Thèmes:
- Préface
- Capteurs passifs
- Capteurs actifs
- Capteurs intelligents
- Applications dans la technologie automobile
- Mesurer sur des capteurs
- Transmission du signal du capteur à l'ECU
- ENVOYÉ (Transmission de grignotage sur un seul bord)
- Alimentation et traitement du signal
Préface:
Les capteurs mesurent des grandeurs physiques et les convertissent en tensions électriques. Ces tensions sont traitées dans le microcontrôleur (ECU) et lues comme un « signal ». Le signal peut être jugé par le niveau de tension ou la fréquence à laquelle un signal change.
Capteurs passifs :
Un capteur passif détecte et mesure une grandeur physique et la convertit en une autre grandeur physique. Un exemple de ceci est la conversion d'une température en valeur de résistance. Un capteur passif ne génère aucune tension lui-même, mais répond à une tension de référence provenant de l'ECU. Un capteur passif ne nécessite pas de tension d'alimentation pour fonctionner.
Les capteurs passifs ont généralement deux ou trois connexions :
- fil de référence ou de signal (bleu);
- fil de terre (marron);
- fil blindé (noir).
Parfois, un capteur passif ne contient qu'un seul fil : dans ce cas, le boîtier du capteur sert de masse. Un troisième fil peut servir de blindage. La veste est mise à la terre via l'ECU. Le fil blindé est particulièrement utilisé pour les signaux sensibles aux interférences, tels que ceux du capteur de position du vilebrequin et du capteur de cliquetis.
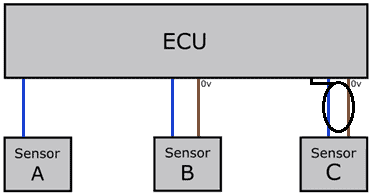
Un exemple de capteur passif est un Capteur de température CTN. La tension de référence de 5 volts est utilisée comme diviseur de tension entre la résistance de l'ECU et du capteur, et non comme tension d'alimentation pour le capteur. Le niveau de tension entre les résistances (en fonction de la valeur de la résistance NTC) est lu par l'ECU et traduit en température. Le circuit avec les résistances est expliqué dans la section : « Alimentation en tension et traitement du signal » plus loin sur cette page.
Capteurs actifs :
Les capteurs actifs contiennent un circuit électrique dans le boîtier pour convertir une grandeur physique en valeur de tension. Le circuit électrique nécessite souvent une tension d’alimentation stabilisée pour fonctionner.
Dans la plupart des cas, ce type de capteur dispose de trois connexions :
- plus (généralement 5,0 volts) ;
- Pâtes;
- signal.
L'alimentation stabilisée de 5 volts est fournie par la centrale et utilisée par le capteur pour former un signal analogique (entre 0 et 5 volts). Les fils positifs et de terre de l'ECU sont souvent connectés à plusieurs capteurs. Cela peut être reconnu par les nœuds auxquels plus de deux fils sont connectés.
Le signal analogique est converti en signal numérique dans l'ECU.
Dans le paragraphe « sPanning Supply et traitement du signal », nous en discuterons plus en détail.
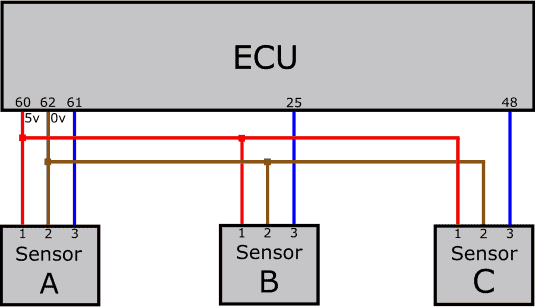
Capteurs intelligents :
Les capteurs intelligents ont généralement trois connexions. Comme pour les capteurs actifs, il y a un fil d'alimentation (12 volts depuis le calculateur ou directement via un fusible) et un fil de terre (via le calculateur ou un point de masse externe. Un capteur intelligent envoie un signal numérique (Autobus LIN) message à l'ECU et aux autres capteurs. Il y a alors un principe maître-esclave.
En interne dans le capteur, un convertisseur A/D convertit un signal analogique en signal numérique.
- Analogique : 0 – 5 volts ;
- Numérique : 0 ou 1.
En Signal du bus LIN en condition récessive (12 volts) c'est un 1, et en condition dominante (0 volts) c'est un 0.
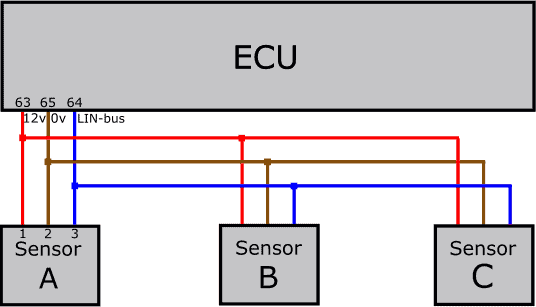
Applications dans la technologie automobile :
Dans la technologie automobile, nous pouvons faire la classification suivante des différents types de capteurs :
Capteurs passifs :
- Détecteur de cliquetis;
- Capteur de position de vilebrequin;
- Capteur de température (NTC/PTC) ;
- Sonde lambda (sonde de saut / zirconium) ;
- Capteur de hauteur inductif ;
- Allumer / éteindre)
Capteurs actifs :
- Capteur de position vilebrequin/arbre à cames (Hall);
- Compteur d'air massique ;
- Sonde lambda à large bande ;
- Capteur de pression (capteur de pression de suralimentation / capteur de pression turbo) ;
- Capteur ABS (Hall/MRE);
- Capteur d'accélération/décélération (YAW) ;
- Capteur radar/LIDAR ;
- Capteur à ultrasons (PDC/alarme) ;
- Capteur de position (vanne gaz / EGR / vanne chauffage).
Capteurs intelligents :
- Capteur de pluie/lumière ;
- Appareils photo;
- Capteur de pression;
- Capteur d'angle de braquage ;
- Capteur de batterie
Mesure sur capteurs :
Lorsqu'un capteur ne fonctionne pas correctement, le conducteur le remarquera dans la plupart des cas car un voyant de dysfonctionnement s'allume ou que quelque chose ne fonctionne plus correctement. Si un capteur dans le compartiment moteur provoque un dysfonctionnement, cela pourrait entraîner une perte de puissance et l'allumage d'un MIL (témoin de dysfonctionnement du moteur).
Lors de la lecture d'un ECU, un code d'erreur peut s'afficher si l'ECU reconnaît le défaut. Cependant, dans tous les cas, le code d'erreur ne mène pas directement à la cause. Le fait que le capteur en question ne fonctionne pas peut être dû à un défaut, mais un problème de câblage et/ou de connexion ne peut pas être exclu.
Il est également possible que le capteur donne une valeur incorrecte qui n'est pas reconnue par le calculateur. Dans ce cas, aucun code défaut n'est stocké, mais le technicien doit utiliser les données en direct (voir la page OBD) il faut rechercher des lectures hors de portée.
L'image suivante montre une mesure provenant d'un capteur actif. L'alimentation électrique (la différence de tension sur les connexions plus et moins) du capteur est vérifiée avec un multimètre numérique. Le compteur indique 5 volts, donc ça va.
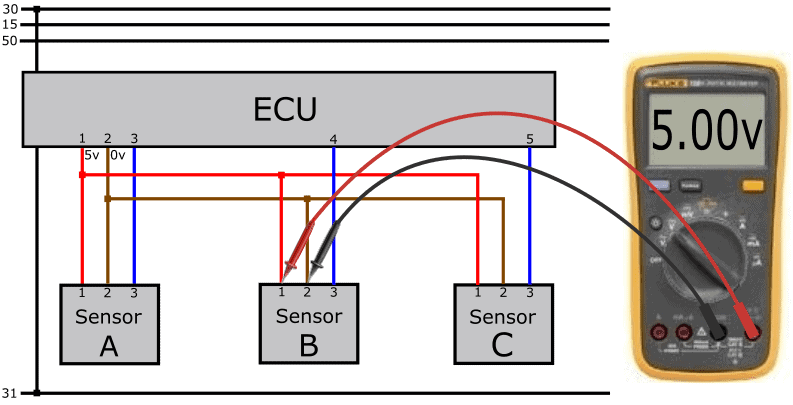
Les tensions des signaux peuvent être mesurées avec un voltmètre ou un oscilloscope. Le compteur approprié dépend du type de signal :
- voltmètre : signaux analogiques quasi constants ;
- oscilloscope : signaux analogiques et signaux numériques (duty cycle / PWM).
Avec une ou plusieurs mesures, nous pouvons démontrer que le capteur ne fonctionne pas correctement (le signal émis n'est pas plausible ou le capteur ne produit pas de signal), ou qu'il y a un problème dans le câblage.
Avec les capteurs passifs, dans la plupart des cas, une mesure de résistance peut être effectuée pour vérifier s'il existe un défaut interne dans le capteur.
Les problèmes possibles dans le câblage du capteur peuvent inclure :
- interruption de la masse positive ou du fil de signal ;
- court-circuit entre les fils ou la carrosserie ;
- résistance de transition dans un ou plusieurs fils ;
- mauvaises connexions.
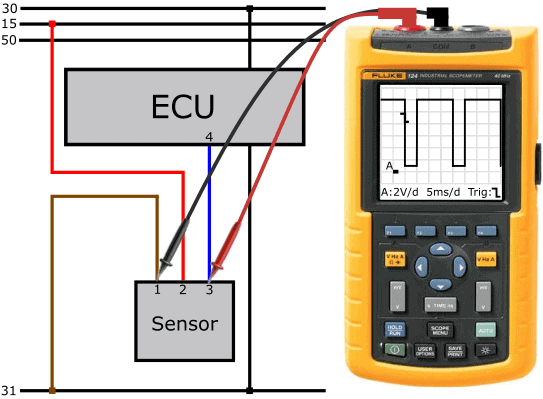
Sur la page: dépanner le câblage du capteur nous examinons sept dysfonctionnements possibles pouvant survenir dans le câblage des capteurs.
Transmission du signal du capteur à l'ECU :
Il existe plusieurs méthodes pour transférer les signaux du capteur vers l'ECU. Dans la technologie automobile, nous pouvons traiter les types de signaux suivants :
- Modulation d'amplitude (AM); le niveau de la tension renseigne ;
- Modulation de fréquence (FM); la fréquence du signal renseigne ;
- Modulation de largeur d'impulsion (PWM) ; la variation temporelle de la tension de bloc (duty cycle) renseigne.
Les trois exemples suivants montrent les signaux d'oscilloscope des différents types de signaux.
La modulation d'amplitude:
Avec un signal AM, le niveau de tension transmet l'information. La figure montre deux tensions provenant des capteurs de position du papillon. Pour garantir la fiabilité, les courbes de tension doivent être inversées les unes par rapport aux autres.
Stress au repos :
- Bleu : 700 mV ;
- Rouge : 4,3 volts.
