Themen:
- Firsthöhe messen
- Hauptlagerzapfen messen
- Messen Sie die Krümmung der Nockenwelle
- Axiales Lagerspiel messen
- Nockenwellenradhub messen
Firsthöhe messen:
Die Nocken der Nockenwelle können aufgrund von Alter oder mangelnder Schmierung verschleißen. Die Firsthöhe nimmt ab. Zu den Beschwerden, die bei verschlissenen Laschen auftreten können, gehören:
- Die Kraftstoffanpassungen ergeben einen negativen Prozentsatz: Aufgrund von Luftmangel wird die Einspritzmenge korrigiert (reduziert);
- Reduzierte Leistung: Aufgrund von Luftmangel kann das maximale Drehmoment nicht mehr erreicht werden. Wenn alle Nocken gleichermaßen verschlissen sind, kann der Motor ruhig im Leerlauf laufen;
- Unregelmäßiger Motorlauf: Dies gilt insbesondere dann, wenn nur eine oder wenige Nocken Verschleiß aufweisen und die anderen noch in Ordnung sind.
Mit dem Messschieber können wir die Firsthöhe bestimmen. Bei Bedarf kann für eine höhere Genauigkeit anstelle eines Messschiebers auch eine Messschraube verwendet werden. Zur Bestimmung der Firsthöhe führen wir zwei Messungen an einem First durch, siehe Bild.
- A = Durchmesser des Grundkreises;
- B = gesamte Firsthöhe;
- C = tatsächliche Firsthöhe / Lichthöhe.
Die Nockenhöhe (C) der Nockenwelle ist der Unterschied zwischen Größe A und B.
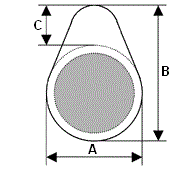
Die Nockenhöhen der Einlass- und Auslassnockenwelle sind unterschiedlich. Die Nockenhöhen einer Nockenwelle dürfen nicht voneinander abweichen. Wir müssen uns mit Toleranzen auseinandersetzen. Erst wenn der Messwert außerhalb der Toleranzen liegt, wird die Nockenwelle aussortiert.
Beispiel:
Die Nockenwellen eines Ottomotors werden vermessen. Laut Werksangaben müssen die Mindestfirsthöhen betragen:
- Einlassnockenwelle: 45,82 – 45,85 mm;
- Auslassnockenwelle: 45,50 – 45,53 mm.
Wir führen acht Messungen durch und vervollständigen die folgende Tabelle. In der Tabelle sehen wir, dass die Messwerte fast alle über den Minimalwerten liegen. Lediglich am Nocken 4 der Einlassnockenwelle sehen wir eine Abweichung: Dieser Nocken liegt 1,03 mm tiefer als der Minimalwert. Aus diesem Grund wird die Nockenwelle aussortiert und muss ersetzt werden.

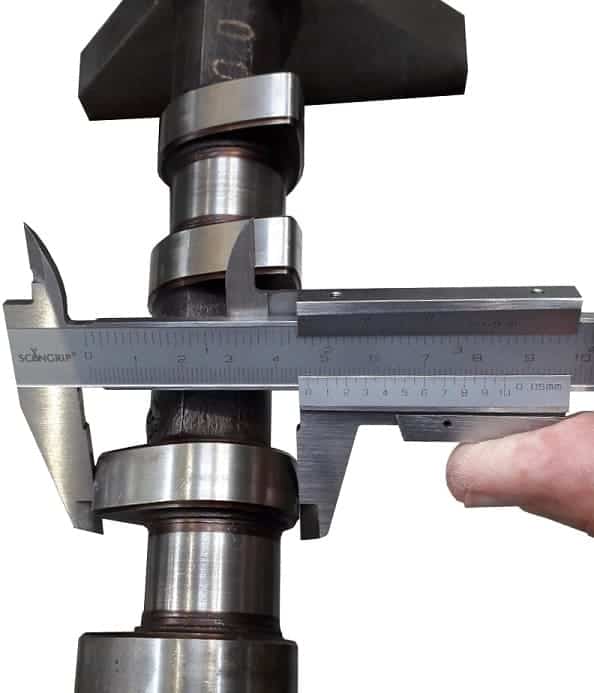
Hauptlagerzapfen messen:
Wir können den Außendurchmesser der Hauptlagerzapfen mit einem Messschieber oder Mikrometer messen. Wie auch bei der Firsthöhe können die Mindestwerte in den Werksdaten nachgeschlagen und mit den Messwerten verglichen werden.
Ein Verschleiß der Hauptlagerzapfen kann auftreten, nachdem die Lagerdeckel bei einer vorherigen Demontage und Montage ihre Position gewechselt haben. Wenn zwei Lagerdeckel ausgetauscht oder um 180 Grad gedreht werden, verschleißen sowohl die Lagerdeckel als auch die Nockenwelle dort, wo der Abstand zwischen den beiden Teilen am kleinsten ist.
Für den Fall, dass wir bei dieser Messung einen zu kleinen Wert messen, der vom Minimalwert abweicht, besteht die Möglichkeit, dass es an dieser Stelle zu Ölverlust kommt: Der Ölstrom kann (zu) leicht an diesem Lager vorbeiströmen, wodurch es zu einem Ölverlust kommt an diesem Lager vorbeiströmen, größer sein als an den Lagern am Ende der Nockenwelle. Die Folge ist, dass es den letzten Nocken an Schmierung mangelt und die Wahrscheinlichkeit groß ist, dass die Nocken verschleißen.
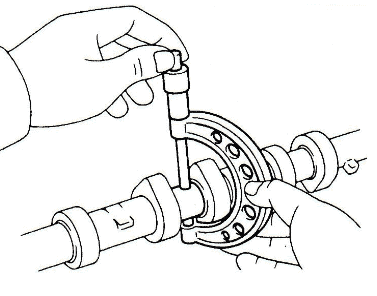
Messung der Krümmung der Nockenwelle:
Die Krümmung der Nockenwelle sollte mit einer Messuhr am mittleren Lagerabschnitt gemessen werden. Bei der Messung mit der Messuhr montieren wir die Messuhr auf einem Stativ und platzieren die Nockenwelle in Halterungen, in denen wir sie drehen können. Der Stift der Messuhr berührt die Rückseite der Messuhr; hier stellen wir eine Vorspannung von mindestens 2 mm ein. Beim Drehen der Nockenwelle können Sie anhand des Zeigerausschlags (vom Einstellen der Vorspannung bis zum Maximalwert auf Nockenhöhe) erkennen, ob die Nockenwelle verbogen ist.
Bei bestimmten Motoren muss die Krümmung weniger als 0,02 mm betragen. Der maximal zulässige Wert beträgt 0,1 mm. Bei einem Wert über 0,1 mm muss die Nockenwelle ausgetauscht werden. Beziehen Sie sich immer auf die Werksspezifikationen.

Axiales Lagerspiel messen:
Mit einer Messuhr können wir das Axiallagerspiel messen. Hierzu müssen die Nockenwellenlagerdeckel natürlich mit dem erforderlichen Drehmoment angezogen werden.
Das Axialspiel der Nockenwelle kann in diesem Beispiel zwischen 0,090 und 0,150 mm betragen. Wenn wir einen Abstand von 0,120 mm messen, ist das in Ordnung.
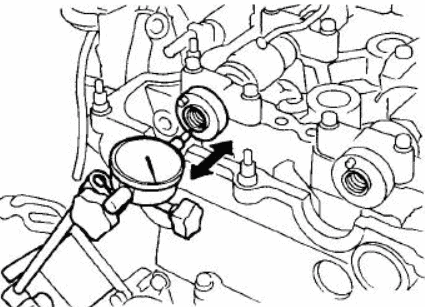
Nockenwellenradhub messen:
Ein Motor mit Steuerkette hat ein Kettenrad. Kommt es aufgrund eines Defekts, einer Beschädigung oder eines Montagefehlers zu einem Klopfen am Kettenrad, folgt die Steuerkette dieser Bewegung bei jeder Umdrehung, was zu erhöhtem Verschleiß oder sogar Bruch führt.
Mit einer Messuhr und einem Stativ kann der Hub des Kettenrads erneut gemessen werden. Der Stift der Messuhr drückt mit einer Vorspannung gegen das Ritzel, sodass der Stift jede Bewegung mitmacht.
Das Kettenrad darf in diesem Beispiel einen Hub von 0,25 mm nicht überschreiten.
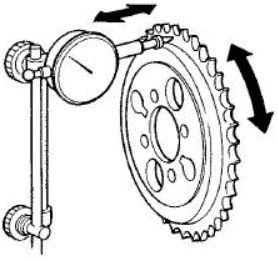
Verwandte Seiten: