Themen:
- Der Beginn des Projekts
- Motor
- Getriebe
- Motorteile prüfen, austauschen und einstellen
- Montieren Sie den Motor auf einem mobilen Rahmen
- Kühlung
- Armaturenbrett und Elektroinstallation
- Kraftstoffpumpe und Tank
- Betreiben Sie den Motor im klassischen Setup
Der Beginn des Projekts:
Nachdem beschlossen wurde, einen Motor mit einem MegaSquirt-Motormanagementsystem auszustatten, wurde über einen geeigneten Motortyp nachgedacht. Standardkonvertierungspakete mit Handbüchern waren nicht interessant. Ziel war es, einen Motor zu verwenden, der die folgenden Bedingungen erfüllt:
- Es sollten keine früheren Umbauprojekte dieses Motors bekannt sein.
- Vierzylinder-Benzinmotor;
- noch nicht mit Einspritz- und elektronischer Zündanlage ausgestattet;
- die Fähigkeit, den Motor zu laden.
Motor:
Die Suche führte zu einem Motor eines Land Rover (Serie 2A) aus den frühen 70er Jahren. Dieser 2,25-Liter-Vierzylinder-Benzinmotor mit drei Hauptlagern war ursprünglich mit einem Vergaser und einer mechanischen Verteilerzündung ausgestattet. Ausschlaggebend für die Wahl war die Kombination dieses Land Rover-Motors und des Originalgetriebes; An der Abtriebswelle des Getriebes ist eine Getriebebremse angebracht. Die Getriebebremse, die eigentlich als Feststellbremse dient, ermöglicht es, den Motor während der Fahrt abzubremsen.
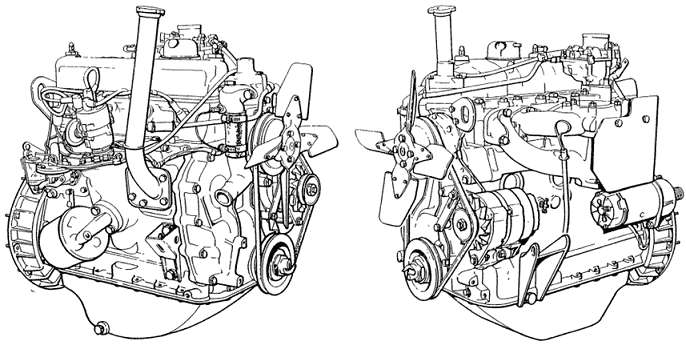
Der Motor hatte vermutlich jahrzehntelang nicht funktioniert. Natürlich muss es zuverlässig genug sein, um mit dem Motormanagementsystem zu laufen. Daher war es notwendig, den Motor zunächst gründlich zu inspizieren und zu testen. Folgende Ziele wurden festgelegt:
- Motorteile prüfen, austauschen und einstellen;
- Montieren Sie den Motor auf einem mobilen Rahmen.
- Lassen Sie die Engine im klassischen Setup laufen;
- Einbau von Komponenten für das Motormanagementsystem;
- MegaSquirt-ECU zusammenbauen und vorbereiten;
- Lassen Sie den Motor über das Motormanagementsystem laufen.
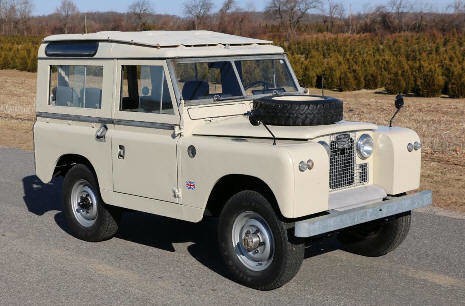
Getriebe:
Das Getriebe stammt von einem Armee-Land Rover. Die grüne Farbe verrät es tatsächlich. Um später mit dem Motor ein möglichst originales Ganzes zu bilden, wurde die grüne Farbe entfernt. Die Getriebebremse ist auf dem Foto noch nicht vorhanden; Dieser wurde später gemäß den Werksanweisungen an der Abtriebswelle montiert.
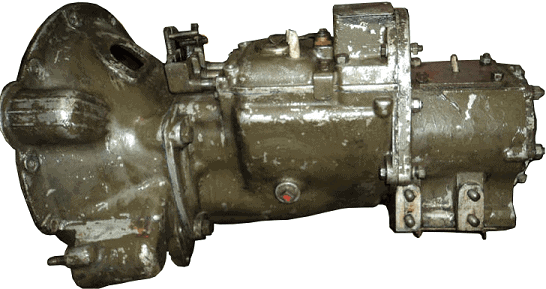
Motorteile prüfen, austauschen und einstellen:
Zu Beginn des Projekts war unklar, ob der zur Verfügung gestellte Motor für den Einsatz geeignet war. Über den Motorblock war wenig bekannt, nur dass der Motor jahrelang stillgestanden hatte. Es war unklar, ob interne Teile beschädigt oder sogar – möglicherweise irreparabel – defekt waren. Im letzteren Fall war der Austausch des Motors durch einen anderen die einzige Möglichkeit, das Projekt fortzusetzen.
Um zu einem späteren Zeitpunkt nicht den Schluss zu ziehen, dass der Motor unbrauchbar sein würde, wurde beschlossen, den Motor zu zerlegen und zu überholen. Verschleißmuster der Teile wurden überprüft und mit den Werksspezifikationen verglichen. Teile, bei denen die Maße innerhalb dieser Toleranzen lagen, wurden ersetzt. Ausgewiesene Teile wurden ersetzt. Der Verwendungszweck des Motors wurde berücksichtigt; Der Motor muss mit möglichst geringen Kosten gebaut werden, um ausreichend zuverlässig für die Umsetzung des Projekts und seinen Einsatz als Lehr- und Lernwerkzeug zu sein.
Der Motor wird an den Befestigungspunkten des Getriebegehäuses mit der Halterung befestigt. Der Motor kann in verschiedene Positionen gedreht werden. Dadurch sind sowohl der Zylinderkopf als auch die Ölwanne für Demontagearbeiten optimal zugänglich. Für die ordnungsgemäße Funktion des Motors ist es wichtig, Vorkehrungen zu treffen, um einen guten Kompressionsenddruck sicherzustellen. Ist der Druck in einem oder mehreren Zylindern zu niedrig, führt dies zu einem schlecht funktionierenden, schwächelnden Motor. In diesem Fall wird die Anpassung mit der neu eingebauten Zündung und dem Einspritzsystem schwierig, wenn nicht sogar unmöglich sein.
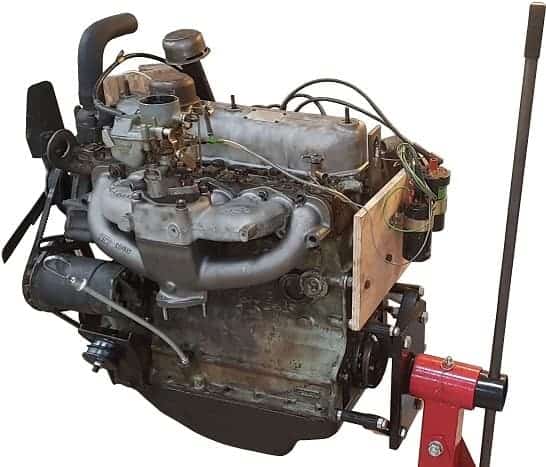
Einer der ersten Kontrollpunkte sind die Kolben und Zylinderwände. Um eine ordnungsgemäße Kontrolle zu gewährleisten, mussten die Kolben aus dem Motorblock entfernt werden. Nach der Demontage von Zylinderkopf und Ölwanne konnten die Kolben ausgebaut werden. Die Kolben wurden auf Ovalität und sichtbare Verschleißerscheinungen überprüft. Auch die Kolbenringe wurden auf Verschleiß geprüft. Abgenutzte Kolbenringe können zu Kompressionsverlust und Ölverbrauch führen; beide Konsequenzen müssen durch diese Prüfung verhindert werden. Neben einer optischen Kontrolle wurde auch das Spiel zwischen den Kolbenringnuten und dem Kolbenring gemessen.
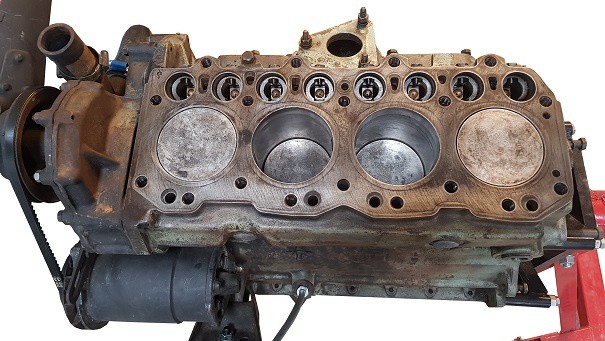
Das Bild unten zeigt eine Messung, bei der der Kolben mit einer Messschraube gemessen wird. Neben der Ovalität kann auch der Abstand zwischen Kolben und Zylinderwand bestimmt werden. Ein zu großer Abstand bedeutet übermäßigen Verschleiß. Für das Projekt würde dies bedeuten, dass möglicherweise weitere überschüssige Kolben eingebaut werden müssten. Nach einer visuellen und geometrischen Beurteilung der vier Kolben wurde festgestellt, dass kein übermäßiger Verschleiß vorlag.
Nach dem Austausch von Kolbenringen muss das endgültige Spiel gemessen und gegebenenfalls angepasst werden, um einen Bruch des Kolbenrings (aufgrund eines zu kleinen oder zu großen Spiels) und einen Kompressionsverlust (Leckverluste durch ein zu großes Spiel) zu verhindern ). Der Kolbenring wird dort in den Zylinder eingesetzt, wo der Durchmesser am kleinsten ist. Das Schlossspiel wird mit einer Fühlerlehre gemessen. Diese Messung ist in der Abbildung dargestellt. Die Kolbenringe von Zylinder 1 wurden aufgrund ihres schlechten Zustands ausgetauscht und mussten um einen Millimeter kleiner gefeilt werden; Im zusammengebauten Zustand berührten sich die Enden.
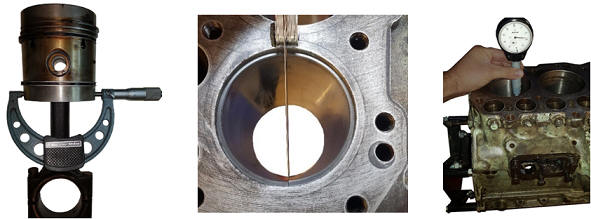
Die Messung des Verschleißes der Zylinderlaufbuchsen erfolgt mit einem geeigneten Messobjekt. Der Ausschlag des Zeigers zeigt den Grad der Abnutzung an. Das Bild zeigt die Zylindervermessung von Zylinder 4. Der Zylinderdurchmesser hat sich vergrößert, insbesondere auf der Seite, auf der die Gleitbahnkraft auftritt. Die Zylinderwände können einen gewissen Verschleiß aufweisen, der jedoch innerhalb der Toleranzen liegen muss. Die Messergebnisse zeigten einen akzeptablen Verschleiß an den Zylinderwänden. Eine optische Inspektion der Zylinderlaufbuchsen ergab, dass einige Teile der Wände glatt waren. Die Honrillen waren kaum noch vorhanden.
Die Honrillen, eine Art kleine Kratzer, sorgen dafür, dass immer ein kleiner Ölfilm zwischen Kolbenring und Zylinderwand vorhanden ist. Die Hauptaufgabe dieses Ölfilms ist die Schmierung, er dient aber auch als Dichtung und trägt so zum Erreichen des Endkompressionsdrucks bei. Mit einem geeigneten Honstein wurden in alle vier Zylinderlaufbuchsen neue Honnuten eingebracht. Das Bild zeigt diesen Vorgang. Es wurde versucht, die Honnuten möglichst kreuzweise in einem Winkel von 45 Grad anzubringen.
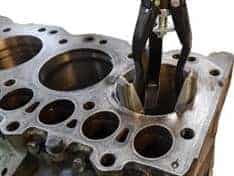
Die Ventile dichten den Brennraum oberhalb des Kolbens ab. Leckagen entlang des Ventilsitzes führen zu Kompressionsverlust; etwas, das verhindert werden sollte. Um den Zustand der Ventile und des Ventilsitzes zu prüfen, müssen zunächst alle Ventile aus dem Zylinderkopf ausgebaut werden. Das Bild zeigt eine demontierte Ventilfeder vom Einlassventil von Zylinder 1. Die Ventilteller der Ventile von Zylinder 1 waren so beschädigt, dass beschlossen wurde, beide auszutauschen.
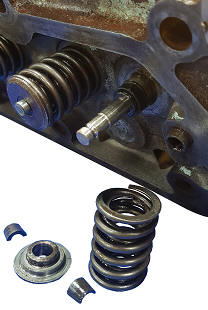
Nach der Demontage schienen einige Ventilsitze angefressen/beschädigt zu sein. Das Bild unten zeigt die Ventilsitze von Zylinder 1. Es ist sehr wahrscheinlich, dass der Motor nicht ordnungsgemäß funktioniert hätte, wenn dies nicht überprüft worden wäre. Ein bloßes Nachschleifen der neuen Ventile würde nicht ausreichen, daher entschied man sich für das Fräsen der Ventilsitze.
Mit einem Ventilsitzfräser wird eine kleine Menge Material abgetragen, sodass der Ventilsitz wieder glatt ist. Der Schaft des Fräsers wird in die Ventilführung geschoben (siehe Abbildung unten). Dadurch ist sichergestellt, dass der Fräser gerade auf dem Sitz platziert werden kann. Bei der Bearbeitung wurden zwei unterschiedliche Winkel berücksichtigt, in denen gefräst werden muss. Am stärksten betroffen waren die Ventile der Zylinder 1 und 2. Der Vollständigkeit halber wurden alle acht Ventilsitze bearbeitet. Nach dem Fräsen werden die Ventile mit einem speziellen Schleifmittel geschliffen, um eine bestmögliche Abdichtung zu gewährleisten.
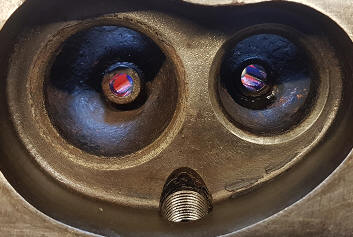
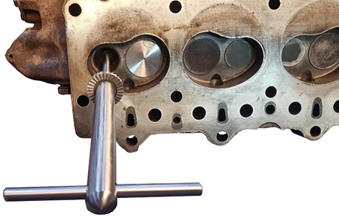
Das axiale Kurbelwellenspiel der Kurbelwelle mit drei Hauptlagern und zwei Axiallagern wird mit einer Messuhr gemessen. Bei zu großem Axialspiel kann, sofern kein mechanischer Defekt vorliegt, ein größeres Axiallager eingebaut werden. Die im Bild gezeigte Messung ergab, dass das Axialspiel in Ordnung war.
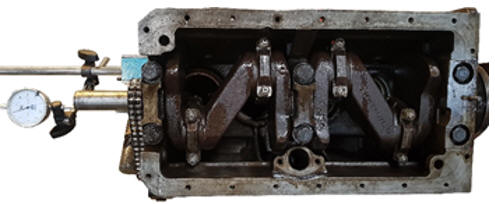
Der Abstand zwischen den Gleitlagern von Kurbelwelle und Pleuel, also das radiale Kurbelwellenspiel, wird mit Plastigage gemessen (siehe Abbildung). Plastigage ist ein spezieller Kunststoffdraht, der sich nach der Kompression dauerhaft verformt. Nach der Montage des Lagerdeckels oder Pleuels hinterlässt das Plastigage einen Abdruck. Die Breite des Aufdrucks gibt an, wie viel Spiel zwischen Gleitlager und Kurbelwelle vorhanden ist.
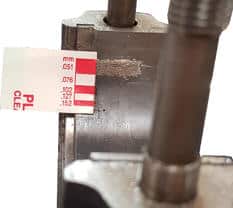
Die Steuerkette überträgt die Bewegung von der Kurbelwelle auf die Nockenwelle. Nach dem Einbau von Kolben, Kurbelwelle und Zylinderkopf muss die Steuerkette nach dem Einbau neu eingestellt werden. Aufgrund der fehlenden Justierung und Markierung musste die Justierung anhand des asymmetrischen Ventildiagramms ermittelt werden. Mithilfe einer Gradscheibe an der Kurbelwelle lässt sich der Öffnungs- und Schließwinkel der Einlass- und Auslassventile bestimmen (siehe Bild). Die Verteilerteile wie Kettenräder, Kette, Führung und Spanner wurden auf optische Abnutzungserscheinungen überprüft. Das war in Ordnung.
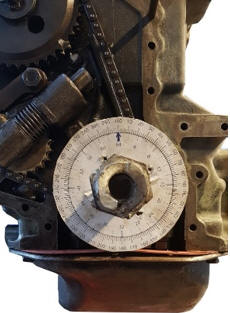
Alle Teile werden entsprechend den vorgeschriebenen Anzugsdrehmomenten angezogen. Da der Motor zerlegt wurde, müssen nach einigen gefahrenen Kilometern Kontrollen durchgeführt werden. Dies ist jedoch nicht möglich, da der Motor nicht in einem Fahrzeug verbaut ist. Daher wurde beschlossen, die von Land Rover vorgeschriebenen Kontrollen nach 24 Betriebsstunden durchzuführen.
Montage des Motors am Fahrgestell:
Ziel war es, den Motor als Lehrmittel zu nutzen, das auf einem Motormanagementsystem läuft. Der Motor ist nicht in einem Auto untergebracht. Um einen sicheren und zuverlässigen Aufbau zu gewährleisten, wurde beschlossen, den Motor auf einem geeigneten Motorrahmen zu platzieren. Ziel ist es, den Motor an den ursprünglichen Stellen der Motorlager am Motorrahmen zu befestigen. Da es keine fertigen Umbausätze gibt, mussten die Stützen individuell angefertigt werden.
In der Bauphase musste entschieden werden, wie der Motor aufgebaut sein sollte. Bei erhöhter Motorlast muss das Motormanagement angepasst werden. Da das Originalgetriebe über eine Getriebebremse verfügt, wurde beschlossen, das Getriebe auch am Motorrahmen zu montieren. Durch Betätigung dieser Getriebebremse ist es möglich, den Motor kurzzeitig unter Last laufen zu lassen.
Durch die Bearbeitung und Anpassung der vorhandenen Motorlager ist eine zuverlässige Anbindung des Motors an den Rahmen möglich. Der Motorrahmen bietet außerdem die Möglichkeit, ein Armaturenbrett anzubringen, auf dem unter anderem die Bedienelemente realisiert werden können. Das Bild zeigt den Moment, in dem der Motor über dem Rahmen hängt und zur Montage bereit ist.
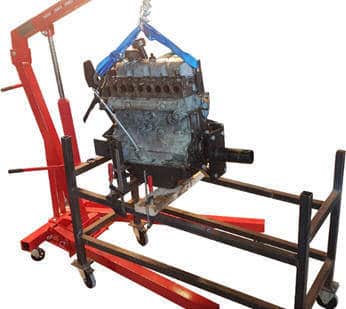
Die Motorlager auf der Verteilerseite bestehen aus Stahlrohren und U-Profilen. Für die Dämpfung sorgt ein Motorradgummi. Unten sind zwei Rohre übereinander montiert, um die Kombination aus Motorblock und Getriebe möglichst horizontal am Rahmen zu montieren. Die Halterungen werden mit M8- und M12-Gewindestangen, Bolzen und Muttern am Motorblock und Rahmen befestigt.
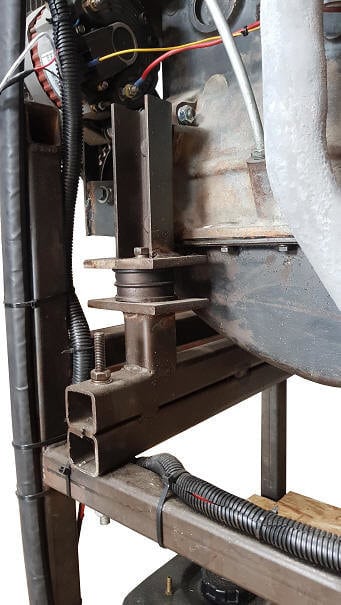
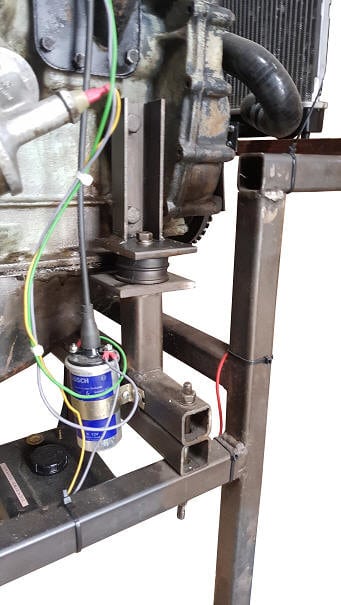
Auf beiden Seiten des Getriebes ist eine solche Getriebeabstützung angebracht, mit der es auf dem Rahmen aufliegt.
Nachdem Motor und Getriebe sicher und zuverlässig am Rahmen montiert waren, konnte mit der Motormontage fortgefahren werden. Nach dem Einbau von verstellbaren und einstellbaren Teilen, wie Vergaser und Zündung, wurden diese entsprechend den Werkswerten eingestellt.
Am Rahmen sind auch weitere Komponenten montiert, die den Betrieb des Motors ermöglichen, etwa der Kühler, das Armaturenbrett mit Bedienelementen und der Kraftstofftank. Diese Komponenten werden in den folgenden Abschnitten beschrieben.
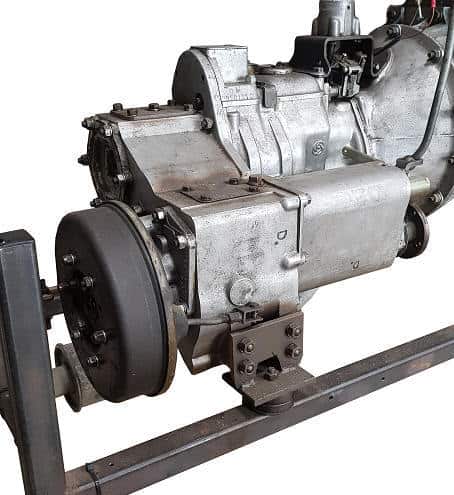
Kühlung:
Im Originalzustand erfolgt die Kühlung durch einen großen Kühler und einen an der Wasserpumpe montierten Kühlventilator aus Metall. Da der Motor nicht in einem Fahrzeug, sondern auf einem mobilen Rahmen montiert wird, ist es wichtig, geeignete Nachrüstkomponenten zu verwenden. Der Kühlventilator aus Metall wurde durch einen elektrisch betriebenen Kühlventilator mit Kunststoff-Lüfterflügeln ersetzt. Die Kunststoffversion ist nicht nur wesentlich sicherer, da der Motor für Ausbildungszwecke geeignet ist (berücksichtigen Sie beim Messen die persönliche Sicherheit), sondern eignet sich auch besser zum schnelleren Aufheizen von Kühler und Motorblock. Der elektrische Kühlventilator kann mit einer Taste am Armaturenbrett ein- und ausgeschaltet werden. Dies ermöglicht ein schnelles Aufwärmen des Motors, da kaum eine mechanische Belastung möglich ist. Bei warmem Motor entsteht eher ein „geschlossener Regelkreis“, bei dem die Daten der Lambdasonde zur Steuerung der Kraftstoffeinspritzung genutzt werden. Beispielsweise findet bei kaltem Motor – im „Open Loop“ – eine zusätzliche Anreicherung statt: Bei der Einspritzung einer größeren Kraftstoffmenge (λ < 1) ist die Kraftstoffkorrektur durch die Lambdasonde unerwünscht.
Die Abbildung zeigt eine Übersicht der Komponenten des verbauten Kühlsystems. Der Originalkühler war nicht vorhanden. Da seine Größe und sein Gewicht für die Montage am Motorradrahmen nicht geeignet waren, entschied man sich für einen kleineren Nachrüstkühler. Die Durchmesser der Anschlüsse der oberen und unteren Kühlerschläuche entsprechen den Originalen.
Die oberen und unteren Kühlerschläuche sind maßgefertigt mit Silikonschläuchen und Anschlüssen. Der elektrische Kühlventilator ist an einer Montagehalterung befestigt. Der obere Kühlerschlauch schützt den Kühler vor dem Umkippen. Eine Überdruckkappe (0,9 bar) schützt das Kühlsystem vor übermäßigem Druck. Steigt der Druck zu stark an, öffnet sich das Ventil im Kühlerdeckel gegen die Kraft und Kühlmittel fließt durch den Überlauf in einen Auffangbehälter.
Es musste experimentell ermittelt werden, ob der Kühler über eine ausreichend hohe Durchflussmenge verfügte und ob der Kühlventilator über ausreichende Kapazität zur Wärmeableitung verfügte. In der ersten Testphase wurde festgestellt, dass das System in Ordnung ist.
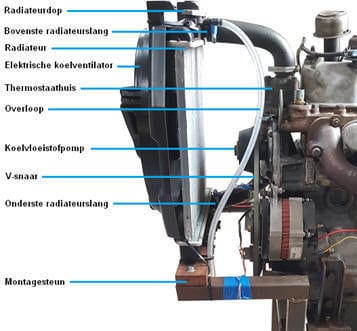
Armaturenbrett und Elektroinstallation:
Am Rahmen ist ein Armaturenbrett befestigt, auf dem sich Kontrollleuchten, Schalter, die MegaSquirt-ECU, diverse Relais und Kabelbündel befinden. Das Dashboard dient zur Überwachung und Steuerung der Motorfunktionen.
Das Bild zeigt das Dashboard. Nummer 1 in der Abbildung gibt die Position des Erdungsschalters an; Ein Schlüssel trennt die Batterie von der Masse. Da der ausgeschaltete Motor nicht mit Strom versorgt werden muss, ist es sicherer, die Erdung zu trennen, wenn der Motor unbeaufsichtigt bleibt. Nummer 2 bezeichnet den Lüfterschalter. Nummer 3 und 4 sind die Kontrollleuchten für die Lichtmaschine (D+), Nummer 5 ist der Startknopf und Nummer 6 ist der Zündschalter (Klemme 15). Auf der Rückseite des Armaturenbretts befindet sich ein Sicherungskasten. Der MegaSquirt ist auf der Bodenplatte montiert und mit der Nummer 7 gekennzeichnet. Nummer 8 bezeichnet das Kraftstoffpumpenrelais. Das Armaturenbrett bietet außerdem die Möglichkeit, eine Breakout-Box zu montieren, an der Studierende Messungen durchführen können. Dadurch ist es möglich, die Sensorwerte und Aktorsteuerungen mit dem Oszilloskop zu messen.
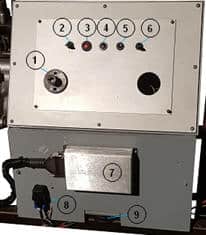
Das Original-Starterrelais steuert den Anlassermotor; Bei einem kleinen Startknopf wird Pin 86 mit Masse verbunden, wodurch ein Steuerstrom fließt. Der Steuerstrom erzeugt ein Magnetfeld, wodurch ein Hauptstrom zwischen den Anschlüssen 30 und 87 fließt. Der Anlassermotor wird mit diesem Hauptstrom versorgt, bis der Startknopf losgelassen wird.
Die nachgerüstete Lichtmaschine stellt die Ladespannung und den Ladestrom für die Batterie bereit. Eine Kontrollleuchte zeigt an, ob die Lichtmaschine ordnungsgemäß lädt. Lambdasonde, Einspritzdüsen und Zündspule erhalten vom Sicherungskasten eine Versorgungsspannung. Die Informationsübertragung sowie die Ein- und Ausschaltbefehle des MegaSquirt erfolgen über weitere Signal- und Erdungsleitungen.
Kraftstoffpumpe und Tank.
Die mechanische Kraftstoffpumpe im klassischen Aufbau wird beim Einbau der Komponenten des Motormanagementsystems nicht mehr verwendet, da der Betriebsdruck zu niedrig ist (200 mbar). Der erforderliche Kraftstoffdruck für MPI-Injektoren, die von der MegaSquirt-ECU gesteuert werden, beträgt 3 bar. Eine handelsübliche elektronische Kraftstoffpumpe aus einem Pkw reicht aus. Aufgrund der begrenzten Platzverhältnisse wurde eine kompakte Einheit gewählt, bei der Kraftstofftank, Pumpe und Filter in einem Gehäuse untergebracht sind. Ein Metallrahmen ermöglicht die Montage des Geräts am Motorrahmen. Zu einem späteren Zeitpunkt des Projekts werden die Kraftstoffschläuche installiert, die die Verbindung zwischen der Kraftstoffpumpe und den Einspritzdüsen im Saugrohr herstellen.
Die Stromleitungen von der Kraftstoffpumpe verlaufen über einen Kabelkanal zur Instrumententafel, deren Einbau bereits beschrieben wurde. Die Plusleitung der Pumpe wird vom MegaSquirt über ein Relais mit Strom versorgt.
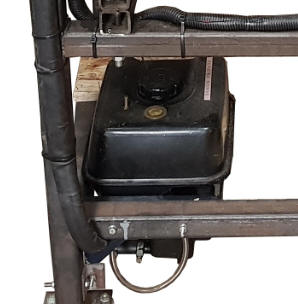
Betreiben Sie den Motor im klassischen Setup.
Bevor die Komponenten für das Motormanagement eingebaut werden, wurde der Motor zunächst im klassischen Setup, also mit Vergaser und Verteilerzündung, funktionsfähig gemacht. Kapitel 5.2 beschreibt die Arbeiten zur Montage des Motors und der Nebenaggregate am Motorrahmen. In der ersten Testphase, in der der Motor im klassischen Setup gestartet wurde, konnten Prüfungen unter folgenden Bedingungen durchgeführt werden:
- Kaltstart;
- Leerlauf;
- Erhöhte Geschwindigkeit, erhöhte Last;
- Langzeitbetrieb bei Betriebstemperatur.
Bei den oben genannten Kontrollen stellte sich heraus, dass noch einige Reparaturen durchgeführt werden mussten, bevor der Motor zuverlässig genug für den Umbau war.
- Nach dem ersten Motorstart stellte sich heraus, dass die Dichtung in der Kühlmittelpumpe nicht mehr in Ordnung war; Das Kühlmittel lief aus dem Motorblock entlang des Lagers. Der Austausch der Kühlmittelpumpe reichte aus, um das Problem zu lösen.
- Das nächste Problem war das Abwürgen, wenn der Motor Betriebstemperatur erreichte. Die Zündung versagte, so dass der Motor nicht gestartet werden konnte. Das Problem lag beim Verteiler und konnte leicht gelöst werden.
- Im Laufe der Zeit bildete sich zwischen Motor und Getriebe ein Ölleck. Das Leck kommt wahrscheinlich von der Kurbelwellendichtung. Dieses Leck wird nach Abschluss des Projekts behoben.
Nachdem festgestellt wurde, dass der Motor im klassischen Setup in Ordnung ist, konnten wir mit der Elektronik fortfahren.
Weiter: Sensoren.