Environ 0,25 seconde après le début de la mesure, la pédale d'accélérateur est enfoncée lentement et le papillon des gaz s'ouvre à 75 %.
À 2,0 s. la pédale d'accélérateur est relâchée et à 3,0 sec. est lancé à plein régime.
Tensions à plein régime :
- Bleu : 4,3 volts ;
- Rouge : 700 mV.
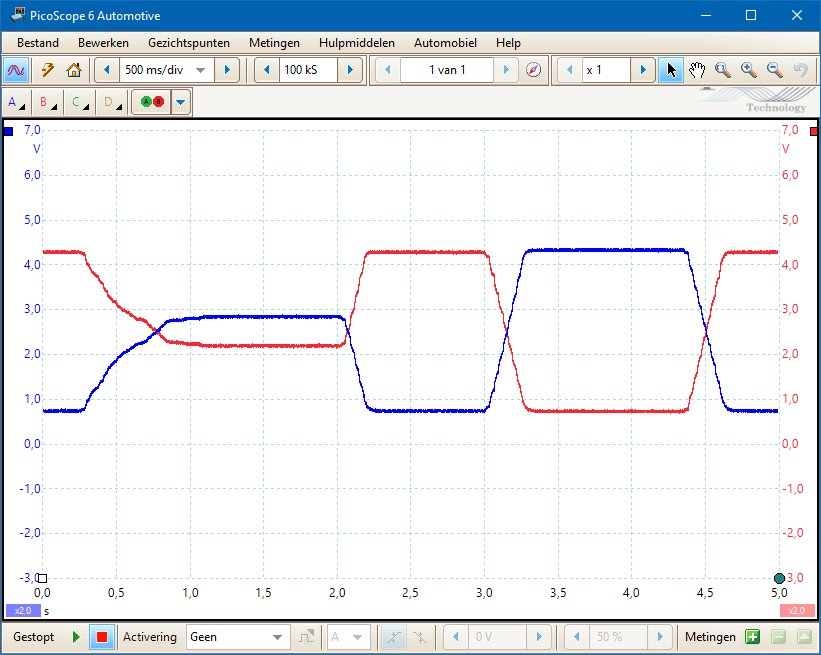
Modulation de fréquence:
Avec les capteurs qui envoient un signal FM, l'amplitude (hauteur) du signal ne change pas. La largeur de la tension de bloc transmet l'information. L'image suivante montre le signal d'un capteur ABS (Hall). La roue a tourné pendant la mesure. À une vitesse de rotation plus élevée, la fréquence du signal augmente.
La différence de tension est provoquée par la modification du champ magnétique dans l’anneau magnétique intégré au roulement de roue. La différence de hauteur (faible : champ magnétique, élevée : pas de champ magnétique) n'est que de 300 mV. Si l'oscilloscope est mal réglé (plage de tension de 0 à 20 volts), le signal de blocage est à peine visible. C'est pour cette raison que l'échelle a été ajustée de manière à ce que le signal de bloc devienne visible, ce qui rend le signal moins pur.
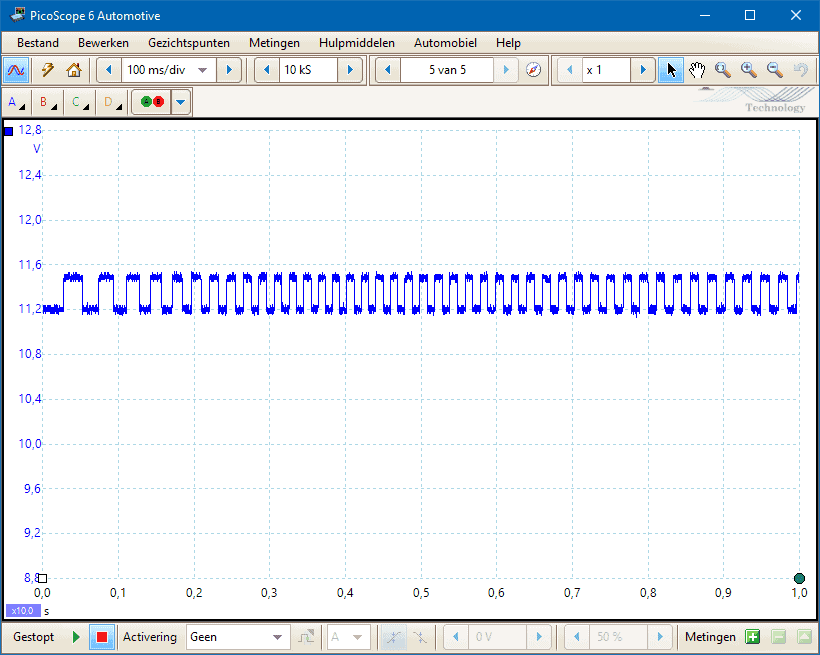
Modulation de largeur d'impulsion :
Avec un signal PWM, le rapport entre la tension haute et basse change, mais la période reste la même. Cela ne doit pas être confondu avec une tension carrée dans un signal FM : la fréquence change et donc aussi la période.
Les deux images suivantes montrent les signaux PWM provenant d'un capteur haute pression dans un tuyau de climatisation. Ce capteur mesure la pression du réfrigérant dans le système de climatisation.
Situation lors de la mesure :
- Contact mis (le capteur reçoit une tension d'alimentation) ;
- Climatisation éteinte ;
- Pression du fluide de refroidissement relevée avec un équipement de diagnostic : 5 bar.
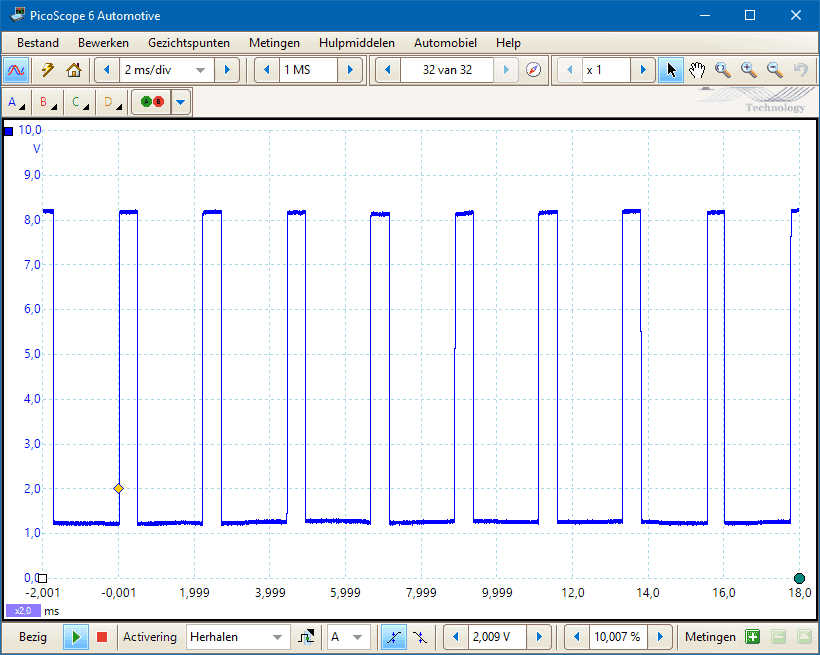
Dans l’image suivante de l’oscilloscope, nous voyons que la période est restée la même, mais que le cycle de service a changé.
Situation lors de la mesure :
- Climatisation allumée ;
- La haute pression est montée à 20 bars ;
- Le cycle de service est désormais de 70 %
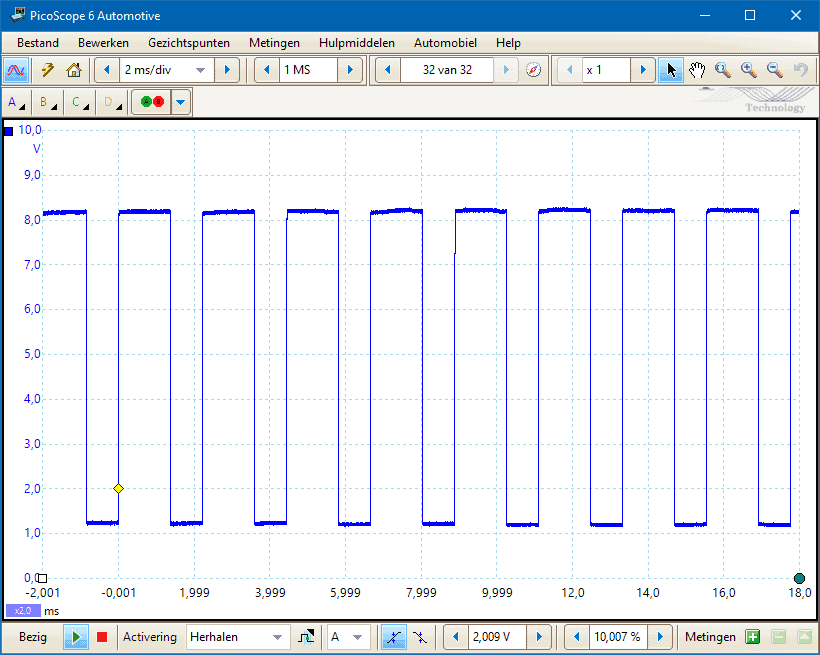
Les capteurs analogiques peuvent envoyer un signal via AM. Un tel signal de tension est sensible à la perte de tension. Une résistance de transition dans un fil ou une fiche entraîne une perte de tension et donc également une tension de signal plus faible. L'ECU reçoit la tension la plus basse et utilise le signal pour le traitement. Cela peut provoquer des dysfonctionnements car plusieurs valeurs de capteurs ne correspondent plus entre elles, entraînant :
- Deux capteurs de température de l'air extérieur qui mesurent simultanément une température différente. Bien qu'une petite marge d'erreur soit acceptable et que l'ECU puisse adopter la valeur moyenne, une différence trop importante peut conduire à un code d'erreur. L'ECU reconnaît l'écart entre les deux capteurs de température.
- une durée d'injection incorrecte car le signal du capteur MAP est trop faible et le calculateur interprète donc une charge moteur incorrecte. Dans ce cas, l'injection de carburant est trop longue ou trop courte et les trims de carburant corrigeront le mélange en fonction du signal de la sonde lambda.
La perte de tension ne joue aucun rôle dans un signal PWM et/ou un signal SENT. Le rapport entre les fronts montants et descendants est une mesure du signal. Le niveau de tension n'a pas d'importance. Le rapport cyclique peut être de 40 % à une tension qui varie entre 0 et 12 volts, mais le rapport est toujours de 40 % si la tension d'alimentation chute à 9 volts.
ENVOYÉ (Transmission de grignotage sur un seul bord)
Les signaux des capteurs mentionnés ci-dessus sont connus depuis des années dans les véhicules de tourisme et les véhicules utilitaires. Dans les modèles les plus récents, nous voyons de plus en plus de capteurs qui utilisent le protocole SENT. Ce capteur ressemble à un capteur actif habituel, tant en réalité que sur le schéma.
Avec les capteurs passifs et actifs, le transfert d'informations s'effectue via deux fils. Dans le cas d'un capteur MAP par exemple : un entre le capteur NTC et le calculateur et l'autre entre le capteur de pression et le calculateur. L'électronique du capteur d'un capteur SENT peut combiner le transfert d'informations de plusieurs capteurs, réduisant ainsi le nombre de fils de signal. La transmission du signal n'est pas non plus affectée en cas de perte de tension sur le fil de signal, tout comme pour un signal PWM.
Un capteur utilisant le protocole SENT, comme un capteur actif envoyant un signal analogique ou numérique, comporte trois fils :
- Tension d'alimentation (souvent 5 volts)
- Signal
- Masse.
Les capteurs avec le protocole SEND envoient un signal comme « sortie ». Il n'y a donc pas de communication bidirectionnelle, comme c'est le cas par exemple avec la communication par bus LIN entre capteurs.
Dans le schéma de droite, nous voyons le capteur de pression différentielle (G505) d'une VW Passat (construite en 2022). Dans le schéma, nous voyons les indications habituelles de l'alimentation (5v), de la masse (GND) et du signal (SIG). Ce capteur de pression convertit la pression en un signal numérique SENT et l'envoie à la broche 53 du connecteur T60 de l'ECU du moteur.
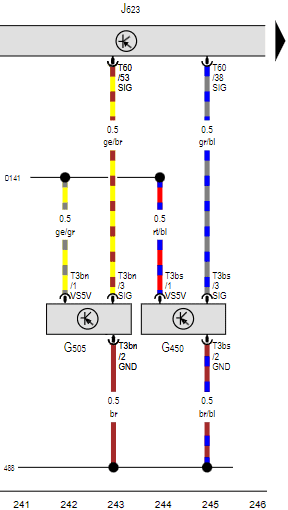
Le capteur de pression différentielle dans l'exemple ci-dessus envoie un seul signal via le protocole SENT sur le fil de signal. Plusieurs capteurs peuvent être connectés à un seul fil de signal à l'aide de SENT. Cela peut s'appliquer, entre autres, à un capteur MAP (pression et température de l'air) ainsi qu'à un capteur de niveau et de qualité d'huile.
Dans l'image suivante, nous voyons un capteur de niveau et de qualité d'huile monté dans le carter d'huile d'un moteur à combustion. Les deux éléments de mesure se trouvent dans l'huile moteur.
Le capteur est alimenté en 12 volts, reçoit sa masse via l'ECU et envoie le signal à l'ECU en utilisant SENT.
Le microcontrôleur dans le boîtier numérise le message (voir : « logique numérique » sur la figure) dans lequel la température et le niveau d'huile sont inclus dans le signal SENT.
Ci-dessous, nous examinons la structure d'un signal SENT.
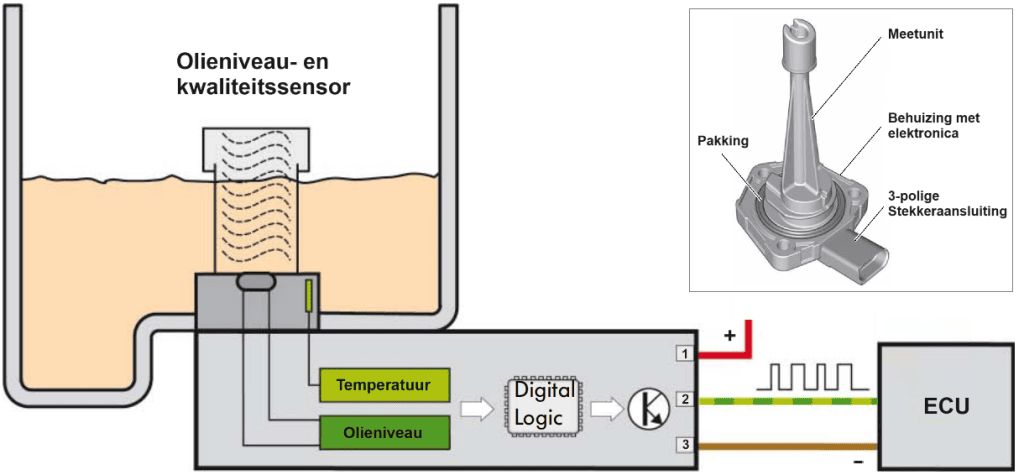
Un signal SENT est constitué d'une série de quartets (groupes de quatre bits) qui transfèrent des informations en envoyant des tensions comprises entre 0 et 5 volts. Voici une brève description de la façon dont un signal SENT est construit. L'image de la structure du message est présentée ci-dessous.
- Impulsion de synchronisation/calibrage : c'est souvent le début du message. Cette impulsion permet au récepteur d'identifier le début du message et de synchroniser le timing de l'horloge ;
- Statut: cette partie indique l'état des informations envoyées, par exemple si les données sont correctes ou s'il y a des problèmes avec celles-ci ;
- Message de début de grignotage (MSN): C'est le premier quartet et indique le début d'un message SENT. Il contient des informations sur la source du message et le moment du transfert des données.
- Nibble d’identifiant de message (MidN): Ce quartet suit le MSN et contient des informations sur le type de message, l'état du message et toute information de détection ou de correction d'erreur.
- Grignotages de données: Après le MidN suit un ou plusieurs blocs de données, chacun composé de quatre quartets de données. Ces blocs de données transportent les données réelles envoyées. Ils contiennent des informations telles que des données de capteur, des informations d'état ou d'autres données utiles.
- Contrôle de redondance cyclique (CRC): Dans certains cas, un quartet CRC peut être ajouté à la fin du message pour faciliter la détection des erreurs. Le quartet CRC est utilisé pour vérifier si les données reçues ont été correctement reçues.
Chaque quartet dans un signal SENT peut avoir des valeurs de 0 à 15, selon le nombre de ticks il s'agit de 5 volts. L'image ci-dessous montre la structure du protocole SENT.
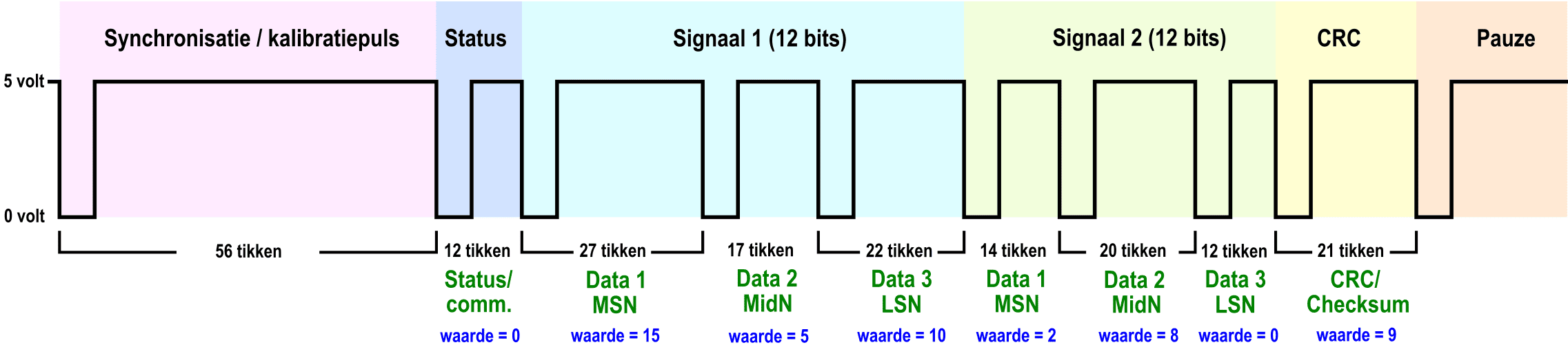
Des « groupes Nibble » sont envoyés numériquement de 0000 à 1111 au format binaire. Chaque quartet représente une valeur de 0 à un maximum de 15, et ils sont représentés en binaire comme suit : 0000b à 1111b et en hexadécimal de 0 à F. Ces quartets numérisés contiennent les valeurs des capteurs et sont envoyés au calculateur.
Pour envoyer ces informations de grignotage, des « ticks » ou ticks informatiques sont utilisés. Le tick de l'horloge indique la rapidité avec laquelle les données sont envoyées. Dans la plupart des cas, le tic d'horloge est de 3 microsecondes (3 μs) jusqu'à un maximum de 90 μs.
Dans le premier cas, cela signifie qu'un nouveau groupe de grignotage est envoyé toutes les 3 microsecondes.
Le message commence par une impulsion de synchronisation/étalonnage à 56 clics. Pour chacun des deux signaux : signal 1 et signal 2, trois quartets sont envoyés, ce qui donne une séquence de 2*12 bits d'information. Le CRC suit ces signaux
(Cyclic Redundancy Check) pour le contrôle, qui permet au destinataire de vérifier que les données reçues sont correctes.
Enfin, une impulsion de pause est ajoutée pour marquer clairement la fin du message au destinataire.
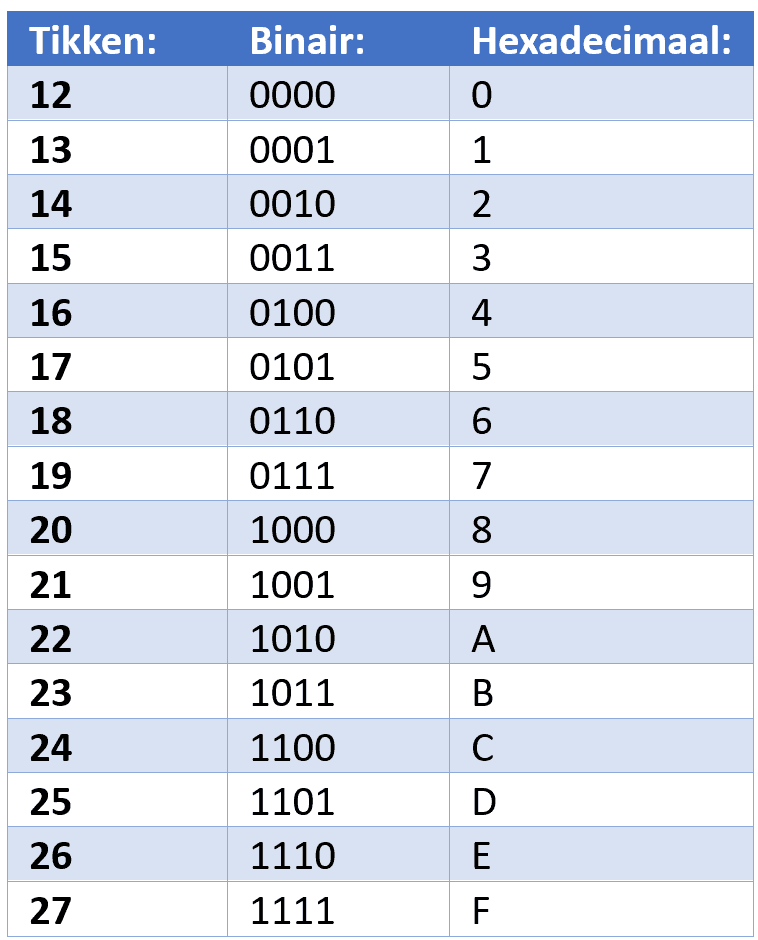
Les images d'oscilloscope ci-dessous (enregistrées avec le PicoScope Automotive) montrent les mesures de plusieurs messages (à gauche) et un zoom avant sur un message (à droite). Dans le message agrandi, il est indiqué en rouge où commence et se termine le signal. Lorsque les conditions changent : la pression et/ou la température augmentent, il y aura un changement dans le nombre de ticks dans un ou plusieurs quartets. Le changement de ticks sera visible dans l'image du scope ci-dessous dans une ou plusieurs tensions variant entre 0 et 5 volts. Les impulsions peuvent devenir plus larges ou plus étroites. Les informations réelles peuvent être décodées avec le logiciel Picoscope.
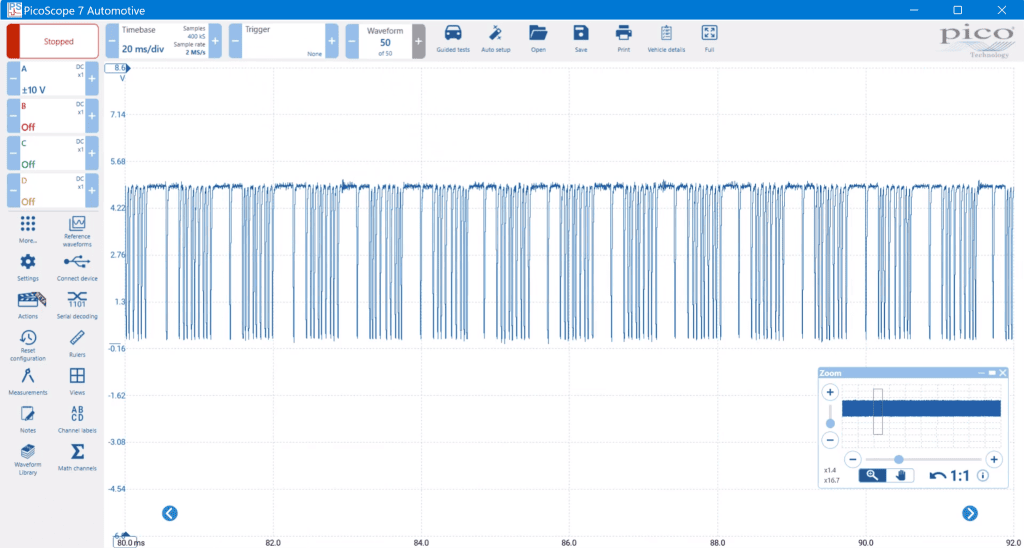
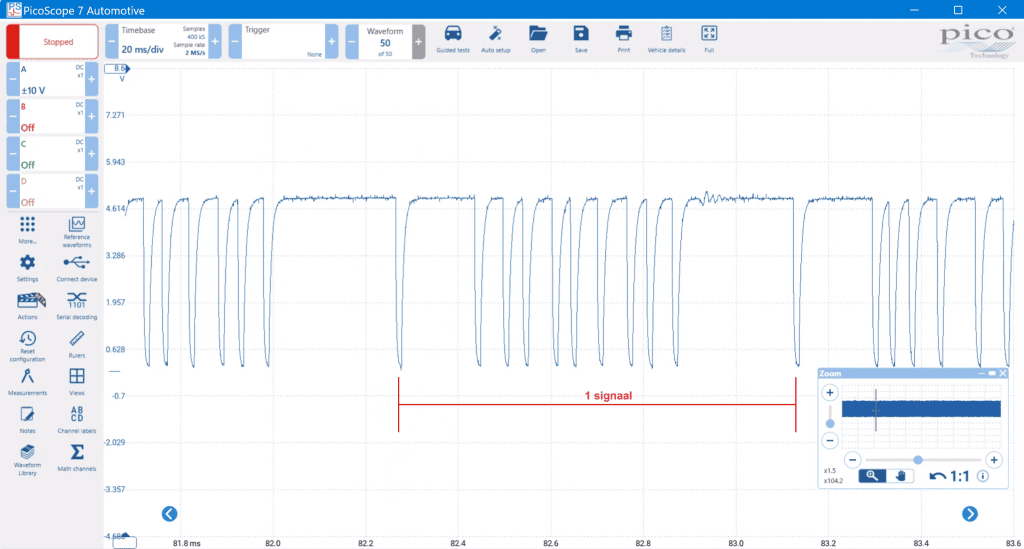
Avec un diagnostic électrique, nous pouvons utiliser le logiciel Picoscope pour décoder le message afin de l'étudier, mais dans la plupart des cas, nous nous concentrons sur la vérification d'un flux de message propre et sans bruit, et si la tension d'alimentation (5 volts) et la masse du capteur sont en être en ordre.
Alimentation et traitement du signal :
Dans les premiers paragraphes, il y avait une discussion sur la présence ou non d'une tension d'alimentation. Dans cette section, nous discutons des principaux composants de l'ECU qui sont responsables de l'alimentation en tension et du traitement du signal du capteur concerné. Les numéros de broches des schémas approfondis sont les mêmes que dans les paragraphes précédents : les broches 35 et 36 du calculateur sont connectées aux broches 1 et 2 du capteur passif, etc.
Sur la première image, nous voyons un Capteur de température NTC. La tension de référence (Uref) de la broche 35 de l'ECU est obtenue à partir du stabilisateur de tension 78L05. Le stabilisateur de tension fournit une tension de 5 volts à une tension de bord de 6 à 16 volts.
La résistance R (valeur de résistance fixe) et RNTC (résistance dépendante de la température) forment ensemble un circuit en série et également un diviseur de tension. Le convertisseur analogique-numérique (ADC) mesure la tension entre les deux résistances (analogique), la convertit en signal numérique et l'envoie au microprocesseur (µP).
Avec un multimètre, vous pouvez mesurer la tension sur la broche 35 de l'ECU ou la broche 1 du capteur.
Sur la page concernant le capteur de température En plus de quelques mesures pour une bonne transmission du signal, les techniques de mesure d'un défaut de câblage sont présentées.
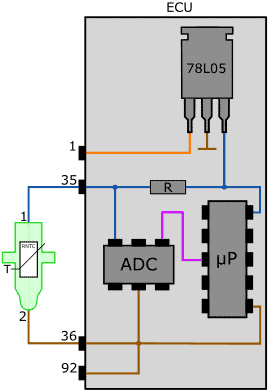
La deuxième image montre le circuit d'un actif Capteur de carte même.
La tension d'alimentation stabilisée de 5 volts atteint ce qu'on appelle "Pont de Wheatstone», qui comprend un certain nombre de résistances fixes (R1, R2, R3) et une résistance variable (Rp).
La valeur de la résistance Rp dépend de la pression dans le collecteur d'admission. Ici aussi, nous avons affaire à un diviseur de tension. Le changement de résistance provoque des changements de tension, provoquant un déséquilibre du pont. La différence de tension créée dans le pont de Wheatstone est convertie dans l'amplificateur/filtre en une tension d'une valeur comprise entre 0,5 et 4,5 volts. La numérisation du signal analogique a lieu dans le convertisseur analogique-numérique (ADC). L'ADC envoie le signal numérique au microprocesseur.
La résolution de l'ADC est dans la plupart des cas de 10 bits, répartis sur 1024 valeurs possibles. À une tension de 5 volts, chaque pas correspond à environ 5 mV.
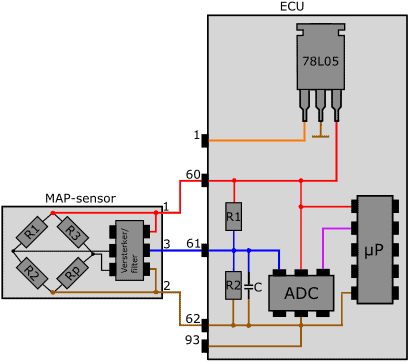
Le circuit interne de l'ECU contient un ou plusieurs capteurs passifs et actifs résistances inclus dans les circuits d’alimentation et de signal. La résistance dans le circuit NTC est également appelée «résistance de polarisation» et sert au diviseur de tension. Le but des résistances R1 et R2 dans le circuit ECU du capteur MAP est de permettre à un petit courant de circuler du plus vers la masse.
Sans ces résistances, une « mesure flottante » se produirait si le fil de signal ou la fiche du capteur était retiré. Dans ces cas, le circuit avec résistances garantit que la tension sur l'entrée ADC est augmentée à environ 5 volts (moins la tension aux bornes de la résistance R1). L'ADC convertit la tension analogique en valeur numérique 255 (décimale), c'est-à-dire FF (hexadécimal) et l'envoie au microprocesseur.
Un très petit courant traverse la résistance R1 (faible ohmique). Il y a une petite chute de tension comprise entre 10 et 100 mV. Il peut arriver que la tension appliquée soit supérieure de quelques dixièmes à 5 volts ; Une résistance basse impédance est incluse entre la connexion de masse du stabilisateur de tension 78L05 et la masse du calculateur (fil marron dans le schéma ci-dessus). La chute de tension aux bornes de cette résistance peut être par exemple de 0,1 volt. Le stabilisateur de tension considère sa connexion à la terre comme étant de 0 volt réel, il élève donc la tension de sortie (le fil rouge) de 0,1 volt. Dans ce cas, la tension de sortie au plus du capteur n’est pas de 5,0 mais de 5,1 volts.
Le capteur intelligent reçoit une tension de 12 volts de l'ECU. Tout comme le capteur actif, le capteur intelligent comprend un pont de Wheatstone et un amplificateur/filtre. La tension analogique de l'amplificateur est envoyée à l'interface LIN (LIN-IC).
L'interface LIN génère un signal de bus numérique LIN. Le signal varie entre 12 volts (récessif) et environ 0 volt (dominant). Le capteur utilise ce signal du bus LIN pour communiquer avec les autres esclaves (généralement les capteurs et actionneurs) et le maître (l'unité de contrôle).
Il y a des branches vers le maître et les autres esclaves sur le fil entre la broche 3 du capteur et la broche 64 de l'ECU.
Pour plus d'informations, consultez la page Autobus LIN.
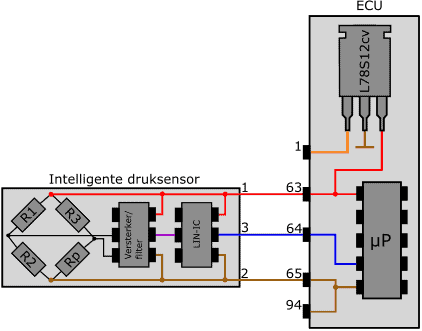