Tárgyak:
- A projekt kezdete
- Motor
- sebességváltómű
- Vizsgálja meg, cserélje ki és állítsa be a motor alkatrészeit
- Szerelje fel a motort egy mobil keretre
- Hűtés
- Műszerfal és villanyszerelés
- Üzemanyag szivattyú és tank
- Működtesse a motort klasszikus beállításban
A projekt kezdete:
Miután elhatározták, hogy egy motort MegaSquirt motorvezérlő rendszerrel szerelnek fel, mérlegelték a megfelelő motortípust. A standard konverziós csomagok kézikönyvekkel nem voltak érdekesek. A cél az volt, hogy olyan motort használjanak, amely megfelel a következő feltételeknek:
- ennek a motornak nem kell ismert korábbi átalakítási projektje;
- négyhengeres benzinmotor;
- még nincs felszerelve befecskendező és elektronikus gyújtórendszerrel;
- a motor terhelésének képessége.
Motor:
A keresés egy Land Rover (2A sorozat) motorjához vezetett az 70-es évek elején. Ezt a 2,25 literes, négyhengeres, három főcsapágyas benzinmotort eredetileg karburátorral és mechanikus elosztó gyújtással szerelték fel. Ennek a Land Rover motornak és az eredeti sebességváltónak a kombinációja volt meghatározó a választásnál; A sebességváltó kimenő tengelyére erőátviteli fék van rögzítve. Az erőátviteli fék, amely tulajdonképpen rögzítőfékként szolgál, lehetővé teszi a motor fékezését futás közben.
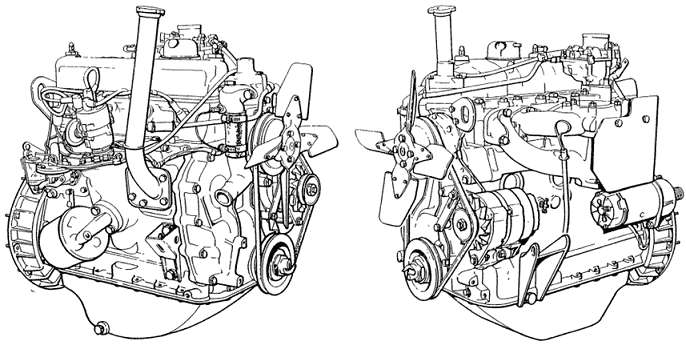
A motor valószínűleg évtizedekig nem működött. Természetesen elég megbízhatónak kell lennie ahhoz, hogy a motorvezérlő rendszerrel működjön. Ezért először alaposan át kellett vizsgálni és tesztelni kellett a motort. A következő célokat tűzték ki:
- Vizsgálja meg, cserélje ki és állítsa be a motor alkatrészeit;
- Szerelje fel a motort egy mobil vázra;
- Hagyja, hogy a motor a klasszikus beállításban működjön;
- Motorvezérlő rendszer alkatrészeinek beszerelése;
- Szerelje össze és készítse elő a MegaSquirt ECU-t;
- Hagyja, hogy a motor működjön a motorvezérlő rendszeren.
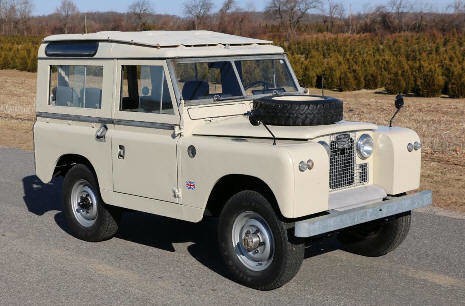
Sebességváltó:
A sebességváltó egy katonai Land Rovertől származik. A zöld szín tulajdonképpen azt adja, hogy a motorral a későbbiekben a lehető legeredetibb egészet alkossa, a zöld festéket eltávolították. A sebességváltó fékje még nincs a képen; ezt később a gyári utasításoknak megfelelően a kimenő tengelyre szerelték fel.
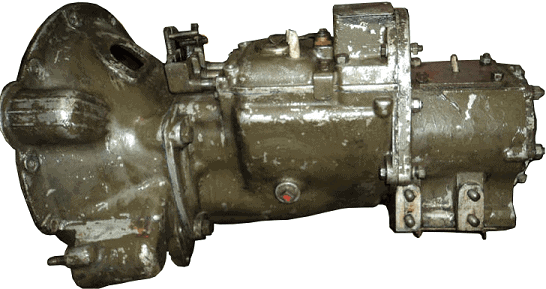
A motor alkatrészeinek ellenőrzése, cseréje és beállítása:
A projekt elején nem volt világos, hogy a rendelkezésre bocsátott motor alkalmas-e a használatra. A motorblokkról keveset tudtak, csak annyit, hogy a motor évekig állt. Nem volt világos, hogy a belső részek sérültek-e, vagy akár – esetleg helyrehozhatatlanul – hibásak. Az utóbbi esetben a motor cseréje volt az egyetlen lehetőség a projekt folytatására.
Annak érdekében, hogy a későbbiekben ne lehessen arra következtetni, hogy a motor használhatatlanná válik, a motor szétszerelése és nagyjavítása mellett döntöttek. Az alkatrészek kopási mintázatait ellenőrizték és összehasonlították a gyári előírásokkal. Azokat az alkatrészeket, amelyeknél a mérések ezen tűréshatáron belül voltak, kicserélték. Az elutasított alkatrészeket kicserélték. Figyelembe vették azt a célt, amelyre a motort használni fogják; a motort a lehető legkisebb költséggel kell megépíteni, hogy kellően megbízható legyen a projekt megvalósításához és tanítási-tanulási eszközként való felhasználásához.
A motort a hajtómű házának rögzítési pontjain rögzítik a tartókonzolhoz. A motor különböző pozíciókba forgatható. Ezáltal mind a hengerfej, mind az olajteknő optimálisan hozzáférhetővé válik a szétszerelési munkákhoz. A motor megfelelő működése érdekében fontos óvintézkedéseket tenni a jó kompressziós végnyomás biztosítására. Ha egy vagy több hengerben túl alacsony a nyomás, az rosszul működő, akadozó motort eredményez. Ebben az esetben a beállítás az újonnan beszerelt gyújtással és a befecskendező rendszerrel nehéz lesz, ha nem lehetetlen.
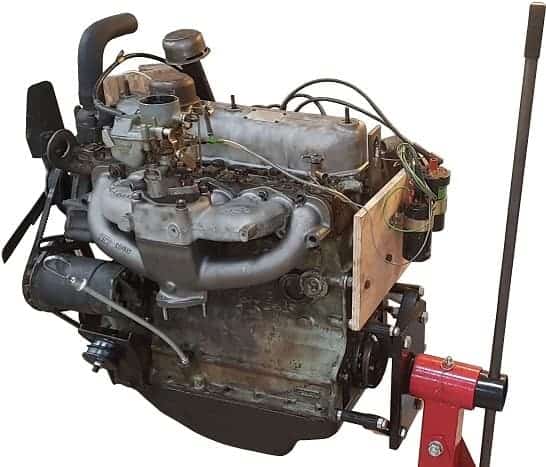
Az egyik első ellenőrzési pont a dugattyúk és a hengerfalak. A megfelelő irányítás érdekében a dugattyúkat el kellett távolítani a motorblokkból. A hengerfej és az olajteknő szétszerelése után a dugattyúkat ki lehetett venni. A dugattyúkat ellenőrizték ovális és látható kopási jelek szempontjából. A dugattyúgyűrűk kopását is ellenőrizték. A kopott dugattyúgyűrűk kompresszióvesztést és olajfogyasztást okozhatnak; mindkét következményt meg kell előzni ezzel az ellenőrzéssel. Az optikai ellenőrzésen kívül a dugattyúgyűrű hornyok és a dugattyúgyűrű közötti hézag mérésére is sor került.
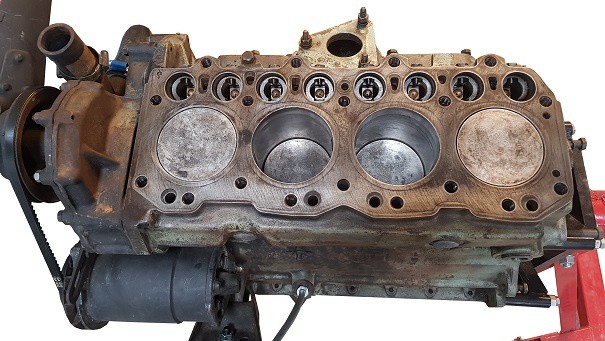
Az alábbi képen egy olyan mérés látható, ahol a dugattyút csavaros idomszerrel mérik. Az oválisság mellett a dugattyú és a hengerfal közötti távolság is meghatározható. A túl nagy távolság túlzott kopást jelent. A projekt esetében ez azt jelentené, hogy esetleg más felesleges dugattyúkat kell beszerelni. A négy dugattyú vizuális és geometriai értékelése után megállapították, hogy nincs túlzott kopás.
A dugattyúgyűrűk cseréje után meg kell mérni a végső hézagot, és szükség esetén be kell állítani, hogy megakadályozzuk a dugattyúgyűrű eltörését (túl kicsi vagy túl nagy hézag miatt), valamint a kompresszió elvesztését (túl nagy hézag miatti szivárgási veszteségek). ). A dugattyúgyűrű a legkisebb átmérőjű hengerben van elhelyezve. A zárhézag mérése hézagmérővel történik. Ez a mérés az ábrán látható. Az 1-es henger dugattyúgyűrűit rossz állapotuk miatt kicserélték és egy milliméterrel kisebbre kellett reszelni; összeszereléskor a végek összeértek.
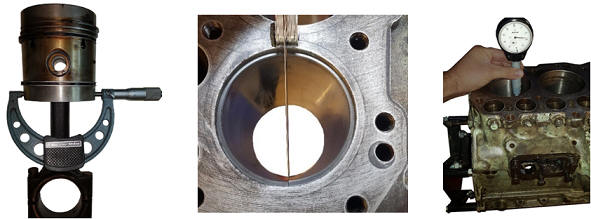
A hengerhüvelyek kopásának mérése megfelelő mérőtárggyal történik. A mutató elhajlása mutatja a kopás mértékét. A képen a 4-es henger hengermérete látható. A henger átmérője megnő, különösen azon az oldalon, ahol a csúszó erő fellép. A hengerfalakon előfordulhat némi kopás, de a kopásnak a tűréshatárokon belül kell lennie. A mérési eredmények azt mutatták, hogy a henger falain elfogadható kopás tapasztalható. A hengerhüvelyek optikai vizsgálata azt mutatta, hogy a falak egy része sima. A csiszoló barázdák már alig voltak jelen.
A hónoló hornyok, egyfajta apró karcolások biztosítják, hogy a dugattyúgyűrű és a hengerfal között mindig legyen egy kis olajréteg. Ennek az olajfóliának a fő feladata a kenés, de egyben tömítésként is szolgál, így segít a végső kompressziós nyomás elérésében. Mind a négy hengerhüvelyben új hónolóhornyokat készítettek megfelelő hónolókővel. A képen ez a művelet látható. Törekedtek arra, hogy a hónoló hornyokat lehetőleg keresztben, 45 fokos szögben alkalmazzák.
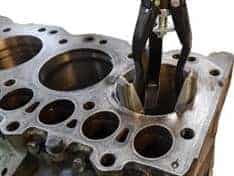
A szelepek lezárják a dugattyú feletti égésteret. A szelepülés mentén történő szivárgás a kompresszió elvesztését okozza; valami, amit meg kell akadályozni. A szelepek és a szelepülék állapotának ellenőrzéséhez először minden szelepet el kell távolítani a hengerfejről. A képen egy leszerelt szeleprugó látható az 1. henger szívószelepéről. Az 1. henger szelepeinek szeleptárcsái annyira megsérültek, hogy mindkettő cseréje mellett döntöttek.
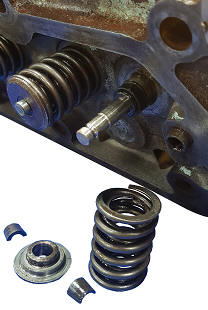
Szétszerelés után úgy tűnt, hogy számos szelepülés megevett/sérült. Az alábbi képen az 1. henger szelepülékei láthatók. Nagyon valószínű, hogy a motor nem működött volna megfelelően, ha ezt nem ellenőrzik. Az új szelepek puszta újracsiszolása nem lenne elegendő, ezért a szelepülékek marása mellett döntöttek.
Szelepülék-vágóval kis mennyiségű anyagot távolítunk el, így a szelepülék ismét sima lesz. A vágószár a szelepvezetőbe van csúsztatva (lásd az alábbi képet). Ez biztosítja, hogy a vágó egyenesen az ülésre helyezhető. A megmunkálási folyamat során két különböző szöget vettek figyelembe, amelyeknél a marást kell elvégezni. Leginkább az 1. és 2. henger szelepei érintettek. A teljesség kedvéért mind a nyolc szelepülés megmunkálásra került. Marás után a szelepeket speciális csiszolóanyaggal csiszolják a lehető legjobb tömítés érdekében.
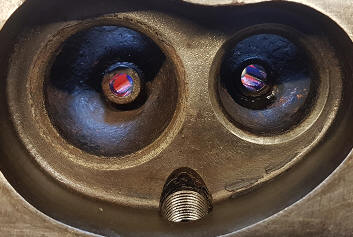
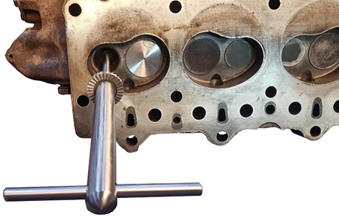
A három főcsapágyas és két nyomócsapágyas főtengely axiális forgattyús tengelyjátékát mérőórával mérjük. Ha túl nagy a tengelyirányú játék, akkor nagyobb axiális csapágyat is be lehet szerelni, ha nincs mechanikai hiba. A képen látható mérés azt mutatta, hogy az axiális hézag rendben van.
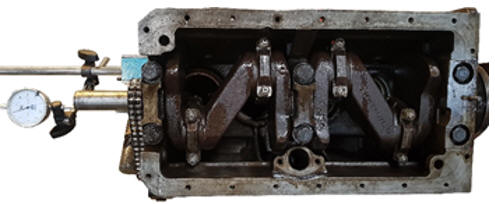
A főtengely és a hajtórúd csúszócsapágyai közötti teret, más szóval: a radiális főtengely hézagát plasztikával mérjük (lásd az ábrát). A plasztik egy speciális műanyag huzal, amely az összenyomás után tartósan deformálódik. A csapágysapka vagy a hajtórúd felszerelése után a plasztik nyomot hagy. A nyomat szélessége jelzi, hogy mekkora játék van a csúszócsapágy és a főtengely között.
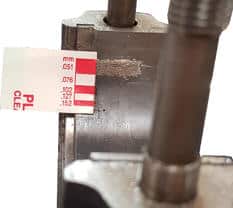
A vezérműlánc továbbítja a mozgást a főtengelyről a vezérműtengelyre. A dugattyúk, a főtengely és a hengerfej felszerelése után a vezérműláncot a beszerelés után újra be kell állítani. A beállítás és jelölések hiánya miatt a beállítást az aszimmetrikus szelepdiagram alapján kellett meghatározni. A főtengelyen lévő fokos tárcsa segítségével meghatározható a szívó- és kipufogószelep nyitási és zárási szöge (lásd a képet). Az elosztó alkatrészeket, például a lánckereket, a láncot, a vezetőt és a feszítőt optikai kopás szempontjából ellenőrizték. Ez rendben volt.
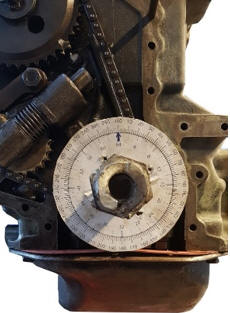
Minden alkatrész az előírt meghúzási nyomatékok szerint van meghúzva. Mivel a motort szétszedték, több megtett kilométer után ellenőrzést kell végezni. Ez azonban nem lehetséges, mert a motor nincs beszerelve a járműbe. Ezért úgy döntöttek, hogy a Land Rover által előírt ellenőrzéseket 24 üzemóra után elvégzik.
A motor felszerelése a mobil vázra:
A cél az volt, hogy a motort oktatási eszközként használják, motorvezérlő rendszeren futva. A motor nincs autóban elhelyezve. A biztonságos és megbízható beállítás érdekében úgy döntöttek, hogy a motort megfelelő motorvázra helyezik. A szándék az, hogy a motort a motortartók eredeti helyére rögzítsék a motorvázra. Mivel nincsenek kész átalakító készletek, a támasztékokat egyedileg kellett elkészíteni.
Az építési szakaszban ki kellett választani a motor felépítését. A motorvezérlő rendszert megnövelt motorterhelés mellett kell beállítani. Mivel az eredeti sebességváltó váltófékes, úgy döntöttek, hogy a váltót a motorvázra is felszerelik. Ennek a sebességváltó-féknek a működtetésével lehetséges a motor rövid ideig tartó terhelés melletti működtetése.
A meglévő motortartók szerkesztése és adaptálása lehetővé tette a motor megbízható csatlakoztatását a vázhoz. A motorváz lehetőséget kínál egy műszerfal rögzítésére is, amelyen többek között a kezelőszervek is megvalósíthatók. A képen az a pillanat látható, amikor a motor a keret fölött lóg és készen áll a rögzítésre.
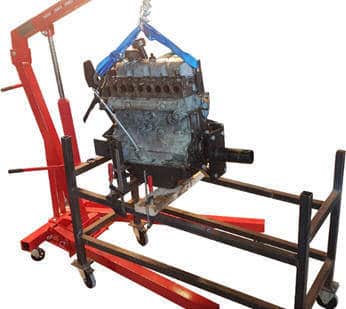
Az elosztóoldali motortartók acélcsövekből és U-profilból készülnek. Motorkerékpár gumi biztosítja a csillapítást. Alul két cső van egymásra szerelve, hogy a motorblokk és a sebességváltó kombinációja a lehető legvízszintesebben kerüljön a vázra. A támasztékokat M8 és M12 menetes rudak, csavarok és anyák segítségével rögzítik a motorblokkhoz és a kerethez.
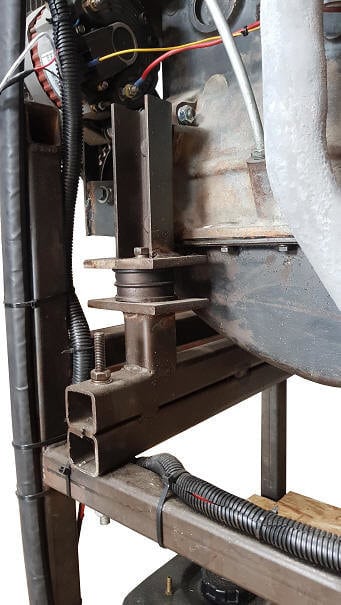
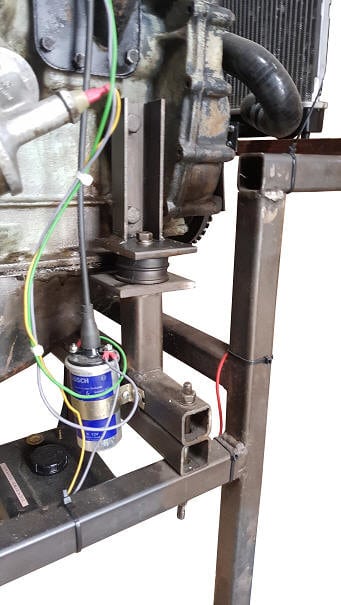
A sebességváltó mindkét oldalán ilyen hajtóműtartó készült, amellyel a vázra támaszkodik.
Miután a motort és a sebességváltót biztonságosan és megbízhatóan felszerelték a vázra, a motor összeszerelése folytatható. Az állítható és állítható alkatrészek, mint például a karburátor és a gyújtás beszerelése után ezek a gyári értékek szerint lettek beállítva.
A vázra más, a motor működését lehetővé tevő alkatrészek is fel vannak szerelve, mint például a hűtő, a kezelőszervekkel ellátott műszerfal és az üzemanyagtartály. Ezeket az összetevőket a következő bekezdések ismertetik.
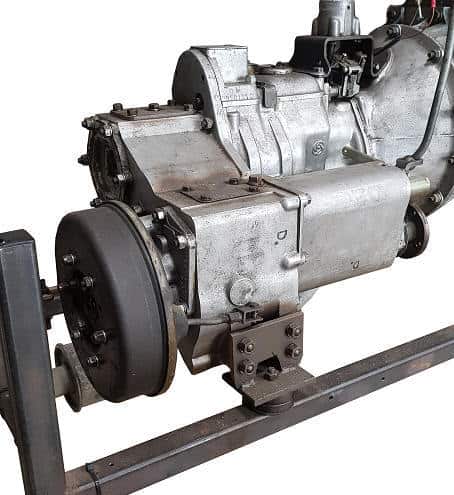
hűtés:
Eredeti állapotában a hűtést egy nagyméretű radiátor és a vízszivattyúra szerelt fém hűtőventilátor biztosítja. Mivel a motort nem járműbe, hanem mobil vázra szerelik, fontos, hogy megfelelő utángyártott alkatrészeket használjanak. A fém hűtőventilátort elektromos hajtású, műanyag ventilátorlapátokkal ellátott hűtőventilátorra cserélték. A műanyag változat nemcsak sokkal biztonságosabb, mert a motor oktatási célokra készült (méréseknél ügyeljen a személyi biztonságra), hanem a hűtő és a motorblokk gyorsabb felfűtésére is alkalmas. Az elektromos hűtőventilátor a műszerfalon található gombbal kapcsolható be és ki. Ez lehetővé teszi a motor gyors felmelegedését, mivel kicsi a mechanikai terhelés lehetősége. Amikor a motor felmelegszik, valószínűbb, hogy "zárt hurok" alakul ki, amelyben a lambda-szonda adatait használják az üzemanyag-befecskendezés szabályozására. Például hideg motornál – „nyílt körben” – extra dúsítás történik: nagyobb mennyiségű üzemanyag befecskendezésekor (λ < 1) nem kívánatos a lambda-szonda általi tüzelőanyag-korrekció.
Az ábra a beépített hűtőrendszer alkatrészeinek áttekintését mutatja. Az eredeti radiátor nem volt meg. Mivel mérete és súlya nem volt alkalmas a motorkerékpár vázra szerelésére, ezért egy kisebb utángyártott radiátort választottak. A felső és alsó hűtőtömlők csatlakozásainak átmérője megegyezik az eredetivel.
A felső és alsó radiátortömlők egyedileg készülnek szilikon tömlőkkel és csatlakozókkal. Az elektromos hűtőventilátor egy tartókonzolhoz van rögzítve. A felső hűtőtömlő védi a radiátort a felborulástól. A túlnyomásos sapka (0,9 bar) védi a hűtőrendszert a túlnyomás ellen. Ha a nyomás túl magasra emelkedik, a hűtősapkában lévő szelep az erő ellenében kinyílik, és a hűtőfolyadék a túlfolyón keresztül egy gyűjtőedénybe áramlik.
Kísérletileg meg kellett állapítani, hogy a radiátor kellően nagy áramlási sebességgel rendelkezik-e, illetve a hűtőventilátor elegendő kapacitással rendelkezik-e a hő elvezetésére. A rendszert az első tesztfázisban rendben találták.
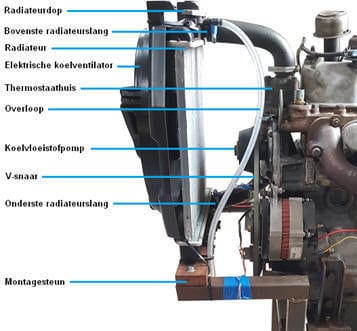
Műszerfal és villanyszerelés:
A kerethez egy műszerfal van rögzítve, amelyen visszajelző lámpák, kapcsolók, a MegaSquirt ECU, különféle relék és kábelkötegek találhatók. A műszerfal a motorfunkciók figyelésére és vezérlésére szolgál.
A képen a műszerfal látható. Az ábrán az 1-es szám a földkapcsoló helyét jelzi; egy kulcs leválasztja az akkumulátort a földről. Mivel nincs szükség áramellátásra a kikapcsolt motorra, biztonságosabb a földelés leválasztása, ha a motort felügyelet nélkül hagyják. A 2-es szám a hűtőventilátor kapcsolóját jelzi. A 3-as és 4-es számok a generátor (D+) jelzőlámpái, az 5-ös az indítógomb, a 6-os pedig a gyújtáskapcsoló (15-ös kapocs). A műszerfal hátulján van egy biztosítékdoboz. A MegaSquirt az alsó panelre van felszerelve, és a 7-es szám jelzi. A 8-as szám az üzemanyag-szivattyú relét jelöli. A műszerfalon lehetőség van egy kitörő doboz felszerelésére is, amelyen a tanulók méréseket végezhetnek. Ez lehetővé teszi az érzékelő értékek és a működtetőelemek vezérlésének mérését az oszcilloszkóppal.
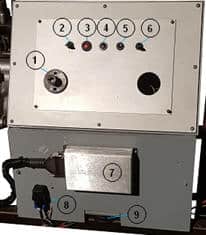
Az eredeti indítórelé vezérli az indítómotort; Egy kis indítógombbal a 86-os érintkező a földre van kötve, ami vezérlőáramot eredményez. A vezérlőáram mágneses mezőt biztosít, aminek következtében a 30. és 87. kapcsok között főáram folyik; az indítómotort ezzel a főárammal látják el, amíg el nem engedik az indítógombot.
Az utólag felszerelt generátor biztosítja a töltőfeszültséget és a töltőáramot az akkumulátornak. A jelzőfény jelzi, hogy a generátor megfelelően töltődik-e. A lambda érzékelő, az injektorok és a gyújtótekercs tápfeszültséget kap a biztosítékdoboztól. A MegaSquirt információátviteli és be- és kikapcsolási parancsait más jel- és földvezetékeken keresztül biztosítják.
Üzemanyag szivattyú és tank.
A klasszikus összeállításban a mechanikus üzemanyag-szivattyút már nem használják a motorvezérlő rendszer alkatrészeinek beszerelésekor, mert az üzemi nyomás túl alacsony (200mbar). A MegaSquirt ECU által vezérelt MPI befecskendezők szükséges üzemanyagnyomása 3 bar. Elegendő egy személygépkocsi szabványos elektronikus üzemanyag-szivattyúja. A helyszűke miatt egy kompakt egységet választottak, amelyben egy házban van az üzemanyagtartály, a szivattyú és a szűrő. A fémkeret lehetővé teszi az egység motorvázra szerelését. A projekt egy későbbi szakaszában beépítik azokat az üzemanyagtömlőket, amelyek az üzemanyag-szivattyú és a szívócső befecskendező szelepei közötti kapcsolatot képezik.
Az üzemanyag-szivattyú tápvezetékei egy kábelcsatornán keresztül vezetnek a műszerfalig, melynek beépítését már leírtuk. A szivattyú pozitív vezetékét a MegaSquirt egy relén keresztül táplálja.
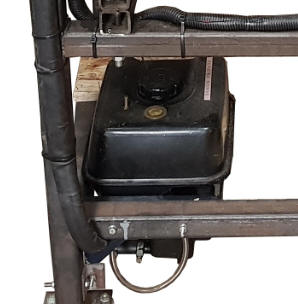
Működtesse a motort klasszikus beállításban.
A motorvezérlő rendszer alkatrészeinek beszerelése előtt a motort kezdetben a klasszikus összeállításban, azaz karburátoros és elosztó gyújtással működőképessé tették. Az 5.2. fejezet leírja a motor és a segédalkatrészek motorvázra szerelésének munkálatait. Az első tesztfázisban, ahol a motort a klasszikus beállítással indították, az alábbi feltételek mellett lehetett ellenőrizni:
- Hideg indítás;
- Üresjárat;
- Megnövekedett sebesség, megnövekedett terhelés;
- Hosszú távú működés üzemi hőmérsékleten.
A fenti ellenőrzések során kiderült, hogy még számos javításra van szükség ahhoz, hogy a motor elég megbízható legyen az átalakításhoz.
- Az első motorindítás után kiderült, hogy a hűtőfolyadék-szivattyú tömítése már nincs rendben; a hűtőfolyadék a csapágy mentén kiszivárgott a motorblokkból. A probléma megoldásához elég volt a hűtőfolyadék szivattyú cseréje.
- A következő probléma a leállás volt, amikor a motor elérte az üzemi hőmérsékletet. A gyújtás meghibásodott, így nem lehetett elindítani a motort. A probléma a forgalmazóban volt, és könnyen megoldódott.
- Idővel olajszivárgás keletkezett a motor és a sebességváltó között. A szivárgás valószínűleg a főtengely tömítéséből származik. Ez a szivárgás a projekt befejezése után megszűnik.
Miután a motort a klasszikus összeállításban rendben találták, folytathattuk az elektronikával.
következő: érzékelők.