Soggetti:
- Storia del motore diesel
- operazione
- Vantaggi e svantaggi del motore diesel
- Ciclo di lavoro del motore diesel a quattro tempi
- Iniezione diretta e indiretta
- Sezione di bassa e alta pressione
- Processo di iniezione
- Bussare al diesel
Storia del motore diesel:
Il motore diesel prende il nome dal suo inventore Rudolf Diesel (1858-1913). Il primo motore diesel secondo la teoria di Diesel divenne realtà il 17 febbraio 1894. Questo motore funzionava secondo il principio dell'autoaccensione e funzionava per 1 minuto lungo 88 giri. Robert Bosch sviluppò la pompa di iniezione ad alta pressione che permise al motore diesel di iniziare la sua conquista globale.
La prima autovettura con motore diesel fu la Mercedes-Benz 170D del 1935.
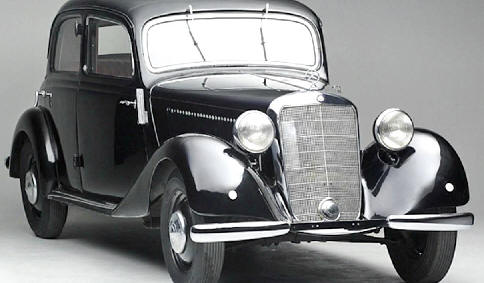
Operazione:
Un motore diesel immette aria nei cilindri. Nessuna miscela, come spesso accade con i motori a benzina. Lì il carburante è spesso già miscelato con l'aria (la miscela). L'aria in un motore diesel viene talvolta aspirata dal motore stesso (senza turbo), solitamente alimentata sotto pressione da un turbo. Questo si chiama sovralimentazione. La sovralimentazione fa entrare una maggiore quantità di aria, che può essere accesa con carburante aggiuntivo. Maggiori informazioni sul riempimento a pressione sono disponibili alla pagina turbo. Il motore diesel viene alimentato con quanta più aria possibile, che non è regolata dalla quantità come nel motore a benzina. La fornitura d'aria illimitata è chiamata “surplus d'aria”.
Nel motore diesel, il carburante non viene acceso con l'aiuto di un componente (proprio come la candela accende la benzina in un motore a benzina). In un motore diesel, la combustione viene ottenuta iniettando carburante diesel. Questo è il motivo per cui il motore diesel prende il nome di “autoaccenditore”. IL pompa del carburante ad alta pressione fornisce la pressione del carburante necessaria.
Questa combustione richiede molto calore. Questo calore è creato dall'elevata pressione di compressione creata dal pistone durante la compressione. La compressione dell'aria (viene posta ad altissima pressione) crea molto calore. Questo calore è necessario per la combustione.
De vertuiver inietta una certa quantità di gasolio appena prima che il pistone raggiunga il PMS. Questo di solito viene fatto in più fasi, con una pre-, una principale e una post-iniezione. Poiché il gasolio viene miscelato con l'aria calda (a causa dell'elevata pressione finale di compressione), questo carburante si accende da solo. Questo si chiama colpo di potenza. (Maggiori informazioni sul processo in quattro movimenti più avanti).
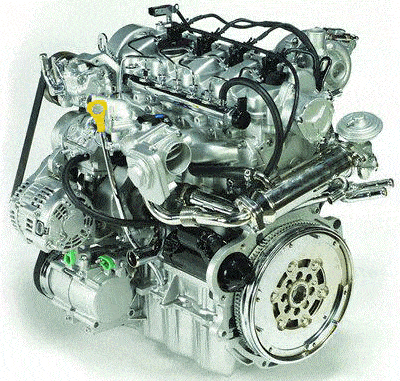
Il motore diesel ha quindi bisogno di calore per avviare la combustione. Questo calore (di almeno 250 gradi) non è ancora presente all'avvio del motore. La pressione finale di compressione spesso non fornisce la temperatura corretta nella camera di combustione. Per risolvere questo ci sono candelette montato nella testata. Queste candelette si attivano all'avviamento e garantiscono che l'aria nella camera di combustione abbia la temperatura corretta per accendere il gasolio.
Vantaggi e svantaggi del motore diesel
- Vantaggi di un motore diesel rispetto a un motore a benzina:
Grazie al rapporto di compressione e al processo di combustione più elevati, un motore diesel è più economico di un motore a benzina. Un motore diesel generalmente ha anche una durata di vita più lunga (a seconda di come viene utilizzato). - Svantaggi di un motore diesel rispetto a un motore a benzina:
Un motore diesel è più rumoroso, ha una potenza inferiore rispetto a un motore a benzina con la stessa cilindrata (senza l'uso di turbo e intercooler) ed è un motore più costoso e di costruzione più pesante. Al giorno d'oggi, il preriscaldamento del motore non è più uno svantaggio, perché un motore diesel a iniezione diretta può avviarsi facilmente senza preriscaldamento. Anche a temperature intorno al punto di congelamento si avvia comunque dopo un po' di tempo.
Oggigiorno i motori diesel stanno diventando sempre più silenziosi, rendendo sempre più difficile distinguere i motori a benzina da quelli diesel.
Ciclo di lavoro del motore diesel a quattro tempi:
Il ciclo di lavoro di un motore diesel è composto da quattro tempi; la corsa di aspirazione, la corsa di compressione, la corsa di potenza e la corsa di scarico. Durante queste corse il pistone si muoveva verso il basso e verso l'alto due volte. L'albero motore ha quindi ruotato due volte.
Accadono molte cose durante ogni colpo; l'aria viene aspirata, il carburante viene iniettato, l'aria e il carburante vengono bruciati e i gas rimanenti vengono espulsi dal cilindro. Di seguito è riportata una descrizione di ciò che accade esattamente in ciascun trucco:
- Corsa di aspirazione:
La valvola di ingresso è aperta, la valvola di scarico è chiusa. Il pistone si sposta dal TDC all'ODP.
– Senza turbo: l'aria viene aspirata a causa della pressione negativa che si crea.
– Con turbo: l'aria aspirata viene alimentata dal turbo a pressione positiva nel vano cilindri.Nel tratto di aspirazione non è presente alcuna valvola di regolazione, come ad esempio la valvola a farfalla del motore a benzina. Nel motore diesel la quantità di aria aspirata non è quindi regolabile. La valvola a farfalla nel sistema di aspirazione (la valvola a farfalla) serve solo per spegnere il motore. Chiudendo questa valvola e interrompendo così l'alimentazione dell'aria, il motore si spegnerà silenziosamente.
Corsa di compressione:
Le valvole di ingresso e uscita sono chiuse. Il pistone si sposta da ODP a TDC. L'aria è compressa. Ciò aumenta la temperatura dell'aria e, a seconda del rapporto di compressione, può raggiungere una temperatura di circa 550 gradi. In un motore a benzina questa temperatura è di circa 400 gradi. Durante l'avviamento a freddo, il motore viene prima riscaldato dal candelette raggiungere la temperatura che consenta alla miscela di accendersi.Colpo di potenza:
Le valvole di ingresso e di uscita sono chiuse e il pistone ha compresso l'aria ad altissima pressione. Pochi gradi prima del PMS, il carburante viene iniettato attraverso l'iniettore e acceso dall'elevata pressione di compressione finale. La pressione risultante dalla combustione spinge il pistone dal PMS all'ODP.Corsa di scarico:
La valvola di ingresso è chiusa, la valvola di scarico aperta. Il pistone si sposta dall'ODP al PMS ed espelle i gas di scarico. Il processo del cerchio è descritto nella pagina del processo Seiliger.
Iniezione diretta e indiretta:
Un motore può essere dotato di iniezione diretta o iniezione indiretta. Di seguito vengono descritte le differenze tra i due sistemi.
Iniezione diretta:
La pressione di iniezione è maggiore con l'iniezione diretta che con l'iniezione indiretta. Il carburante viene iniettato direttamente nel cilindro (o nel fondo del pistone appositamente formato) alla fine della corsa di compressione. La miscelazione avviene quindi nel cilindro e non nella camera di turbolenza come nell'iniezione indiretta. Per migliorare la formazione della miscela, l'aria in ingresso viene fatta roteare. Il vortice è creato dalla forma del collettore di aspirazione e dalla forma del fondo del pistone.
Rispetto a un motore diesel a iniezione indiretta, un motore diesel a iniezione diretta ha il vantaggio di richiedere una superficie delle pareti della camera di combustione inferiore. Di conseguenza, un motore diesel a iniezione diretta avrà minori perdite di calore di compressione e combustione, con conseguente maggiore efficienza e gas di scarico più puliti.
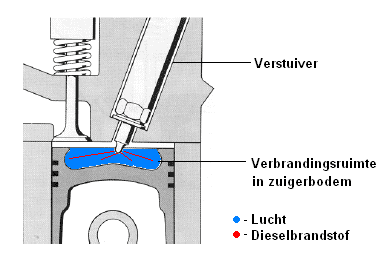
Iniezione indiretta:
L'iniezione indiretta era più comunemente utilizzata nei motori diesel più vecchi. Al giorno d'oggi difficilmente lo incontri più.
In un motore ad iniezione indiretta, il carburante non viene iniettato sopra il pistone, ma viene iniettato, miscelato ed evaporato nella camera di turbolenza. Il carburante viene iniettato nell'aria vorticosa della camera di turbolenza durante la corsa di compressione. Ciò garantisce una buona miscelazione del carburante con l'aria. In questo caso il fondo del pistone è piatto (a volte con incavi per le valvole).
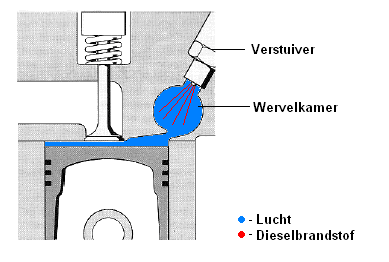
Sezione bassa e alta pressione:
L'alimentazione di carburante di un motore diesel è divisa in 2 parti; la sezione a bassa pressione e la sezione ad alta pressione.
La sezione di bassa pressione è composta dalle seguenti parti:
- Serbatoio di carburante
- Pompa booster (montato nel serbatoio del carburante o in un'unità con pompa ad alta pressione)
- Filtro del carburante (montato sotto l'auto o sotto il cofano, rimuove le particelle contaminate e l'umidità dal gasolio)
- Tubazioni del carburante a bassa pressione (il carburante viene consegnato dal serbatoio alla pompa ad alta pressione attraverso queste tubazioni)
- Linea di ritorno del carburante (conduce il carburante di ritorno e di perdita dagli iniettori, dalla pompa ad alta pressione e dal filtro al serbatoio del carburante) Questo carburante di ritorno/di perdita è necessario per il raffreddamento e la lubrificazione delle parti interessate. Il calore viene così ceduto al serbatoio.
La sezione ad alta pressione è composta dalle seguenti parti:
- Tubazioni del carburante ad alta pressione (il carburante viene fornito attraverso queste tubazioni dalla pompa ad alta pressione agli iniettori. Le tubazioni devono avere tutte la stessa lunghezza e spessore per evitare differenze di pressione)
- Pompa ad alta pressione (il carburante pompato dalla pompa di mandata alla pompa ad alta pressione viene pompato da qui attraverso le linee del carburante ad alta pressione agli iniettori)
- atomizzatore (iniettare il carburante nel cilindro al raggiungimento della pressione di apertura)
Processo di iniezione:
Il tempo che intercorre tra l'iniezione del carburante e la combustione effettiva è chiamato tempo di ritardo. Le piccole goccioline di carburante iniettate attraverso l'iniettore devono passare alla forma gassosa. Questa transizione è possibile a causa dell'elevata temperatura nella camera di combustione (che viene raggiunta dalla pressione finale di compressione o dalla candeletta durante l'avviamento). Questo tempo dovrebbe essere il più breve possibile, altrimenti influenzerà la combustione. Ciò significa anche che il motore funzionerà peggio e sarà disponibile meno potenza.
L'immagine seguente mostra il processo di iniezione completo.
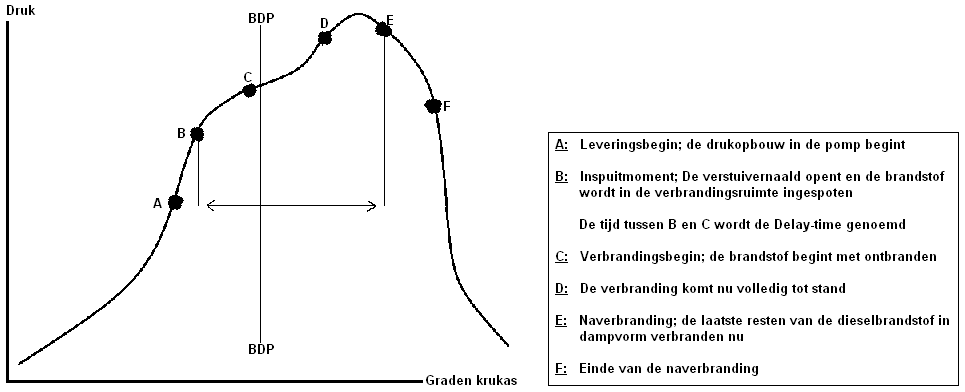
Colpo diesel:
Tra l'inizio dell'iniezione (vedi A nell'immagine sopra) e l'inizio della combustione (C) intercorrono alcuni millisecondi. Le piccolissime goccioline di carburante che vengono iniettate attraverso l'iniettore (la nebbia di carburante) devono prima essere portate a temperatura prima di poter essere convertite in forma di vapore. La parte esterna della gocciolina di carburante si trasforma prima in forma gassosa e poi brucia gradualmente. I resti rimanenti della goccia poi si accendono spontaneamente e provocano il riconoscibile rumore del motore; il colpo del diesel. Si tratta di una combustione incontrollata e può verificarsi nel momento sbagliato.
Le seguenti cose possono causare un battito in testa del diesel:
- Atomizzatori difettosi (gocciolamento o scarsa atomizzazione con gocce troppo grandi)
- Pompa di iniezione difettosa (valvole di mandata o pistoni difettosi)
- Carburante (acqua presente, numero di cetano troppo basso, aria nel carburante
- Motore (pressione finale di compressione troppo bassa, candelette non funzionanti)
- Fasatura errata della pompa del carburante