Themen:
- Einführung
- Positionierung des Sensors und des Impulsrades
- Der fehlende Zahn im Impulsrad
- Funktionsweise des Kurbelwellen-Positionssensors
- Signale mit dem Oszilloskop messen
Einführung:
Der Kurbelwellenpositionssensor (auch OT-Sensor oder Motordrehzahlsensor genannt) ist normalerweise unten am Motorblock in der Nähe des Schwungrads montiert. Bei laufendem Motor misst der Kurbelwellen-Positionssensor die Zähne oder Magnete des Impulsrads, die sich am Messelement des Sensors vorbeibewegen. Der Kurbelwellen-Positionssensor erzeugt eine Änderung des Magnetfeldes zwischen Sensor und Impulsrad, eine Änderung der Signalspannung (induktiv oder Hall). Die Geschwindigkeit, mit der diese Impulse aufeinander folgen, ist ein Maß für die Geschwindigkeit. Irgendwann fehlen am Impulsrad ein oder zwei Zähne. Das resultierende Signal ist für den Motor Motorsteuergerät ein Hinweis auf die Position, in der sich die Kolben befinden. Dadurch kann das Motormanagement unter anderem den Einspritzzeitpunkt und den Zündzeitpunkt bestimmen. Auch die Kurbelwellendrehzahl wird angepasst Drehzahlmesser im Kombiinstrument gesendet.
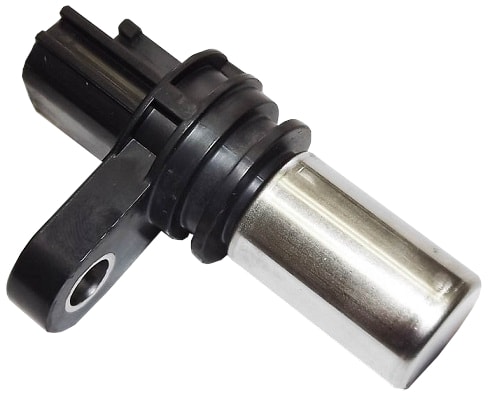
Positionierung von Sensor und Impulsrad:
Das Impulsrad (auch Geberrad, Referenzrad oder Reluktorrad genannt) kann sich an verschiedenen Stellen im oder am Motor befinden:
- außen an der Kurbelwellenriemenscheibe: Bei älteren Motoren sieht man, dass die Kurbelwellenriemenscheibe, über die der Keil- oder Mehrfachriemen angetrieben wird, Zähne hat. Bei modernen Motoren begegnet uns diese Form der außenliegenden Impulsräder nicht mehr;
- innen durch geschliffene Zähne an der Kurbelwelle: Das Impulsrad befindet sich auf der Kurbelwelle an der Innenseite des Kurbelwellenflansches und ist bei demontierter Ölwanne sichtbar;
- außen am hinteren Kurbelwellendichtring: Ein Zahnring oder Magnetring ist außen am Motorblock zwischen der Außenseite des Kurbelwellenflansches und dem Schwungrad angebracht. Dies ist zugänglich, wenn das Schwungrad demontiert wurde.
Der Kurbelwellensensor ist auf das Impulsrad gerichtet. Bei modernen Motoren befindet sich der Kurbelwellensensor häufig seitlich am Motor in der Nähe des Schwungrads. Die folgenden Bilder zeigen drei verschiedene Einbauorte des Kurbelwellen-Positionssensors und des Impulsrads: Zähne an der Kurbelwelle an der Innenseite des Flansches und an der Außenseite des Flansches einen Magnetring und einen Zahnring.
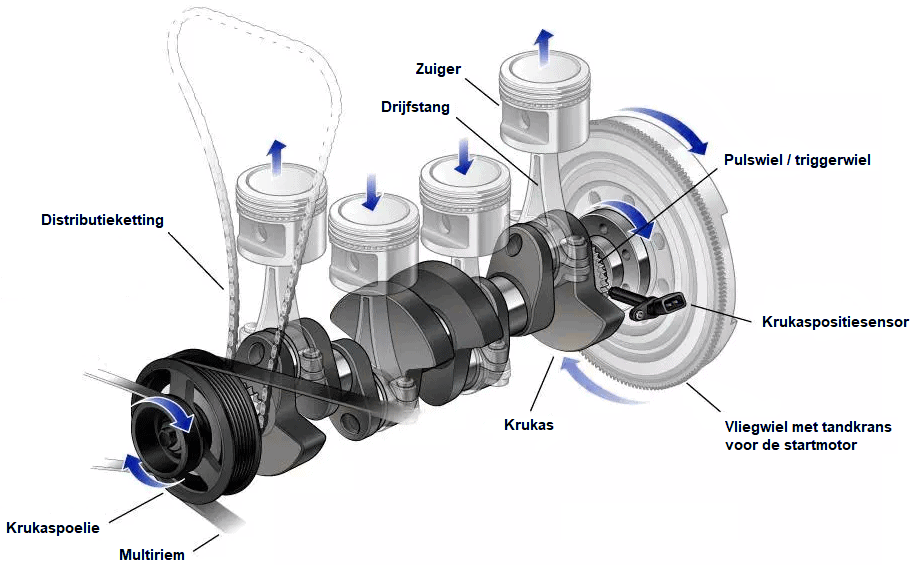
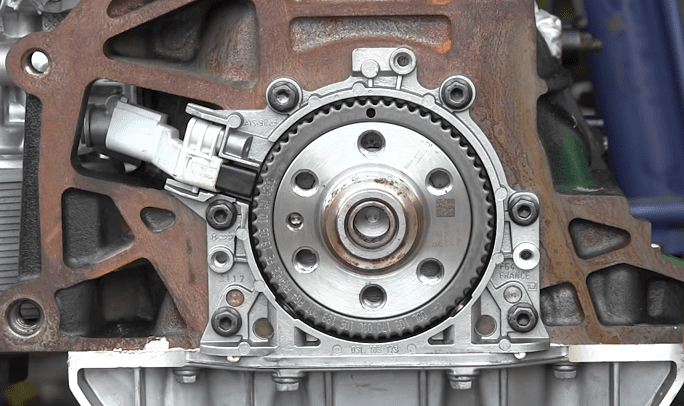
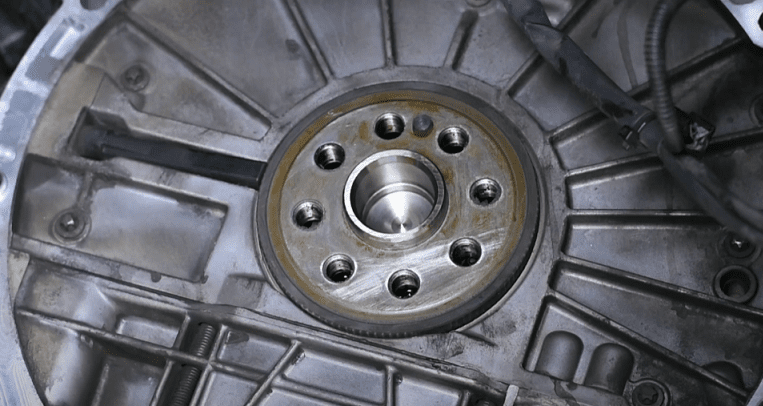
Die Bilder oben zeigen Impulsräder mit Kurbelwellenpositionssensoren, die von VAG und BMW verwendet werden. Die bei VAG häufig verwendete Ausführung besteht aus einer Kassette, in der das Impulszahnrad auch das Gehäuse des Kurbelwellendichtrings enthält. Der BMW-Magnetring wurde über den Kurbelwellenflansch geschoben. Achten Sie beim Austausch des Schwungrads darauf, dass dieser Magnetring nicht herausfällt. Es kommt häufig vor, dass nach dem Austausch der Kupplung samt Schwungrad der Motor nicht mehr starten will, weil der Magnetring nicht wieder eingebaut wurde.
Der fehlende Zahn im Impulsrad:
Der Kurbelwellen-Positionssensor misst die Zähne am Referenzrad, das auf der Kurbelwelle montiert ist. Der Kurbelwellen-Positionssensor „zählt“ die vorbeiziehenden Zähne und „merkt“, dass bei jeder Umdrehung ein Zahn fehlt. Anhand dieses fehlenden Zahns weiß das Motormanagement, in welcher Position sich die Kurbelwelle befindet und damit auch, auf welcher Höhe sich der Kolben während des Kompressionshubs im Zylinder befindet.
Der fehlende Zahn befindet sich an der Stelle, an der sich der Kolben von Zylinder 1 zwischen 90 und 120 Grad vor dem oberen Totpunkt befindet. Der Name „OT-Sensor“ ist daher falsch: Der Sensor misst nicht den Punkt, an dem sich der Kolben am oberen Totpunkt befindet, sondern die Position, in der der Kolben bereit ist, sich zum oberen Totpunkt zu bewegen.
Viele Motoren sind mit einem 36-1 oder einem 60-2 Impulsrad ausgestattet. In diesem Beispiel besprechen wir das 36-1-Impulsrad. Dieses Impulsrad hat 36 Zähne, von denen einer abgeschliffen ist. Bei jeder Kurbelwellenumdrehung (360°) vergehen 36 (abzüglich der fehlenden) Zähne. Das bedeutet, dass alle 10° ein Zahn am Sensor vorbeiläuft.
Auf dem Bild sehen wir, dass der fehlende Zahn fast oben ist. In dieser Position steht der Motor im oberen Totpunkt. Die Drehrichtung ist im Uhrzeigersinn, der fehlende Zahn war also 90° früher am Sensor vorbeigedreht. Diese Position ist der Referenzpunkt. Während dieser 90°-Drehung hat sich der Kolben von Zylinder 1 vom ODP zum OTP bewegt.
Sobald der fehlende Zahn den Sensor passierte, übersetzte der Sensor dies in eine Änderung des Kurbelwellensignals, und dies war der Erkennungspunkt (Referenzpunkt) für das Motormanagementsystem, um einige Zähne später mit der Einspritzung und/oder Zündung zu beginnen.
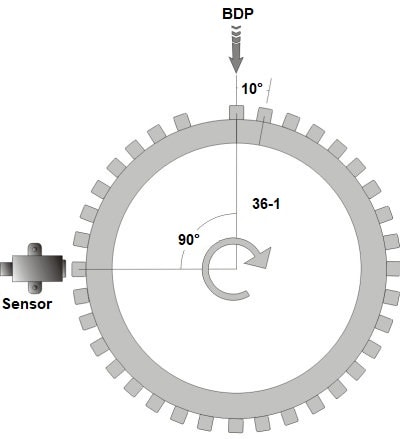
Wenn die Motordrehzahl oder die Belastung des Motors zunimmt, spricht man von „Voreinspritzung"Oder"Zündvorlauf„. Dies ist möglich, indem der Referenzpunkt bei 90 oder 120° für den OT liegt. Beispiel zum Zündzeitpunkt:
- Bei niedriger Drehzahl und geringer Last (1000 U/min bei 25 kPa) beträgt der Zündvorlauf 15°† Dies entspricht eineinhalb Zähne vor BDP;
- Bei erhöhter Drehzahl und erhöhter Last (3100 U/min bei 60 kPa) beträgt der Zündvorlauf ca 30°† Dies entspricht drei Zähne vor BDP.
Wenn im letzteren Fall drei Zähne vor dem oberen Totpunkt gezündet werden müssen, hat das Motormanagementsystem Zeit, die Zündspule zwischen 9 Zähnen (90°) vom Referenzpunkt und drei Zähnen (30°) von der gewünschten Zündung einzuschalten so dass die Zündung eingeleitet wird, bevor der Kolben den oberen Totpunkt erreicht.
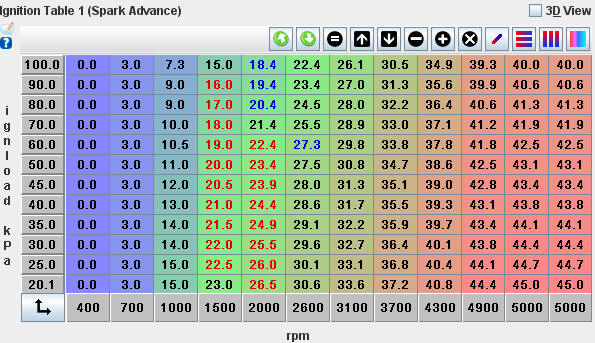
Ein Kurbelwellen-Positionssensor sendet ein Signal, aus dem das Motormanagementsystem schließen kann, dass sich der Kolben von Zylinder 1 in Position 90 befindet° von 120° vor BDP. Unbekannt ist, ob der Kolben mit dem Verdichtungstakt oder dem Ausstoßtakt beschäftigt ist.
- Ein Motor, der nur über einen Kurbelwellenpositionssensor verfügt, ist mit einer DIS-Zündspule ausgestattet, bei der alle Zündkerzen bei jeder Kurbelwellendrehung Funken erzeugen, was zu einem „verschwendeten Funken“ während des Auspuffhubs führt;
- Zur individuellen Ansteuerung von Stiftspulen und Einspritzdüsen ist ein Nockenwellensensor erforderlich. Anhand der Informationen des Nockenwellensensors kann das Motormanagementsystem feststellen, dass Zylinder 1 mit dem Verdichtungstakt und nicht mit dem Ausstoßtakt beschäftigt ist.
Durch die Kombination von Kurbelwellen- und Nockenwellensensor wird die Geschwindigkeit und Steuerung des Einspritz- und Zündsystems pro Zylinder erreicht.
Funktionsweise des Kurbelwellen-Positionssensors:
Das Bild unten links zeigt die magnetischen Feldlinien, die entstehen, wenn sich ein Kurbelwellenzahn am Magneten des Kurbelwellen-Positionssensors vorbeibewegt. Das Kurbelwellensignal ist im Bild unten rechts zu sehen. Für jeden fehlenden Zahn an der Kurbelwelle ist ein vergrößerter Breitenabstand und eine erhöhte Amplitude des Signals zu erkennen. Das Motormanagement erkennt die vergrößerte Signalbreite als Referenzpunkt, bei dem der Kolben 90° oder 120° vor OT steht.
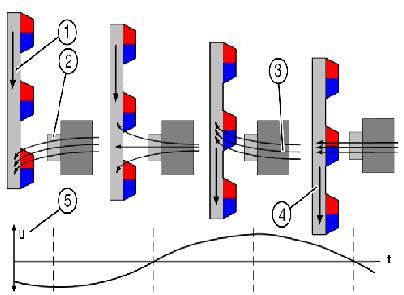
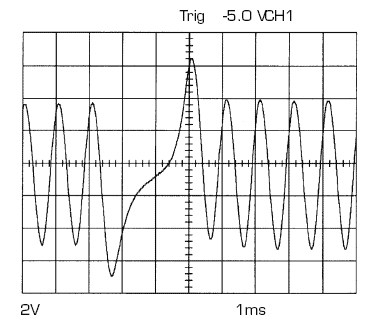
Schaltpläne des Kurbelwellen-Positionssensors:
Um den Kurbelwellen-Positionssensor zu messen, konsultieren wir zunächst den elektrische Diagramme. Die folgenden Diagramme beziehen sich auf den Sensor desselben Motors (VW Golf VI).
- Im VAG-Diagramm hat der Kurbelwellen-Positionssensor den Komponentencode G28 und in den HGS-Daten B56);
- Die VAG-Diagramme haben auf dem Steuergerät den Code T60 mit der Pin-Nummer des Steckers dahinter (T60/25) und die HGS-Daten den Buchstaben B (B25). An anderer Stelle im Diagramm wird angegeben, dass Stecker B der 60-polige Stecker am Steuergerät ist.
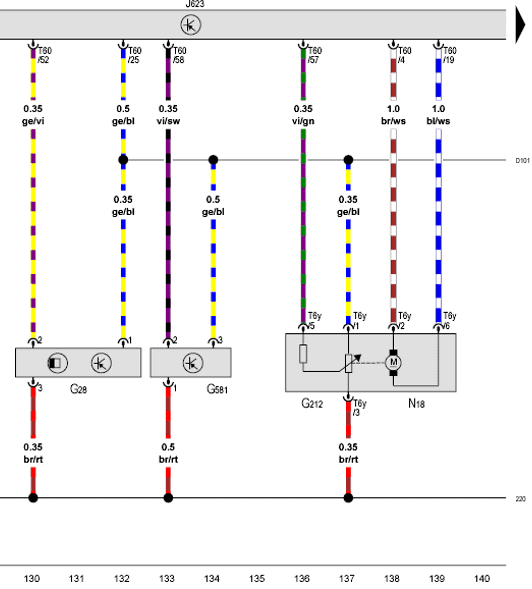
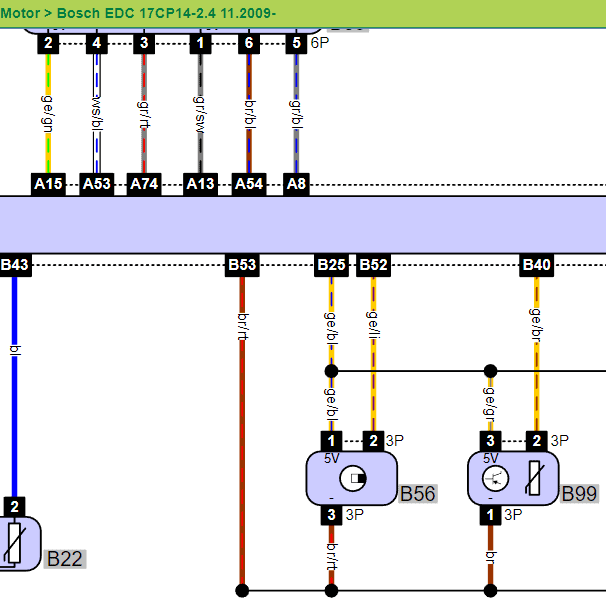
Eine Versorgungsspannung von 25 Volt wird von Pin 5 an der ECU an den Kurbelwellen-Positionssensor, den Kraftstoffdrucksensor, das AGR-Ventil, die Drosselklappe und den Turbo-Einstellpositionssensor gesendet. Oben sind nicht alle Komponenten abgebildet. Pin 25 ist also für die Stromversorgung. Pin 53 für Masse (siehe HGS-Datendiagramm) und Pin 52 für das Signal vom Kurbelwellen-Positionssensor. Wir können direkt an Pin 52 im Steuergerätestecker messen, oder wir schließen einen an Breakout-Box um im Anschluss 52 der Breakout-Box sicher und übersichtlich messen zu können.
Signale mit dem Oszilloskop messen:
Mit einer zweikanaligen Messung kann das Kurbelwellensignal im Verhältnis zum Nockenwellensignal dargestellt werden. Anhand dieser Signale kann festgestellt werden, ob der zeitliche Verlauf der Verteilung noch in Ordnung ist oder ob beispielsweise aufgrund einer gedehnten Steuerkette das Nockenwellensignal dem Kurbelwellensignal hinterherhinkt. Das Bild unten zeigt eine Messung eines Kurbelwellensignals (Kanal A, blau) im Vergleich zu einem Nockenwellensignal (Kanal B, rot).

An den Signalen der Kurbelwellen- und Nockenwellensensoren können wir folgende Punkte erkennen:
- Bei jeder Nockenwellenumdrehung (Erkennungspunkte: die beiden schmalen Blöcke) sind vier fehlende Zähne der Kurbelwelle vergangen;
- Die Kurbelwelle dreht sich zwei Umdrehungen, während die Nockenwelle eine Umdrehung macht (Verhältnis 2:1), was bedeutet, dass sich bei jeder halben Umdrehung der Kurbelwelle ein fehlender Zahn am Sensor vorbei dreht.
Der Motor in diesem Beispiel (VW Golf VI) ist mit einem gezahnten Impulsrad ausgestattet, bei dem alle 180 Grad (eine halbe Umdrehung) ein Zahn fehlt. Dieses Impulsrad ist im Bild des Abschnitts „Positionierung des Sensors und des Impulsrads“ dargestellt. Wenn Sie genau hinsehen, können Sie auf diesem Bild die fehlenden Zähne erkennen. Wenn die Drehzahl des Motors erhöht wird, erhöht sich auch die Frequenz des Signals. Die Impulse rücken dann näher zusammen. Die Amplitude (die Höhe der Spannung) bleibt gleich. Eine Messung am gleichen Motor mit erhöhter Drehzahl ist im Scope-Bild unten zu sehen:

Bei Verdacht auf Timing-Probleme können Referenzpunkte im Kurbel- und Nockenwellensignal problemlos mit einem Mustersignal oder einem anderen Motor verglichen werden.
Durch Markieren zweier Punkte kann die Differenz der Zähnezahl im gemessenen Signal mit dem Probensignal verglichen werden. Liegt im Messsignal das Kurbelwellensignal vor dem Nockenwellensignal (der Bezugspunkt der Kurbelwelle verschiebt sich nach links), ist möglicherweise die Steuerkette gedehnt.
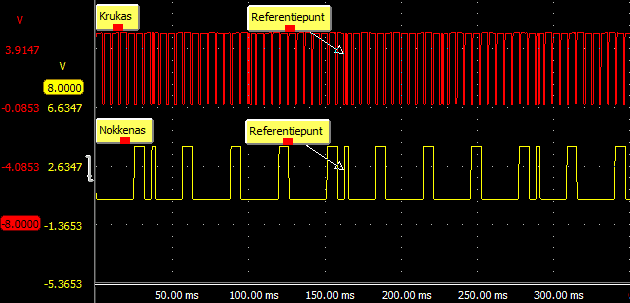
Das obige Kurbelwellensignal stammt von einem Hallsensor. Auch ein Motorrad ist möglich sind. Ausgestattet mit einem induktiven Sensor. Ein Beispiel hierfür ist in der folgenden Messung zu sehen. Bei einem induktiven Sensor erhöht sich mit zunehmender Geschwindigkeit nicht nur die Frequenz (die Impulse rücken näher zusammen), sondern auch die Amplitude. Die Frequenz ist wichtig, damit das Steuergerät die Geschwindigkeit bestimmen kann. Auch in diesem Signal ist der fehlende Zahn deutlich zu erkennen. Die gelbe Leitung (vom Nockenwellensensor kommend) sendet nach jedem zweiten Kurbelwellensignal einen Impuls. Diese Signale können auch miteinander verglichen werden.
Für das induktive Kurbelwellensignal kann auch ein Referenzpunkt gewählt werden, z.B.:
- das Nockenwellensignal fällt auf 0 Volt;
- Dies geschieht zwei (Kurbelwellen-)Zähne nach dem fehlenden Zahn.
Anhand eines Beispielsignals prüft man, ob auch zwei Zähne dazwischen liegen. Liegen drei Zähne dazwischen, liegt wiederum eine Anomalie vor.
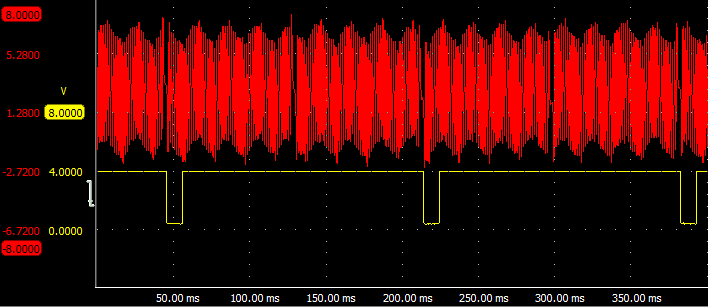
Mögliche Fehler im Kurbelwellensensorsignal:
Möglicherweise ist der Kurbelwellensensor defekt und gibt kein Signal aus. Das Motormanagementsystem empfängt kein Motordrehzahlsignal, was bedeutet, dass der Motor beim Starten nicht anspringt. Das Nockenwellensignal kann erfasst werden und der Motor kann nach längerem Neustart nur mit dem Nockenwellensignal laufen.
Wenn das Impulsrad beschädigt ist, erkennt das Motormanagementsystem den Schaden möglicherweise fälschlicherweise als fehlenden Zahn. Der Schaden verursacht eine Abweichung in der Amplitude der vom Kurbelwellensensor gelieferten Wechselspannung. Ein Beispiel sehen wir in den Bildern unten.
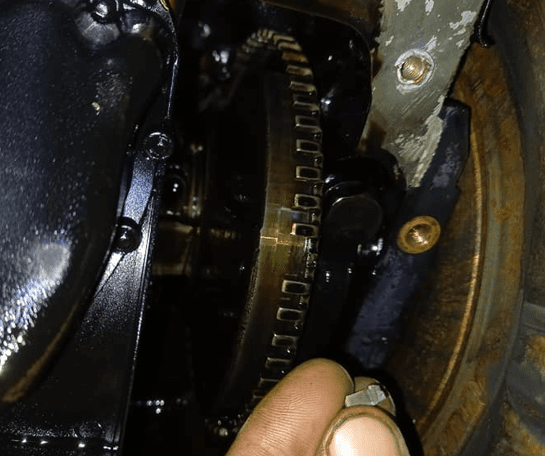
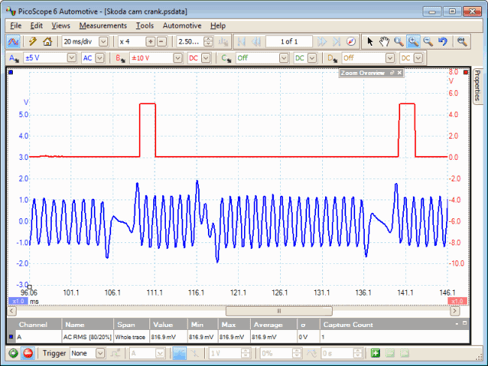
Im Scope-Bild sehen wir den charakteristischen Verlauf des fehlenden Zahns zweimal (links relativ zum Nockenwellenimpuls). Rechts vom Nockenwellenimpuls sehen wir eine Störung im Bild. Das Motormanagement erkennt die Störung und kann daher zum falschen Zeitpunkt einspritzen und zünden. Wenn das MMS das Kurbelwellensignal mit dem Nockenwellensignal vergleicht, kann ein Fehler erkannt und ein DTC (Fehlercode) in Bezug auf das Kurbelwellensignal gespeichert werden. In diesem Fall wurde der Kurbelwellenpositionssensor möglicherweise falsch ausgetauscht.
Der beschädigte Zahn am Impulsrad kann durch Arbeiten am Motor verursacht worden sein, bei denen versucht wurde, die Kurbelwelle zwischen den Zähnen des Impulsrades mit einem Schraubenzieher zu blockieren, statt mit dem Starterring am Schwungrad.
Verwandte Seiten: