Themen:
- Einführung
- Materialien und Spezifikationen verschiedener Batterien
- Blei-Säure-Batterie
- Nickel-Cadmium (Ni-Cd)
- Nickel-Metallhydrid (Ni-MH)
- Lithium-Ionen (Li-Ion)
- Superkondensator (Supercap)
- Ausbalancieren der Batteriezellen
Einführung:
Das Hybrid- oder Vollelektroauto verfügt über größere und schwerere Batterien als Autos mit nur einem Verbrennungsmotor. Bei Hybridautos kommt es zu hohen Spannungen, die lebensgefährlich sein können, wenn Reparaturen von unqualifizierten Personen durchgeführt werden. Als Beispiel:
- Ein in Betrieb befindlicher Anlasser verbraucht etwa 1,2 kW (1200 Watt).
- Ein vollständig elektrisch betriebenes Hybridauto verbraucht etwa 60 kW (60.000 Watt).
Arbeiten an Hybridfahrzeugen dürfen nur von Personen durchgeführt werden, die eine spezielle Ausbildung absolviert haben. Für die Stromversorgung von Zubehör (wie Radio etc.) mit eigener kleiner Batterie gibt es ein 12-Volt-Bordnetz, außerdem gibt es ein Hochvolt-Bordnetz, das mit 400 Volt (je nach Marke) arbeitet ). Die 400-V-Spannung wird durch einen speziellen DC/DC-Wandler in 12 V umgewandelt und lädt die entsprechende Batterie.
An Hybridantriebsbatterien werden hohe Anforderungen gestellt. Sie müssen sehr groß sein Speicherkapazität haben. Es werden große Energiereserven gespeichert und bei der Unterstützung des Verbrennungsmotors (Hybrid) oder bei der Bereitstellung von Energie für den Gesamtantrieb (BEV) werden sehr hohe Spannungen entnommen.
Das Bild unten zeigt einen Akku eines Toyota Prius. Dieser Nickel-Metallhydrid-Akku (NiMH) enthält 28 Module mit jeweils 6 Zellen. Jede Zelle hat eine Spannung von 1,2 Volt. Die Gesamtspannung dieses Akkupacks beträgt 201,6 Volt.
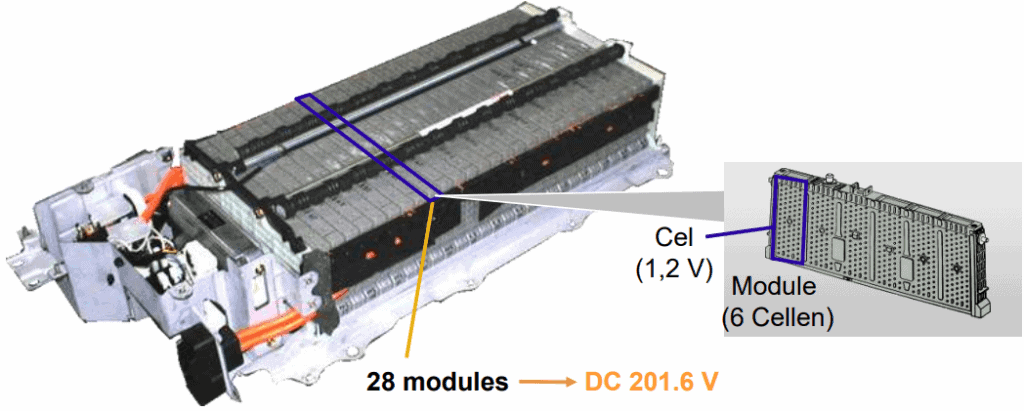
Materialien und Spezifikationen verschiedener Batterietypen:
Bei der Entwicklung des elektrischen Antriebsstrangs wird zwischen verschiedenen Batterietypen gewählt. Dabei spielen Eigenschaften, Leistung, Baumöglichkeiten und Kosten eine große Rolle. Die am häufigsten verwendeten Batterietypen in Hybrid- und vollelektrischen Fahrzeugen sind Ni-MH-Batterien (Nickel-Metallhydrid) und Li-Ionen-Batterien (Lithium-Ionen).
Neben den Ni-MH- und Li-Ion-Typen gibt es eine Entwicklung von Elektrolytkondensatoren, die wir unter dem Namen „Superkondensator“ oder „Supercaps“ bezeichnen.
Die Tabelle zeigt die Materialien der verschiedenen Batterien mit ihren Spezifikationen.
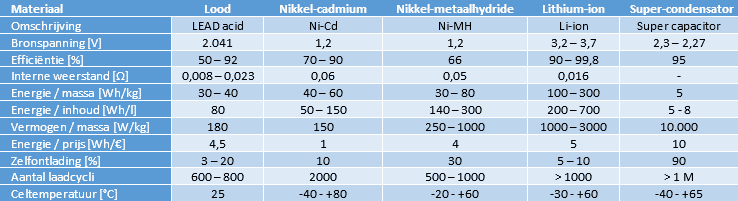
Bleibatterie:
In der Tabelle wird auch die Blei-Säure-Batterie erwähnt (Gel- und AGM-Versionen sind nicht berücksichtigt). Da die Blei-Säure-Batterie bei einer maximalen Entladung von 20 % die längste Lebensdauer hat, mit zunehmender Alterung unter Sulfatierung leidet und eine geringe Energiedichte und einen geringen Energiegehalt aufweist, ist sie für den Einsatz in Elektrofahrzeugen nicht geeignet. Wir finden die Blei-Säure-Batterie als Zubehörbatterie; Niederspannungsverbraucher wie Beleuchtung, Komfortsysteme (Karosserie) und Infotainment arbeiten mit einer Spannung von etwa 14 Volt.
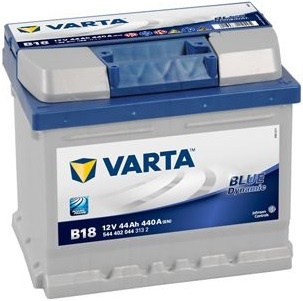
Nickel-Cadmium (Ni-Cd):
Früher Ni-Cd Batterien unterliegen einem Memory-Effekt und sind daher für den Einsatz in Elektroantrieben ungeeignet: Teilladung und -entladung treten ständig auf. Moderne Ni-Cd-Akkus sind vom Memory-Effekt praktisch nicht mehr betroffen. Der größte Nachteil dieses Batterietyps ist das Vorhandensein des giftigen Stoffes Cadmium. Dies macht den Ni-Cd-Akku äußerst unfreundlich für die Umwelt. Die Verwendung dieser Batterie ist daher gesetzlich verboten.
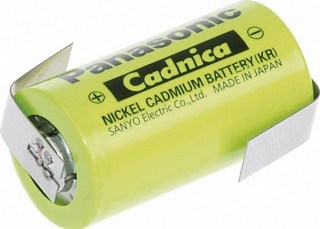
Nickel-Metallhydrid (Ni-MH):
Der Ni-MH-Akku kann schneller aufgeladen werden als ein Blei-Säure-Akku. Beim Laden entsteht sowohl Wärme als auch Gas, die abgeführt werden müssen. Die Batterien sind mit einem Kühlsystem und einem Entlüftungsventil ausgestattet. Dank seiner langen Lebensdauer und hohen Energie- und Leistungsdichte eignet sich der Ni-MH-Akku für den Einsatz in Elektrofahrzeugen. Allerdings ist dieser Batterietyp empfindlich gegenüber Überladung, übermäßiger Entladung, hohen Temperaturen und schnellen Temperaturwechseln.
Das Bild unten zeigt den Ni-MH-Akku eines Toyota Prius. Dieser Akku befindet sich im Kofferraum hinter der Rücksitzlehne. Wenn die Temperatursensoren eine hohe Temperatur registrieren, wird der Kühlventilator aktiviert (auf dem Foto rechts am weißen Gehäuse zu erkennen). Der Lüfter saugt die Luft aus dem Innenraum an und bläst sie durch die Luftkanäle im Akkupack, um die Zellen zu kühlen.
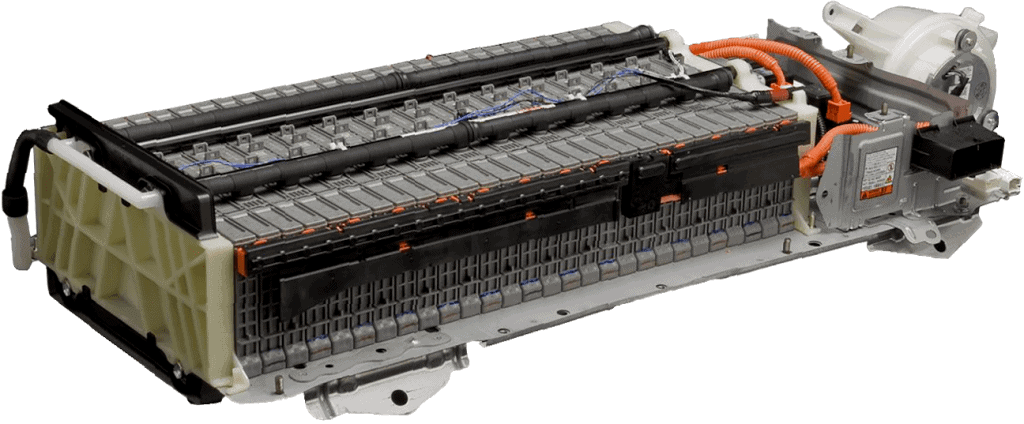
Lithium-Ionen (Li-Ion):
Aufgrund der hohen Energie- und Leistungsdichte des Lithium-Ionen-Akkus (im Vergleich zu Ni-MH) wird ein Li-Ionen-Akkupack meist in Plug-in-Hybriden und vollelektrischen Fahrzeugen verwendet. Der Li-Ionen-Akku funktioniert gut bei niedrigen Temperaturen und hat eine lange Lebensdauer. Es wird erwartet, dass sich die Immobilien in den kommenden Jahren durch weitere Entwicklungen verbessern werden.
Im nächsten Bild sehen wir den (Li-Ionen-)Akku eines BMW i3. Der Deckel ist abgeschraubt und liegt dahinter. Im montierten Zustand schließt der Deckel luftdicht.
Der Akku des i3 ist unter dem Fahrzeug montiert. Der Platz im Bodenraum zwischen Vorder- und Hinterachse wurde so weit wie möglich ausgenutzt, um möglichst viel Platz für den Akku zu schaffen.
Im Bild sehen wir die acht separaten Blöcke mit jeweils zwölf Zellen. Jeder Block hat eine Kapazität von 2,6 kWh, also insgesamt 22 kWh. Zum Vergleich: Die aktuelle Generation i3 (2020) verfügt über einen Akku mit einer Kapazität von 94 Ah und einer Leistung von 22 kWh. Die Größe des Akkus ist seit seiner Einführung im Jahr 2013 gleich geblieben, seine Leistung (und damit seine Reichweite) hat sich jedoch deutlich verbessert.
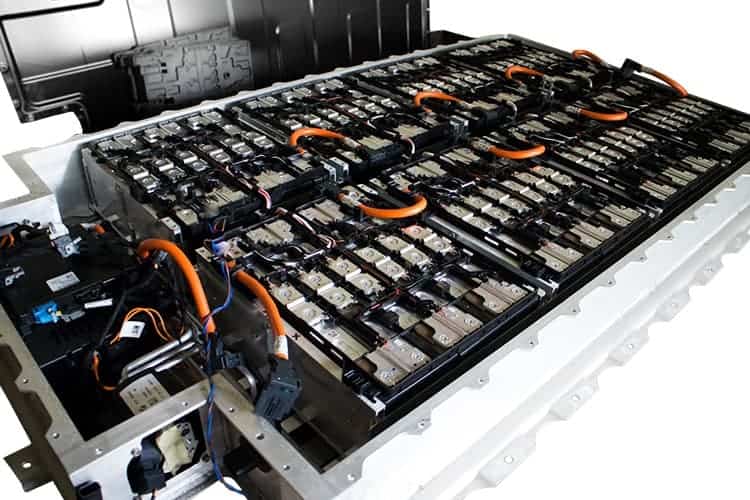
Tesla setzt in den Modellen ab 2013 (Model S und Model X) kleine Batteriezellen ein, die etwas größer sind als herkömmliche AA-Batterien, die wir aus der Fernsehfernbedienung kennen. Die Akkuzellen (18650 von Panasonic) sind 65 mm lang und haben einen Durchmesser von 18 mm. Die umfangreichsten Akkupacks enthalten nicht weniger als 7104 dieser Zellen.
In den Bildern unten sehen wir links die einzelnen Akkuzellen und rechts einen Akkupack mit den 7104-Zellen.
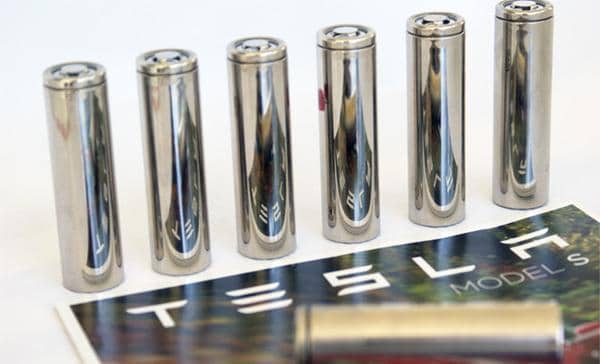
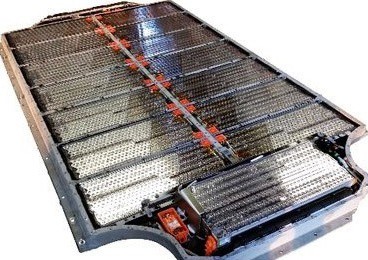
Der Lithium-Ionen-Akku besteht aus vier Hauptkomponenten:
- Die Kathode (+) besteht aus einer Lithiumlegierung
- die Anode (-) besteht aus Graphit oder Kohlenstoff
- der poröse Separator
- der Elektrolyt
Beim Entladen bewegen sich die Lithiumionen durch den Elektrolyten von der Anode (-) zur Kathode (+), zum Verbraucher und zurück zur Anode. Beim Laden bewegen sich die Ionen in entgegengesetzte Richtungen und gelangen dann von der Kathode (+) zur Anode (-).
Der Elektrolyt enthält Lithiumsalze zum Transport der Ionen. Der Separator sorgt dafür, dass die Lithiumionen passieren können, während Anode und Kathode getrennt bleiben.
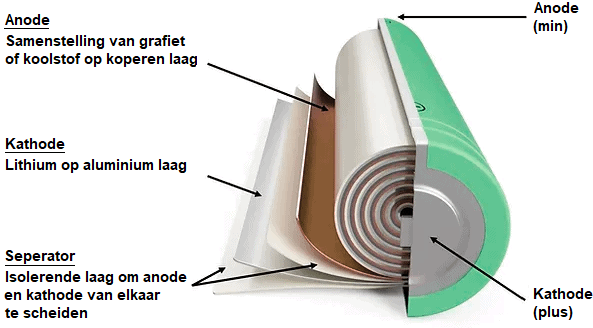
Die Batteriezellen sind in Modulen untergebracht, die in Reihe geschaltet sind. Die folgende schematische Darstellung unten zeigt ein Batteriepaket, das starke Ähnlichkeiten mit dem eines Volkswagen E-UP aufweist! und Renault Zoe. Lediglich die Anzahl der Zellen unterscheidet sich: Der Akku des E-UP! hat 204 Zellen und der des Renault Zoë 192.
In diesem Beispiel besteht das Batteriepaket aus zwei Paketen mit je sechs Modulen. Jedes Modul enthält zwei Gruppen von 10 parallel in Reihe geschalteten Zellen.
- Reihenschaltung: Die Batteriespannung steigt. Bei einer Zellspannung (Li-Ion) von 3,2 Volt liefert ein Batteriemodul (3,2 * 10) = 32 Volt.
Der Nachteil einer Reihenschaltung besteht darin, dass bei einer schlechten Zelle die Kapazität der gesamten Reihenschaltung geringer wird. - Parallelschaltung: Die Spannung bleibt gleich, aber Strom und Kapazität steigen. Eine defekte Zelle hat keinen Einfluss auf die Zellen im Parallelschaltkreis.
Hersteller können sich daher dafür entscheiden, mehrere Parallelschaltungen pro Modul zu verwenden. In den Modulen des Volkswagen E-Golf sind also nicht (in diesem Beispiel zwei), sondern drei Gruppen von Zellen parallel geschaltet.
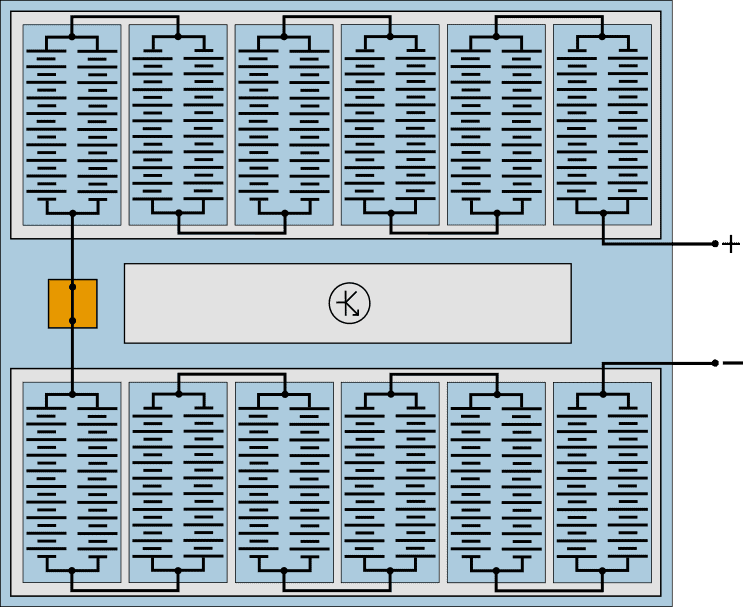
Lithium-Ionen-Zellen haben eine Lebensdauer von etwa 2000 Entlade- und Ladezyklen, bevor ihre Kapazität auf etwa 80 % ihrer ursprünglichen Ladekapazität sinkt.
Die Spannungen einer Li-Ionen-Zelle sind wie folgt:
- Nennspannung: 3,6 Volt;
- Entladegrenze: 2,5 Volt;
- maximale Ladespannung: 4,2 Volt.
Die meisten Batteriemanagementsysteme (BMS) verwenden eine Untergrenze von 2,8 Volt. Wenn die Zelle über 2,5 Volt entladen wird, wird die Zelle beschädigt. Die Lebensdauer der Zelle wird verkürzt. Auch ein Überladen der Li-Ionen-Zelle verringert deren Lebensdauer, ist aber auch gefährlich. Eine Überladung der Zelle kann dazu führen, dass sie entflammbar wird. Auch die Temperatur der Zellen beeinflusst deren Lebensdauer: Bei einer Temperatur unter 0°C kann es sein, dass die Zellen nicht mehr geladen werden. Eine Heizfunktion bietet hier Abhilfe.
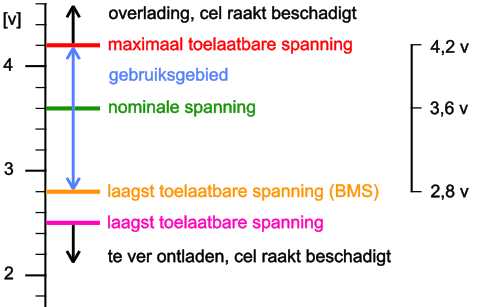
Supercode-Kondensator (Supercap):
In den vorherigen Absätzen wurden verschiedene Batterietypen mit jeweils ihren Einsatzmöglichkeiten, Vor- und Nachteilen erwähnt. Ein Nachteil, den jeder mit einem solchen Akku hat, ist die Ladezeit. Das Aufladen eines Akkus kann mehrere Stunden dauern. Schnellladen ist eine Option, allerdings ist dies mit mehr Hitze und möglicherweise auch einer schnelleren Alterung (und Beschädigung) des Akkupacks verbunden.
Derzeit wird viel an Superkondensatoren geforscht und entwickelt. Wir nennen diese auch „Super-Caps“ oder „Ultrakondensatoren“. Der Einsatz von Supercaps könnte hierfür eine Lösung bieten:
- Der Ladevorgang geht sehr schnell;
- Sie können sehr schnell Energie abgeben (entladen), sodass eine deutliche Leistungssteigerung möglich ist;
- Langlebiger als ein Li-Ionen-Akku durch unbegrenzte Anzahl an Ladezyklen (mindestens 1 Million), da keine elektrochemischen Reaktionen stattfinden;
- Teilweise im Zusammenhang mit dem vorherigen Punkt kann ein Supercap vollständig entladen werden, ohne dass dies negative Auswirkungen auf seine Lebensdauer hat.
Supercaps sind Kondensatoren mit einer tausendfach höheren Kapazität und Energiedichte als herkömmliche Elektrolytkondensatoren. Die Kapazität wird durch die Verwendung eines speziellen Elektrolyten (Isoliermaterial) erhöht, der Ionen enthält und daher eine sehr hohe Dielektrizitätskonstante zwischen den Platten aufweist. Ein Separator (eine dünne Folie) wird in einem Lösungsmittel mit Ionen getränkt und zwischen den Platten platziert. Die Platten bestehen meist aus Carbon.
Die Kapazität des gezeigten Kondensators beträgt 5000 F.
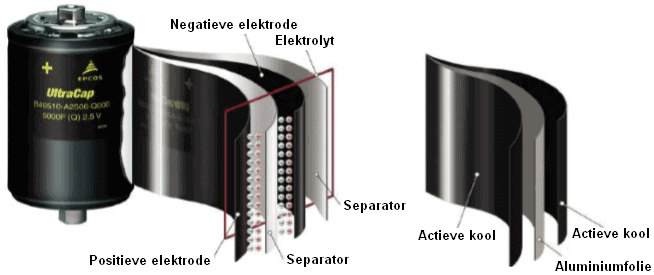
Die Supercaps können mit einer Li-Ionen-HV-Batterie kombiniert werden; Beim kurzzeitigen Beschleunigen kann anstelle der Energie aus der HV-Batterie die Energie aus den Kondensatoren genutzt werden. Beim regenerativen Bremsen laden sich die Kondensatoren innerhalb von Sekundenbruchteilen vollständig auf. Zukünftige Entwicklungen könnten es auch ermöglichen, die Li-Ionen-Batterie durch ein Supercap-Paket zu ersetzen. Leider ist beim aktuellen Stand der Technik die Kapazität und damit die Leistungsdichte im Vergleich zu einem Lithium-Ionen-Akku zu gering. Wissenschaftler suchen nach Möglichkeiten, die Kapazität und Leistungsdichte zu erhöhen.
Balancing der Batteriezellen:
Durch passives und aktives Ausbalancieren der Batteriezellen wird jede Zelle vom Steuergerät überwacht, um einen gesunden Batteriestatus aufrechtzuerhalten. Dies verlängert die Lebensdauer der Zellen, indem eine Tiefentladung oder Überladung verhindert wird. Insbesondere Lithium-Ionen-Zellen müssen strenge Grenzwerte einhalten. Die Spannung der Zellen ist proportional zum Ladezustand. Die Ladungen der Zellen müssen möglichst im Gleichgewicht gehalten werden. Mit dem Zellausgleich ist es möglich, den Ladezustand auf 1 mV (0,001 Volt) genau zu steuern.
- Das passive Balancing sorgt für einen ausgeglichenen Ladezustand aller Batteriezellen, indem es die Zellen mit einem zu hohen Ladezustand teilweise entlädt (wir werden später in diesem Abschnitt darauf zurückkommen);
- Beim aktiven Balancing handelt es sich um eine komplexere Balancing-Technik, mit der die Zellen beim Laden und Entladen individuell gesteuert werden können. Die Ladezeit beim aktiven Balancing ist kürzer als beim passiven Balancing.
Im folgenden Bild sehen wir ein Batteriemodul mit acht Zellen.
Die acht Zellen sind zu 90 % geladen. Die Lebensdauer einer Zelle verkürzt sich, wenn sie kontinuierlich auf 100 % geladen wird. Umgekehrt verringert sich auch die Lebensdauer, wenn die Batterie über 30 % entladen wird: Bei einem Ladezustand von <30 % ist die Zelle tiefentladen.
Der Ladezustand der Zellen liegt daher immer zwischen 30 % und 90 %. Dies wird von der Elektronik überwacht, ist für den Fahrer des Fahrzeugs jedoch nicht sichtbar.
Die Digitalanzeige im Armaturenbrett zeigt bei Erreichen von 0 % oder 100 % 30 % oder 90 % an.
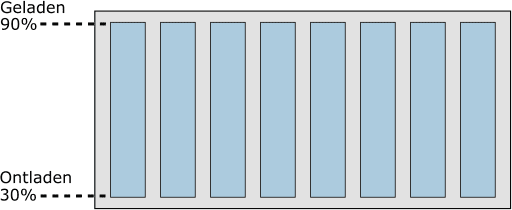
Aufgrund des Alters können einige Zellen schwächer werden als andere. Dies hat großen Einfluss auf den Ladezustand des Batteriemoduls. In den nächsten beiden Bildern sehen wir den Ladezustand, wenn zwei Zellen altersbedingt eine geringere Kapazität haben. Die Batteriezellen sind in diesen Situationen nicht ausgeglichen.
- Schnellere Entladung durch schlechte Zellen: Die beiden mittleren Zellen entladen sich aufgrund ihrer geringeren Kapazität schneller. Um eine Tiefentladung zu verhindern, können die anderen sechs Zellen im Modul keine Energie mehr abgeben und sind somit nicht mehr nutzbar;
- Lädt aufgrund schlechter Zellen nicht vollständig auf: Aufgrund der geringen Kapazität der mittleren beiden Zellen werden diese schneller aufgeladen. Da sie 90 % schneller als die anderen sechs Zellen erreichen, ist eine weitere Aufladung nicht möglich.
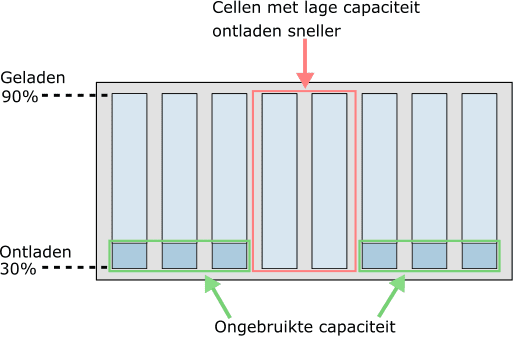
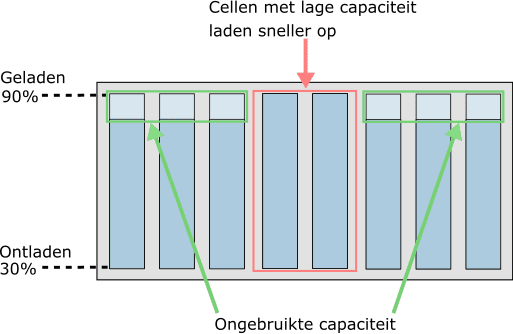
Es ist klar, dass Zellen mit geringerer Kapazität sowohl beim Entladen (während der Fahrt) als auch beim Laden der limitierende Faktor sind. Um die volle Kapazität des Akkupacks optimal auszunutzen und eine lange Lebensdauer zu gewährleisten.
Es gibt zwei Methoden zum Batterieausgleich: passiv und aktiv.
- Ohne Balancing: Vier Zellen haben alle einen unterschiedlichen Ladezustand. Zelle 2 ist fast leer und Zelle 4 ist vollständig geladen;
- Passiv: Die Zellen mit der höchsten Kapazität werden entladen, bis der Ladezustand der schwächsten Zelle (im Beispiel Zelle 2) erreicht ist. Die Entladung der Zellen 1, 3 und 4 ist Verlust.
Im Beispiel sehen wir, dass die Becher solange entladen werden, bis sie den Ladezustand von Zelle 2 erreichen; - Aktiv: Die Energie der vollen Zellen wird zum Auffüllen der leeren Zellen genutzt. Es kommt nun zu keinem Verlust, sondern zu einem Energietransfer von einer Zelle zur anderen.
Nachfolgend wird das Funktionsprinzip des passiven und aktiven Zellausgleichs erläutert.
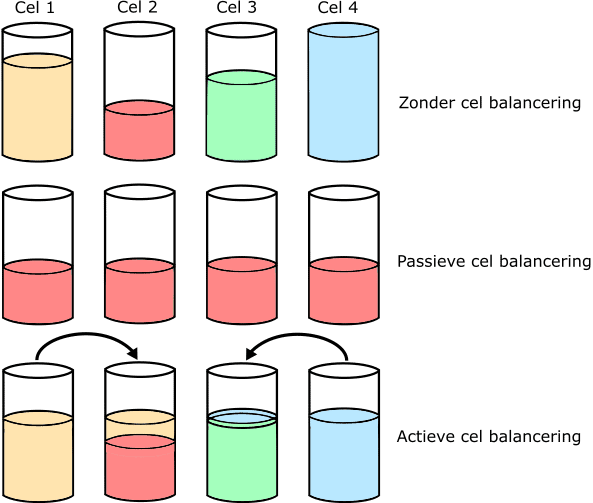
Passiver Zellausgleich:
Im Beispiel sehen wir vier in Reihe geschaltete Batteriezellen mit einem schaltbaren Widerstand (R) parallel. In diesem Beispiel ist der Widerstand über den Schalter mit Masse verbunden. In Wirklichkeit handelt es sich hierbei um einen Transistor oder FET.
Im Beispiel sehen wir, dass Zelle 3 zu 100 % geladen ist. Aus den vorherigen Absätzen wissen wir, dass diese Zelle schneller lädt, weil sie schwächer ist als die anderen drei. Da der Ladezustand der Zelle 3 100 % beträgt, werden die anderen drei Zellen nicht mehr geladen.
Der parallel zur Zelle 3 liegende Widerstand wird durch den Schalter in den Stromkreis einbezogen. Zelle 3 entlädt sich, da der Widerstand Spannung aufnimmt, sobald Strom durch ihn fließt. Die Entladung wird fortgesetzt, bis die Zelle auf dem Niveau der anderen Zellen ist; in diesem Fall 90 %.
Wenn alle vier Zellen in diesem Modul den gleichen Ladezustand haben, können sie weiter aufgeladen werden.

Beim passiven Zellbalancing geht Energie verloren: Die von den parallel geschalteten Widerständen aufgenommene Spannung ist verloren gegangen. Dennoch nutzen viele Hersteller diese Methode des Auswuchtens auch heute noch.
Aktiver Zellausgleich:
Viel effizienter ist natürlich der aktive Zellausgleich. Die Energie aus der überfüllten Zelle wird zum Laden der leeren Zelle verwendet. Unten sehen wir ein Beispiel für einen aktiven Zellausgleich.
Im Beispiel sehen wir zwei in Reihe geschaltete Zellen (3 und 4), deren Spannungen darüber liegen (4 bzw. 3,9 Volt). Zelle 3 wird über den Transformator entladen. Der FET auf der Primärseite ermöglicht die Entladung. Damit wird die Primärspule im Transformator aufgeladen. Der FET auf der Sekundärseite schaltet die Sekundärspule des Transformators ein. Der erhaltene Ladestrom wird verwendet, um den Transformator unter einer anderen Zelle mit Strom zu versorgen. Der Transformator unter Zelle 4 wird ebenfalls über FETs ein- und ausgeschaltet.
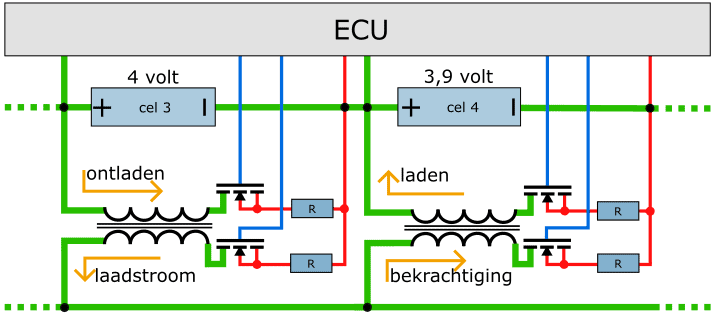