Tópicos:
- Injeção indireta e direta
- Controle de pressão de combustível com injeção indireta
- Estratégia de injeção injeção multiponto
- Injetor eletromagnético (MPI)
- Injetor Piezo (DI)
- Estratégias de injeção injeção direta
- Injeção dupla
- Medição das características de tensão e corrente em um injetor multiponto
- Tempo de injeção em relação à posição do virabrequim
- Limitação atual da ECU
- Determinação da quantidade necessária de combustível
- Tabela VE
- Tabela AFR
Injeção indireta e direta:
Os tipos de sistemas de injeção de um motor a gasolina são divididos em injeção indireta para válvula borboleta, injeção indireta por cilindro e injeção direta de alta pressão. Os parágrafos desta página explicam esses diferentes sistemas de injeção.
Injeção indireta:
Há um injetor na frente da válvula borboleta. O combustível é pulverizado contra a válvula borboleta, onde se mistura com o ar que passa. A principal desvantagem é que não existe uma dosagem precisa de combustível por cilindro; um cilindro sempre fica um pouco mais ou menos que o outro. O sistema, portanto, não é ajustável e, portanto, não é mais utilizado em relação aos requisitos ambientais. Este sistema também é denominado injeção central (Monopoint).
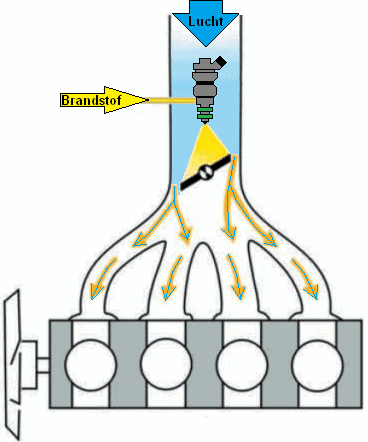
Injeção indireta:
Cada cilindro possui seu próprio injetor. O injetor injeta combustível na válvula de admissão. O ar que passa também garante a mistura neste sistema antes que a mistura ar-combustível entre na câmara de combustão. A vantagem sobre a injeção indireta é que a quantidade de combustível pode ser controlada com muito mais precisão. Este sistema também é chamado de MPI (MultiPoint Injection) ou PFI (Port Fuel Injection).
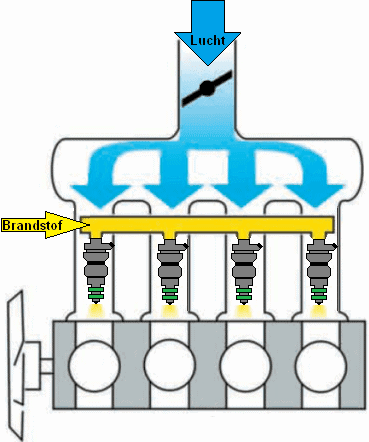
Injeção direta:
Os injetores para DI (Injeção Direta) ou DISI (Ignição por Faísca com Injeção Direta) estão localizados próximos à vela, na parte superior da câmara de combustão. O combustível é injetado através deste injetor a uma alta pressão de aproximadamente 200 bar durante o curso de admissão. As principais vantagens deste sistema são que a quantidade de combustível pode ser ajustada com ainda mais precisão, que as injeções podem ser feitas diversas vezes durante o curso de admissão e que a mistura ar-combustível é mais fria. Isso permite que os fabricantes aumentem a taxa de compressão do motor. O injetor pode ser projetado como um injetor piezoelétrico ou de bobina magnética.
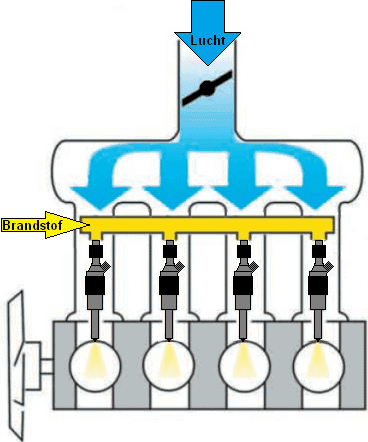
DI requer pressões de injeção mais altas que MPI/PFI, porque a injeção ocorre durante o curso de compressão; o combustível deve ser suficientemente atomizado enquanto o ar no cilindro é comprimido. É por isso que o DI possui uma bomba de alta pressão separada. A bomba de alta pressão aumenta a pressão do combustível na galeria de combustível. Os injetores são fixados a esta galeria de combustível por meio de tubos. Assim que a gestão do motor enviar um sinal ao injetor, ele abrirá e fechará no horário desejado.
As vantagens do DI em comparação com o PFI incluem:
- Injeção mais precisa;
- Possibilidade de múltiplas injeções;
- O tempo de injeção pode ser ajustado;
- É possível uma pressão efetiva mais alta acima do pistão (permitindo assim a redução do tamanho com uma taxa de compressão mais alta);
- Menor consumo de combustível, menores emissões de CO2.
As desvantagens incluem:
- Custos de sistema mais elevados devido a uma bomba de combustível de alta pressão, injetores avançados e cabeçote de cilindro mais complexo;
- As emissões de fuligem aumentaram (emissões de PM);
- A injeção direta na câmara de combustão fornece resfriamento em vez do calor necessário para a evaporação do combustível.
Um motor de injeção dupla aproveita as vantagens de ambos os sistemas. A injeção direta e indireta podem ser alternadas dependendo das condições de operação. O funcionamento e aplicação da dupla injeção estão descritos no parágrafo de mesmo nome desta página.
Controle de pressão de combustível com injeção indireta:
A pressão constante do combustível é um pré-requisito para controlar com precisão a injeção de combustível. A pressão do combustível (pressão do trilho) está na parte superior do injetor e a pressão do coletor de admissão está na parte inferior. A pressão no coletor de admissão varia com a variação da carga do motor e, sem um regulador de pressão, influenciará a diferença de pressão do combustível e, portanto, a quantidade de injeção. Por esse motivo usamos um regulador de pressão de combustível. Nesta seção nos aprofundaremos na operação e na finalidade deste controlador.
A imagem abaixo mostra os componentes de um motor a gasolina com injeção indireta e injeção multiponto. Observamos o fluxo de combustível da bomba no tanque até o injetor.
Quando a ECU controla o relé da bomba de combustível, a bomba funciona. A bomba suga o combustível da parte mais baixa possível do tanque de combustível e força o fluxo de combustível em direção ao filtro de combustível. Partículas de sujeira no combustível permanecem no material do filtro. O combustível filtrado chega então à galeria de combustível. Na maioria dos casos a galeria de combustível é montada diretamente na entrada do injetor.
Há uma pressão constante na galeria de combustível: somente quando o injetor é controlado eletricamente pela ECU (veja o fio azul) o injetor abre e o combustível é injetado no coletor de admissão na válvula de admissão aberta. A quantidade de combustível injetado depende de:
- o tempo de injeção (determinado pela ECU aumentando ou diminuindo o sinal de injeção);
- a pressão do combustível (com um tempo de injeção de 2 milissegundos, o injetor injetará mais do que a ECU calculou se a pressão do combustível for muito alta).
A pressão do combustível na galeria de combustível (também chamada de pressão do rail) é ajustada com base na carga do motor. Discutiremos isso com mais detalhes na próxima seção.
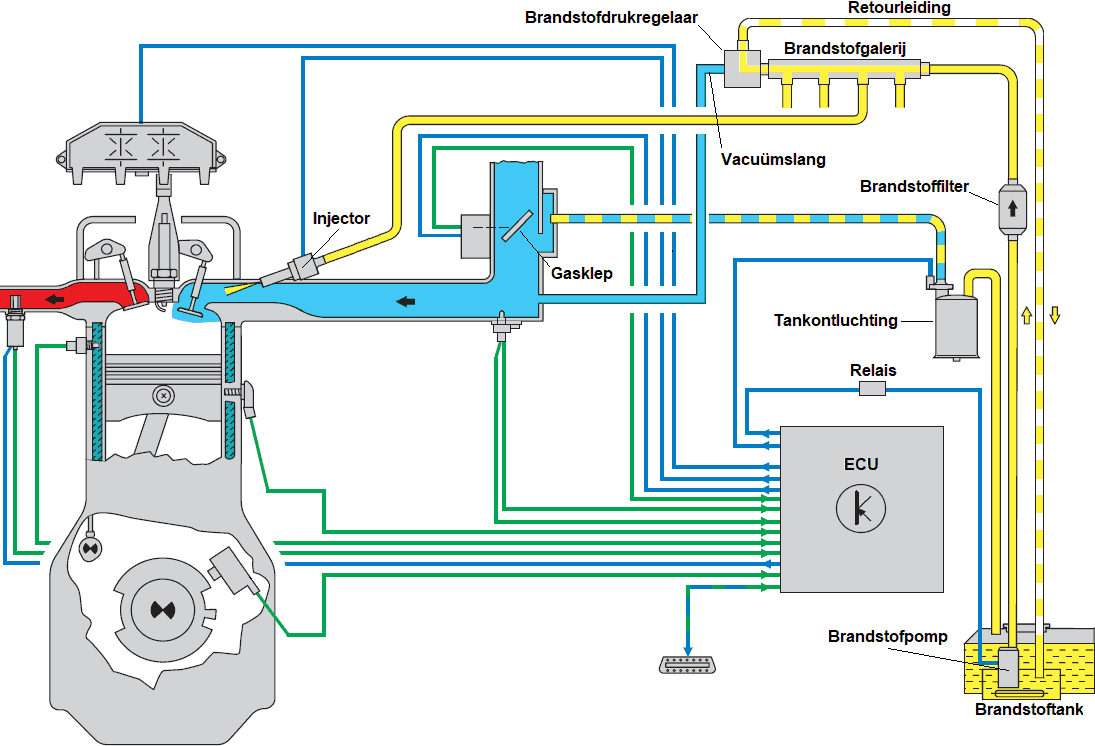
Sem usar um regulador de pressão, surgem as seguintes situações:
- Em marcha lenta, o vácuo mais alto (ou seja, baixa pressão de ar) no coletor de admissão produziria uma pressão de combustível indesejavelmente mais alta;
- Ao acelerar, há menos ou quase nenhum vácuo (carga total) e a pressão do combustível cairia, enquanto uma pressão de combustível mais alta é desejada.
O regulador de pressão do combustível aumenta ou diminui a pressão da gasolina na galeria de combustível com base na pressão do ar no coletor de admissão. Podemos considerar o regulador de pressão do combustível como uma válvula dinâmica, que permite uma abertura entre a linha de alimentação da bomba de combustível e a linha de retorno.
À direita vemos um diagrama de pressão de combustível onde a diferença de pressão relativa em todas as condições (marcha lenta, carga parcial e carga total) é de 4 bar graças ao regulador de pressão.
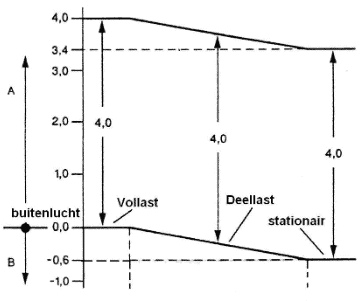
A explicação abaixo refere-se às imagens que mostram o regulador de pressão na situação sem e com vácuo. À direita está um regulador de pressão de combustível da Bosch, usado por vários fabricantes de automóveis.
Sem vácuo (esquerda):
O regulador de pressão é fechado em repouso: a mola pressiona o diafragma fechado, evitando que o combustível fornecido chegue à linha de retorno.
Com vácuo (meio):
Quando a pressão acima do diafragma é reduzida, a pressão do combustível no lado da alimentação empurra o diafragma para cima contra a força da mola. É criada uma abertura através da qual o combustível fornecido é drenado pela linha de retorno ao tanque de combustível.
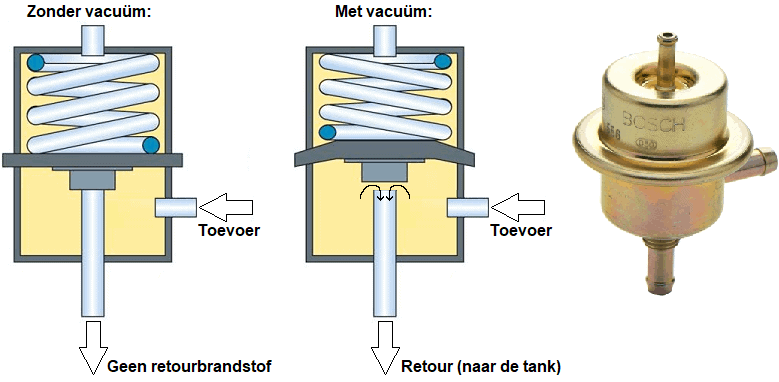
Estratégia de injeção injeção multiponto:
Com a injeção multiponto (indireta), são usados três métodos de injeção diferentes:
- Simultânea: a injeção ocorre ao mesmo tempo em todos os cilindros.
- Grupo: a injeção ocorre por grupo; há uma distinção entre um ou mais grupos.
- Sequencial: cada injetor é controlado separadamente e portanto possui seu próprio momento de injeção.
O sistema de gerenciamento do motor na figura abaixo ilustra uma injeção em grupo. Os injetores dos cilindros 1 e 2 possuem alimentação comum (vermelho) e estão ambos conectados ao terra ao mesmo tempo (verde). Os injetores dos cilindros 3 e 4 são iguais, mas são controlados separadamente dos cilindros 1 e 2.
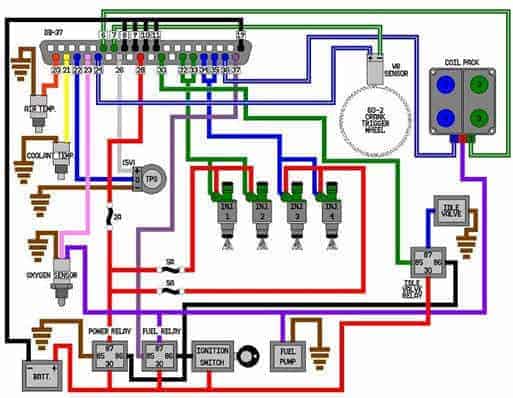
Injetor Eletromagnético (MPI):
O injetor eletromagnético é usado em muitos motores a gasolina que não utilizam injeção (direta) de alta pressão com uma bomba de alta pressão separada. O combustível está sob pressão constante de 1 bar na entrada do injetor. A pressão do combustível é fornecida pela bomba de combustível no tanque. Com a injeção multiponto (descrito mais adiante na página), cada cilindro possui seu próprio injetor. Este injetor é montado no coletor de admissão e injeta combustível com pressão de até 6 bar antes da abertura da válvula. O combustível tem então tempo suficiente, quando a válvula de admissão começa a abrir, para se misturar com todo o oxigênio (indicado na figura como a seta azul escura) que flui para dentro do cilindro.
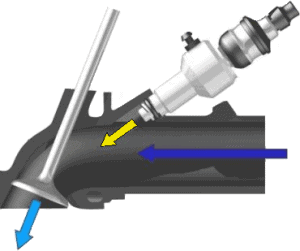
A unidade de controle do motor analisa a posição do virabrequim para regular o ponto de injeção e o ponto de ignição. Com base em vários fatores (temperatura do motor e ambiente, carga, velocidade, etc., ele dará um sinal para o injetor no momento certo para abrir. O plugue deste injetor contém dois fios. Um fio tem um positivo constante em torno de 14 volts. O outro fio é conectado ao terra pela ECU para permitir que a corrente flua através da bobina do injetor. Quando a bobina está suficientemente carregada, a agulha do injetor abre contra a força da mola. Quando o controle para, uma mola comprime a agulha do injetor de volta . O fornecimento de combustível é então cortado. Quando o controle para, a bobina ainda está eletricamente carregada. A energia na bobina forma um pico de indução, que pode ser observado no osciloscópio. A tensão de indução fica brevemente em torno de 60 volts.
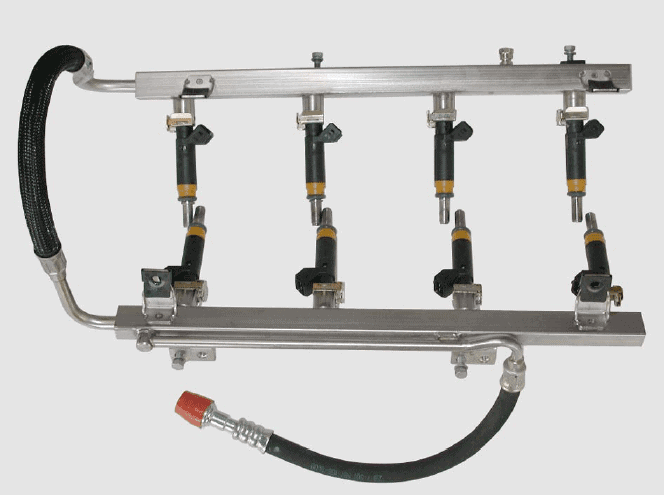
Esses injetores são abastecidos com combustível pelo trilho de combustível (também chamado de galeria de combustível). A bomba de reforço no tanque de combustível fornece a pressão no trilho de combustível. A pressão do combustível no trilho é constante (aprox. 4 bar). Como a pressão é muito baixa, os injetores são fixados com um clipe de travamento e um anel de vedação para vedação. Especialmente em carros mais antigos onde o sistema é desmontado, é aconselhável substituir os O-rings antes da instalação.
A carcaça de um injetor geralmente é feita de plástico. Na parte superior da caixa encontramos a conexão do plugue, que está conectada internamente à bobina. Há um anel de borracha na parte superior sobre o qual desliza a galeria de combustível. O-rings ou anéis de vedação de Teflon podem ser encontrados na parte inferior. Um O-ring é usado principalmente em injetores MPI com injeção de baixa pressão, enquanto os anéis de Teflon podem ser encontrados em motores com injeção de alta pressão, como um motor FSI.
A bobina é enrolada em torno do núcleo do injetor. Na imagem anexa a bobina está destacada em vermelho. No centro do injetor, também interno à bobina, há um êmbolo. Este êmbolo possui um acoplamento mecânico com a agulha. Acima do êmbolo há uma mola que mantém o êmbolo e, portanto, a agulha em sua sede, fechando a abertura de injeção.
Em repouso, a tensão em ambos os terminais da bobina é de aproximadamente 14 volts em relação ao terra. Para escorvar o injetor, a ECU do motor fornece terra a um lado da bobina, enquanto o outro lado recebe tensão positiva. Nesse ponto, a corrente começa a fluir pela bobina, resultando na formação de um campo magnético. Este campo magnético puxa o êmbolo e, portanto, a agulha de injeção para cima.
Quando a injeção precisa ser interrompida, a ECU desconecta o terra, fazendo com que o campo magnético desapareça. A mola empurra o êmbolo de volta para baixo, fazendo com que a agulha interrompa o fornecimento de combustível para a câmara de combustão.
O injetor geralmente possui múltiplas aberturas. Estas aberturas são muito pequenas, de modo que o combustível é injetado do injetor na câmara de combustão como uma névoa. Quanto mais fina a névoa, mais fácil ela evapora.
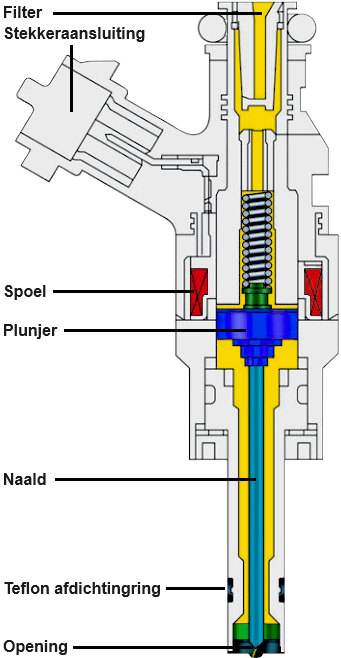
Injetor Piezo (DI):
Os injetores piezoelétricos podem ser usados em motores a gasolina e diesel. A BMW foi a primeira marca a utilizar tecnologia piezoelétrica em motores a gasolina, mas deixou de fazê-lo com os motores mais recentes.
Um injetor piezoelétrico faz parte da injeção de alta pressão. Uma bomba de alta pressão separada fornece pressão no trilho de combustível. Este trilho de combustível distribui o combustível para todos os injetores (ver imagem). Devido às pressões muito elevadas, são utilizados tubos de alumínio com bucins. Os bucins (que são aparafusados no tubo e nos injetores) devem ser sempre apertados com a força correta. Isto é indicado no manual de reparo do motor relevante.
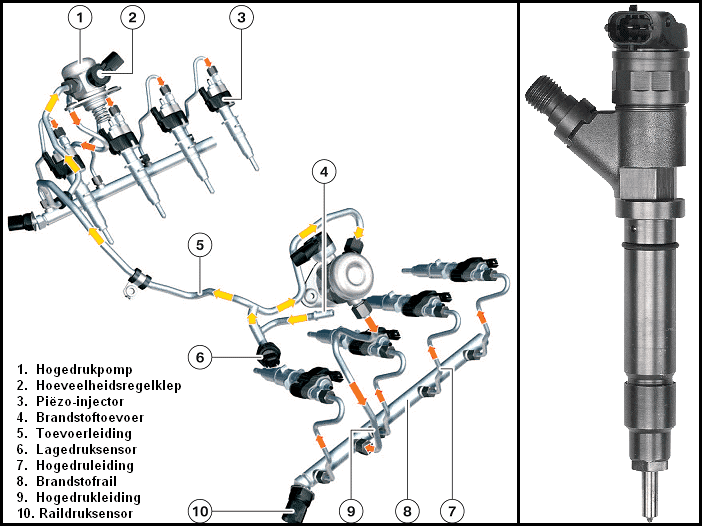
O elemento piezoelétrico no injetor tem a propriedade de mudar de comprimento quando uma tensão positiva ou negativa é conectada a ele. Isso é usado com o injetor. Assim que a unidade de controle do motor fornece uma tensão de controle de aproximadamente 100 a 150 Volts, o elemento piezo expande aproximadamente 0,03 mm. Esta mudança de comprimento é suficiente para estabelecer uma ligação entre a câmara de alta e baixa pressão. A injeção começa imediatamente. O elemento piezoelétrico pode ligar e desligar em um milésimo de segundo. Juntamente com a pressão de injeção muito alta de até 2000 bar, isso proporciona injeções muito rápidas e precisas. Essas velocidades também permitem que múltiplas injeções ocorram uma após a outra.
Múltiplas injeções durante o curso de admissão têm a vantagem de que a mistura ar-combustível é ideal. A alta pressão faz com que as gotas de combustível sejam atomizadas ultrafinamente, de modo que se misturem ainda melhor com o ar. Podem ocorrer até 8 injeções durante o curso de admissão. Isto tem consequências positivas no consumo de combustível, na potência e nas emissões de gases de escape.
Estratégias de injeção injeção direta:
A estratégia de injeção direta possui diferentes variantes: guiada por parede, guiada por ar e guiada por jato (veja as imagens abaixo). Nestas situações ocorre um processo de combustão em camadas. Isto não se aplica em todas as condições de operação.
- Guiado pela parede: O pistão guia a nuvem de combustível até a vela de ignição. A distância entre a vela e o injetor é grande. Aplicado a motores GDI e HPI.
- Guiado por ar: O movimento do ar traz a nuvem de combustível para a vela de ignição. A distância entre a vela e o injetor é grande. Aplicado a motores FSI e JTS.
- Guiado por jato: A vela de ignição está localizada na borda da nuvem de combustível. A distância entre o injetor e a vela é pequena. Aplicado a motores BMW.
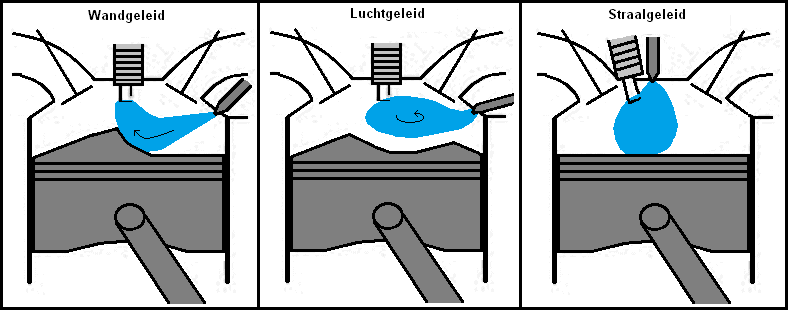
Conforme já indicado, os motores a gasolina com injeção direta não apresentam combustão estratificada em todas as condições de funcionamento. Os motores com injeção direta guiada por jato podem funcionar em fases com carga parcial. Um processo de combustão em camadas significa que existem várias camadas de ar no espaço de combustão. Perto da vela de ignição, o valor lambda é 1. Mais longe, o valor lambda torna-se mais alto (mais pobre, portanto, mais ar). Este ar fornece uma camada de ar isolante. Num processo em camadas o tempo de injeção é mais tardio do que no processo homogéneo. Com a ajuda de uma injeção em camadas, a válvula borboleta pode ser totalmente aberta, de modo que obstrua menos o ar. Como o ar aspirado é desobstruído, encontra menos resistência e pode, portanto, ser aspirado mais facilmente. Como o valor lambda no espaço de combustão com injeção em camadas é menor que 1 devido à camada de ar isolante, isso não causa problemas de combustão. Durante o processo de estratificação, o consumo de combustível diminui.
Com uma mistura homogénea, o valor lambda é sempre 1. Isto significa que num motor a gasolina a proporção de ar e combustível é de 14,7:1 (14,7 kg de ar para 1 kg de combustível). Cada motor pode funcionar de forma homogênea. Se ocorrer enriquecimento, o valor lambda diminuirá e se a mistura ficar mais pobre, o valor lambda aumentará:
<1 = Rico
>1 = Ruim
Um motor sempre oscilará entre rico e pobre para manter o conversor catalítico funcionando corretamente. O sonda lambda envia os dados para o sistema de gerenciamento do motor.
Em plena carga o motor funciona sempre de forma homogênea. Isto proporciona um torque mais alto do que com um processo em camadas. Se o motor funcionar de maneira homogênea, o combustível será injetado antecipadamente. O motor também funciona de forma homogênea ao sair da paralisação. Há então um torque de partida mais alto do que se o motor funcionasse em camadas.
A curva característica abaixo mostra as situações de operação em diferentes velocidades em comparação com o pressão de combustão, com e sem uso de EGR.
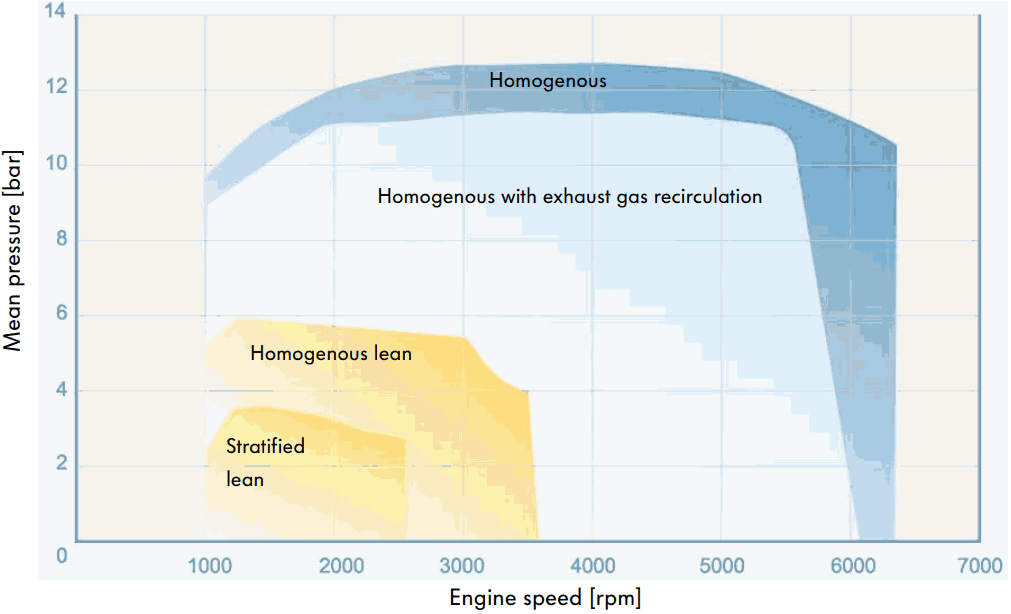
Injeção dupla:
O grupo VAG utiliza motores a gasolina de dupla injeção para atender aos padrões de emissões atuais. Nos motores de injeção dupla, existem dois sistemas de injeção de combustível: um sistema de baixa pressão e um sistema de alta pressão.
- O sistema de baixa pressão contém injetores MPI que são usados há décadas. Os injetores MPI são montados no coletor de admissão e injetam na válvula de admissão a uma pressão de 4 a 5 bar;
- O sistema de alta pressão contém injetores de alta pressão que injetam diretamente na câmara de combustão com uma pressão de injeção máxima de 150 a 200 bar.
O sistema de gerenciamento do motor determina qual injetor é controlado.
A imagem a seguir mostra um corte transversal do cabeçote com os dois sistemas de combustível.
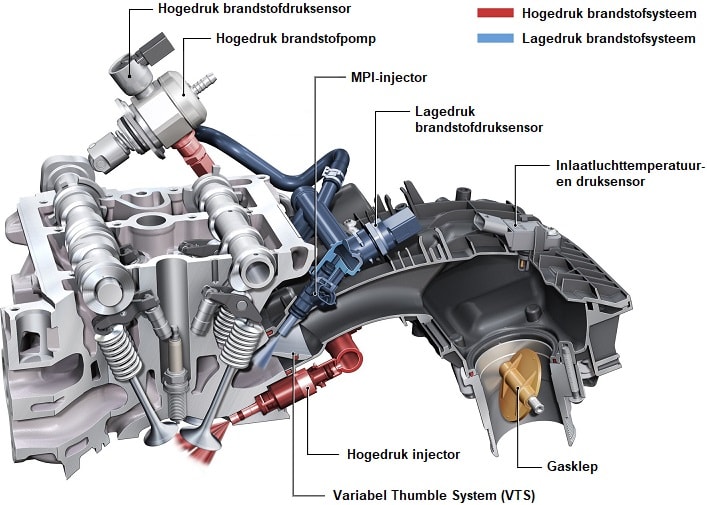
A injeção MPI oferece melhor mistura entre ar e combustível. Os injetores diretos são usados em marcha lenta e plena carga. Com a injeção direta, consegue-se um melhor resfriamento, o que possibilita uma maior taxa de compressão. No entanto, a mistura de ar e combustível não é ideal. Isso causa mais emissões de fuligem. Por esta razão, os motores com injeção direta são hoje equipados com filtro de partículas. Este não é um problema com a injeção dupla. O “sistema de polegar variável”, abreviado como VTS, é uma versão de um coletor de admissão variável que proporciona melhor fluxo de ar. O “polegar” é um fluxo de ar que forma um vórtice ao entrar no cilindro. O redemoinho de ar é necessário para misturar adequadamente o combustível do injetor MPI com o ar.
A dupla injeção em combinação com VTS garante melhores emissões de escape. Uma vantagem adicional é que a válvula de admissão é limpa pelo injetor MPI. Os motores com injeção direta geralmente apresentam um trato de admissão sujo (coletor de admissão e válvulas de admissão), o que causa problemas como fornecimento de ar limitado. No cenário extremo, a admissão fica tão obstruída que a válvula de admissão não consegue mais fechar adequadamente na cabeça do cilindro e, por fim, queima porque não consegue dissipar o calor suficientemente.
Sabe-se que os mesmos motores nos Estados Unidos são equipados apenas com injeção direta para os motores VAG com injeção dupla. O coletor de admissão está tampado. Isto porque, no momento em que este artigo foi escrito, os requisitos ambientais são mais rigorosos na Europa do que nos EUA, e o fabricante não fornece motores para mercados onde os padrões de emissão são menos rigorosos com sistemas tão caros por razões de custo.
Medição das características de tensão e corrente em um injetor multiponto:
O osciloscópio só pode medir tensão. Os cabos de medição podem ser conectados em paralelo entre os componentes elétricos. Medir corrente em série não é possível. A corrente pode ser medida usando uma pinça de corrente indutiva. Os sensores Hall na pinça de corrente medem o campo magnético e o convertem em tensão. A tensão pode ser medida com o osciloscópio. Neste caso existe um fator de conversão de 10 mv por ampere; Para cada 0,010 volts que a pinça de corrente transmite, isso pode ser convertido para 1 A.
A imagem do osciloscópio a seguir mostra o perfil de tensão e corrente de um injetor eletromagnético.
- Vermelho: gradiente de tensão;
- Amarelo: fluxo atual.
Em repouso a tensão é de 14 volts. Agora não há diferença de tensão no plugue, portanto não há fluxo de corrente. A ECU conecta um fio ao terra para controlar o injetor. A diferença de tensão faz com que a corrente flua através da bobina do injetor.
A linha amarela indica o fluxo de corrente: no momento em que a tensão cai para 0 volts, começa o aumento da corrente. Carregar a bobina leva tempo. A corrente não aumenta mais do que aproximadamente 0,9 A. A meio da acumulação de corrente, vemos uma curvatura na linha: este é o momento em que se acumula magnetismo suficiente para levantar a agulha do seu assento. O injetor começa a injetar.
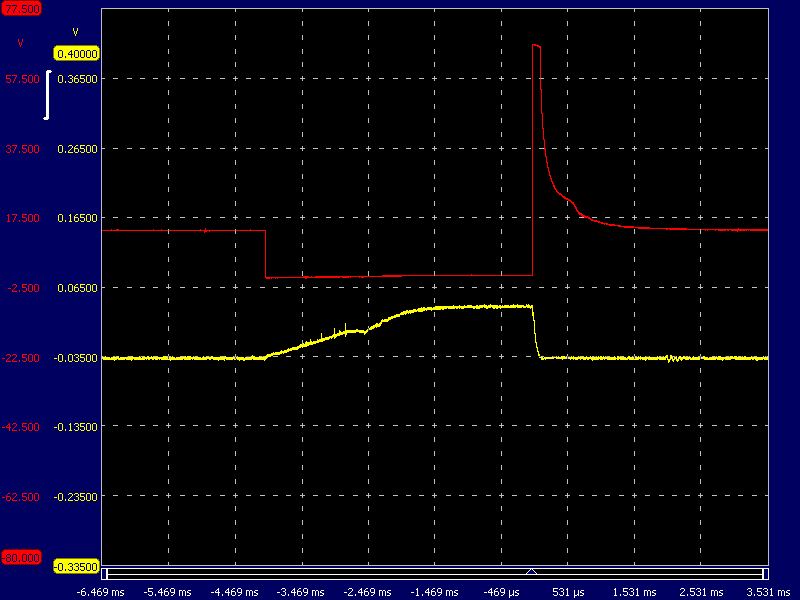
A ECU interrompe a conexão à terra para interromper o controle. A energia residual na bobina fornece uma tensão de indução de aproximadamente 60 volts. O injetor para de injetar porque a mola empurra a agulha de volta para seu assento. Isso pode ser visto na imagem do osciloscópio pelo aumento no sinal de tensão.
Se o motor funcionar irregularmente e ocorrer falha na ignição do cilindro, isso pode ser devido a uma série de causas:
- Nenhuma ou fraca faísca devido a uma vela de ignição, cabo da vela ou bobina de ignição com defeito;
- Restrição no fornecimento de combustível devido a filtro de combustível entupido, regulador de pressão com defeito, problema na bomba de combustível ou injetor;
- Perda de compressão devido a um problema nos anéis do pistão, junta do cabeçote ou vedações da válvula com defeito.
Durante um diagnóstico, um osciloscópio pode ser usado para verificar se os injetores ainda estão funcionando corretamente. No início desta seção, foram mostradas medições onde não houve mau funcionamento. As linhas azuis mostram, como exemplo, como seria o perfil de tensão e corrente de um injetor defeituoso.
Caso o controle do injetor esteja correto, mas não haja dobras visíveis na imagem de tensão e corrente, pode-se concluir que a agulha do injetor não está se movendo. Como o injetor de um cilindro não funciona corretamente e os outros injetores funcionam corretamente, as imagens dos diferentes injetores podem ser facilmente comparadas entre si.
Se você bater suavemente no injetor, a agulha do injetor poderá se soltar. Nesse caso, o motor funcionará imediatamente de forma mais silenciosa e as torções ficarão visíveis novamente nas imagens do osciloscópio. Contudo, isto não garante uma solução permanente; há uma boa chance de que o problema retorne em pouco tempo. É necessário substituir o injetor relevante.
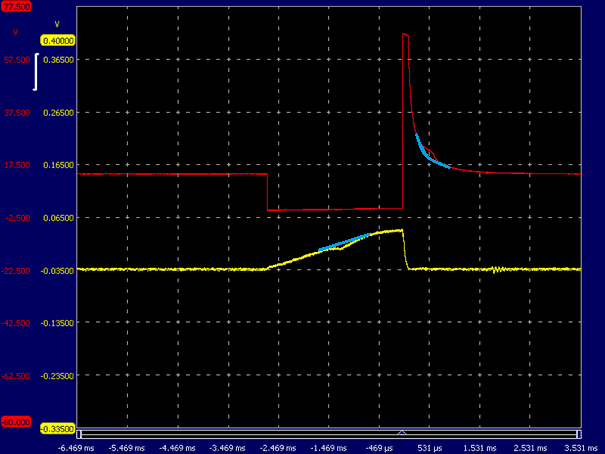
A agulha no injetor só abre depois que a bobina está suficientemente carregada. Como resultado, o injetor não injeta combustível imediatamente quando a ECU começa a controlá-lo. Após a conclusão do acionamento, a mola pressiona a agulha do injetor em sua sede. Isso também leva tempo. O tempo de controle geralmente não é igual ao tempo de injeção. A imagem a seguir mostra a curva de tensão e corrente do mesmo injetor acima, mas com velocidade aumentada.
- Início do controle: a ECU liga o fio de controle ao terra. A corrente flui através da bobina do injetor para abri-la. A dobra no padrão de fluxo indica o momento em que a agulha do injetor se abre. A corrente então aumenta um pouco e, portanto, permanece constante. A agulha do injetor permanece aberta.
- Fim do controle: conforme já descrito, reconhecemos o momento em que a agulha do injetor é fechada pela colisão na imagem de tensão.
O controle leva 4 ms, mas o tempo real de injeção é de 3 ms. Chamamos a diferença entre estes de “atraso”, traduzido em holandês como “atraso”. A ECU, portanto, controla o injetor por 4 ms para permitir que ele injete por 3 ms.
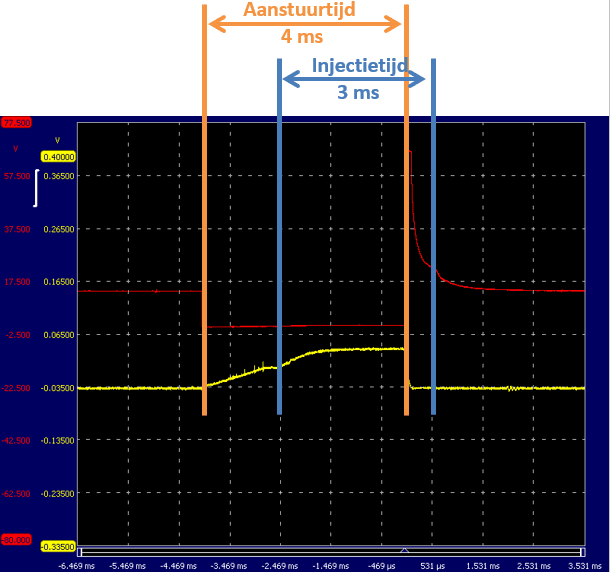
Tempo de injeção em relação à posição do virabrequim:
O momento de injeção pode ser visualizado usando um osciloscópio. O canal A (vermelho) está no fio terra do injetor e o canal B (amarelo) está no fio do injetor sensor de posição do virabrequim conectado. Enquanto o motor está funcionando, podemos usar esta imagem do osciloscópio para determinar o tempo de injeção e o tempo de injeção.
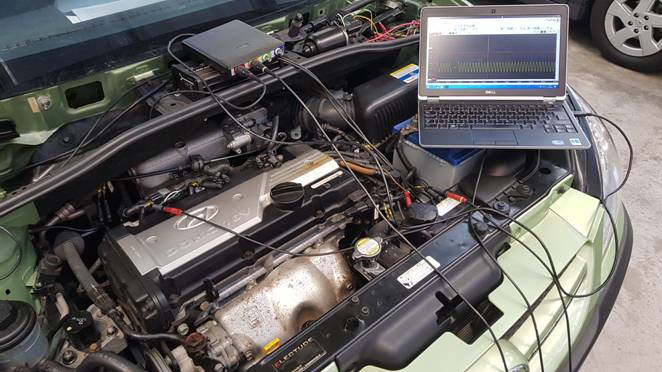
A imagem do osciloscópio foi tirada durante a velocidade de marcha lenta. A imagem vermelha da tensão mostra a abertura e o fechamento do injetor (veja a seção: Medição das características de tensão e corrente em um injetor multiponto). No tempo -2,860 ms o controle é iniciado; a tensão de 12 volts cai para 0 volts. Este é o ponto em que a bobina do injetor é aterrada e a corrente flui. O controle do injetor termina quando a linha vermelha sobe novamente. Devido à energia acumulada na bobina, ocorre uma tensão de indução superior a 60 volts. Então a tensão cai gradualmente para 12 volts; aqui o injetor é desligado novamente.
A tensão alternada vermelha vem do indutivo sensor de posição do virabrequim. Cada vez que os dentes da roda de impulso passam pelo sensor do virabrequim, uma tensão alternada senoidal é criada. A roda de impulso contém 60 dentes, 2 dos quais foram retificados. Os dois dentes retificados formam o ponto de referência no qual o sistema de gerenciamento do motor reconhece que os pistões dos cilindros 1 e 4 estão entre 90⁰ e 120⁰ antes do PMS (ponto morto superior). Depois que o dente perdido for reconhecido, o sistema de gerenciamento do motor terá tempo para (possivelmente em combinação com o sensor de árvore de cames) para determinar o momento correto de injeção e ignição e para ativar o injetor e a bobina de ignição antes que o pistão esteja no PMS.
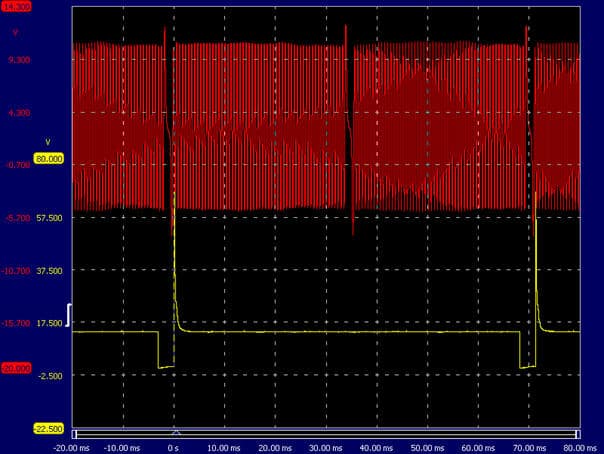
A imagem do osciloscópio mostra o momento em que a injeção começa; a injeção começa com o quarto pulso do sensor do virabrequim. Supondo que existam 60 - 2 dentes, a cada 6⁰ rotação do virabrequim (360⁰ para 1 rotação / 60 dentes) a injeção ocorre 24 graus após o ponto de referência. O dente perdido está 90⁰ antes do TDC, então a injeção começa (90⁰ – 24⁰) = 66⁰ antes do TDC.
Com uma velocidade aumentada de 2000 rpm, os pulsos do sensor indutivo do virabrequim ficam mais próximos. A frequência deste sinal é traduzida em velocidade pelo sistema de gerenciamento do motor. Dependendo da velocidade, a carga (medida pelo Sensor MAPA) e o temperaturas do ar de admissão e do líquido refrigerante, é determinado o tempo de injeção necessário. O tempo de injeção ocorre mais cedo e o injetor fica mais tempo no solo: o injetor injeta mais cedo e por mais tempo.
Do início do acionamento até o ponto de disparo (seta ao nível do desligamento do injetor), o tempo de acionamento é de aproximadamente 5,2 ms. O tempo de acionamento do injetor não é igual ao da injeção real (ver parágrafo anterior).
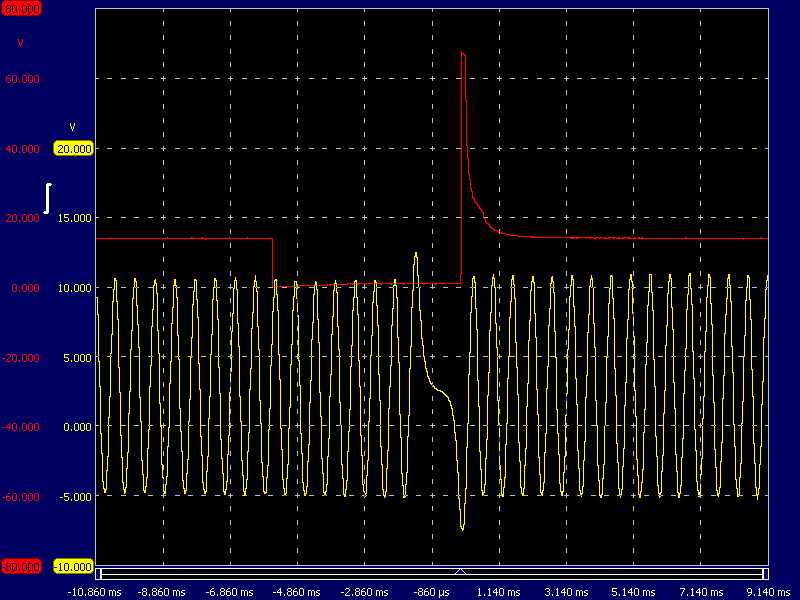
Na imagem do osciloscópio a seguir, o sinal indutivo do virabrequim é mostrado em vermelho e o sinal do injetor é mostrado em amarelo. Ao aumentar a velocidade para aproximadamente 3000 rpm, dois controles dos injetores podem ser vistos. É claramente visível que a injeção de combustível do cilindro 1 ocorre a cada segunda rotação do virabrequim.
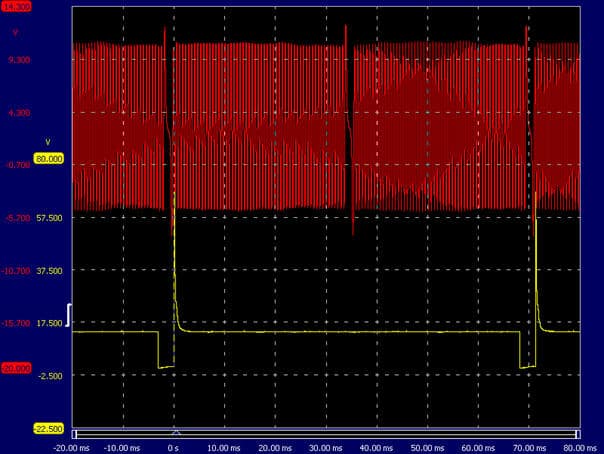
Limitação atual na ECU:
Conforme as medições mostradas na seção “Medição de tensão e corrente em um injetor multiponto”, existe um atraso entre o acionamento e a abertura efetiva da agulha do injetor. Neste caso leva 1,5 ms para abrir.
A agulha do injetor abriria mais rápido se a corrente através da bobina aumentasse mais rapidamente. A corrente depende da resistência da bobina: quanto menor a resistência, mais rápido será o aumento da corrente. Os injetores de alta impedância utilizados no motor das medições possuem resistência de 16 Ohm. Na tensão on-board de 14 volts, uma pequena corrente fluirá:
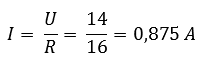
A corrente é suficiente para abrir a agulha do injetor, mas não muito alta para que fique muito quente devido à potência muito alta:

Como apenas uma potência baixa é acumulada, não é necessário usar um controle de corrente. Isto seria necessário com injetores de baixa impedância.
- Os injetores de baixa impedância têm a vantagem de que o acúmulo de corrente aumenta rapidamente desde o início. Isso resulta em uma abertura rápida da agulha do injetor, com pouco atraso.
- Os injetores de baixo ohm têm uma resistência de aproximadamente 2,8 ohms. A baixa resistência faz com que uma alta corrente flua:
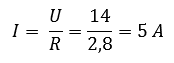
A potência também aumenta acentuadamente:

O consumo de energia é quase sete vezes maior do que com os injetores de alta impedância. Se a corrente aumentar muito, é desenvolvido calor nos injetores e no estágio de saída do dispositivo de controle. Para limitar a corrente, a tensão é ligada e desligada várias vezes em um curto período de tempo. Depois que a agulha do injetor é aberta, é necessária pouca energia para mantê-la aberta. A corrente diminui durante a ligação e desligamento. Essa progressão pode ser vista na imagem do osciloscópio.
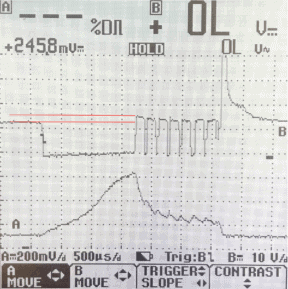
Determinação da quantidade necessária de combustível:
O fabricante determinou a quantidade necessária de combustível em vários campos característicos armazenados na memória ROM da ECU. Isto sistema de gerenciamento do motor lê nesses gráficos quanto combustível é necessário sem correções. É claro que isso depende da rotação, temperatura e carga do motor. Os parâmetros mais importantes para determinar a quantidade correta de combustível são explicados nesta seção como tabela VE e tabela AFR.
Tabela VE:
A tabela VE representa a eficiência volumétrica e a relação ar/combustível em cada rotação do motor e pressão do coletor de admissão. A eficiência volumétrica é a razão entre a quantidade medida de ar que enche os cilindros e a quantidade de ar que encheria o cilindro em uma situação estática, dependendo da rotação do motor e da pressão do coletor de admissão. Os valores da tabela são utilizados pela ECU para determinar a massa de ar atual e, portanto, o nível de enchimento. Esses dados são usados para calcular a quantidade de combustível a ser injetada.
Esta abordagem teórica difere da realidade. As especificações do motor ainda não foram levadas em consideração aqui. Considere o diagrama da válvula (sobreposição da válvula ou possivelmente temporização variável da válvula), a resistência do ar no trato de admissão, etc. É por isso que é aplicado um fator de correção que fornece um desvio da relação linear. O fator de correção é mostrado na imagem acima pela linha tracejada. A curva indica até que ponto a relação linear está correta. A uma pressão de 60 kPa o desvio é de aproximadamente 50% da linha que mostra a relação linear. O fator de correção pode ser formado em uma porcentagem.
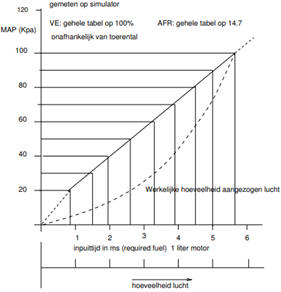
Numa tabela VE, cada célula indica a percentagem associada à pressão negativa em relação à velocidade. Esta porcentagem será maior na velocidade em que o torque for maior. Afinal, o motor é mais eficiente lá porque o motor abastece melhor.
Os valores nas tabelas VE e AFR mais adiante nesta seção são derivados da curva de torque e potência de um motor 1.8 20v de um VW Golf.
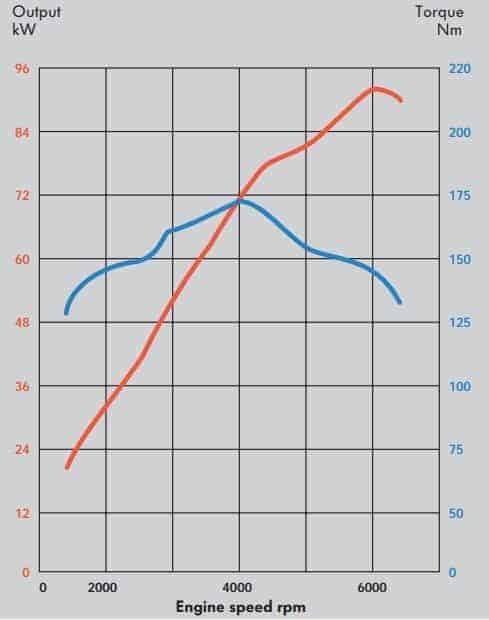
As imagens abaixo mostram a tabela VE como tabela de preenchimento e a representação tridimensional criada a partir da curva de torque e potência no programa “TunerStudio”. Este programa é usado principalmente para fornecer software para uma ECU programável como MegaSquirt ou Speeduino. Para mais informações: veja as páginas sobre o assunto Projeto MegaSquirt.
O eixo vertical mostra a MAP (pressão do ar no coletor) de 15 kPa (muita pressão negativa) a 100 kPa (a pressão do ar externo). O MAP indica a carga do motor. O eixo horizontal indica a rotação do motor entre a rotação de marcha lenta e a rotação máxima do motor.
As células da tabela VE mostram o nível de enchimento do motor. Em outras palavras; quão eficiente é o motor em uma determinada velocidade e carga. O motor é mais eficiente na velocidade em que o torque é mais alto (cerca de 4200 rpm); as porcentagens são as mais altas aqui. É aqui que o motor “enche” melhor. A aplicação de técnicas que aumentem o nível de enchimento, como comando de válvulas variável, ajuste do coletor de admissão ou uso de turbo, beneficiará os percentuais.
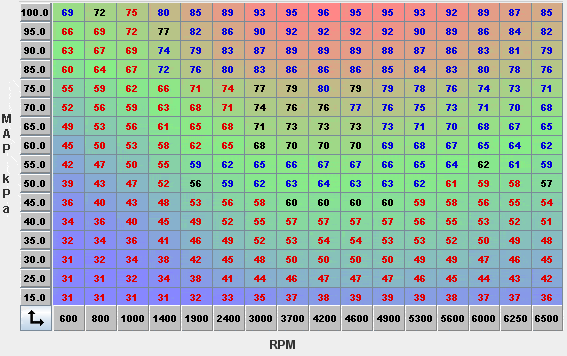
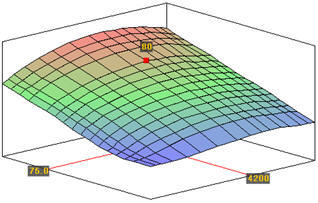
Tabela AFR:
A composição necessária de ar/combustível é registrada em uma tabela AFR. AFR é a abreviatura de “Relação Ar-Combustível”. A uma proporção de mistura estequiométrica (lambda = 1), são necessários 14,7 kg de ar para queimar 1 kg de gasolina. Uma mistura estequiométrica não é desejável em todas as situações.
- Uma mistura pobre beneficia o consumo de combustível;
- Uma mistura rica permite maior potência.
Quando o motor precisa fornecer mais potência (P), ocorre o enriquecimento. Uma mistura mais rica também proporciona resfriamento. Enriquecer para λ = 0,8 significa que se aplica uma proporção de mistura (AFR) de 11,76 kg de ar para 1 kg de gasolina. Portanto, há menos ar disponível para queimar 1 kg de combustível do que com uma mistura estequiométrica. Uma mistura pobre, por outro lado, proporciona um melhor consumo de combustível (ser), mas dá mais chances de detonação. O enriquecimento ou empobrecimento da mistura deve sempre permanecer dentro dos limites de combustão.
Durante a marcha lenta, a velocidade está entre 600 e 900 rpm. A válvula de gás está quase completamente fechada e a pressão negativa é elevada: está entre 25 e 40 kPa. A mistura é estequiométrica (14,7:1) nesta faixa de velocidade.
Quando houver carga parcial, a rotação do motor terá aumentado para 4200 rpm. A válvula borboleta é aberta ainda mais, de modo que o vácuo no coletor de admissão cai para 40 – 75 kPa. À medida que a carga do motor aumenta, a pressão negativa diminui; ocorre o enriquecimento (AFR de 13:1). Uma mistura pobre é possível com baixa carga do motor. Em plena carga, o acelerador está totalmente aberto. A pressão negativa cai para 100 kPa (a pressão do ar externo) e ocorre o enriquecimento máximo (12,5:1).
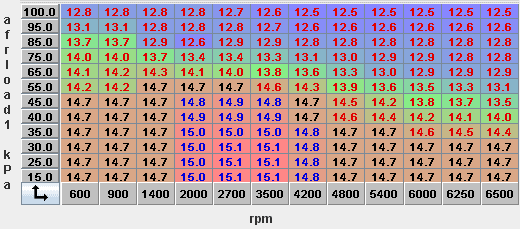
O valor lambda não afeta apenas a potência e o consumo de combustível, mas também as emissões de escape. Uma mistura mais rica garante um menor teor de NOx, mas também maiores emissões de CO e HC. Com uma mistura mais pobre, as partículas de combustível ficam mais afastadas, de modo que a combustão não é mais ideal; com o resultado de que as emissões de HC também aumentam.
Ao usar um catalisador, é desejável garantir que a injeção alterne constantemente entre rico e pobre. Numa mistura rica, o CO é formado como resultado de uma deficiência de oxigénio, com a qual o catalisador reduz o NOx. Uma mistura pobre contém um excesso de oxigênio, que oxida CO e HC.
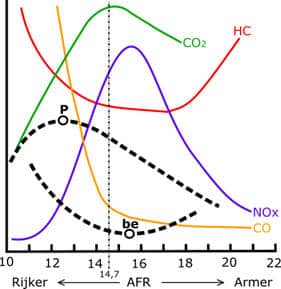
A unidade de controle determina quanto combustível deve ser injetado. Primeiramente, os dados básicos de injeção são lidos nos campos característicos. Os valores das tabelas VE e AFR, entre outros, estão incluídos no cálculo da quantidade de injeção. Também são levados em consideração os seguintes valores determinados pelo fabricante:
- enriquecimento dependendo da temperatura do líquido refrigerante e do ar de admissão;
- enriquecimento de aceleração de curto prazo ao abrir (rapidamente) o acelerador;
- correção devido à variação na tensão de bordo.
Além desses valores determinados, são cuidadosamente levadas em consideração as tensões que a sonda lambda envia para a unidade de controle. Essas tensões dependem do teor de oxigênio nos gases de exaustão. Este é um fator variável que muda continuamente. A entrada dessas tensões do sensor é chamada de “guarnições de combustível" incorporado.
A forma como são determinados os valores da tabela VE e AFR e as demais configurações citadas estão descritas nas páginas do realizado Projeto MegaSquirt.