Themen:
- Allgemeines
- Geregelte und ungeregelte LPG-Systeme
- Autogas und Gastank
- Füllanschluss
- Gasventil
- Kraftstoffabsperrventil
- Von Benzin auf Gas umsteigen
- Betrieb des Verdampfers
- System mit Schrittmotor mit Trocknungsgasschlauch (AMS)
- Dampfgasinjektion (VSI/EGI)
- Betrieb des EGI-Verdampfers
- Flüssiggasinjektion (LPi)
- Koppelblock (LPi)
- Injektoren (LPi)
Gesamt:
Autogas wird weltweit in geringem Umfang als Kraftstoff für Pkw-Motoren eingesetzt. (Stand 2013) werden rund 700.000 Fahrzeuge mit diesem Kraftstoff betrieben. Diese Zahl könnte sinken, da der Kfz-Steuervorteil für Oldtimer unter 40 Jahren abgeschafft wurde. Der Steuersatz für diese älteren Autos ist der gleiche wie für ein jüngeres Auto. Wenn die LPG-Anlage ausgebaut (und natürlich überprüft) wird, können Sie den Steuervorteil wieder nutzen, wenn das Fahrzeug zwischen 26 und 40 Jahre alt ist.
Autogas ist umweltfreundlicher als beispielsweise Benzin oder Diesel. Die Abgase sind sauberer. Auch der Kraftstoff selbst ist pro Liter günstiger als Benzin. Der Verbrauch ist bei Flüssiggas oft etwas höher, der Wendepunkt ist jedoch niedrig. Mit Ausnahme des LPi-Systems nimmt die Motorleistung bei LPG im Vergleich zu Benzin leicht ab. Mehr dazu erfahren Sie weiter unten auf dieser Seite.
Es gibt 3 verschiedene Arten von LPG-Systemen. Diese Systeme werden auf dieser Seite ausführlich erklärt:
- System mit Schrittmotor im Trocknungsgasschlauch (AMS) (Singlepoint-Injektion vor dem Gasventil)
- Dampfgasinjektion (VSI/EGI) (Mehrpunktinjektion am Einlassventil)
- Flüssiggasinjektion (LPi) (Mehrpunktinjektion am Einlassventil)
Der Begriff G2 oder G3 wird häufig verwendet:
G2-Installationen verwenden ein Gas-Venturi-System oder eine Dampfgasinjektion. Eventuell ist am Auto ein Katalysator mit Lambdasonde vorhanden und die Ausstattung entspricht ggf. einem G3-Einbau. Dennoch fallen sie möglicherweise nicht unter den Steuervorteil einer G3-Installation, weil das Fahrzeug nicht den Abgasnormen ECE94-12 entspricht oder weil das Fahrzeug nicht von einer anerkannten Prüfstelle geprüft wurde. G3-Installationen verwenden die vom Motormanagementsystem berechneten Aktivierungszeiten der Einspritzdüsen. Diese Zeiten werden in Steuerzeiten für die Gasinjektoren umgerechnet.
Geregelte und ungeregelte Flüssiggasanlagen:
Bei alten Autos (Oldtimer) ohne Motormanagementsystem, also ohne Katalysator und Lambdaregelung, kommt ein ungeregeltes LPG-System zum Einsatz. Dieses konventionelle System wurde bis 1990 verwendet, da zu dieser Zeit die Umweltanforderungen strenger wurden. Außerdem gab es beim ungeregelten System mehr Probleme mit Rückzündungen. Eine Regelstrecke, wie sie heute noch verwendet wird, ist mit einer elektronischen Steuereinheit ausgestattet. Mit Hilfe der Lambdasonde kann eine genauere Gasmenge eingespritzt werden. Der Katalysator wandelt schädliche Abgase in weniger schädliche um.
Autogas und Gastank:
Die Zusammensetzung von Autogas variiert zwischen 30 % Propan und 70 % Butan im Sommer und bis zu 70 % Propan und 30 % Butan im Winter. Butan verlässt den Tank nicht mehr mit einer Temperatur von -10 Grad, da der Dampfdruck zu niedrig ist, sodass der Anteil im Winter niedriger sein muss als im Sommer. Dies erfolgt automatisch an den Tankstellen. Wenn das Auto sehr wenig gefahren wird, kann es zu Kraftstoffproblemen kommen, da die Zusammensetzung im Tank noch aus einer wärmeren Zeit stammt.
Das flüssige Autogas wird im Tank gespeichert. Das Gas hat einen maximalen Arbeitsdruck von 2500 kPa (25 bar).
Ein Tank mit flüssigem Flüssiggas sollte niemals zu 100 % gefüllt sein, da sonst nicht genügend Platz für die Ausdehnung des Gases beim Erhitzen vorhanden ist. Der Gastank ist so konzipiert, dass er nur zu 80 % gefüllt werden kann. Das flüssige Autogas verlässt den Tank über das elektromagnetische Entnahmeventil, das beim Starten des Motors öffnet. Dabei strömt das flüssige Autogas durch das Rohr zum Gasventil. Mehr dazu später auf dieser Seite.
Nach der Herstellung des Tanks wird das Herstellungsdatum in den Tank eingestanzt. Der Tank wird für die nächsten 10 Jahre in einem guten Zustand sein. Gastanks werden auf einen Druck von 3000 kPa (30 bar) getestet. Der Berstdruck eines Gastanks beträgt 10.000 kPa (100 bar). Um die Gliedmaßen wird eine gasdichte Box gelegt, die sogenannte Gliedmaßenbox. Über einen Belüftungsschlauch ist die Anhängebox mit der Außenluft verbunden. Der Anhangkasten hat die Aufgabe, im Falle einer Leckage die vorhandenen Leckagegase an die Außenluft abzuleiten. Diese Leckagegase dürfen auf keinen Fall in den Innenraum gelangen.
Die Gastanks sind mit Spanngurten an einem Stahl-Hilfsrahmen befestigt. Dieser Stahl-Hilfsrahmen wird mit der Karosserie des Autos verschraubt. Zum Schutz wurden zwischen Tank und Spanngurten Kunststoffstreifen angebracht. Der Gastank darf nicht auf andere Weise mit der Karosserie verbunden werden!
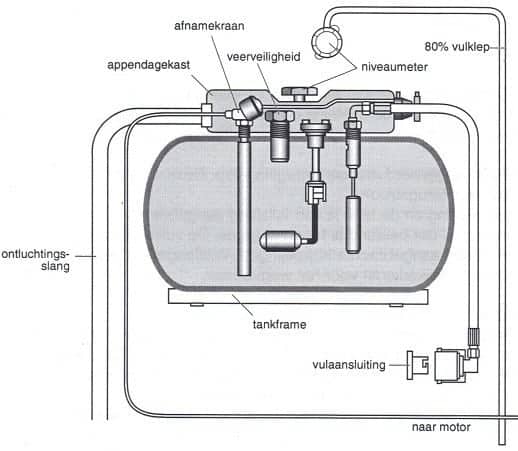
Füllanschluss:
Im Füllanschluss befindet sich ein Gewinde. Darin kann ein Adapter (Adapter) eingeschraubt werden. Dies kann beim Tanken im Ausland erforderlich sein. Das äußere Füllventil ist mit einem Rückschlagventil ausgestattet, das ein Zurückströmen des Gases nach dem Befüllen verhindert. Die Pumpe an der Tankstelle pumpt das unter Druck stehende Gas durch diesen Füllanschluss. Das Gas strömt über den Füllschlauch über den Füllanschluss zum Gastank.
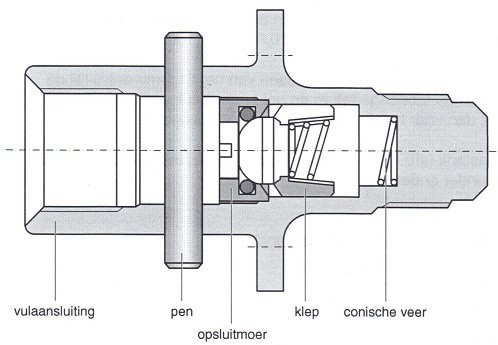
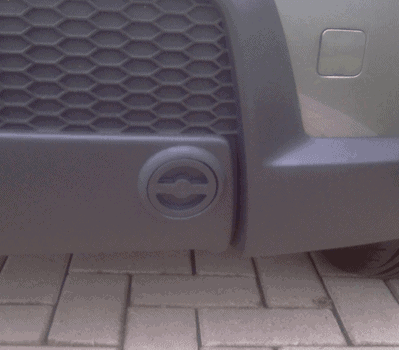
Gasventil:
Das Gasventil wird so nah wie möglich am Verdampfer montiert. Das Gasabsperrventil wird aktiviert, wenn die Zündung eingeschaltet und der Kraftstoffwahlschalter auf Gas gestellt ist. Die Steuereinheit steuert dieses Gasventil. Die Regelung wird gestoppt, wenn der Motor abgestellt wird. Das Autogas, das aus dem Gastank in das Gasventil gelangt, strömt durch den Filter. Wenn die Spule nicht mit Strom versorgt wird, verschließt das Ventil den Durchgang zum Verdampfer. Über die Bohrung „A“ gelangt das Flüssiggas dann in den Raum um und über dem Ventil. Da das Flüssiggas auf das Ventil drückt, ist der Durchgang zum Verdampfer fest verschlossen. Sobald die Spule bestromt wird, wird der Weicheisenkern magnetisch. Der Magnetismus zieht das Ventil nach oben. Der Durchgang zum Verdampfer ist nun geöffnet, so dass Autogas zum Verdampfer strömen kann. Sobald der Motor abbremst, unterbricht das Gasventil vorübergehend die Gaszufuhr, bis der Fahrer wieder Gas gibt.
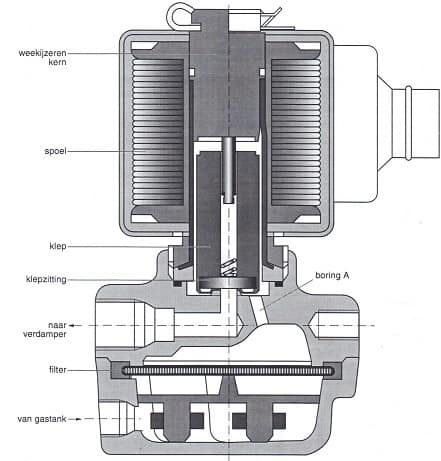
Kraftstoffabsperrventil:
Beim Fahren mit Gas wird die Benzinzufuhr abgeschaltet. In diesem Moment ist die Spule nicht erregt und das Ventil verschließt den Durchgang. Beim erneuten Wechsel von Gas auf Benzin wird die Spule bestromt und der Weicheisenkern wird magnetisch. Dadurch wird das Ventil nach oben gezogen, sodass das Benzin durchströmen kann.
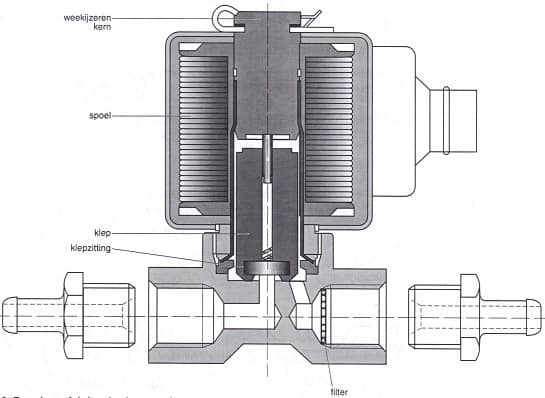
Umstellung von Benzin auf Gas:
Wenn Sie mit Benzin starten und auf Gas umstellen, erfolgt dieser Wechsel nicht sofort. Der Motor läuft vorübergehend mit beiden Kraftstoffen. Dadurch ist ein reibungsloser Übergang von Benzin auf Gas gewährleistet. Diese Situation wird als „doppelte Laufzeit“ bezeichnet.
Das Steuergerät bestimmt, wie lange der Motor mit beiden Kraftstoffen gleichzeitig läuft. Bei kaltem Motor ist dies länger als bei warmem Motor, da die Kraftstoffverdunstung bei kalter Außenluft schlechter ist. Nach einigen Minuten (system- und temperaturabhängig) wird die Kraftstoffzufuhr über das Kraftstoffabsperrventil vollständig abgeschaltet.
Funktionsweise des Verdampfers:
Um die Funktionsweise des Verdampfers möglichst deutlich zu machen, ist der Verdampfer im Bild möglichst einfach gezeichnet. Später auf dieser Seite wird eine Erklärung zu einem echten (EGI-)Verdampfer gegeben, der viel schwieriger ist. Deshalb wird zunächst der einfache Verdampfer erklärt, um die Grundlagen zu verdeutlichen.
Die Aufgabe des Verdampfers besteht darin, das flüssige Autogas im Tank gasförmig zu machen. Das Flüssiggas muss verdampft werden (daher der Name Verdampfer). Zum Verdampfen des Flüssiggases wird Wärme benötigt. Diese Wärme wird dem Kühlmittel entzogen. Diese wird vom Motor erwärmt und beträgt daher bei betriebswarmem Motor etwa 90 Grad. Wichtig ist, dass der Verdampfer möglichst schnell aufheizt, deshalb wird das Kühlmittel vor dem Thermostat abgelassen. Dies ist auch mit dem Kühlkreislauf des Heizgeräts möglich, da diese Zuleitung ebenfalls vor dem Thermostat angeschlossen ist.
Da der Verdampfer reine Wärme benötigt, ist es logisch, dass der Motor zunächst warmlaufen muss, bevor der Verdampfungsprozess beginnen kann. Das ist auch der Grund, warum man nicht direkt mit Gas starten kann. Beim Kaltstart läuft der Motor in den ersten Minuten mit Benzin, bevor das System auf Gas umschaltet.
Theoretischer Betrieb des Verdampfers:
Raum A ist der Raum des ersten Treppenhauses, Raum C ist der Raum des zweiten Treppenhauses.
In den Räumen B und D herrscht der Referenzdruck, in diesem Fall der Außenluftdruck.
Gasventil offen, Motor läuft nicht:
Das flüssige Flüssiggas strömt vom Gastank am Ventil der 1. Stufe vorbei in den Raum A. Das Flüssiggas geht dabei vom flüssigen in den gasförmigen Zustand über.
Das Flüssiggas baut im Raum A einen Druck auf. Dieser Druck drückt die Membran der 1. Stufe nach links. Feder 1 wird komprimiert, während Feder 2 entspannt. Wenn der Druck im Raum A etwa 135 kPa beträgt, ist die Membran der 1. Stufe so weit nach links bewegt, dass das Ventil der 1. Stufe schließt. Es fließt nun kein Flüssiggas mehr zum Raum A. Die Feder 3 sorgt dafür, dass das Ventil der 2. Stufe in diesem Zustand geschlossen bleibt.
Gasventil geöffnet, Motor läuft:
Bei laufendem Motor erzeugt die Ansaugluft an der Ausströmöffnung des Gas-Luft-Mischers einen Unterdruck. Dieser Unterdruck gelangt über den Trocknungsgasschlauch zum Raum C (die 2. Stufe) des Verdampfers/Druckreglers. Der Referenzdruck im Raum D bewirkt nun, dass sich die Membran der zweiten Stufe nach links bewegt. Feder 3 wird komprimiert und das Ventil der zweiten Stufe öffnet. Autogas strömt nun von Raum A nach Raum C und von dort zum Motor. Da Flüssiggas von Raum A nach Raum C fließt, sinkt der Druck in Raum A. Das Ventil der ersten Stufe öffnet sich, sodass Flüssiggas wieder vom Tank in Raum A strömt. Das am Ventil der zweiten Stufe vorbei zum Raum C strömende Flüssiggas baut im Raum C einen Druck auf. Abhängig vom Kraftstoffbedarf des Motors nimmt die Membran der zweiten Stufe eine bestimmte Position ein, sodass der Durchgang des Ventils der zweiten Stufe zunimmt oder abnimmt. Je größer der Unterdruck an den Ausströmöffnungen des Gas-Luft-Mischers ist, desto mehr Flüssiggas kann zum Motor strömen. Es stellt sich eine Gleichgewichtssituation ein, bei der je nach Unterdruck an den Ausströmöffnungen des Gas-Luft-Mischers mehr oder weniger Gas an den Ventilen der ersten und zweiten Stufe vorbeiströmt.

System mit Schrittmotor mit Trocknungsgasschlauch (AMS):
Dies ist das AMS-System von Vialle. Der Tank enthält flüssiges Autogas. Der Verdampfer/Druckregler sorgt dafür, dass das Gas beim Austritt aus dem Tank verdampft und der Druck reduziert wird. Die den Verdampfer verlassende Gasmenge wird durch die Venturidüse im Gas-Luft-Mischer gesteuert, wodurch ein Unterdruck entsteht. Je größer der Unterdruck, desto mehr Flüssiggas wird angesaugt. Der Unterdruck ist abhängig von der Drehzahl und Belastung des Motors (aufgrund der Luftgeschwindigkeit). Je mehr Umdrehungen man macht, desto mehr Gas wird angesaugt. Dies ist jedoch nicht wirklich korrekt. Um genau die Gasmenge zu liefern, die der Motor benötigt, ist eine Feineinstellung erforderlich. Das richtige Mischungsverhältnis wurde anhand der Lambdasondenmessung ermittelt.
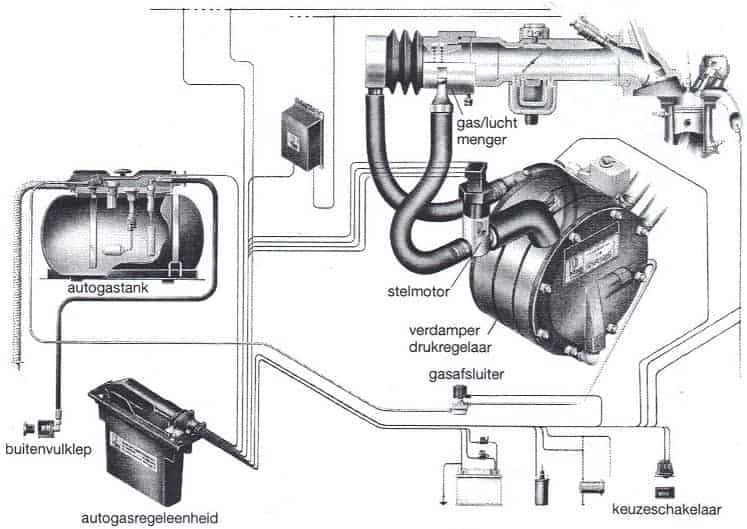
Wurde zu wenig Gas eingespritzt, ist das Gemisch mager (Lambda > 1). Bei zu viel Gas ist das Gemisch zu fett (Lambda < 1). (Das >-Zeichen bedeutet größer als und < bedeutet kleiner als). Die Lambdasonde wird dies in den Abgasen messen. Das Motormanagement erkennt somit ein zu fettes oder zu schlechtes Gemisch und steuert den Schrittmotor an. Der Schrittmotor vergrößert oder verkleinert dann den Gasdurchgang. Dieser Schrittmotor wird üblicherweise am Verdampfer angebracht. Bei einem Kaltstart befindet sich dieser Schrittmotor in Neutralstellung und läuft noch nicht. Der Motor läuft immer noch in einer „Open-Loop“-Situation. Das bedeutet, dass das Lambdasondensignal noch nicht genutzt wird, da die Kaltstartanreicherung noch aktiv ist. Der Nachteil des AMS-Systems besteht darin, dass es sich um eine Single-Point-Injection handelt. Das Gas wird vor der Drosselklappe eingespritzt und mit der Luft auf die verschiedenen Zylinder verteilt. Aufgrund der großen Gasmenge im Einlassrohr besteht eine große Gefahr einer Rückzündung.
Dampfgasinjektion (VSI/EGI):
Dies ist die Vapour Sequential Injection (VSI) oder Electronic Vapour Gas Injection (EGI). Der Einfachheit halber heißt es jetzt nur noch EGI. Das Dampfgas-Injektionssystem ist ein Mehrpunkt-Injektionssystem, das über eine Steuereinheit gesteuert wird. Die Einspritzung kann nun pro Zylinder statt zentral vor der Drosselklappe erfolgen. Dies kann mit einem 4-Zylinder-Motor geschehen, aber auch problemlos mit einem 6- oder 8-Zylinder-Motor. Das Gas wird kurz vor dem Einlassventil eingespritzt. Die Wahrscheinlichkeit einer Fehlzündung ist jetzt im Vergleich zum AMS-System viel geringer. Bei dieser Art der Gasinstallation muss zum Starten des Motors immer Benzin verwendet werden. Nach kurzer Zeit schaltet sich die Gasanlage automatisch ein.
Operation:
Das Flüssiggas kommt in gasförmigem Zustand aus dem Verdampfer. Der Druck wurde durch den Druckregler im Verdampfer reduziert. Das Gas fließt dann zum Verteilerhaus. Das Verteilergehäuse dosiert die Gasmenge und verteilt sie über die Steuerschlitze auf die Injektoren. Die Einspritzdüsen sprühen das dampfförmige Gas in den Ansaugkrümmer, kurz vor dem Einlassventil.
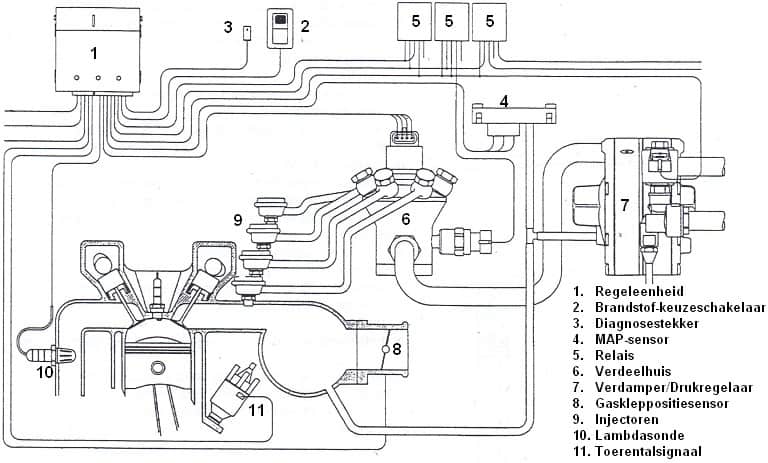
Funktionsweise des EGI-Verdampfers:
Der folgende Text bezieht sich auf das Bild unten.
- Betrieb der ersten Stufe:
Im drucklosen Zustand Feder 6 gegen Membran 7 den Hebel gegen die Feder 8 nach unten drücken und das Ventil der 1. Stufe freigeben 3 ist offen.
Wenn das Gas an der Einlasstülle ist 1 Wenn Gas eindringt, zerbricht das Gas die Membran 7 gegen die Feder 6 hochdrücken. Der Siphon 4 ist jetzt freigegeben, und Feder 8 drückt den Hebel nach oben. Dadurch schließt das Ventil der 1. Stufe 3.An der Oberseite der Membran 7 Im Motor herrscht Unterdruck, wodurch auch der Druck in der 1. Stufe vom Motorunterdruck abhängig wird. Der Druck in der 1. Stufe kann mittels Einstellschraube eingestellt werden 5. Druck 1. Stufe = Angepasster Druck 1. Stufe – Motorvakuum.
- Betrieb der zweiten Stufe:
Das Gas der ersten Stufe kann zunächst durch die freigegebene Öffnung durch das Ventil der zweiten Stufe strömen 13. Das Gas drückt dann gegen die Feder 11 und Membran 10, was das Ventil der 2. Stufe verursacht 13 bis zum Frühjahr 14 Schlampe.
Auf der Unterseite der Membran 10 Im Motor herrscht Unterdruck, das heißt, der Druck in der 2. Stufe ist vom Unterdruck des Motors abhängig. Der Druck in der 2. Stufe kann mittels Einstellschraube eingestellt werden 12.
Druck 2. Stufe = Angepasster Druck 2. Stufe – Motorvakuum.

- Überdruckschutz 1. Stufe:
Wenn der Druck in der 1. Stufe zu hoch wird, löst sich die Membran 7 zusammen mit Membranplatte 19 nach oben bewegen.
Wenn die Membranachse 18 gegen die Einstellschraube 17 kommt zur Ruhe, die Membranachse kann 18 nicht weiter oben.
Membran 7 bewegt sich mit Membranplatte 19 weiter oben, wodurch eine Membranplatte entsteht 19 am schmaleren Teil der Membranachse 18 werde mich hinlegen. Hier entsteht eine Öffnung, durch die das Gas der 1. Stufe durch den Weltraum gelangt 16, Kanal 20 und Krümmerdrucktülle 15 zum Ansaugkrümmer des Motors.
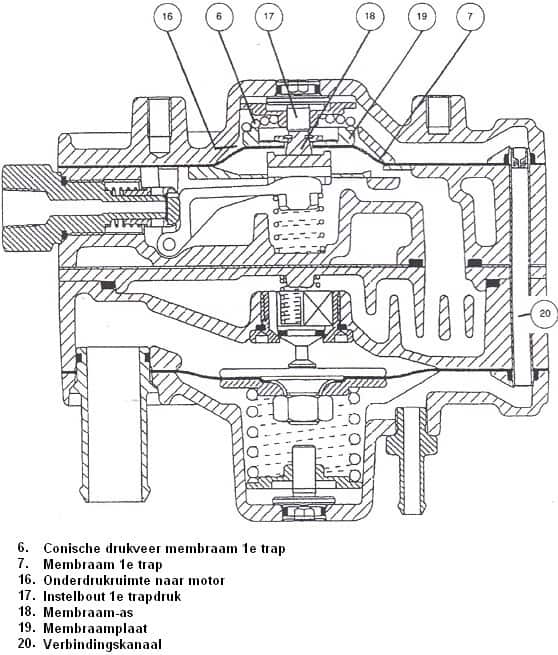
- Rückmeldung:
Über einen Kanal kann der Gasdruck der 1. Stufe zugeführt werden 22 unter dem Kolben 23 zu kommen.
Dieser Gasdruck wirkt also unten auf den Kolben 23, entgegengesetzt zum Gasdruck der 1. Stufe am Ventil der 2. Stufe 21.
Jetzt liegt der Gasdruck der 1. Stufe am Ventil der 2. Stufe an 21 keinen Einfluss mehr auf die Öffnung des Ventils der 2. Stufe 21, da der Gasdruck der 1. Stufe unterhalb des Kolbens liegt 23 ist gegensätzlich ausgerichtet.
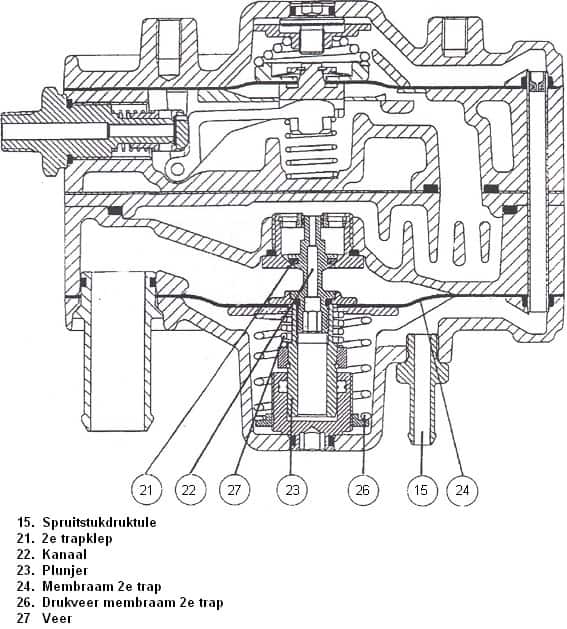
Flüssiggasinjektion (LPi)
LPi bedeutet: Flüssigpropan-Injektion). Bei der Flüssiggaseinspritzung wird Autogas flüssig eingeblasen. In diesem System gibt es also keinen Verdampfer.
Da das Flüssiggas nicht verdampft werden muss, können Sie einfach mit Gas beginnen. Das Benzineinspritzsystem wird dadurch faktisch außer Betrieb gesetzt. Dies hat jedoch den Nachteil, dass das Benzineinspritzsystem durch seltenen Gebrauch verschmutzen kann. Daher empfiehlt es sich, gelegentlich eine Zeit lang mit Benzin zu fahren. Das LPi-System versucht, dem Benzineinspritzsystem so weit wie möglich anzunähern. Das flüssige Autogas wird über die Einspritzdüsen am Einlassventil eingespritzt (genau wie bei indirekt eingespritzten Benzinmotoren).
Der Verdampfer und der Gas-Luft-Mischer wurden durch den Kupplungsblock und die Injektoren ersetzt. Zur Förderung des flüssigen Autogases ist im Tank eine Pumpe eingebaut. Die Steuerung der Flüssigkeitseinspritzung erfolgt über das bestehende Motormanagementsystem, das seine selbstlernenden Eigenschaften vollständig behält und nutzt. Das LPi-System nutzt lediglich das Signal der Öffnungszeit der Benzineinspritzdüse und wandelt es in LPG um. Flüssiggas lässt sich sehr genau dosieren. Besser als Gas in Dampfform.
Das LPi-System folgt der Einspritzstrategie des Benzinsteuergeräts. Alle Optionen wie Kraftstoffabschaltung beim Verzögern, Geschwindigkeitsbegrenzung, Volllastanreicherung und Lambadaregelung werden auch mit Flüssiggas betrieben. Mit LPi hat der Motor keinen Leistungsverlust. Dies ist auf den fehlenden Luftverdrängungseffekt zurückzuführen, der bei der Dampfdosierung bestehen bleibt. Durch den Luftverdrängungseffekt sinkt der Füllstand des Motors um ca. 6 %. Die Flüssigkeitseinspritzung sorgt außerdem für einen kühlenden Effekt bei der Verdampfung des Gases im Zylinder. Dadurch wird ein besserer Füllgrad erreicht. Dies führt auch zu einer besseren Motorleistung. Der Kraftstoffverbrauch ist immer noch höher als beim Antrieb desselben Motors mit Benzin, da pro kg Benzin weniger Verbrennungsenergie anfällt als in einem kg Benzin.
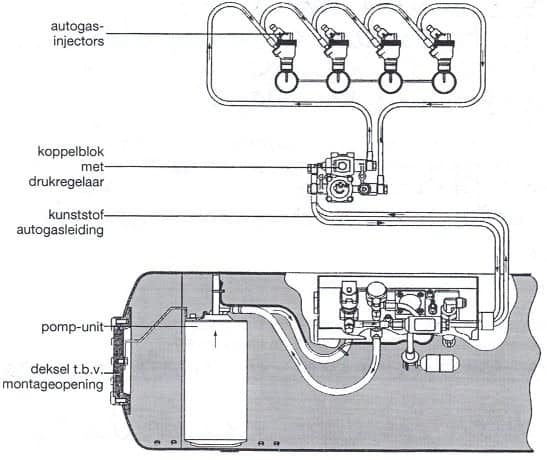
Um das Flüssiggas in flüssiger Form einzuspritzen, ist ein hoher Systemdruck erforderlich. Der Systemdruck wird von der Membranpumpe im Tank bereitgestellt. Dieser pumpt das Flüssiggas über den Kupplungsblock zu den Flüssiggas-Injektoren. Der Systemdruck wird durch den Druckregler auf 5 bar über dem Tankdruck eingestellt.
Durch Erhitzen kann es zur Bildung von Dampfblasen in den Rohren kommen. Dampf ist komprimierbar und kann daher nicht präzise injiziert werden. Durch das Umpumpen des flüssigen Flüssiggases unter Druck wird eine Erwärmung und damit die Bildung von Dämpfen im Rohr verhindert. Auch die Rohre bestehen aus Kunststoff und sind hitzeisoliert.
Am Rücklaufrohr ist außerdem ein Filter montiert, der eventuelle Verunreinigungen und Metallpartikel zurückhalten muss.
Koppelblock (LPi):
Der Kupplungsblock stellt die Verbindung zwischen Tank und den Injektoren her (siehe Bild unten). Im Kupplungsblock ist ein elektromagnetisches Ventil enthalten, das gleichzeitig mit dem Entnahmeventil am Tank öffnet und schließt. Der Druckregler (der normalerweise im Lieferumfang des Verdampfers enthalten ist) und der Drucksensor sind ebenfalls im Kupplungsblock montiert. Am Koppelblock befinden sich 4 Anschlüsse. Die flexiblen Hochdruckleitungen werden mit einer Hohlschraube am Kupplungsblock befestigt. Aufgrund des Flüssiggasflusses dürfen die Anschlüsse nicht vertauscht werden. Im Falle eines Defekts muss der Kupplungsblock komplett ausgetauscht werden, da er auf keinen Fall zerlegt werden darf.
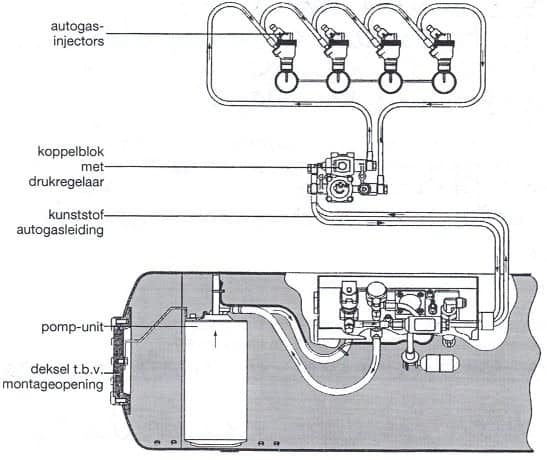
Injektoren (LPi):
Zur Einspritzung des flüssigen Autogases werden „Bottom-Feed-Injektoren“ eingesetzt. Dieser Injektortyp hat (im Gegensatz zu Top-Feed-Injektoren) den Vorteil, dass die Wärme der Injektorspule nicht zu einer Erwärmung des Autogases führt. Außerdem ist im Injektor fast kein LPG-Vorrat mehr vorhanden. Die Einspritzspule hat einen Widerstand von 1,8 Ohm. Um zu verhindern, dass grober Montageschmutz in den Injektor gelangt, ist vor dem Gaseinlass des Bottom-Feed-Injektors ein Filter montiert.
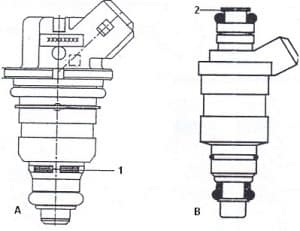
Die Injektoren sind in einem universellen Injektorhalter untergebracht. Die Abdichtung erfolgt durch O-Ringe. Der Injektor wird durch einen verschraubten Ring gehalten. Je nach Platzierung am Verteiler wird das Gas durch die Abflussrohre geleitet (siehe Teil 9 in der Abbildung).
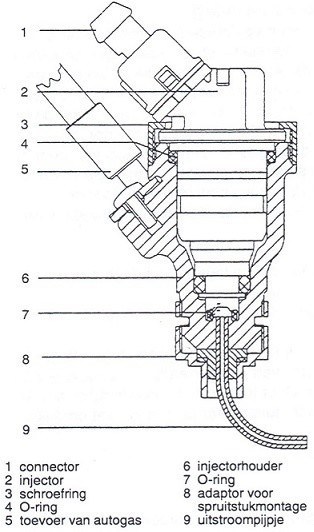