Tópicos:
- O início do projeto
- Motor
- Caixa de velocidades
- Inspecionar, substituir e ajustar peças do motor
- Monte o motor em uma estrutura móvel
- Refrigeração
- Painel e instalação elétrica
- Bomba de combustível e tanque
- Opere o motor em uma configuração clássica
O início do projeto:
Depois que foi decidido equipar um motor com sistema de gerenciamento de motor MegaSquirt, um tipo de motor adequado foi considerado. Pacotes de conversão padrão com manuais não eram interessantes. O objetivo era utilizar um motor que atendesse às seguintes condições:
- não deve haver nenhum projeto de conversão anterior conhecido deste mecanismo;
- motor a gasolina de quatro cilindros;
- ainda não equipado com sistema de injeção e ignição eletrônica;
- a capacidade de carregar o motor.
Motor:
A busca levou a um motor de um Land Rover (série 2A) do início dos anos 70. Este motor a gasolina de quatro cilindros e 2,25 litros com três rolamentos principais foi originalmente equipado com carburador e distribuidor mecânico de ignição. A combinação deste motor Land Rover e da caixa de velocidades original foi decisiva para a escolha; Um freio de transmissão é acoplado ao eixo de saída da caixa de câmbio. O freio da transmissão, que na verdade funciona como freio de estacionamento, permite carregar o motor em funcionamento através da aplicação deste freio.
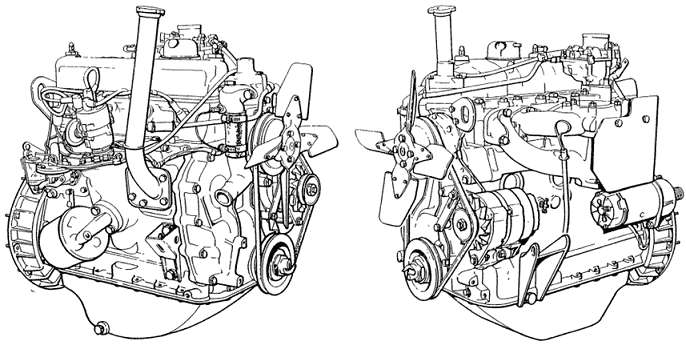
O motor provavelmente não funcionava há décadas. Naturalmente, deve ser confiável o suficiente para funcionar no sistema de gerenciamento do motor. Portanto, foi necessário primeiro inspecionar e testar minuciosamente o motor. Foram definidos os seguintes objetivos:
- Inspecionar, substituir e ajustar peças do motor;
- Monte o motor em uma estrutura móvel;
- Permitir que o motor funcione na configuração clássica;
- Instalação de componentes do sistema de gerenciamento do motor;
- Montar e preparar a ECU MegaSquirt;
- Permita que o motor funcione no sistema de gerenciamento do motor.
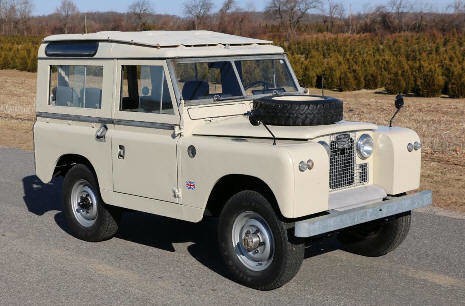
Caixa de engrenagens:
A caixa de câmbio vem de um Land Rover do exército. A cor verde realmente denuncia isso. Para formar um todo o mais original possível com o motor posteriormente, a tinta verde foi removida. O freio da transmissão ainda não está presente na foto; posteriormente, ele foi montado no eixo de saída de acordo com as instruções de fábrica.
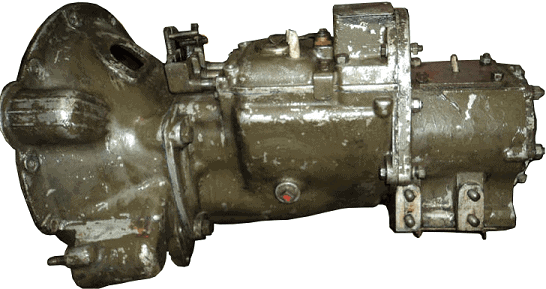
Inspecione, substitua e ajuste as peças do motor:
No início do projeto não estava claro se o motor disponibilizado era adequado para uso. Pouco se sabia sobre o bloco do motor, apenas que o motor estava parado há anos. Não ficou claro se alguma peça interna estava danificada ou mesmo - possivelmente irreparavelmente - defeituosa. Neste último caso, a substituição do motor por outro foi a única opção para retomar o projeto.
Para não concluir posteriormente que o motor estaria inutilizável, decidiu-se desmontar e revisar o motor. Os padrões de desgaste das peças foram verificados e comparados com as especificações de fábrica. As peças onde as medições estavam dentro dessas tolerâncias foram substituídas. As peças que foram rejeitadas foram substituídas. A finalidade para a qual o motor será utilizado foi levada em consideração; o motor deve ser construído com o menor custo possível para ser suficientemente confiável para a implementação do projeto e sua utilização como ferramenta de ensino-aprendizagem.
O motor é fixado ao suporte de montagem nos pontos de montagem da carcaça da caixa de câmbio. O motor pode ser girado em diferentes posições. Isto torna tanto a cabeça do cilindro como o cárter de óleo perfeitamente acessíveis para trabalhos de desmontagem. Para o bom funcionamento do motor é importante tomar precauções para garantir uma boa pressão final de compressão. Se a pressão em um ou mais cilindros for muito baixa, isso resultará em um motor com mau funcionamento e falhando. Nesse caso, o ajuste com a ignição e o sistema de injeção recém-instalados será difícil, se não impossível.
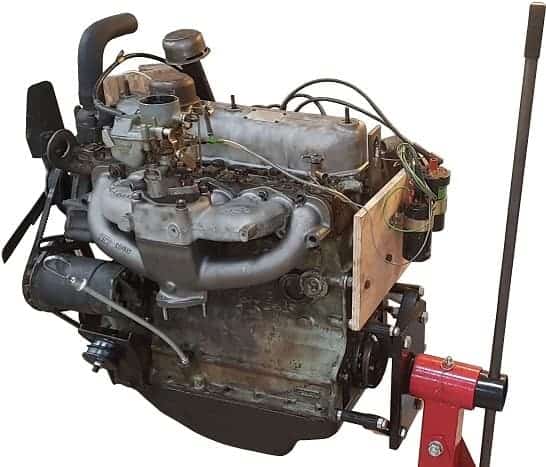
Um dos primeiros pontos de verificação são os pistões e as paredes do cilindro. Para exercer o controle adequado, os pistões tiveram que ser removidos do bloco do motor. Após a desmontagem do cabeçote e do cárter, os pistões puderam ser removidos. Os pistões foram verificados quanto à ovalização e sinais visíveis de desgaste. Os anéis do pistão também foram verificados quanto a desgaste. Anéis de pistão desgastados podem causar perda de compressão e consumo de óleo; ambas as consequências devem ser evitadas por esta verificação. Além de uma verificação óptica, também foi medida a folga entre as ranhuras do anel do pistão e o anel do pistão.
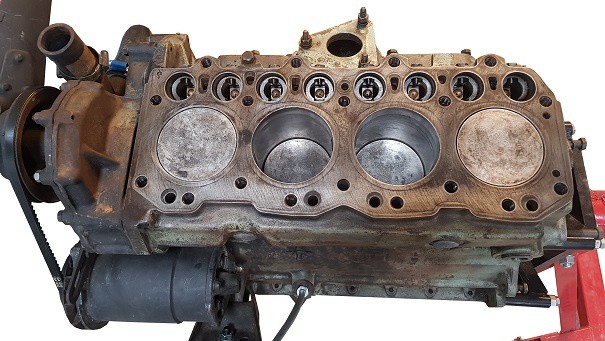
A imagem abaixo mostra uma medição onde o pistão é medido com um medidor de parafuso. Além da ovalização, também pode ser determinada a distância entre o pistão e a parede do cilindro. Uma distância muito grande significa desgaste excessivo. Para o projeto, isso significaria que outros pistões excedentes poderiam ter que ser instalados. Após avaliação visual e geométrica dos quatro pistões, constatou-se que não houve desgaste excessivo.
Após a substituição dos anéis do pistão, a folga final deve ser medida e, se necessário, ajustada para evitar a quebra do anel do pistão (devido a uma folga muito pequena ou muito grande) e para evitar perda de compressão (perdas por vazamento devido a uma folga muito grande). ). O anel do pistão é colocado no cilindro onde o diâmetro é menor. A folga da trava é medida com um calibrador de folga. Esta medida é mostrada na figura. Os anéis de pistão do cilindro 1 foram substituídos devido ao seu mau estado e tiveram que ser limados um milímetro menores; quando montadas, as pontas se tocavam.
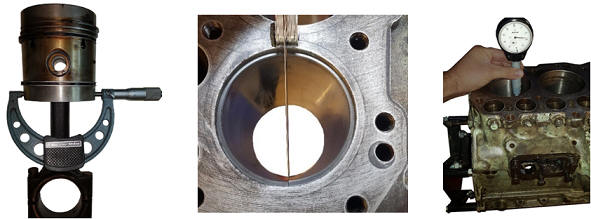
A medição do desgaste das camisas do cilindro é realizada com um objeto de medição adequado. A deflexão do ponteiro mostra o grau de desgaste. A imagem mostra a medição do cilindro 4. O diâmetro do cilindro terá aumentado, especialmente no lado onde ocorre a força da guia. As paredes do cilindro podem apresentar algum desgaste, mas o desgaste deve estar dentro das tolerâncias. Os resultados da medição mostraram que havia desgaste aceitável nas paredes do cilindro. Uma inspeção óptica das camisas do cilindro mostrou que várias partes das paredes eram lisas. As ranhuras de brunimento quase não estavam mais presentes.
As ranhuras de brunimento, uma espécie de pequenos arranhões, garantem que haja sempre uma pequena película de óleo entre o anel do pistão e a parede do cilindro. A principal tarefa desta película de óleo é a lubrificação, mas também serve como vedação e, portanto, ajuda a atingir a pressão de compressão final. Novas ranhuras de brunimento foram feitas em todas as quatro camisas do cilindro usando uma pedra de brunimento adequada. A imagem mostra esta operação. Foi feita uma tentativa de aplicar as ranhuras de brunimento transversalmente, tanto quanto possível, em um ângulo de 45 graus.
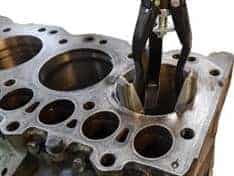
As válvulas vedam o espaço de combustão acima do pistão. Vazamento ao longo da sede da válvula causa perda de compressão; algo que deveria ser evitado. Para verificar a condição das válvulas e da sede da válvula, todas as válvulas devem primeiro ser removidas do cabeçote. A imagem mostra uma mola desmontada da válvula de admissão do cilindro 1. Os discos das válvulas do cilindro 1 estavam tão danificados que foi decidido substituir ambos.
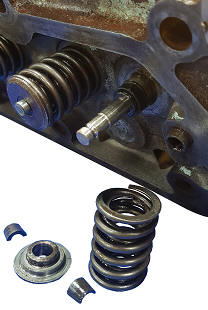
Após a desmontagem, várias sedes de válvula pareciam estar danificadas/comidas. A imagem abaixo mostra as sedes das válvulas do cilindro 1. É muito provável que o motor não tivesse funcionado corretamente se isso não tivesse sido verificado. Apenas lixar novamente as novas válvulas não seria suficiente, por isso decidiu-se fresar as sedes das válvulas.
Com um cortador de sede de válvula, uma pequena quantidade de material é removida, para que a sede da válvula fique lisa novamente. A haste do cortador é inserida na guia da válvula (veja a imagem abaixo). Isso garante que o cortador possa ser colocado diretamente no assento. Durante o processo de usinagem foram levados em consideração dois ângulos diferentes nos quais o fresamento deve ser feito. As válvulas dos cilindros 1 e 2 foram as mais afetadas. Para completar, todas as oito sedes de válvula foram usinadas. Após a fresagem, as válvulas são lixadas com um abrasivo especial para garantir a melhor vedação possível.
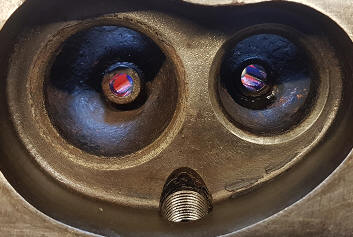
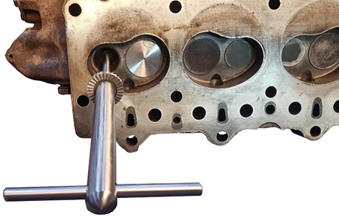
A folga axial do virabrequim com três rolamentos principais e dois rolamentos axiais é medida com um relógio comparador. Se houver muita folga axial, um rolamento axial maior poderá ser instalado se não houver defeito mecânico. A medição mostrada na imagem mostrou que a folga axial estava OK.
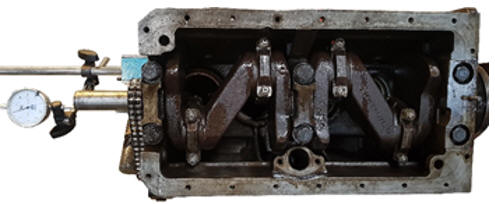
O espaço entre os mancais deslizantes do virabrequim e a biela, ou seja: a folga radial do virabrequim, é medido com plastigagem (ver figura). Plastigage é um fio plástico especial que se deforma permanentemente após a compressão. Após a montagem da capa do mancal ou biela, o plastigage deixará uma marca. A largura da impressão indica quanta folga existe entre o mancal deslizante e o virabrequim.
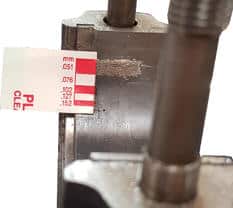
A corrente de distribuição transmite o movimento do virabrequim para o eixo de comando. Após a instalação dos pistões, virabrequim e cabeçote, a corrente de distribuição deve ser reajustada após a instalação. Devido à falta de ajustes e marcações, o ajuste teve que ser determinado com base no diagrama de válvula assimétrica. Usando um disco graduado no virabrequim, pode ser determinado o ângulo em que as válvulas de admissão e escape abrem e fecham (ver imagem). As peças de distribuição, como rodas dentadas, corrente, guia e tensor, foram verificadas quanto a desgaste óptico. Tudo bem.
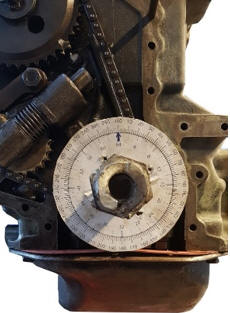
Todas as peças são apertadas de acordo com os torques prescritos. Dado que o motor foi desmontado, as verificações devem ser efectuadas após alguns quilómetros percorridos. No entanto, isso não é possível porque o motor não está instalado no veículo. Foi portanto decidido realizar as verificações prescritas pela Land Rover após 24 horas de funcionamento.
Montagem do motor na estrutura móvel:
O objetivo era utilizar o motor como ferramenta de ensino, rodando em um sistema de gerenciamento de motor. O motor não é colocado em um carro. Para garantir uma configuração segura e confiável, foi decidido colocar o motor em uma estrutura adequada. A intenção é que o motor seja fixado à carcaça do motor nos locais originais dos suportes do motor. Como não existem kits de conversão prontos, os suportes tiveram que ser customizados.
Na fase de construção, foi necessário escolher como o motor deveria ser construído. O sistema de gerenciamento do motor deve ser ajustado sob carga aumentada do motor. Como a caixa de câmbio original possui freio de transmissão, optou-se por montar a caixa de câmbio também no chassi do motor. Ao acionar este freio de transmissão é possível fazer o motor funcionar sob carga por um curto período de tempo.
A edição e adaptação dos suportes do motor existentes tornou possível conectar o motor ao chassi de maneira confiável. A estrutura do motor também oferece a possibilidade de fixar um painel de instrumentos, no qual, entre outras coisas, podem ser realizados os controles. A imagem mostra o momento em que o motor está pendurado acima da estrutura e pronto para ser fixado.
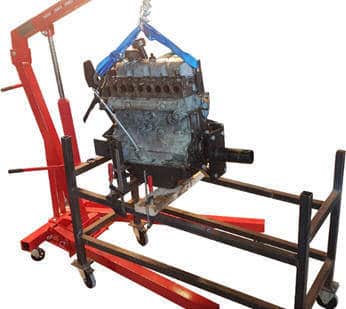
Os suportes do motor no lado da distribuição são feitos de tubos de aço e perfis em U. Uma borracha de motocicleta fornece o amortecimento. Dois tubos são montados um em cima do outro na parte inferior para montar a combinação do bloco do motor e da caixa de câmbio o mais horizontalmente possível no chassi. Os suportes são fixados ao bloco e chassi do motor por meio de hastes roscadas M8 e M12, parafusos e porcas.
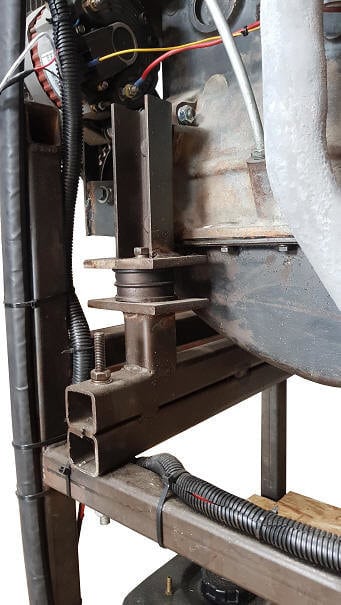
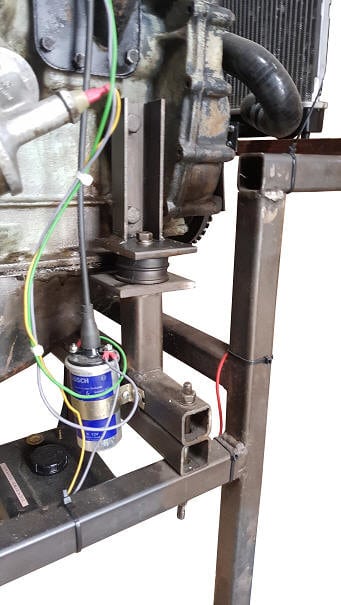
Tal suporte da caixa de velocidades foi feito em ambos os lados da caixa de velocidades com a qual se apoia na estrutura.
Depois que o motor e a caixa de câmbio tiverem sido montados no chassi de maneira segura e confiável, a montagem do motor poderá ser retomada. Após a instalação de peças ajustáveis e ajustáveis, como carburador e ignição, estas foram ajustadas de acordo com os valores de fábrica.
Outros componentes que permitem o funcionamento do motor também estão montados no chassi, como o radiador, o painel com controles e o tanque de combustível. Esses componentes são descritos nos parágrafos seguintes.
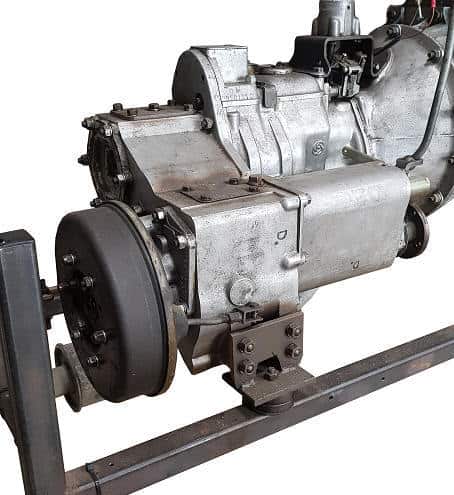
Arrefecimento:
Em sua condição original, o resfriamento é obtido por um grande radiador e uma ventoinha de metal montada na bomba d’água. Como o motor não está instalado num veículo, mas sim numa estrutura móvel, é importante utilizar componentes de reposição adequados. O ventilador de resfriamento de metal foi substituído por um ventilador elétrico com pás de plástico. A versão de plástico não só é muito mais segura, pois o motor é adequado para fins educacionais (considere a segurança pessoal ao fazer medições), mas também é mais adequada para aquecer o radiador e o bloco do motor mais rapidamente. O ventilador elétrico pode ser ligado e desligado por meio de um botão no painel. Isso permite aquecer o motor rapidamente, pois há pouca possibilidade de exercer carga mecânica sobre ele. Quando o motor está aquecido, é mais provável que haja um “circuito fechado” no qual os dados do sensor lambda são usados para controlar a injeção de combustível. Por exemplo, quando o motor está frio – em “malha aberta” – ocorre um enriquecimento extra: ao injetar uma quantidade maior de combustível (λ < 1), a correção de combustível pela sonda lambda é indesejável.
A figura mostra uma visão geral dos componentes do sistema de refrigeração instalado. O radiador original não estava presente. Como seu tamanho e peso não eram adequados para montagem no quadro da motocicleta, foi escolhido um radiador menor de reposição. Os diâmetros das conexões das mangueiras superior e inferior do radiador correspondem aos originais.
As mangueiras superior e inferior do radiador são feitas sob medida com mangueiras e conectores de silicone. O ventilador elétrico de resfriamento é preso a um suporte de montagem. A mangueira superior do radiador protege o radiador contra tombamento. Uma tampa de sobrepressão (0,9 bar) protege o sistema de refrigeração contra pressão excessiva. Quando a pressão sobe muito, a válvula na tampa do radiador abre contra a força e o líquido refrigerante flui através do transbordamento para um recipiente de coleta.
Foi necessário determinar experimentalmente se o radiador tinha uma vazão suficientemente alta e se a ventoinha de resfriamento tinha capacidade suficiente para dissipar o calor. O sistema foi considerado em ordem durante a primeira fase de teste.
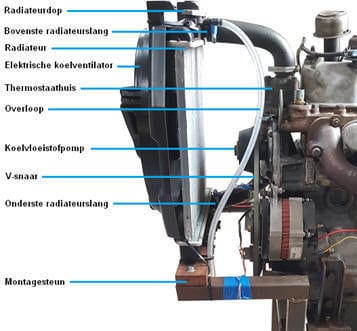
Painel e instalação elétrica:
Um painel é preso à estrutura na qual estão localizadas luzes indicadoras, interruptores, a ECU MegaSquirt, vários relés e feixes de cabos. O painel é usado para monitorar e controlar as funções do motor.
A imagem mostra o painel. O número 1 na figura indica a localização do interruptor de aterramento; uma chave desconecta a bateria do terra. Como não há necessidade de aplicar energia ao motor desligado, é mais seguro desconectar o terra quando o motor for deixado sem supervisão. O número 2 indica o interruptor do ventilador de resfriamento. Os números 3 e 4 são as luzes indicadoras do alternador (D+), o número 5 é o botão de partida e o número 6 é a chave de ignição (terminal 15). Há uma caixa de fusíveis na parte traseira do painel. O MegaSquirt é montado no painel inferior e é indicado pelo número 7. O número 8 indica o relé da bomba de combustível. O painel também oferece a opção de montar uma caixa de distribuição na qual os alunos podem fazer medições. Isso torna possível medir os valores dos sensores e os controles do atuador com o osciloscópio.
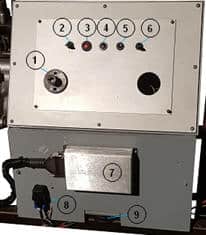
O relé de partida original controla o motor de partida; Com um pequeno botão de partida, o pino 86 é conectado ao terra, fazendo com que uma corrente de controle flua. A corrente de controle fornece um campo magnético, fazendo com que uma corrente principal flua entre os terminais 30 e 87; o motor de partida é alimentado com esta corrente principal até que o botão de partida seja liberado.
O alternador adaptado fornece a tensão e a corrente de carga à bateria. Uma luz indicadora indica se o alternador está carregando corretamente. O sensor lambda, os injetores e a bobina de ignição recebem tensão de alimentação da caixa de fusíveis. A transferência de informações e os comandos de ligar e desligar do MegaSquirt são fornecidos através de outros fios de sinal e terra.
Bomba de combustível e tanque.
A bomba mecânica de combustível na configuração clássica não é mais utilizada na instalação dos componentes do sistema de gerenciamento do motor, pois a pressão de operação é muito baixa (200 mbar). A pressão de combustível necessária para injetores MPI controlados pela ECU MegaSquirt é de 3 bar. Uma bomba de combustível eletrônica padrão de um carro de passeio é suficiente. Devido ao espaço limitado, optou-se por uma unidade compacta, na qual o tanque de combustível, a bomba e o filtro ficam em um único alojamento. Uma estrutura metálica permite montar a unidade na estrutura do motor. Numa fase posterior do projeto serão instaladas as mangueiras de combustível que fazem a ligação entre a bomba de combustível e os injetores no coletor de admissão.
Os fios de alimentação da bomba de combustível passam por um duto de cabos até o painel de instrumentos, cuja instalação já foi descrita. O fio positivo da bomba é energizado pelo MegaSquirt através de um relé.
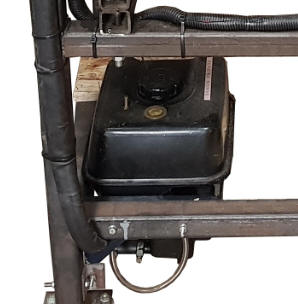
Opere o motor em uma configuração clássica.
Antes da instalação dos componentes do sistema de gerenciamento do motor, o motor foi inicialmente colocado em funcionamento na configuração clássica, ou seja, com carburador e ignição por distribuidor. O capítulo 5.2 descreve o trabalho realizado para montar o motor e os componentes auxiliares na carcaça do motor. Na primeira fase de testes, onde o motor foi ligado na configuração clássica, as verificações puderam ser feitas nas seguintes condições:
- Partida a frio;
- Inativo;
- Maior velocidade, maior carga;
- Operação de longo prazo em temperatura operacional.
Durante as verificações acima, descobriu-se que ainda precisavam ser feitos vários reparos antes que o motor fosse confiável o suficiente para a conversão.
- Após a primeira partida do motor, descobriu-se que a vedação da bomba de refrigeração não estava mais em ordem; o líquido refrigerante vazou do bloco do motor ao longo do rolamento. A substituição da bomba de refrigeração foi suficiente para resolver o problema.
- O próximo problema foi parar quando o motor atingiu a temperatura operacional. A ignição falhou, impossibilitando a partida do motor. O problema estava na distribuidora e foi facilmente resolvido.
- Com o tempo, formou-se um vazamento de óleo entre o motor e a caixa de câmbio. O vazamento provavelmente vem da vedação do virabrequim. Esse vazamento será resolvido após a conclusão do projeto.
Depois que o motor estava em ordem na configuração clássica, pudemos continuar com a eletrônica.
Volgende: sensores.