Themen:
- Einführung
- Intelligenter Batteriesensor
- Komponenten und Messprinzipien des Batteriesensors
- Laden und Ersetzen des Akkus
Einführung:
Bei modernen Fahrzeugen wird der Ladezustand der Lichtmaschine den Gegebenheiten angepasst. Die Lichtmaschine wird vom Motor-ECU gesteuert und erhält Signale, um mehr oder weniger aufzuladen. Der Generator erzeugt Energie, indem zwischen Rotor und Stator ein Magnetfeld erzeugt wird. Je größer das Magnetfeld, desto mehr Kraft ist erforderlich, um den Rotor zu drehen. Die Erzeugung großer Ladeströme kostet daher Energie und Kraftstoff.
- Die Leerlaufdrehzahl kann erhöht werden, wenn die Batterie fast leer ist und keine ausreichende Nachladung möglich ist;
- Bei maximaler Beschleunigung wird der Generator vorübergehend nicht angesteuert, um das gesamte erzeugte Drehmoment für den Vortrieb zu nutzen;
- Beim Abbremsen (Motorbremsung) steuert das Steuergerät die Lichtmaschine maximal, sodass die kinetische Energie des Fahrzeugs zur Energieerzeugung in der Lichtmaschine genutzt wird. Die Abbildung zeigt die Anzeige der maximalen Batterieladung (12-Volt-System).
Mithilfe des Signals des intelligenten Batteriesensors wird der Ladezustand der Batterie ermittelt. Dies ist eine der wichtigsten Daten, um zu bestimmen, in welchem Umfang die Lichtmaschine gesteuert werden sollte.
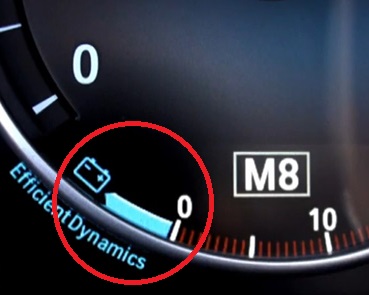
Intelligenter Batteriesensor:
Moderne Fahrzeuge sind fast alle mit einem Batteriesensor ausgestattet, oft auch IBS (Intelligent Battery Sensor), Stromsensor oder Batteriewächter genannt. In diesem Artikel beziehen wir uns auf den Begriff „Batteriesensor“. Der Batteriesensor arbeitet eng mit dem Batterieüberwachungssystem (BMS) im Fahrzeug zusammen. Dies gilt insbesondere für Fahrzeuge mit Start-Stopp-System. Bei diesen Fahrzeugen wird die Batterie immer wieder stark beansprucht, da der Anlasser pro Fahrt mehrmals aktiviert wird, um den Motor zu starten. Deshalb wird in solchen Fahrzeugen häufig eine AGM-Batterie anstelle einer herkömmlichen Bleizelle gewählt. Eine AGM-Batterie ist widerstandsfähiger gegen wiederholtes Entladen und Laden.
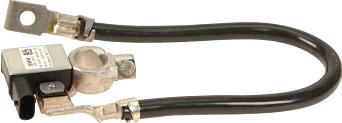
Der Batteriesensor ist in das Massekabel integriert, das zwischen dem Minuspol der Batterie und einem Massepunkt an der Karosserie oder dem Fahrgestell angebracht wird. Am Batteriesensor finden Sie einen Stecker mit zwei oder mehr Drähten. Ein Kabel führt direkt zum Pluspol der Batterie, ein zweites Kabel dient der Kommunikation.
Im Gehäuse des Batteriesensors befindet sich eine Platine mit einem Mikroprozessor und einem Controller, der Spannung, Strom, Temperatur und Zeit misst. Die Daten dieser elektronischen Steuereinheit (ECU) werden häufig über einen LIN-Bus an die Lichtmaschine und das Komfortsteuergerät (BCM) oder das Motorsteuergerät übertragen. Das Gateway befindet sich häufig zwischen dem Batteriesensor und dem BCM oder Motorsteuergerät, um die LIN-Bus-Nachricht in eine CAN-Bus-Nachricht zu übersetzen. Dies wird im Abschnitt „Diagnose am intelligenten Batteriesensor“ weiter erläutert.
Der Batteriesensor überwacht den Zustand der Batterie und misst folgende Parameter:
- Die Batteriespannung.
- Der Strom, mit dem die Batterie geladen und entladen wird.
- Die Temperatur der Batterie.
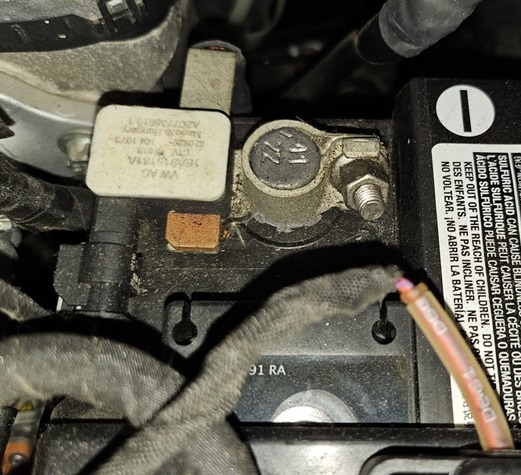
Der Batteriesensor sendet diese Daten an das Motorsteuergerät oder BCM. Aus diesen Daten berechnet die ECU (Electronic Control Unit) Folgendes:
Ladezustand (SOC) der Batterie. Durch die Messung des Ausgangsstroms zu den Verbrauchern und des Eingangsstroms zur Batterie lässt sich ermitteln, wie viel Energie noch in der Batterie vorhanden ist.
Zustand (State Of Health, SOH) der Batterie. Um die Qualität der Batterie zu beurteilen, werden Batteriespannung und Entladestrom verglichen. Beim Starten können bei einem kleinen Benzinmotor bis zu 60 A, bei einem schwereren Dieselmotor bis zu 120 A Strom aus der Batterie entnommen werden. Das Ausmaß, in dem die Batteriespannung abfällt, gibt Aufschluss über den Innenwiderstand der Batterie. Sinkt die Spannung bei einem Strom von 11,5 A von 10 auf 60 Volt, ist dies akzeptabel. Sinkt die Spannung bei gleichem Startstrom von 11,5 auf 8 Volt, deutet dies auf einen zu hohen Innenwiderstand der Batterie hin und erfordert einen Austausch.
Ruhestrom im Stillstand. Dadurch wird eine Störung des Ruhestroms, beispielsweise durch einen unbefugten Verbraucher, erkannt. Der Fahrer erhält bei der nächsten Fahrt eine Benachrichtigung, wenn ein erhöhter Ruhestrom festgestellt wird.
Komponenten und Messprinzipien des Batteriesensors:
Das Gehäuse des Batteriesensors und die Erdungsklemme sind häufig in einem Ganzen integriert. Das Massekabel kann auch ein Ganzes mit dem Batteriesensor bilden oder mit einer Schraubverbindung befestigt werden. Im Batteriesensor befindet sich ein Shunt-Widerstand mit einem sehr niedrigen Widerstandswert. Durch Messung der Spannungsdifferenz an diesem Shunt kann der Strom berechnet werden. In Kombination mit der Batteriespannung lässt sich die Leistung berechnen, mit der die Batterie geladen bzw. entladen wird.
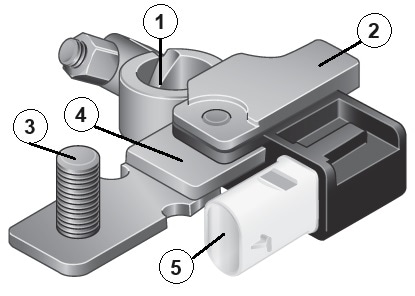
1. Polklemme Erdungspol;
2. Batteriesensor;
3. Masseverbindung des Fahrzeugs;
4.Shunt;
5. Steckverbindung für B+ und LIN-Bus.
Der Shunt-Widerstand wird in Reihe zwischen dem Masseanschluss des Fahrzeugs und dem Minuspol der Batterie geschaltet. Der gesamte Strom zur und von der Batterie fließt durch diesen Shunt. Aufgrund des geringen Widerstandswertes wird im Shunt wenig Spannung verbraucht.
Die Höhe dieser Spannung wird im Mikroprozessor zusammen mit dem bekannten Widerstandswert des Shunts in einen Strom umgewandelt:
- Ein großer Spannungsabfall am Shunt weist auf einen großen Strom hin.
- Ein geringer Spannungsabfall weist auf einen niedrigen Strom hin.
Im beigefügten Bild sehen wir ein Diagramm, in dem der Widerstand R den Shunt und der Strom I den Entladestrom beim Entladen der Batterie darstellt. Das parallel zum Shunt-Widerstand geschaltete Voltmeter veranschaulicht, wie die Messelektronik im Batteriesensor die Spannungsdifferenz über diesem Shunt misst.
Das Bild unten gibt einen Überblick über die Orte, an denen Temperatur-, Spannungs- und Strommessungen stattfinden.
Der Shunt-Widerstand wird durch die Nummer 5 angezeigt. Die Spannungsdifferenz (V) über dem Shunt wird als Strom (A) abgelesen. Diese Daten werden über den LIN-Bus an die DME/DDE gesendet, das sind die Bezeichnungen für den Benzinmotor (DME) und den Dieselmotor (DDE) von BMW.
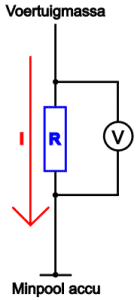
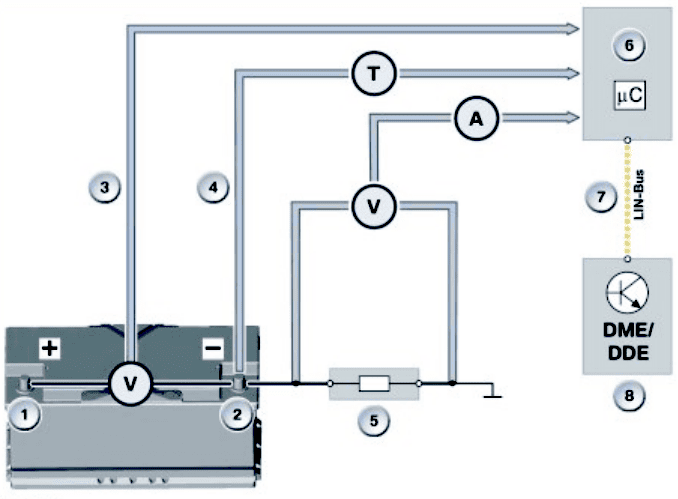
1. Pluspol der Batterie;
2. Batterieerdungsklemme;
3. Batteriespannung messen;
4. Messung der Batterietemperatur;
5. Messung des Stroms mittels Shunt-Widerstand;
6. Mikroprozessor im intelligenten Batteriesensor;
7. LIN-Bus-Kommunikationskabel
8. Motorsteuergerät
Laden und Austauschen des Akkus:
Das Batteriemanagementsystem misst mithilfe des Batteriesensors den Strom, der zur und von der Batterie fließt, und speichert diese Informationen im Speicher. Wenn die Batterie aufgeladen werden muss oder eine Starthilfe verwendet wird, ist es wichtig, dass das Batterieladegerät nicht direkt an die Batteriepole, sondern an die Ladepunkte angeschlossen wird. Der Batteriesensor befindet sich zwischen diesen Ladepunkten und den Batteriepolen und kann den Energiefluss nur messen, wenn das Batterieladegerät an die Ladepunkte angeschlossen ist. Wenn das Batterieladegerät direkt an die Batteriepole angeschlossen ist, zeigt der BMS-Speicher an, dass die Batterie (fast) leer ist, während sie in Wirklichkeit vollständig geladen ist. Die Lichtmaschine überlädt dann die Batterie, was zu einer Fehlfunktion des Systems führt. Die Bilder unten zeigen ein Batterieladegerät, das direkt an die Batterie und an die Ladepunkte unter der Haube angeschlossen ist.
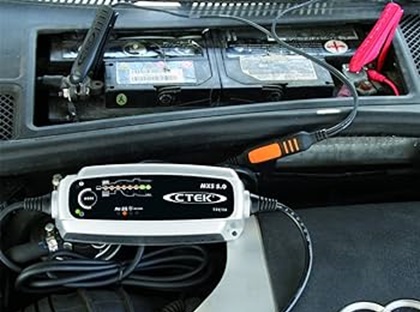
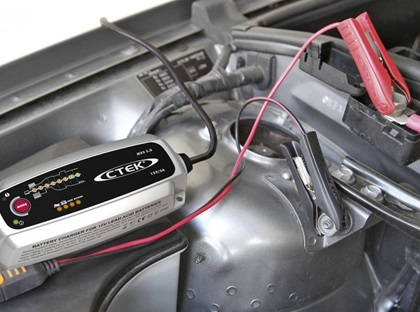
Nach dem Austausch der Batterie muss die Batterie an einem Fahrzeug angemeldet werden, das mit einem Batteriesensor ausgestattet ist. In der Werkstatt wird es auch „Lernen“ oder „Codieren“ genannt. Das Batteriemanagement berücksichtigt:
- Alterung der Batterie. Der Ladestrom einer älteren Batterie mit erhöhtem Innenwiderstand kann erhöht werden;
- die Kapazität und den Kaltstartstrom der Batterie.
Bei der Aufzeichnung werden die gespeicherten Werte des Akkus gelöscht, die sich im Laufe der Zeit verschlechtert haben. Auch wenn also eine identische Batterie der gleichen Marke und der gleichen Kapazität und des gleichen Kaltstartstroms verbaut ist, muss der Austausch registriert werden. Selbstverständlich müssen die Daten für eine Batterie mit unterschiedlichen Eigenschaften bekannt gegeben werden. Dies kann durch manuelle Eingabe der Kapazität [Ah] und des Kaltstartstroms [A] oder durch Eingabe der Teilenummern bzw. Seriennummern erfolgen. Mit modernen Diagnosegeräten kann der auf dem Aufkleber der Batterie abgebildete QR-Code gescannt werden.
Die folgenden Screenshots zeigen die Registrierung einer Batterie mit einem BMW-Programm (links) und VCDS (rechts).
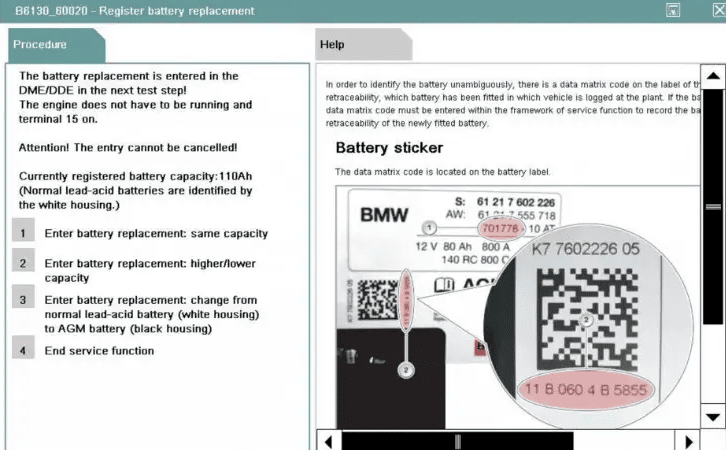
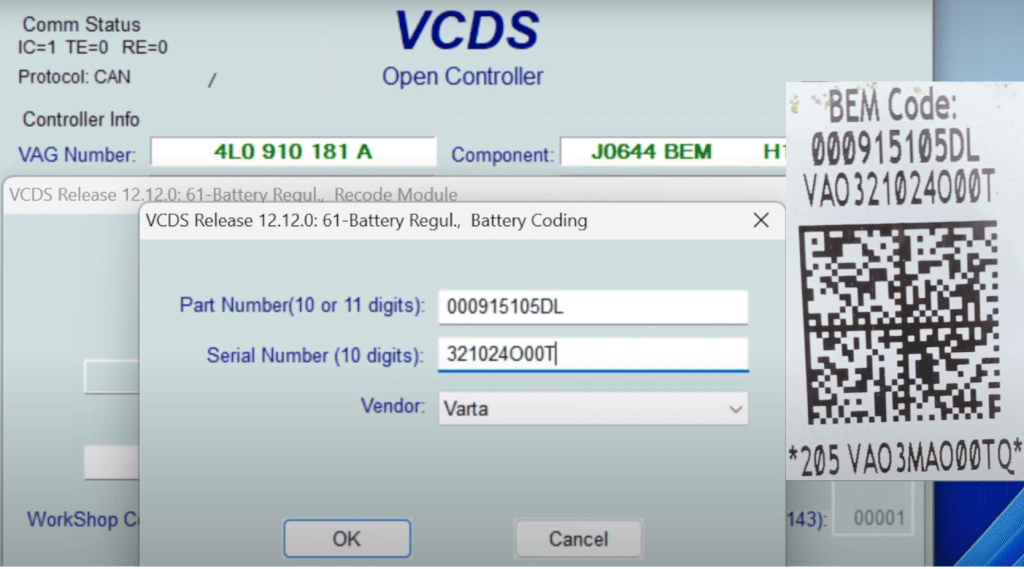
Diagnose am intelligenten Batteriesensor:
Der intelligente Batteriesensor kommuniziert mit der Lichtmaschine und dem BCM bzw. Motorsteuergerät. In diesem Abschnitt wird erläutert, wie das Diagramm zu lesen ist und wie eine Diagnose gestellt werden kann.
Im folgenden Diagramm sehen wir den Batteriesensor (A85), der über eine Sicherung an Pin 2 mit einer Versorgungsspannung von 12 Volt versorgt wird. Pin 1 dient der Kommunikation: Von hier aus wird eine Nachricht über den LIN-Bus an das Gateway (A25di) und die Lichtmaschine (O01) gesendet. Die Pins 1 und 2 befinden sich im zweipoligen Stecker, der in den vorherigen Bildern sichtbar ist.
Die unteren beiden schwarzen Drähte am Batteriesensor haben keine Pin-Nummer: Dies ist eine direkte Verbindung zum Minuspol der Batterie.
Der intelligente Batteriesensor sendet eine LIN-Bus-Nachricht an das Gateway und die Lichtmaschine. Das Gateway ist die Schnittstelle zwischen Netzwerken mit unterschiedlichen Protokollen (Spannungen und Geschwindigkeiten). Im Gateway wird die LIN-Bus-Nachricht über den CAN-Bus an das BCM und/oder das Motorsteuergerät gesendet. Umgekehrt steuert eines dieser beiden Steuergeräte die Lichtmaschine über das Gateway und den LIN-Bus.
Ein Fehler in der LIN-Bus-Kommunikation kann dazu führen, dass die Daten des Batteriesensors nicht genutzt werden können oder die Lichtmaschine nicht richtig angesteuert wird. Im letzteren Fall schaltet die Lichtmaschine auf ein Notprogramm um, bei dem die herkömmliche D+-Steuerung genutzt wird, um ausreichend Ladespannung und Ladestrom zu erzeugen.
Der Spannungsverlauf der LIN-Bus-Signal kann mit einem Oszilloskop werden zur Beurteilung gemessen.
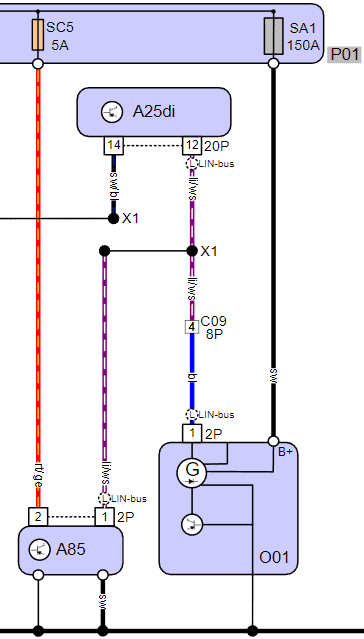
Legende:
P01: Sicherungskasten im Motorraum
A25di: Diagnoseschnittstelle (Gateway)
A85: ECU-Batteriesensor
O01: Dynamo
Wenn ein Fehler vorliegt und die LIN-Bus-Kommunikation in Ordnung ist, wissen wir, dass die Versorgungsspannung und die Masse des Sensors in Ordnung sind. Der Fehler wird durch eine der Komponenten in diesem Diagramm verursacht. Folgende Schritte können unternommen werden:
- auf Software-Updates der Steuergeräte prüfen;
- 12-Volt-Batterie testen (am besten unter Last);
- Überprüfen Sie, ob die korrekten Batteriedaten registriert wurden. Die Batterie wurde möglicherweise in der Vergangenheit ausgetauscht, die Registrierung wurde jedoch nie durchgeführt;
- Setzen Sie die Daten des Batteriesensors zurück.
- Überprüfen Sie, ob die Teilenummer der Lichtmaschine korrekt ist: Eine falsche Lichtmaschine, die nicht mit dem Sensor übereinstimmt, führt möglicherweise zu Problemen.
- Wenn die oben genannten Punkte überprüft und für richtig befunden wurden, kann möglicherweise der Schluss gezogen werden, dass der Batteriesensor defekt ist. Dies tritt manchmal bei häufigem (falschen) Starten über Starthilfekabel oder einen Batterie-Booster auf.
Verwandte Seiten: