Themen:
- Aktoren für das Motormanagementsystem ermitteln und einbauen
- Einspritzdüsen
- Auswahl geeigneter Injektoren
- Einbau der Einspritzdüsen in den Ansaugkrümmer
- Entzündung
- Vorbereiten mit der konventionellen Zündung
- Zündspule für das Motormanagementsystem
- Stromaufbau in der Primärspule
- Zündvorlauf
- Drosselklappengehäuse
- Testaufbau des Schrittmotors mit Simulator
- Schrittmotoreinstellungen
- Kraftstoffpumpenkreislauf
- Abschluss der mechanischen Arbeiten
Ermittlung und Einbau von Aktoren für das Motormanagementsystem:
Die Aktoren, die mit dem MegaSquirt gesteuert werden, sind die Einspritzdüsen, die Zündspule, die Kraftstoffpumpe und der Schrittmotor für die Leerlaufdrehzahl. In diesem Kapitel wird der Prozess beschrieben, bei dem die Aktuatoren getestet und am Motorblock installiert wurden, sowie die getroffene Auswahl.
Einspritzdüsen:
Der MegaSquirt steuert die Injektoren. Die Injektoren sind mit Masse verbunden. Bei einem geerdeten Bauteil liegt eine Versorgungsspannung an, Strom fließt jedoch nur, wenn die Erde eingeschaltet ist. In diesem Fall spritzt der Injektor nur dann ein, wenn das MegaSquirt-ECU auf Masse schaltet. Sobald die Aktivierung gestoppt wird, stoppt der Injektor die Injektion. Die einzuspritzende Kraftstoffmenge wird anhand der VE-Tabelle und der AFR-Tabelle ermittelt.
Ein MOS-FET schaltet die Einspritzdüse ein und aus, wodurch der Kraftstoff eingespritzt wird. Die vom MegaSquirt ermittelte Treibstoffmenge hängt von mehreren Faktoren ab:
- Das ideale Gasgesetz, das die Luftmenge mit ihrem Druck, Volumen und Temperatur in Beziehung setzt;
- Von den Sensoren im Motorblock gemessene Werte: Druck im Ansaugkrümmer (MAP-Sensor), Kühlmittel- und Ansauglufttemperatur, Kurbelwellendrehzahl und die Daten des Drosselklappenstellungssensors;
• Einstellparameter: erforderliche Kraftstoffmenge, Füllgrad (VE), Einspritzöffnungszeit und Anreicherung unter bestimmten Bedingungen.
Um eine gute Kraftstoffdosierung zu erreichen, sollte die Einspritzzeit im Leerlauf des Motors möglichst lang sein. Daher kann nicht jeder beliebige Einspritzer am Motor verwendet werden. Die Eigenschaften unterschiedlicher Einspritzventiltypen müssen verglichen werden und Berechnungen müssen Aufschluss über die erforderliche Kraftstoffmenge für den jeweiligen Motor geben. Es gab auch die Wahl zwischen Einspritzdüsen mit hoher und niedriger Impedanz. Niederohmige Einspritzdüsen eignen sich für Motoren, bei denen ein sehr schnelles Öffnen der Einspritzdüsennadel erforderlich ist. Der typische Widerstand beträgt 4 Ohm. Der Nachteil dieser Injektoren ist der hohe Strom. Die dabei entstehende Hitzeentwicklung im MegaSquirt ist unerwünscht. Durch die Montage spezieller IGBTs auf einer Wärmeleitplatte am MegaSquirt-Gehäuse ist der Einsatz niederohmiger Injektoren möglich. Es wurde beschlossen, hochohmige Injektoren zu verwenden. Die Wärmeentwicklung ist geringer und diese IGBTs kommen nicht zum Einsatz.
Die Kanalgröße (Durchfluss) ist sehr wichtig, um die richtige Einspritzmenge und damit die Steuerung zu bestimmen. Wenn Sie zu große Einspritzdüsen wählen, ist die Einspritzzeit im Leerlauf so kurz, dass der Motor unruhig laufen kann. Die Einspritzmenge muss ausreichen, um den gesamten Kraftstoff in der verfügbaren Zeit einzuspritzen. Die Injektionsmenge wird als Injektionszeit in Millisekunden angegeben. Bei hoher Motordrehzahl wird von einer hohen Last ausgegangen. Dies ist bei einem MAP von 100 kPa der Fall. Der erforderliche Injektordurchfluss kann anhand der Motoreigenschaften berechnet werden. Der Injektorfluss gibt an, wie viele Milliliter Kraftstoff pro Minute eingespritzt werden.
Auswahl der passenden Injektoren:
Für das Projekt wurden Injektoren in drei verschiedenen Typen zur Verfügung gestellt. Untersuchungen ergaben, welcher Injektortyp für den Einsatz in diesem Projekt am besten geeignet war.
Jeder Injektortyp hat einen anderen Durchfluss; Die Ausbeute nach einer Minute Injektion variiert je nach Typ. Bevor die Injektoren getestet wurden, wurden sie im Ultraschallbad gereinigt. Bei dieser Reinigungsmethode wird der Injektor mittels Ultraschallschwingungen und einer speziellen Prüfflüssigkeit von innen und außen gereinigt, so dass etwaige alte Schmutzrückstände keinen Einfluss auf die Durchflussmessung oder das Einspritzbild haben. Während der Ultraschallreinigung wurden die Injektoren kontinuierlich geöffnet und geschlossen und das Injektionsmuster jedes Injektors untersucht; Das war ein wunderschöner Nebel. Beim Schließen waren keine Auffälligkeiten wie Tropfenbildung oder ein abweichender Strahl erkennbar. Nach der Ultraschallreinigung und -prüfung wurden die O-Ringe ausgetauscht, um eine gute Abdichtung bei der Montage im Ansaugkrümmer zu gewährleisten.
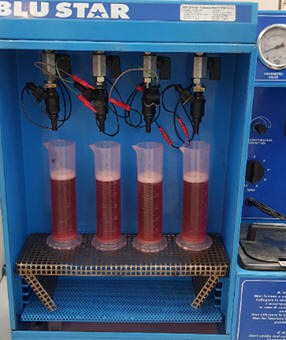
Mithilfe eines Testaufbaus (siehe Bild oben) können die Injektoren in mehrere Messbecher einspritzen, so dass nach einer gewissen Zeit die eingespritzte Kraftstoffmenge abgelesen werden kann. Durch die Ansteuerung der Einspritzdüsen auf einen Arbeitsdruck von 3 bar kann die eingespritzte Kraftstoffmenge gesteuert werden. Der Kraftstoffdruck in der Versorgungsleitung (dem Rail) muss 3 bar betragen und die Einspritznadel muss für 30 oder 60 Sekunden bei einem Arbeitszyklus von 100 % aktiviert werden. Nachdem die Injektoren 30 Sekunden lang aktiviert wurden, konnten folgende Daten eingegeben werden:
Typ 1: 120 ml
Typ 2: 200 ml
Typ 3: 250 ml
Es wird nur ein Injektortyp verwendet. Die Injektorgröße wird anhand der folgenden Formel ermittelt:

Die Größe der Einspritzdüsen wird auf der Grundlage der bei einer bestimmten Geschwindigkeit abgegebenen effektiven Leistung (Pe), des bremsspezifischen Kraftstoffverbrauchs (BSFC), der Anzahl der Einspritzdüsen (n Einspritzdüsen) und des maximalen Arbeitszyklus, mit dem die Einspritzdüsen gesteuert werden, bestimmt. Das Ganze wird mit 10.5 multipliziert, um von Pfund pro Stunde (lb/h) in ml/min umzurechnen.
Das Ergebnis der Berechnung gibt Aufschluss darüber, welcher Injektor für diese Motorkonfiguration geeignet ist. Eine Abweichung von weniger als 20 ml vom berechneten Wert stellt kein Problem dar. Dieser Unterschied wird durch eine Anpassung der Software im MegaSquirt ausgeglichen. Die folgende Tabelle gibt einen Überblick über die in den Formeln verwendeten Daten:
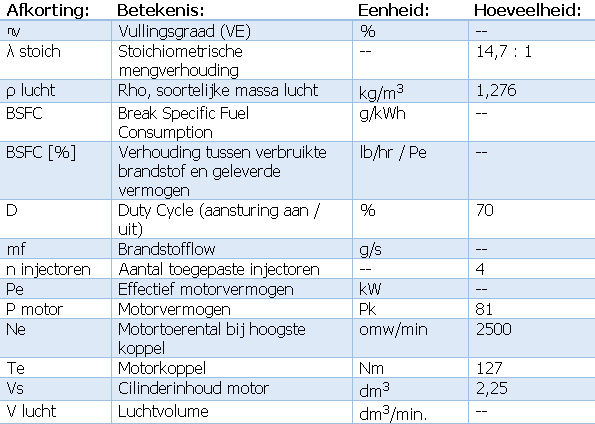
Der erste Schritt besteht darin, den bei der Drehmomentdrehzahl eingespritzten Kraftstoff zu bestimmen. Pro zwei Umdrehungen der Kurbelwelle wird eine bestimmte Menge Luft angesaugt. Der Füllgrad ist bei der Drehmomentdrehzahl am höchsten. Aufgrund der Motoreigenschaften (u.a. der Ventilüberschneidung) füllt sich der Motor bei dieser Drehzahl am besten und der Wirkungsgrad ist am höchsten. Es wird geschätzt, dass die Füllungsrate etwa 70 % betragen wird. Formel 4 berechnet das Luftvolumen, das sich zu diesem Zeitpunkt im Motor befindet.
In Formel 5 wird die eingespritzte Kraftstoffmenge anhand des vorhandenen Luftvolumens berechnet. Die bei der Drehmomentdrehzahl erreichte Motorleistung wird in Formel 6 berechnet. Das Verhältnis zwischen der eingespritzten Kraftstoffmenge und der Leistung gibt in den Formeln 7 und 8 den BSFC an.
Der tatsächliche BSFC wird in Formel 6 mit 3600 multipliziert, um ihn in kWh umzurechnen. Der BSFC eines Benzinmotors liegt oft zwischen 250 und 345 g/kWh. Je niedriger der Wert, desto effizienter ist der Motor. Formel 8 gibt die Beziehung zwischen dem Kraftstoffdurchfluss in Pfund/Stunde und der effektiven Motorleistung an. Dieser Prozentsatz ist in Formel 9 enthalten.



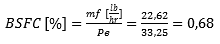

Die Antwort auf Formel 9 hat deutlich gemacht, dass die Injektoren mit einem Durchfluss von 200 ml/min für den Einsatz im Motor geeignet sind. Der Unterschied von 7 ml ist vernachlässigbar, da dieser in der Software beim Ausfüllen der VE-Tabelle ausgeglichen wird.
Einbau der Einspritzdüsen in das Ansaugrohr:
Das elektronisch gesteuerte Einspritzsystem ermöglicht den Verzicht auf den zum klassischen Setup gehörenden Vergaser. Der Vergaser wird daher durch ein Drosselklappengehäuse (für die Luftversorgung) und vier separate Kraftstoffeinspritzdüsen ersetzt. Der Ansaugkrümmer blieb erhalten und wurde modifiziert, um den Umbau auf das Motormanagementsystem zu ermöglichen. Die Kraftstoffeinspritzung erfolgt im Ansaugkrümmer. Man entschied sich dafür, die Einspritzdüsen so nah wie möglich am Einlassventil zu montieren. In den meisten Fällen entscheiden sich Automotorenhersteller dafür, das Einlassventil schräg im Ansaugkrümmer zu montieren. Der Kraftstoff wird gegen das Einlassventil gesprüht. Für das aktuelle Projekt wurde jedoch ein Aufbau gewählt, bei dem die Injektoren in einem Winkel von 45 Grad zu den Luftkanälen im Krümmer platziert sind.
Der Ansaugstutzen besteht aus Aluminiumguss. Es wurde beschlossen, Aluminiumbuchsen am Krümmer anzubringen. Eine manuelle Bearbeitung auf eine gute Größe war keine Option, da die Buchsen andere Abmessungen als eine Standardbohrergröße haben mussten. Dies bedeutete, dass die Auslagerung der Transporter an ein Unternehmen mit geeigneter Ausstattung vergeben werden musste. Die Buchsen könnten dann durch WIG-Schweißen am Verteiler befestigt werden. Die Entscheidung, die Injektoren aufrecht statt schräg zu montieren, wurde aus folgendem Grund getroffen:
- Der Aufbauablauf: Es ist einfacher, die Transporter in einer geraden, horizontalen Anordnung aufzustellen. Das Anschweißen der Transporter an den Krümmer ist einfacher, da es jetzt einfacher ist, rundherum zu schweißen, als wenn der Transporter schräg steht.
- Nachbearbeitung: Beim Schweißen werden die Buchsen etwas oval. Die Verformung entsteht durch die beim Schweißvorgang freigesetzte Wärme. Dem wurde dadurch Rechnung getragen, dass der Innendurchmesser der Buchsen kleiner ist als der Außendurchmesser der Einspritzdüsen. Das Nachbearbeiten (Reiben) ist weniger riskant: Wenn die Hülsen innen abgerundet sind, ist der Durchmesser optimal für die Injektoren und die Abdichtung durch die O-Ringe ist gewährleistet. Die Höhe der Transporter ist wichtig; Der Injektor darf nicht zu weit im Verteiler platziert werden. Das Ende des Injektors darf den Luftstrom nicht behindern. Aus den Informationen der Quelle: (Banish, Engine Management, advanced tuning, 2007) wurde beschlossen, die Einspritzdüsen so tief im Krümmer zu montieren, dass die Enden genau in den Löchern im Krümmer liegen; der Luftstrom wird nicht behindert.
- Kraftstoffeinspritzung: Da die Vermischung des Kraftstoffnebels mit der Luft vor dem Öffnen des Einlassventils optimal ist, spielt es keine große Rolle, ob der Injektor genau am Einlassventil oder kurz davor in das Ansaugrohr einspritzt.
Bei der Simultaneinspritzung erfolgt die Einspritzung bei jeder Kurbelwellenumdrehung (360°). Die vier Injektoren spritzen gleichzeitig ein. Das bedeutet, dass Kraftstoff auch dann in den Ansaugtrakt eingespritzt wird, wenn das Einlassventil nicht geöffnet ist. Einige Zeit später öffnet sich das Einlassventil und der Kraftstoff gelangt immer noch in den Zylinder.
Die Buchsen werden auf einer Drehmaschine speziell zugeschnitten. Der Innendurchmesser ist etwas kleiner als der Außendurchmesser des Injektors; Da es beim Schweißvorgang zu Verformungen kommt, muss bei der Nachbearbeitung durch Reiben die Möglichkeit bestehen, Material abzutragen. Das heißt, der Durchmesser vergrößert sich leicht, da Material abgeschliffen wird. Der Durchmesser sollte nicht zu groß sein, da sonst die Gefahr besteht, dass der Gummi-O-Ring am Injektor nicht mehr gut genug abdichten kann. Eine gute Abdichtung ist sehr wichtig; Luftlecks am Injektor vorbei führen zu einem geringeren Unterdruck im Ansaugkrümmer.
Der gemessene Unterdruck entspricht dann nicht mehr dem berechneten Unterdruck. Dies wirkt sich auf die Einspritzung aus, die anhand der VE-Tabelle ermittelt wird. Dabei spielt der Unterdruck eine große Rolle. Die Funktionen und Einstellungen der VE-Tabelle werden in einem nächsten Kapitel beschrieben.
An der Unterseite der Buchsen wurde eine abgeschrägte Kante gefeilt, sodass die Formen mit denen des Ansaugkrümmers übereinstimmen. Der Transporter muss dann möglichst aufrecht stehen. Das Bild unten zeigt den Ansaugkrümmer mit Kanister während des Montagevorgangs. Die Hülse ist einseitig verklebt, so dass deutlich erkennbar ist, wie sich die Schweißung auf das Material auswirkt. Es war unklar, ob das Aluminium des Verteilers zu viele Verunreinigungen enthielt, die das Schweißen erschweren würden. Das hat sich als in Ordnung herausgestellt. Um zu verhindern, dass sich die Buchsen beim Schweißen aus ihrer Position verschieben, wurden vorab Löcher in den Verteiler gebohrt und die Buchsen mit einer speziell angefertigten Vorrichtung in der richtigen Position gehalten. Auf diese Weise werden die vier Buchsen rundherum verschweißt. Eine abschließende Kontrolle ergab, dass die Verbindungen zwischen den Buchsen und dem Verteiler luftdicht waren.
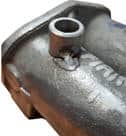
Die Verbindung zwischen den Injektoren wird normalerweise durch eine massive Injektorschiene gebildet. Dieses Rohr mit Anschlüssen, oft aus einer Aluminiumlegierung, wird von einem Hersteller nach Maß gefertigt. Der für das Projekt verwendete Land Rover-Motor verfügt über zwei Einspritzdüsen direkt nebeneinander, der Abstand zwischen den Einspritzdüsenpaaren ist jedoch recht groß. Die Abmessungen des Kraftstoffverteilers und der Raum zwischen den Luftkanälen des Ansaugkrümmers stimmten nicht überein. Daher musste die Schiene angepasst werden.
Das Verkürzen einiger Teile und das Verlängern anderer Teile durch Löten ist sehr schwierig; Die Verschmutzung durch alten Kraftstoff, der nur sehr schwer von der Innenseite der Schiene entfernt werden kann, kann zu einer verschlechterten Haftung führen. Da es sich um Kraftstoff handelt, wurde die sicherste Methode gewählt; Die Teile, an denen die Einspritzdüsen befestigt sind, sind durch einen hochwertigen Kraftstoffschlauch verbunden. An allen Enden sind gesäumte Kanten angebracht und stabile Schlauchklemmen verhindern, dass die Schläuche über die gesäumten Kanten rutschen.
Das Bild unten zeigt den Ansaugkrümmer zum Zeitpunkt der Bearbeitung. Die Versorgungsleitung (mit der Nummer 1 gekennzeichnet) wird an den Ausgang der Kraftstoffpumpe angeschlossen. Der Kraftstoff wird mit einem Druck von 3 bar am Eingang der vier Einspritzdüsen zugeführt. Der Druckregler (3) regelt den Druck in Abhängigkeit vom Saugrohrdruck, da die Druckdifferenz zwischen Kraftstoffdruck und Unterdruck im Saugrohr 3 bar betragen muss. Über die Rücklaufleitung (2) fließt der Kraftstoff zurück zum Tank. Es findet eine kontinuierliche Kraftstoffzirkulation statt. Die Einspritzung erfolgt nur, wenn die Einspritzdüsen vom MegaSquirt-Steuergerät gesteuert werden.
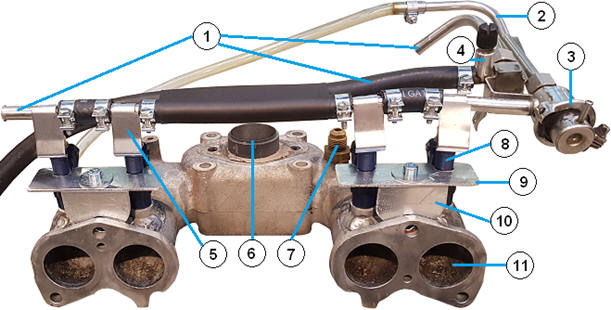
- Versorgungsleitung
- Rückleitung
- Druckregler
- Druckkontrolle
- Hitzeschild
- Gasventilanschluss
- Unterdruckanschluss
- Einspritzzylinder 1
- Einspritzdüsenhalterung A
- Einspritzdüsenhalterung B
- Ansaugkanal Zylinder 1
Bei bestehenden Pkw wird die Einspritzschiene mittels Schellen oder Ösen am Ansaugkrümmer befestigt. Die Injektorschiene klemmt die Injektoren im Verteiler fest. Da bei diesem Projekt ein flexibler Kraftstoffschlauch als Einspritzschiene gewählt wurde, ist das oben Gesagte nicht möglich. Daher wurde beschlossen, die Einspritzdüsen mit einer speziell angefertigten Halterung im Ansaugrohr zu befestigen. Die Halterungen bestehen aus zwei Teilen: Oberteil (Halterung A) und Unterteil (Halterung B).
Halterung A enthält zwei Kerben, die über die Einspritzdüsen geschoben werden können. Dadurch können die Injektoren über die flachen Seiten in den Krümmer gedrückt werden. Beide Halterungen A verfügen über Langlöcher, sodass der Abstand zwischen den Injektoren und den Langlöchern eingestellt werden kann. Die Halterungen A und B werden miteinander verschraubt: Halterung B wird an demselben Bolzen befestigt, mit dem der Krümmer am Motor befestigt ist. Durch ein Langloch lässt sich die Halterung in vertikaler Richtung verstellen. Je weiter die Halterung nach unten bewegt wird, desto fester wird der Injektor geklemmt.
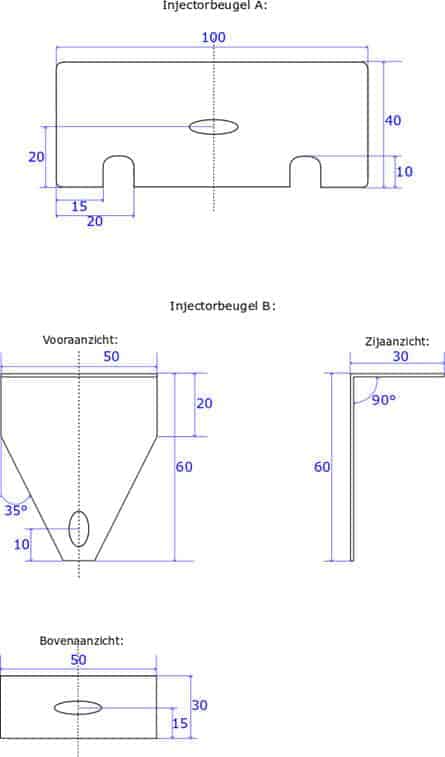
Zündung:
Die herkömmliche Zündung wurde durch ein elektronisch gesteuertes Zündsystem mit einer Zündspule ersetzt, die vom MegaSquirt gesteuert wird. Damit der Motor mit den Originaltechniken voll funktionsfähig ist, muss zunächst das konventionelle System mit Kontaktstellen angeschlossen werden. Erst nach einigen Betriebsstunden kann festgestellt werden, dass der Motor ordnungsgemäß funktioniert, und dann mit dem Einbau und der Einstellung unter anderem der elektronisch gesteuerten Zündung begonnen werden.
Vorbereiten mit der konventionellen Zündung:
Der Land Rover-Motor war ursprünglich mit einem Zündsystem mit Kontaktpunkten ausgestattet, das heute auch als konventionelles Zündsystem bezeichnet wird. Das Bild zeigt diese Art von Zündsystem.
Bei geschlossenen Kontaktstellen beginnt der Aufbau des Primärstroms. Der Strom wird durch den Widerstand der Primärwicklung auf 3 bis 4 Ampere begrenzt. Wenn ein Strom durch die Primärspule der Zündspule fließt, wird ein Magnetfeld aufgebaut. Sowohl die Primärspule (3) als auch die Sekundärspule (4) befinden sich in diesem Magnetfeld. Wenn der Strom durch die Kontaktstellen (10) durch den Unterbrechernocken (9) auf der Verteilerwelle unterbrochen wird, wird in beiden Spulen eine Spannung induziert. In der Primärspule werden ca. 250 Volt erzeugt. Durch den Wicklungsunterschied entsteht in der Sekundärspule eine Induktionsspannung von 10 bis 15 kV. Der Zündkerzenfunke entsteht beim Öffnen der Weichen.
Die Induktionsspannung kann begrenzt werden, indem der Primärstrom nach dem Öffnen der Kontaktstellen noch eine Weile fließen kann. Dies wird durch einen Kondensator erreicht, der über die Kontaktpunkte parallel geschaltet wird. Der Kondensator ist ein zeitbestimmendes Element, das abhängig von der Kapazität tatsächlich die Höhe der Induktionsspannung anpasst. Auch das Verbrennen der Kontaktstellen wird verhindert.
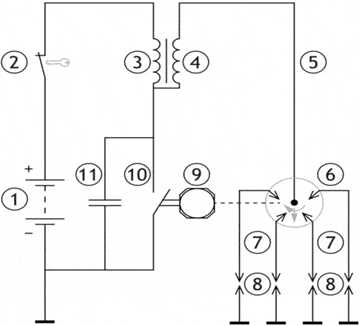
Zündspule für das Motormanagementsystem:
Das Motormanagementsystem steuert die Zündspule. Die klassische Zündspule mit Verteiler verbleibt als Testaufbau am Motor, ist aber nicht mehr Teil der Funktionsweise des Verbrennungsmotors. Die Wahl fiel auf ein verteilerloses Zündsystem (DIS-Zündspule), frei übersetzt: „verteilerloses Zündsystem“. Diese Art von Zündsystem verwendet keinen Verteiler. Eine weitere Möglichkeit bestand darin, eine Coil-on-Plug-Zündspule (COP) zu wählen. An jede Zündkerze ist eine eigene Zündspule angeschlossen. Eine COP-Zündspule wird auch Stiftzündspule genannt. Der Nachteil einer COP-Zündspule besteht darin, dass die Wärmeableitung schlechter ist als bei einer DIS-Zündspule. Bei Verwendung von COP-Zündspulen ist zusätzlich ein Signal eines Nockenwellensensors erforderlich, das beim aktuellen Motor nicht vorhanden ist.
Der fehlende Zahn in der Kurbelwellenriemenscheibe dient als Bezugspunkt für die Bestimmung des Zündzeitpunkts. Mit der DIS-Zündspule werden zu einem Zündzeitpunkt zwei Zündkerzen gleichzeitig aktiviert. Bei der DIS-Zündspule handelt es sich eigentlich um eine Einheit, in der zwei Zündspulen montiert sind. Wenn sich die Kolben der Zylinder 1 und 4 nach oben bewegen, ist einer mit dem Verdichtungstakt und der andere mit dem Ausstoßtakt beschäftigt. Dennoch erzeugen beide Zündkerzen einen Funken. Der Funke, der von dem Zylinder erzeugt wird, der sich im Kompressionstakt befindet, führt zu einer zündenden Mischung. Der andere Funke, der sogenannte „wasted spark“, entsteht, wenn das Abgas den Brennraum verlässt. Der verlorene Funke ist ein Funke, der entsteht, wenn kein Gemisch gezündet wird. Die Zündenergie ist gering; Trotz des Funkens gibt es kaum Energieverluste. Es ist auch nicht schädlich.
Die Abbildung zeigt das Funktionsschema eines Vierzylinder-Ottomotors mit DIS-Zündspule. Dieses Arbeitsdiagramm zeigt zwei Zündmarken pro Zündzeitpunkt; Einer von ihnen erzeugt den Funken, um das Gemisch zu entzünden, der andere ist der verschwendete Funke. Mit nur zwei Impulsen kann eine DIS-Zündspule vom MegaSquirt angesteuert werden.
Wenn der Kompressionstakt in Zylinder 1 und der Auslasstakt in Zylinder 4 stattfindet, steuert der MegaSquirt die Primärspule A über Pin 36 am DB37 (siehe Abbildung unten). Diese Steuerung erfolgt basierend auf dem Kurbelwellen-Referenzpunkt (zwischen 90 und 120 Grad vor OT). Der MegaSquirt steuert die Primärspule B, die für die Funkenbildung der Zylinder 2 und 3 verantwortlich ist, und wird um 180 Grad nach Spule A eingeschaltet. Es gibt keinen Referenzpunkt für Spule B, aber der Zündzeitpunkt kann einfach durch Zählen der Zähne am 36-1-Impulsrad bestimmt werden.
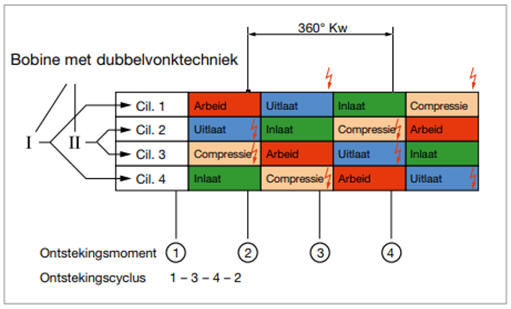
Zwischen Spule A der Zündspule und Pin 7 des Prozessors wird ein Widerstand von 330 Ohm angezeigt. Dieser Widerstand begrenzt den Strom und die Induktionsspannung des Antriebsimpulses. Da dieser Widerstand nicht standardmäßig auf der MegaSquirt-Platine vorhanden ist, muss er nachgerüstet werden. Links von der vertikalen gestrichelten Linie im Bild unten ist die interne Schaltung des MegaSquirt dargestellt. Die abgebildeten Bauteile (die beiden 330 Ohm Widerstände und die LEDs) mussten anschließend auf die Leiterplatte gelötet werden.
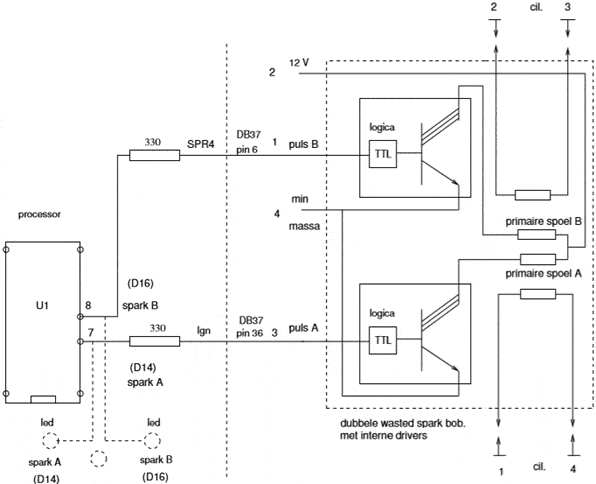
Stromaufbau in der Primärspule:
Es ist wichtig, Einblick in den Stromaufbau in der Primärspule zu gewinnen. Damit lässt sich nicht nur die Stromstärke, sondern auch die Ladezeit der Zündspule ermitteln. Die Ladezeit hängt von einer Reihe von Faktoren ab, die der MegaSquirt berücksichtigen muss.
Der Selbstinduktionskoeffizient (L-Wert) der ausgewählten Zündspule beträgt 3,7 mH. Zusammen mit dem ohmschen Widerstand R werden der maximale Primärstrom und die Anstiegszeit der Kurve ermittelt. Ein kleiner L-Wert und Widerstand sorgen dafür, dass der Strom nach dem Einschalten schnell ansteigt. Aus den bekannten Daten der Zündspule kann berechnet werden, wie sich der Primärstrom aufbaut.
Die folgende Formel zeigt die allgemeine Lösung der Differentialgleichung 1. Ordnung, die die Ströme, Lade- und Entladezeiten berechnet, um das Schaltphänomen als Kurve darzustellen.
Die Gleichung lautet:

wobei die Zeitkonstante (Tau) wie folgt berechnet wird:

Der maximale Strom würde nach dem Ohmschen Gesetz 28 Ampere betragen:
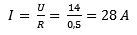
In der Realität wird diese Stromstärke nicht erreicht.
Die Spule wird früher ausgeschaltet. Der Grund wird später erläutert. Die Eingabe dieser Informationen in die allgemeine Formel ergibt:
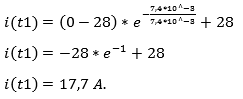
Die Abbildung zeigt die Ladekurve der Primärspule. Vom Zeitpunkt T0 bis 1 Tau ist die Spule auf 63,2 % geladen. Dies ist ein fester Prozentsatz für die Ladezeit einer Spule. Das Ergebnis der Formel 13 zeigt, dass die Spule bei 1 Tau mit 17,7 Ampere belastet wird. Bei t = 5 Tau ist der Endwert praktisch erreicht.
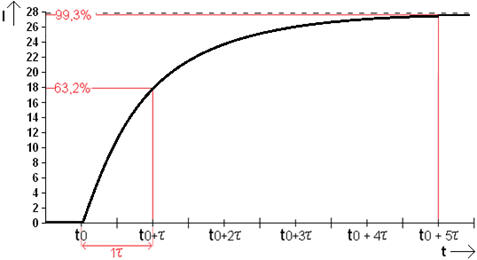
Gemäß den Spezifikationen der Zündspule beträgt der Primärstrom der Zündspule nach dem Laden 7,5 A. Der Strom steigt nicht an. Die Zeit, die benötigt wird, um 7,5 A zu erreichen, wird Verweilzeit genannt. Die Verweildauer hängt von der Batteriespannung ab, die in diesem Fall 14 Volt beträgt. Wird der Ladevorgang nicht angepasst, beträgt der Strom durch die Spule gemäß Formel 12 maximal 28 Ampere.
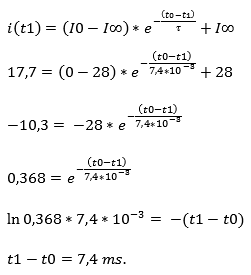
Die Spule nach Formel 14 wird bei t = 7,4 ms auf 17,7 A aufgeladen. Die tatsächliche Ladezeit ist kürzer, da die Spule mit maximal 7,5 A aufgeladen wird. Die benötigte Zeit kann durch Eingabe der bekannten Daten in Formel 15 berechnet werden.
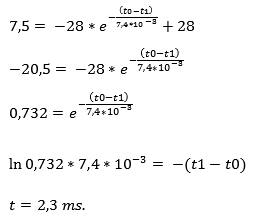
Der Primärstromaufbau wird bei 7,5 A gestoppt. Dadurch wird verhindert, dass die Zündspule übermäßig und unnötig warm wird. Das Wichtigste ist, dass die Spule in möglichst kurzer Zeit optimal aufgeladen wird. Die Abbildung zeigt die Ladekurve bis t = 2,3 ms.
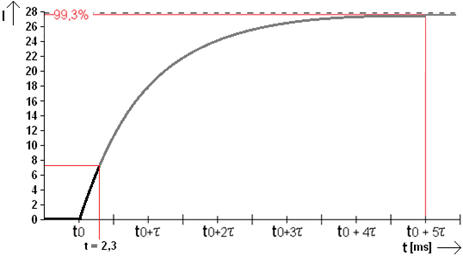
Wenn die Batteriespannung sinkt, beispielsweise beim Starten des Motors, wirkt sich dies auf die Verweildauer aus. Es dauert dann länger als 2,3 ms, bis 7,5 A erreicht sind. Die neue Ladezeit wird nach der mittlerweile bekannten Formel ermittelt. Der maximale Strom wird anhand der Batteriespannung ermittelt:
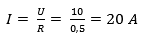
Die Ladezeit bis 7,5 A bei maximal 20 A berechnet sich nach Formel 17:
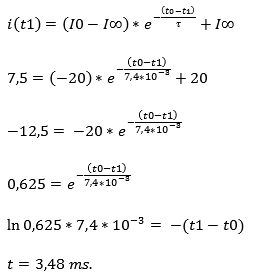
In der Abbildung ist die Ladezeit bei 14 Volt mit der schwarzen Linie und die Ladezeit bei 10 Volt mit der grünen Linie dargestellt. Die Linien fallen gleichzeitig auf 0; das ist der Zündzeitpunkt. Da eine niedrigere Batteriespannung mehr Zeit zum Laden der Primärspule benötigt, muss der MegaSquirt den Primärstrom früher einschalten.
Die schwarzen Linien (steigend und fallend) geben die Verweildauer bei einer Batteriespannung von 14 Volt an. Die grüne Linie zeigt die Vorladezeit bei niedrigerer Spannung an: Dies ergibt Δt. Die tatsächliche Ladezeit beträgt in diesem Fall Δt + 100 %.
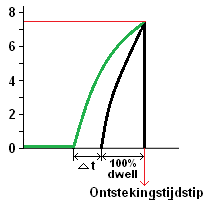
Dies wird später in diesem Abschnitt anhand eines Beispiels und Abbildung 36 verdeutlicht. Die Ladezeit verlängert sich und der Zündzeitpunkt bleibt gleich. Geschieht dies nicht oder nicht ausreichend, hat dies Konsequenzen für die bei der Zündung freigesetzte Energie. In diesem Fall wird der Primärstrom zu früh abgeschaltet, so dass der Strom von 7,5 A nicht erreicht wird. Die Verlängerung der Ladezeit der Primärspule (Verweilzeit) ist formelmäßig eine Funktion der Batteriespannung. Die Berechnung der Verweilzeit bei verschiedenen Spannungen ergibt einen unterschiedlichen maximalen Strom in der Spule.
Unter der Annahme, dass die Batteriespannung beim Starten auf 6 Volt sinken und beim Laden auf 14,7 Volt ansteigen kann, lässt sich durch die Berechnung mehrerer Zwischenwerte eine Kurve skizzieren. Das Bild unten zeigt die Verweilzeitkorrektur für die verwendete DIS-Zündspule. Für jeden Anstieg um 2 Volt wird ein (roter) Punkt in die Grafik eingefügt. Da im TunerStudio-Programm eine zuvor eingegebene Verweilzeit von 2,3 ms bei einer Spannung von 14 Volt eingegeben wurde, wird aus dieser Spannung ein Korrekturfaktor gebildet. Eine Spannung von 14 Volt ist also 100 % (keine Korrektur).
Nun wurde klargestellt, dass sich die Ladezeit bei einer Batteriespannung von 315 Volt um bis zu 6 % verlängert.
Unter ungünstigen Bedingungen kann die Batteriespannung um bis zu 6 Volt absinken. Dies bedeutet eine Abschwächung des Zündfunkens. Durch die Verlängerung der Verweilzeit (der Zeit, in der der Primärstrom fließt) wird dies ausgeglichen, so dass auch bei dieser niedrigen Spannung ausreichend Zündenergie erhalten wird. Dies bedeutet, dass sich Δt aus Abbildung 36 verdreifacht (2,3 ms * 315 % = 7,26 ms) im Vergleich zur schwarz dargestellten Verweilzeit von 100 % (2,3 ms).
Die im Bild oben rot markierten Koeffizienten können direkt in das TunerStudio-Programm kopiert werden.
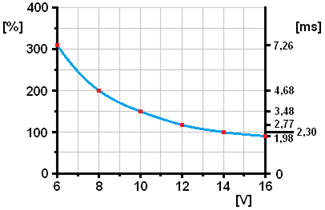
Einige Zeit nach der Entladung der Primärspule beginnt der Aufbau für die nächste Zündung. Je höher die Motordrehzahl, desto schneller wird die Spule wieder aufgeladen. Abbildung 37 zeigt zwei Kurven, bei denen der Primärstrom auf 8,85 A ansteigt. Der Zündzeitpunkt liegt an dem Punkt, an dem die Linie auf 0 A abfällt.
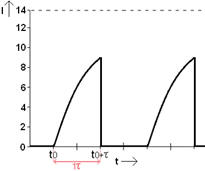
Bestimmung des Zündzeitpunkts:
Das Zündsignal wird aus dem Kurbelwellen-Referenzpunkt ermittelt.
Im Zahnkranz der Kurbelwellenriemenscheibe wurde 36 Zahn der 1 Zähne bei 100 Grad vor dem oberen Totpunkt des Kolbens von Zylinder 1 gefräst. Zwischen 100 und 0 Grad, also während des Kompressionshubs, arbeitet der Mikroprozessor von Der MegaSquirt kann den Zündzeitpunkt bestimmen. . Dabei wird der Vorschuss berücksichtigt.
Das Bild zeigt das Zweikanal-Oszilloskopbild, wobei das obere Bild den Kurbelwellen-Referenzpunkt und das untere Bild das Steuersignal vom MegaSquirt zur DIS-Zündspule zeigt. Das Steuersignal hat eine Spannung von 5 Volt (eine logische 1) und dauert etwa 1,5 ms.
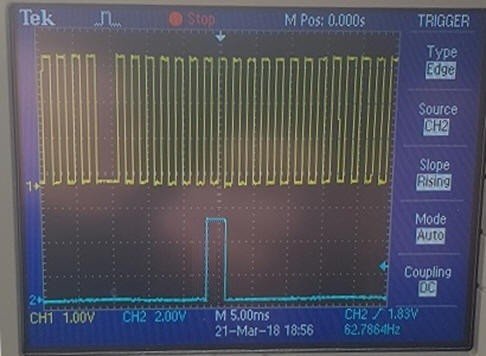
Zündzeitpunkt:
Klopfsensoren werden in diesem Projekt nicht verwendet. Es ist möglich, Informationen von Klopfsensoren zu verarbeiten, aber der bloße Einbau eines Klopfsensors reicht nicht aus. Die Verarbeitung der Signale ist komplex. Das Klopfsignal muss zunächst in ein Ja/Nein-Signal oder in ein analoges Signal umgewandelt werden, das die Stärke der Detonation anzeigt.
Die Umwandlung der Motorschwingungen in ein Klopfsignal erfolgt über eine Schnittstellenschaltung. Diese Schaltung ist im MegaSquirt II nicht vorhanden. Deshalb wurde beschlossen, die Volllast- und Teillastvoreilung sicher einzustellen, damit der Motor nicht in den Klopfbereich geraten kann. Die einzustellende Volllast-Vorlaufkurve muss innerhalb der Klopfgrenzen ermittelt werden. Die Zentrifugal- und Vakuumverstellungsdaten der konventionellen Zündung werden anhand der Werksdaten aus dem Motorhandbuch ermittelt. Die Punkte können in einem Diagramm dargestellt werden (Beispiel im Bild unten).
Die rosa Linie zeigt den ursprünglichen, mechanischen Vorschub an. Aufgrund der mechanischen Konstruktion der Fliehgewichte ist dies teilweise linear. Die schwarze Linie zeigt die Kartensteuerung im MegaSquirt; Diese Linie folgt einer Kurve. Es ist wichtig, sich von den Klopfbereichen bei Teillast und Volllast fernzuhalten; Daher ist die Kennfeldsteuerung bei Teillast begrenzt (rote Linie) und der Vorschub bei Volllast erhöht sich nicht weiter als bei mechanischem Vorschub (rote Linie). Die tatsächliche Kartenanordnung folgt der blauen Linie.
Zunächst musste die Volllastverstellungskurve in die Zündverstellungstabelle eingegeben werden. Bei höheren Geschwindigkeiten und geringeren Lasten ist ein größerer Vorschub erforderlich. Bei Teillast addiert sich die Vorverstellung zur Volllastvorverlegung. Die ausgefüllte Zündverstellungstabelle und die Voreinstellungen bei kaltem Motor finden Sie auf Seite 7.
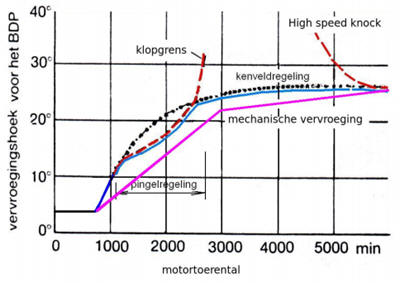
Drosselklappengehäuse:
Die Luft-/Kraftstoffzufuhr wurde im Originalzustand über den Vergaser gesteuert. Für das Motormanagementsystem wird der Vergaser durch ein Drosselklappengehäuse und vier Einspritzdüsen ersetzt, die im Ansaugkrümmer montiert sind. Dies ermöglicht eine präzisere und kontrollierte Einspritzung als beim Vergaser, bei dem ein Luft-Kraftstoff-Gemisch zentral im Verteiler gebildet und in vier Kanäle aufgeteilt wird. Der Gashebel wird über einen Bowdenzug geöffnet, der manuell über die Instrumententafel bedient wird.
Schließlich unterstützt der MegaSquirt II kein elektronisch betätigtes Drosselklappengehäuse. Aus diesem Grund ist die Bowdenzugsteuerung die einzige Möglichkeit.
Die Drosselklappenstellung wird mittels einer Spannung an den MegaSquirt übermittelt. Die Höhe der Spannung hängt vom Öffnungswinkel der Drosselklappe ab. Der Drosselklappensensor ist ein Potentiometer mit einer Versorgungsspannung von 5 Volt (siehe Bild). Anschluss 3 und ein Masseanschluss 1 sind erforderlich. Der Läufer (Pin 2) nimmt über den Widerstand eine Position ein, die von der Drosselklappenstellung abhängt. Der Läufer ist daher mit der Drosselklappe verbunden. Wenn der Läufer eine kleine Distanz über den Widerstand überwinden muss (der Läufer zeigt nach links), ist der Widerstand gering. Im Bild ist der Läufer auf der rechten Seite (Erdseite) positioniert, was bedeutet, dass ein hoher Widerstand und daher eine niedrige Signalspannung vorhanden sind.
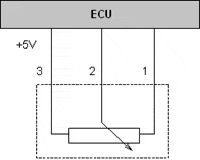
Bei Verwendung des Drosselklappengehäuses liegt am Läufer bei geschlossener Drosselklappe eine Spannung von 600 mV und bei vollständig geöffnetem Ventil eine Spannung von 3,9 V an. Das Steuergerät empfängt die Spannung und berechnet daraus den Öffnungswinkel der Drosselklappe. Eine schnelle Vergrößerung des Öffnungswinkels bedeutet, dass eine Beschleunigung stattfindet; Das Steuergerät reagiert darauf mit einer kurzzeitigen Anreicherung. Dies wird als Beschleunigungsanreicherung bezeichnet. Der Drosselklappenstellungssensor wird nicht zur Bestimmung der Anreicherung des Gemisches bei verschiedenen Betriebsbedingungen verwendet; Zu diesem Zweck wird der MAP-Sensor verwendet.
Testaufbau des Schrittmotors mit Simulator:
Nachdem der MegaSquirt hardwaremäßig angepasst wurde, konnte mit der Breakout-Box überprüft werden, ob die Steuerung des Schrittmotors empfangen wurde. Das Aufleuchten von zweifarbigen LEDs zeigt an, dass die Steuerung erfolgt. Die Schritte, in denen der Schrittmotor gesteuert wird, können anhand der Farbveränderung verfolgt werden. Die Farben wechseln zwischen Rot und Gelb. Schrittmotordaten können im Menü „Leerlaufsteuerung“ des TunerStudio-Programms eingegeben werden. Neben dem Typ (4-Draht) kann auch die Anzahl der Stufen eingestellt werden. Dazu gehört auch die Ausgangsposition, in der sich der Schrittmotor beim Starten des Motors befinden muss. Darüber hinaus kann die Zeit eingestellt werden, wie lange es dauert, einen Schritt anzupassen.
Die Anzahl der Schritte hängt unter anderem von der Kühlmitteltemperatur ab; Eine niedrigere Temperatur erfordert eine größere Öffnung des Schrittmotors. Die Schritte relativ zur Temperatur können in einem Diagramm eingestellt werden. Mit dem Simulator kann überprüft werden, ob der Schrittmotor tatsächlich ordnungsgemäß angesteuert wird. Da die Überprüfung zuerst am Simulator und nicht am Motor erfolgt, können Probleme beim Starten oder Laufen des Motors aufgrund eines möglichen Hardware- oder Softwareproblems verhindert werden. Da vor allem die Kühlmitteltemperatur und die Motordrehzahl den Öffnungswinkel des Schrittmotors beeinflussen, können Sie durch Drehen dieser Potentiometer überprüfen, ob die Ansteuerung korrekt ist. Das Messgerät auf dem Dashboard in TunerStudio zeigt die Anpassung in der Anzahl der angepassten Schritte an.
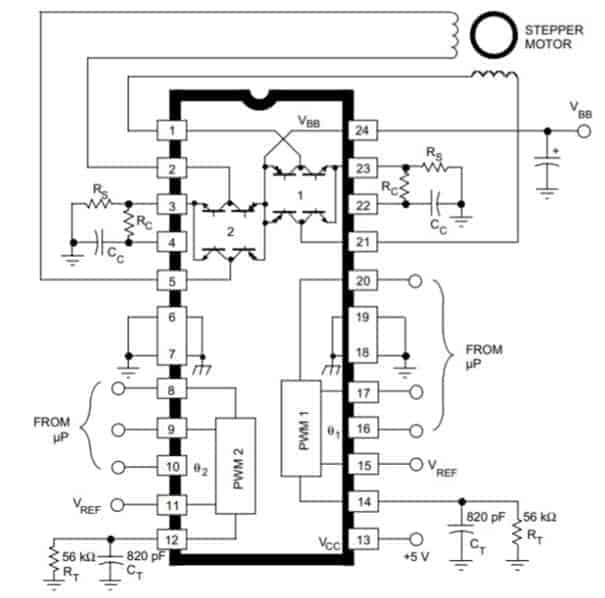
Schrittmotoreinstellungen:
Die Abbildung zeigt den Einstellungsbildschirm für den Schrittmotor, der für die Leerlaufdrehzahl (Leerlaufregelung) verwendet wird.
Die Schritte, in denen der Motor verstellt wird, werden vorab mit einem Arduino festgelegt. Außerdem muss die Anzahl der Schritte eingegeben werden, um die Grundposition anzufahren (Referenzschritte). Der Schrittmotor ist in der Aufwärmphase aktiv (Algorithmus) und bestromt die Spulen im Stillstand (Haltestrom zwischen den Schritten).
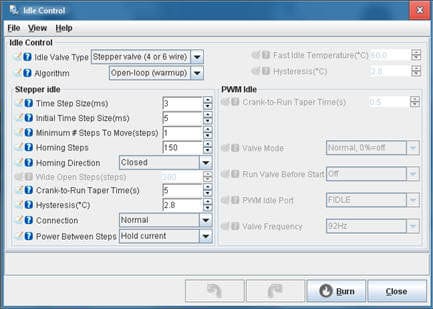
Die Position des Schrittmotors hängt von der Kühlmitteltemperatur ab. Beim Starten eines kalten Motors sollte das Ventil etwas weiter geöffnet sein als beim Starten eines warmen Motors. Das Bild unten zeigt den Einstellungsbildschirm zum Einstellen der Schritte (Steps) in Bezug auf die Kühlmitteltemperatur (Coolant). Bei kaltem Motor ist der Schrittmotor im Leerlauf vollständig geöffnet. Während der Aufwärmphase schließt der Schrittmotor leicht.
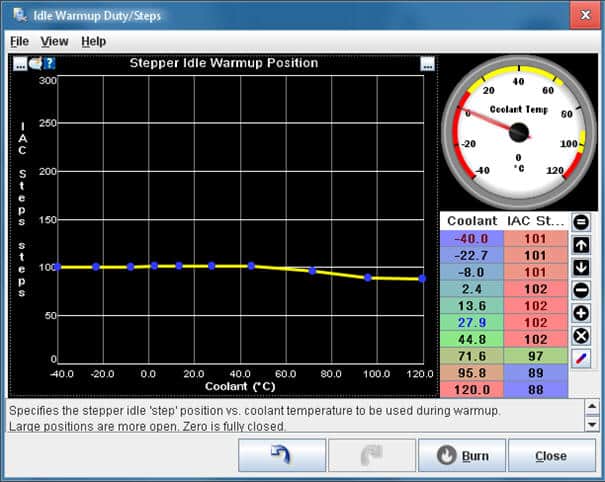
Es ist auch möglich, die Position des Schrittmotors basierend auf der Kühlmitteltemperatur beim Starten des Motors anzupassen. Dies wird als „Leerlaufstartbetrieb/-schritte“ bezeichnet. Das Bild unten zeigt den Einstellungsbildschirm.
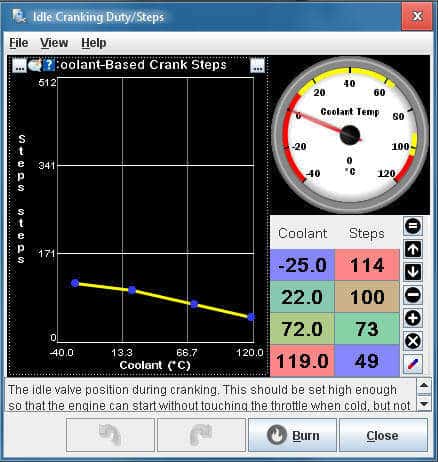
Kraftstoffpumpenkreis:
Der MegaSquirt sorgt dafür, dass die Kraftstoffpumpe ein- und ausgeschaltet wird. Der Transistor Q19 in der Abbildung unten schützt den Transistor Q2 vor übermäßigem Strom. Wenn der Strom zu hoch ist, kann der Transistor durchbrennen. Wenn der Strom durch den Kollektor-Emitter-Bereich von Q2 und R40 ansteigt, wird die Sättigungsspannung an der Basis von Q19 erreicht. Der Transistor Q19 schaltet ein, wodurch die Basis-Emitter-Spannung an Q2 abnimmt.
Die Verbindung FP-1 PTA0 wird intern vom MegaSquirt gesteuert. Zur Steuerung der Transistorschaltung ist ein Eingangssignal vom Kurbelwellen-Positionssensor (Hall-Sensor oder Induktivsensor) erforderlich. Bei Signalverlust, zum Beispiel bei ungewolltem Abwürgen des Motors, wird die Stromversorgung der Kraftstoffpumpe sofort unterbrochen.
Der Ausgang der Transistorschaltung (FP1 OUT) ist mit dem Kraftstoffpumpenrelais verbunden. Pin 85 des Relais ist der Ausgang des Steuerstroms. Bei angezogenem Relais wird der Hauptstromteil (Pin 30 und 87) geschaltet, so dass die Kraftstoffpumpe eine Versorgungsspannung zum Betrieb erhält.
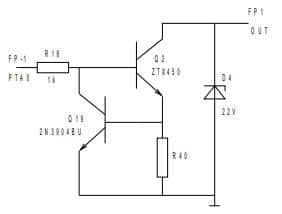
Zum Einsatz kommt eine elektronische Kraftstoffpumpe mit einem Betriebsdruck von 3 bar. Der Kraftstoff wird durch den Kraftstofffilter zum Kraftstoffverteiler geleitet, wo der Druck am Eingang der Einspritzdüsen anliegt. Der Injektor spritzt eine vorberechnete Kraftstoffmenge in den Ansaugkrümmer, wenn ein Signal vom MegaSquirt kommt. Die Steuerung des MegaSquirt bestimmt nicht nur die eingespritzte Kraftstoffmenge, sondern auch den Kraftstoffdruck im Rail.
Bei einem höheren Raildruck wird bei gleicher Ansteuerung eine größere Kraftstoffmenge eingespritzt. Der Raildruck muss daher anhand des Unterdrucks im Saugrohr angepasst werden. Die Druckdifferenz (∆P) muss jederzeit 3 bar betragen. Die Abbildung zeigt das Schema des Kraftstoffsystems. Die rosa, gelben, orangefarbenen und schwarzen Linien zeigen die elektrischen Verbindungen. Die rote Linie zeigt den Kraftstoffvorlauf und die blaue Linie den Kraftstoffrücklauf.
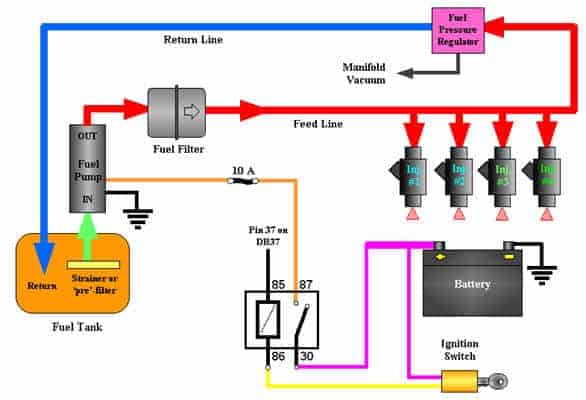
Abschluss der mechanischen Arbeiten:
Die nächsten drei Fotos zeigen den Motor in der letzten Phase der mechanischen Modifikationen.
Foto 1:
Dies ist die Seite, auf der die meisten Anwendungsteile sichtbar sind. Hier befinden sich auch das Dashboard für die Steuerung und das MegaSquirt-Steuergerät. Unterhalb des Fotos befindet sich eine Legende mit der Beschreibung der Nummern der Teile. Durch Anklicken können Sie die Fotos in größerer Größe öffnen.
- Drosselklappe;
- Kraftstoffleitung für die Einspritzdüsen;
- Verbindungsrohr für Drosselklappe am Saugrohr;
- Kraftstoffdruckmesser;
- Ansaug- und Abgaskrümmer;
- Armaturenbrett mit Kühlgebläseschalter, Lichtern für Lichtmaschine und Öldruck, Zündschalter und Masseschalter;
- Unterdruckschlauch für MAP-Sensor;
- Lambdasonde;
- Kraftstoffschläuche (Vor- und Rücklauf) zusammen in einer Schrumpfbox;
- Kraftstoffpumpen-/Tankeinheit;
- Kraftstoffpumpenrelais;
- MegaSquirt;
- Abgasschalldämpfer.
Foto 2:
Dieses Foto zeigt die andere Seite des Motors. Hier sieht man den Vergaser (15) und die konventionelle Zündung (17). Der Zweck dieser klassischen Zündung besteht darin, die Zündkerzen im Prüfaufbau (14) zum Funken zu bringen. Für den Motor hat das natürlich keine Funktion, aber es gibt Einblick in die Funktionsweise der Zündung, wie sie bei Oldtimern funktionierte.
Nummer 20 bezeichnet den Getriebebremsmechanismus. Über einen Bowdenzug kann die Stange der Bremstrommel gespannt werden, sodass die Abtriebswelle des Getriebes gebremst wird. Die Getriebebremse wird betätigt, um den Motor beim Einlegen eines Gangs kurzzeitig zu belasten.
Foto 3:
Hier ist die Draufsicht auf den Motor mit dem Prüfaufbau für die Zündung und das Kraftstoffverteilerrohr deutlich zu erkennen.
Die mechanischen Anpassungen sind abgeschlossen. Der Motor kann noch nicht gestartet werden, da zunächst einige Daten in den MegaSquirt eingegeben werden müssen.
Weiter: MegaSquirt II-ECU-Anpassung.