Soggetti:
- Introduzione
- Sensore batteria intelligente
- Componenti e principi di misura del sensore batteria
- Ricarica e sostituzione della batteria
Introduzione:
Nei veicoli moderni lo stato di carica dell'alternatore viene adattato alle circostanze. L'alternatore è controllato dalla ECU del motore e riceve segnali per caricare più o meno. L'alternatore genera energia poiché viene creato un campo magnetico tra il rotore e lo statore. Maggiore è il campo magnetico, maggiore è la forza necessaria per far girare il rotore. Generare una grande quantità di corrente di carica costa quindi energia e carburante.
- Il regime del minimo può essere aumentato quando la batteria è quasi scarica quando non è possibile effettuare una ricarica sufficiente;
- Durante la massima accelerazione, l'alternatore viene temporaneamente non controllato per utilizzare tutta la coppia generata per la propulsione;
- Durante la decelerazione (freno motore), l'ECU controlla l'alternatore al massimo effetto, in modo che l'energia cinetica del veicolo venga utilizzata per generare energia nell'alternatore. In figura è riportata l'indicazione della carica massima della batteria (sistema a 12 volt).
Il segnale del sensore intelligente della batteria viene utilizzato per determinare lo stato di carica della batteria. Questo è uno dei dati più importanti per determinare in che misura l'alternatore deve essere controllato.
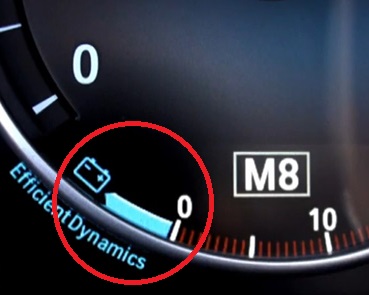
Sensore batteria intelligente:
I veicoli moderni sono quasi tutti dotati di un sensore della batteria, spesso noto come IBS (sensore intelligente della batteria), sensore di corrente o monitor della batteria. In questo articolo faremo riferimento al termine “sensore batteria”. Il sensore della batteria funziona in stretta collaborazione con il sistema di monitoraggio della batteria (BMS) nel veicolo. Ciò è particolarmente vero per i veicoli dotati di sistema di avvio e arresto. In questi veicoli la batteria viene sottoposta ripetutamente a forti sollecitazioni poiché il motorino di avviamento viene attivato più volte durante ogni viaggio per avviare il motore. Questo è il motivo per cui in tali veicoli spesso viene scelta una batteria AGM invece di una tradizionale cella al piombo. Una batteria AGM è più resistente alle scariche e alle ricariche ripetute.
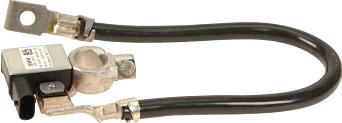
Il sensore della batteria è integrato nel cavo di massa, che è collegato tra il terminale negativo della batteria e un punto di massa sulla carrozzeria o sul telaio. Sul sensore della batteria troverai una spina con due o più fili. Un filo porta direttamente al terminale positivo della batteria e un secondo filo serve per la comunicazione.
All'interno dell'alloggiamento del sensore della batteria è presente un circuito con un microprocessore e un controller che misura tensione, corrente, temperatura e tempo. I dati di questa unità di controllo elettronico (ECU) vengono spesso trasmessi tramite un bus LIN all'alternatore e all'unità di controllo comfort (BCM) o alla centralina del motore. Il gateway si trova spesso tra il sensore della batteria e la BCM o la centralina del motore per tradurre il messaggio del bus LIN in un messaggio del bus CAN. Questo verrà discusso più approfonditamente nella sezione “diagnosi del sensore batteria intelligente”.
Il sensore della batteria monitora le condizioni della batteria e misura i seguenti parametri:
- La tensione della batteria.
- La corrente con cui la batteria viene caricata e scaricata.
- La temperatura della batteria.
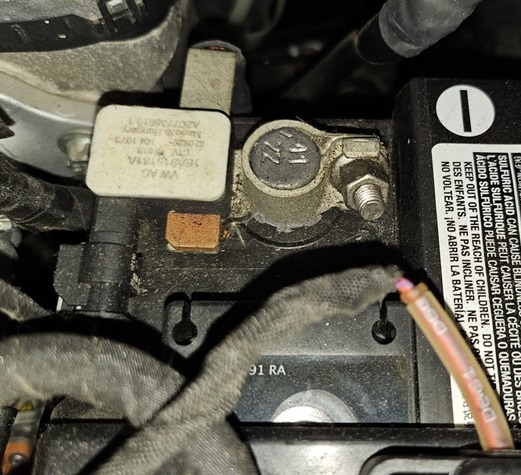
Il sensore della batteria invia questi dati alla centralina del motore o al BCM. Utilizzando questi dati, l'ECU (unità di controllo elettronico) calcola quanto segue:
Stato di carica (SOC) della batteria. Misurando la corrente in uscita verso le utenze e la corrente in entrata nella batteria, è possibile determinare quanta energia è ancora disponibile nella batteria.
Condizione (State Of Health, SOH) della batteria. La tensione della batteria e la corrente di scarica vengono confrontate per valutare la qualità della batteria. Durante l'avviamento è possibile prelevare dalla batteria fino a 60 A di corrente con un piccolo motore a benzina o fino a 120 A con un motore diesel più pesante. La misura in cui la tensione della batteria diminuisce indica il livello di resistenza interna della batteria. Se con una corrente di 11,5 A la tensione scende da 10 a 60 volt, ciò è accettabile. Se la tensione scende da 11,5 a 8 volt con la stessa corrente di avviamento, ciò indica una resistenza interna troppo elevata nella batteria e richiede la sostituzione.
Corrente di riposo durante l'arresto. Questo rileva un disturbo della corrente di riposo, ad esempio da parte di un utente non autorizzato. Il conducente riceverà una notifica durante il viaggio successivo se viene rilevato un aumento della corrente di riposo.
Componenti e principi di misurazione del sensore batteria:
L'alloggiamento del sensore della batteria e il terminale di terra sono spesso integrati in un unico pezzo. Il cavo di massa può anche formare un tutt'uno con il sensore della batteria o essere fissato con un collegamento a vite. All'interno del sensore della batteria è presente un resistore di shunt con un valore di resistenza molto basso. Misurando la differenza di tensione attraverso questo shunt, è possibile calcolare la corrente. In combinazione con la tensione della batteria è possibile calcolare la potenza con cui la batteria viene caricata o scaricata.
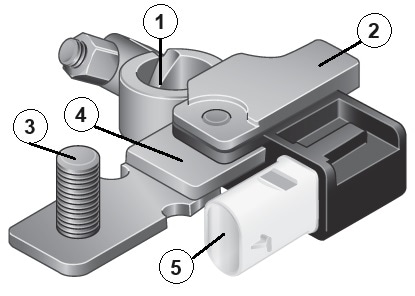
1. Polo di terra con morsetto per palo;
2. Sensore batteria;
3. Collegamento a massa del veicolo;
4.Shunt;
5. Collegamento a spina per bus B+ e LIN.
La resistenza di shunt è posta in serie tra la connessione di terra del veicolo e il terminale negativo della batteria. Tutta la corrente da e verso la batteria passa attraverso questo shunt. A causa del basso valore di resistenza, nello shunt viene consumata poca tensione.
Il livello di questa tensione viene convertito in corrente nel microprocessore, insieme al valore noto di resistenza dello shunt:
- Una grande caduta di tensione attraverso lo shunt indica una grande corrente.
- Una bassa caduta di tensione indica una corrente bassa.
Nell'immagine allegata vediamo uno schema in cui il resistore R rappresenta lo shunt e la corrente I rappresenta la corrente di scarica durante la scarica della batteria. Il voltmetro, posizionato in parallelo sul resistore di shunt, illustra come l'elettronica di misurazione nel sensore della batteria misura la differenza di tensione attraverso questo shunt.
L'immagine seguente fornisce una panoramica dei luoghi in cui vengono effettuate le misurazioni di temperatura, tensione e corrente.
La resistenza dello shunt è indicata dal numero 5. La differenza di tensione (V) attraverso lo shunt viene letta come corrente (A). Questi dati vengono inviati tramite il bus LIN al DME/DDE, che sono le denominazioni del motore a benzina (DME) e del motore diesel (DDE) della BMW.
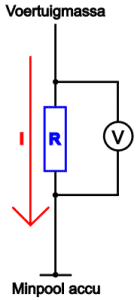
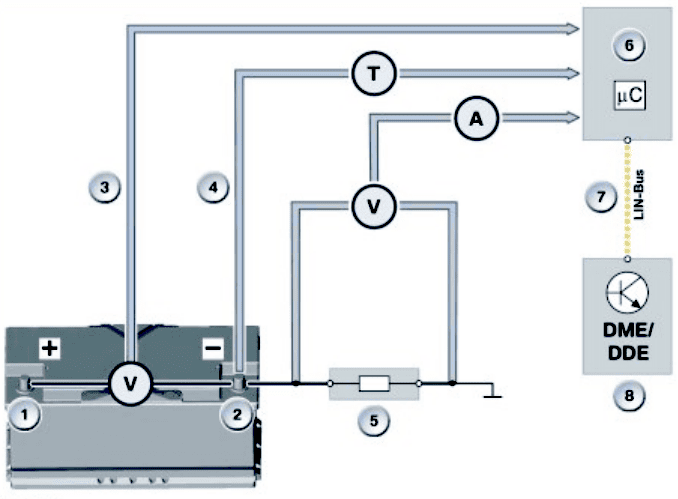
1. Polo positivo della batteria;
2. Terminale di terra della batteria;
3. Misurazione della tensione della batteria;
4. Misurazione della temperatura della batteria;
5. Misura della corrente mediante resistore shunt;
6. Microprocessore nel sensore intelligente della batteria;
7. Cavo di comunicazione del bus LIN
8. Centralina motore
Caricare e sostituire la batteria:
Il sistema di gestione della batteria utilizza il sensore della batteria per misurare la corrente che fluisce da e verso la batteria e archivia queste informazioni in memoria. Quando è necessario caricare la batteria o se viene utilizzato un ausilio all'avviamento, è importante che il caricabatteria non sia collegato direttamente ai terminali della batteria, ma ai punti di ricarica. Il sensore della batteria si trova tra questi punti di ricarica e i terminali della batteria e può misurare il flusso di energia solo quando il caricabatterie è collegato ai punti di ricarica. Se il caricabatteria viene collegato direttamente ai terminali della batteria, la memoria BMS indicherà che la batteria è (quasi) scarica, mentre in realtà è completamente carica. L'alternatore sovraccaricherà quindi la batteria, dopodiché il sistema non funzionerà correttamente. Le immagini sottostanti mostrano un caricabatteria collegato direttamente alla batteria e ai punti di ricarica sotto il cofano.
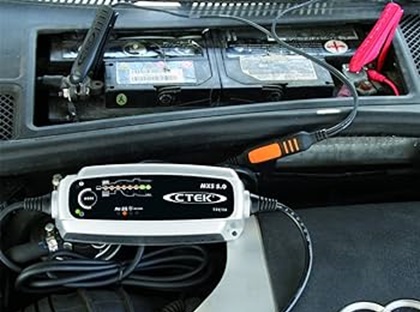
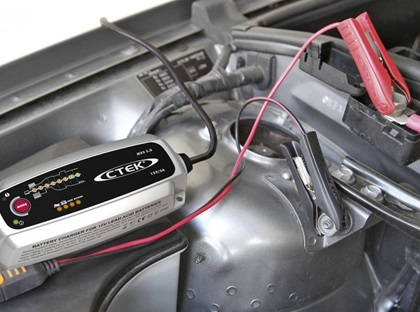
Dopo aver sostituito la batteria, è necessario registrare la batteria su un veicolo dotato di sensore batteria. In officina viene chiamato anche “apprendimento” o “codificazione”. La gestione della batteria tiene conto di:
- invecchiamento della batteria. È possibile aumentare la corrente di carica di una batteria più vecchia con una maggiore resistenza interna;
- la capacità e la corrente di avviamento a freddo della batteria.
Durante la registrazione vengono cancellati i valori memorizzati della batteria che si sono deteriorati nel tempo. Quindi, anche se viene installata una batteria identica della stessa marca e con la stessa capacità e corrente di avviamento a freddo, la sostituzione deve essere registrata. Naturalmente è necessario rendere noti i dati di una batteria con caratteristiche diverse. Ciò può essere fatto inserendo manualmente la capacità [Ah] e la corrente di avviamento a freddo [A] oppure inserendo i codici prodotto o i numeri di serie. Con le moderne apparecchiature diagnostiche è possibile scansionare il codice QR riportato sull'adesivo della batteria.
Le schermate seguenti mostrano la registrazione di una batteria con un programma BMW (a sinistra) e VCDS (a destra).
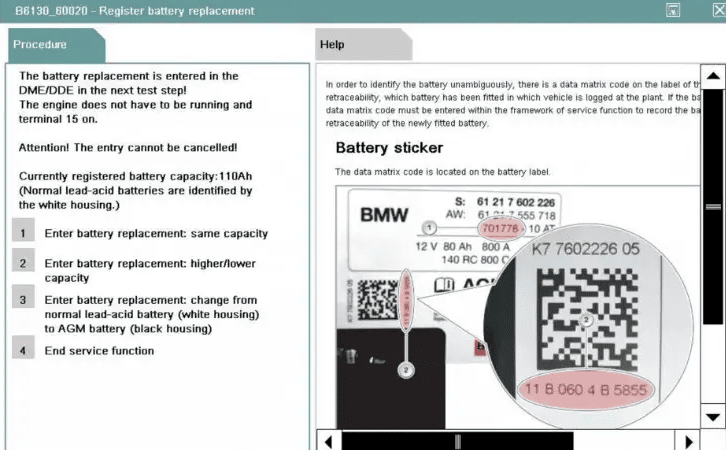
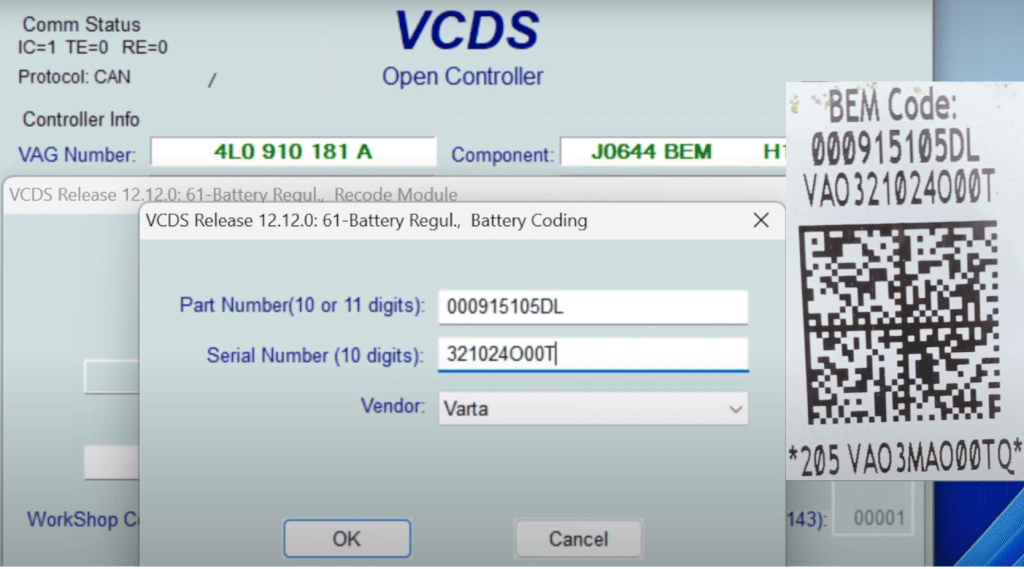
Diagnosi sul sensore batteria intelligente:
Il sensore intelligente della batteria comunica con l'alternatore e la BCM o la centralina del motore. Questa sezione spiega come leggere il diagramma e come effettuare una diagnosi.
Nello schema seguente vediamo il sensore batteria (A85) che viene alimentato con una tensione di alimentazione di 2 volt tramite un fusibile sul pin 12. Il pin 1 è di comunicazione: da qui viene inviato un messaggio tramite bus LIN al gateway (A25di) e all'alternatore (O01). I pin 1 e 2 si trovano nella spina bipolare visibile nelle immagini precedenti.
I due fili neri inferiori sul sensore della batteria non hanno un numero di pin: si tratta di un collegamento diretto al terminale negativo della batteria.
Il sensore batteria intelligente invia un messaggio bus LIN al gateway e all'alternatore. Il gateway è la giunzione tra reti con protocolli diversi (tensioni e velocità). Nel gateway il messaggio del bus LIN viene inviato tramite bus CAN al BCM e/o alla centralina del motore. Viceversa, uno di questi due dispositivi di controllo controlla l'alternatore tramite il gateway e il bus LIN.
Un guasto nella comunicazione del bus LIN può significare che i dati del sensore della batteria non possono essere utilizzati o che l'alternatore non viene controllato correttamente. In quest'ultimo caso, l'alternatore passa a un programma di emergenza in cui viene utilizzato il convenzionale controllo D+ per creare una tensione di carica e una corrente di carica sufficienti.
Il corso di tensione del Segnale del bus LIN può con uno oscilloscopio vengono misurati per la valutazione.
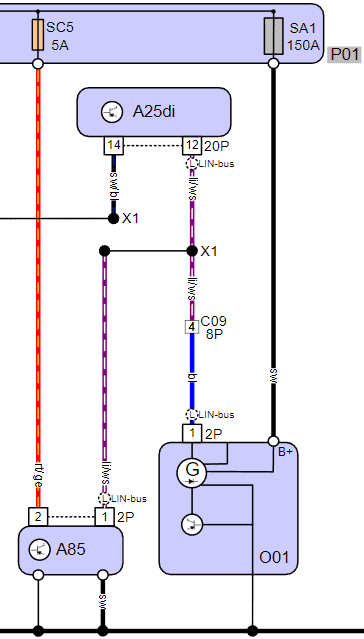
Legenda:
P01: scatola fusibili vano motore
A25di: interfaccia diagnostica (gateway)
A85: Sensore batteria ECU
O01: dinamo
Quando c'è un guasto e la comunicazione del bus LIN è corretta, sappiamo che la tensione di alimentazione e la terra del sensore sono buone. Il guasto è causato da uno dei componenti di questo schema. È possibile eseguire i seguenti passaggi:
- verificare la presenza di aggiornamenti software dei dispositivi di controllo;
- Testare la batteria da 12 volt (preferibilmente sotto carico);
- verificare se sono stati registrati i dati corretti della batteria. La batteria potrebbe essere stata sostituita in passato, ma la registrazione non è mai stata effettuata;
- reimpostare i dati del sensore della batteria;
- verificare che il codice articolo dell'alternatore sia corretto: un alternatore errato che non corrisponde al sensore prima o poi causerà problemi;
- Se quanto sopra è stato controllato e ritenuto corretto, è possibile concludere che il sensore della batteria è difettoso. Questo a volte si verifica con avviamenti frequenti (errati) tramite cavi jumper o un booster batteria.
Pagine correlate: