Themen:
- Allgemeines
- Material
- Mit Natrium gefüllte Ventile
- Ventilführungen
- Verschiedene Arten der Ventilsteuerung
- Ventilmechanismus mit indirekter Ventilsteuerung
- Ventilmechanismus mit direkter Ventilsteuerung
- Ventilspiel einstellen
- Mehrventiltechnik
- Variable Ventilsteuerung und Ventilhub
Gesamt:
In jedem Verbrennungsmotor gibt es Ventile. Es gibt immer mindestens ein Einlass- und ein Auslassventil. Diese Ventile werden von einer oder mehreren Nockenwellen durch das Verteilergetriebe angetrieben und sorgen dafür, dass Frischluft in den Brennraum strömen kann, die Luft dann beim Verdichten eingeschlossen wird und dann den Brennraum verlassen kann. Die Strömung der Einlass- und Abgase muss möglichst widerstandsfrei erfolgen.
Die Materialien sind hierfür bestmöglich geformt.
Die Ventile sind im Zylinderkopf montiert. Das Einlassventil ist häufig größer als das Auslassventil, da möglichst viel Gemisch in den Zylinder gelangen muss. Das Auslassventil sollte kleiner sein, da verbrannte Abgase den Zylinder nach dem Ausstoßtakt verlassen, wenn der Kolben die Gase aus dem Zylinder drückt.
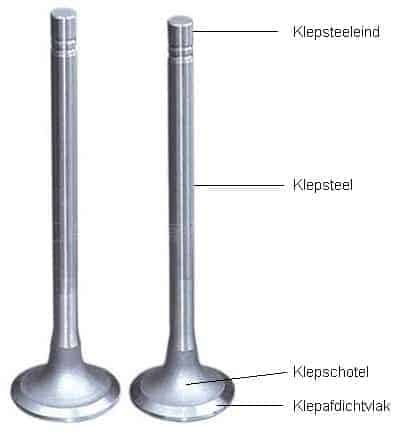
Als Beispiel nehmen wir den Viertaktvorgang eines Benzinmotors. Beim Ansaugtakt des Motors öffnet sich das Einlassventil und bei einem indirekt einspritzenden Benzinmotor wird ein Luft-Kraftstoff-Gemisch angesaugt, bei einem direkt einspritzenden Benzinmotor wird nur Frischluft angesaugt . Durch die Abwärtsbewegung des Kolbens wird die Luft angesaugt. Die einströmende Luft nimmt den frei werdenden Raum ein. Wenn sich der Kolben wieder nach oben bewegt, schließt sich das Einlassventil. Das Kraftstoff-Luft-Gemisch kann nun nicht mehr entweichen und wird komprimiert. Dies wird als Kompressionshub bezeichnet. Deshalb ist es wichtig, dass die Ventile richtig schließen. Das Gemisch entzündet sich, wenn die Zündkerze einen Funken erzeugt. Der Kolben wird daher mit erheblicher Kraft nach unten gedrückt. Dies wird als Krafthub bezeichnet.
Beim Ausstoßhub öffnet sich das Auslassventil und der Kolben bewegt sich nach oben. Die verbrannten Gase verlassen nun den Zylinder und gelangen zum Auspuff. Wenn der Kolben oben ist, schließt das Auslassventil und das Einlassventil öffnet. Der Kolben bewegt sich wieder nach unten und es folgt der Ansaugtakt. In Wirklichkeit öffnet das Einlassventil etwas früher, so dass Einlass- und Auslassventil für kurze Zeit gleichzeitig geöffnet sind. Dies wird als „Ventilüberlappung“ bezeichnet. Die Geschwindigkeit der verbrannten Gase, die den Zylinder durch das Auslassventil verlassen, erzeugt einen Unterdruck, der die Ansaugluft zusätzlich anzieht. Dadurch kann mehr Luft in den Zylinder strömen, als wenn nur das Einlassventil geöffnet und der Kolben nach unten bewegt würde. Der Füllgrad wird dadurch verbessert.
Eine ausführlichere Erläuterung des Viertaktverfahrens finden Sie auf der Seite „Betrieb des Benzinmotors".
Material
Ventile werden stark belastet. Vor allem die Auslassventile, denn diese werden extrem heiß und lassen sich nicht so gut kühlen. Die Einlassventile werden teilweise durch die kalte angesaugte Luft gekühlt, die in den Zylinder gelangt. Die verbrannten Abgase strömen mit einer Temperatur von bis zu 900 Grad Celsius an den Auslassventilen vorbei. Deshalb bestehen auch Auslassventile aus einem anderen Material als Einlassventile. Einlassventile bestehen häufig aus Chromnickelstahl. Auslassventile bestehen häufig aus Chrom-Silizium-Stahl. Um den Verschleiß aufgrund der hohen Temperaturbedingungen zu begrenzen, sind die Außenkanten des Ventiltellers (die Dichtfläche) und die Ventilschäfte mit einer Schicht aus einer Karbidlegierung (Stellit) gepanzert. Die Ventile leiten den Großteil der Wärme über den Ventilteller und den Ventilschaft ab. Mit Natrium gefüllte Ventile weisen eine noch bessere Wärmeableitung auf.
Mit Natrium gefüllte Ventile:
Auslassventile sind innen hohl. Der Hohlraum ist zu ca. 60 % mit Natrium gefüllt. Natrium ist ein Metall, das bei hoher Temperatur (ab etwa 100 Grad Celsius) flüssig wird. Bei laufendem Motor geht das Ventil oft auf und ab. Das Natrium im Ventil wird ständig hin und her geschleudert und transportiert so die Wärme. Das Natrium nimmt Wärme vom Ventilteller auf und gibt sie an den Ventilschaft ab. Mit natriumgefüllten Ventilen können Sie im Vergleich zu nicht natriumgefüllten Ventilen eine Temperatursenkung von 80 bis 100 Grad erreichen.
Einlassventile benötigen dies nicht, da sie bereits durch die einströmende Luft gekühlt werden.
In der Abbildung stellt die graue Oberfläche das Material und der rote Teil den mit Natrium gefüllten Hohlraum dar.
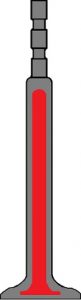
Ventilführungen:
Die Ventile bewegen sich im Zylinderkopf auf und ab. Zwischen dem Ventil und dem Zylinderkopf muss eine gute Abdichtung bestehen, damit kein Öl vom Zylinderkopf entlang des Ventilschafts zu einem Einlass- oder Auslasskanal fließen kann. Zur Schmierung befindet sich zwischen Ventil und Ventilführung immer ein kleiner Ölfilm. Die Ventilführung ist in der Abbildung orange dargestellt.
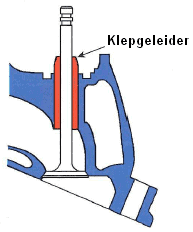
Wenn blauer Rauch aus dem Auspuff austritt, kann dies an defekten Ventilführungen liegen. Es kann sein, dass die Ventilführungen breiter geworden sind (siehe Bild unten), sodass das Ventil sogar Spiel im Zylinderkopf hat. In dieser Situation kann Öl am Ventil vorbei in den Einlass- oder Auslasskanal gelangen. An der Oberseite der Ventilführung herrscht Außenluftdruck, teilweise sogar Überdruck aufgrund eines höheren Kurbelgehäusedrucks. Am unteren Ende der Ventilführung strömen die Gase zum Abgaskrümmer, wodurch ein Vakuumeffekt entsteht. Dadurch erhöht sich die Leckage, da das Öl sozusagen am Ventilschaft entlang nach unten gesaugt wird. Wenn das Öl in den Abgaskrümmer gelangt, wird es nicht verbrannt. Das Öl wird erhitzt, wodurch es teilweise verdampft. Dies kann dazu führen, dass blauer Rauch aus dem Auspuff austritt.
Ventilführungen können oft separat ausgetauscht werden. Dazu muss der Zylinderkopf demontiert und das Ventil aus dem Zylinderkopf entfernt werden. Anschließend können die Ventilführungen ausgetauscht werden. Die Ventilführungen können nicht bei allen Zylinderköpfen einzeln ausgetauscht werden. Remanufacturing-Unternehmen haben dafür oft eine Lösung. Erkundigen Sie sich bei einem renommierten Überholungsunternehmen nach den Möglichkeiten zum Austausch von Ventilführungen.
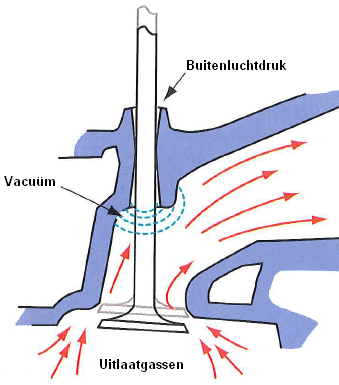
Verschiedene Arten der Ventilsteuerung:
Die Ventile können auf unterschiedliche Weise betätigt werden. Das Bild unten zeigt fünf verschiedene Versionen. Diese verschiedenen Versionen und die Methoden zur Anpassung werden auf dieser Seite weiter erläutert.
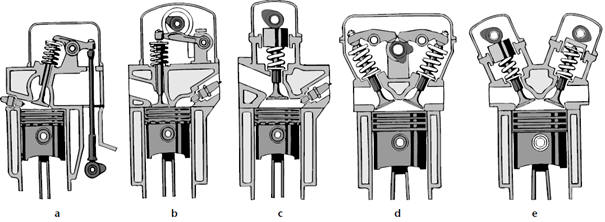
- A: Indirekte Ventilsteuerung mit Kipphebeln.
- B: Direkte Ventilsteuerung mit Rollenschleppwippen.
- C: Direkte Ventilsteuerung mit hydraulischen Ventileinstellern.
- D: Direkte Ventilsteuerung mit Kipphebeln und mehreren Ventilen pro Zylinder.
- E: Direkte Ventilsteuerung mit hydraulischen Ventilstößeln und mehreren Ventilen pro Zylinder.
Bei Motoren ohne hydraulische Ventilstößel (A, B und D) ist es notwendig, das Ventilspiel regelmäßig zu überprüfen. Mehr dazu im Kapitel „Ventilspiel einstellen“ auf dieser Seite. Bei Motoren mit hydraulischen Ventilstößeln ist eine Einstellung des Ventilspiels weder notwendig noch möglich; Die Hydraulikzylinder sind mit Öl gefüllt, wodurch das überschüssige Spiel beseitigt wird.
Ventilmechanismus mit indirekter Ventilsteuerung:
Früher waren Motoren mit einem Unterlager ausgestattet Nockenwelle. Heutzutage sind Pkw-Motoren nur noch mit einer obenliegenden Nockenwelle ausgestattet. Die Konstruktion mit der darunter liegenden Nockenwelle verschwindet. Der Nachteil dieser Konstruktion besteht darin, dass diese Motoren keine hohen Drehzahlen bewältigen können, da sich zwischen Nockenwelle und Ventil viel Masse befindet. Bei hohen Geschwindigkeiten entsteht zu viel Spiel und das Ventil öffnet und schließt nicht mehr zum richtigen Zeitpunkt.
Die Kurbelwelle treibt mittels an eine kleine Steuerkette oder einen kleinen Steuerriemen an die darunter liegende Nockenwelle (siehe Abbildung unten). Die Nockenwelle drückt den Ventilstößel und die Stößelstange gerade nach oben. Die rechte Seite des Kipphebels wird nach oben gedrückt. Der Kipphebel „taumelt“ um die Kipphebelachse und drückt die linke Seite nach unten. Dadurch wird das Ventil gegen die Kraft der Ventilfeder nach unten gedrückt. Bei weiterer Drehung der Nockenwelle drückt die Ventilfeder das Ventil zu und der Kipphebel kehrt in seine Ausgangsposition zurück.
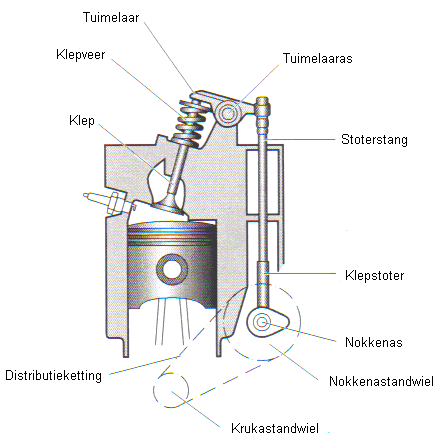
Ventilmechanismus mit direkter Ventilsteuerung:
Die obenliegende Nockenwelle wird heutzutage nur noch in Pkw eingesetzt. Anschließend wird die Nockenwelle in den Zylinderkopf eingesetzt. Der Vorteil von Motoren mit oben liegender Nockenwelle besteht darin, dass sie höhere Drehzahlen bewältigen können als mit unten liegender Nockenwelle.
Im linken Bild oben sehen Sie, dass das Ventil geschlossen ist, weil die Ventilfeder das Ventil zudrückt und sich die Nockenwelle im Uhrzeigersinn dreht. Im rechten Bild ist die Nockenwelle verdreht, wodurch der Nocken das Ventil nach unten drückt. Die Feder ist jetzt zusammengedrückt und drückt das Ventil nach unten. Bei weiterer Drehung der Nockenwelle drückt die Ventilfeder das Ventil wieder nach oben. Die Ventilfeder übt einen Gegendruck von ca. 20 kg aus.
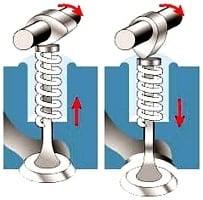
Das Bild zeigt eine schematische Darstellung eines Ventils mit Ventilfeder. Hier ist deutlich zu erkennen, mit welchem Teil das Ventil auf der Ventilschließfläche des Ventilsitzes aufliegt. Oben befindet sich der Federsitz (der Teil, an dem der Nocken der Nockenwelle das Ventil nach unten drückt), darunter der Ventilkegel und die Ventilfeder. Der Ventilschlüssel dient als Halterung für das Ventil. Um das Ventil vom Zylinderkopf zu entfernen, müssen die Ventilkeile entfernt werden. Bei der Demontage muss der Federsitz gegen die Kraft der Ventilfeder nach unten gedrückt werden (hierfür sind Spezialwerkzeuge erhältlich). Das Ventil ist dann frei beweglich. Durch Entfernen der beiden Ventilkeile mit Magnet zwischen Federsitz und Ventilschaft kann das Ventil von unten aus dem Zylinderkopf entnommen werden.
Beim Einbau muss darauf geachtet werden, dass das richtige Ventil wieder an der richtigen Stelle eingebaut wird. Diese sind vom Umtausch ausgeschlossen. Wenn ein neues Ventil eingebaut wird, muss es mit einer speziellen Schleifpaste geschliffen werden. Nach dem Schleifen dichtet das Ventil gut ab. Anschließend kann das neue Ventil durch die Ventilschaftführung geschoben und die Ventilkeile wieder eingesetzt werden. Anschließend kann die Ventilfeder wieder entspannt werden.
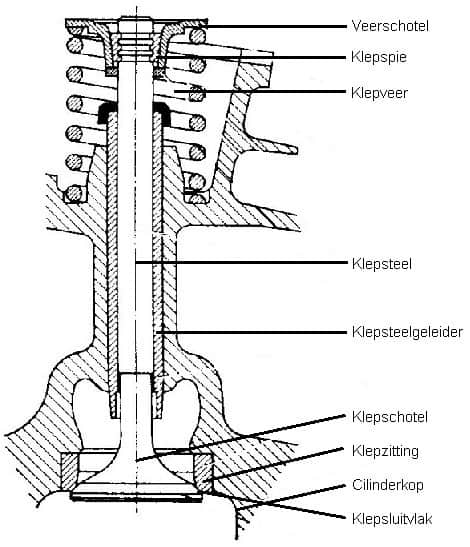
Ventilspiel einstellen:
Zwischen der Nockenwelle und dem Kipphebel bzw. der Oberseite des Ventils muss immer ein gewisses Spiel vorhanden sein. Dieser Abstand gibt dem Material die Möglichkeit, sich auszudehnen. Das Stück sollte nicht zu groß sein; Das Ventil öffnet dann weniger weit und für kürzere Zeit. Wenn das Spiel zu groß ist, dauert es länger, bis die Nockenwelle das Ventil aufdrückt, und das Ventil schließt früher. Das Spiel sollte auch nicht zu klein sein; das Ventil wird dann früher geöffnet und später geschlossen. Das Ventil ist dann jedes Mal zu lange geöffnet. Die Zeit, in der das Ventil geschlossen ist, ist daher kürzer; Es besteht die Möglichkeit, dass das Ventil seine Wärme nicht an den Ventilsitz des Zylinderkopfes abgeben kann und daher überhitzt. Das Ventil kann dann brennen.
Heutzutage sind fast alle Pkw mit hydraulischen Ventilstößeln ausgestattet. Es gibt jedoch immer noch Hersteller, die Motoren entwickeln, die eine Einstellung des Ventilspiels erfordern. Bei Autos aus den 90er-Jahren war der Einsatz hydraulischer Ventilstößel keineswegs selbstverständlich. Daher gibt es immer noch viele Fahrzeuge, bei denen das Ventilspiel regelmäßig überprüft und gegebenenfalls angepasst werden muss. In den Werksdaten ist häufig der Kilometerstand aufgeführt, bei dem dies durchgeführt werden sollte (häufig bei jeder größeren Wartung). Für die Einstellung des Ventilspiels gibt es zwei unterschiedliche Konstruktionen; mittels Unterlegscheiben und durch Verstellen von Exzenterbolzen. Beide werden im Folgenden beschrieben.
Beim Einstellen der Ventile sollte man nicht an beliebiger Stelle beginnen. Es muss sorgfältig darauf geachtet werden, wann die Ventile auf „Tumble“ eingestellt werden. Taumeln bedeutet, dass die Nockenwelle gerade die Auslassventile geschlossen hat und dabei ist, die Einlassventile zu öffnen. Wenn Zylinder 1 taumelt, bedeutet dies, dass er sich am Anfang des Ansaugtakts befindet. Der Kolben von Zylinder 1 steht dann oben. Zylinder 1 und 4 sind von der Höhe her immer auf gleicher Höhe (genau wie 2 und 3 auf gleicher Höhe, siehe Bild unten). Da die Zündreihenfolge 1-3-4-2 ist (denken Sie an das Arbeitsdiagramm), bedeutet dies, dass sich Zylinder 4 am Anfang des Arbeitstakts befindet. Nach Zylinder 4 ist Zylinder 2 an der Reihe und dann Zylinder 3.
Das Bild unten zeigt den Kolben von Zylinder 1 im BPD. Die Laschen sind nach unten gerichtet; Die Einlassventile haben sich gerade geschlossen und die Auslassventile stehen kurz vor dem Öffnen. In diesem Moment können die Ventile von Zylinder 4 verstellt werden; die Nocken dort sind nach oben gerichtet.
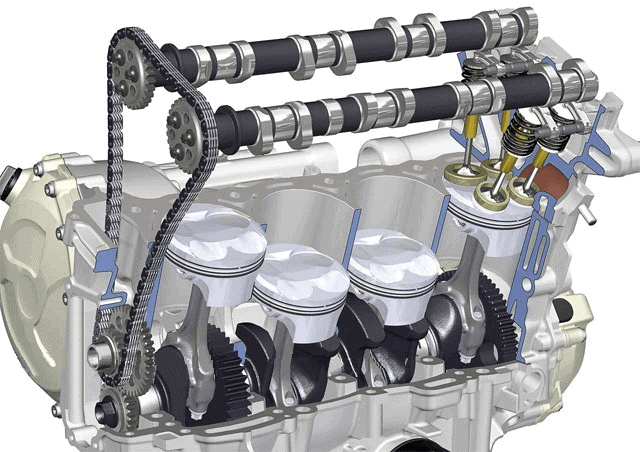
Das Ventilspiel wird mit einem sogenannten „Fühlerlehre„. Die Fühlerlehre enthält Metallstreifen unterschiedlicher Größe, von denen jeder 0,05 mm dicker ist als der andere. Indem Sie mehrere Streifen zwischen Nockenwelle und Ventil schieben, können Sie prüfen, wie viel Spiel vorhanden ist. Der betreffende Streifen darf nicht zu leicht durchgeschoben werden; Das Ventilspiel ist dann größer als der Wert des Streifens. Wenn der Streifen nicht passt oder sehr schwer ist und hängen bleibt, ist der Streifen zu dick. Wenn der Streifen dazwischen bewegt wird, kann ein Widerstand spürbar sein.
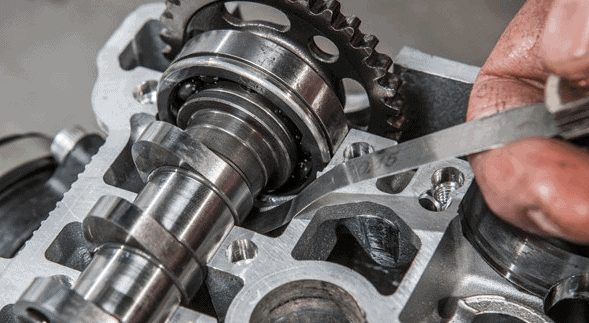
Ventilspiel mit Shims einstellen:
Die Dicke der Unterlegscheibe, auch „Shim“ genannt, bestimmt in diesem Fall das Ventilspiel. Im Bild unten ist die Unterlegscheibe rot markiert. Wenn Sie die Unterlegscheibe durch eine dickere ersetzen, verringert sich das Ventilspiel. Zwischen Nockenwelle und Ausgleichsscheibe ist dann weniger Platz. Unterhalb des Bildes wird erklärt, wie das Ventilspiel eingestellt werden sollte. Um die Ventile einzustellen, muss der Nocken des betreffenden Ventils nach oben zeigen, wie in der Abbildung unten gezeigt. Wenn die Nocke verdreht ist, werden falsche Messungen durchgeführt. Beim Einstellen der Ventile eines Vierzylindermotors müssen folgende Maßnahmen ergriffen werden:
- Zylinder 1 umschalten = Ventile von Zylinder 4 einstellen.
- Zylinder 2 umschalten = Ventile von Zylinder 3 einstellen.
- Zylinder 3 umschalten = Ventile von Zylinder 2 einstellen.
- Zylinder 4 umschalten = Ventile von Zylinder 1 einstellen.
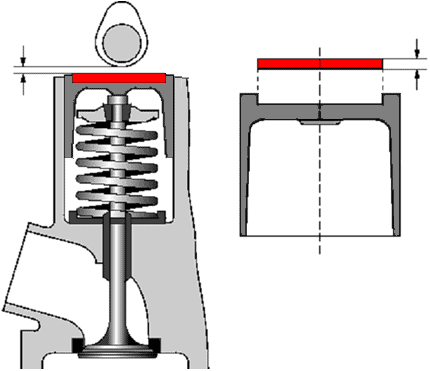
Beispielsweise kann der Werkswert des oben genannten Ventilspiels 0,35 mm betragen. Daher muss zwischen der Unterlegscheibe und der Nockenwelle ein Abstand von 0,35 mm bestehen, wenn die Nocke nach oben zeigt. Der Abstand zwischen den beiden Teilen kann mit der Fühlerlehre gemessen werden. Lässt sich der 0,35-mm-Streifen sehr leicht durchziehen, ohne dass ein Widerstand spürbar ist, bedeutet dies, dass der Abstand zwischen Ventil und Nockenwelle größer als 0,35 mm ist. Dann ist das Ventilspiel zu groß. Passt ein 0,45mm Fühlerlehrenstreifen kaum dazwischen, weil zum Hineinschieben viel Kraft aufgewendet werden muss, ist dieser Streifen zu dick. Das tatsächliche Spiel liegt dann zwischen 0,35 und 0,45 mm. Zur Sicherheit kann ein 0,40mm Streifen dazwischen geschoben werden. Wenn es anspringt, sich aber hin- und herbewegen lässt (möglicherweise ist ein Widerstand zu spüren), dann können Sie sicher sein; Das Ventilspiel beträgt 0,40 mm statt der vorgeschriebenen 0,35 mm.
Da das Ventilspiel zu groß ist, muss eine dickere Unterlegscheibe eingebaut werden. Die Größen sind oft auf den Unterlegscheiben angegeben. Lesen Sie in diesem Fall den Wert der zu dünnen Unterlegscheibe ab. Das sind zum Beispiel 2,75 mm.
Das Ventilspiel ist zu groß; Die Unterlegscheibe muss 0,05 mm dicker sein als die montierte, nämlich 2,75 mm. Wenn eine Unterlegscheibe von (2,75 + 0,05) = 2,80 mm eingebaut ist, ist das Ventilspiel korrekt. In diesem Fall die 2,80-mm-Unterlegscheibe einbauen, die Kurbelwelle zwei Umdrehungen drehen, damit die richtigen Ventile wieder wippen und das Ventilspiel erneut prüfen.
Für den einfachen Austausch der Unterlegscheiben gibt es oft spezielle Demontagewerkzeuge. Ein Beispiel hierfür ist im Bild zu sehen.
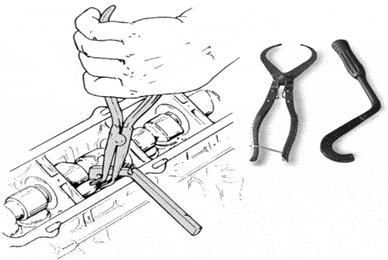
Ventilspiel mit einstellbaren Exzentern einstellen:
Ein häufig verwendetes System ist der verstellbare Exzenter. Die Einstellschraube lässt sich erst drehen, wenn die Kontermutter um eine Vierteldrehung gelöst wurde. Wenn dann die Einstellschraube gedreht wird, vergrößert oder verkleinert sich der Abstand zwischen Ventilschaft und Kipphebel sofort. Durch das anschließende Anziehen der Kontermutter wird die Einstellschraube wieder arretiert.
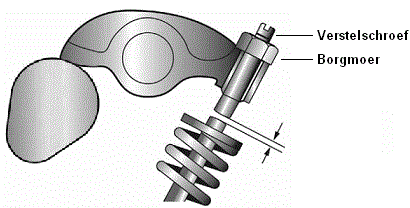
Auch hier müssen natürlich zunächst die Ventile des richtigen Zylinders auf Umschalten gestellt werden! Durch Abtasten zwischen Ventilschaft und Kipphebel mit einer Fühlerlehre der richtigen Dicke (d. h. dem gleichen Wert wie der Werkswert) kann festgestellt werden, ob das Ventilspiel zu groß, zu klein oder korrekt ist. Durch Drehen der Einstellschraube und ständiges Bewegen der Fühlerlehre dazwischen kann die richtige Position der Einstellschraube gefunden werden, bei der das Ventilspiel stimmt. Ziehen Sie dann die Kontermutter fest und prüfen Sie, ob das Spiel noch gleich ist. Es besteht eine gute Chance, dass die Einstellschraube beim Anziehen der Kontermutter leicht verdreht wird, es sei denn, es wird ein vom Hersteller angegebenes Spezialwerkzeug verwendet.
Mehrventiltechnik:
Jeder Viertaktmotor verfügt über mindestens 1 Einlassventil und 1 Auslassventil. Stärkere und sparsamere Motoren verfügen oft über 2 Einlassventile und 2 Auslassventile. Einige Typen haben 2 Einlassventile und 1 Auslassventil oder 3 Einlassventile und 1 Auslassventil.
Die Verwendung mehrerer Ventile bietet zwei Hauptvorteile:
- Die Ventile werden einen etwas kleineren Durchmesser haben, was zu einer geringeren Masse (weniger Gewicht) pro Ventil führt. Der größte Vorteil dabei ist, dass die Ventile bei hohen Motordrehzahlen nicht schwimmen. Schwimmventile bedeuten, dass sich die Ventile bei hoher Motordrehzahl (z. B. 5000 U/min) so schnell öffnen und schließen, dass die Ventilfedern keine Zeit mehr haben, das Ventil zu schließen. Das Ventil schließt daher nicht vollständig auf dem Ventilsitz. Dies kann dazu führen, dass der Kolben am Ventil anschlägt oder das Ventil überhitzt, da es keine Wärme mehr an den Ventilsitz übertragen kann. Die Mehrfachventile machen die Ventile leichter und geben den Ventilfedern genügend Zeit, das Ventil zu schließen.
- Durch die geringere Masse pro Ventil schließen die Ventile schneller. Dies ermöglicht die Anwendung einer variablen Ventilsteuerung, bei der die Position der Nockenwelle bei einer bestimmten Motordrehzahl oder -last geändert wird.
Variable Ventilsteuerung und Ventilhub:
Moderne Motoren verwenden häufig eine variable Ventilsteuerung. Einige Motorenhersteller nutzen auch den variablen Ventilhub (u.a. BMW). Diese Kapitel werden auf den Seiten separat beschrieben: