Soggetti:
- Determinare e installare gli attuatori per il sistema di gestione del motore
- Iniettori di carburante
- Scelta degli iniettori adatti
- Installazione degli iniettori nel collettore di aspirazione
- infiammazione
- Preparazione con l'accensione convenzionale
- Bobina di accensione per il sistema di gestione del motore
- Accumulo di corrente nella bobina primaria
- Anticipo dell'accensione
- corpo farfallato
- Prova la configurazione del motore passo-passo con il simulatore
- Impostazioni del motore passo-passo
- Circuito della pompa del carburante
- Completamento del lavoro meccanico
Determinazione e installazione degli attuatori per il sistema di gestione del motore:
Gli attuatori che verranno controllati con il MegaSquirt sono gli iniettori, la bobina di accensione, la pompa del carburante e il motore passo-passo per il minimo. Questo capitolo descrive il processo in cui gli attuatori sono stati testati e installati sul blocco motore e la selezione effettuata.
Iniettori di carburante:
Il MegaSquirt controlla gli iniettori. Gli iniettori sono collegati a massa. Con un componente collegato a terra è presente una tensione di alimentazione, ma la corrente circola solo quando la terra è collegata. In questo caso l'iniettore inietterà solo quando la ECU MegaSquirt passa a massa. Non appena si interrompe l'attivazione, l'iniettore smette di iniettare. La quantità di carburante da iniettare viene determinata in base alla tabella VE e alla tabella AFR.
Un MOS FET accende e spegne l'iniettore, provocando l'iniezione del carburante. La quantità di carburante determinata dal MegaSquirt dipende da diversi fattori:
- La legge dei gas ideali che mette in relazione la quantità di aria con la sua pressione, volume e temperatura;
- Valori misurati dai sensori nel blocco motore: pressione nel collettore di aspirazione (sensore MAP), temperatura del liquido di raffreddamento e dell'aria aspirata, velocità dell'albero motore e dati dal sensore di posizione dell'acceleratore;
• Parametri di regolazione: quantità di carburante richiesta, grado di riempimento (VE), tempo di apertura dell'iniettore e arricchimento in determinate condizioni.
Il tempo di iniezione dovrebbe essere il più lungo possibile mentre il motore è al minimo per ottenere un buon dosaggio del carburante. Pertanto, sul motore non è possibile utilizzare un iniettore qualsiasi. È necessario confrontare le proprietà dei diversi tipi di iniettori e i calcoli devono fornire informazioni sulla quantità di carburante necessaria per il motore in questione. C'era anche la possibilità di scegliere tra iniettori ad alta e bassa impedenza. Gli iniettori a bassa impedenza sono adatti per motori dove è richiesta un'apertura molto rapida dello spillo dell'iniettore. La resistenza tipica è di 4 ohm. Lo svantaggio di questi iniettori è l'elevata corrente. Lo sviluppo di calore che questo crea nel MegaSquirt non è desiderabile. È possibile utilizzare iniettori a bassa impedenza montando IGBT speciali su una piastra termoconduttiva sull'alloggiamento MegaSquirt. Si è deciso di utilizzare iniettori ad alta impedenza. C'è meno sviluppo di calore e questi IGBT non vengono utilizzati.
La dimensione del passaggio (flusso) è molto importante per determinare la corretta quantità di iniezione, e quindi il controllo. Se si scelgono iniettori troppo grandi, il tempo di iniezione al minimo sarà così breve che il motore potrebbe funzionare in modo irregolare. La quantità iniettata deve essere sufficiente ad iniettare tutto il carburante nel tempo a disposizione. La quantità di iniezione è indicata come tempo di iniezione in millisecondi. Ad un regime motore elevato si presuppone un carico elevato. Questo è ad una MAP di 100 kPa. Il flusso dell'iniettore richiesto può essere calcolato in base alle proprietà del motore. Il flusso dell'iniettore indica quanti millilitri di carburante vengono iniettati al minuto.
Scelta degli iniettori adatti:
Per il progetto sono stati resi disponibili iniettori di tre diversi tipi. La ricerca ha dimostrato quale tipo di iniettore era più adatto all'uso in questo progetto.
Ogni tipo di iniettore ha un flusso diverso; la resa dopo un minuto di iniezione varia a seconda del tipo. Prima del test gli iniettori sono stati sottoposti a pulizia in un bagno ad ultrasuoni. Con questo metodo di pulizia, l'iniettore viene pulito dentro e fuori utilizzando vibrazioni ultrasoniche e uno speciale fluido di prova, in modo che eventuali vecchi residui di sporco non possano influenzare la misurazione del flusso o il modello di iniezione. Durante la pulizia ad ultrasuoni, gli iniettori sono stati aperti e chiusi continuamente ed è stato esaminato il modello di iniezione di ciascun iniettore; questa era una bellissima nebbia. Durante la chiusura non erano visibili anomalie come la formazione di gocce o un getto deviato. Dopo la pulizia e il test ad ultrasuoni, gli O-ring sono stati sostituiti per garantire una buona tenuta quando montati nel collettore di aspirazione.
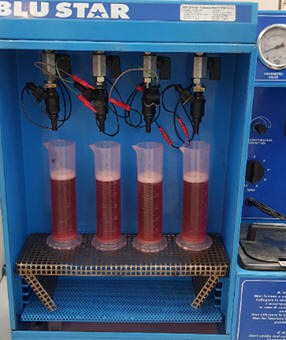
Utilizzando una configurazione di prova (vedi immagine sopra), gli iniettori possono iniettare in più misurini, in modo che la quantità di carburante iniettata possa essere letta dopo un certo tempo. Controllando gli iniettori ad una pressione di esercizio di 3 bar, è possibile controllare la quantità di carburante iniettato. La pressione del carburante sulla linea di alimentazione (rail) deve essere di 3 bar e lo spillo dell'iniettore deve essere attivato per 30 o 60 secondi con un duty cycle del 100%. Dopo aver attivato gli iniettori per 30 secondi è stato possibile inserire i seguenti dati:
Tipo 1: 120 ml
Tipo 2: 200 ml
Tipo 3: 250 ml
Verrà utilizzato un solo tipo di iniettore. La dimensione dell'iniettore viene determinata utilizzando la formula seguente:

La dimensione degli iniettori viene determinata in base alla potenza effettiva (Pe) erogata ad una determinata velocità, al Break Specific Fuel Consumption (BSFC), al numero di iniettori (n iniettori) e al duty cycle massimo con cui vengono controllati gli iniettori. Il totale viene moltiplicato per 10.5 per convertire da libbre all'ora (lb/hr) a ml/min.
