowicy lub uszczelkami zaworów.
Podczas diagnozy można za pomocą oscyloskopu sprawdzić, czy wtryskiwacze nadal działają prawidłowo. Na początku tej sekcji pokazano pomiary, w których nie wystąpiła żadna awaria. Niebieskie linie pokazują jako przykład, jak wyglądałby profil napięcia i prądu uszkodzonego wtryskiwacza.
W przypadku, gdy sterowanie wtryskiwaczem jest prawidłowe, ale na obrazie napięcia i prądu nie widać żadnych załamań, można wnioskować, że igła wtryskiwacza nie porusza się. Ponieważ wtryskiwacz jednego cylindra nie działa prawidłowo, a pozostałe wtryskiwacze działają prawidłowo, obrazy różnych wtryskiwaczy można łatwo porównać ze sobą.
Delikatne puknięcie we wstrzykiwacz może spowodować poluzowanie się iglicy wstrzykiwacza. W takim przypadku silnik natychmiast zacznie pracować ciszej, a załamania będą ponownie widoczne na zdjęciach z lunety. Nie gwarantuje to jednak trwałego rozwiązania; istnieje duża szansa, że problem powróci w krótkim czasie. Konieczna jest wymiana odpowiedniego wtryskiwacza.
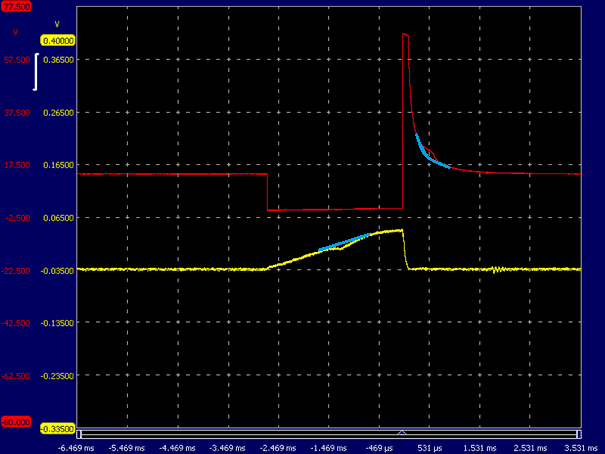
Igła we wtryskiwaczu otwiera się dopiero po wystarczającym naładowaniu cewki. W rezultacie wtryskiwacz nie wtryskuje paliwa od razu, gdy ECU zaczyna nim sterować. Po zakończeniu zadziałania sprężyna dociska iglicę wtryskiwacza do jej gniazda. To również wymaga czasu. Czas kontroli z reguły nie jest równy czasowi wtrysku. Poniższy rysunek przedstawia krzywą napięcia i prądu tego samego wtryskiwacza co powyżej, ale ze zwiększoną prędkością.
- Rozpoczęcie sterowania: ECU przełącza przewód sterujący do masy. Prąd przepływa przez cewkę wtryskiwacza, aby ją otworzyć. Załamanie na schemacie przepływu wskazuje moment otwarcia iglicy wtryskiwacza. Prąd następnie nieznacznie wzrasta i dlatego pozostaje stały. Igła wstrzykiwacza pozostaje otwarta.
- Koniec kontroli: jak już opisano, moment zamknięcia iglicy wtryskiwacza po uderzeniu rozpoznajemy na obrazie napięcia.
Sterowanie trwa 4 ms, ale rzeczywisty czas wtrysku wynosi 3 ms. Różnicę między nimi nazywamy „opóźnieniem”, tłumaczonym na język niderlandzki jako „opóźnieniem”. ECU steruje zatem wtryskiwaczem przez 4 ms, aby umożliwić mu wtrysk przez 3 ms.
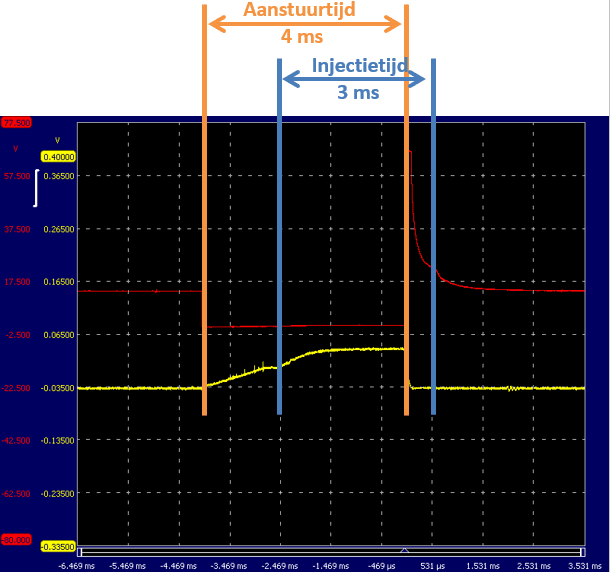
Czas wtrysku w zależności od położenia wału korbowego:
Moment wtrysku można obejrzeć za pomocą oscyloskopu. Kanał A (czerwony) znajduje się na przewodzie uziemiającym wtryskiwacza, a kanał B (żółty) na przewodzie wtryskiwacza Czujnik położenia wału korbowego połączony. Gdy silnik pracuje, możemy użyć tego obrazu oscyloskopu do określenia czasu wtrysku i czasu wtrysku.
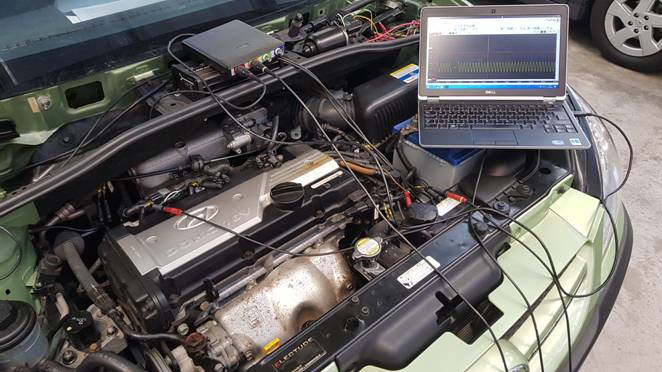
Zdjęcie oscyloskopowe zostało wykonane na biegu jałowym. Czerwony obraz napięcia przedstawia otwieranie i zamykanie wtryskiwacza (patrz rozdział: Pomiar charakterystyki napięciowej i prądowej na wtryskiwaczu wielopunktowym). W chwili -2,860 ms rozpoczyna się regulacja; napięcie z 12 woltów spada do 0 woltów. Jest to punkt, w którym cewka wtryskiwacza jest uziemiona i przepływa prąd. Kontrola wtryskiwaczy kończy się w momencie ponownego podniesienia się czerwonej linii. Ze względu na energię zgromadzoną w cewce powstaje napięcie indukcyjne o wartości ponad 60 woltów. Następnie napięcie stopniowo spada do 12 woltów; tutaj wtryskiwacz jest ponownie wyłączony.
Czerwone napięcie przemienne pochodzi z przewodu indukcyjnego Czujnik położenia wału korbowego. Za każdym razem, gdy zęby koła impulsowego obracają się obok czujnika wału korbowego, wytwarzane jest sinusoidalne napięcie przemienne. Koło impulsowe zawiera 60 zębów, z czego 2 zostały zeszlifowane. Dwa szlifowane zęby tworzą punkt odniesienia, w którym układ sterujący silnikiem rozpoznaje, że tłoki cylindrów 1 i 4 znajdują się w przedziale od 90⁰ do 120⁰ przed GMP (górny martwy punkt). Po rozpoznaniu brakującego zęba system zarządzania silnikiem ma czas na (prawdopodobnie w połączeniu z czujnik wałka rozrządu) w celu ustalenia prawidłowego momentu wtrysku i zapłonu oraz włączenia wtryskiwacza i cewki zapłonowej, zanim tłok znajdzie się w GMP.
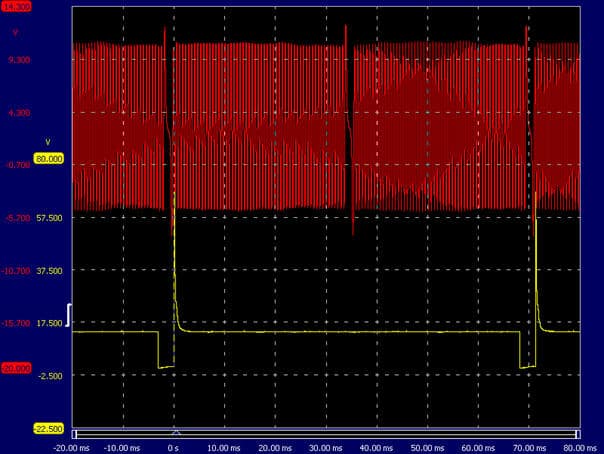
Obraz oscyloskopu pokazuje czas rozpoczęcia wstrzyknięcia; wtrysk rozpoczyna się od czwartego impulsu z czujnika wału korbowego. Zakładając że zębów jest 60 - 2 to po każdych 6⁰ obrotu wału korbowego (360⁰ dla 1 obrotu / 60 zębów) wtrysk następuje o 24 stopnie od punktu odniesienia. Brakujący ząb znajduje się 90⁰ przed GMP, zatem wtrysk rozpoczyna się (90⁰ – 24⁰) = 66⁰ przed GMP.
Przy zwiększonej prędkości obrotowej 2000 obr/min impulsy indukcyjnego czujnika wału korbowego zbliżają się do siebie. Częstotliwość tego sygnału jest przekładana na prędkość przez system zarządzania silnikiem. W zależności od prędkości obciążenie (mierzone przez Czujnik mapy) i temperatura powietrza dolotowego i płynu chłodzącego określany jest wymagany czas wtrysku. Czas wtrysku następuje wcześniej i wtryskiwacz dłużej stoi na ziemi: wtryskiwacz wtryskuje wcześniej i dłużej.
Od początku załączenia do momentu zadziałania (strzałka na poziomie wyłączenia wtryskiwacza) czas załączenia wynosi około 5,2 ms. Czas włączenia wtryskiwacza nie jest równy faktycznemu wtryskowi (patrz poprzedni akapit).
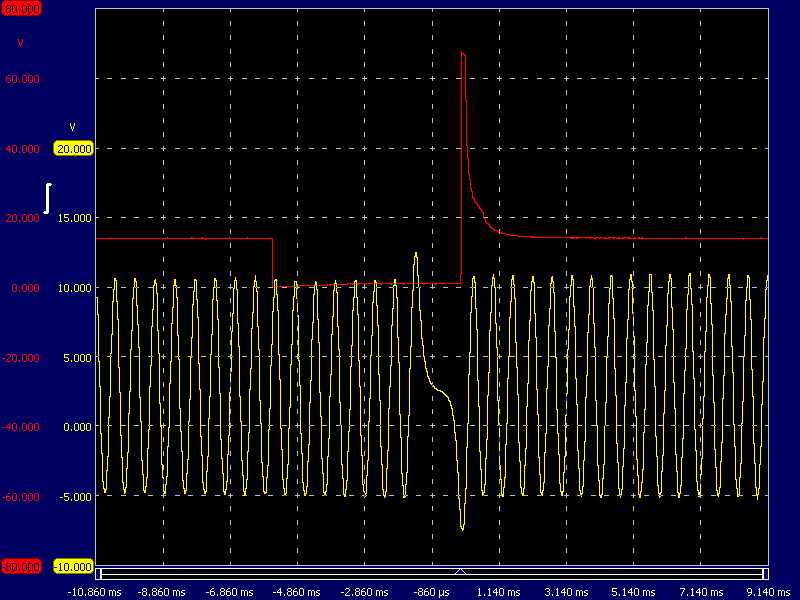
Na poniższym obrazie oscyloskopu sygnał indukcyjny wału korbowego jest pokazany na czerwono, a sygnał wtryskiwacza na żółto. Po zwiększeniu prędkości do około 3000 obr./min widoczne są dwa elementy sterujące wtryskiwaczami. Wyraźnie widać, że wtrysk paliwa do pierwszego cylindra następuje przy co drugim obrocie wału korbowego.
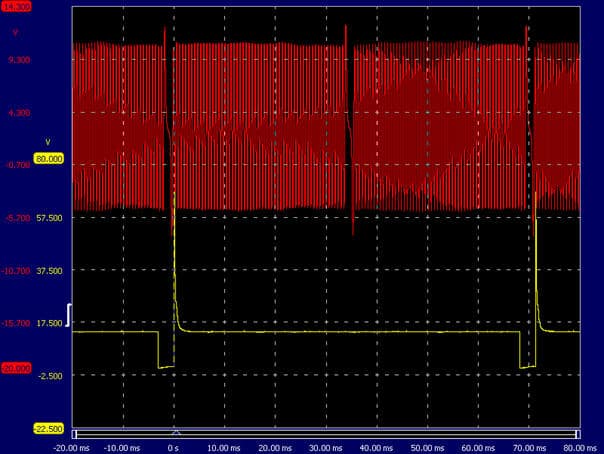
Ograniczenie prądu w ECU:
Jak wykazały pomiary w rozdziale „Pomiar napięcia i prądu na wtryskiwaczu wielopunktowym”, pomiędzy uruchomieniem, a faktycznym otwarciem iglicy wtryskiwacza występuje opóźnienie. W tym przypadku otwarcie trwa 1,5 ms.
Igła wtryskiwacza otwierałaby się szybciej, gdyby prąd płynący przez cewkę wzrastał szybciej. Prąd zależy od rezystancji cewki: im niższa rezystancja, tym szybsze narastanie prądu. Wtryskiwacze o wysokiej impedancji zastosowane w silniku pomiarów mają rezystancję 16 Ohm. Przy napięciu pokładowym 14 woltów popłynie niewielki prąd:
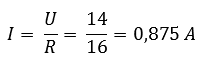
Prąd jest wystarczający, aby otworzyć igłę wtryskiwacza, ale nie za duży, aby na skutek zbyt dużej mocy się nie nagrzał:

Ponieważ generowana jest tylko niewielka moc, nie ma potrzeby stosowania kontroli prądu. Byłoby to konieczne w przypadku wtryskiwaczy o niskiej impedancji.
- Wtryskiwacze o niskiej impedancji mają tę zaletę, że narastanie prądu szybko rośnie od samego początku. Powoduje to szybkie otwarcie igły wtryskiwacza, a więc niewielkie opóźnienie.
- Wtryskiwacze o niskiej rezystancji mają rezystancję około 2,8 oma. Niski opór powoduje przepływ dużego prądu:
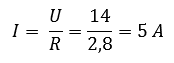
Moc również gwałtownie wzrasta:

Pobór mocy jest prawie siedmiokrotnie wyższy niż w przypadku wtryskiwaczy o wysokiej impedancji. Jeśli prąd wzrośnie zbyt mocno, we wtryskiwaczach i stopniu wyjściowym urządzenia sterującego wytwarza się ciepło. Aby ograniczyć prąd, napięcie jest wielokrotnie włączane i wyłączane w krótkim czasie. Po otwarciu igły wstrzykiwacza potrzeba niewielkiej ilości energii, aby utrzymać igłę otwartą. Prąd maleje podczas włączania i wyłączania. Postęp ten można zobaczyć na obrazie zakresu.
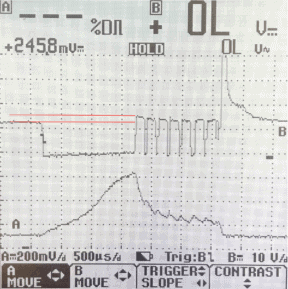
Określenie wymaganej ilości paliwa:
Producent określił wymaganą ilość paliwa w różnych charakterystycznych polach, które przechowywane są w pamięci ROM ECU. To system zarządzania silnikiem odczytuje z tych wykresów ile paliwa potrzeba bez poprawek. Zależy to oczywiście od prędkości obrotowej silnika, temperatury i obciążenia. Najważniejsze parametry umożliwiające określenie prawidłowej ilości paliwa wyjaśniono w tej sekcji jako tabele VE i tabele AFR.
Tabela VE:
Tabela VE przedstawia wydajność objętościową i stosunek powietrza do paliwa przy każdej prędkości obrotowej silnika i ciśnieniu w kolektorze dolotowym. Sprawność objętościowa to stosunek zmierzonej ilości powietrza wypełniającego cylindry do ilości powietrza, która wypełniłaby cylinder w sytuacji statycznej, w zależności od prędkości obrotowej silnika i ciśnienia w kolektorze dolotowym. Wartości z tabeli służą ECU do określenia aktualnej masy powietrza i tym samym poziomu napełnienia. Na podstawie tych danych obliczana jest ilość wtryskiwanego paliwa.
To teoretyczne podejście różni się od rzeczywistości. Specyfikacje silnika nie zostały jeszcze tutaj uwzględnione. Weź pod uwagę schemat zaworów (nakładanie się zaworów lub ewentualnie zmienny rozrząd zaworów), opór powietrza w układzie dolotowym itp. Dlatego stosuje się współczynnik korygujący, który daje odchylenie od zależności liniowej. Współczynnik korekcji pokazano na powyższym obrazku linią przerywaną. Krzywa wskazuje, w jakim stopniu zależność liniowa jest poprawna. Przy ciśnieniu 60 kPa odchylenie wynosi około 50% od linii pokazującej zależność liniową. Współczynnik korygujący można wyrazić w procentach.
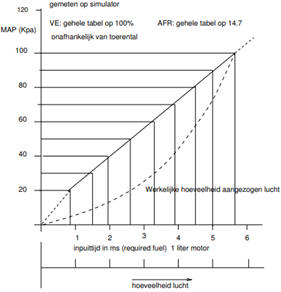
W tabeli VE każda komórka wskazuje wartość procentową związaną z podciśnieniem w stosunku do prędkości. Wartość procentowa będzie najwyższa przy prędkości, przy której moment obrotowy jest najwyższy. Przecież tam silnik jest najbardziej wydajny, bo silnik tankuje najlepiej.
Wartości w tabelach VE i AFR w dalszej części tej sekcji pochodzą z krzywej momentu obrotowego i mocy silnika 1.8 20v z VW Golfa.
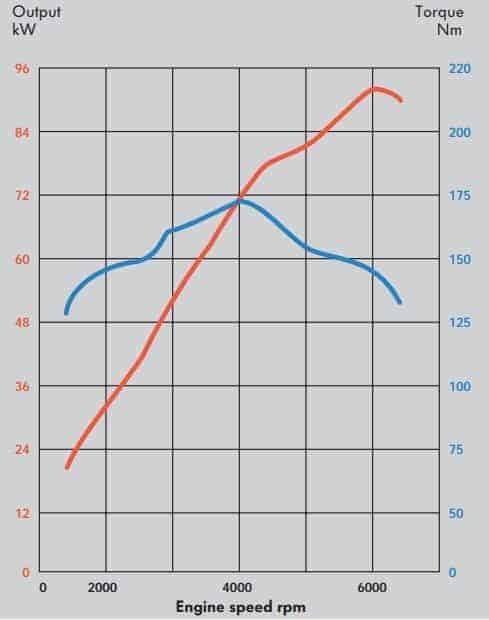
Poniższe obrazy przedstawiają tabelę VE jako tabelę wypełniającą oraz trójwymiarową reprezentację utworzoną przy użyciu krzywej momentu obrotowego i mocy w programie „TunerStudio”. Ten program jest używany głównie do dostarczania oprogramowania dla programowalnego ECU, takiego jak MegaSquirt lub Speeduino. Więcej informacji: zobacz strony o tym Projekt MegaSquirt.
Oś pionowa pokazuje MAP (ciśnienie powietrza w kolektorze) od 15 kPa (duże podciśnienie) do 100 kPa (ciśnienie powietrza zewnętrznego). MAP wskazuje obciążenie silnika. Oś pozioma wskazuje prędkość obrotową silnika od biegu jałowego do maksymalnej prędkości obrotowej silnika.
Komórki w tabeli VE pokazują poziom napełnienia silnika. Innymi słowy; jak wydajny jest silnik przy określonej prędkości i obciążeniu. Silnik jest najbardziej wydajny przy prędkości obrotowej, przy której moment obrotowy jest najwyższy (około 4200 obr./min). tutaj odsetki są najwyższe. To tutaj silnik najlepiej się „napełnia”. Stosowanie technik zwiększających poziom napełnienia, takich jak zmienne fazy rozrządu, regulacja kolektora dolotowego lub użycie turbosprężarki, będzie korzystne dla wartości procentowych.
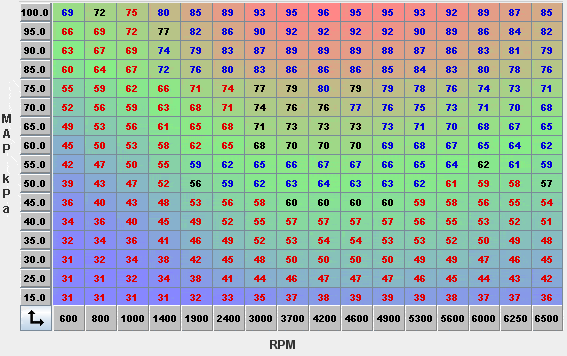
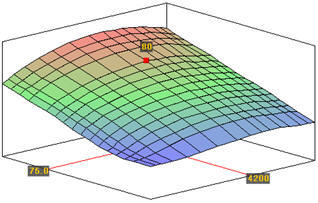
Tabela AFR:
Wymagany skład powietrza i paliwa jest rejestrowany w tabeli AFR. AFR to skrót od „stosunek paliwa do powietrza”. Przy stechiometrycznym stosunku zmieszania (lambda = 1) do spalenia 14,7 kg benzyny potrzeba 1 kg powietrza. Nie we wszystkich sytuacjach pożądana jest mieszanina stechiometryczna.
- Uboga mieszanka korzystnie wpływa na zużycie paliwa;
- Bogata mieszanka pozwala na większą moc.
Gdy silnik musi dostarczyć większą moc (P), następuje wzbogacenie. Bogatsza mieszanka zapewnia również chłodzenie. Wzbogacanie do λ = 0,8 oznacza, że obowiązuje stosunek mieszania (AFR) wynoszący 11,76 kg powietrza na 1 kg benzyny. Zatem jest mniej powietrza do spalenia 1 kg paliwa niż w przypadku mieszanki stechiometrycznej. Z drugiej strony uboga mieszanka zapewnia lepsze zużycie paliwa (be), ale zwiększa ryzyko stukania. Wzbogacanie lub zubażanie mieszanki musi zawsze mieścić się w granicach spalania.
Na biegu jałowym prędkość obrotowa wynosi od 600 do 900 obr./min. Zawór gazowy jest prawie całkowicie zamknięty, a podciśnienie jest wysokie: wynosi od 25 do 40 kPa. W tym zakresie prędkości mieszanina jest stechiometryczna (14,7:1).
W przypadku częściowego obciążenia prędkość obrotowa silnika wzrośnie do 4200 obr./min. Przepustnica otwiera się bardziej, przez co podciśnienie w kolektorze dolotowym spada do 40 – 75 kPa. Wraz ze wzrostem obciążenia silnika podciśnienie maleje; następuje wzbogacenie (AFR 13:1). Uboga mieszanka jest możliwa przy niskim obciążeniu silnika. Przy pełnym obciążeniu przepustnica jest całkowicie otwarta. Podciśnienie spada do 100 kPa (ciśnienie powietrza zewnętrznego) i następuje maksymalne wzbogacenie (12,5:1).
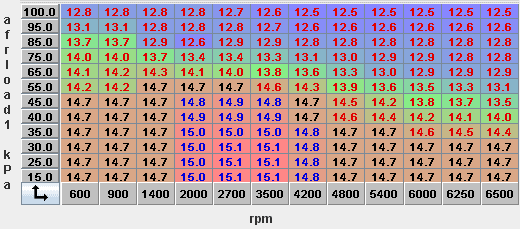
Wartość lambda wpływa nie tylko na zużycie mocy i paliwa, ale także na emisję spalin. Bogatsza mieszanka zapewnia niższą zawartość NOx, ale także wyższą emisję CO i HC. W przypadku uboższej mieszanki cząsteczki paliwa są bardziej od siebie oddalone, przez co spalanie nie jest już optymalne; w wyniku czego wzrasta również emisja HC.
W przypadku stosowania katalizatora pożądane jest zapewnienie ciągłej zmiany wtrysku mieszanki bogatej i ubogiej. W bogatej mieszaninie w wyniku niedoboru tlenu powstaje CO, przez co katalizator redukuje NOx. Uboga mieszanka zawiera nadmiar tlenu, który utlenia CO i HC.
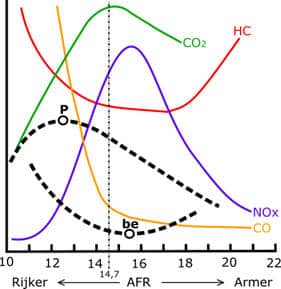
Jednostka sterująca określa, ile paliwa należy wtrysnąć. W pierwszej kolejności z pól charakterystycznych odczytywane są podstawowe dane wtrysku. Do obliczenia ilości wtrysku uwzględniane są m.in. wartości z tabel VE i AFR. Uwzględniane są również następujące wartości określone przez producenta:
- wzbogacanie w zależności od temperatury płynu chłodzącego i powietrza dolotowego;
- krótkotrwałe wzbogacenie przyspieszenia przy (szybkim) otwarciu przepustnicy;
- korekta ze względu na zmiany napięcia na pokładzie.
Oprócz tych określonych wartości dokładnie uwzględniane są napięcia wysyłane przez sondę lambda do jednostki sterującej. Napięcia te zależą od zawartości tlenu w spalinach. Jest to czynnik zmienny, który zmienia się w sposób ciągły. Wejście tych napięć czujników określane jest jako tzw.listwy paliwowe„włączona.
Sposób ustalania wartości tabeli VE i AFR oraz pozostałych wymienionych ustawień opisano na stronach wykonanych Projekt MegaSquirt.