Themen:
- Einführung
- Messung ohne Störungen
- Fehler 1 – Signalleitung unterbrochen
- Fehler 2 – Unterbrochenes Stromversorgungskabel
- Fehler 3 – Unterbrochenes Erdungskabel
- Fehler 4 – Übergangswiderstand
- Fehler 5 – Kurzschluss zwischen Strom- und Signalleitung
- Fehler 6 – Kurzschluss zwischen Strom- und Erdungskabel
- Fehler 7 – Kurzschluss im Sensor C
- Fehler 8 – Keine Versorgungsspannung aufgrund defekter ECU
- Fehler 9 – Unterbrechung des PWM-Signalkabels
- Reparatur einer unterbrochenen Plusleitung
Einführung:
Wenn wir den Verdacht haben, dass eine Störung vorliegt, scannen wir zunächst das Auto. Der Fehlercode gibt uns eine Richtung, in der wir unsere Suche fortsetzen können. Sind keine Fehlercodes im Fehlerspeicher hinterlegt, prüfen wir, ob wir Abweichungen in den Live-Daten erkennen können. Siehe die Seite On-Board-Diagnose.
Bezieht sich der Fehlercode auf einen Sensor, bedeutet das nicht, dass der Sensor defekt ist. Um auszuschließen, ob ein Problem in der Verkabelung und/oder den Steckverbindungen vorliegt, verwenden Sie: elektrische Diagramme und Messgeräte schließen bestimmte Dinge aus. Diese Seite beschreibt eine Reihe möglicher Situationen und zeigt, dass die Beschreibung des Fehlercodes von der tatsächlichen Ursache abweichen kann.
Störungsfreie Messung:
Die folgende Abbildung zeigt die Messung der Versorgungsspannung und Masse eines aktiven Sensors.
Der aktive Sensor erhält über ihn ein Plus (5 Volt) und eine Masse Kontrollgerät. In diesem Fall ist die Stromversorgung in Ordnung. Wir können eine zweite Messung am Erdungskabel durchführen (Pin 3 am Sensor und/oder Pin 4 am Steuergerät). Das Signal muss zwischen 0,5 und 4,5 Volt liegen.
Neben aktiven Sensoren befassen wir uns auch mit passiven und intelligenten Sensoren. Lesen Sie mehr dazu auf der Seite: Sensortypen und Signale.
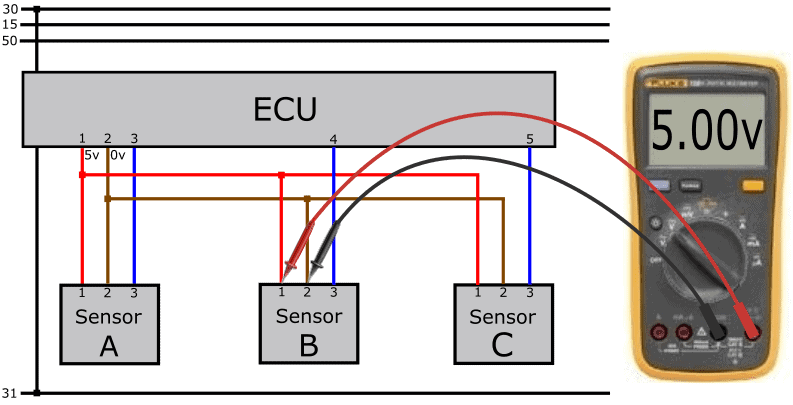
Zur Signalbildung nutzt der Sensor die 5 Volt Versorgungsspannung. Das Signal muss zwischen 0,5 und 4,5 Volt liegen. Das Steuergerät liest den Spannungspegel (oder in anderen Fällen die Frequenz) und wandelt diesen in einen Wert um. Dies könnte beispielsweise der Wert sein Ladedrucksensor sind: Bei einem Turbodruck von 1,5 bar sendet der Sensor eine Spannung von 3,25 Volt an das Steuergerät.
Bei dieser Messung wird die Signalspannung gegen Masse gemessen und ist in Ordnung.
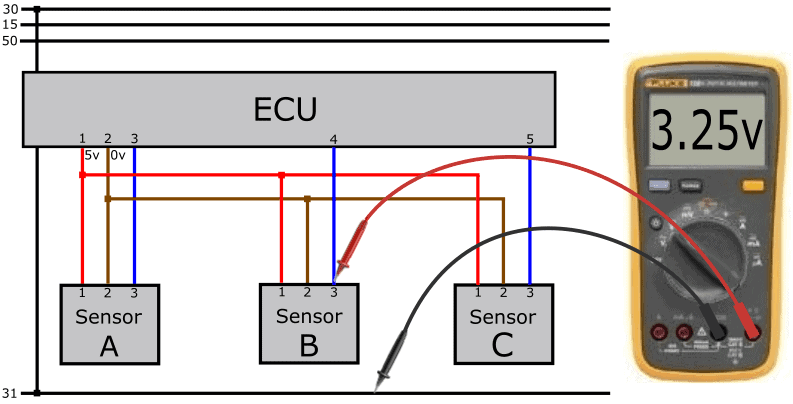
Verwenden eines Breakout-Box Wir können im Stecker des Steuergeräts messen. Wir wissen dann, welche Spannungen das Steuergerät sendet und empfängt.
Bei der nächsten Messung messen wir erneut 3,25 Volt, allerdings dann am Eingang der ECU. Das bedeutet, dass die Signalleitung in Ordnung ist: Die Spannung wird 1:1 vom Sensor zum Steuergerät übertragen.
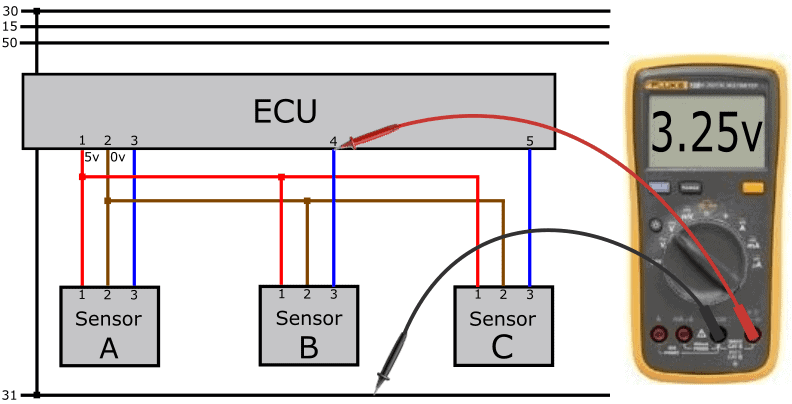
Das Sensorsignal wird niemals 0,0 oder 5,0 Volt betragen. Eine bestimmte Reichweite wird immer eingehalten. Diese liegt häufig zwischen 0,5 und 4,5 Volt. Der Sensor gibt keine Spannungen unter 0,5 oder über 4,5 Volt aus. Bei Defekten an den Sensoren oder der Verkabelung kann das Steuergerät anhand der Höhe der Spannung erkennen, ob der Wert innerhalb oder außerhalb des Messbereichs liegt:
- Spannungen unter 0,5 Volt: Das Steuergerät generiert einen Fehlercode mit der Beschreibung: „Sensor
- Bei Spannungen über 4,5 Volt wird in der Beschreibung des Fehlercodes „Pluskreis“ angegeben.
Aktive Sensoren können auch ein digitales Signal senden. Die Versorgung dieser Sensoren erfolgt häufig nicht über das Steuergerät, sondern über Klemme 15. In den meisten Fällen handelt es sich um ein PWM-Signal.
Das folgende Bild zeigt einen Teil des Schaltplans, in dem ein aktiver Sensor über eine externe Stromversorgung verfügt und die Signalleitung über Pin 3 des Sensors mit Pin 4 der ECU verbunden ist. Mit dem Oszilloskop wird der Spannungsverlauf des Sensors gegenüber dem Masseanschluss gemessen.
Das Oszilloskop ist auf 2 Volt und 5 Millisekunden pro Teilung eingestellt. Die Einschaltdauer beträgt 50 %.
Im Absatz: Fehler 9 – Unterbrechung des PWM-Signalkabels Wir besprechen die Schritte zur Erstellung einer korrekten Diagnose.
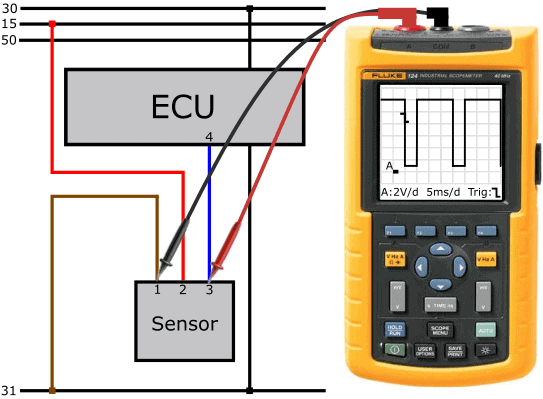
Diagnose der Sensorverkabelung:
Bevor wir Sensoren diagnostizieren, müssen wir uns über die Art des Sensors (passiv, aktiv, intelligent) und die Art und Weise im Klaren sein, wie der Sensor sein Signal an das Steuergerät sendet (analog oder digital, in Form einer AM (Amplitudenmodulation) oder FM (Frequenzmodulation). Nach Betrachtung des Schaltplans können wir abschätzen, welche Spannungen wir an der Verkabelung messen werden.
Die folgenden Absätze beschreiben mögliche Störungen, die in der Praxis auftreten können. Anstatt mit „der Beschwerde des Kunden“ zu beginnen, wird gleich der Grund genannt; z.B.: eine Leitungsunterbrechung, ein Kurzschluss usw. Hier geht es darum, einen Einblick in die Messtechnik zu gewinnen. Denn wie verhält man sich im Störungsfall? Und mit welchen Messungen ermitteln Sie die Ursache?
Beherrschen Sie die Messtechnik und sind Sie neugierig auf einen Fall? Dann besuchen Sie die Seite: Fall: Fehlfunktion des Kraftstoffdrucksensors, Kurzschluss mit Plus.
Fehler 1 – Signalleitung unterbrochen:
Wenn die Signalleitung unterbrochen ist, kann die Signalspannung vom Sensor nicht zum Steuergerät gelangen. In diesem Abschnitt können Sie nachlesen, was Sie in dieser Situation an den Anschlüssen des Sensors und des Steuergeräts messen.
Wir führen folgende Messungen am aktiven Sensor durch und erhalten folgende Messwerte:
- Stromkabel (Pin 1) relativ zur Sensormasse (Pin 2). 5 Volt;
- Signalspannung gegen Masse 2,9 Volt.
Die Stromversorgung und das erzeugte Sensorsignal sind in Ordnung. Aufgrund der Unterbrechung gelangt das Sensorsignal jedoch nicht zum Steuergerät.
Um die Spannung am Eingang des Steuergeräts zu messen, verwenden wir eine Breakout-Box.
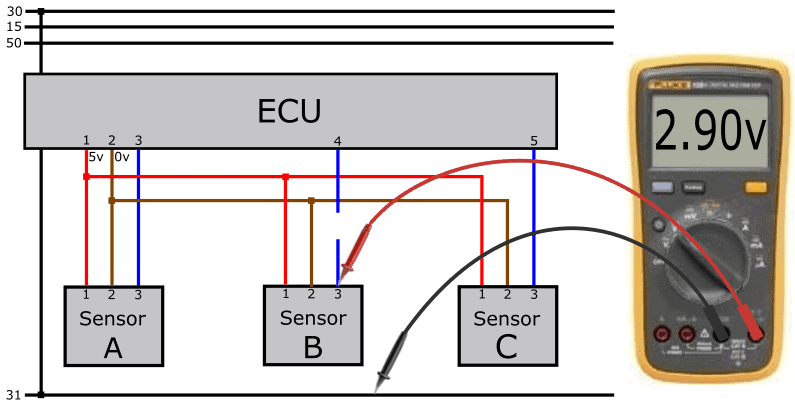
Mithilfe einer Breakout-Box führen wir eine Messung an Pin 4 des Steuergeräts im Vergleich zur Masse (oder Pin 2 des Sensors) durch. Wir messen eine Spannung von 4,98 Volt.
Die Spannung auf der ECU-Seite ist daher höher als die vom Sensor gesendete Spannung. Für die Ausgangsspannung von 4,98 Volt ist ein Schaltkreis im Steuergerät verantwortlich. Dies hängt zum einen mit der Art der Signalverarbeitung zusammen, aber auch mit der Erkennung von Unterbrechungen.
Das Steuergerät misst nun seine eigene Ausgangsspannung und erkennt diese aufgrund der Versorgungsspannung von 4,98 Volt als Pluskreis.
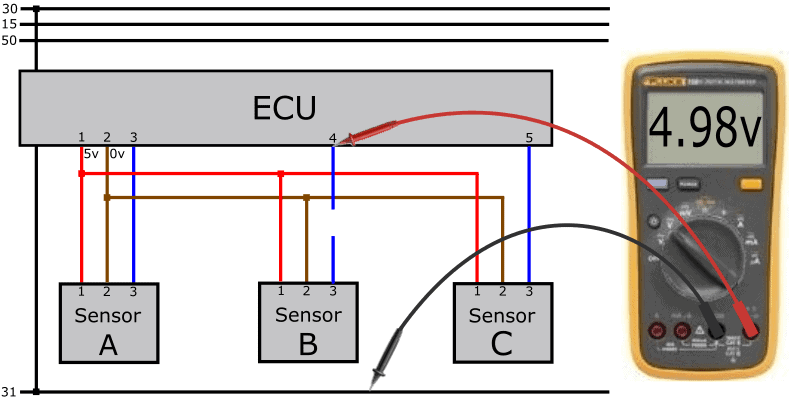
Anschließend messen wir die Spannungsdifferenz zwischen dem Steuergerät und dem Sensor. Im störungsfreien Zustand muss die Spannungsdifferenz nahezu 0 Volt betragen.
In diesem Fall messen wir eine Spannungsdifferenz von 2,08 Volt; nämlich 2,9 Volt (Sensor) im Vergleich zu 4,98 Volt (ECU).
Die Spannungen können Sie auf die falsche Spur bringen.
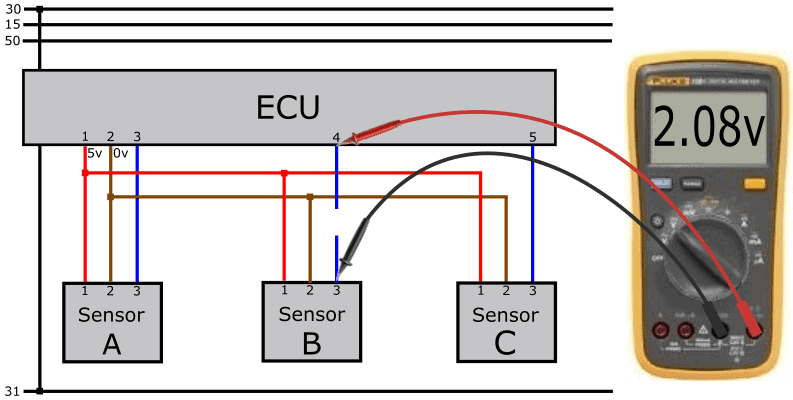
Entfernen Sie den Stecker vom Sensor. Wenn es keinen Kabelbruch gäbe, würden wir im ausgebauten Stecker 4,98 Volt vom Steuergerät messen. Jetzt messen wir 4 Volt an Pin 4,98 der ECU, aber 0 Volt im ausgebauten Stecker.
In diesem Fall können wir bereits auf eine Unterbrechung der Signalleitung schließen.
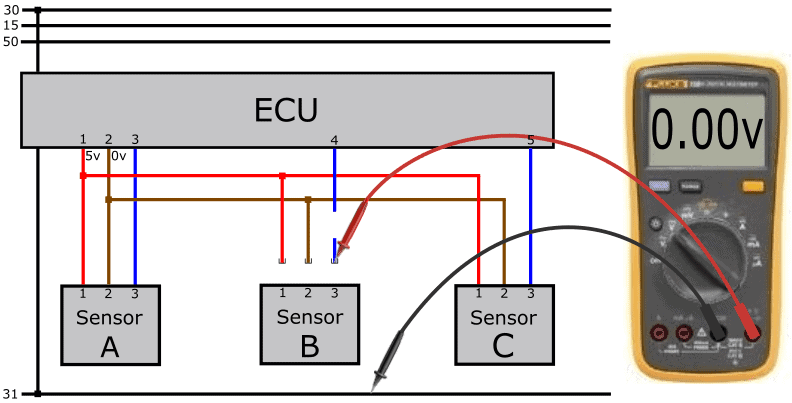
Bei unterbrochener Signalleitung beträgt die Spannung am Signaleingang des Steuergeräts ca. 5.0 Volt. Auf der Seite: Sensortypen und SignaleIm Abschnitt „Spannungsversorgung und Signalverarbeitung“ können Sie nachlesen, wie das Steuergerät das Signal des aktiven Sensors verarbeitet. Mit diesem Wissen können Sie besser verstehen, wie wir mit Störungen wie der unterbrochenen Signalleitung umgehen können.
Im Steuergerät wird eine Spannung von 4,98 Volt erzeugt. Zwischen dem Pluskabel (vom 78L05) und dem ADC gibt es eine Reihe von Widerständen, die die Signalspannung auf 5 Volt ziehen, wenn über den Signalanschluss keine Spannung eingeht. Der ADC misst diese Spannung und verarbeitet diese Spannung in ein digitales Signal. Das Steuergerät erhält daher ein Signal über eine außerhalb des zulässigen Bereichs liegende Spannung und generiert einen Fehlercode.
Bitte beachten Sie: Bei einem ähnlichen Fehler beträgt die Spannung nicht immer genau 4,98 oder 5,0 Volt!
Auf der Seite: Fall: Fehlfunktion des Kraftstoffdrucksensors – Kurzschluss mit Plus Es wird ein Fehler beschrieben, bei dem dieser Spannungswert abweicht.
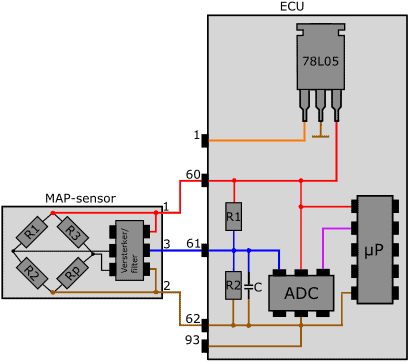
Fehler 2 – Unterbrechung der Stromversorgungsleitung:
Zwischen der Verbindung des Pluskabels zwischen den drei Sensoren und dem Sensorstecker liegt eine Unterbrechung vor. Die 5-Volt-Versorgungsspannung kann den Sensor jetzt nicht erreichen. Ohne Versorgungsspannung und Masse kann der Sensor nicht funktionieren.
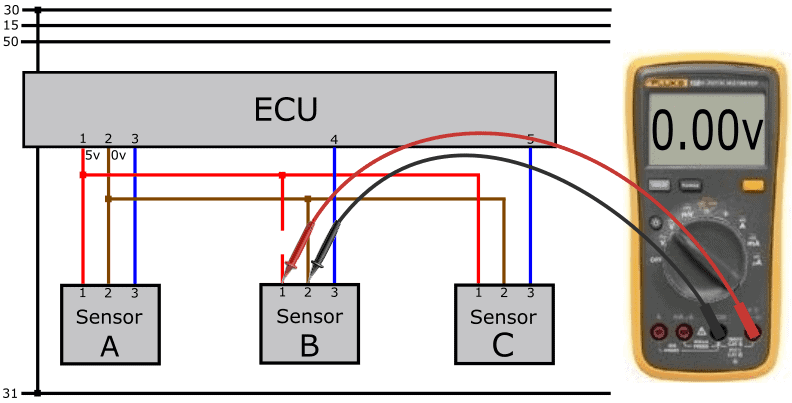
Da wir bei der vorherigen Messung die Stromversorgung und die Masse am Stecker gemessen haben, müssen wir noch ausschließen, bei welcher der beiden Leitungen ein Problem vorliegt. Wir messen daher das Plus an einem anderen Sensor im gleichen Plusstromkreis. Dies kann natürlich auch am Steuergerät erfolgen, sofern eine Breakout-Box vorhanden ist.
Wir messen 1 Volt an Pin 5 von Sensor A im Vergleich zur Masse von Sensor B. Das bedeutet, dass die Masse von Sensor B in Ordnung ist.
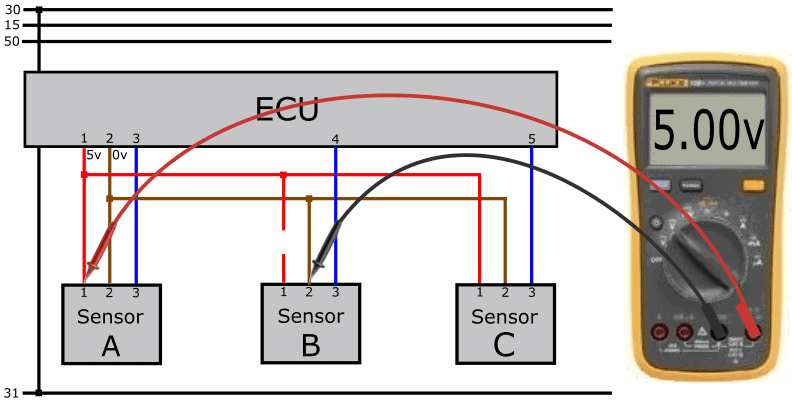
Wenn aufgrund der unterbrochenen Stromversorgungsleitung kein Strom durch die Elektronik des aktiven Sensors fließt, messen wir am Signaleingang des Steuergeräts eine Spannung von 4,98 Volt. Wir haben eine ähnliche Situation wie bei der unterbrochenen Signalleitung: Die internen Widerstände im Steuergerät ziehen die Signalspannung hoch: auf 4,98 Volt. Da in diesem Fall die Signalleitung in Ordnung ist, messen wir zusätzlich die Spannung von 4,98 Volt am Sensorstecker.
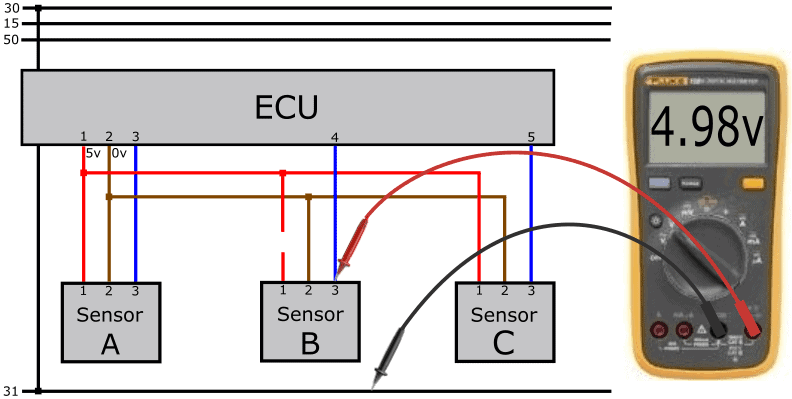
In Fällen, in denen die Spannung knapp über 5,0 Volt liegt, kann es sein, dass die Spannung des Spannungsstabilisators angehoben ist. Siehe den Absatz: „Spannungsversorgung und Signalverarbeitung“ auf der Seite: „Sensortypen und Signale".
Fehler 3 – Unterbrochenes Erdungskabel:
In diesem Fall ist nicht das Plus, sondern das Erdungskabel unterbrochen. Dem Sensor wird eine Versorgungsspannung von 5 Volt zugeführt, da wir aber gegen eine unterbrochene Leitung messen, hat das Voltmeter keine Referenzspannung und zeigt 0 Volt an.
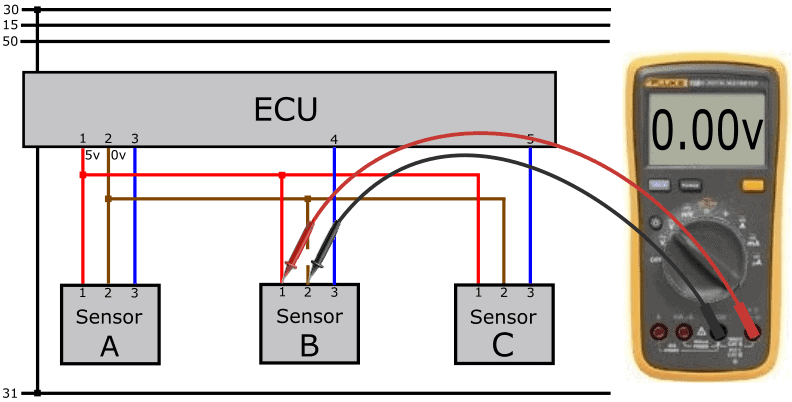
Wenn man den Minus-Messstift auf die Masse der Karosserie oder der Batterie legt, zeigt das Voltmeter tatsächlich 5 Volt an.
Wenn wir den negativen Messstift mit dem Masseanschluss der Sensoren A und C verbinden, müssen wir auch eine Differenz von 5 Volt messen. Würden wir an Pin 2 von Sensor A 5 Volt messen, an Sensor C jedoch nicht 5 Volt, dann läge die Unterbrechung in der Leitung zwischen Sensor A und B, also zwischen den ersten beiden Knoten.
Wie bei der unterbrochenen Signal- und Plusleitung messen wir nun auf der Signalleitung eine Spannung von 4,98 Volt.
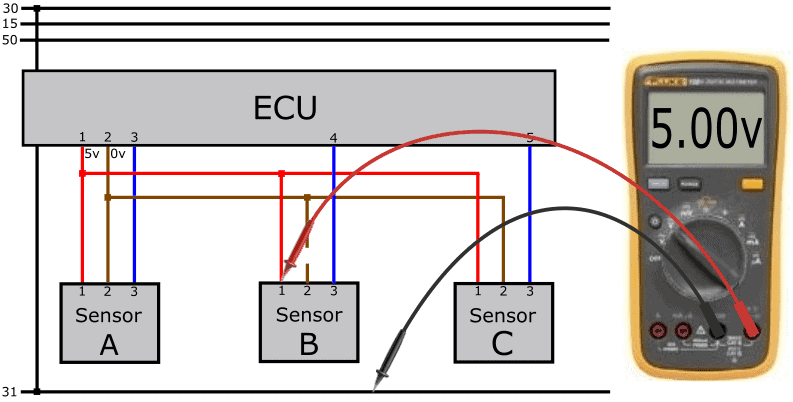
Fehler 4 – Übergangswiderstand:
Im vorherigen Absatz wurde bereits auf den Spannungsverlust durch einen Übergangswiderstand eingegangen. Im nächsten Diagramm sehen wir einen Widerstand im Stromkabel. Wenn Strom durch die Stromleitung fließt, sorgt der Übergangswiderstand für eine (vermutlich) zu niedrige Spannung an Pin 1 von Stecker B. Wir messen 4 Volt statt der erwarteten 5 Volt.
Die gespeicherte DTC-Beschreibung kann in diesem Fall lauten: „Signal unterer Grenzwert unterschritten“.
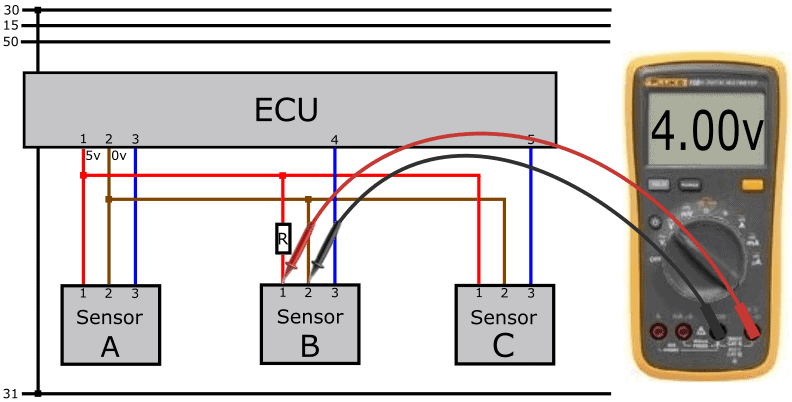
Wenn wir Pin 1 von Stecker B gegenüber Pin 1 von Stecker C messen, sollten wir eine Differenz von (5-5) = 0 Volt haben. Wir sehen jetzt einen Unterschied von 1 Volt.
Da der Spannungsverlust nur im Kabel von Sensor B und nicht von Sensor C auftritt, können wir davon ausgehen, dass das Kabel zwischen der Verbindungsstelle des horizontalen Kabels im Diagramm und dem Stecker nicht in Ordnung ist.
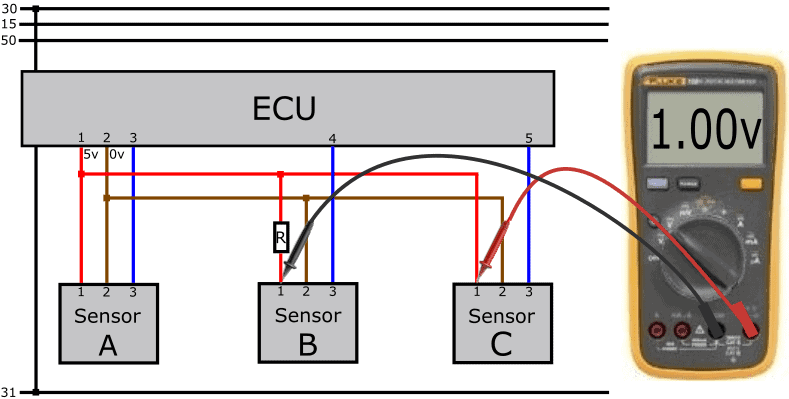
Fehler 5 – Kurzschluss zwischen Strom- und Signalleitung:
Ein möglicher Fehler in der Verkabelung ist ein Kurzschluss. Kurzschlüsse treten in folgenden Situationen auf:
- zwischen dem Stromkabel und dem Signalkabel (positiver Verschluss);
- zwischen dem Erdungskabel und dem Signalkabel (Massekurzschluss);
- zwischen einem der drei Kabel untereinander und/oder mit der Karosserie (Masseverbindung);
In diesem Diagramm sehen wir einen Kurzschluss zwischen der Signalleitung und der positiven Leitung (positiver Stromkreis). Wir messen eine Signalspannung, die der Versorgungsspannung von 5 Volt entspricht.
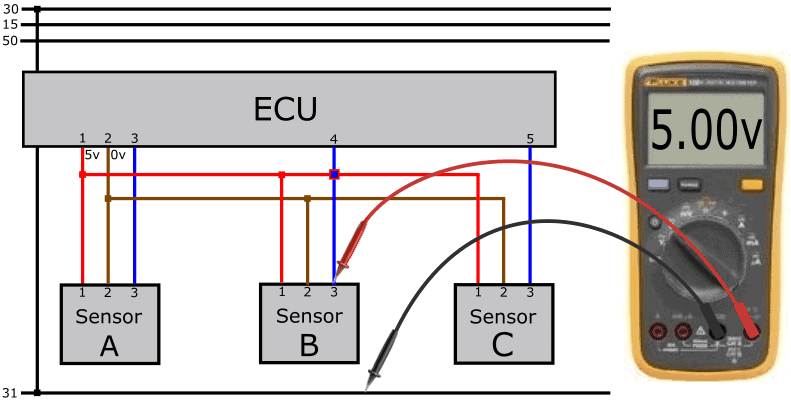
Wenn 5 Volt an Pin 3 des Sensors und Pin 4 des Steuergeräts gemessen werden, liegt das Problem möglicherweise intern am Sensor. Um dies auszuschließen, prüfen wir mit einem Ohmmeter, ob in der Verkabelung ein Kurzschluss vorliegt. Um eine sichere und korrekte Messung zu erhalten, schalten wir das Steuergerät aus, demontieren den Stecker des Steuergeräts und entfernen die Stecker der Sensoren, die an die Knoten angeschlossen sind. Da ein Kurzschluss vorliegt, messen wir eine Verbindung mit dem Ohmmeter.
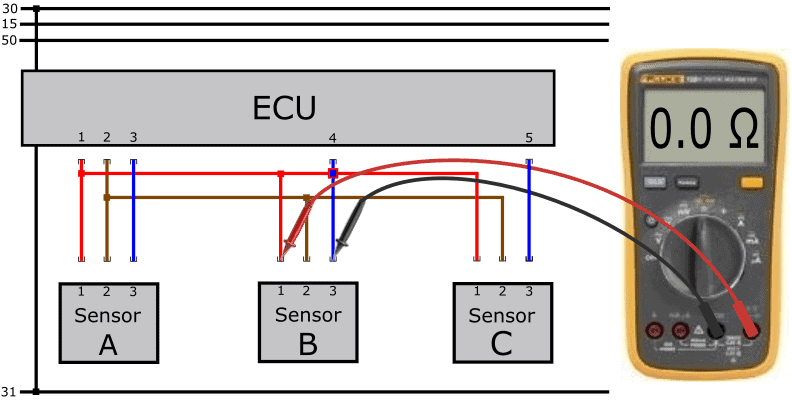
In diesem Fall beträgt er 0,0 Ohm, da die Drähte miteinander verbunden sind. In der Realität kann dieser Wert um einige Ohm höher liegen. Wenn kein Kurzschluss vorliegt, zeigt das Ohmmeter OL oder 1. (unendlich hoher Widerstand) an, da zwischen den Drähten und den Prüfspitzen keine elektrische Verbindung besteht.
Fehler 6 – Kurzschluss zwischen Strom- und Erdungskabel:
Bei einem Kurzschluss zwischen Strom- und Massekabel schaltet das Steuergerät die Spannungsversorgung an Pin 1 ab. Alle über Pin 1 gespeisten Sensoren funktionieren nicht mehr. Fehlercodes werden daher über mehrere Sensoren hinweg gespeichert.
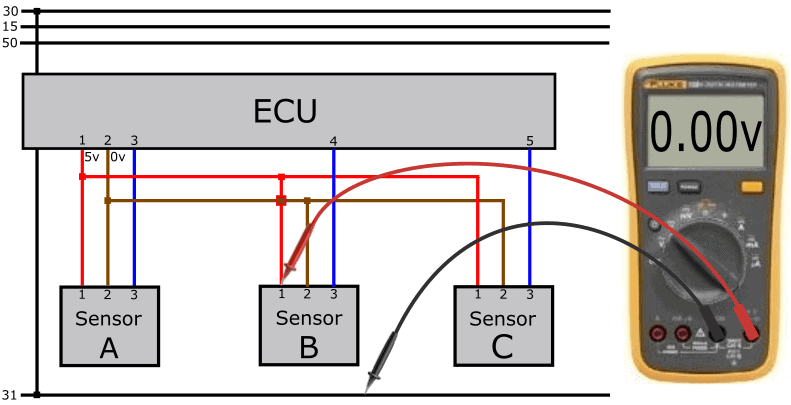
In diesem Fall messen wir auch eine Spannung von 5,0 auf der Signalleitung, die vom Steuergerät kommt.
Um auszuschließen, dass es sich um einen Kurzschluss handelt, zerlegen wir wie im vorherigen Absatz die Stecker sowohl des Steuergeräts als auch aller Sensoren im betreffenden Stromkreis. Messen Sie mit einem Ohmmeter den Widerstand zwischen dem roten und dem braunen Kabel.
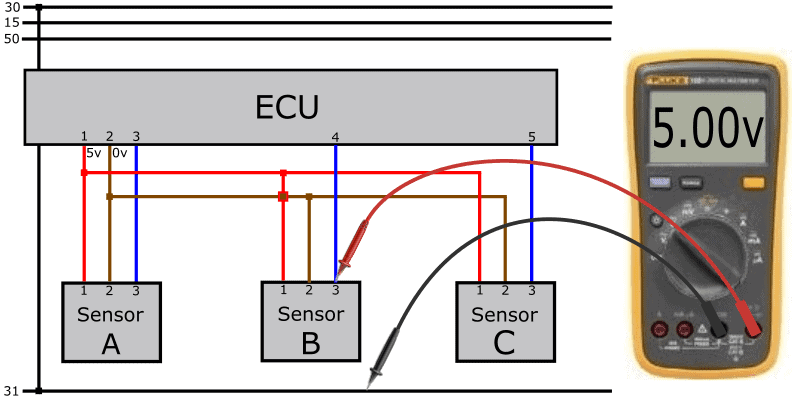
Fehler 7 – Kurzschluss im Sensor C:
Bei der Messung der Versorgungsspannung relativ zur Erde messen wir wiederum 0 Volt. Bei der vorherigen Störung hatten wir einen Kurzschluss in der Verkabelung. In diesem Fall liegt der Kurzschluss innerhalb eines Sensors.
Wir ziehen nacheinander die Stecker der Sensoren heraus, die wir im Diagramm sehen. Wenn Sie den Stecker vom Sensor C abziehen, liegt kein Kurzschluss mehr vor und das Steuergerät versorgt die Plusleitung wieder mit 5 Volt. Bei einigen Ausführungen geschieht dies automatisch, bei anderen Ausführungen ist ein Klammerwechsel erforderlich.

Fehler 8 – Keine Versorgungsspannung aufgrund defekter ECU:
In manchen Fällen kann es vorkommen, dass das Steuergerät für die fehlende Versorgungsspannung verantwortlich ist. Intern ist ein Stromkreis beschädigt und es werden keine 5 Volt ausgegeben.
Das Steuergerät wird oft fälschlicherweise als defekt gemeldet. In den meisten Fällen gibt es eine andere Ursache. Überprüfen Sie daher zunächst mögliche Unterbrechungen und Kurzschlüsse in der Verkabelung und den angeschlossenen Sensoren. Um auszuschließen, ob ein interner Defekt im Steuergerät die Ursache ist, überprüfen wir alle Masseverbindungen des Steuergeräts.
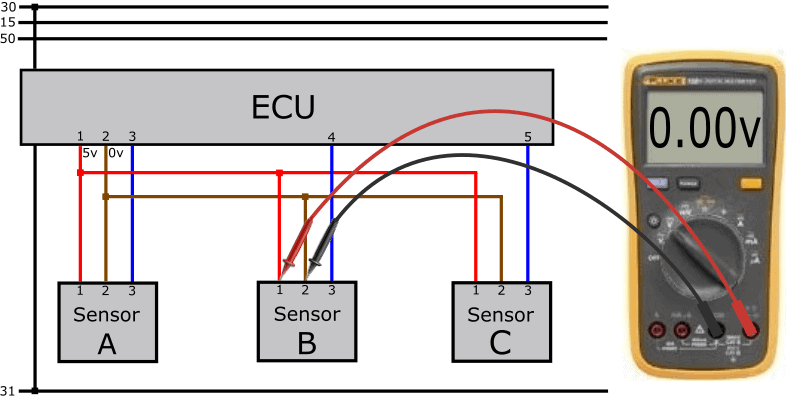
Bei einem umfangreichen Motormanagementsystem sehen wir in einem Steuergerät mehrere Schaltkreise, jeder mit seinem eigenen Erdungskabel. Manchmal finden wir bis zu acht Erdungskabel in einem Stecker. Sobald ein Stift im Stecker einen schlechten Kontakt hat oder ein Erdungskabel im Kabelbaum eine Unterbrechung aufweist, fällt dieser Stromkreis aus. Messen Sie daher am besten unter Last mit einer Prüflampe (Plus an der Batterie, Minus an jedem Masseanschluss im Steuergerätestecker), ob die Masse in Ordnung ist. Die Prüflampe muss an jedem Erdungskabel gleich hell brennen. Leuchtet die Lampe bei einem Masseanschluss nicht? Dann haben Sie möglicherweise die Ursache identifiziert und das Steuergerät ist nicht defekt.
Fehler 9 – Unterbrechung des PWM-Signalkabels:
Bisher haben wir über analoge Spannungen gesprochen, die mit einem Multimeter gemessen werden können. Handelt es sich um ein digitales Signal, reicht ein Multimeter nicht mehr aus. Wir nutzen dann das Oszilloskop. Im folgenden Text geht es um das Oszilloskop in den Bildern unten. Hier sehen wir den Fluke 124 mit veränderter Bildschirmdarstellung.
Der Grund für die Durchführung dieser Messung ist die Fehlerbeschreibung, die aus dem Fehlercode übersetzt werden kann. Die Beschreibung lautet: „Sensorsignal unterbrochen“.
Das Oszilloskopbild zeigt eine konstante Spannungslinie von 0 Volt. Dadurch besteht kein Spannungsunterschied zwischen den Messsonden. Haben Sie gemessen, dass die Plus- und Massekabel des Sensors in Ordnung sind (Pin 2 im Vergleich zu 1), in diesem Fall etwa 13 Volt, stimmt etwas mit dem Signalkabel nicht? Bitte beachten Sie, dass der Sensor die Informationen auf zwei Arten übertragen kann:
- Der Sensor sendet eine positive Spannung an das Steuergerät (normalerweise eine analoge Spannung;
- Das Steuergerät sendet eine Spannung, die vom Sensor zeitabhängig an Masse angelegt wird (mittels PWM; ein digitales Signal).
Im Beispiel beträgt die Signalspannung auf der Sensorseite 0 Volt, wir gehen also von Methode 2 aus.
Da die Signalleitung unterbrochen ist, erhält der Sensor keinen Strom vom Steuergerät.
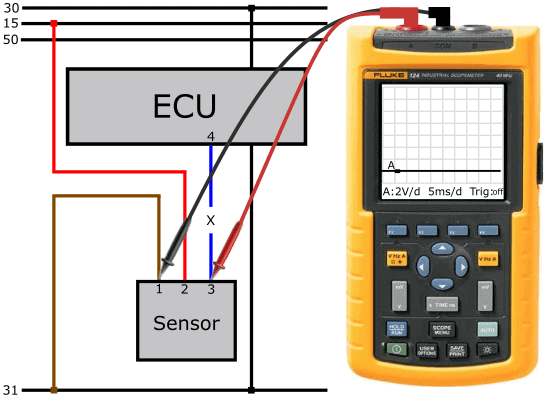
Wir messen Pin 4 der ECU gegen Pin 1 des Steckers. Die Spannung beträgt 12 Volt. Mit diesen Messungen haben wir festgestellt, dass der Sensoreingang des Steuergeräts in Ordnung ist.
Das Steuergerät sendet offenbar eine konstante Spannung, diese erreicht den Sensor jedoch nicht. Der Sensor hat daher keine Spannung zum Anschließen an Masse.
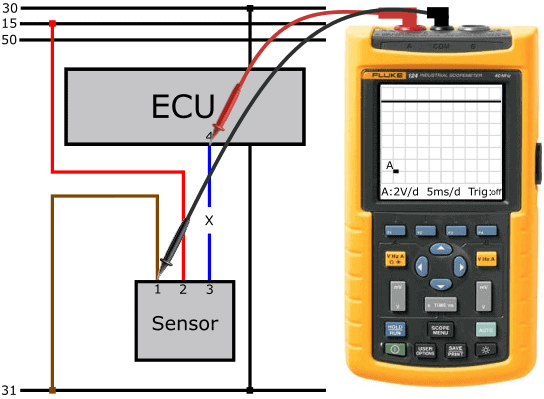
Bei der nächsten Messung verbinden wir die Messpins auf beiden Seiten der Signalleitung. Damit ermitteln wir die Spannungsdifferenz im aktiven Zustand über der Leitung. Im störungsfreien Zustand muss die Spannung 0 Volt betragen. Am aktiven Teil der Blockspannung sehen wir jedoch eine Spannung von 12 Volt. Wenn wir das bekommen voll Misst man die Versorgungsspannung im maximal positiven Teil der Blockspannung, dann handelt es sich in den meisten Fällen um eine unterbrochene Leitung. Dies ist nun auch der Fall: Die Ausgangsspannung der ECU (Pin 4 gegenüber Masse) beträgt 12 Volt.
Darüber hinaus sehen wir im unteren Teil des Blockspannung a Abweichung: dDie Spannungsleitung sinkt auf etwa 5 Volt, bleibt mit einer Welligkeit 10 Millisekunden lang konstant und steigt dann wieder auf 12 Volt an. Da das Oszilloskop nun in Reihe zwischen dem Pull-Up-Widerstand im Steuergerät und dem Pull-Down-Widerstand im Sensor geschaltet ist, entsteht eine Reihenschaltung. Das Oszilloskop hat einen hohen Innenwiderstand, der das Signal beeinflusst. Aus diesem Grund ist das Signal nicht nutzbar.
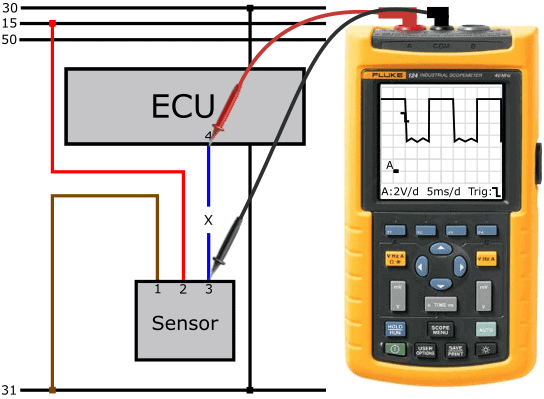
Obwohl die Messung der Belastungsspannung für eine gute Diagnose ausreichend ist, kann es nicht schaden, mithilfe einer Widerstandsmessung nachzuweisen, dass tatsächlich eine unterbrochene Verbindung im Kabel vorliegt. In diesem Fall messen wir einen unendlich hohen Widerstand (OL oder 1.)
Nach der Reparatur des Signalkabels messen wir erneut die Signalspannung gegen Erde. Bitte beachten Sie: Wir messen hier relativ zur Erde, daher ist der „aktive“ Teil des Sensors im PWM-Signal jetzt invertiert…
Wir sehen in diesem Scope-Bild Folgendes:
- Die Spannung beträgt maximal 12 Volt. Hier ist der Sensor nicht aktiv: Die Spannung auf der Signalleitung wird nicht gegen Masse gezogen.
- die Spannung sinkt auf 1 Volt. Hier ist der Sensor aktiv: Der Sensor legt die Spannung vom Steuergerät über die Sensorelektronik an Masse.
Der Sensor enthält eine elektronische Schaltung, die immer noch 1 Volt verbraucht. Anhand dieser Spannung erkennt das Steuergerät auch, dass der Sensor ordnungsgemäß einschaltet. Anhand der Spannungswerte kann das Steuergerät feststellen, ob der Sensor ordnungsgemäß funktioniert:
- Spannung über einen längeren Zeitraum gleich oder höher als 12 Volt:
ECU erkennt eine Unterbrechung bzw. Plusschaltung; - Spannung kleiner als 1 Volt: Das Steuergerät erkennt einen Masseschluss.
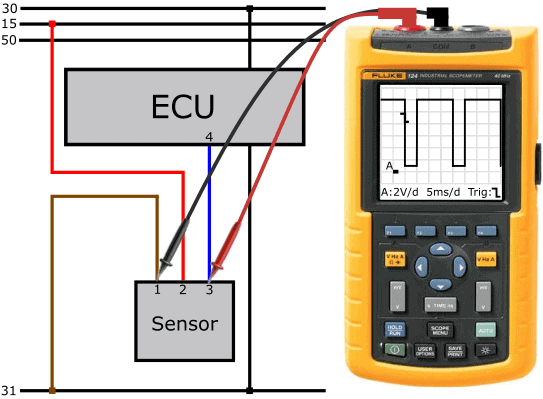
Eine unterbrochene Plusleitung reparieren:
Von den fünf in den vorherigen Absätzen beschriebenen Fehlern können diese in den meisten Fällen recht einfach behoben werden.
Schneiden Sie die Ader der Leitung mit dem Unterbrechungs- bzw. Übergangswiderstand im Kabelbaum möglichst kurz ab.
Bei Bedarf Isolierung anbringen. Suchen Sie den nächstgelegenen Sensor, der an denselben Stromkreis angeschlossen ist. Bei aktiven Sensoren können Sie dies leicht in einem Schaltplan finden. Im Diagramm ist C der nächstgelegene Sensor. Löten Sie einen neuen Draht sauber an den Plusdraht.
Arbeiten Sie immer mit Schrumpfschläuchen, um künftigen Problemen durch eindringende Feuchtigkeit vorzubeugen. Wenn Sie diese mit Isolierband verschließen, entstehen in absehbarer Zeit neue Probleme!
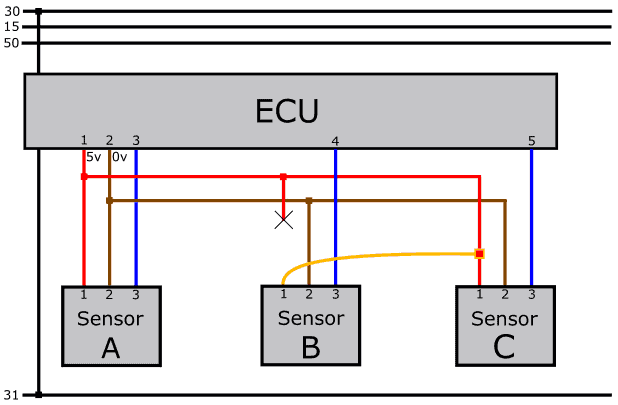