La risposta al calcolo indica quale iniettore è adatto per questa configurazione del motore. Non è un problema se c'è una deviazione inferiore a 20 ml dal valore calcolato. Questa differenza viene compensata adattando il software nel MegaSquirt. La tabella seguente fornisce una panoramica dei dati utilizzati nelle formule:
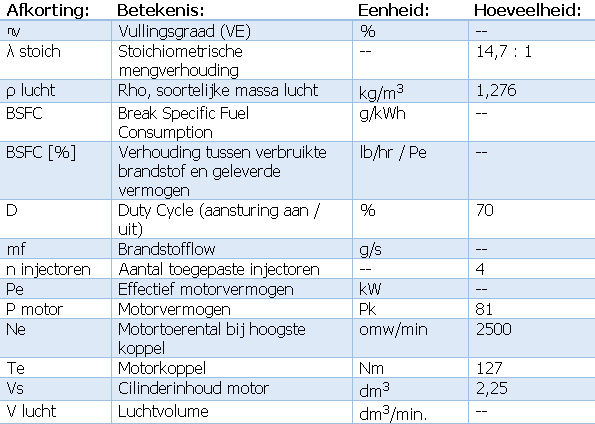
Il primo passo è determinare il carburante iniettato alla velocità di coppia. Ogni due giri dell'albero motore viene aspirata una certa quantità d'aria. Il grado di riempimento è massimo alla velocità di coppia. A causa delle caratteristiche del motore (inclusa la sovrapposizione delle valvole), a questa velocità il motore si riempie meglio e l'efficienza è massima. Si stima che il tasso di riempimento sarà di circa il 70%. La Formula 4 calcola il volume d'aria presente nel motore in quel momento.
Nella formula 5 la quantità di carburante iniettato viene calcolata in base al volume di aria presente. La potenza del motore raggiunta al regime di coppia viene calcolata nella formula 6. Il rapporto tra la quantità di carburante iniettato e la potenza indica il BSFC nelle formule 7 e 8.
Il BSFC effettivo viene moltiplicato per 6 nella formula 3600 per convertirlo in kWh. Il BSFC di un motore a benzina è spesso compreso tra 250 e 345 g/kWh. Più basso è il valore, più efficiente è il motore. La formula 8 indica la relazione tra il flusso di carburante in libbre/ora e la potenza effettiva del motore. Questa percentuale è inclusa nella formula 9.



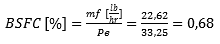

La risposta alla formula 9 ha chiarito che gli iniettori con un flusso di 200 ml/min sono adatti per l'uso nel motore. La differenza di 7 ml è trascurabile perché viene compensata nel software durante la compilazione della tabella VE.
Installazione degli iniettori nel collettore di aspirazione:
Il sistema di iniezione a controllo elettronico consente la rimozione del carburatore, che fa parte dell'allestimento classico. Il carburatore viene quindi sostituito da un corpo farfallato (per l'alimentazione dell'aria) e quattro iniettori di carburante separati. Il collettore di aspirazione è stato mantenuto ed è stato modificato per consentire la conversione al sistema di gestione del motore. L'iniezione del carburante avviene nel collettore di aspirazione. Si è deciso di montare gli iniettori il più vicino possibile alla valvola di aspirazione. Nella maggior parte dei casi, i produttori di motori automobilistici scelgono di montare la valvola di aspirazione obliquamente nel collettore di aspirazione. Il carburante viene spruzzato contro la valvola di ingresso. Tuttavia, per il progetto attuale, è stata scelta una configurazione in cui gli iniettori sono posizionati ad un angolo di 45 gradi rispetto ai condotti dell'aria nel collettore.
Il collettore di aspirazione è realizzato in fusione di alluminio. Si è deciso di fissare delle boccole in alluminio al collettore. La lavorazione manuale ad una buona dimensione non era un'opzione, perché le boccole dovevano avere dimensioni diverse rispetto a una punta di dimensioni standard. Ciò significava che l'outsourcing dei furgoni doveva essere affidato a un'azienda con attrezzature adeguate. Le boccole potranno poi essere fissate al collettore mediante saldatura TIG. La scelta di montare gli iniettori in posizione verticale anziché inclinata è stata fatta per il seguente motivo:
- Il processo di assemblaggio: è più semplice disporre i furgoni in una disposizione diritta e orizzontale. Saldare i furgoni al collettore è più semplice perché ora è più facile saldare tutto intorno rispetto alla situazione in cui il furgone è ad angolo.
- Post-lavorazione: Durante la saldatura le boccole diventano un po' ovali. La deformazione è causata dal calore rilasciato durante il processo di saldatura. Di ciò si è tenuto conto riducendo il diametro interno delle boccole rispetto al diametro esterno degli iniettori. La finitura (alesatura) è meno rischiosa: una volta arrotondati i manicotti all'interno, il diametro è ottimale per gli iniettori, e la tenuta da parte degli O-ring è garantita. L'altezza dei furgoni è importante; l'iniettore non deve essere posizionato troppo in profondità nel collettore. L'estremità dell'iniettore non deve ostacolare il flusso d'aria. Dalle informazioni della fonte: (Banish, Engine Management, advanced tuning, 2007) si è deciso di montare gli iniettori così in profondità nel collettore che le estremità si trovino esattamente nei fori del collettore; il flusso d'aria non è ostacolato.
- Iniezione di carburante: poiché la miscelazione della nebbia di carburante con l'aria è ottimale prima dell'apertura della valvola di aspirazione, non ha molta importanza se l'iniettore inietta esattamente nella valvola di aspirazione o subito prima nel collettore di aspirazione.
Con l'iniezione simultanea, l'iniezione avviene ad ogni rotazione dell'albero motore (360°). I quattro iniettori iniettano contemporaneamente. Ciò significa che il carburante viene iniettato nel tratto di aspirazione anche quando la valvola di aspirazione non è aperta. Dopo qualche tempo la valvola di ingresso si apre e il carburante entra ancora nel cilindro.
Le boccole vengono appositamente tagliate su misura al tornio. Il diametro interno è leggermente inferiore al diametro esterno dell'iniettore; Poiché durante il processo di saldatura avviene una deformazione, deve esserci la possibilità di rimuovere il materiale durante la post-lavorazione mediante alesatura. Ciò significa che il diametro aumenta leggermente perché il materiale viene asportato. Il diametro non dovrebbe essere troppo grande, altrimenti c'è la possibilità che l'O-ring di gomma sull'iniettore non riesca più a chiudere abbastanza bene. Una buona tenuta è molto importante; la perdita d'aria oltre l'iniettore determina una depressione inferiore nel collettore di aspirazione.
La pressione negativa misurata quindi non corrisponde più alla pressione negativa calcolata. Ciò influisce sull'iniezione, che viene determinata sulla base della tabella VE. La pressione negativa gioca un ruolo importante in questo. Le caratteristiche e le impostazioni della tabella VE sono descritte nel capitolo successivo.
Sul fondo delle boccole è stato limato il bordo smussato in modo che le forme corrispondano a quelle del collettore di aspirazione. Il furgone deve quindi essere il più verticale possibile. L'immagine sotto mostra il collettore di aspirazione con una bombola durante il processo di assemblaggio. Il manicotto è incollato su un lato, in modo che si possa vedere chiaramente come la saldatura influisce sul materiale. Non era chiaro se l'alluminio del collettore contenesse troppa contaminazione, il che avrebbe reso difficile la saldatura. Questo si è rivelato ok. Per evitare che le boccole si spostassero dalla loro posizione durante la saldatura, sono stati praticati preventivamente dei fori nel collettore e le boccole sono state mantenute nella posizione corretta con una maschera appositamente realizzata su misura. In questo modo le quattro boccole vengono saldate tutt'intorno. Da un ultimo controllo è emerso che i collegamenti tra le boccole ed il collettore erano a tenuta d'aria.
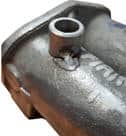
Il collegamento tra gli iniettori è normalmente formato da una solida guida per iniettori. Questo tubo con raccordi, spesso in lega di alluminio, viene realizzato su misura da un produttore. Il motore Land Rover utilizzato per il progetto ha due iniettori uno accanto all'altro, ma lo spazio tra le coppie di iniettori è piuttosto ampio. Le dimensioni del condotto del carburante e lo spazio tra i condotti dell'aria del collettore di aspirazione non corrispondevano. La rotaia ha quindi dovuto essere adattata.
Accorciare alcune parti ed allungarne altre mediante saldatura è molto difficile; la contaminazione da vecchio carburante, molto difficile da rimuovere dall'interno della rotaia, può causare un deterioramento dell'adesione. Poiché si tratta di carburante, è stato scelto il metodo più sicuro; le parti su cui sono fissati gli iniettori sono collegate da un tubo del carburante di alta qualità. I bordi aggraffati sono stati montati su tutte le estremità e sono state utilizzate robuste fascette stringitubo per evitare che i tubi scivolino sui bordi aggraffati.
L'immagine sotto mostra il collettore di aspirazione al momento della lavorazione. La linea di alimentazione (contrassegnata con il numero 1) è collegata all'uscita della pompa del carburante. Il carburante viene fornito all'ingresso dei quattro iniettori ad una pressione di 3 bar. Il regolatore di pressione (3) regola la pressione in base alla pressione del collettore di aspirazione, poiché la differenza di pressione tra la pressione del carburante e la depressione nel collettore di aspirazione deve rimanere di 3 bar. Il carburante ritorna al serbatoio attraverso la linea di ritorno (2). C'è una circolazione continua di carburante. L'iniezione avviene solo quando gli iniettori sono controllati dalla ECU MegaSquirt.
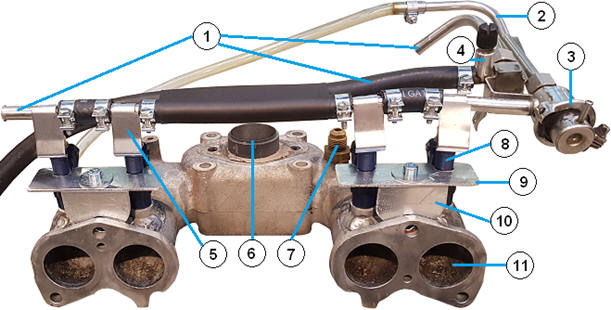
- linea di alimentazione
- linea di ritorno
- regolatore di pressione
- Controllo della pressione
- scudo termico
- Collegamento valvola gas
- Collegamento a pressione negativa
- Cilindro dell'iniettore 1
- Staffa dell'iniettore A
- Staffa dell'iniettore B
- Cilindro del condotto di aspirazione 1
Nelle autovetture esistenti, il binario dell'iniettore è fissato al collettore di aspirazione mediante fascette o occhielli. La guida degli iniettori blocca gli iniettori nel collettore. Poiché per questo progetto è stato scelto un tubo flessibile del carburante come binario iniettore, quanto sopra non è possibile. Si è quindi deciso di fissare gli iniettori nel collettore di aspirazione con una staffa realizzata su misura. Le staffe sono composte da due parti: la parte superiore (staffa A) e la parte inferiore (staffa B).
La staffa A contiene due tacche che possono essere fatte scorrere sugli iniettori. Ciò consente agli iniettori di essere pressati nel collettore mediante i lati piatti. Entrambe le staffe A sono dotate di fori asolati in modo da poter regolare la distanza tra gli iniettori e le asole stesse. Le staffe A e B sono avvitate insieme: la staffa B è fissata allo stesso prigioniero che monta il collettore al motore. Un foro asolato consente di regolare la staffa in direzione verticale. Quanto più la staffa viene spostata verso il basso, tanto più saldamente l'iniettore viene bloccato.
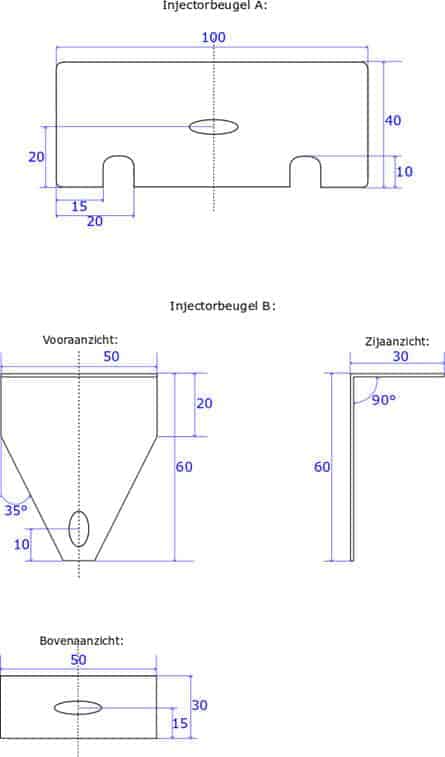
accensione:
L'accensione convenzionale è stata sostituita da un sistema di accensione a controllo elettronico con una bobina di accensione controllata dal MegaSquirt. Affinché il motore funzioni pienamente con le tecniche originali, è necessario prima collegare il sistema convenzionale con punti di contatto. Solo dopo alcune ore di funzionamento è possibile accertarsi che il motore funzioni correttamente, dopodiché si può iniziare l'installazione e la regolazione, tra le altre cose, dell'accensione controllata elettronicamente.
Preparazione con l'accensione convenzionale:
Il motore Land Rover era originariamente dotato di un sistema di accensione con punti di contatto, ora chiamato anche sistema di accensione convenzionale. L'immagine mostra questo tipo di sistema di accensione.
Con i punti di contatto chiusi inizia l'accumulo della corrente primaria. La corrente è limitata a 3-4 A dalla resistenza dell'avvolgimento primario. Quando una corrente scorre attraverso la bobina primaria della bobina di accensione, verrà creato un campo magnetico. Sia la bobina primaria (3) che quella secondaria (4) si trovano in questo campo magnetico. Quando la corrente attraverso i punti di contatto (10) viene interrotta dalla camma dell'interruttore (9) sull'albero del distributore, viene indotta una tensione in entrambe le bobine. Nella bobina primaria vengono prodotti circa 250 volt. La differenza negli avvolgimenti creerà una tensione di induzione compresa tra 10 e 15 kV nella bobina secondaria. La scintilla della candela si crea quando si aprono le puntine.
La tensione di induzione può essere limitata lasciando fluire la corrente primaria per un po' dopo l'apertura dei punti di contatto. Ciò si ottiene con un condensatore collegato in parallelo attraverso i punti di contatto. Il condensatore è un elemento che determina il tempo che, a seconda della capacità, regola effettivamente il livello della tensione di induzione. Inoltre si evita che i punti di contatto brucino.
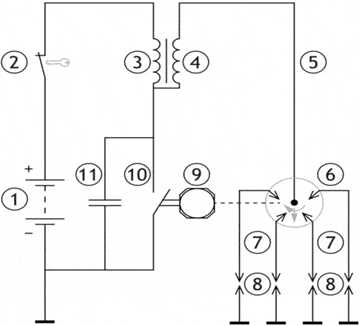
Bobina di accensione per il sistema di gestione del motore:
Il sistema di gestione del motore controllerà la bobina di accensione. La classica bobina di accensione con distributore rimane sul motore e funge da banco di prova, ma non fa più parte del funzionamento del motore a combustione. È stato scelto un sistema di accensione senza distributore (bobina di accensione DIS), liberamente tradotto come: “sistema di accensione senza distributore”. Questo tipo di sistema di accensione non utilizza un distributore. Un'altra opzione era quella di scegliere una bobina di accensione Coil on Plug (COP). A ciascuna candela è collegata una bobina di accensione separata. Una bobina di accensione COP è anche chiamata bobina di accensione a pin. Lo svantaggio di una bobina d'accensione COP è che la dissipazione del calore è meno buona di quella di una bobina d'accensione DIS. Quando si utilizzano bobine di accensione COP è necessario anche il segnale di un sensore albero a camme, che nel motore attuale non è presente.
Il dente mancante nella puleggia dell'albero motore funge da punto di riferimento in base al quale viene determinata la fasatura dell'accensione. Con la bobina di accensione DIS, due candele verranno attivate contemporaneamente al momento dell'accensione. La bobina d'accensione DIS è in realtà un'unità in cui sono montate due bobine d'accensione. Quando i pistoni dei cilindri 1 e 4 si spostano verso l'alto, uno sarà impegnato nella corsa di compressione e l'altro in quella di scarico. Tuttavia, entrambe le candele genereranno una scintilla. La scintilla creata dal cilindro impegnato nella corsa di compressione provocherà una miscela di accensione. L'altra scintilla, la cosiddetta “scintilla sprecata”, scintilla quando i gas di scarico lasciano la camera di combustione. La scintilla sprecata è una scintilla che si forma quando non viene accesa alcuna miscela. L'energia di accensione è bassa; nonostante la scintilla, la perdita di energia è minima. Inoltre non è dannoso.
La figura mostra lo schema di funzionamento di un motore a benzina a quattro cilindri con bobina di accensione DIS. Questo diagramma di lavoro mostra due segni di accensione per momento di accensione; 1 di essi genera la scintilla per accendere la miscela, l'altro è la scintilla sprecata. Una bobina d'accensione DIS può essere controllata dal MegaSquirt con soli due impulsi.
Quando la corsa di compressione avviene nel cilindro 1 e la corsa di scarico nel cilindro 4, MegaSquirt controlla la bobina primaria A tramite il pin 36 su DB37 (vedi immagine sotto). Questo controllo avviene in base al punto di riferimento dell'albero motore (tra 90 e 120 gradi prima del PMS). Il MegaSquirt controlla la bobina primaria B, responsabile della formazione della scintilla nei cilindri 2 e 3, e viene ruotata di 180 gradi dopo la bobina A. Non esiste un punto di riferimento per la bobina B, ma il momento dell'accensione può essere determinato semplicemente contando i denti sulla ruota fonica 36-1.
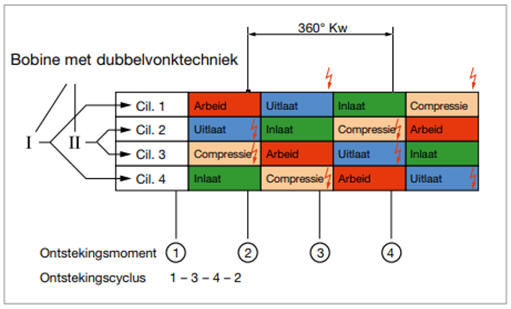
Tra la bobina A della bobina di accensione e il pin 7 del processore è mostrata una resistenza di 330 ohm. Questo resistore limita la corrente e la tensione di induzione dell'impulso pilota. Poiché questa resistenza non è standard sulla scheda MegaSquirt, deve essere adattata. A sinistra della linea tratteggiata verticale nell'immagine sottostante, viene mostrato il circuito interno del MegaSquirt. I componenti mostrati (le due resistenze da 330 Ohm e i LED) hanno dovuto essere successivamente saldati al circuito stampato.
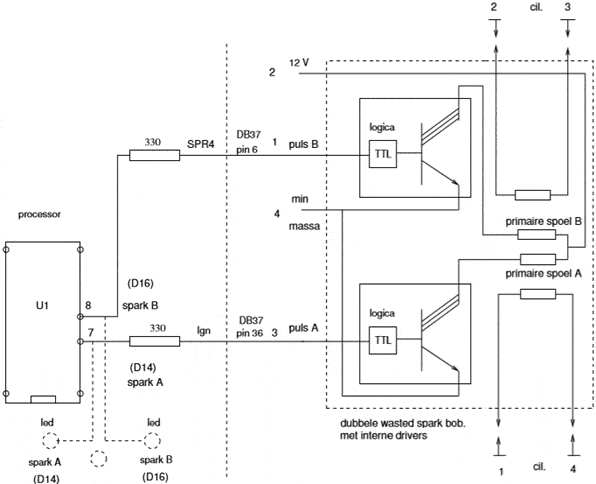
Accumulo di corrente nella bobina primaria:
È importante ottenere informazioni dettagliate sull'accumulo di corrente nella bobina primaria. In questo modo è possibile determinare non solo l'amperaggio, ma anche il tempo di ricarica della bobina di accensione. Il tempo di caricamento dipende da una serie di fattori di cui MegaSquirt deve tenere conto.
Il coefficiente di autoinduzione (valore L) della bobina di accensione selezionata è 3,7 mH. Insieme alla resistenza ohmica R vengono determinati la corrente primaria massima e il tempo di salita della curva. Un piccolo valore L e una resistenza assicurano che la corrente aumenti rapidamente dopo l'accensione. Utilizzando i dati noti della bobina di accensione è possibile calcolare come si forma la corrente primaria.
La seguente formula mostra la soluzione generale dell'equazione differenziale del 1° ordine, che calcola le correnti, i tempi di carica e scarica per rappresentare il fenomeno di commutazione come una curva.
L'equazione è:

dove la costante di tempo (Tau) si calcola come segue:

La corrente massima sarebbe di 28 A secondo la legge di Ohm:
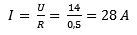
In realtà, questo amperaggio non verrà raggiunto.
La bobina si spegne prima. Il motivo viene spiegato più avanti. Inserendo queste informazioni nella formula generale si ottiene:
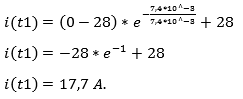
La figura mostra la curva di carica della bobina primaria. Dal tempo T0 a 1 Tau la bobina viene caricata al 63,2%. Si tratta di una percentuale fissa per il tempo di ricarica di una bobina. Il risultato della formula 13 mostra che la bobina è caricata con 1 ampere a 17,7 Tau. A t = 5 Tau il valore finale è praticamente raggiunto.
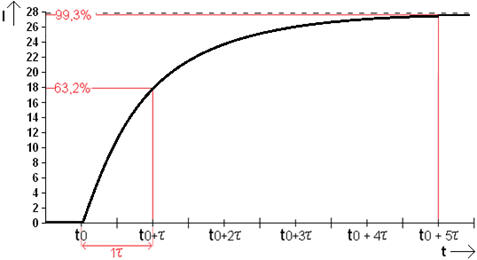
Secondo le specifiche della bobina di accensione, la corrente primaria della bobina di accensione dopo la ricarica è di 7,5 A. La corrente non aumenta. Il tempo necessario per raggiungere 7,5 A è chiamato tempo di permanenza. Il tempo di permanenza dipende dalla tensione della batteria, che in questo caso è di 14 volt. Se il processo di carica non viene regolato, la corrente attraverso la bobina è al massimo di 12 A secondo la formula 28.
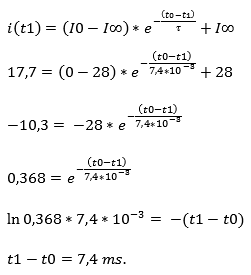
La bobina secondo la formula 14 viene caricata con 7,4 A con t = 17,7 ms. Il tempo di ricarica effettivo è più breve perché la bobina viene caricata fino a un massimo di 7,5 A. Il tempo richiesto può essere calcolato inserendo i dati noti nella formula 15.
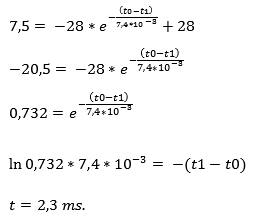
L'accumulo di corrente primaria viene interrotto a 7,5 A. Ciò impedisce che la bobina di accensione si riscaldi eccessivamente e inutilmente. La cosa più importante è che la bobina venga caricata in modo ottimale il più possibile nel più breve tempo possibile. La figura mostra la curva di carica fino a t = 2,3 ms.
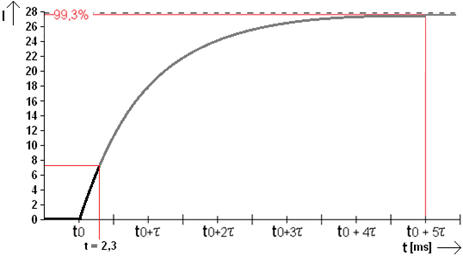
Quando la tensione della batteria diminuisce, ad esempio all'avvio del motore, ciò influisce sul tempo di permanenza. Sono quindi necessari più di 2,3 ms prima che vengano raggiunti i 7,5 A. Il nuovo tempo di caricamento viene determinato utilizzando la formula ormai nota. La corrente massima è determinata in base alla tensione della batteria:
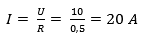
Il tempo di ricarica fino a 7,5 A con un massimo di 20 A si calcola nella formula 17:
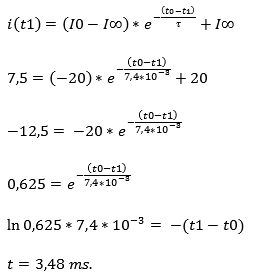
Nella figura il tempo di ricarica a 14 volt è indicato con la linea nera, mentre il tempo di ricarica a 10 volt è indicato con il verde. Le linee scendono contemporaneamente a 0; questo è il momento dell'accensione. Poiché una tensione della batteria inferiore richiede più tempo per caricare la bobina primaria, MegaSquirt deve attivare l'alimentazione primaria prima.
Le linee nere (in salita e in discesa) indicano il tempo di permanenza con una tensione della batteria di 14 volt. La linea verde indica il tempo di ricarica anticipato a una tensione inferiore: da questo si ottiene Δt. Il tempo di ricarica effettivo in questo caso è Δt + 100%.
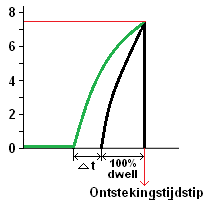
Ciò verrà chiarito più avanti in questa sezione con un esempio e la figura 36. Il tempo di ricarica viene prolungato e l'anticipo di accensione rimane lo stesso. Se ciò non avviene o non avviene in maniera sufficiente, ciò avrà conseguenze sull'energia rilasciata durante l'accensione. In questo caso la corrente primaria viene disinserita troppo presto e non viene raggiunta la corrente di 7,5 A. L'estensione del tempo di carica della bobina primaria (dwell time) è in formula funzione della tensione della batteria. Calcolando il tempo di permanenza a tensioni diverse si ottiene una corrente massima diversa nella bobina.
Supponendo che la tensione della batteria possa scendere a 6 Volt durante l'avviamento e salire a 14,7 Volt durante la carica, è possibile tracciare una curva calcolando una serie di valori intermedi. L'immagine seguente mostra la correzione del tempo di permanenza per la bobina di accensione DIS utilizzata. Nel grafico viene posizionato un punto (rosso) per ogni aumento di 2 volt. Poiché nel programma TunerStudio è stato inserito in precedenza un tempo di permanenza di 2,3 ms con una tensione di 14 volt, da questa tensione viene formato un fattore di correzione. Una tensione di 14 Volt corrisponde quindi al 100% (nessuna correzione).
Ora è stato chiarito che il tempo di ricarica aumenta fino al 315% con una tensione della batteria di 6 volt.
In condizioni sfavorevoli la tensione della batteria può scendere fino a 6 Volt. Ciò significa un indebolimento della scintilla di accensione. L'estensione del tempo di permanenza (il tempo durante il quale scorre la corrente primaria) compensa questo problema, in modo che anche a questa bassa tensione si ottenga sufficiente energia di accensione. Ciò significa che Δt della Figura 36 è triplicato (2,3 ms * 315% = 7,26 ms) rispetto al tempo di permanenza del 100% (2,3 ms) indicato in nero.
I coefficienti indicati in rosso nell'immagine sopra possono essere copiati direttamente nel programma TunerStudio.
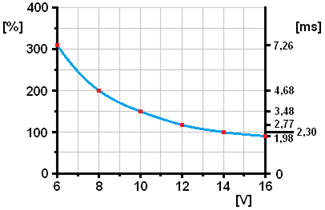
Qualche tempo dopo che la bobina primaria è stata scaricata, inizia la preparazione per l'accensione successiva. Maggiore è la velocità del motore, più velocemente la bobina verrà ricaricata. La Figura 37 mostra due curve in cui la corrente primaria aumenta a 8,85 A. Il momento dell'accensione è nel punto in cui la linea scende a 0 A.
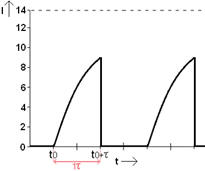
Determinazione dell'anticipo di accensione:
Il segnale di accensione viene determinato dal punto di riferimento dell'albero motore.
Nella corona dentata della puleggia dell'albero motore, 36 dente dei 1 denti è stato fresato a 100 gradi davanti al punto morto superiore del pistone del cilindro 1. Tra 100 e 0 gradi, quindi durante la corsa di compressione, il microprocessore di il MegaSquirt può determinare i tempi di accensione. . Ciò tiene conto dell'anticipo.
L'immagine mostra l'immagine dell'oscilloscopio a due canali in cui l'immagine superiore mostra il punto di riferimento dell'albero motore e l'immagine inferiore mostra il segnale di controllo dal MegaSquirt alla bobina di accensione DIS. Il segnale di controllo ha una tensione di 5 volt (un 1 logico) e dura circa 1,5 ms.
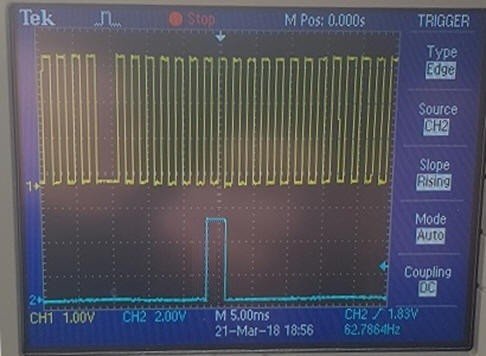
Anticipo accensione:
In questo progetto non vengono utilizzati sensori di detonazione. È possibile elaborare le informazioni dai sensori di battito, ma la semplice installazione di un sensore di battito non è sufficiente. L'elaborazione dei segnali è complessa. Il segnale di detonazione deve essere prima convertito in un segnale sì/no o in un segnale analogico che indichi la forza della detonazione.
La conversione delle vibrazioni del motore in un segnale di battito viene effettuata da un circuito di interfaccia. Questo circuito non è presente nel MegaSquirt II. Per questo motivo si è deciso di impostare in sicurezza l'avanzamento a pieno carico e quello a carico parziale, in modo che il motore non possa finire nella zona dei colpi. La curva di anticipo a pieno carico da impostare deve essere determinata entro i limiti di detonazione. I dati di anticipo centrifugo e depressione dell'accensione convenzionale sono determinati in base ai dati di fabbrica del manuale del motore. I punti possono essere tracciati su un grafico (esempio nell'immagine sotto).
La linea rosa indica l'avanzamento meccanico originale. Ciò è in parte lineare a causa della costruzione meccanica delle masse centrifughe. La linea nera mostra il controllo della mappa nel MegaSquirt; questa linea segue una curva. È importante restare fuori dalle zone soggette a collisioni a carico parziale e a pieno carico; quindi il controllo della mappatura è limitato a carico parziale (linea rossa) e l'anticipo a pieno carico non aumenta ulteriormente che nella situazione con anticipo meccanico (linea rossa). La disposizione effettiva della mappa segue la linea blu.
Per prima cosa è stato necessario inserire la curva di anticipo a pieno carico nella tabella dell'anticipo. A velocità più elevate e carichi inferiori sarà necessario un avanzamento maggiore. A carico parziale l'anticipo si somma all'anticipo a pieno carico. La tabella completa dell'anticipo di accensione e le impostazioni dell'anticipo a motore freddo sono riportate a pag. 7.
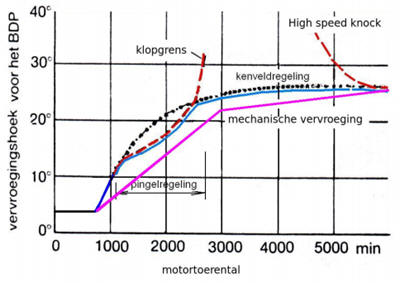
Corpo farfallato:
Nella condizione originale l'alimentazione aria/carburante era controllata dal carburatore. Nel sistema di gestione del motore il carburatore viene sostituito da un corpo farfallato e quattro iniettori montati nel collettore di aspirazione. Ciò garantisce un'iniezione più precisa e controllata rispetto al carburatore, dove al centro del collettore si forma una miscela aria/carburante suddivisa in quattro canali. L'apertura dell'acceleratore avviene tramite un cavo Bowden azionabile manualmente dal quadro strumenti.
Dopotutto, MegaSquirt II non supporta un corpo farfallato azionato elettronicamente. Ecco perché il comando tramite cavo Bowden è l'unica opzione da utilizzare.
La posizione dell'acceleratore viene trasmessa al MegaSquirt tramite una tensione. L'entità della tensione dipende dall'angolo di apertura della valvola a farfalla. Il sensore di posizione della valvola a farfalla è un potenziometro con una tensione di alimentazione di 5 volt (vedi immagine). Sono necessari il collegamento 3 e il collegamento a terra 1. Il corridore (perno 2) assume una posizione sulla resistenza che dipende dalla posizione dell'acceleratore. Il corridore è quindi collegato alla valvola a farfalla. Quando il corridore deve superare una piccola distanza oltre la resistenza (il corridore punta a sinistra), la resistenza è bassa. Nell'immagine il corridore è posizionato a destra (lato terra), il che significa che c'è un'alta resistenza e quindi una bassa tensione del segnale.
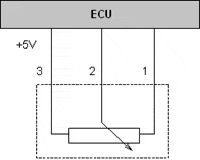
Con il corpo farfallato utilizzato, sulla guida è presente una tensione di 600mV quando la farfalla è chiusa e una tensione di 3,9V quando la valvola è completamente aperta. L'ECU riceve la tensione e la utilizza per calcolare l'angolo di apertura della valvola a farfalla. Un rapido aumento dell'angolo di apertura indica che è in corso un'accelerazione; l'ECU risponde arricchendosi brevemente. Questo si chiama arricchimento dell'accelerazione. Il sensore di posizione farfalla non viene utilizzato per determinare l'arricchimento della miscela nelle diverse condizioni di funzionamento; A questo scopo viene utilizzato il sensore MAP.
Configurazione di prova del motore passo-passo con simulatore:
Dopo la regolazione dell'hardware del MegaSquirt, è stato possibile utilizzare la breakout box per verificare se veniva ricevuto il controllo del motore passo-passo. L'accensione dei LED bicolore indica che è in corso il controllo. I passaggi in cui viene controllato il motore passo-passo possono essere seguiti osservando il cambiamento dei colori. I colori si alternano tra rosso e giallo. I dati del motore passo-passo possono essere inseriti nel menu "Controllo minimo" nel programma TunerStudio. Oltre alla tipologia (4 fili) è possibile impostare anche il numero di passi. Ciò include anche la posizione iniziale in cui deve trovarsi il motore passo-passo quando viene avviato. Inoltre, è possibile impostare il tempo necessario per regolare un passaggio.
Il numero di passi dipende, tra l'altro, dalla temperatura del liquido di raffreddamento; una temperatura più bassa richiede una maggiore apertura del motore passo-passo. I passi relativi alla temperatura possono essere impostati in un grafico. Il simulatore può essere utilizzato per verificare se il motore passo-passo è effettivamente controllato correttamente. Poiché viene controllato prima sul simulatore anziché sul motore, è possibile evitare problemi durante l'avvio o il funzionamento del motore a causa di un possibile problema hardware o software. Poiché la temperatura del liquido di raffreddamento e la velocità del motore influenzano principalmente l'angolo di apertura del motore passo-passo, è possibile verificare se il controllo è corretto ruotando questi potenziometri. Il misuratore sul dashboard di TunerStudio mostrerà la regolazione nel numero di passaggi regolati.
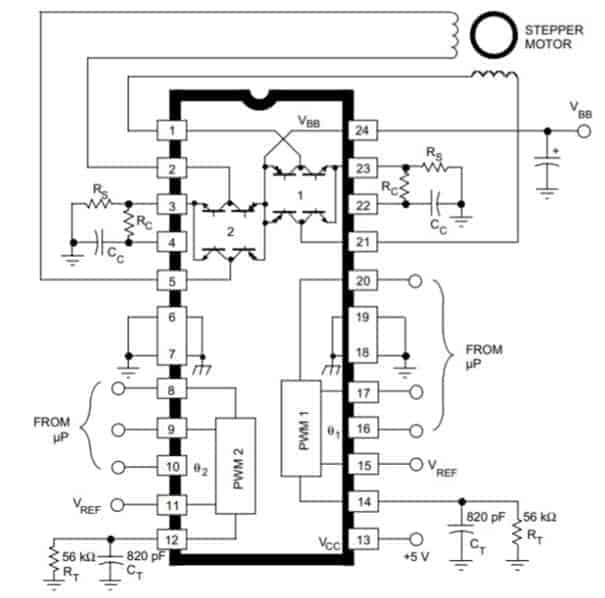
Impostazioni del motore passo-passo:
La figura mostra la schermata delle impostazioni per il motore passo-passo utilizzato per il minimo (controllo del minimo).
Le fasi di regolazione del motore vengono determinate in anticipo utilizzando un Arduino. È necessario inserire anche il numero di passi per raggiungere la posizione di base (passi di homing). Il motore passo-passo è attivo nella fase di riscaldamento (algoritmo) ed eccita le bobine quando è fermo (mantiene la corrente tra i passi).
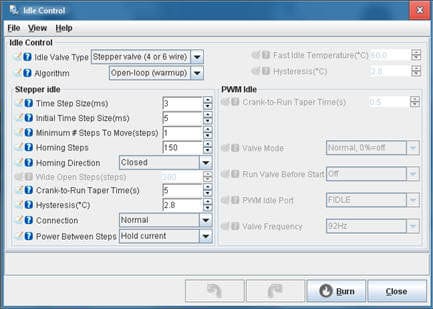
La posizione del motore passo-passo dipende dalla temperatura del liquido di raffreddamento. Quando si avvia un motore freddo, la valvola deve essere leggermente più aperta rispetto all'avvio di un motore caldo. L'immagine sotto mostra la schermata delle impostazioni per impostare i passaggi (Steps) in relazione alla temperatura del liquido refrigerante (Coolant). Quando il motore è freddo, il motore passo-passo è completamente aperto mentre il motore è al minimo. Durante la fase di riscaldamento il motore passo-passo si chiude leggermente.
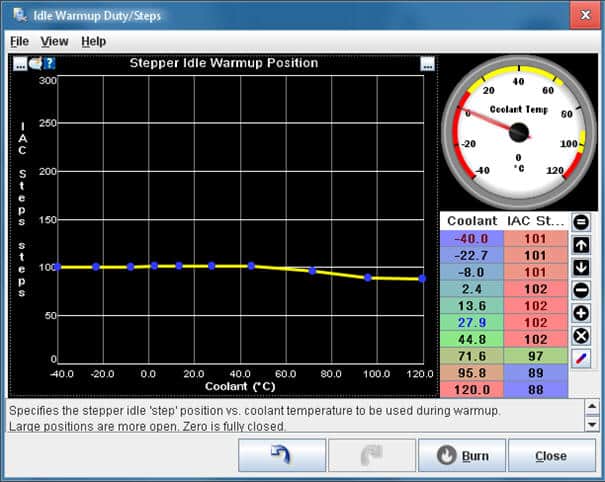
È anche possibile regolare la posizione del motore passo-passo in base alla temperatura del liquido di raffreddamento all'avvio del motore. Questo è chiamato “Idle Cranking Duty/Steps”. L'immagine sotto mostra la schermata delle impostazioni.
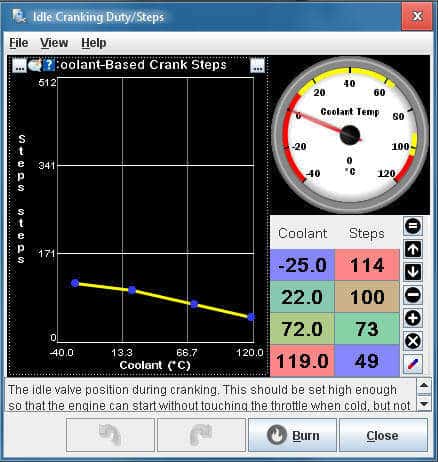
Circuito pompa carburante:
Il MegaSquirt assicura che la pompa del carburante sia accesa e spenta. Il transistor Q19 nella figura seguente protegge il transistor Q2 da una corrente eccessiva. Se la corrente è troppo elevata, il transistor può bruciarsi. Quando la corrente che attraversa la porzione collettore-emettitore di Q2 e R40 aumenta, viene raggiunta la tensione di saturazione alla base di Q19. Il transistor Q19 si accende, provocando una diminuzione della tensione dell'emettitore base su Q2.
La connessione FP-1 PTA0 è controllata internamente dal MegaSquirt. Per controllare il circuito a transistor è necessario un segnale di ingresso dal sensore di posizione dell'albero motore (un sensore Hall o un sensore induttivo). Se il segnale viene perso, ad esempio se il motore si spegne involontariamente, l'alimentazione elettrica alla pompa del carburante viene immediatamente interrotta.
L'uscita del circuito a transistor (FP1 OUT) è collegata al relè della pompa del carburante. Il pin 85 del relè è l'uscita della corrente di controllo. Con un relè eccitato, la sezione di alimentazione principale (pin 30 e 87) viene commutata, in modo che la pompa del carburante riceva una tensione di alimentazione per funzionare.
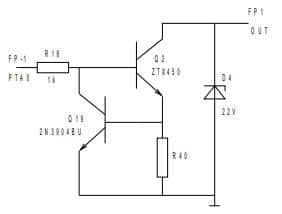
Viene utilizzata una pompa del carburante elettronica con una pressione di esercizio di 3 bar. Il carburante viene guidato attraverso il filtro del carburante fino al condotto del carburante, dove la pressione si trova all'ingresso degli iniettori. L'iniettore inietterà una quantità precalcolata di carburante nel collettore di aspirazione quando arriva un segnale dal MegaSquirt. Il controllo del MegaSquirt non determina solo la quantità di carburante iniettato, ma anche la pressione del carburante nel rail.
A una pressione del rail più elevata, con lo stesso controllo verrà iniettata una quantità maggiore di carburante. La pressione del rail deve quindi essere regolata in base alla pressione negativa nel collettore di aspirazione. La differenza di pressione (∆P) deve rimanere sempre pari a 3 bar. La figura mostra lo schema del sistema di alimentazione. Le linee rosa, gialle, arancioni e nere mostrano i collegamenti elettrici. La linea rossa indica l'alimentazione del carburante e la linea blu il ritorno del carburante.
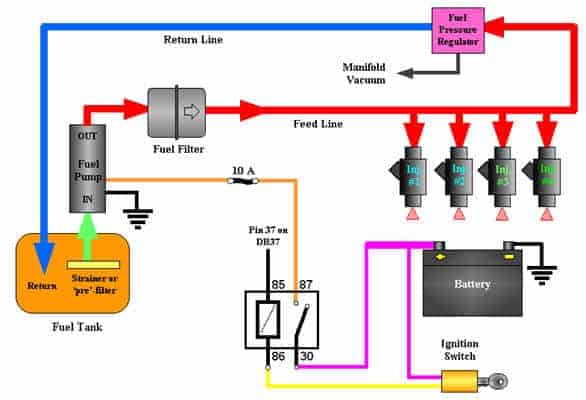
Completamento del lavoro meccanico:
Le tre foto successive mostrano il motore nelle fasi finali delle modifiche meccaniche.
Foto 1:
Questo è il lato in cui sono visibili la maggior parte delle parti applicate. Qui si trovano anche il cruscotto per i controlli e la ECU MegaSquirt. Sotto la foto c'è una legenda con la descrizione dei numeri delle parti. È possibile aprire le foto in dimensioni maggiori facendo clic su di esse.
- Valvola a farfalla;
- Linea carburante per gli iniettori;
- Tubo di collegamento per valvola a farfalla sul collettore di aspirazione;
- Manometro del carburante;
- Collettore di aspirazione e scarico;
- Cruscotto con interruttore ventola raffreddamento, spie alternatore e pressione olio, interruttore di accensione e sezionatore di terra;
- Tubo di aspirazione per sensore MAP;
- Sonda lambda;
- Tubi flessibili del carburante (mandata e ritorno) insieme in una scatola termoretraibile;
- Gruppo pompa/serbatoio carburante;
- Relè pompa carburante;
- MegaSquirt;
- Silenziatore di scarico.
Foto 2:
Questa foto mostra l'altro lato del motore. Qui potete vedere il carburatore (15) e l'accensione convenzionale (17). Lo scopo di questa accensione classica è quello di far accendere le candele nella configurazione di prova (14). Questo ovviamente non ha alcuna funzione per il motore, ma fornisce informazioni sul funzionamento dell'accensione come funzionava nelle auto d'epoca.
Il numero 20 indica il meccanismo del freno della trasmissione. L'asta del tamburo del freno può essere tesa mediante un cavo Bowden, in modo che l'albero di uscita del cambio venga frenato. Il freno della trasmissione viene applicato per caricare brevemente il motore quando viene inserita una marcia.
14. Configurazione di prova dell'accensione del distributore meccanico;
15. Carburatore;
16. Bobina di accensione DIS;
17. Accensione meccanica del distributore con anticipo a depressione;
18. Cruscotto posteriore;
19. Pompa meccanica del carburante;
20. Meccanismo del freno della trasmissione;
21. Bobina di accensione classica.
Foto 3:
Qui è chiaramente visibile la vista dall'alto del motore con la configurazione di prova per l'accensione e il condotto del carburante.
Le regolazioni meccaniche sono state completate. Il motore non può ancora essere avviato perché è necessario prima inserire alcuni dati nel MegaSquirt.
prossimo: Regolazione ECU MegaSquirt II.