Emner:
- introduksjon
- Intelligent batterisensor
- Komponenter og måleprinsipper for batterisensoren
- Lading og utskifting av batteri
Forord:
I moderne kjøretøy er ladestatusen til dynamoen tilpasset omstendighetene. Generatoren styres fra motorens ECU og mottar signaler om å lade mer eller mindre. Generatoren genererer energi når et magnetisk felt skapes mellom rotoren og statoren. Jo større magnetfelt, jo mer kraft kreves det for å snu rotoren. Å generere store mengder ladestrøm koster derfor energi og drivstoff.
- Tomgangshastigheten kan økes når batteriet er nesten tomt når det ikke er tilstrekkelig opplading mulig;
- Under maksimal akselerasjon er dynamoen midlertidig ikke kontrollert for å bruke alt det genererte dreiemomentet til fremdrift;
- Ved nedbremsing (motorbremsing) styrer ECU dynamoen til maksimal effekt, slik at kjøretøyets kinetiske energi brukes til å generere energi i dynamoen. Figuren viser indikasjonen av maksimal batterilading (12 volt system).
Signalet fra den intelligente batterisensoren brukes til å bestemme ladestatusen til batteriet. Dette er en av de viktigste dataene for å avgjøre i hvilken grad dynamoen skal kontrolleres.
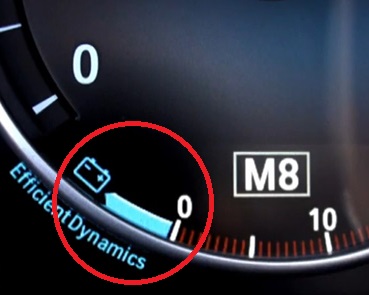
Intelligent batterisensor:
Moderne kjøretøy er nesten alle utstyrt med en batterisensor, ofte kjent som en IBS (Intelligent Battery Sensor), strømsensor eller batterimonitor. I denne artikkelen vil vi referere til begrepet "batterisensor". Batterisensoren fungerer i nært samarbeid med Battery Monitor System (BMS) i kjøretøyet. Dette gjelder spesielt for kjøretøy med start- og stoppsystem. I disse kjøretøyene blir batteriet gjentatte ganger utsatt for stor belastning da startmotoren aktiveres flere ganger per tur for å starte motoren. Derfor velges ofte et AGM-batteri i slike kjøretøy i stedet for en tradisjonell blycelle. Et AGM-batteri er mer motstandsdyktig mot gjentatt utlading og lading.
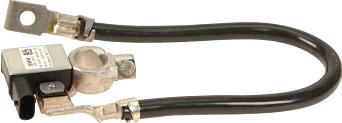
Batterisensoren er integrert i jordkabelen, som festes mellom batteriets minuspol og et jordingspunkt på karosseriet eller chassiset. På batterisensoren finner du en plugg med to eller flere ledninger. En ledning fører direkte til den positive polen på batteriet, og en andre ledning er for kommunikasjon.
Inne i batterisensorhuset er det et kretskort med en mikroprosessor og en kontroller som måler spenning, strøm, temperatur og tid. Dataene fra denne elektroniske kontrollenheten (ECU) overføres ofte via en LIN-buss til dynamoen og komfortkontrollenheten (BCM) eller motorkontrollenheten. Gatewayen er ofte plassert mellom batterisensoren og BCM eller motorkontrollenheten for å oversette LIN-bussmeldingen til en CAN-bussmelding. Dette diskuteres videre i avsnittet "diagnose på den intelligente batterisensoren".
Batterisensoren overvåker tilstanden til batteriet og måler følgende parametere:
- Batterispenningen.
- Strømmen som batteriet lades og utlades med.
- Temperaturen på batteriet.
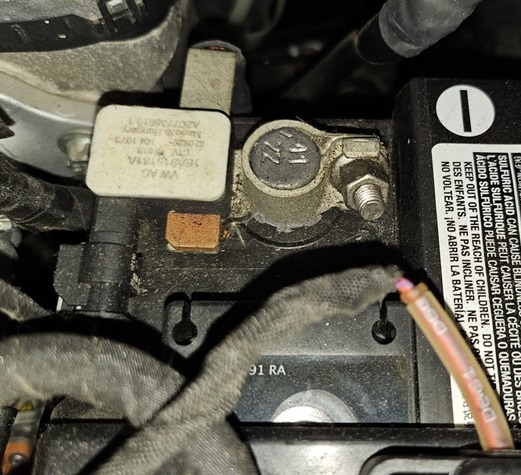
Batterisensoren sender disse dataene til motorkontrollenheten eller BCM. Ved å bruke disse dataene, beregner ECU (elektronisk kontrollenhet) følgende:
Batteriets ladetilstand (SOC). Ved å måle utgående strøm til forbrukerne og inngående strøm til batteriet kan det bestemmes hvor mye energi som fortsatt er tilgjengelig i batteriet.
Batteriets tilstand (State Of Health, SOH). Batterispenningen og utladningsstrømmen sammenlignes for å vurdere kvaliteten på batteriet. Under start kan det trekkes inntil 60 A strøm fra batteriet med en liten bensinmotor eller opptil 120 A med en tyngre dieselmotor. Hvorvidt batterispenningen faller indikerer nivået på intern motstand i batteriet. Hvis spenningen faller fra 11,5 til 10 volt ved en strøm på 60 A, er dette akseptabelt. Hvis spenningen faller fra 11,5 til 8 volt med samme startstrøm, indikerer dette for høy intern motstand i batteriet og krever utskifting.
Stillegående strøm under stillstand. Denne oppdager en forstyrrelse av hvilestrømmen, for eksempel av en uautorisert forbruker. Sjåføren vil motta et varsel under neste tur dersom det oppdages økt hvilestrøm.
Komponenter og måleprinsipper for batterisensoren:
Huset til batterisensoren og jordterminalen er ofte integrert i en helhet. Jordkabelen kan også danne en helhet med batterisensoren eller festes med skruforbindelse. Inne i batterisensoren er det en shuntmotstand med svært lav motstandsverdi. Ved å måle spenningsforskjellen over denne shunten kan strømmen beregnes. I kombinasjon med batterispenningen kan kraften som batteriet lades eller utlades beregnes med.
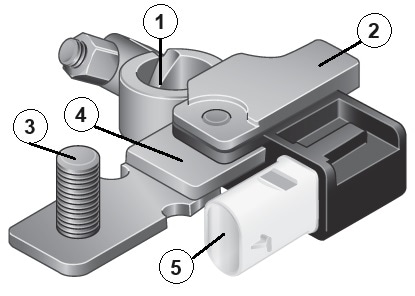
1. Polklemme jordstang;
2. Batterisensor;
3. Kjøretøy jordforbindelse;
4. Shunt;
5. Pluggforbindelse for B+ og LIN buss.
Shuntmotstanden er plassert i serie mellom jordforbindelsen til kjøretøyet og minuspolen på batteriet. All strøm til og fra batteriet går gjennom denne shunten. På grunn av den lave motstandsverdien forbrukes det lite spenning i shunten.
Nivået på denne spenningen konverteres til en strøm i mikroprosessoren, sammen med den kjente motstandsverdien til shunten:
- Et stort spenningsfall over shunten indikerer stor strøm.
- Et lavt spenningsfall indikerer lav strøm.
På det vedlagte bildet ser vi et diagram der motstanden R representerer shunten og strømmen I representerer utladningsstrømmen under utladingen av batteriet. Voltmeteret, som er plassert parallelt over shuntmotstanden, illustrerer hvordan måleelektronikken i batterisensoren måler spenningsforskjellen over denne shunten.
Bildet nedenfor gir en oversikt over stedene hvor temperatur-, spennings- og strømmålinger finner sted.
Shuntmotstanden er angitt med nummer 5. Spenningsforskjellen (V) over shunten avleses som strøm (A). Disse dataene sendes via LIN-bussen til DME/DDE, som er betegnelsene for BMWs bensinmotor (DME) og dieselmotor (DDE).
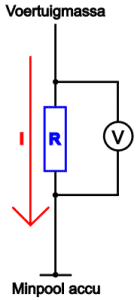
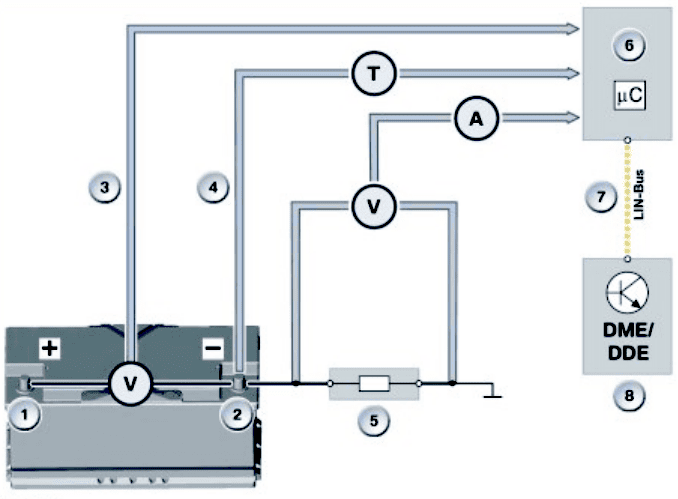
1. Batteriets positive pol;
2. Batterijordingsterminal;
3. Måling av batterispenning;
4. Måling av batteritemperatur;
5. Måling av strømmen ved hjelp av en shuntmotstand;
6. Mikroprosessor i den intelligente batterisensoren;
7. LIN-buss kommunikasjonsledning
8. Motorkontrollenhet
Lading og bytte av batteri:
Batteristyringssystemet bruker batterisensoren til å måle strømmen som flyter til og fra batteriet og lagre denne informasjonen i minnet. Når batteriet skal lades eller hvis det brukes starthjelp, er det viktig at batteriladeren ikke kobles direkte til batteripolene, men til ladepunktene. Batterisensoren er plassert mellom disse ladepunktene og batteripolene og kan kun måle energiflyten når batteriladeren er koblet til ladepunktene. Hvis batteriladeren kobles direkte til batteripolene, vil BMS-minnet indikere at batteriet er (nesten) tomt, mens det i realiteten er fulladet. Generatoren vil da overlade batteriet, hvoretter systemet vil fungere feil. Bildene nedenfor viser en batterilader koblet direkte til batteriet og til ladepunktene under panseret.
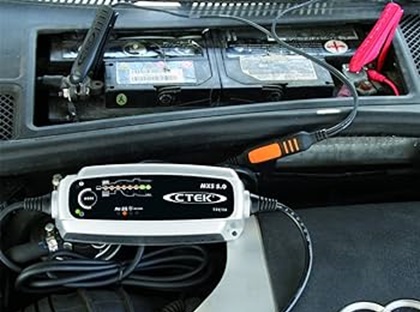
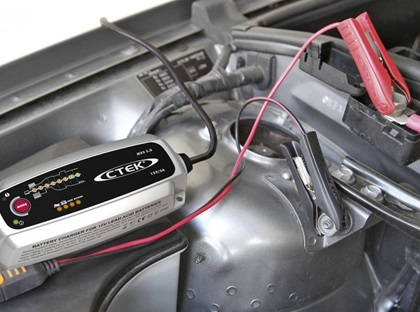
Etter utskifting av batteri skal batteriet registreres på kjøretøy utstyrt med batterisensor. I verkstedet kalles det også «læring» eller «koding». Batterihåndtering tar hensyn til:
- aldring av batteriet. Ladestrømmen til et eldre batteri med økt intern motstand kan økes;
- kapasiteten og kaldstartstrømmen til batteriet.
Under opptak slettes de lagrede verdiene for batteriet som har blitt dårligere over tid. Så selv om et identisk batteri av samme merke og samme kapasitet og kaldstartstrøm er installert, må byttet registreres. Naturligvis må dataene for et batteri med forskjellige egenskaper gjøres kjent. Dette kan gjøres ved å manuelt legge inn kapasiteten [Ah] og kaldstartstrømmen [A], eller ved å taste inn delenumre eller serienumre. Med moderne diagnoseutstyr kan QR-koden som vises på klistremerket til batteriet skannes.
Skjermbildene nedenfor viser registrering av et batteri med et BMW-program (til venstre) og VCDS (til høyre).
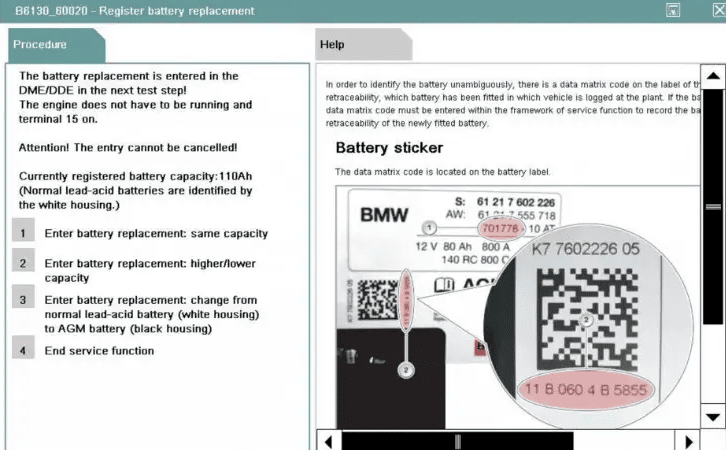
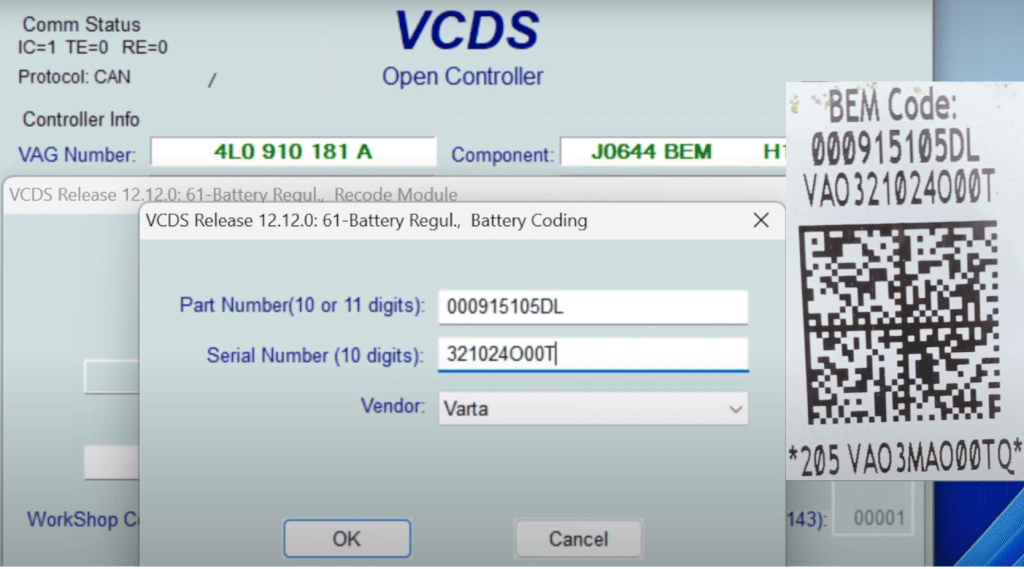
Diagnose på den intelligente batterisensoren:
Den intelligente batterisensoren kommuniserer med dynamoen og BCM eller motorkontrollenheten. Denne delen forklarer hvordan du leser diagrammet og hvordan en diagnose kan stilles.
I det følgende diagrammet ser vi batterisensoren (A85) som forsynes med en forsyningsspenning på 2 volt av en sikring på pinne 12. Pin 1 er for kommunikasjon: herfra sendes en melding via LIN-buss til gatewayen (A25di) og dynamoen (O01). Pinne 1 og 2 er plassert i to-pinners plugg som er synlig på tidligere bilder.
De to nederste svarte ledningene på batterisensoren har ikke et pinnenummer: dette er en direkte tilkobling til den negative polen på batteriet.
Den intelligente batterisensoren sender en LIN-bussmelding til gatewayen og dynamoen. Gatewayen er knutepunktet mellom nettverk med forskjellige protokoller (spenninger og hastigheter). I gatewayen sendes LIN-bussmeldingen via CAN-buss til BCM og/eller motorstyringsenhet. Omvendt styrer en av disse to kontrollenhetene dynamoen via gatewayen og LIN-bussen.
En feil i LIN-busskommunikasjonen kan bety at batterisensordataene ikke kan brukes, eller at dynamoen ikke styres riktig. I sistnevnte tilfelle går dynamoen over til et nødprogram der den konvensjonelle D+-kontrollen brukes til å skape tilstrekkelig ladespenning og ladestrøm.
Spenningsløpet til LIN-busssignal kan med en oscilloskop måles for vurdering.
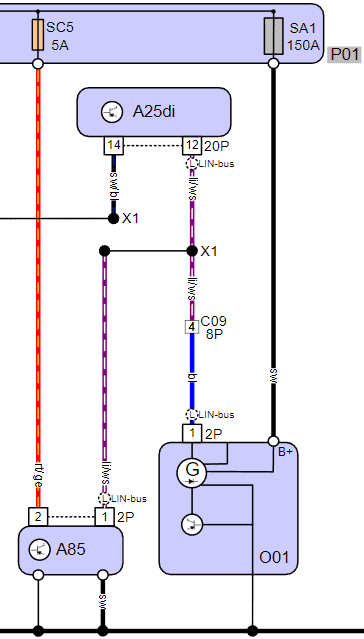
Teksting:
P01: sikringsskap for motorrom
A25di: diagnostisk grensesnitt (gateway)
A85: ECU batterisensor
O01: dynamo
Når det er en feil og LIN-buss-kommunikasjonen er OK, vet vi at forsyningsspenningen og jordingen til sensoren er god. Feilen er forårsaket av en av komponentene i dette diagrammet. Følgende trinn kan tas:
- se etter programvareoppdateringer for kontrollenhetene;
- Test 12 volt batteri (helst under belastning);
- sjekk om riktig batteridata er registrert. Batteriet kan ha blitt byttet ut tidligere, men registreringen ble aldri utført;
- tilbakestill batterisensordataene;
- sjekk at delenummeret til dynamoen er riktig: en feil dynamo som ikke samsvarer med sensoren vil til slutt forårsake problemer;
- Hvis ovenstående er kontrollert og funnet å være riktig, kan det være mulig å konkludere med at batterisensoren er defekt. Dette skjer noen ganger med hyppig (feil) start via startkabler eller en batteriforsterker.
Relaterte sider: