Soggetti:
- Iniezione indiretta e diretta
- Controllo della pressione del carburante con iniezione indiretta
- Strategia di iniezione iniezione multipoint
- Iniettore elettromagnetico (MPI)
- Iniettore piezoelettrico (DI)
- Strategie di iniezione iniezione diretta
- Doppia iniezione
- Misurazione delle caratteristiche di tensione e corrente su un iniettore multipunto
- Fasatura dell'iniezione in relazione alla posizione dell'albero motore
- Limitazione corrente dell'ECU
- Determinazione della quantità richiesta di carburante
- Tavolo VE
- Tabella AFR
Iniezione indiretta e diretta:
I tipi di sistemi di iniezione di un motore a benzina si dividono in iniezione indiretta per la valvola a farfalla, iniezione indiretta per cilindro e iniezione diretta ad alta pressione. I paragrafi di questa pagina spiegano questi diversi sistemi di iniezione.
Iniezione indiretta:
C'è un iniettore davanti alla valvola a farfalla. Il carburante viene spruzzato contro la valvola a farfalla, dove si mescola con l'aria che scorre. Lo svantaggio principale è che non esiste un dosaggio accurato del carburante per cilindro; un cilindro ottiene sempre un po' più o meno dell'altro. Il sistema quindi non è regolabile e quindi non viene più utilizzato per quanto riguarda i requisiti ambientali. Questo sistema è anche chiamato iniezione centrale (Monopoint).
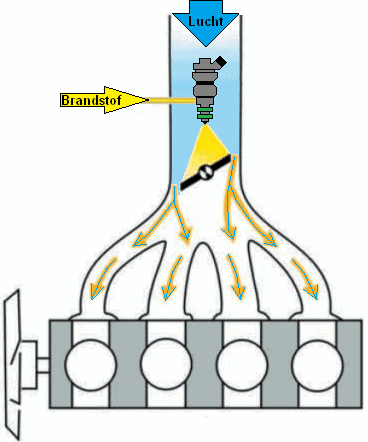
Iniezione indiretta:
Ogni cilindro ha il proprio iniettore. L'iniettore inietta il carburante nella valvola di aspirazione. Il flusso d'aria garantisce anche la miscelazione in questo sistema prima che la miscela aria-carburante entri nella camera di combustione. Il vantaggio rispetto all'iniezione indiretta è che la quantità di carburante può essere controllata in modo molto più accurato. Questo sistema è anche chiamato MPI (MultiPoint Injection) o PFI (Port Fuel Injection).
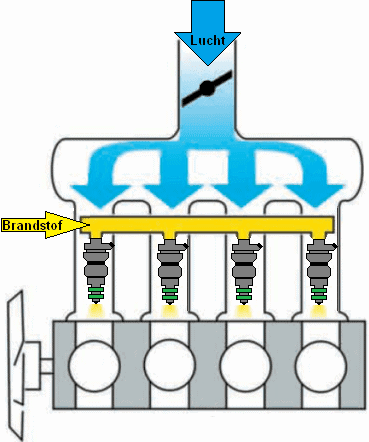
Iniezione diretta:
Gli iniettori per DI (Direct Injection) o DISI (Direct Injection Spark Ignition) si trovano accanto alla candela, nella parte superiore della camera di combustione. Il carburante viene iniettato attraverso questo iniettore ad un'alta pressione di circa 200 bar durante la fase di aspirazione. I principali vantaggi di questo sistema sono che la quantità di carburante può essere regolata in modo ancora più preciso, che le iniezioni possono essere effettuate più volte durante la fase di aspirazione e che la miscela aria-carburante è più fresca. Ciò consente ai produttori di aumentare il rapporto di compressione del motore. L'iniettore può essere progettato come iniettore piezoelettrico o a bobina magnetica.
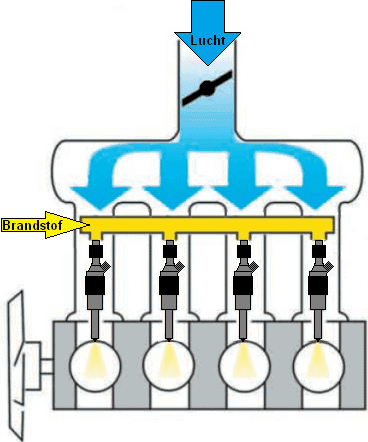
DI richiede pressioni di iniezione più elevate rispetto a MPI/PFI, perché l'iniezione avviene durante la corsa di compressione; il carburante deve essere sufficientemente nebulizzato mentre l'aria nel cilindro viene compressa. Ecco perché DI dispone di una pompa ad alta pressione separata. La pompa ad alta pressione aumenta la pressione del carburante nel condotto del carburante. Gli iniettori sono collegati a questo condotto del carburante tramite tubi. Non appena la gestione del motore invia un segnale all'iniettore, questo si aprirà e si chiuderà all'ora desiderata.
I vantaggi del DI rispetto al PFI includono:
- Iniezione più accurata;
- Possibili iniezioni multiple;
- Il tempo di iniezione può essere regolato;
- È possibile una pressione effettiva più elevata sopra il pistone (consentendo così il ridimensionamento con un rapporto di compressione più elevato);
- Minori consumi di carburante, minori emissioni di CO2.
Gli svantaggi includono:
- Costi di sistema più elevati dovuti a una pompa del carburante ad alta pressione, iniettori avanzati, testata più complessa;
- Aumento delle emissioni di fuliggine (emissioni di PM);
- L'iniezione diretta nella camera di combustione fornisce il raffreddamento invece del calore necessario per l'evaporazione del carburante.
Un motore a doppia iniezione sfrutta i vantaggi di entrambi i sistemi. L'iniezione diretta e indiretta può essere commutata a seconda delle condizioni operative. Il funzionamento e l'applicazione della doppia iniezione è descritto nel paragrafo omonimo di questa pagina.
Controllo pressione carburante con iniezione indiretta:
Una pressione costante del carburante è un prerequisito per un controllo accurato dell'iniezione di carburante. La pressione del carburante (pressione rail) si trova nella parte superiore dell'iniettore e la pressione del collettore di aspirazione è nella parte inferiore. La pressione nel collettore di aspirazione varia al variare del carico del motore e, senza regolatore di pressione, influenza la differenza di pressione del carburante e quindi la quantità di iniezione. Per questo motivo utilizziamo un regolatore di pressione del carburante. In questa sezione approfondiremo il funzionamento e lo scopo di questo controller.
L'immagine sotto mostra i componenti di un motore a benzina ad iniezione indiretta con iniezione multipoint. Osserviamo il flusso di carburante dalla pompa nel serbatoio all'iniettore.
Quando l'ECU controlla il relè della pompa del carburante, la pompa funziona. La pompa aspira il carburante dalla parte più bassa possibile del serbatoio e forza il flusso di carburante verso il filtro del carburante. Le particelle di sporco nel carburante rimangono nel materiale del filtro. Il carburante filtrato arriva quindi al condotto del carburante. Nella maggior parte dei casi il condotto del carburante è montato direttamente sull'ingresso dell'iniettore.
C'è una pressione costante nel condotto del carburante: solo quando l'iniettore è controllato elettricamente dalla ECU (vedi filo blu) l'iniettore si apre e il carburante viene iniettato nel collettore di aspirazione sulla valvola di aspirazione aperta. La quantità di carburante iniettato dipende da:
- il tempo di iniezione (determinato dalla ECU allungando o accorciando il segnale di iniezione);
- la pressione del carburante (con un tempo di iniezione di 2 millisecondi, l'iniettore inietterà più di quanto calcolato dalla ECU se la pressione del carburante è troppo alta).
La pressione del carburante nel condotto del carburante (detta anche pressione del rail) viene regolata in base al carico del motore. Ne discuteremo più dettagliatamente nella sezione successiva.
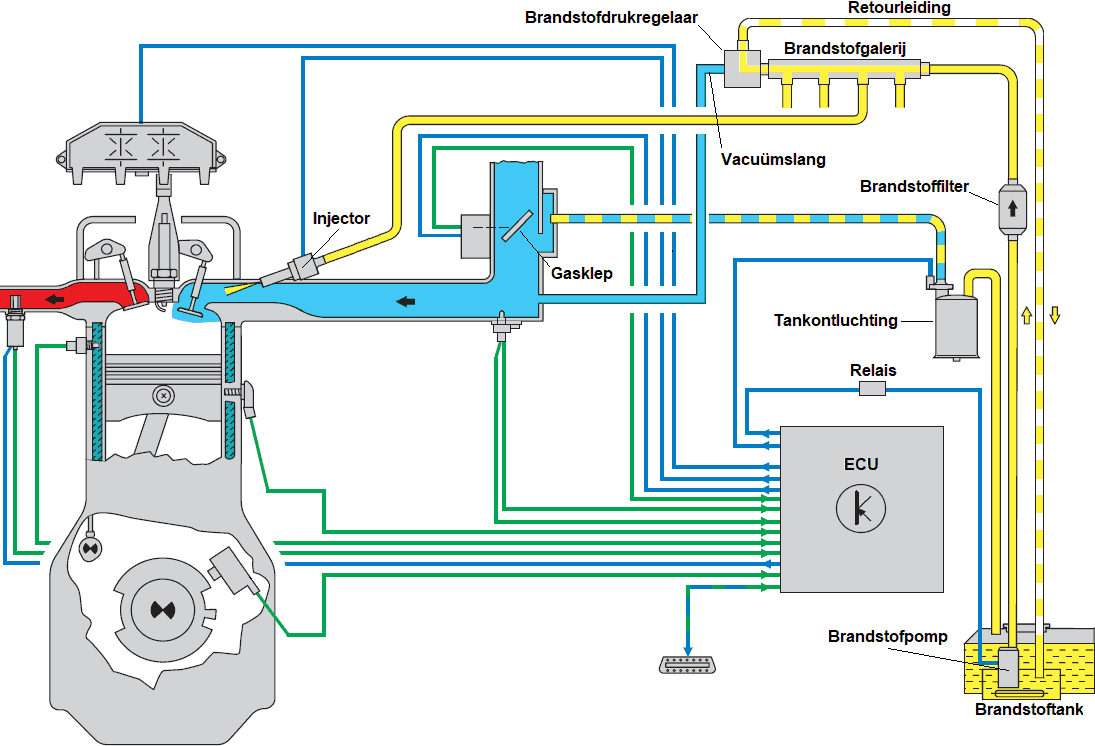
Senza l'utilizzo di un regolatore di pressione si verificano le seguenti situazioni:
- Al minimo, il vuoto più elevato (cioè la bassa pressione dell'aria) nel collettore di aspirazione produrrebbe una pressione del carburante indesiderabilmente più elevata;
- Durante l'accelerazione la depressione (a pieno carico) è minore o addirittura assente e la pressione del carburante diminuirebbe, mentre sarebbe auspicabile una pressione del carburante più elevata.
Il regolatore della pressione del carburante aumenta o diminuisce la pressione della benzina nel condotto del carburante in base alla pressione dell'aria nel collettore di aspirazione. Possiamo considerare il regolatore di pressione del carburante come una valvola dinamica, che consente un'apertura tra la linea di alimentazione dalla pompa del carburante e la linea di ritorno.
A destra vediamo un diagramma della pressione del carburante dove la differenza di pressione relativa in tutte le condizioni (minimo, carico parziale e pieno carico) è di 4 bar grazie al regolatore di pressione.
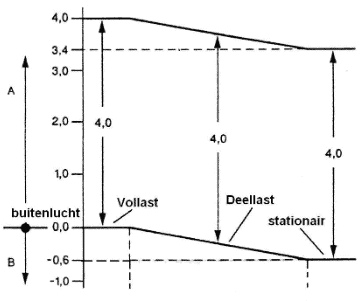
La spiegazione seguente si riferisce alle immagini che mostrano il regolatore di pressione nella situazione senza e con vuoto. A destra c'è un regolatore di pressione del carburante Bosch, utilizzato da diversi produttori di automobili.
Senza vuoto (a sinistra):
Il regolatore di pressione è chiuso a riposo: la molla preme la membrana in chiusura, impedendo al carburante alimentato di raggiungere la linea di ritorno.
Con vuoto (al centro):
Quando la pressione sopra la membrana viene ridotta, la pressione del carburante sul lato di alimentazione spinge la membrana verso l'alto contrastando la forza della molla. Viene creata un'apertura attraverso la quale il carburante fornito viene scaricato attraverso la linea di ritorno al serbatoio del carburante.
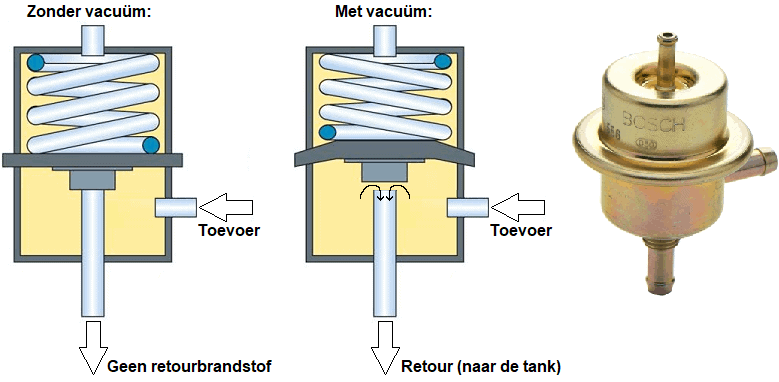
Strategia di iniezione iniezione multipoint:
Con l'iniezione multipoint (indiretta) vengono utilizzati tre diversi metodi di iniezione:
- Simultanea: l'iniezione avviene contemporaneamente su tutti i cilindri.
- Gruppo: l'iniezione avviene per gruppo; c'è una distinzione tra uno o più gruppi.
- Sequenziale: ogni iniettore è controllato separatamente e quindi ha il proprio momento di iniezione.
Il sistema di gestione del motore nella figura seguente illustra un'iniezione di gruppo. Gli iniettori dei cilindri 1 e 2 hanno un'alimentazione comune (rosso) e sono entrambi collegati a massa contemporaneamente (verde). Gli iniettori dei cilindri 3 e 4 sono uguali, ma vengono comandati separatamente dai cilindri 1 e 2.
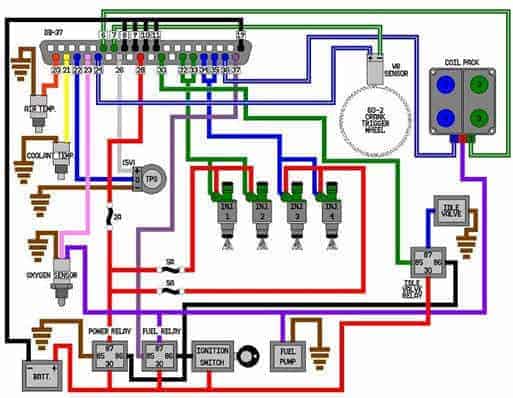
Iniettore elettromagnetico (MPI):
L'iniettore elettromagnetico viene utilizzato su molti motori a benzina che non utilizzano l'iniezione (diretta) ad alta pressione con una pompa ad alta pressione separata. All'ingresso dell'iniettore il carburante si trova ad una pressione costante di 1 bar. La pressione del carburante è fornita dalla pompa del carburante nel serbatoio. Con l'iniezione multipoint (descritta più avanti nella pagina), ogni cilindro ha il proprio iniettore. Questo iniettore è montato nel collettore di aspirazione e inietta il carburante con una pressione fino a 6 bar prima dell'apertura della valvola. Il carburante ha poi tempo sufficiente, quando la valvola di aspirazione inizia ad aprirsi, per mescolarsi con tutto l'ossigeno (indicato in figura dalla freccia blu scuro) che affluisce nel cilindro.
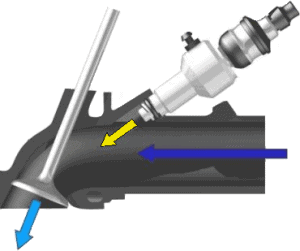
La centralina del motore controlla la posizione dell'albero motore per regolare i tempi di iniezione e di accensione. In base a diversi fattori (temperatura del motore e dell'ambiente, carico, velocità, ecc., darà un segnale all'iniettore al momento giusto per aprirsi. La spina di questo iniettore contiene due fili. Un filo ha un positivo costante di circa 14 volt. L'altro filo è collegato a massa dall'ECU per consentire alla corrente di fluire attraverso la bobina dell'iniettore. Quando la bobina è sufficientemente carica, lo spillo dell'iniettore si apre contro la forza della molla. Quando il controllo si ferma, una molla comprime indietro lo spillo dell'iniettore . L'alimentazione del carburante viene quindi interrotta. Quando il controllo si ferma, la bobina è ancora carica elettricamente. L'energia nella bobina forma un picco di induzione, che può essere osservato sull'oscilloscopio. La tensione di induzione è per breve tempo intorno a 60 volt.
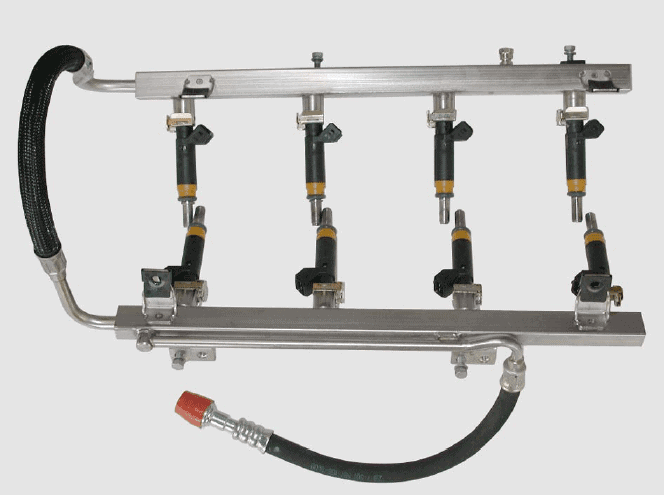
Questi iniettori vengono alimentati con il carburante dal condotto del carburante (chiamato anche condotto del carburante). La pompa di sovralimentazione nel serbatoio del carburante fornisce la pressione nel condotto del carburante. La pressione del carburante nel rail è costante (ca. 4 bar). Poiché la pressione è così bassa, gli iniettori sono fissati con una clip di bloccaggio e un O-ring per sigillarli. Soprattutto nelle auto più vecchie in cui il sistema viene smontato, è consigliabile sostituire gli O-ring prima dell'installazione.
L'alloggiamento di un iniettore è solitamente in plastica. Nella parte superiore della custodia troviamo la connessione a spina, che è collegata internamente alla bobina. Nella parte superiore è presente un O-ring di gomma sul quale scorre il condotto del carburante. Nella parte inferiore si trovano gli O-ring o gli anelli di tenuta in Teflon. Un O-ring viene utilizzato principalmente negli iniettori MPI con iniezione a bassa pressione, mentre gli anelli in teflon si trovano nei motori con iniezione ad alta pressione, come un motore FSI.
La bobina è avvolta attorno al nucleo dell'iniettore. Nell'immagine allegata la bobina è evidenziata in rosso. Al centro dell'iniettore, anch'esso interno alla bobina, è presente uno stantuffo. Questo stantuffo ha un accoppiamento meccanico con l'ago. Sopra lo stantuffo c'è una molla che mantiene lo stantuffo e quindi l'ago nella sua sede, chiudendo l'apertura di iniezione.
A riposo, la tensione su entrambi i terminali della bobina è di circa 14 volt rispetto a terra. Per adescare l'iniettore, la ECU del motore fornisce massa a un lato della bobina, mentre l'altro lato riceve tensione positiva. A quel punto la corrente comincia a fluire attraverso la bobina, determinando la formazione di un campo magnetico. Questo campo magnetico tira verso l'alto lo stantuffo e quindi l'ago per l'iniezione.
Quando è necessario interrompere l'iniezione, la ECU scollega la massa, facendo scomparire il campo magnetico. La molla spinge indietro lo stantuffo, facendo sì che l'ago interrompa l'alimentazione del carburante alla camera di combustione.
L'iniettore di solito ha più aperture. Queste aperture sono molto piccole, in modo che il carburante venga iniettato dall'iniettore nella camera di combustione sotto forma di nebbia. Quanto più fine è la nebbia, tanto più facile evapora.
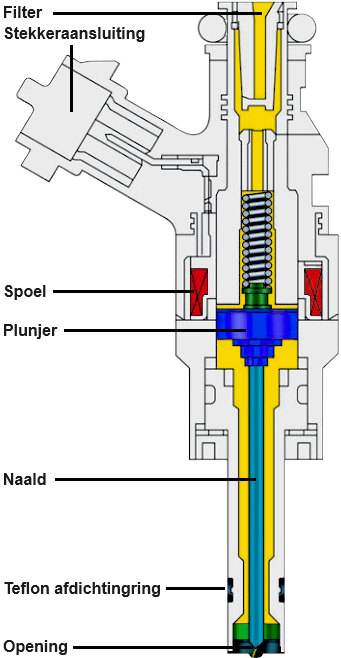
Iniettore piezoelettrico (DI):
Gli iniettori piezoelettrici possono essere utilizzati sia nei motori a benzina che diesel. BMW è stato il primo marchio a utilizzare la tecnologia piezoelettrica nei motori a benzina, ma ha smesso di farlo con i motori più recenti.
Un iniettore piezoelettrico fa parte dell'iniezione ad alta pressione. Una pompa ad alta pressione separata fornisce pressione sulla rotaia del carburante. Questo condotto del carburante distribuisce il carburante a tutti gli iniettori (vedi immagine). A causa delle pressioni molto elevate vengono utilizzati tubi in alluminio con pressacavi. I premistoppa (che sono avvitati sul tubo e sugli iniettori) devono essere sempre serrati con la forza corretta. Ciò è indicato nel manuale di riparazione del motore in questione.
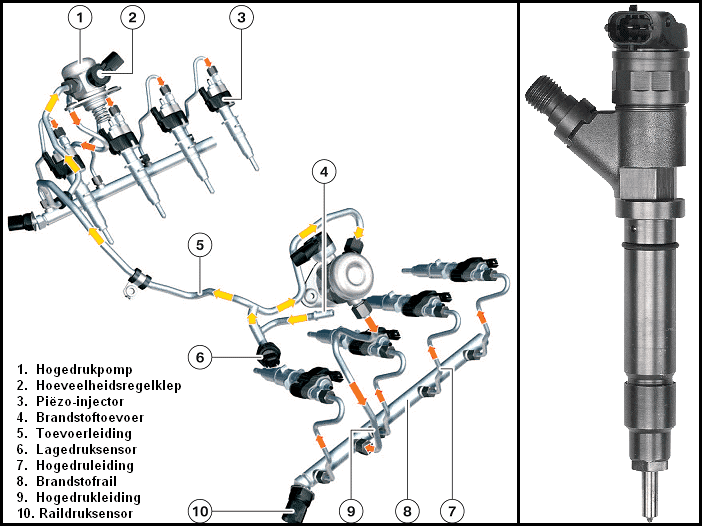
L'elemento piezoelettrico nell'iniettore ha la proprietà di cambiare lunghezza quando ad esso viene collegata una tensione positiva o negativa. Questo viene utilizzato con l'iniettore. Non appena la centralina del motore fornisce una tensione di comando compresa tra circa 100 e 150 Volt, l'elemento piezoelettrico si espande di circa 0,03 mm. Questa variazione di lunghezza è sufficiente per stabilire un collegamento tra la camera di alta e quella di bassa pressione. L'iniezione inizia immediatamente. L'elemento piezoelettrico può accendersi e spegnersi entro un millesimo di secondo. Insieme alla pressione di iniezione molto elevata fino a 2000 bar, ciò garantisce iniezioni molto veloci e precise. Queste velocità consentono inoltre di effettuare più iniezioni una dopo l'altra.
Le iniezioni multiple durante la corsa di aspirazione hanno il vantaggio che la miscelazione aria-carburante è ottimale. L'alta pressione fa sì che le goccioline di carburante vengano nebulizzate in modo ultra fine, in modo che si mescolino ancora meglio con l'aria. Durante la corsa di aspirazione possono essere effettuate fino a 8 iniezioni. Ciò ha conseguenze positive sul consumo di carburante, sulla potenza e sulle emissioni di scarico.
Strategie di iniezione iniezione diretta:
La strategia di iniezione dell'iniezione diretta ha diverse varianti: guidata dalla parete, guidata dall'aria e guidata dal getto (vedere le immagini sottostanti). In queste situazioni si ha un processo di combustione a strati. Ciò non si applica a tutte le condizioni operative.
- Guidata alla parete: il pistone guida la nuvola di carburante verso la candela. La distanza tra la candela e l'iniettore è ampia. Applicato ai motori GDI e HPI.
- Guidata dall'aria: il movimento dell'aria porta la nuvola di carburante alla candela. La distanza tra la candela e l'iniettore è ampia. Applicato ai motori FSI e JTS.
- Getto guidato: la candela si trova sul bordo della nuvola di carburante. La distanza tra l'iniettore e la candela è piccola. Applicato ai motori BMW.
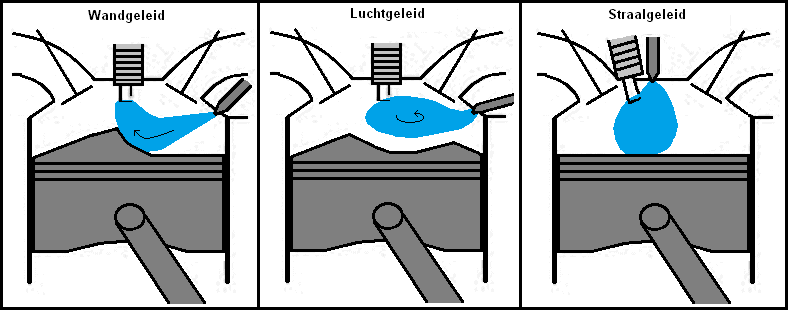
Come già accennato, i motori benzina a iniezione diretta non hanno la combustione stratificata in tutte le condizioni di funzionamento. I motori con iniezione diretta guidata dal getto possono funzionare in fasi a carico parziale. Un processo di combustione a strati significa che nello spazio di combustione sono presenti diversi strati d'aria. Vicino alla candela il valore lambda è 1. Più lontano il valore lambda diventa più alto (più magra, quindi più aria). Quest'aria fornisce uno strato d'aria isolante. In un processo a strati il tempo di iniezione è successivo rispetto al processo omogeneo. Con l'aiuto di un'iniezione stratificata, la valvola a farfalla può essere completamente aperta, in modo da soffocare meno l'aria. Poiché l'aria aspirata viene desmodata, incontra meno resistenza e può quindi essere aspirata più facilmente. Poiché a causa dello strato d'aria isolante il valore lambda nello spazio di combustione con iniezione stratificata è inferiore a 1, ciò non causa problemi con la combustione. Durante il processo di stratificazione il consumo di carburante diminuisce.
Con miscela omogenea il valore lambda è ovunque 1. Ciò significa che in un motore a benzina il rapporto aria/carburante è 14,7:1 (14,7 kg di aria con 1 kg di carburante). Ogni motore può funzionare in modo omogeneo. Se avviene l'arricchimento il valore lambda diminuirà mentre se la miscela viene magra il valore lambda aumenterà:
<1 = Ricco
>1 = Scarso
Un motore oscillerà sempre tra ricco e magro per mantenere il corretto funzionamento del convertitore catalitico. IL sonda lambda invia i dati al sistema di gestione del motore.
A pieno carico il motore funziona sempre in modo omogeneo. Ciò fornisce una coppia maggiore rispetto a un processo a strati. Se il motore funziona in modo omogeneo, il carburante viene iniettato anticipatamente. Il motore funziona in modo omogeneo anche durante la partenza da fermo. Si ottiene quindi una coppia di avviamento più elevata rispetto a quella che si otterrebbe se il motore funzionasse a strati.
La curva caratteristica sottostante mostra le situazioni operative a velocità diverse rispetto al pressione di combustione, con e senza uso dell'EGR.
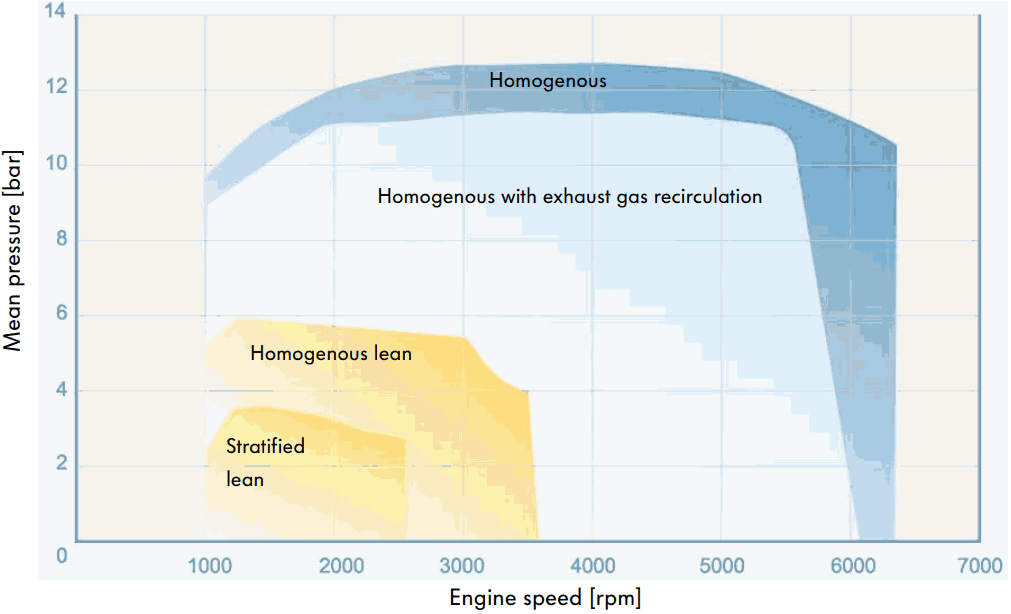
Doppia iniezione:
Il gruppo VAG utilizza motori a benzina a doppia iniezione per soddisfare gli attuali standard sulle emissioni. Nei motori a doppia iniezione sono presenti due sistemi di iniezione del carburante: un sistema a bassa pressione e un sistema ad alta pressione.
- Il sistema a bassa pressione contiene iniettori MPI utilizzati da decenni. Gli iniettori MPI sono montati nel collettore di aspirazione e iniettano nella valvola di aspirazione ad una pressione compresa tra 4 e 5 bar;
- Il sistema ad alta pressione contiene iniettori ad alta pressione che iniettano direttamente nella camera di combustione con una pressione di iniezione massima compresa tra 150 e 200 bar.
Il sistema di gestione del motore determina quale iniettore viene controllato.
L'immagine seguente mostra una sezione trasversale della testata con i due impianti di alimentazione.
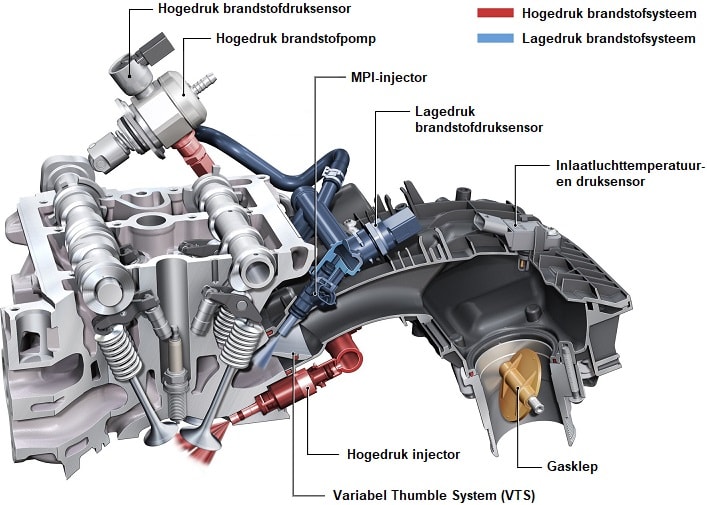
L'iniezione MPI offre una migliore miscelazione tra aria e carburante. Gli iniettori diretti vengono utilizzati al minimo e a pieno carico. Con l'iniezione diretta si ottiene un migliore raffreddamento, che rende possibile un rapporto di compressione più elevato. Tuttavia, la miscelazione di aria e carburante non è ottimale. Ciò provoca più emissioni di fuliggine. Per questo motivo i motori ad iniezione diretta sono oggi dotati di filtro antiparticolato. Questo non è un problema con la doppia iniezione. Il "sistema a pollice variabile", abbreviato VTS, è una versione di un collettore di aspirazione variabile che fornisce un migliore flusso d'aria. Il "pollice" è un flusso d'aria che si crea in un vortice quando entra nel cilindro. Il vortice d'aria è necessario per miscelare correttamente il carburante proveniente dall'iniettore MPI con l'aria.
La doppia iniezione in combinazione con il VTS garantisce migliori emissioni di scarico. Un ulteriore vantaggio è che la valvola di aspirazione viene pulita dall'iniettore MPI. I motori con iniezione diretta spesso soffrono di un tratto di aspirazione sporco (collettore di aspirazione e valvole di aspirazione), che causa problemi come un'alimentazione d'aria limitata. In uno scenario estremo, l'aspirazione diventa così intasata che la valvola di aspirazione non può più chiudersi correttamente sulla testata e alla fine brucia perché non riesce a dissipare sufficientemente il calore.
È noto che gli stessi motori negli Stati Uniti sono dotati di sola iniezione diretta per i motori VAG a doppia iniezione. Il collettore di aspirazione è tappato. Questo perché, al momento in cui scrivo, i requisiti ambientali sono più severi in Europa che negli Stati Uniti e il produttore non fornisce motori per mercati in cui gli standard sulle emissioni sono meno severi con sistemi così costosi per ragioni di costo.
Misurazione delle caratteristiche di tensione e corrente su un iniettore multipunto:
L'oscilloscopio può misurare solo la tensione. I cavi di misura possono essere collegati in parallelo ai componenti elettrici. Non è possibile misurare la corrente in serie. La corrente può essere misurata utilizzando una pinza amperometrica induttiva. I sensori Hall nella pinza amperometrica misurano il campo magnetico e lo convertono in tensione. La tensione può essere misurata con l'oscilloscopio. In questo caso si applica un fattore di conversione di 10 mv per ampere; Per ogni 0,010 Volt trasmessi dalla pinza amperometrica è possibile convertirli in 1 A.
La seguente immagine dell'oscilloscopio mostra il profilo di tensione e corrente di un iniettore elettromagnetico.
- Rosso: gradiente di tensione;
- Giallo: flusso di corrente.
A riposo la tensione è di 14 volt. Ora non c'è alcuna differenza di tensione sulla spina, quindi non scorre corrente. L'ECU collega un filo a terra per controllare l'iniettore. La differenza di tensione fa sì che la corrente circoli attraverso la bobina dell'iniettore.
La linea gialla indica il flusso di corrente: nel momento in cui la tensione scende a 0 volt, inizia l'accumulo di corrente. Il caricamento della bobina richiede tempo. La corrente non aumenta oltre circa 0,9 A. A metà dell'accumulo di corrente vediamo una curva nella linea: questo è il momento in cui si è accumulato abbastanza magnetismo per sollevare l'ago dalla sua sede. L'iniettore inizia a iniettare.
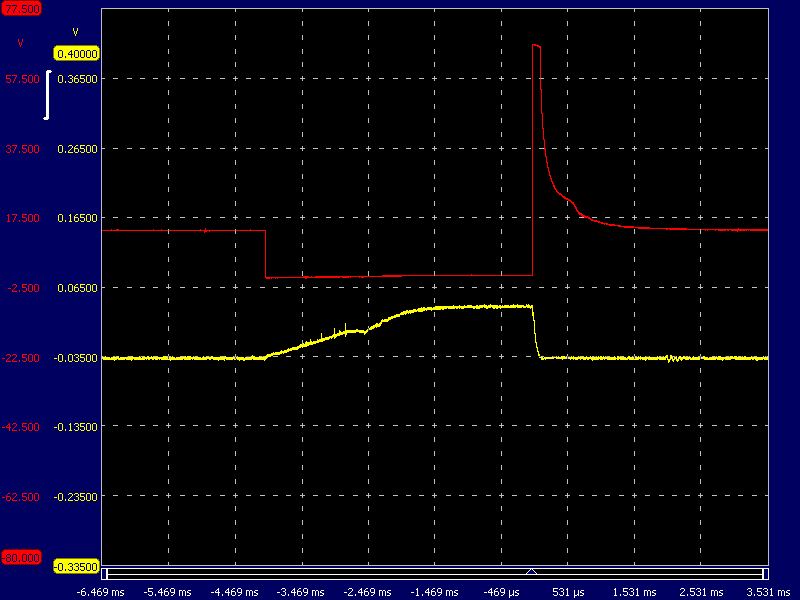
L'ECU interrompe il collegamento a terra per interrompere il controllo. L'energia residua nella bobina fornisce una tensione di induzione di circa 60 volt. L'iniettore smette di iniettare perché la molla spinge nuovamente l'ago nella sua sede. Ciò può essere visto nell'immagine dell'oscilloscopio dall'urto nel segnale di tensione.
Se il motore funziona in modo irregolare e si verifica una mancata accensione del cilindro, ciò può essere dovuto a diverse cause:
- Scintilla assente o scarsa a causa di una candela, di un cavo della candela o di una bobina di accensione difettosi;
- Limitazione dell'erogazione di carburante a causa di filtro del carburante intasato, regolatore di pressione difettoso, problema con la pompa del carburante o l'iniettore;
- Perdita di compressione dovuta a un problema con le fasce elastiche, guarnizione della testata difettosa o guarnizioni delle valvole.
Durante una diagnosi è possibile utilizzare un oscilloscopio per verificare se gli iniettori funzionano ancora correttamente. All'inizio di questa sezione sono state mostrate le misurazioni in cui non si sono verificati malfunzionamenti. Le linee blu mostrano ad esempio come sarebbe il profilo di tensione e corrente di un iniettore difettoso.
Nel caso in cui il controllo dell'iniettore sia corretto, ma nell'immagine della tensione e della corrente non siano visibili pieghe, si può concludere che l'ago dell'iniettore non si muove. Poiché l'iniettore di un cilindro non funziona correttamente e gli altri iniettori funzionano correttamente, le immagini dei diversi iniettori possono essere facilmente confrontate tra loro.
Se si tocca delicatamente l'iniettore, l'ago dell'iniettore potrebbe allentarsi. In questo caso il motore girerà subito più silenziosamente e le pieghe saranno nuovamente visibili nelle immagini del telescopio. Ciò tuttavia non garantisce una soluzione permanente; ci sono buone probabilità che il problema si ripresenti in breve tempo. È necessaria la sostituzione del relativo iniettore.
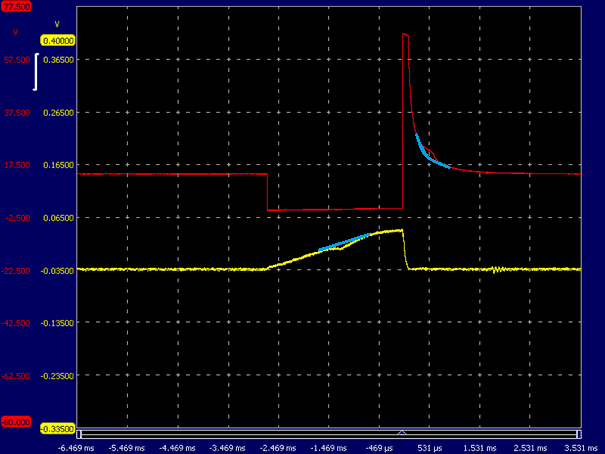
L'ago nell'iniettore si apre solo dopo che la bobina è stata sufficientemente carica. Di conseguenza, l'iniettore non inietta immediatamente il carburante quando l'ECU inizia a controllarlo. Al termine dell'azionamento la molla preme l'ago dell'iniettore nella sua sede. Anche questo richiede tempo. Il tempo di controllo solitamente non è uguale al tempo di iniezione. L'immagine seguente mostra la curva di tensione e corrente dello stesso iniettore di cui sopra, ma con una velocità maggiore.
- Inizio del controllo: l'ECU commuta il filo di controllo a massa. La corrente scorre attraverso la bobina dell'iniettore per aprirlo. La piega nel flusso indica il momento in cui l'ago dell'iniettore si apre. La corrente poi aumenta leggermente e quindi rimane costante. L'ago dell'iniettore rimane aperto.
- Fine del controllo: come già descritto, nell'immagine della tensione riconosciamo il momento in cui lo spillo dell'iniettore viene chiuso dalla gobba.
Il controllo dura 4 ms, ma il tempo di iniezione effettivo è 3 ms. Chiamiamo la differenza tra questi "ritardo", tradotto in olandese come "ritardo". L'ECU controlla quindi l'iniettore per 4 ms per consentirgli di iniettare per 3 ms.
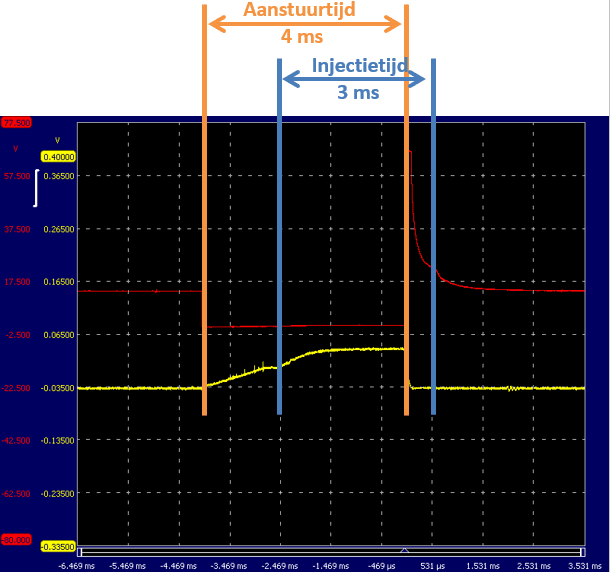
Fasatura dell'iniezione in relazione alla posizione dell'albero motore:
Il momento dell'iniezione può essere visualizzato utilizzando un oscilloscopio. Il canale A (rosso) è sul filo di terra dell'iniettore e il canale B (giallo) è sul filo dell'iniettore sensore di posizione dell'albero motore collegato. Mentre il motore è in funzione, possiamo utilizzare questa immagine dell'oscilloscopio per determinare i tempi e il tempo di iniezione.
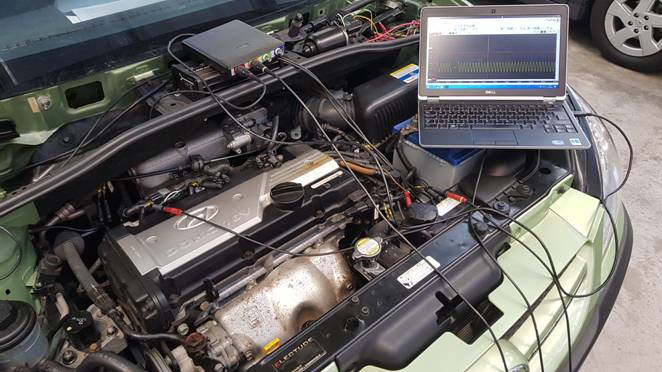
L'immagine dell'oscilloscopio è stata scattata al minimo. L'immagine rossa della tensione mostra l'apertura e la chiusura dell'iniettore (vedere la sezione: Misurazione delle caratteristiche di tensione e corrente su un iniettore multipunto). Al tempo -2,860 ms inizia il controllo; la tensione da 12 volt scende a 0 volt. Questo è il punto in cui la bobina dell'iniettore è messa a terra e la corrente scorre. Il controllo dell'iniettore termina quando la linea rossa risale. A causa dell'energia accumulata nella bobina si verifica una tensione di induzione di oltre 60 volt. Quindi la tensione scende gradualmente a 12 volt; qui l'iniettore viene nuovamente spento.
La tensione alternata rossa proviene da quella induttiva sensore di posizione dell'albero motore. Ogni volta che i denti della ruota fonica girano davanti al sensore dell'albero motore, viene creata una tensione alternata sinusoidale. La ruota fonica contiene 60 denti, 2 dei quali sono stati levigati. I due denti rettificati costituiscono il punto di riferimento in cui la gestione del motore riconosce che i pistoni dei cilindri 1 e 4 si trovano tra 90⁰ e 120⁰ prima del PMS (punto morto superiore). Dopo che il dente mancante è stato riconosciuto, la gestione del motore ha il tempo di (eventualmente in combinazione con sensore albero a camme) per determinare il momento corretto di iniezione e accensione e per attivare l'iniettore e la bobina di accensione prima che il pistone raggiunga il PMS.
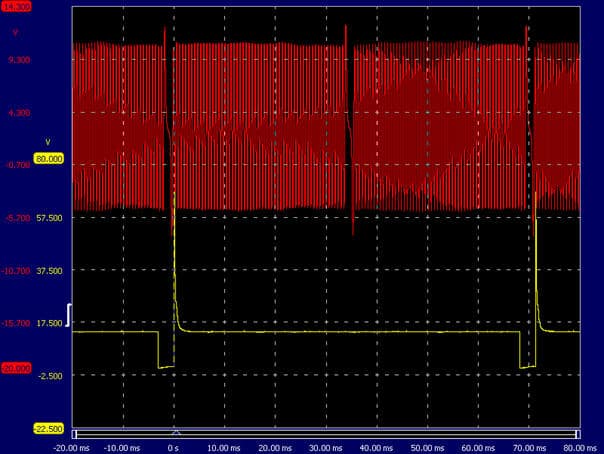
L'immagine dell'oscilloscopio mostra l'ora in cui inizia l'iniezione; l'iniezione inizia con il quarto impulso del sensore albero motore. Supponendo che ci siano 60 - 2 denti, dopo ogni 6⁰ di rotazione dell'albero motore (360⁰ per 1 giro / 60 denti) l'iniezione avviene 24 gradi dopo il punto di riferimento. Il dente mancante è 90⁰ prima del TDC, quindi l'iniezione inizia (90⁰ – 24⁰) = 66⁰ prima del TDC.
Con un aumento del numero di giri di 2000 giri/min gli impulsi del sensore induttivo dell'albero motore sono più ravvicinati. La frequenza di questo segnale viene tradotta in velocità dal sistema di gestione del motore. A seconda della velocità, il carico (misurato dal Sensore MAP) e il temperature dell'aria aspirata e del liquido di raffreddamento, viene determinato il tempo di iniezione richiesto. Il tempo di iniezione avviene prima e l'iniettore rimane a terra per un tempo più lungo: l'iniettore inietta prima e più a lungo.
Dall'inizio dell'attivazione fino al punto di attivazione (freccia all'altezza dello spegnimento dell'iniettore), il tempo di attivazione è di circa 5,2 ms. Il tempo di attivazione dell'iniettore non è pari all'iniezione effettiva (vedere paragrafo precedente).
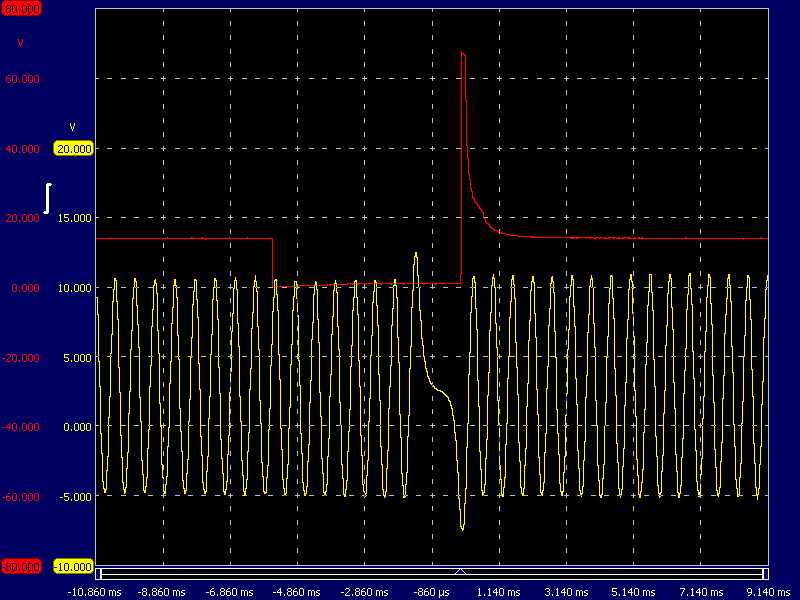
Nella seguente immagine dell'oscilloscopio, il segnale induttivo dell'albero motore è mostrato in rosso e il segnale dell'iniettore è mostrato in giallo. Aumentando la velocità fino a circa 3000 giri/min si notano due comandi degli iniettori. È chiaramente visibile che l'iniezione di carburante del cilindro 1 avviene ad ogni seconda rotazione dell'albero motore.
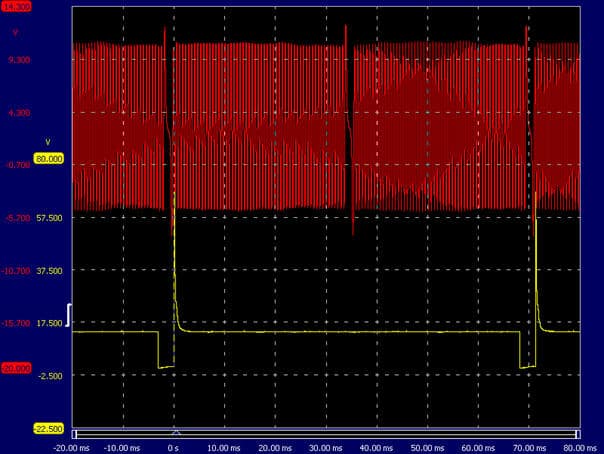
Limitazione corrente nell'ECU:
Come mostrato dalle misurazioni nella sezione “Misurazione di tensione e corrente su un iniettore multipunto”, c'è un ritardo tra l'attivazione e l'effettiva apertura dell'ago dell'iniettore. In questo caso l'apertura richiede 1,5 ms.
L'ago dell'iniettore si aprirebbe più velocemente se la corrente attraverso la bobina aumentasse più velocemente. La corrente dipende dalla resistenza della bobina: minore è la resistenza, più veloce si accumula la corrente. Gli iniettori ad alta impedenza utilizzati nel motore delle misurazioni hanno una resistenza di 16 Ohm. Con una tensione di bordo di 14 volt scorrerà una piccola corrente:
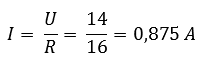
La corrente è sufficiente per aprire l'ago dell'iniettore, ma non troppo alta in modo che diventi troppo caldo a causa della potenza troppo elevata:

Poiché viene accumulata solo una potenza ridotta, non è necessario utilizzare un controllo di corrente. Ciò sarebbe necessario con iniettori a bassa impedenza.
- Gli iniettori a bassa impedenza hanno il vantaggio che l'accumulo di corrente aumenta rapidamente fin dall'inizio. Ciò si traduce in una rapida apertura dell'ago dell'iniettore, quindi un ritardo minimo.
- Gli iniettori a basso ohm hanno una resistenza di circa 2,8 ohm. La bassa resistenza fa fluire una corrente elevata:
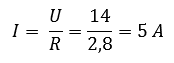
Anche la potenza aumenta notevolmente:

Il consumo energetico è quasi sette volte superiore rispetto agli iniettori ad alta impedenza. Se la corrente aumenta troppo, si sviluppa calore negli iniettori e nello stadio di uscita del dispositivo di controllo. Per limitare la corrente, la tensione viene attivata e disattivata più volte in un breve periodo di tempo. Dopo che l'ago dell'iniettore è stato aperto, è necessaria poca energia per mantenerlo aperto. La corrente diminuisce durante l'accensione e lo spegnimento. Questa progressione può essere vista nell'immagine dell'oscilloscopio.
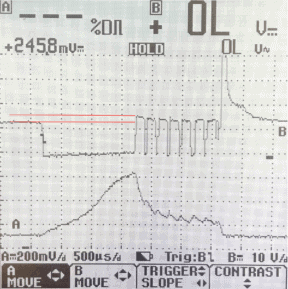
Determinazione della quantità richiesta di carburante:
Il produttore ha determinato la quantità necessaria di carburante in vari campi caratteristici che sono memorizzati nella memoria ROM della ECU. Esso sistema di gestione del motore legge da questi grafici la quantità di carburante necessaria senza correzioni. Questo ovviamente dipende dalla velocità del motore, dalla temperatura e dal carico. I parametri più importanti per determinare la corretta quantità di carburante sono spiegati in questa sezione come tabella VE e tabella AFR.
Tabella VE:
La tabella VE rappresenta l'efficienza volumetrica e il rapporto aria/carburante ad ogni regime del motore e pressione nel collettore di aspirazione. L'efficienza volumetrica è il rapporto tra la quantità misurata di aria che riempie i cilindri e la quantità di aria che riempirebbe il cilindro in una situazione statica, a seconda della velocità del motore e della pressione del collettore di aspirazione. I valori nella tabella vengono utilizzati dall'ECU per determinare la massa d'aria attuale e quindi il livello di riempimento. Questi dati vengono utilizzati per calcolare la quantità di carburante da iniettare.
Questo approccio teorico differisce dalla realtà. Le specifiche del motore non sono ancora state prese in considerazione qui. Considerare il diagramma delle valvole (sovrapposizione delle valvole o eventualmente fasatura variabile delle valvole), la resistenza dell'aria nel tratto di aspirazione, ecc. Ecco perché viene applicato un fattore di correzione che dà una deviazione dalla relazione lineare. Il fattore di correzione è mostrato nell'immagine sopra dalla linea tratteggiata. La curva indica fino a che punto la relazione lineare è corretta. Ad una pressione di 60 kPa la deviazione è di circa il 50% dalla linea che mostra la relazione lineare. Il fattore di correzione può essere espresso in percentuale.
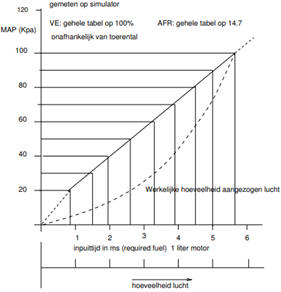
In una tabella VE, ogni cella indica la percentuale associata alla pressione negativa rispetto alla velocità. Questa percentuale sarà massima alla velocità alla quale la coppia è massima. Dopotutto, lì il motore è più efficiente perché riempie meglio.
I valori nelle tabelle VE e AFR più avanti in questa sezione derivano dalla curva di coppia e potenza di un motore 1.8 20v di una VW Golf.
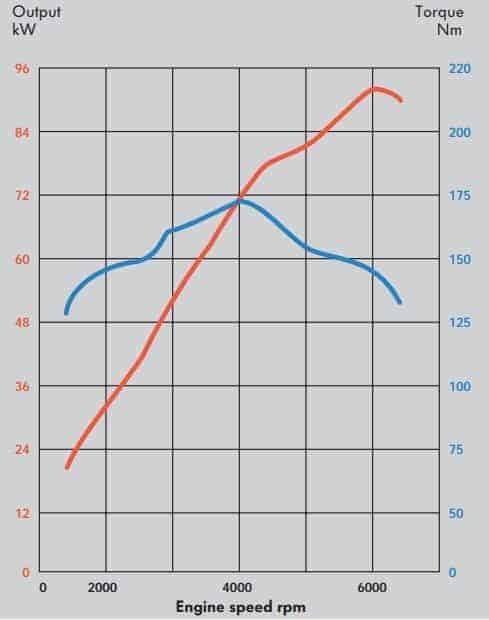
Le immagini sottostanti mostrano la tabella VE come tabella compilabile e la rappresentazione tridimensionale creata utilizzando la curva di coppia e potenza nel programma “TunerStudio”. Questo programma viene utilizzato principalmente per fornire software per una ECU programmabile come MegaSquirt o Speeduino. Per maggiori informazioni: consultare le pagine a riguardo Progetto MegaSquirt.
L'asse verticale mostra la MAP (pressione dell'aria nel collettore) da 15 kPa (molta pressione negativa) a 100 kPa (la pressione dell'aria esterna). La MAP indica il carico del motore. L'asse orizzontale indica la velocità del motore tra il minimo e il regime massimo.
Le celle della tabella VE mostrano il livello di riempimento del motore. In altre parole; quanto è efficiente il motore a una determinata velocità e carico. Il motore è più efficiente attorno alla velocità in cui la coppia è massima (circa 4200 giri/min); le percentuali sono le più alte qui. È qui che il motore si “riempie” meglio. L'applicazione di tecniche che aumentano il livello di riempimento, come la fasatura variabile delle valvole, la regolazione del collettore di aspirazione o l'utilizzo di un turbo, avvantaggerà le percentuali.
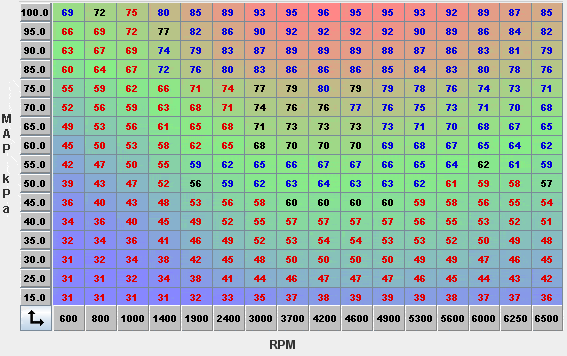
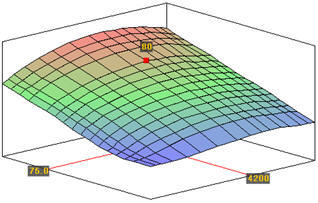
Tabella AFR:
La composizione aria/carburante richiesta viene registrata in una tabella AFR. AFR è l’abbreviazione di “Air Fuel Ratio”. Con un rapporto di miscelazione stechiometrico (lambda = 1), per bruciare 14,7 kg di benzina sono necessari 1 kg di aria. Una miscela stechiometrica non è desiderabile in tutte le situazioni.
- Una miscela magra favorisce i consumi;
- Una miscela ricca consente una potenza maggiore.
Quando il motore deve erogare maggiore potenza (P) avviene l'arricchimento. Una miscela più ricca fornisce anche il raffreddamento. Arricchire a λ = 0,8 significa che si applica un rapporto di miscelazione (AFR) di 11,76 kg di aria per 1 kg di benzina. Quindi c'è meno aria disponibile per bruciare 1 kg di carburante rispetto a una miscela stechiometrica. Una miscela magra, invece, garantisce un miglior consumo di carburante (be), ma dà più possibilità di battere in testa. Arricchire o impoverire la miscela deve sempre restare entro i limiti di combustione.
Al minimo, la velocità è compresa tra 600 e 900 giri/min. La valvola del gas è quasi completamente chiusa e la pressione negativa è elevata: è compresa tra 25 e 40 kPa. In questo intervallo di velocità la miscela è stechiometrica (14,7:1).
In caso di carico parziale, la velocità del motore sarà aumentata a 4200 giri/min. La valvola a farfalla viene aperta ulteriormente, quindi la depressione nel collettore di aspirazione scende a 40 – 75 kPa. All'aumentare del carico del motore, la pressione negativa diminuisce; avviene l'arricchimento (AFR di 13:1). Una miscela magra è possibile con un carico motore basso. A pieno carico l'acceleratore è completamente aperto. La pressione negativa scende a 100 kPa (la pressione dell'aria esterna) e si verifica l'arricchimento massimo (12,5:1).
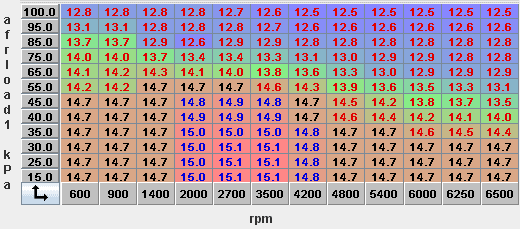
Il valore lambda non influisce solo sulla potenza e sul consumo di carburante, ma anche sulle emissioni di scarico. Una miscela più ricca garantisce un contenuto di NOx inferiore, ma anche emissioni di CO e HC più elevate. Con una miscela più magra, le particelle di carburante sono più distanziate, per cui la combustione non è più ottimale; con il risultato che aumentano anche le emissioni di HC.
Quando si utilizza un catalizzatore, è auspicabile garantire che l'iniezione sia costantemente alternata tra ricca e magra. In una miscela ricca, a causa della carenza di ossigeno, si forma CO, con la quale il catalizzatore riduce gli NOx. Una miscela magra contiene un surplus di ossigeno, che ossida CO e HC.
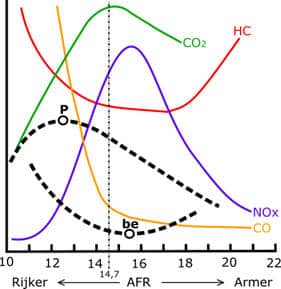
L'unità di controllo determina la quantità di carburante da iniettare. Innanzitutto vengono letti i dati base dell'iniezione dai campi caratteristici. Nel calcolo della quantità iniettata vengono inclusi, tra gli altri, i valori delle tabelle VE e AFR. Vengono inoltre presi in considerazione i seguenti valori determinati dal produttore:
- arricchimento in funzione della temperatura del liquido refrigerante e dell'aria aspirata;
- arricchimento dell'accelerazione a breve termine quando si apre (rapidamente) l'acceleratore;
- correzione dovuta alla variazione della tensione di bordo.
Oltre a questi valori rilevati vengono attentamente prese in considerazione le tensioni che la sonda lambda invia alla centralina. Queste tensioni dipendono dal contenuto di ossigeno nei gas di scarico. Questo è un fattore variabile che cambia continuamente. L'ingresso di queste tensioni del sensore viene definito cosiddetto "finiture del carburante"incorporato.
Come vengono determinati i valori della tabella VE e AFR e le altre impostazioni citate sono descritte nelle pagine dell'esecuzione Progetto MegaSquirt.