Tópicos:
- Determinar e instalar atuadores para o sistema de gerenciamento do motor
- Injetores de combustível
- Escolhendo injetores adequados
- Instalando os injetores no coletor de admissão
- Inflamação
- Preparando com a ignição convencional
- Bobina de ignição para o sistema de gerenciamento do motor
- Acúmulo de corrente na bobina primária
- Avanço de ignição
- corpo do acelerador
- Configuração de teste do motor de passo com simulador
- Configurações do motor de passo
- Circuito da bomba de combustível
- Conclusão do trabalho mecânico
Determinação e instalação de atuadores para o sistema de gerenciamento do motor:
Os atuadores que serão controlados com o MegaSquirt são os injetores, bobina de ignição, bomba de combustível e motor de passo para marcha lenta. Este capítulo descreve o processo no qual os atuadores foram testados e instalados no bloco do motor e a seleção feita.
Injetores de combustível:
O MegaSquirt controla os injetores. Os injetores estão conectados ao terra. Com um componente ligado à terra, existe uma tensão de alimentação, mas a corrente só flui quando a terra está ligada. Neste caso, o injetor só injetará quando a ECU MegaSquirt ligar à terra. Assim que a ativação for interrompida, o injetor para de injetar. A quantidade de combustível a ser injetada é determinada com base na tabela VE e na tabela AFR.
Um MOS FET liga e desliga o injetor, fazendo com que o combustível seja injetado. A quantidade de combustível determinada pelo MegaSquirt depende de vários fatores:
- A lei dos gases ideais que relaciona a quantidade de ar com sua pressão, volume e temperatura;
- Valores medidos pelos sensores do bloco do motor: pressão no coletor de admissão (sensor MAP), temperatura do líquido refrigerante e do ar de admissão, velocidade do virabrequim e dados do sensor de posição do acelerador;
• Parâmetros de ajuste: quantidade de combustível necessária, grau de enchimento (VE), tempo de abertura dos injetores e enriquecimento sob determinadas condições.
O tempo de injeção deve ser o maior possível com o motor em marcha lenta para obter uma boa dosagem de combustível. Portanto, não é qualquer injetor que pode ser usado no motor. As propriedades dos diferentes tipos de injetores devem ser comparadas e os cálculos devem fornecer informações sobre a quantidade de combustível necessária para o motor em questão. Também houve escolha entre injetores de alta e baixa impedância. Os injetores de baixa impedância são adequados para motores onde é necessária uma abertura muito rápida da agulha do injetor. A resistência típica é de 4 ohms. A desvantagem desses injetores é a alta corrente. O desenvolvimento de calor que isto cria no MegaSquirt é indesejável. É possível usar injetores de baixa impedância montando IGBTs especiais em uma placa condutora de calor na carcaça do MegaSquirt. Decidiu-se usar injetores de alta impedância. Há menos desenvolvimento de calor e esses IGBTs não são usados.
O tamanho da passagem (vazão) é muito importante para determinar a quantidade correta de injeção e, portanto, o controle. Se você escolher injetores muito grandes, o tempo de injeção em marcha lenta será tão curto que o motor poderá funcionar irregularmente. A quantidade de injeção deve ser suficiente para injetar todo o combustível no tempo disponível. A quantidade de injeção é indicada como tempo de injeção em milissegundos. Uma carga alta é assumida em uma rotação alta do motor. Isto está em um MAP de 100 kPa. O fluxo necessário do injetor pode ser calculado com base nas propriedades do motor. O fluxo do injetor indica quantos mililitros de combustível são injetados por minuto.
Escolhendo os injetores adequados:
Injetores de três tipos diferentes foram disponibilizados para o projeto. A pesquisa mostrou qual tipo de injetor era mais adequado para uso neste projeto.
Cada tipo de injetor possui uma vazão diferente; o rendimento após um minuto de injeção varia de acordo com o tipo. Antes de os injetores serem testados, eles passaram por limpeza em banho ultrassônico. Com este método de limpeza, o injetor é limpo por dentro e por fora usando vibrações ultrassônicas e um fluido de teste especial, para que quaisquer resíduos de sujeira antigos não possam influenciar a medição do fluxo ou o padrão de injeção. Durante a limpeza ultrassônica, os injetores foram abertos e fechados continuamente e o padrão de injeção de cada injetor foi examinado; esta era uma bela névoa. Ao fechar, não foram visíveis anormalidades, como formação de gotas ou jato desviado. Após limpeza e testes ultrassônicos, os O-rings foram substituídos para garantir uma boa vedação quando montados no coletor de admissão.
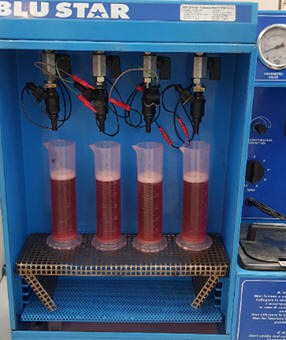
Usando uma configuração de teste (veja a imagem acima), os injetores podem injetar em vários copos medidores, para que a quantidade de combustível injetada possa ser lida após um certo tempo. Ao controlar os injetores a uma pressão de trabalho de 3 bar, a quantidade de combustível injetado pode ser controlada. A pressão do combustível na linha de alimentação (trilho) deve ser de 3 bar e a agulha do injetor deve ser acionada por 30 ou 60 segundos com ciclo de trabalho de 100%. Após os injetores terem sido ativados por 30 segundos, os seguintes dados puderam ser inseridos:
Tipo 1: 120ml
Tipo 2: 200ml
Tipo 3: 250ml
Apenas um tipo de injetor será usado. O tamanho do injetor é determinado usando a fórmula abaixo:

O tamanho do injetor é determinado com base na potência efetiva (Pe) fornecida a uma determinada velocidade, no consumo específico de combustível de frenagem (BSFC), no número de injetores (n injetores) e no ciclo de trabalho máximo com o qual os injetores são controlados. O total é multiplicado por 10.5 para converter de libras por hora (lb/h) em ml/min.
A resposta ao cálculo indica qual injetor é adequado para esta configuração de motor. Não há problema se houver um desvio inferior a 20 ml do valor calculado. Essa diferença é compensada ajustando o software do MegaSquirt. A tabela a seguir fornece uma visão geral dos dados usados nas fórmulas:
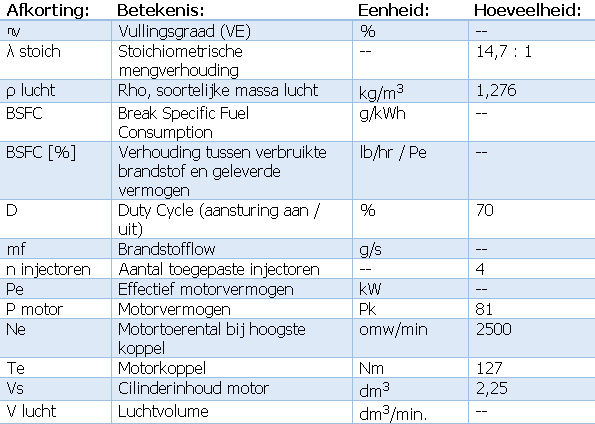
O primeiro passo é determinar o combustível injetado na velocidade de torque. Uma certa quantidade de ar é sugada a cada duas rotações do virabrequim. O grau de enchimento é mais alto na velocidade de torque. Devido às propriedades do motor (incluindo a sobreposição das válvulas), o motor enche melhor nesta velocidade e a eficiência é mais alta. Estima-se que a taxa de preenchimento fique em torno de 70%. A Fórmula 4 calcula o volume de ar que está presente no motor naquele momento.
Na fórmula 5, a quantidade de combustível injetado é calculada com base no volume de ar presente. A potência do motor alcançada na velocidade de torque é calculada na fórmula 6. A relação entre a quantidade de combustível injetado e a potência indica o BSFC nas fórmulas 7 e 8.
O BSFC real é multiplicado por 6 na fórmula 3600 para converter em kWh. O BSFC de um motor a gasolina está frequentemente entre 250 e 345 g/kWh. Quanto menor o valor, mais eficiente é o motor. A Fórmula 8 indica a relação entre o fluxo de combustível em libras/hora e a potência efetiva do motor. Esta percentagem está incluída na fórmula 9.



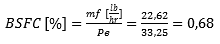

A resposta à fórmula 9 deixou claro que os injetores com vazão de 200 ml/min são adequados para uso no motor. A diferença de 7 ml é insignificante porque é compensada no software ao preencher a tabela VE.
Instalando os injetores no coletor de admissão:
O sistema de injeção controlado eletronicamente permite a remoção do carburador, que faz parte da configuração clássica. O carburador é, portanto, substituído por um corpo de borboleta (para fornecimento de ar) e quatro injetores de combustível separados. O coletor de admissão foi mantido e modificado para permitir a conversão para o sistema de gerenciamento do motor. A injeção de combustível ocorre no coletor de admissão. A decisão foi de montar os injetores o mais próximo possível da válvula de admissão. Na maioria dos casos, os fabricantes de motores de automóveis optam por montar a válvula de admissão em ângulo no coletor de admissão. O combustível é pulverizado contra a válvula de admissão. Porém, para o projeto atual, foi escolhida uma configuração em que os injetores são colocados em um ângulo de 45 graus em relação aos dutos de ar do manifold.
O coletor de admissão é feito de alumínio fundido. Decidiu-se fixar buchas de alumínio ao manifold. A usinagem manual em um bom tamanho não era uma opção, porque as buchas precisavam ter dimensões diferentes das de um tamanho de broca padrão. Isso significava que a terceirização das vans teria que ser terceirizada para uma empresa com equipamentos adequados. As buchas poderiam então ser fixadas ao coletor por soldagem TIG. A escolha de montar os injetores na vertical em vez de em ângulo foi feita pelo seguinte motivo:
- O processo de montagem: É mais fácil montar as vans em uma disposição reta e horizontal. Soldar as vans ao coletor é mais fácil porque agora é mais fácil soldar em toda a volta do que na situação em que a van está inclinada.
- Pós-processamento: Durante a soldagem as buchas tornam-se um pouco ovais. A deformação é causada pelo calor liberado durante o processo de soldagem. Isto foi levado em consideração tornando o diâmetro interno das buchas menor que o diâmetro externo dos injetores. O acabamento (alargamento) é menos arriscado: quando as buchas são arredondadas por dentro, o diâmetro é ideal para os injetores e a vedação pelos O-rings é garantida. A altura das vans é importante; o injetor não deve ser colocado muito fundo no coletor. A extremidade do injetor não deve obstruir o fluxo de ar. A partir das informações da fonte: (Banish, Engine Management, advanced tuning, 2007) foi decidido montar os injetores tão profundamente no coletor que as extremidades fiquem exatamente nos orifícios do coletor; o fluxo de ar não é prejudicado.
- Injeção de combustível: Como a mistura da névoa de combustível com o ar é ideal antes da válvula de admissão abrir, não importa muito se o injetor injeta exatamente na válvula de admissão ou logo antes no coletor de admissão.
Com a injeção simultânea, a injeção ocorre a cada rotação do virabrequim (360°). Os quatro injetores injetam simultaneamente. Isso significa que o combustível também é injetado no trato de admissão quando a válvula de admissão não está aberta. Algum tempo depois a válvula de admissão abre e o combustível ainda entra no cilindro.
Os arbustos são cortados especialmente em um torno. O diâmetro interno é ligeiramente menor que o diâmetro externo do injetor; Como a deformação ocorre durante o processo de soldagem, deve haver uma oportunidade de remoção de material durante o pós-processamento por meio de alargamento. Isto significa que o diâmetro aumenta ligeiramente porque o material é retificado. O diâmetro não deve ser muito grande, pois existe a possibilidade de o anel de borracha do injetor não conseguir mais vedar bem. Uma boa vedação é muito importante; o vazamento de ar após o injetor resulta em um vácuo menor no coletor de admissão.
A pressão negativa medida não corresponde mais à pressão negativa calculada. Isto afeta a injeção, que é determinada com base na tabela VE. A pressão negativa desempenha um papel importante nisso. Os recursos e configurações da tabela VE são descritos no próximo capítulo.
Uma borda chanfrada foi limada na parte inferior das buchas para que os formatos correspondam aos do coletor de admissão. A van deve então estar o mais vertical possível. A imagem abaixo mostra o coletor de admissão com canister durante o processo de montagem. A manga é colada de um lado, para que se possa ver claramente como a soldagem afeta o material. Não estava claro se o alumínio do manifold continha muita contaminação, o que dificultaria a soldagem. Isso acabou dando certo. Para evitar que as buchas se deslocassem de sua posição durante a soldagem, furos foram perfurados antecipadamente no manifold e as buchas foram mantidas na posição correta com um gabarito especialmente feito sob medida. Desta forma, os quatro arbustos são soldados em toda a volta. Uma verificação final mostrou que as conexões entre as buchas e o coletor estavam herméticas.
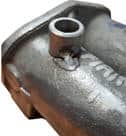
A conexão entre os injetores normalmente é formada por um trilho sólido de injetores. Este tubo com conexões, geralmente feito de liga de alumínio, é feito sob medida por um fabricante. O motor Land Rover utilizado no projeto possui dois injetores um ao lado do outro, mas o espaço entre os pares de injetores é bastante grande. As dimensões do trilho de combustível e o espaço entre os dutos de ar do coletor de admissão não correspondiam. O trilho, portanto, teve que ser ajustado.
Encurtar algumas peças e alongar outras por soldagem é muito difícil; a contaminação por combustível velho, muito difícil de remover do interior do trilho, pode causar deterioração na aderência. Por se tratar de combustível, optou-se pelo método mais seguro; as peças nas quais os injetores estão fixados são conectadas por uma mangueira de combustível de alta qualidade. Bordas costuradas foram instaladas em todas as extremidades e braçadeiras de mangueira resistentes foram usadas para evitar que as mangueiras deslizassem sobre as bordas costuradas.
A imagem abaixo mostra o coletor de admissão no momento da usinagem. A linha de abastecimento (marcada com o número 1) está conectada à saída da bomba de combustível. O combustível é fornecido à entrada dos quatro injetores sob uma pressão de 3 bar. O regulador de pressão (3) regula a pressão em função da pressão do coletor de admissão, pois a diferença de pressão entre a pressão do combustível e o vácuo no coletor de admissão deve permanecer em 3 bar. O combustível retorna ao tanque através da linha de retorno (2). Existe uma circulação contínua de combustível. A injeção só ocorre quando os injetores são controlados pela ECU MegaSquirt.
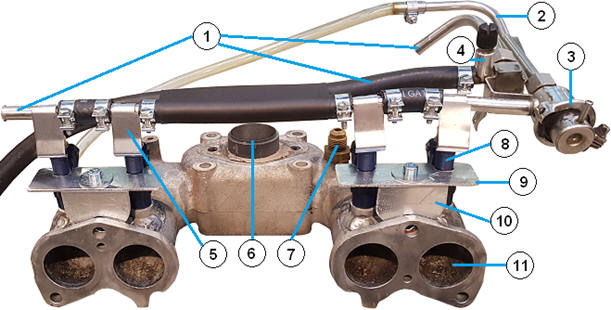
- linha de suprimentos
- linha de retorno
- regulador de pressão
- Controle de pressão
- escudo térmico
- Conexão da válvula de gás
- Conexão de pressão negativa
- Cilindro injetor 1
- Suporte do injetor A
- Suporte do injetor B
- Duto de admissão do cilindro 1
Nos automóveis de passageiros existentes, o trilho do injetor é fixado ao coletor de admissão por meio de braçadeiras ou ilhós. O trilho do injetor fixa os injetores no coletor. Como uma mangueira flexível de combustível foi escolhida como trilho injetor para este projeto, o acima mencionado não é possível. Decidiu-se, portanto, fixar os injetores no coletor de admissão com um suporte feito sob medida. Os colchetes consistem em duas partes: parte superior (suporte A) e parte inferior (suporte B).
O suporte A contém dois entalhes que podem ser deslizados sobre os injetores. Isto permite que os injetores sejam pressionados no coletor por meio dos lados planos. Ambos os suportes A possuem furos ranhurados para que a distância entre os injetores e os furos ranhurados possa ser ajustada. Os suportes A e B são aparafusados: o suporte B é preso ao mesmo pino que fixa o coletor ao motor. Um orifício com fenda permite que o suporte seja ajustado na direção vertical. Quanto mais o suporte for movido para baixo, mais firmemente o injetor ficará preso.
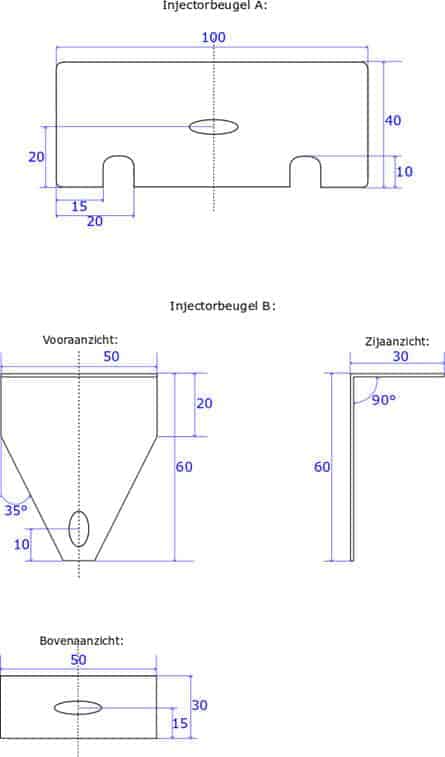
Ignição:
A ignição convencional foi substituída por um sistema de ignição controlado eletronicamente com bobina de ignição controlada pelo MegaSquirt. Para que o motor funcione plenamente com as técnicas originais, inicialmente deve-se conectar o sistema convencional com pontos de contato. Somente após algumas horas de operação é possível determinar se o motor está funcionando corretamente, após o que a instalação e o ajuste, entre outras coisas, da ignição controlada eletronicamente podem ser iniciados.
Preparando com a ignição convencional:
O motor Land Rover foi originalmente equipado com um sistema de ignição com pontos de contato, que agora também é chamado de sistema de ignição convencional. A imagem mostra este tipo de sistema de ignição.
Com pontos de contato fechados, começa o acúmulo da corrente primária. A corrente é limitada a 3 a 4 amperes pela resistência do enrolamento primário. Quando uma corrente flui através da bobina primária da bobina de ignição, um campo magnético será criado. Tanto a bobina primária (3) quanto a secundária (4) estão neste campo magnético. Quando a corrente através dos pontos de contato (10) é interrompida pelo came do disjuntor (9) no eixo distribuidor, uma tensão é induzida em ambas as bobinas. Aproximadamente 250 volts são produzidos na bobina primária. A diferença nos enrolamentos criará uma tensão de indução de 10 a 15 kV na bobina secundária. A faísca da vela é criada quando os pontos são abertos.
A tensão de indução pode ser limitada permitindo que a corrente primária flua por um tempo após a abertura dos pontos de contato. Isto é conseguido com um capacitor conectado em paralelo entre os pontos de contato. O capacitor é um elemento determinante do tempo que, dependendo da capacitância, ajusta efetivamente o nível da tensão de indução. Os pontos de contato também são impedidos de queimar.
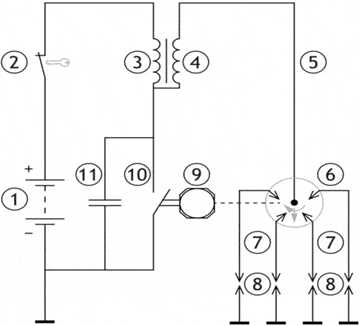
Bobina de ignição para o sistema de gerenciamento do motor:
O sistema de gerenciamento do motor controlará a bobina de ignição. A clássica bobina de ignição com distribuidor permanece no motor para servir de configuração de teste, mas não faz mais parte do funcionamento do motor de combustão. Foi escolhido um sistema de ignição sem distribuidor (bobina de ignição DIS), traduzido livremente como: “sistema de ignição sem distribuidor”. Este tipo de sistema de ignição não utiliza distribuidor. Outra opção era escolher uma bobina de ignição Coil on plug (COP). Uma bobina de ignição separada é conectada a cada vela de ignição. Uma bobina de ignição COP também é chamada de bobina de ignição de pino. A desvantagem de uma bobina de ignição COP é que a dissipação de calor é menos boa do que a de uma bobina de ignição DIS. Ao usar bobinas de ignição COP, também é necessário um sinal do sensor da árvore de cames, que não está presente no motor atual.
O dente faltante na polia do virabrequim serve como ponto de referência pelo qual o ponto de ignição é determinado. Com a bobina de ignição DIS, duas velas serão acionadas simultaneamente no momento da ignição. A bobina de ignição DIS é na verdade uma unidade na qual são montadas duas bobinas de ignição. Quando os pistões dos cilindros 1 e 4 se movem para cima, um estará ocupado com o curso de compressão e o outro com o curso de escape. Ainda assim, ambas as velas irão gerar uma faísca. A faísca criada pelo cilindro que está envolvido no curso de compressão causará uma mistura em ignição. A outra faísca, a chamada “faísca desperdiçada”, acende quando os gases de escape saem da câmara de combustão. A faísca desperdiçada é aquela que se forma quando nenhuma mistura é acesa. A energia de ignição é baixa; apesar da faísca, há pouca perda de energia. Também não é prejudicial.
A figura mostra o diagrama de funcionamento de um motor a gasolina de quatro cilindros com bobina de ignição DIS. Este diagrama de trabalho mostra duas marcas de ignição por momento de ignição; Um deles gera a faísca para acender a mistura, o outro é a faísca desperdiçada. Uma bobina de ignição DIS pode ser controlada pelo MegaSquirt com apenas dois pulsos.
Quando o curso de compressão ocorre no cilindro 1 e o curso de exaustão no cilindro 4, o MegaSquirt controla a bobina primária A através do pino 36 no DB37 (veja imagem abaixo). Este controle ocorre com base no ponto de referência do virabrequim (entre 90 e 120 graus antes do PMS). O MegaSquirt controla a bobina primária B, responsável pela formação de faísca dos cilindros 2 e 3, e é ligada 180 graus após a bobina A. Não há ponto de referência para a bobina B, mas o ponto de ignição pode ser determinado simplesmente contando os dentes na roda de pulso 36-1.
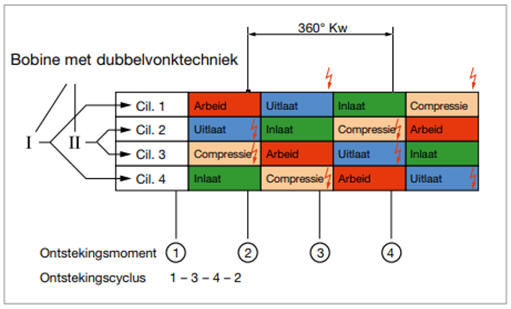
Uma resistência de 7 ohms é mostrada entre a bobina A da bobina de ignição e o pino 330 do processador. Este resistor limita a corrente e a tensão de indução do pulso de acionamento. Como esse resistor não é padrão na placa de circuito MegaSquirt, ele deve ser adaptado. À esquerda da linha vertical tracejada na imagem abaixo, é mostrado o circuito interno do MegaSquirt. Os componentes mostrados (os dois resistores de 330 Ohm e os LEDs) tiveram que ser soldados posteriormente na placa de circuito impresso.
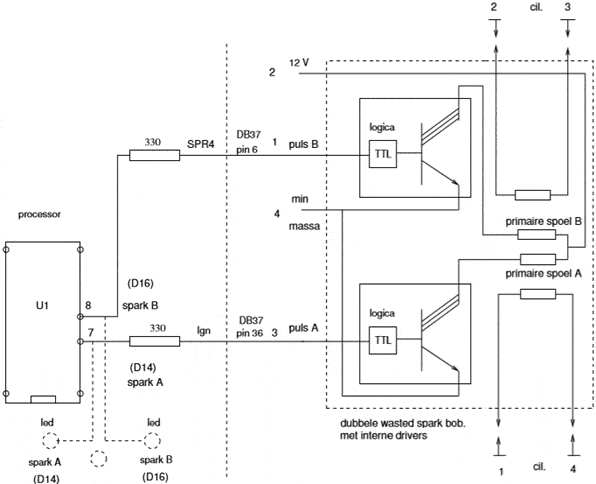
Acúmulo de corrente na bobina primária:
É importante obter informações sobre o acúmulo de corrente na bobina primária. Com isso você pode determinar não apenas a amperagem, mas também o tempo de carga da bobina de ignição. O tempo de carregamento depende de uma série de fatores que o MegaSquirt deve levar em consideração.
O coeficiente de autoindução (valor L) da bobina de ignição selecionada é 3,7mH. Juntamente com a resistência ôhmica R, são determinados a corrente primária máxima e o tempo de subida da curva. Um pequeno valor L e uma resistência garantem que a corrente aumente rapidamente após a ligação. Os dados conhecidos da bobina de ignição podem ser usados para calcular como a corrente primária é construída.
A fórmula a seguir mostra a solução geral da equação diferencial de 1ª ordem, que calcula as correntes, tempos de carga e descarga para mostrar o fenômeno de comutação como uma curva.
A equação é:

onde a constante de tempo (Tau) é calculada da seguinte forma:

A corrente máxima seria de 28 amperes de acordo com a Lei de Ohm:
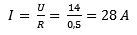
Na realidade, esta amperagem não será alcançada.
A bobina é desligada mais cedo. O motivo será explicado mais adiante. Inserir essas informações na fórmula geral fornece:
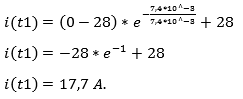
A figura mostra a curva de carga da bobina primária. Do tempo T0 a 1 Tau, a bobina é carregada a 63,2%. Esta é uma percentagem fixa para o tempo de carregamento de uma bobina. O resultado da fórmula 13 mostra que a bobina está carregada com 1 amperes a 17,7 Tau. Em t = 5 Tau o valor final foi praticamente alcançado.
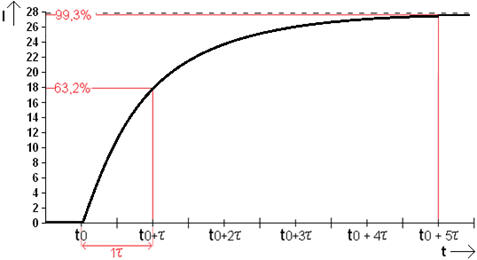
De acordo com as especificações da bobina de ignição, a corrente primária da bobina de ignição após o carregamento é de 7,5 A. A corrente não aumenta. O tempo que leva para atingir 7,5 A é chamado de tempo de permanência. O tempo de permanência depende da tensão da bateria, que neste caso é de 14 volts. Se o processo de carregamento não for ajustado, a corrente através da bobina será de no máximo 12 amperes de acordo com a fórmula 28.
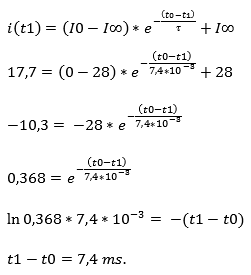
A bobina de acordo com a fórmula 14 é carregada com 7,4 A em t = 17,7 ms. O tempo real de carregamento é mais curto, porque a bobina é carregada até um máximo de 7,5 A. O tempo necessário pode ser calculado inserindo os dados conhecidos na fórmula 15.
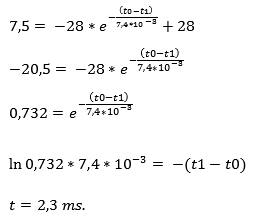
O aumento da corrente primária é interrompido em 7,5 A. Isto evita que a bobina de ignição aqueça excessiva e desnecessariamente. O mais importante é que a bobina seja carregada de maneira ideal, tanto quanto possível, no menor tempo possível. A figura mostra a curva de carga até t = 2,3 ms.
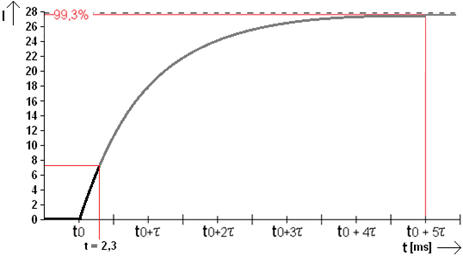
Quando a tensão da bateria cai, por exemplo ao ligar o motor, isso afeta o tempo de permanência. Em seguida, leva mais de 2,3 ms antes que 7,5 A sejam alcançados. O novo tempo de carregamento é determinado usando a fórmula já conhecida. A corrente máxima é determinada com base na tensão da bateria:
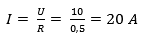
O tempo de carregamento de até 7,5 A com máximo de 20 A é calculado na fórmula 17:
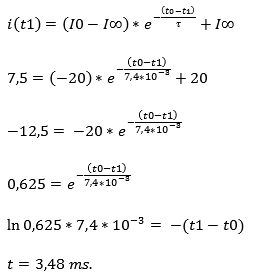
Na figura, o tempo de carregamento de 14 volts é mostrado com a linha preta e o tempo de carregamento de 10 volts é mostrado com verde. As linhas caem para 0 ao mesmo tempo; este é o ponto de ignição. Como uma tensão mais baixa da bateria requer mais tempo para carregar a bobina primária, o MegaSquirt deve ligar a alimentação primária mais cedo.
As linhas pretas (subindo e descendo) indicam o tempo de permanência com uma tensão de bateria de 14 volts. A linha verde indica o tempo de carregamento avançado com uma tensão mais baixa: isto dá Δt. O tempo real de carregamento nesse caso é Δt + 100%.
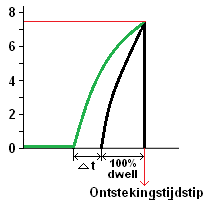
Isto será esclarecido posteriormente nesta seção com um exemplo e a figura 36. O tempo de carregamento é prolongado e o ponto de ignição permanece o mesmo. Se isso não acontecer ou não acontecer de forma suficiente, terá consequências na energia liberada durante a ignição. Neste caso, a corrente primária é desligada muito cedo, de modo que a corrente de 7,5 A não é alcançada. A extensão do tempo de carregamento da bobina primária (tempo de permanência) é, na fórmula, uma função da tensão da bateria. O cálculo do tempo de permanência em diferentes tensões fornece uma corrente máxima diferente na bobina.
Supondo que a tensão da bateria pode cair para 6 volts durante a partida e subir para 14,7 volts durante o carregamento, uma curva pode ser esboçada calculando uma série de valores intermediários. A imagem abaixo mostra a correção do tempo de permanência para a bobina de ignição DIS utilizada. Um ponto (vermelho) é colocado no gráfico para cada aumento de 2 volts. Como um tempo de permanência previamente inserido de 2,3 ms a uma tensão de 14 volts foi inserido no programa TunerStudio, um fator de correção é formado a partir desta tensão. Uma tensão de 14 volts é, portanto, 100% (sem correção).
Agora ficou claro que o tempo de carregamento aumenta em até 315% com uma tensão de bateria de 6 volts.
A tensão da bateria pode cair até 6 volts em condições desfavoráveis. Isto significa um enfraquecimento da faísca de ignição. O prolongamento do tempo de permanência (o tempo durante o qual a corrente primária flui) compensa isso, de modo que é obtida energia de ignição suficiente mesmo nesta baixa tensão. Isto significa que Δt da Figura 36 é triplicado (2,3 ms * 315% = 7,26 ms) em comparação com o tempo de permanência de 100% (2,3 ms) indicado em preto.
Os coeficientes indicados em vermelho na imagem acima podem ser copiados diretamente no programa TunerStudio.
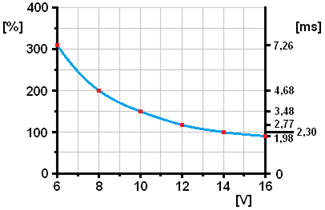
Algum tempo após a bobina primária ter sido descarregada, começa a preparação para a próxima ignição. Quanto maior a rotação do motor, mais rápido a bobina é recarregada. A Figura 37 mostra duas curvas onde a corrente primária aumenta para 8,85 A. O ponto de ignição está no ponto onde a linha cai para 0 A.
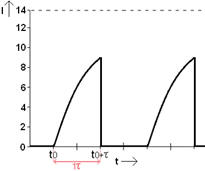
Determinando o ponto de ignição:
O sinal de ignição é determinado a partir do ponto de referência do virabrequim.
Na coroa dentada da polia do virabrequim, 36 dente dos 1 dentes foi fresado a 100 graus na frente do ponto morto superior do pistão do cilindro 1. Entre 100 e 0 graus, portanto, durante o curso de compressão, o microprocessador de o MegaSquirt pode determinar o ponto de ignição. Isso leva em conta o adiantamento.
A imagem mostra a imagem do osciloscópio de dois canais em que a imagem superior mostra o ponto de referência do virabrequim e a imagem inferior mostra o sinal de controle do MegaSquirt para a bobina de ignição DIS. O sinal de controle tem tensão de 5 volts (lógico 1) e dura aproximadamente 1,5 ms.
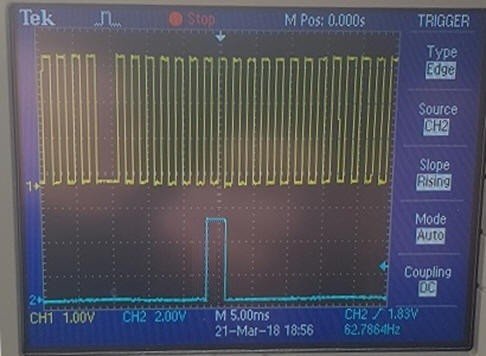
Avanço de ignição:
Sensores de detonação não são usados neste projeto. É possível processar informações de sensores de detonação, mas simplesmente instalar um sensor de detonação não é suficiente. O processamento dos sinais é complexo. O sinal de detonação deve primeiro ser convertido em um sinal sim/não ou em um sinal analógico que indique a força da detonação.
A conversão das vibrações do motor em sinal de detonação é feita por um circuito de interface. Este circuito não está presente no MegaSquirt II. Por isso foi decidido definir com segurança o avanço de carga total e de carga parcial, para que o motor não possa parar na área de detonação. A curva de avanço de carga total a ser definida deve ser determinada dentro dos limites de detonação. Os dados de avanço centrífugo e de vácuo da ignição convencional são determinados com base nos dados de fábrica do manual do motor. Os pontos podem ser plotados em um gráfico (exemplo na imagem abaixo).
A linha rosa indica o avanço mecânico original. Isto é parcialmente linear devido à construção mecânica dos pesos centrífugos. A linha preta mostra o controle do mapa no MegaSquirt; esta linha segue uma curva. É importante ficar fora das áreas de carga parcial e de carga total; portanto, o controle do mapa é limitado em carga parcial (linha vermelha) e o avanço em plena carga não aumenta mais do que na situação com avanço mecânico (linha vermelha). A disposição real do mapa segue a linha azul.
Primeiro, a curva de avanço de carga total teve que ser inserida na tabela de avanço de faísca. Em velocidades mais altas e cargas mais baixas, será necessário mais avanço. Em carga parcial, o avanço é adicionado ao avanço de carga total. A tabela de avanço de ignição completa e os ajustes de avanço com o motor frio são mostrados na página 7.
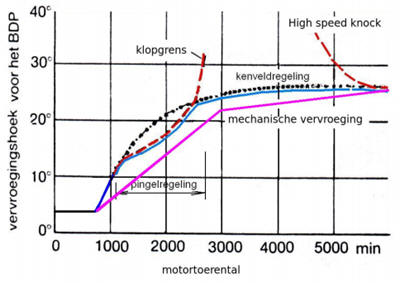
Corpo do acelerador:
O fornecimento de ar/combustível era controlado pelo carburador na condição original. Para o sistema de gerenciamento do motor, o carburador é substituído por um corpo de borboleta e quatro injetores montados no coletor de admissão. Isto proporciona uma injeção mais precisa e controlada do que com o carburador, onde uma mistura ar/combustível é formada centralmente no coletor e é dividida em quatro canais. O acelerador é aberto por um cabo Bowden operado manualmente a partir do painel de instrumentos.
Afinal, o MegaSquirt II não suporta um corpo de borboleta operado eletronicamente. É por isso que o controle por cabo Bowden é a única opção de uso.
A posição do acelerador é transmitida ao MegaSquirt por meio de uma tensão. A magnitude da tensão depende do ângulo de abertura da válvula borboleta. O sensor de posição do acelerador é um potenciômetro com tensão de alimentação de 5 volts (ver imagem). A conexão 3 e uma conexão terra 1 são necessárias. O corredor (pino 2) assume uma posição na resistência que depende da posição do acelerador. O corredor está, portanto, conectado à válvula borboleta. Quando o corredor tem que superar uma pequena distância acima da resistência (o corredor aponta para a esquerda), a resistência é baixa. Na imagem, o rotor está posicionado à direita (lado terra), o que significa que há alta resistência e, portanto, baixa tensão de sinal.
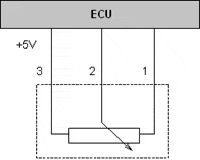
Com o corpo do acelerador utilizado, há uma tensão de 600mV no corredor quando o acelerador está fechado e uma tensão de 3,9V quando a válvula está totalmente aberta. A ECU recebe a tensão e a utiliza para calcular o ângulo de abertura da válvula borboleta. Um rápido aumento no ângulo de abertura significa que está ocorrendo aceleração; a ECU responde a isso enriquecendo brevemente. Isso é chamado de enriquecimento de aceleração. O sensor de posição do acelerador não é utilizado para determinar o enriquecimento da mistura em diferentes condições de operação; O sensor MAP é usado para esta finalidade.
Configuração de teste do motor de passo com simulador:
Após o ajuste do hardware do MegaSquirt, a breakout box poderia ser usada para verificar se o controle do motor de passo estava sendo recebido. A iluminação dos LEDs de duas cores indica que o controle está sendo realizado. As etapas nas quais o motor de passo é controlado podem ser acompanhadas observando a mudança nas cores. As cores alternam entre vermelho e amarelo. Os dados do motor de passo podem ser inseridos no menu “Idle control” no programa TunerStudio. Além do tipo (4 fios), o número de passos também pode ser definido. Isso também inclui a posição inicial na qual o motor de passo deve estar quando o motor for ligado. Além disso, o tempo pode ser definido para quanto tempo leva para ajustar uma etapa.
O número de etapas depende, entre outras coisas, da temperatura do líquido refrigerante; uma temperatura mais baixa requer uma abertura maior do motor de passo. As etapas relativas à temperatura podem ser definidas em um gráfico. O simulador pode ser usado para verificar se o motor de passo está realmente controlado corretamente. Como é verificado primeiro no simulador e não no motor, problemas podem ser evitados durante a partida ou funcionamento do motor devido a um possível problema de hardware ou software. Como a temperatura do líquido refrigerante e a rotação do motor influenciam principalmente o ângulo de abertura do motor de passo, você pode verificar se o controle está correto girando esses potenciômetros. O medidor no painel do TunerStudio exibirá o ajuste no número de etapas ajustadas.
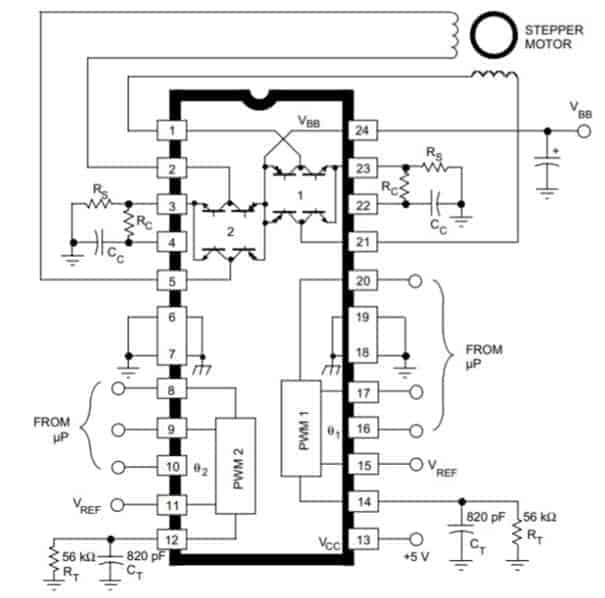
Configurações do motor de passo:
A figura mostra a tela de configurações do motor de passo utilizado para marcha lenta (controle de marcha lenta).
As etapas de ajuste do motor são determinadas previamente por meio de um Arduino. O número de passos também deve ser inserido para passar para sua posição básica (passos de retorno). O motor de passo está ativo na fase de aquecimento (algoritmo) e energiza as bobinas quando paradas (mantém a corrente entre as etapas).
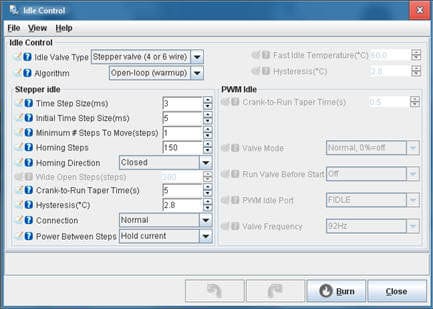
A posição do motor de passo depende da temperatura do líquido refrigerante. Ao dar partida em um motor frio, a válvula deve estar um pouco mais aberta do que ao dar partida em um motor aquecido. A imagem abaixo mostra a tela de configurações para definir os passos (Steps) em relação à temperatura do líquido refrigerante (Coolant). Quando o motor está frio, o motor de passo fica totalmente aberto enquanto o motor está em marcha lenta. Durante a fase de aquecimento, o motor de passo fecha ligeiramente.
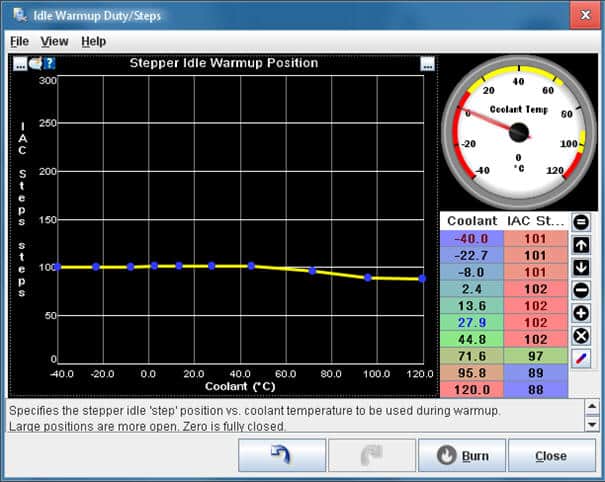
Também é possível ajustar a posição do motor de passo com base na temperatura do líquido refrigerante ao dar partida no motor. Isso é chamado de “Etapa/serviço de partida em marcha lenta”. A imagem abaixo mostra a tela de configurações.
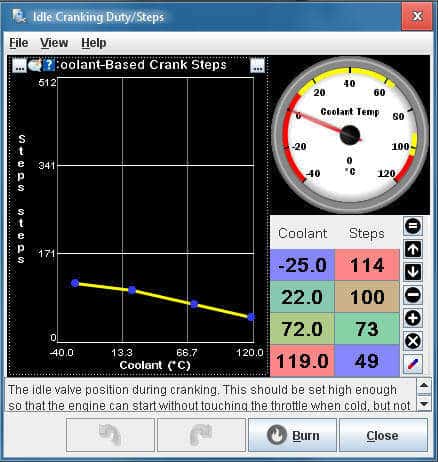
Circuito da bomba de combustível:
O MegaSquirt garante que a bomba de combustível seja ligada e desligada. O transistor Q19 na figura abaixo protege o transistor Q2 contra corrente excessiva. Se a corrente for muito alta, o transistor pode queimar. Quando a corrente através da porção coletor-emissor de Q2 e R40 aumenta, a tensão de saturação na base de Q19 é atingida. O transistor Q19 é ligado, fazendo com que a tensão base-emissor em Q2 diminua.
A conexão FP-1 PTA0 é controlada internamente pelo MegaSquirt. Um sinal de entrada do sensor de posição do virabrequim (um sensor Hall ou sensor indutivo) é necessário para controlar o circuito do transistor. Se o sinal for perdido, por exemplo, se o motor parar involuntariamente, a alimentação da bomba de combustível é imediatamente interrompida.
A saída do circuito do transistor (FP1 OUT) está conectada ao relé da bomba de combustível. O pino 85 do relé é a saída da corrente de controle. Com um relé energizado, a seção de alimentação principal (pinos 30 e 87) é comutada, para que a bomba de combustível receba uma tensão de alimentação para funcionar.
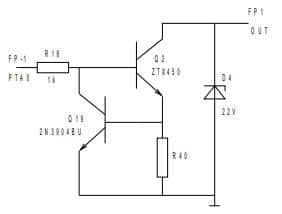
É utilizada uma bomba de combustível eletrônica com pressão operacional de 3 bar. O combustível é conduzido através do filtro de combustível até o trilho de combustível, onde a pressão está na entrada dos injetores. O injetor injetará uma quantidade pré-calculada de combustível no coletor de admissão quando um sinal vier do MegaSquirt. O controle do MegaSquirt não apenas determina a quantidade de combustível injetado, mas também a pressão do combustível no trilho.
A uma pressão mais alta no rail, uma maior quantidade de combustível será injetada com o mesmo controle. A pressão do rail deve, portanto, ser ajustada com base na pressão negativa no coletor de admissão. A diferença de pressão (∆P) deve permanecer sempre em 3 bar. A figura mostra o esquema do sistema de combustível. As linhas rosa, amarela, laranja e preta mostram as conexões elétricas. A linha vermelha indica o abastecimento de combustível e a linha azul o retorno do combustível.
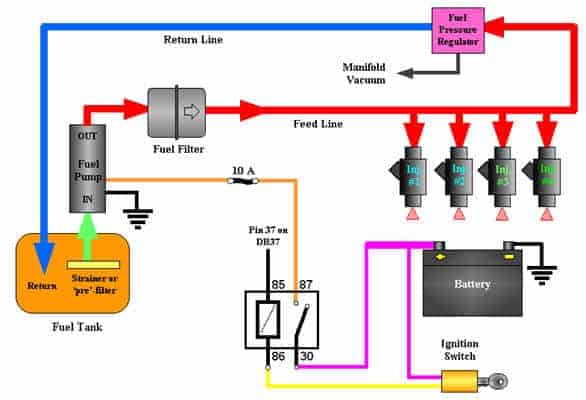
Conclusão do trabalho mecânico:
As próximas três fotos mostram o motor em fase final de modificações mecânicas.
Foto 1:
Este é o lado onde a maioria das peças aplicadas são visíveis. O painel dos controles e a ECU MegaSquirt também estão localizados aqui. Abaixo da foto há uma legenda com a descrição dos números das peças. Você pode abrir as fotos em tamanho maior clicando nelas.
- Válvula aceleradora;
- Linha de combustível para injetores;
- Tubo de conexão para válvula borboleta no coletor de admissão;
- Manômetro de combustível;
- Coletor de admissão e escapamento;
- Painel com interruptor do ventilador de refrigeração, luzes do alternador e pressão do óleo, interruptor de ignição e interruptor de aterramento;
- Mangueira de vácuo para sensor MAP;
- Sonda lambda;
- Mangueiras de combustível (alimentação e retorno) juntas em caixa retrátil;
- Unidade bomba/tanque de combustível;
- Relé da bomba de combustivel;
- MegaSquirt;
- Silenciador de escape.
Foto 2:
Esta foto mostra o outro lado do motor. Aqui você pode ver o carburador (15) e a ignição convencional (17). O objetivo desta ignição clássica é fazer com que as velas de ignição na configuração de teste (14) faísquem. É claro que isso não tem função para o motor, mas fornece informações sobre o funcionamento da ignição, como funcionava em carros clássicos.
O número 20 indica o mecanismo de freio da transmissão. A haste do tambor do freio pode ser apertada com um cabo Bowden, para que o eixo de saída da caixa de câmbio seja freado. O freio da transmissão é aplicado para carregar brevemente o motor quando uma marcha é engatada.
Foto 3:
A vista superior do motor com a configuração de teste para a ignição e o trilho de combustível são claramente visíveis aqui.
Os ajustes mecânicos foram concluídos. O motor ainda não pode ser ligado porque alguns dados devem primeiro ser inseridos no MegaSquirt.
Volgende: Ajuste da ECU MegaSquirt II.