Themen:
- Indirekte und direkte Injektion
- Kraftstoffdruckregelung mit indirekter Einspritzung
- Injektionsstrategie Multipoint-Injektion
- Elektromagnetischer Injektor (MPI)
- Piezo-Injektor (DI)
- Einspritzstrategien Direkteinspritzung
- Doppelte Injektion
- Messung von Spannungs- und Stromeigenschaften an einem Mehrpunkt-Injektor
- Einspritzzeitpunkt im Verhältnis zur Kurbelwellenposition
- ECU-Strombegrenzung
- Ermittlung der benötigten Kraftstoffmenge
- VE-Tisch
- AFR-Tabelle
Indirekte und direkte Einspritzung:
Die Arten der Einspritzsysteme eines Ottomotors werden in die indirekte Einspritzung für die Drosselklappe, die indirekte Einspritzung pro Zylinder und die direkte Hochdruckeinspritzung unterteilt. Die Absätze auf dieser Seite erläutern diese verschiedenen Einspritzsysteme.
Indirekte Injektion:
Vor der Drosselklappe befindet sich ein Injektor. Der Kraftstoff wird gegen die Drosselklappe gespritzt und vermischt sich dort mit der vorbeiströmenden Luft. Der größte Nachteil besteht darin, dass es keine genaue Kraftstoffdosierung pro Zylinder gibt; Ein Zylinder bekommt immer etwas mehr oder weniger als der andere. Das System ist daher nicht anpassbar und wird daher im Hinblick auf Umweltanforderungen nicht mehr eingesetzt. Dieses System wird auch Zentraleinspritzung (Monopoint) genannt.
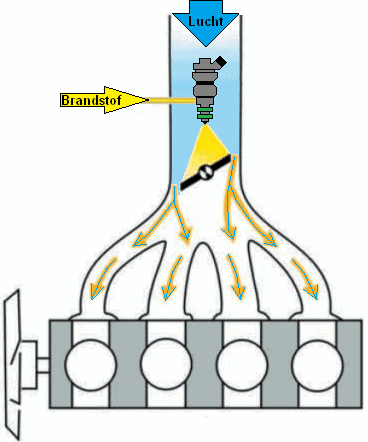
Indirekte Injektion:
Jeder Zylinder verfügt über einen eigenen Injektor. Der Injektor spritzt Kraftstoff in das Einlassventil. Die vorbeiströmende Luft sorgt auch bei diesem System für eine Durchmischung, bevor das Luft-Kraftstoff-Gemisch in den Brennraum gelangt. Der Vorteil gegenüber der indirekten Einspritzung besteht darin, dass die Kraftstoffmenge viel genauer gesteuert werden kann. Dieses System wird auch MPI (MultiPoint Injection) oder PFI (Port Fuel Injection) genannt.
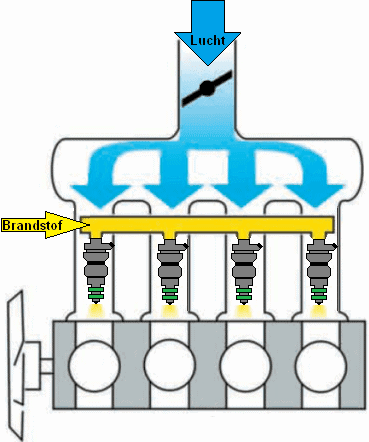
Direkte Injektion:
Die Einspritzdüsen für DI (Direkteinspritzung) oder DISI (Direkteinspritzung mit Funkenzündung) befinden sich neben der Zündkerze oben im Brennraum. Durch diesen Injektor wird der Kraftstoff während des Ansaugtakts mit einem hohen Druck von etwa 200 bar eingespritzt. Die großen Vorteile dieses Systems bestehen darin, dass die Kraftstoffmenge noch genauer eingestellt werden kann, dass während des Ansaugtakts mehrmals eingespritzt werden kann und dass das Luft-Kraftstoff-Gemisch kühler ist. Dies ermöglicht es den Herstellern, das Verdichtungsverhältnis des Motors zu erhöhen. Der Injektor kann als Piezo- oder Magnetspuleninjektor ausgebildet sein.
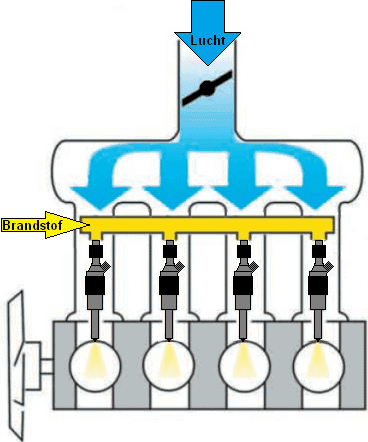
DI erfordert höhere Einspritzdrücke als MPI/PFI, da die Einspritzung während des Kompressionshubs erfolgt; Der Kraftstoff muss ausreichend zerstäubt sein, während die Luft im Zylinder komprimiert wird. Deshalb verfügt DI über eine separate Hochdruckpumpe. Die Hochdruckpumpe baut im Kraftstoffkanal Kraftstoffdruck auf. An diesem Kraftstoffkanal sind die Einspritzdüsen mit Rohren befestigt. Sobald das Motormanagement ein Signal an den Injektor sendet, öffnet und schließt dieser zum gewünschten Zeitpunkt.
Zu den Vorteilen von DI im Vergleich zu PFI gehören:
- Genauere Injektion;
- Mehrfachinjektionen möglich;
- Die Einspritzzeit kann angepasst werden;
- Höherer effektiver Druck über dem Kolben möglich (dadurch Downsizing mit höherem Verdichtungsverhältnis möglich);
- Geringerer Kraftstoffverbrauch, geringere CO2-Emissionen.
Zu den Nachteilen zählen:
- Höhere Systemkosten durch Hochdruck-Kraftstoffpumpe, fortschrittliche Einspritzdüsen, komplexerer Zylinderkopf;
- Rußemissionen erhöht (PM-Emissionen);
- Die direkte Einspritzung in den Brennraum sorgt für Kühlung anstelle der für die Kraftstoffverdampfung erforderlichen Wärme.
Ein Doppeleinspritzmotor nutzt die Vorteile beider Systeme. Abhängig von den Betriebsbedingungen kann zwischen direkter und indirekter Einspritzung umgeschaltet werden. Die Funktionsweise und Anwendung der Doppelinjektion wird im gleichnamigen Absatz auf dieser Seite beschrieben.
Kraftstoffdruckregelung mit indirekter Einspritzung:
Ein konstanter Kraftstoffdruck ist eine Voraussetzung für die genaue Steuerung der Kraftstoffeinspritzung. Oben am Injektor liegt der Kraftstoffdruck (Raildruck) und unten der Saugrohrdruck an. Der Druck im Ansaugkrümmer variiert je nach Motorlast und hat ohne Druckregler Einfluss auf die Kraftstoffdruckdifferenz und damit auf die Einspritzmenge. Aus diesem Grund verwenden wir einen Kraftstoffdruckregler. In diesem Abschnitt werden wir uns mit der Funktionsweise und dem Zweck dieses Controllers befassen.
Das Bild unten zeigt die Komponenten eines Benzinmotors mit indirekter Einspritzung und Mehrpunkteinspritzung. Wir betrachten den Kraftstofffluss von der Pumpe im Tank zum Injektor.
Wenn das Steuergerät das Kraftstoffpumpenrelais steuert, läuft die Pumpe. Die Pumpe saugt den Kraftstoff aus dem tiefstmöglichen Teil des Kraftstofftanks an und zwingt den Kraftstoff zum Kraftstofffilter. Schmutzpartikel im Kraftstoff verbleiben im Filtermaterial. Der gefilterte Kraftstoff gelangt dann in den Kraftstoffkanal. In den meisten Fällen ist der Kraftstoffkanal direkt am Injektoreingang montiert.
Im Kraftstoffkanal herrscht ein konstanter Druck: Erst wenn der Injektor elektrisch vom Steuergerät gesteuert wird (siehe blaues Kabel), öffnet sich der Injektor und der Kraftstoff wird in den Ansaugkrümmer auf das geöffnete Einlassventil eingespritzt. Die eingespritzte Kraftstoffmenge hängt ab von:
- die Einspritzzeit (wird vom Steuergerät durch Verlängern oder Verkürzen des Einspritzsignals bestimmt);
- der Kraftstoffdruck (bei einer Einspritzzeit von 2 Millisekunden spritzt der Injektor mehr ein, als das Steuergerät berechnet hat, wenn der Kraftstoffdruck zu hoch ist).
Der Kraftstoffdruck im Kraftstoffkanal (auch Raildruck genannt) wird abhängig von der Motorlast angepasst. Wir werden dies im nächsten Abschnitt ausführlicher besprechen.
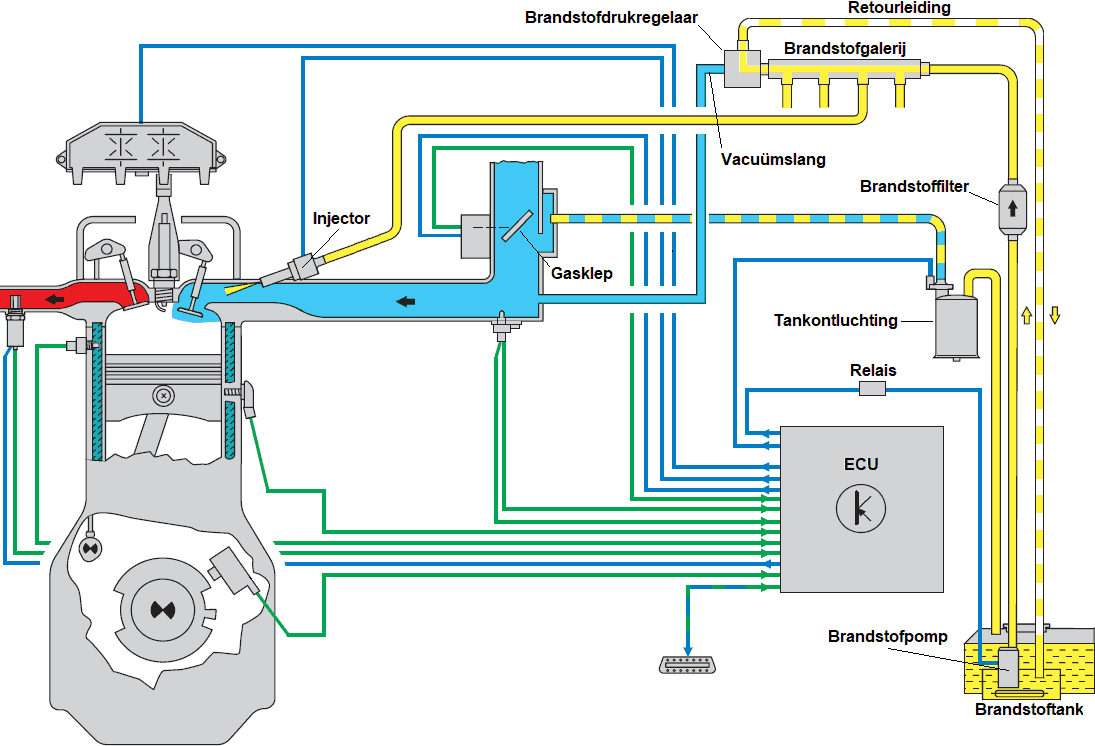
Ohne Verwendung eines Druckreglers ergeben sich folgende Situationen:
- Im Leerlauf würde der höhere Unterdruck (also der niedrige Luftdruck) im Ansaugkrümmer einen unerwünscht höheren Kraftstoffdruck erzeugen;
- Beim Beschleunigen entsteht weniger oder kaum noch Unterdruck (Volllast) und der Kraftstoffdruck würde sinken, während ein höherer Kraftstoffdruck gewünscht wird.
Der Kraftstoffdruckregler erhöht oder verringert den Benzindruck im Kraftstoffkanal basierend auf dem Luftdruck im Ansaugkrümmer. Den Kraftstoffdruckregler können wir als dynamisches Ventil betrachten, das eine Öffnung zwischen der Vorlaufleitung der Kraftstoffpumpe und der Rücklaufleitung ermöglicht.
Rechts sehen wir ein Kraftstoffdruckdiagramm, bei dem die relative Druckdifferenz in allen Zuständen (Leerlauf, Teillast und Volllast) dank des Druckreglers 4 bar beträgt.
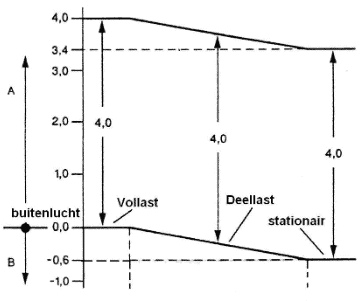
Die nachstehende Erläuterung bezieht sich auf die Bilder, die den Druckregler in der Situation ohne und mit Vakuum zeigen. Rechts ist ein Kraftstoffdruckregler von Bosch zu sehen, der bei mehreren Automobilherstellern im Einsatz ist.
Ohne Vakuum (links):
Im Ruhezustand ist der Druckregler geschlossen: Die Feder drückt die Membran zu und verhindert so, dass der zugeführte Kraftstoff in die Rücklaufleitung gelangt.
Mit Vakuum (Mitte):
Wenn der Druck über der Membran abnimmt, drückt der Kraftstoffdruck auf der Versorgungsseite die Membran gegen die Federkraft nach oben. Es entsteht eine Öffnung, durch die der zugeführte Kraftstoff über die Rücklaufleitung zum Kraftstofftank abgelassen wird.
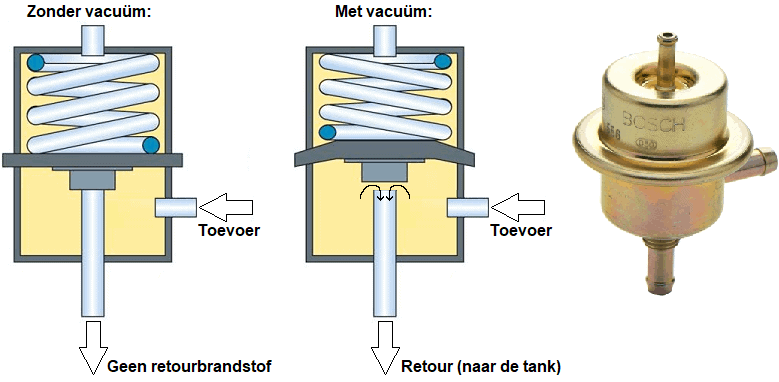
Injektionsstrategie Multipoint-Injektion:
Bei der (indirekten) Mehrpunktinjektion kommen drei unterschiedliche Injektionsmethoden zum Einsatz:
- Gleichzeitig: Die Einspritzung erfolgt gleichzeitig an allen Zylindern.
- Gruppe: Die Injektion erfolgt pro Gruppe; Es wird zwischen einer oder mehreren Gruppen unterschieden.
- Sequentiell: Jeder Injektor wird separat gesteuert und hat daher seinen eigenen Einspritzzeitpunkt.
Das Motormanagementsystem in der Abbildung unten zeigt eine Gruppeneinspritzung. Die Injektoren der Zylinder 1 und 2 verfügen über eine gemeinsame Stromversorgung (rot) und sind beide gleichzeitig mit Masse verbunden (grün). Die Einspritzdüsen der Zylinder 3 und 4 sind gleich, werden jedoch getrennt von den Zylindern 1 und 2 angesteuert.
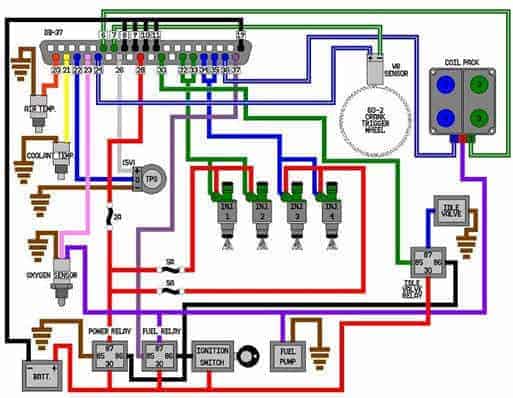
Elektromagnetischer Injektor (MPI):
Der elektromagnetische Injektor wird bei vielen Benzinmotoren eingesetzt, die keine (direkte) Hochdruckeinspritzung mit separater Hochdruckpumpe nutzen. Der Kraftstoff steht am Eingang des Injektors unter einem konstanten Druck von 1 bar. Der Kraftstoffdruck wird von der Kraftstoffpumpe im Tank bereitgestellt. Bei der Mehrpunkteinspritzung (dies wird später auf der Seite beschrieben) verfügt jeder Zylinder über eine eigene Einspritzdüse. Dieser Injektor ist im Ansaugrohr montiert und spritzt Kraftstoff mit einem Druck von bis zu 6 bar ein, bevor das Ventil öffnet. Sobald sich das Einlassventil zu öffnen beginnt, hat der Kraftstoff dann genügend Zeit, sich mit dem gesamten in den Zylinder einströmenden Sauerstoff (in der Abbildung durch den dunkelblauen Pfeil gekennzeichnet) zu vermischen.
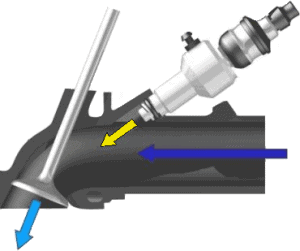
Das Motorsteuergerät berücksichtigt die Position der Kurbelwelle, um den Einspritzzeitpunkt und den Zündzeitpunkt zu regeln. Basierend auf mehreren Faktoren (Motor- und Umgebungstemperatur, Last, Geschwindigkeit usw.) gibt es zum richtigen Zeitpunkt ein Signal an den Injektor zum Öffnen. Der Stecker dieses Injektors enthält zwei Drähte. Ein Draht hat ein konstantes Plus von etwa 14 Volt. Das andere Kabel ist über das Steuergerät mit Masse verbunden, damit Strom durch die Einspritzspule fließen kann. Wenn die Spule ausreichend geladen ist, öffnet sich die Einspritznadel gegen die Federkraft. Wenn die Steuerung stoppt, drückt eine Feder die Einspritznadel zurück . Dann wird die Kraftstoffzufuhr abgeschaltet. Wenn die Steuerung stoppt, ist die Spule noch elektrisch geladen. Die Energie in der Spule bildet eine Induktionsspitze, die auf dem Oszilloskop beobachtet werden kann. Die Induktionsspannung beträgt kurzzeitig etwa 60 Volt.
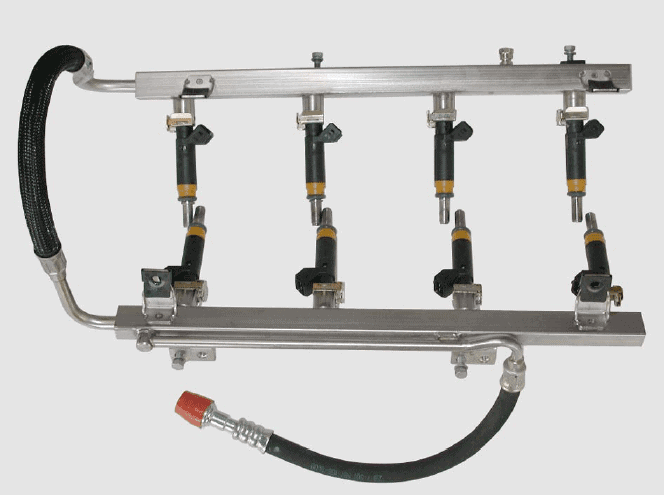
Diese Einspritzdüsen werden über die Kraftstoffverteilerleitung (auch Kraftstoffgalerie genannt) mit Kraftstoff versorgt. Die Druckerhöhungspumpe im Kraftstofftank sorgt für den Druck im Kraftstoffverteiler. Der Kraftstoffdruck im Rail ist konstant (ca. 4 bar). Da der Druck so niedrig ist, werden die Einspritzdüsen mit einer Sicherungsklammer und einem O-Ring zur Abdichtung befestigt. Besonders bei älteren Fahrzeugen, bei denen das System demontiert wird, ist es sinnvoll, die O-Ringe vor dem Einbau auszutauschen.
Das Gehäuse eines Injektors besteht üblicherweise aus Kunststoff. An der Oberseite des Gehäuses finden wir den Steckanschluss, der intern mit der Spule verbunden ist. Oben befindet sich ein Gummi-O-Ring, über den die Kraftstoffgalerie gleitet. Unten finden sich O-Ringe oder Teflondichtringe. Ein O-Ring wird hauptsächlich in MPI-Injektoren mit Niederdruckeinspritzung verwendet, während Teflonringe in Motoren mit Hochdruckeinspritzung, wie beispielsweise einem FSI-Motor, zu finden sind.
Die Spule ist um den Kern des Injektors gewickelt. Im beigefügten Bild ist die Spule rot hervorgehoben. In der Mitte des Injektors, ebenfalls innerhalb der Spule, befindet sich ein Kolben. Dieser Kolben verfügt über eine mechanische Kopplung mit der Nadel. Über dem Kolben befindet sich eine Feder, die den Kolben und damit die Nadel in ihrem Sitz hält und die Injektionsöffnung verschließt.
Im Ruhezustand beträgt die Spannung an beiden Anschlüssen der Spule etwa 14 Volt gegenüber Masse. Um den Injektor vorzubereiten, versorgt das Motorsteuergerät eine Seite der Spule mit Masse, während die andere Seite positive Spannung erhält. An diesem Punkt beginnt Strom durch die Spule zu fließen, was zur Bildung eines Magnetfelds führt. Dieses Magnetfeld zieht den Kolben und damit die Injektionsnadel nach oben.
Wenn die Einspritzung gestoppt werden muss, trennt das Steuergerät die Masse, wodurch das Magnetfeld verschwindet. Die Feder drückt den Kolben wieder nach unten, wodurch die Nadel die Kraftstoffzufuhr zur Brennkammer unterbricht.
Der Injektor hat normalerweise mehrere Öffnungen. Diese Öffnungen sind sehr klein, so dass der Kraftstoff vom Injektor als Nebel in den Brennraum eingespritzt wird. Je feiner der Nebel ist, desto leichter verdunstet er.
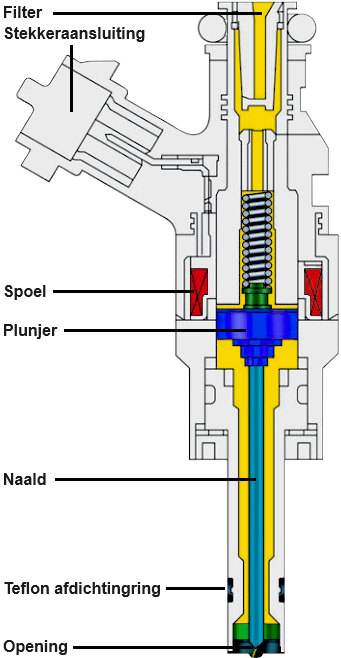
Piezo-Injektor (DI):
Piezo-Injektoren können sowohl in Benzin- als auch in Dieselmotoren eingesetzt werden. BMW war die erste Marke, die die Piezo-Technologie in Benzinmotoren einsetzte, hat bei den neueren Motoren jedoch damit aufgehört.
Zur Hochdruckeinspritzung gehört ein Piezoinjektor. Eine separate Hochdruckpumpe sorgt für Druck auf das Kraftstoffverteilerrohr. Dieser Kraftstoffverteiler verteilt den Kraftstoff auf alle Einspritzdüsen (siehe Bild). Aufgrund der sehr hohen Drücke werden Aluminiumrohre mit Verschraubungen verwendet. Die Verschraubungen (die auf das Rohr und die Injektoren aufgeschraubt werden) müssen immer mit der richtigen Kraft angezogen werden. Dies ist im Reparaturhandbuch des jeweiligen Motors angegeben.
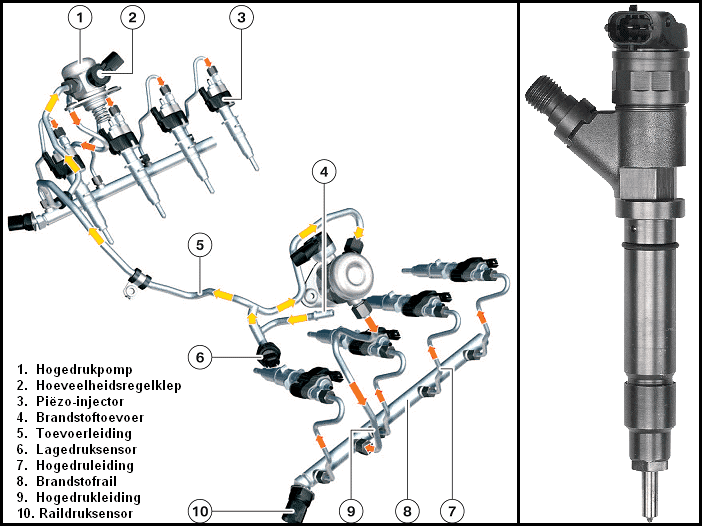
Das Piezoelement im Injektor hat die Eigenschaft, seine Länge zu ändern, wenn eine positive oder negative Spannung an es angelegt wird. Dies wird mit dem Injektor verwendet. Sobald das Motorsteuergerät eine Steuerspannung von ca. 100 bis 150 Volt liefert, dehnt sich das Piezoelement um ca. 0,03 mm aus. Diese Längenänderung reicht aus, um eine Verbindung zwischen Hoch- und Niederdruckkammer herzustellen. Die Injektion beginnt sofort. Das Piezoelement kann innerhalb einer Tausendstelsekunde ein- und ausgeschaltet werden. Zusammen mit dem sehr hohen Injektionsdruck von bis zu 2000 bar ermöglicht dies eine sehr schnelle und präzise Injektion. Diese Geschwindigkeiten ermöglichen auch die Durchführung mehrerer Injektionen nacheinander.
Mehrfacheinspritzungen während des Ansaugtakts haben den Vorteil, dass die Luft-Kraftstoff-Mischung optimal ist. Durch den hohen Druck werden die Kraftstofftröpfchen feinst zerstäubt, sodass sie sich noch besser mit der Luft vermischen. Während des Ansaugtaktes können bis zu 8 Einspritzungen erfolgen. Dies hat positive Auswirkungen auf Kraftstoffverbrauch, Leistung und Abgasemissionen.
Einspritzstrategien Direkteinspritzung:
Bei der Einspritzstrategie der Direkteinspritzung gibt es verschiedene Varianten: wandgeführt, luftgeführt und strahlgeführt (siehe Bilder unten). In diesen Situationen kommt es zu einem geschichteten Verbrennungsprozess. Dies gilt nicht in allen Betriebszuständen.
- Wandgeführt: Der Kolben leitet die Kraftstoffwolke zur Zündkerze. Der Abstand zwischen Zündkerze und Einspritzdüse ist groß. Wird auf GDI- und HPI-Motoren angewendet.
- Luftgeführt: Die Luftbewegung bringt die Kraftstoffwolke zur Zündkerze. Der Abstand zwischen Zündkerze und Einspritzdüse ist groß. Wird auf FSI- und JTS-Motoren angewendet.
- Strahlgeführt: Die Zündkerze befindet sich am Rand der Kraftstoffwolke. Der Abstand zwischen Einspritzdüse und Zündkerze ist gering. Wird auf BMW-Motoren angewendet.
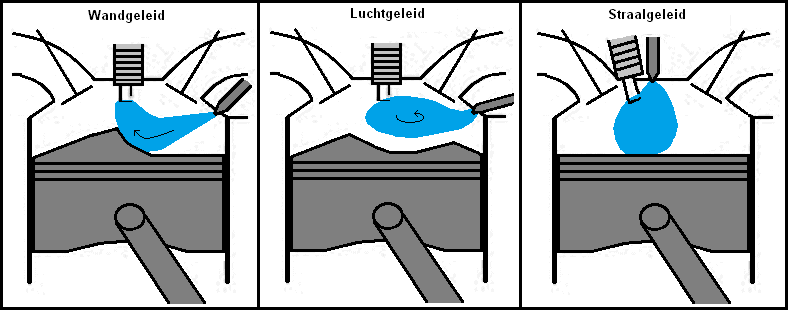
Wie bereits erwähnt, verfügen Benzinmotoren mit Direkteinspritzung nicht in allen Betriebszuständen über eine geschichtete Verbrennung. Motoren mit strahlgeführter Direkteinspritzung können phasenweise im Teillastbetrieb laufen. Bei einem geschichteten Verbrennungsprozess handelt es sich um verschiedene Luftschichten im Brennraum. In der Nähe der Zündkerze beträgt der Lambda-Wert 1. Weiter entfernt wird der Lambda-Wert höher (magerer, also mehr Luft). Diese Luft bildet eine isolierende Luftschicht. Bei einem Schichtverfahren ist der Einspritzzeitpunkt später als beim Homogenverfahren. Mit Hilfe einer Schichteinspritzung kann die Drosselklappe vollständig geöffnet werden, so dass sie die Luft weniger drosselt. Da die angesaugte Luft entfettet wird, stößt sie auf weniger Widerstand und kann daher leichter angesaugt werden. Da der Lambdawert im Brennraum bei geschichteter Einspritzung aufgrund der isolierenden Luftschicht kleiner als 1 ist, führt dies zu keinen Problemen bei der Verbrennung. Während des Schichtprozesses sinkt der Kraftstoffverbrauch.
Bei einem homogenen Gemisch beträgt der Lambdawert überall 1. Das bedeutet, dass bei einem Benzinmotor das Verhältnis von Luft und Kraftstoff 14,7:1 beträgt (14,7 kg Luft auf 1 kg Kraftstoff). Jeder Motor kann homogen laufen. Erfolgt eine Anreicherung, sinkt der Lambdawert, wird das Gemisch abgemagert, erhöht sich der Lambdawert:
<1 = Reich
>1 = Schlecht
Ein Motor schwankt ständig zwischen fett und mager, damit der Katalysator ordnungsgemäß funktioniert. Der Lambdasonde sendet die Daten an das Motormanagementsystem.
Bei Volllast läuft der Motor immer homogen. Dadurch ergibt sich ein höheres Drehmoment als bei einem Schichtverfahren. Läuft der Motor homogen, wird der Kraftstoff früh eingespritzt. Auch beim Anfahren aus dem Stand läuft der Motor homogen. Es ergibt sich dann ein höheres Anlaufmoment, als wenn der Motor geschichtet laufen würde.
Die folgende Kennlinie zeigt die Betriebssituationen bei unterschiedlichen Geschwindigkeiten im Vergleich zum Verbrennungsdruck, mit und ohne Einsatz von AGR.
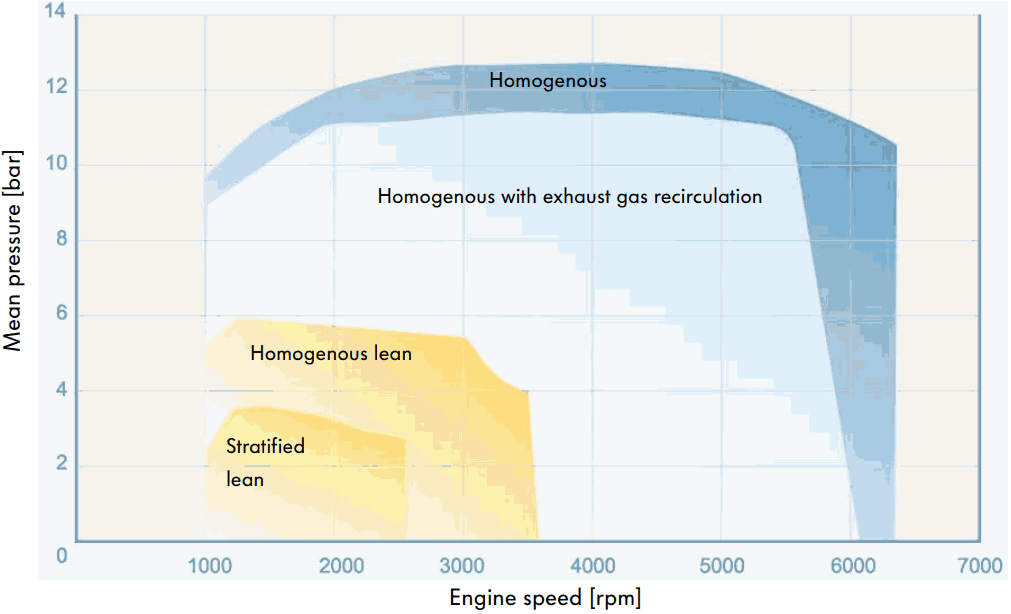
Doppeleinspritzung:
Um die aktuellen Abgasnormen zu erfüllen, setzt der VAG-Konzern Benzinmotoren mit Doppeleinspritzung ein. Bei Motoren mit Doppeleinspritzung gibt es zwei Kraftstoffeinspritzsysteme: ein Niederdrucksystem und ein Hochdrucksystem.
- Das Niederdrucksystem enthält MPI-Injektoren, die seit Jahrzehnten im Einsatz sind. Die MPI-Injektoren sind im Saugrohr montiert und spritzen mit einem Druck von 4 bis 5 bar in das Einlassventil ein;
- Das Hochdrucksystem enthält Hochdruckinjektoren, die mit einem Einspritzdruck von maximal 150 bis 200 bar direkt in den Brennraum einspritzen.
Das Motormanagementsystem bestimmt, welcher Einspritzer gesteuert wird.
Das folgende Bild zeigt einen Querschnitt des Zylinderkopfes mit den beiden Kraftstoffsystemen.
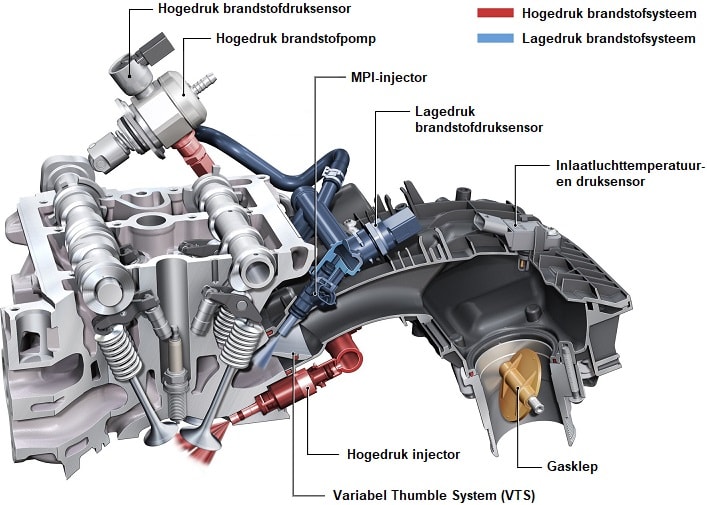
Die MPI-Einspritzung sorgt für eine bessere Vermischung von Luft und Kraftstoff. Die Direkteinspritzer kommen im Leerlauf und bei Volllast zum Einsatz. Durch die Direkteinspritzung wird eine bessere Kühlung erreicht, was ein höheres Verdichtungsverhältnis ermöglicht. Allerdings ist die Vermischung von Luft und Kraftstoff nicht optimal. Dies verursacht mehr Rußemissionen. Aus diesem Grund sind Motoren mit Direkteinspritzung heutzutage mit einem Partikelfilter ausgestattet. Bei der Doppeleinspritzung ist das kein Problem. Das „Variable Thumble System“, abgekürzt VTS, ist eine Version eines variablen Ansaugkrümmers, der für einen besseren Luftstrom sorgt. Der „Thumble“ ist ein Luftstrom, der beim Eintritt in den Zylinder einen Wirbel erzeugt. Der Luftwirbel ist notwendig, um den Kraftstoff aus dem MPI-Injektor richtig mit der Luft zu vermischen.
Die Doppeleinspritzung in Kombination mit VTS sorgt für bessere Abgasemissionen. Ein zusätzlicher Vorteil besteht darin, dass das Einlassventil durch den MPI-Injektor gereinigt wird. Motoren mit Direkteinspritzung leiden häufig unter einem verschmutzten Ansaugtrakt (Ansaugkrümmer und Einlassventile), was zu Problemen wie einer eingeschränkten Luftzufuhr führt. Im Extremfall verstopft der Ansaugtrakt so sehr, dass das Einlassventil nicht mehr richtig am Zylinderkopf schließen kann und schließlich verbrennt, weil es die Wärme nicht ausreichend abführen kann.
Es ist bekannt, dass die gleichen Motoren in den USA nur mit Direkteinspritzung ausgestattet sind, während die VAG-Motoren mit Doppeleinspritzung ausgestattet sind. Der Ansaugkrümmer ist verschlossen. Dies liegt daran, dass zum Zeitpunkt des Verfassens dieses Artikels die Umweltauflagen in Europa strenger sind als in den USA und der Hersteller aus Kostengründen keine Motoren mit solch teuren Systemen für Märkte anbietet, in denen die Emissionsstandards weniger streng sind.
Spannungs- und Stromeigenschaften an einem Mehrpunktinjektor messen:
Das Oszilloskop kann nur Spannung messen. Messleitungen können über die elektrischen Komponenten hinweg parallel geschaltet werden. Eine Strommessung in Reihe ist nicht möglich. Der Strom kann mit einer induktiven Stromzange gemessen werden. Die Hall-Sensoren in der Stromzange messen das Magnetfeld und wandeln es in eine Spannung um. Die Spannung kann mit dem Oszilloskop gemessen werden. In diesem Fall beträgt der Umrechnungsfaktor 10 mV pro Ampere; Pro 0,010 Volt, die die Stromzange überträgt, kann dies in 1 A umgerechnet werden.
Das folgende Oszilloskopbild zeigt das Spannungs- und Stromprofil eines elektromagnetischen Injektors.
- Rot: Spannungsgradient;
- Gelb: aktueller Fluss.
Im Ruhezustand beträgt die Spannung 14 Volt. Es besteht nun kein Spannungsunterschied am Stecker, es fließt also kein Strom. Das Steuergerät verbindet einen Draht mit Masse, um den Einspritzer zu steuern. Der Spannungsunterschied bewirkt, dass Strom durch die Einspritzspule fließt.
Die gelbe Linie zeigt den Stromfluss an: Sobald die Spannung auf 0 Volt sinkt, beginnt der Stromaufbau. Das Laden der Spule dauert einige Zeit. Der Strom steigt nicht weiter als etwa 0,9 A. In der Mitte des Stromaufbaus sehen wir eine Krümmung der Leitung: Dies ist der Moment, in dem sich ausreichend Magnetismus aufgebaut hat, um die Nadel aus ihrem Sitz zu heben. Der Injektor beginnt mit der Injektion.
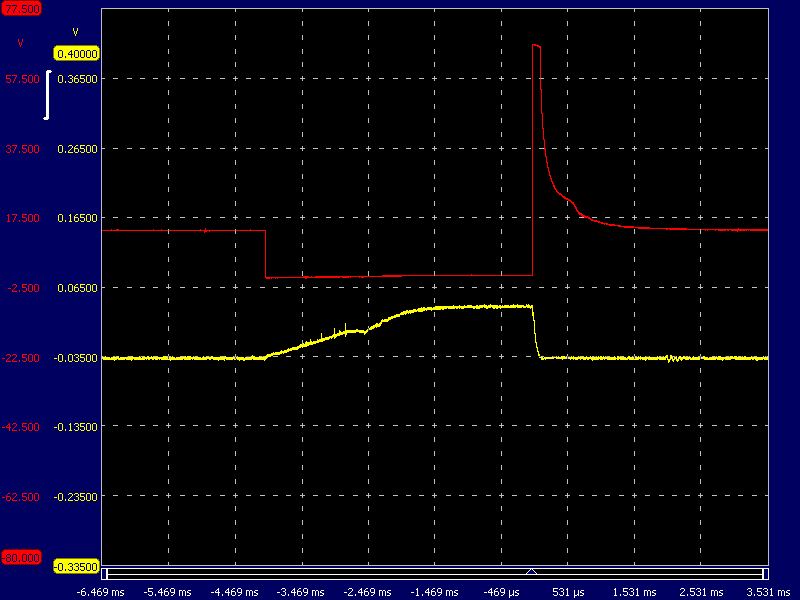
Das Steuergerät unterbricht die Masseverbindung, um die Steuerung zu stoppen. Die Restenergie in der Spule sorgt für eine Induktionsspannung von ca. 60 Volt. Der Injektor stoppt die Injektion, da die Feder die Nadel in ihren Sitz zurückdrückt. Dies ist im Bild des Oszilloskops an der Erhebung im Spannungssignal zu erkennen.
Wenn der Motor unregelmäßig läuft und es zu Zylinderaussetzern kommt, kann das verschiedene Ursachen haben:
- Kein oder schlechter Funke aufgrund defekter Zündkerze, Zündkerzenkabel oder Zündspule;
- Einschränkung der Kraftstoffzufuhr aufgrund eines verstopften Kraftstofffilters, eines defekten Druckreglers, eines Problems mit der Kraftstoffpumpe oder dem Einspritzventil;
- Kompressionsverlust aufgrund eines Problems mit den Kolbenringen, defekter Kopfdichtung oder Ventildichtungen.
Bei einer Diagnose kann mit einem Scope überprüft werden, ob die Injektoren noch ordnungsgemäß funktionieren. Am Anfang dieses Abschnitts wurden Messungen gezeigt, bei denen keine Störung auftrat. Blaue Linien zeigen beispielhaft, wie der Spannungs- und Stromverlauf eines defekten Injektors aussehen würde.
Für den Fall, dass die Ansteuerung des Injektors korrekt ist, aber im Spannungs- und Strombild keine Knicke sichtbar sind, kann daraus geschlossen werden, dass sich die Injektornadel nicht bewegt. Da die Einspritzdüse eines Zylinders nicht ordnungsgemäß funktioniert und die anderen Einspritzdüsen jedoch ordnungsgemäß funktionieren, können die Bilder verschiedener Einspritzdüsen problemlos miteinander verglichen werden.
Wenn Sie leicht auf den Injektor klopfen, kann sich die Injektornadel lösen. In diesem Fall läuft der Motor sofort ruhiger und die Knicke sind in den Zielfernrohrbildern wieder sichtbar. Dies garantiert jedoch keine dauerhafte Lösung; Es besteht eine gute Chance, dass das Problem innerhalb kurzer Zeit erneut auftritt. Der Austausch des entsprechenden Injektors ist erforderlich.
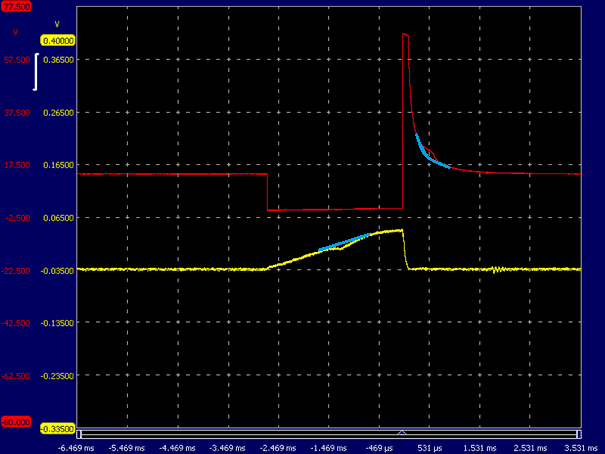
Die Nadel im Injektor öffnet sich erst, wenn die Spule ausreichend geladen ist. Dies hat zur Folge, dass der Einspritzer nicht sofort Kraftstoff einspritzt, wenn das Steuergerät mit der Steuerung beginnt. Nach Abschluss der Betätigung drückt die Feder die Düsennadel auf ihren Sitz. Auch das braucht Zeit. Die Steuerzeit ist in der Regel nicht gleich der Einspritzzeit. Das folgende Bild zeigt den Spannungs- und Stromverlauf desselben Injektors wie oben, jedoch mit erhöhter Geschwindigkeit.
- Beginn der Steuerung: Das Steuergerät schaltet die Steuerleitung auf Masse. Strom fließt durch die Einspritzspule, um sie zu öffnen. Der Knick im Strömungsverlauf zeigt den Zeitpunkt an, an dem sich die Düsennadel öffnet. Der Strom steigt dann etwas an und bleibt daher konstant. Die Einspritznadel bleibt geöffnet.
- Ende der Regelung: Wie bereits beschrieben, erkennen wir den Moment, in dem die Düsennadel geschlossen ist, an der Erhebung im Spannungsbild.
Die Ansteuerung dauert 4 ms, die tatsächliche Einspritzzeit beträgt jedoch 3 ms. Den Unterschied zwischen diesen bezeichnen wir als „Verzögerung“, ins Niederländische übersetzt als „Verzögerung“. Das Steuergerät steuert den Injektor daher 4 ms lang, damit er 3 ms lang einspritzen kann.
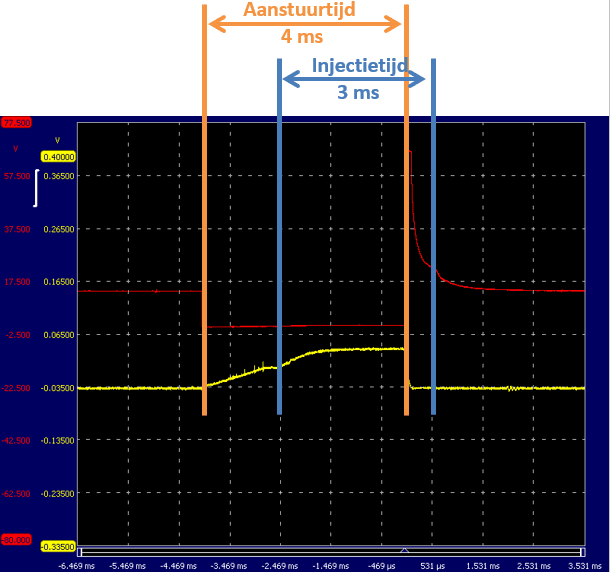
Einspritzzeitpunkt im Verhältnis zur Kurbelwellenposition:
Der Einspritzzeitpunkt kann mit einem Oszilloskop betrachtet werden. Kanal A (rot) befindet sich am Erdungskabel des Einspritzventils und Kanal B (gelb) befindet sich am Einspritzventilkabel Kurbelwellenpositionssensor in Verbindung gebracht. Während der Motor läuft, können wir dieses Oszilloskopbild verwenden, um den Einspritzzeitpunkt und die Einspritzzeit zu bestimmen.
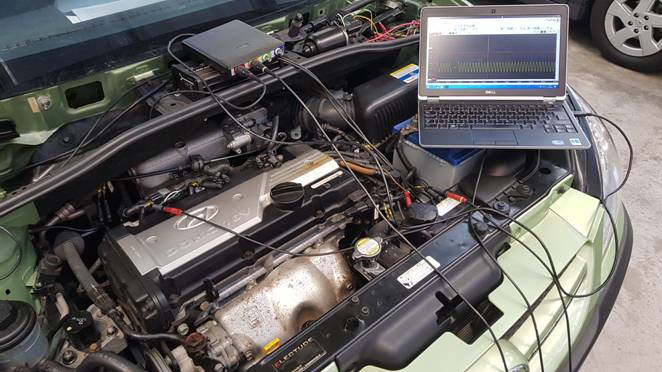
Das Scope-Bild wurde im Leerlauf aufgenommen. Das rote Spannungsbild zeigt das Öffnen und Schließen des Injektors (siehe Abschnitt: Spannungs- und Stromeigenschaften an einem Mehrpunktinjektor messen). Zum Zeitpunkt -2,860 ms beginnt die Regelung; die Spannung sinkt von 12 Volt auf 0 Volt. Dies ist der Punkt, an dem die Einspritzspule geerdet ist und Strom fließt. Die Injektorsteuerung endet, wenn die rote Linie wieder ansteigt. Aufgrund der in der Spule gespeicherten Energie entsteht eine Induktionsspannung von mehr als 60 Volt. Dann sinkt die Spannung allmählich auf 12 Volt; hier wird der Injektor wieder abgeschaltet.
Die rote Wechselspannung kommt von der Induktivität Kurbelwellenpositionssensor. Jedes Mal, wenn sich die Zähne des Impulsrades am Kurbelwellensensor vorbeidrehen, entsteht eine sinusförmige Wechselspannung. Das Impulsrad enthält 60 Zähne, davon sind 2 abgeschliffen. Die beiden abgeschliffenen Zähne bilden den Referenzpunkt, an dem das Motormanagement erkennt, dass sich die Kolben der Zylinder 1 und 4 zwischen 90⁰ und 120⁰ vor OT (oberer Totpunkt) befinden. Nachdem der fehlende Zahn erkannt wurde, hat das Motormanagement (ggf. in Kombination mit dem Nockenwellensensor), um den richtigen Einspritz- und Zündzeitpunkt zu ermitteln und den Einspritzer und die Zündspule zu aktivieren, bevor der Kolben den oberen Totpunkt erreicht.
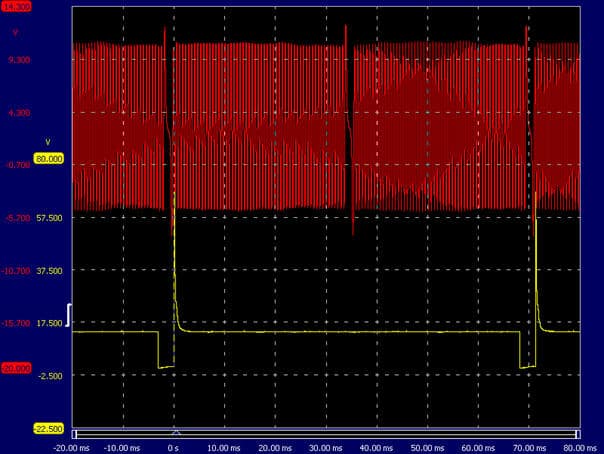
Das Scope-Bild zeigt den Zeitpunkt, zu dem die Injektion beginnt; Die Einspritzung beginnt mit dem vierten Impuls vom Kurbelwellensensor. Unter der Annahme, dass 60 – 2 Zähne vorhanden sind, erfolgt nach jeder 6⁰ Umdrehung der Kurbelwelle (360⁰ für 1 Umdrehung / 60 Zähne) die Einspritzung 24 Grad nach dem Referenzpunkt. Der fehlende Zahn liegt 90⁰ vor OT, die Einspritzung beginnt also (90⁰ – 24⁰) = 66⁰ vor OT.
Bei einer erhöhten Drehzahl von 2000 U/min liegen die Impulse des induktiven Kurbelwellensensors näher beieinander. Die Frequenz dieses Signals wird vom Motormanagementsystem in eine Geschwindigkeit umgewandelt. Abhängig von der Geschwindigkeit ist die Belastung (gemessen am Kartensensor) und die Temperatur aus Ansaugluft und Kühlmittel wird die erforderliche Einspritzzeit ermittelt. Der Einspritzzeitpunkt erfolgt früher und der Injektor bleibt länger am Boden: Der Injektor spritzt früher und länger ein.
Vom Beginn der Aktivierung bis zum Auslösepunkt (Pfeil auf Höhe der Injektorabschaltung) beträgt die Aktivierungszeit ca. 5,2 ms. Die Zeit, in der der Injektor aktiviert wird, entspricht nicht der tatsächlichen Einspritzung (siehe vorheriger Absatz).
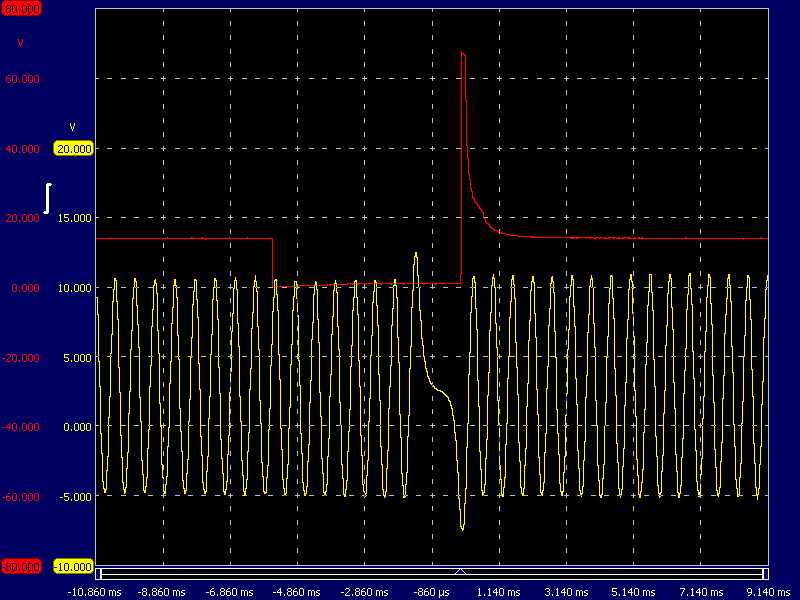
Im folgenden Oszilloskopbild ist das induktive Kurbelwellensignal in Rot und das Einspritzventilsignal in Gelb dargestellt. Beim Erhöhen der Drehzahl auf ca. 3000 U/min sind zwei Injektorsteuerungen zu erkennen. Es ist deutlich zu erkennen, dass bei jeder zweiten Kurbelwellenumdrehung eine Kraftstoffeinspritzung des Zylinders 1 erfolgt.
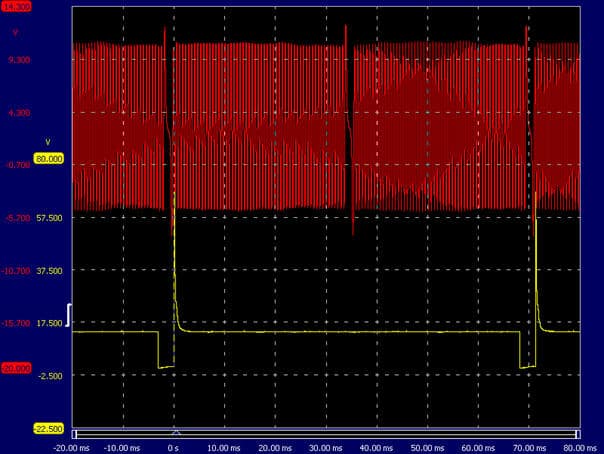
Strombegrenzung im Steuergerät:
Wie die Messungen im Abschnitt „Spannungs- und Strommessung an einem Multipoint-Injektor“ zeigten, kommt es zwischen der Betätigung und dem tatsächlichen Öffnen der Injektornadel zu einer Verzögerung. In diesem Fall dauert das Öffnen 1,5 ms.
Die Einspritznadel würde sich schneller öffnen, wenn der Strom durch die Spule schneller ansteigen würde. Der Strom hängt vom Widerstand der Spule ab: Je geringer der Widerstand, desto schneller der Stromaufbau. Die im Motor der Messungen verwendeten Hochimpedanz-Injektoren haben einen Widerstand von 16 Ohm. Bei einer Bordspannung von 14 Volt fließt ein kleiner Strom:
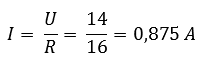
Der Strom reicht aus, um die Einspritznadel zu öffnen, aber nicht zu hoch, sodass diese durch zu hohe Leistung zu heiß werden würde:

Da nur eine geringe Leistung aufgebaut wird, ist der Einsatz einer Stromregelung nicht erforderlich. Dies wäre bei niederohmigen Injektoren notwendig.
- Niederohmige Injektoren haben den Vorteil, dass der Stromaufbau von Anfang an schnell ansteigt. Dies führt zu einem schnellen Öffnen der Einspritznadel und somit zu einer geringen Verzögerung.
- Niederohm-Injektoren haben einen Widerstand von ca. 2,8 Ohm. Durch den geringen Widerstand fließt ein hoher Strom:
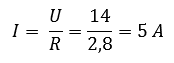
Auch die Leistung steigt stark an:

Der Stromverbrauch ist fast siebenmal höher als bei den Hochimpedanz-Injektoren. Steigt der Strom zu stark an, entsteht Wärme in den Injektoren und in der Endstufe des Steuergerätes. Um den Strom zu begrenzen, wird die Spannung innerhalb kurzer Zeit mehrmals ein- und ausgeschaltet. Nach dem Öffnen der Injektornadel ist nur wenig Energie erforderlich, um die Nadel offen zu halten. Beim Ein- und Ausschalten nimmt der Strom ab. Dieser Verlauf ist im Bild des Zielfernrohrs zu sehen.
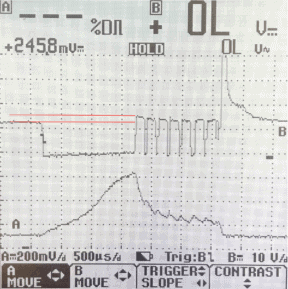
Ermittlung der benötigten Kraftstoffmenge:
Der Hersteller ermittelt die erforderliche Kraftstoffmenge anhand verschiedener Kennfelder, die im ROM-Speicher des Steuergeräts abgelegt sind. Es Motormanagementsystem liest aus diesen Diagrammen ab, wie viel Kraftstoff ohne Korrekturen benötigt wird. Dies hängt natürlich von der Motordrehzahl, Temperatur und Last ab. Die wichtigsten Parameter zur Bestimmung der richtigen Kraftstoffmenge werden in diesem Abschnitt als VE-Tabelle und AFR-Tabelle erläutert.
VE-Tabelle:
Die VE-Tabelle stellt den volumetrischen Wirkungsgrad und das Luft-/Kraftstoffverhältnis bei jeder Motordrehzahl und jedem Ansaugkrümmerdruck dar. Der volumetrische Wirkungsgrad ist das Verhältnis zwischen der gemessenen Luftmenge, die die Zylinder füllt, und der Luftmenge, die den Zylinder in einer statischen Situation füllen würde, abhängig von der Motordrehzahl und dem Ansaugkrümmerdruck. Anhand der Werte in der Tabelle ermittelt das Steuergerät die aktuelle Luftmasse und damit den Füllstand. Aus diesen Daten wird die einzuspritzende Kraftstoffmenge berechnet.
Dieser theoretische Ansatz weicht von der Realität ab. Die Motorspezifikationen sind hier noch nicht berücksichtigt. Berücksichtigen Sie das Ventildiagramm (Ventilüberschneidung oder ggf. variable Ventilsteuerung), den Luftwiderstand im Ansaugtrakt usw. Deshalb wird ein Korrekturfaktor angewendet, der eine Abweichung vom linearen Zusammenhang ergibt. Der Korrekturfaktor ist im obigen Bild durch die gestrichelte Linie dargestellt. Die Kurve gibt an, inwieweit der lineare Zusammenhang korrekt ist. Bei einem Druck von 60 kPa beträgt die Abweichung etwa 50 % von der Linie, die den linearen Zusammenhang darstellt. Der Korrekturfaktor kann in Prozent umgerechnet werden.
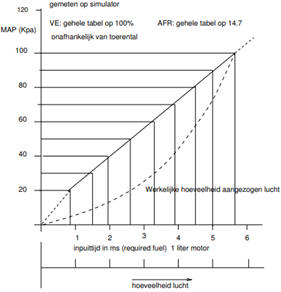
In einer VE-Tabelle gibt jede Zelle den Prozentsatz an, der dem Unterdruck im Verhältnis zur Geschwindigkeit zugeordnet ist. Dieser Prozentsatz ist bei der Drehzahl am höchsten, bei der das Drehmoment am höchsten ist. Denn dort ist der Motor am effizientesten, weil er am besten füllt.
Die Werte in den VE- und AFR-Tabellen weiter unten in diesem Abschnitt werden aus der Drehmoment- und Leistungskurve eines 1.8-20-V-Motors aus einem VW Golf abgeleitet.
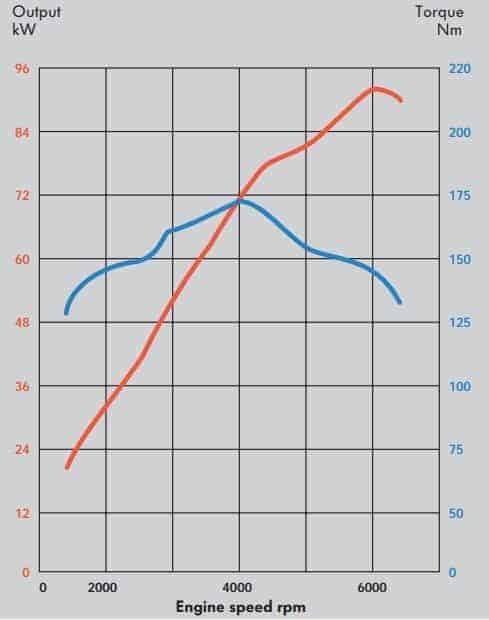
Die folgenden Bilder zeigen die VE-Tabelle als Ausfülltabelle und die dreidimensionale Darstellung, die mithilfe der Drehmoment- und Leistungskurve im Programm „TunerStudio“ erstellt wurde. Dieses Programm wird hauptsächlich zur Bereitstellung von Software für ein programmierbares Steuergerät wie MegaSquirt oder Speeduino verwendet. Weitere Informationen finden Sie auf den Seiten dazu MegaSquirt-Projekt.
Die vertikale Achse zeigt den MAP (Manifold Air Pressure) von 15 kPa (viel Unterdruck) bis 100 kPa (Außenluftdruck). Der MAP gibt die Motorlast an. Die horizontale Achse zeigt die Motordrehzahl zwischen Leerlauf und maximaler Motordrehzahl an.
Die Zellen in der VE-Tabelle zeigen den Füllstand des Motors. Mit anderen Worten; wie effizient der Motor bei einer bestimmten Drehzahl und Last ist. Der Motor ist bei der Drehzahl am effizientesten, bei der das Drehmoment am höchsten ist (ca. 4200 U/min); Hier sind die Prozentsätze am höchsten. Hier „füllt“ der Motor am besten. Der Einsatz von Techniken, die den Füllstand erhöhen, wie z. B. eine variable Ventilsteuerung, eine Ansaugkrümmerverstellung oder der Einsatz eines Turbos, wird sich positiv auf die Prozentsätze auswirken.
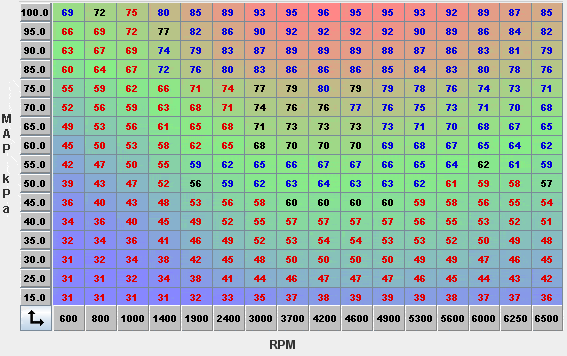
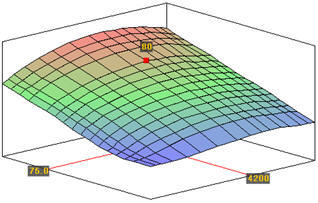
AFR-Tabelle:
Die erforderliche Luft-/Kraftstoffzusammensetzung wird in einer AFR-Tabelle erfasst. AFR ist die Abkürzung für „Air Fuel Ratio“. Bei einem stöchiometrischen Mischungsverhältnis (Lambda = 1) werden zur Verbrennung von 14,7 kg Benzin 1 kg Luft benötigt. Eine stöchiometrische Mischung ist nicht in allen Situationen wünschenswert.
- Eine magere Mischung begünstigt den Kraftstoffverbrauch;
- Eine fette Mischung ermöglicht eine höhere Leistung.
Wenn der Motor mehr Leistung (P) liefern muss, findet eine Anreicherung statt. Eine reichhaltigere Mischung sorgt zusätzlich für Kühlung. Die Anreicherung auf λ = 0,8 bedeutet, dass ein Mischungsverhältnis (AFR) von 11,76 kg Luft zu 1 kg Benzin gilt. Für die Verbrennung von 1 kg Kraftstoff steht also weniger Luft zur Verfügung als bei einem stöchiometrischen Gemisch. Ein mageres Gemisch hingegen führt zu einem besseren Kraftstoffverbrauch, erhöht jedoch die Klopfgefahr. Eine Anreicherung oder Verarmung des Gemisches muss immer innerhalb der Verbrennungsgrenzen bleiben.
Im Leerlauf liegt die Drehzahl zwischen 600 und 900 U/min. Das Gasventil ist fast vollständig geschlossen und der Unterdruck ist hoch: Er liegt zwischen 25 und 40 kPa. In diesem Drehzahlbereich ist die Mischung stöchiometrisch (14,7:1).
Bei Teillast erhöht sich die Motordrehzahl auf 4200 U/min. Die Drosselklappe wird weiter geöffnet, so dass der Unterdruck im Ansaugrohr auf 40 – 75 kPa sinkt. Mit zunehmender Motorlast nimmt der Unterdruck ab; Es findet eine Anreicherung statt (AFR von 13:1). Bei geringer Motorlast ist ein mageres Gemisch möglich. Bei Volllast ist die Drosselklappe vollständig geöffnet. Der Unterdruck sinkt auf 100 kPa (Außenluftdruck) und es findet die maximale Anreicherung statt (12,5:1).
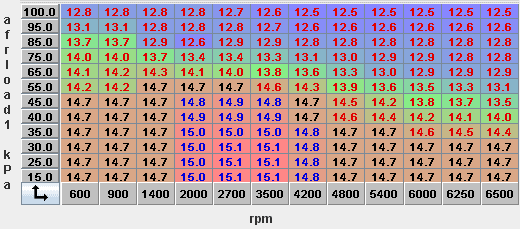
Der Lambda-Wert hat nicht nur Einfluss auf Leistung und Kraftstoffverbrauch, sondern auch auf die Abgasemissionen. Eine fettere Mischung sorgt für einen geringeren NOx-Gehalt, aber auch für höhere CO- und HC-Emissionen. Bei einem magereren Gemisch liegen die Kraftstoffpartikel weiter auseinander, so dass die Verbrennung nicht mehr optimal ist; mit der Folge, dass auch die HC-Emissionen steigen.
Beim Einsatz eines Katalysators ist darauf zu achten, dass die Einspritzung ständig zwischen fett und mager erfolgt. In einem fetten Gemisch entsteht durch Sauerstoffmangel CO, mit dem der Katalysator das NOx reduziert. Ein mageres Gemisch enthält einen Überschuss an Sauerstoff, der CO und HC oxidiert.
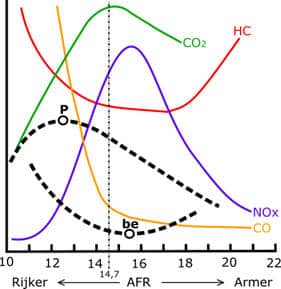
Das Steuergerät bestimmt, wie viel Kraftstoff eingespritzt werden soll. Zunächst werden die Einspritzgrunddaten aus den Kennfeldern ausgelesen. In die Berechnung der Einspritzmenge fließen unter anderem die Werte aus den VE- und AFR-Tabellen ein. Berücksichtigt werden außerdem folgende vom Hersteller ermittelte Werte:
- Anreicherung abhängig von Kühlmittel- und Ansauglufttemperatur;
- kurzfristige Beschleunigungsanreicherung beim (schnellen) Gasgeben;
- Korrektur aufgrund von Schwankungen der Bordspannung.
Zusätzlich zu diesen ermittelten Werten werden die Spannungen, die die Lambdasonde an das Steuergerät sendet, sorgfältig berücksichtigt. Diese Spannungen hängen vom Sauerstoffgehalt in den Abgasen ab. Dies ist ein variabler Faktor, der sich kontinuierlich ändert. Der Eingang dieser Sensorspannungen wird als sogenannte „Kraftstoffverkleidungen„eingearbeitet.
Wie die Werte der VE- und AFR-Tabelle und der anderen genannten Einstellungen ermittelt werden, ist auf den Seiten der durchgeführten Einstellungen beschrieben MegaSquirt-Projekt.