科目:
- 一般
- ノギス
- ネジゲージ
- ダイヤルインジケーター
- 隙間ゲージ
- プラスティゲージ
一般:
測定ツールは、エンジン検査などの自動車技術でよく使用されます。 ただし、測定ツールはブレーキライニングやブレーキディスクの厚さを測定するためにも使用されます。 測定を実行するには、ツールがどのような測定精度で設計されているかを知ることが重要です。 シリンダーの直径はノギスの内側の測定ジョーで測定できますが、精度は十分ではありません (1/20 mm)。 ダイヤルインジケーターはより正確です (1/100 mm)。
作業場で最も一般的な測定ツールとその精度は次のとおりです。
- ノギス(0,05mm、1/20mmと同じ)
- ネジサイズ(0,01mmまたは1/100mm)
- ダイヤルインジケーター(0,01mm)
- すきまゲージ(0,05mm)
- プラスティゲージ (精度はバージョンによって異なります)。
このページでは、前述の測定ツールの設定、読み取り、必要に応じて校正する方法を説明し、測定例を示します。
ノギス:
キャリパーは自動車技術で広く使用されている測定ツールです。 ノギスを使用すると、部品の内側、外側、深さの寸法を XNUMX ミリメートル単位で正確に測定できます。
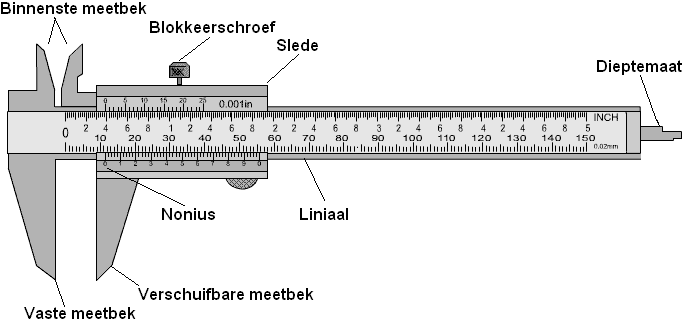
固定測定ジョーによる測定:
固定測定ジョーにコンポーネントをクランプすることでサイズを読み取ることができます。 定規は 20mm を読み取ります。 これはリングの外径です。
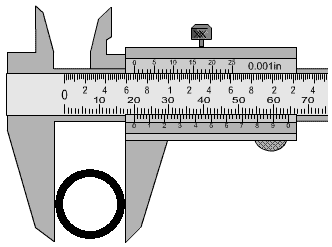
内側の測定ジョーを使用した測定:
リングの内側に測定ジョーをクランプすることで内径を読み取ることができます。 こちらは18mmです。 これは、リングの厚さが (20-18) = 2 mm であることを意味します。
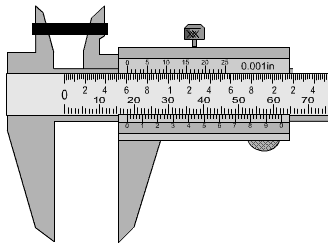
デプスゲージによる測定:
例えば、表面から取り除くことができない物体や、底のある円柱の場合は、デプスゲージを使用して高さを測定できます。 デプスゲージの端を表面に置き、キャリパーの厚い部分をコンポーネントに置くことで、その高さを決定できます。 この場合、黒いブロックの高さは次のように決定されます。
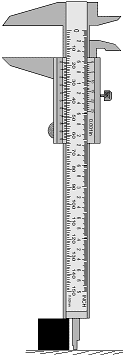
キャリパーを読み取るには、0分の1,1ミリメートルも見る必要があります。 バーニアの次の線と定規の線が全く同じになる箇所が、寸法を11分の10ミリ(小数点以下)で示します。 画像ではバーニアの11,0がXNUMXcmなので、定規からXNUMXmmの位置にあります。 バーニアのXNUMXの線も定規の線と同じです。 これは、ちょうど XNUMX mm があることを意味します。 wordt 測定した。
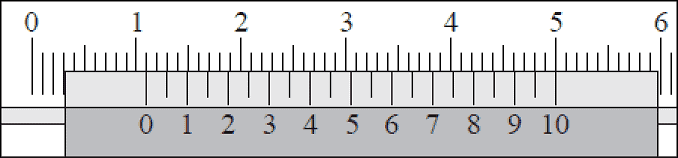
次の測定ではバーニアがわずかに左に移動し、小数点以下の数値を扱っています。 バーニヤの次の線が定規の線と全く同じになるところを見ます。 画像ではバーニアの0が1,1cmなので11(丸)ミリです。 バーニアの9の線も定規の線と同じです。 これは、正確に 10,9 mm が測定されることを意味します。
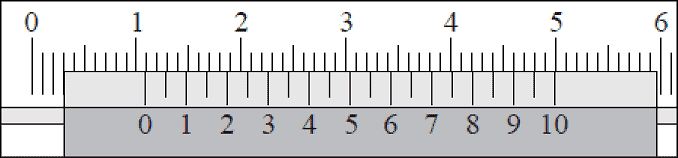
画像の測定も同じ原理に従います。 この場合、バーニアの 0 は定規の 15 mm と 16 mm の中間にあります。 その場合、原則として 4 進数は 5、6、または 5 程度であることがすでにわかっています。 定規と副尺の線は 15 で対応します。 したがって、(0,5+15,5) = XNUMX mm が測定されます。
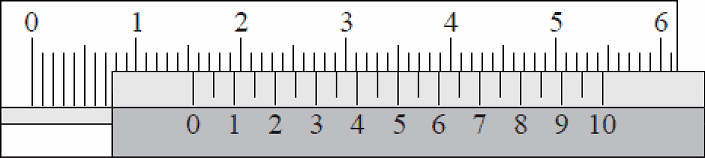
バーニアの数字の間にも小さな線があります。 これらは 0 分の 1 ミリメートルを示します。 バーニアの 10 と 0,05 の間の線は定規の線に対応します。 図では、(10,05 + XNUMX) = XNUMX mm となります。 XNUMX分のXNUMXを読むには訓練された目が必要です。
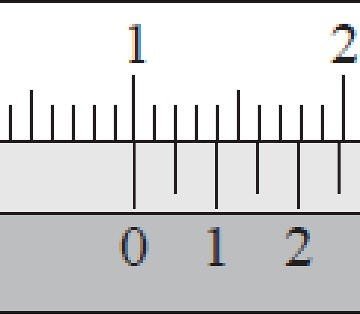
このアニメーションでは、バーニアの読み取りを赤い矢印で明確にしています。

画像に示すように、キャリパーをデジタルで作成することもできます。 測定対象の部品の寸法はデジタル表示で読み取ることができます。 多くの場合、これはインチとミリメートルの両方に設定することもできます。
上の画像ではデジタル表示になっているアナログ ダイヤル インジケーターを備えたノギスもあります。 このキャリパーはあまり使用されませんが、ユーザーが何を使用するかを好みます。
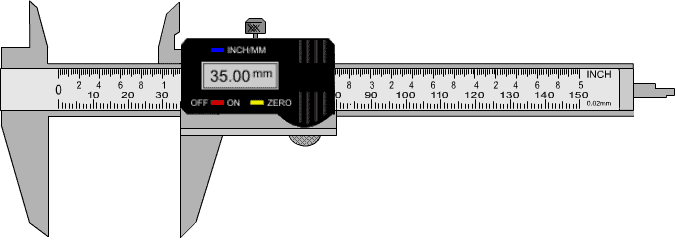
ネジサイズ:
ネジゲージ(マイクロメーター、ブラケットマイクロメーターとも呼ばれます)が使用できます。 ワーデン サイズが 25 mm までのコンポーネントを 0,01 分の 0,5 ミリメートル (XNUMX mm) の精度で測定するために使用されます。 測定ドラムが XNUMX 回転すると、測定スピンドルは XNUMX mm 移動します。
手の熱が測定結果に影響を与えるため、マイクロメーターは常に絶縁ハンドルを持ってください。 マイクロメーター内の局所加熱により、材料がわずかに膨張する可能性があります。 特に、結果を XNUMX 分の XNUMX の位まで測定する必要がある測定の場合は、規則に従うことが重要です。
測定するコンポーネントは、アンビルと測定スピンドルの間に配置する必要があります。 測定ドラムを回転させることにより、測定軸が前後に移動します。 測定スピンドルがコンポーネントに接触する前に、感度ネジを使って最後の距離を締める必要があります。 感覚ネジにはクリック機構が組み込まれており、一定の力を加えると「カチッ」と音が鳴ります。 その瞬間、これ以上メーターを回すことはできないことがわかります。 マイクロメーターを締めすぎると、誤った測定結果が得られる可能性があります。 測定ドラムは、ロッキングレバーでそれ以上回転しないようにロックできます。
以下はボールベアリング(測定対象物)のサイズを計測するマイクロメーターのイメージです。 wordt 測定した。
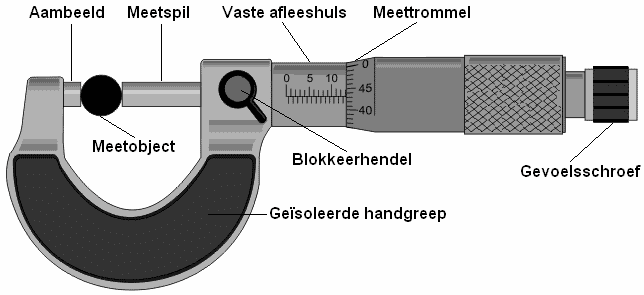
上の画像では、ボール ベアリングの厚さは 13,43 mm です。 一番上のスケールには 10 が表示され、その横に 3 本の線があります。 各線は 10 ミリメートルなので、3+13 = 40 mm となります。 小数点以下の数値を計量ドラム上で読み取ります。 ここに 45 と 43 という数字があります。よく見ると目盛りの線が 13,43 に等しいことがわかります。これを合わせると XNUMX mm になります。
測定ドラムには 0,0 ~ 0,49 mm の目盛りが付いています。 これは、全ミリメートルの目盛り (計量ドラムの左側) にも XNUMX ミリメートルが含まれているためです。 下の線はXNUMXミリメートルを示します。 以下にいくつかの例を示します。
横線にはミリメートル単位が表示されます。 この場合は13mmです。 測定ドラム上の 16mm の線は、読み取りスリーブ上の水平線と等しくなります。 この画像に示されているサイズは、(13 + 0,16) = 13,16 mm です。
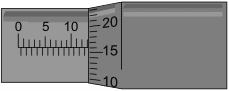
リーディングスリーブの目盛線の下の線が画像に表示されます。 水平線の下にあるこの線は、5,5 ミリメートルであることを示しています。 スケールによると、少なくとも 36 ミリメートルです (測定ドラムを考慮せずに)。 計量ドラムの目盛は 5,5 を示しています。 現在表示されているサイズは合計 (0,36 + 5,86) = XNUMX mm です。
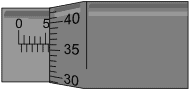
この画像では、目盛線の下部の線が再び測定ドラムに最も近くなります。 したがって、水平スケールによると、やはり少なくとも 12,5 mm になります。 次に、測定ドラムの指示値を追加します。 この値は 0,35 mm です。 次に、12,5 と 0,35 を加算します。
合計すると、(12,5 + 0,35) = 12,85 mm になります。
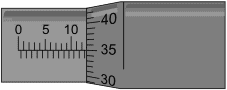
この画像では、示されているサイズは (16 + 0,355) = 16,355 mm です。
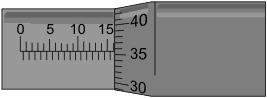
画像はネジ サイズの値 75,235 mm を示しています。 測定ドラムの目盛りは 23 ~ 24 mm です。 口径が75mmなのでネジサイズは0,235mmずれます。 したがって、実行されるすべての測定値は高すぎます。 適切な調整フォークを使用して、読み取りスリーブをハンドルに対して回転させる必要があります。 調整フォークは上の画像で見ることができます。
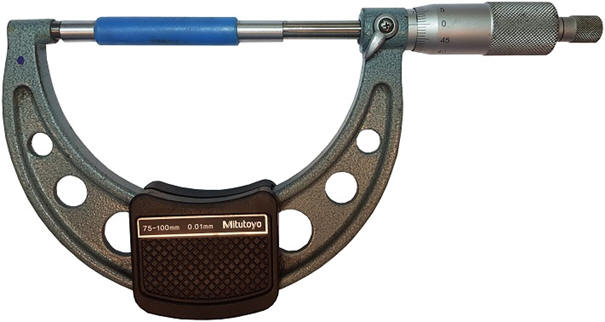
マイクロメータで測定する前に、まず校正する必要があります。 不適切な校正は測定エラーにつながります。 ネジのサイズは適切な口径を使用して校正されます。 下の画像の口径は正確に 75,00 mm です。 これは、ねじゲージが口径を測定するときに、ねじゲージがこの数値を正確に示す必要があることを意味します。 測定値が正しくない場合は、まずフォークでインナードラムを回転させてネジのサイズを校正する必要があります。
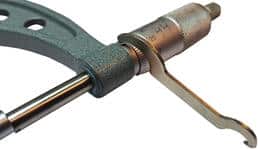
ダイヤルインジケーター:
ダイヤルインジケーターにより、非常に正確な深さ測定が可能です。 内側の小さな針はミリメートルを示し、大きな針は小数点以下の数字を示します。 ダイヤルゲージを真っ直ぐな面に置くと、下図のように 0,00 mm と表示されます。 外輪を回転させて校正することができます。 真っ直ぐな面に置いて0,3mmを測る場合、大きい針が0を指すように外輪を回してください。
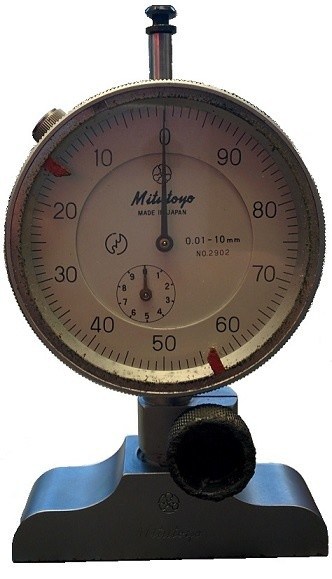
写真のダイヤルインジケーターは5,00mmを示しています。 小さな針は 5 にあり、大きな針は 0 にあります。大きな針が 81 にあり、小さな針が 5 ~ 6 の間にある場合、メーターは 5,81 mm の値を示します。 測定ピンの底部を押し上げるほど、読み取り値は小さくなります。
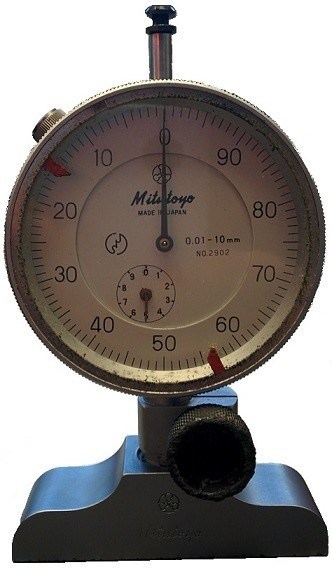
マイクロメーターの目盛りは 0.01 ~ 10 mm を示します。 これは、マイクロメータが 0.01 ~ 10 mm の値を指示できることを意味します。 したがって、深さが 12 mm の場合は、測定ピンが短すぎて針でそれを示すことができないため、深さ測定を実行することはできません。 10mmを超える値を測定できるように、マイクロメーターにはさまざまなエクステンションが付属しています。 この例を画像で見ることができます。 ここでは伸びをマイクロメーターで測定します。 これは10,0mmの値を示します。
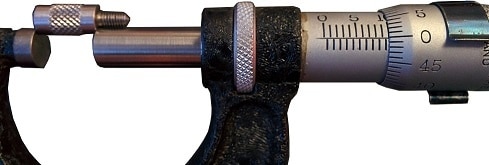
ねじ山ではなく、樽型部分のみが測定されます。 このエクステンションをマイクロメーターに取り付けることで、測定ロッドが短すぎることがなくなります。 たとえば、12mm の値は引き続き測定できます。 ここで、拡張部分のサイズが測定値に追加されていることを確認する必要があります。 例として、マイクロメーターが5,19mmを指している場合、実際の寸法は測定値+測定ピンの長さになりますので、 5,19 + 10,00 = 15,19 mm.
これらのページでは、ダイヤル インジケーターを使用して測定が行われます。
隙間ゲージ:
隙間ゲージは、30 つの部品間の間隔を測定するために使用されます。 隙間ゲージは、それぞれ異なる厚さの多数の金属ストリップで構成されています。 厚さは金属ストリップに記載されています。 下の画像の隙間ゲージの一番下のストリップには「0,30」と書かれています。 これは、金属ストリップの厚さが XNUMX mm であることを意味します。
XNUMX つの部品間のスペースを測定するには、金属ストリップを広げて部品間にスライドさせます。 ストリップが非常に簡単に、または抵抗なく通過できる場合、スペースはストリップの厚さよりも大きいことになります。 したがって、より厚い金属ストリップを広げる必要があります。 ストリップが入らなくなった場合は、ストリップが厚すぎます。 ある程度の抵抗を感じながらストリップをパーツ間でスライドさせることができる場合は、それが適切なサイズです。
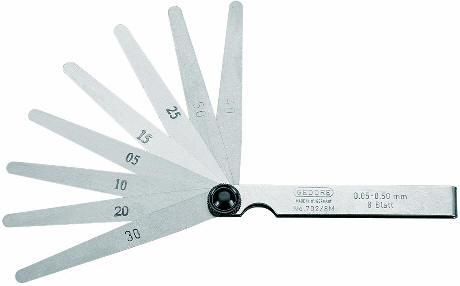
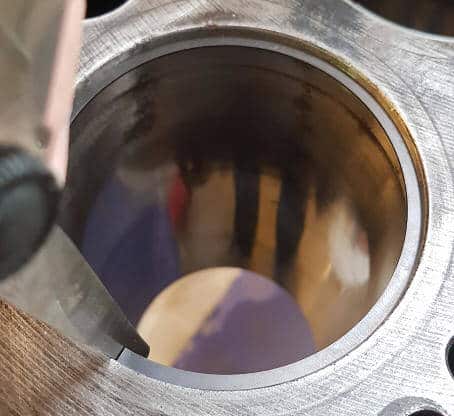
プラスティゲージ:
プラスチゲージを使用して、滑り軸受間の隙間を確認できます。 プラスステージは、隙間を測定する必要がある部品に適用する必要がある特殊なプラスチック ワイヤです。 次に、プラスティゲージが平らになるようにベアリング キャップを固定する必要があります。 プラスティゲージの変形はクリアランスの尺度になります。
プラスティッジにはさまざまな色があります。 各色は異なるサイズを表します。
- 緑: ベアリングすきまが 0,025 ~ 0,076 mm の場合。
- 赤: 0,050 – 0,150 mm。
- 青: 0,102 – 0,229 mm。
- 黄色: 0,23 – 0,51 mm。
このページでは、プラスティゲージを使用した測定が実行されます。
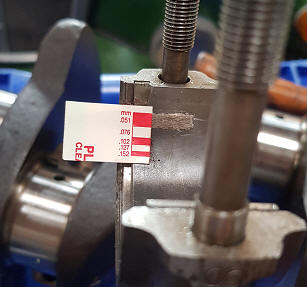
関連ページ: