Thèmes:
- Déterminer et installer des actionneurs pour le système de gestion du moteur
- Injecteurs de carburant
- Choisir des injecteurs adaptés
- Installation des injecteurs dans le collecteur d'admission
- L'inflammation
- Préparation avec l'allumage classique
- Bobine d'allumage pour le système de gestion du moteur
- Accumulation de courant dans la bobine primaire
- Avance à l'allumage
- corps de papillon
- Configuration de test du moteur pas à pas avec simulateur
- Paramètres du moteur pas à pas
- Circuit de pompe à essence
- Achèvement des travaux mécaniques
Détermination et installation des actionneurs pour le système de gestion moteur :
Les actionneurs qui seront contrôlés avec le MegaSquirt sont les injecteurs, la bobine d'allumage, la pompe à carburant et le moteur pas à pas pour le ralenti. Ce chapitre décrit le processus dans lequel les actionneurs ont été testés et installés sur le bloc moteur, ainsi que la sélection effectuée.
Injecteurs de carburant:
Le MegaSquirt contrôle les injecteurs. Les injecteurs sont reliés à la masse. Avec un composant connecté à la terre, une tension d'alimentation est présente, mais le courant ne circule que lorsque la terre est activée. Dans ce cas, l'injecteur n'injectera que lorsque le calculateur MegaSquirt passe à la masse. Dès l'arrêt de l'activation, l'injecteur arrête d'injecter. La quantité de carburant à injecter est déterminée sur la base du tableau VE et du tableau AFR.
Un MOS FET allume et éteint l'injecteur, provoquant l'injection du carburant. La quantité de carburant déterminée par le MegaSquirt dépend de plusieurs facteurs :
- La loi des gaz parfaits qui relie la quantité d’air à sa pression, son volume et sa température ;
- Valeurs mesurées par les capteurs du bloc moteur : pression dans le collecteur d'admission (capteur MAP), température du liquide de refroidissement et de l'air d'admission, régime du vilebrequin et les données du capteur de position du papillon ;
• Paramètres de réglage : quantité de carburant requise, degré de remplissage (VE), temps d'ouverture des injecteurs et enrichissement sous certaines conditions.
Le temps d'injection doit être le plus long possible lorsque le moteur tourne au ralenti pour obtenir un bon dosage de carburant. Par conséquent, n’importe quel injecteur ne peut pas être utilisé sur le moteur. Les propriétés des différents types d'injecteurs doivent être comparées et les calculs doivent donner un aperçu de la quantité de carburant requise pour le moteur en question. Il y avait également le choix entre des injecteurs à haute et basse impédance. Les injecteurs à faible impédance conviennent aux moteurs où une ouverture très rapide de l'aiguille de l'injecteur est requise. La résistance typique est de 4 ohms. L'inconvénient de ces injecteurs est le courant élevé. Le développement de chaleur que cela crée dans le MegaSquirt n'est pas souhaitable. Il est possible d'utiliser des injecteurs à faible impédance en montant des IGBT spéciaux sur une plaque conductrice de chaleur sur le boîtier MegaSquirt. Il a été décidé d'utiliser des injecteurs à haute impédance. Il y a moins de dégagement de chaleur et ces IGBT ne sont pas utilisés.
La taille du passage (débit) est très importante pour déterminer la bonne quantité d’injection, et donc le contrôle. Si vous choisissez des injecteurs trop gros, le temps d'injection au ralenti sera si court que le moteur risque de tourner de manière irrégulière. La quantité injectée doit être suffisante pour injecter tout le carburant dans le temps disponible. La quantité injectée est indiquée sous forme de temps d'injection en millisecondes. Une charge élevée est supposée à un régime moteur élevé. C'est à une MAP de 100 kPa. Le débit d'injecteur requis peut être calculé en fonction des propriétés du moteur. Le débit de l'injecteur indique combien de millilitres de carburant sont injectés par minute.
Choisir les injecteurs adaptés :
Des injecteurs de trois types différents ont été mis à disposition pour le projet. La recherche a montré quel type d’injecteur était le plus approprié pour ce projet.
Chaque type d'injecteur a un débit différent ; le rendement après une minute d'injection varie selon le type. Avant d’être testés, les injecteurs ont été nettoyés dans un bain à ultrasons. Avec cette méthode de nettoyage, l'intérieur et l'extérieur de l'injecteur sont nettoyés à l'aide de vibrations ultrasoniques et d'un liquide de test spécial, de sorte que d'éventuels résidus de saleté ne puissent pas influencer la mesure du débit ou le modèle d'injection. Pendant le nettoyage par ultrasons, les injecteurs ont été ouverts et fermés en continu et le schéma d'injection de chaque injecteur a été examiné ; c'était une belle brume. Lors de la fermeture, aucune anomalie n'était visible, telle qu'une formation de gouttes ou un jet dévié. Après un nettoyage et des tests aux ultrasons, les joints toriques ont été remplacés pour assurer une bonne étanchéité une fois montés dans le collecteur d'admission.
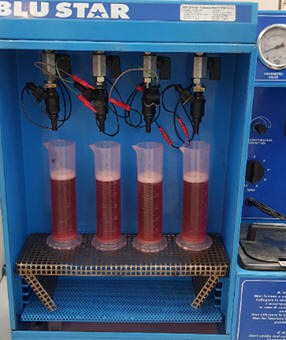
À l'aide d'une configuration de test (voir image ci-dessus), les injecteurs peuvent injecter dans plusieurs tasses à mesurer, de sorte que la quantité de carburant injectée puisse être lue après un certain temps. En contrôlant les injecteurs à une pression de travail de 3 bars, la quantité de carburant injectée peut être contrôlée. La pression du carburant sur la conduite d'alimentation (la rampe) doit être de 3 bars et l'aiguille de l'injecteur doit être actionnée pendant 30 ou 60 secondes avec un rapport cyclique de 100 %. Après 30 secondes d'activation des injecteurs, les données suivantes ont pu être saisies :
Type 1 : 120 ml
Type 2 : 200 ml
Type 3 : 250 ml
Un seul type d’injecteur sera utilisé. La taille de l'injecteur est déterminée à l'aide de la formule ci-dessous :

La taille des injecteurs est déterminée sur la base de la puissance effective (Pe) délivrée à une certaine vitesse, de la consommation de carburant spécifique au freinage (BSFC), du nombre d'injecteurs (n injecteurs) et du cycle de service maximal avec lequel les injecteurs sont contrôlés. Le tout est multiplié par 10.5 pour passer de livres par heure (lb/hr) à ml/min.
La réponse au calcul indique quel injecteur est adapté à cette configuration moteur. Ce n'est pas un problème s'il y a un écart inférieur à 20 ml par rapport à la valeur calculée. Cette différence est compensée par un ajustement du logiciel dans le MegaSquirt. Le tableau suivant donne un aperçu des données utilisées dans les formules :
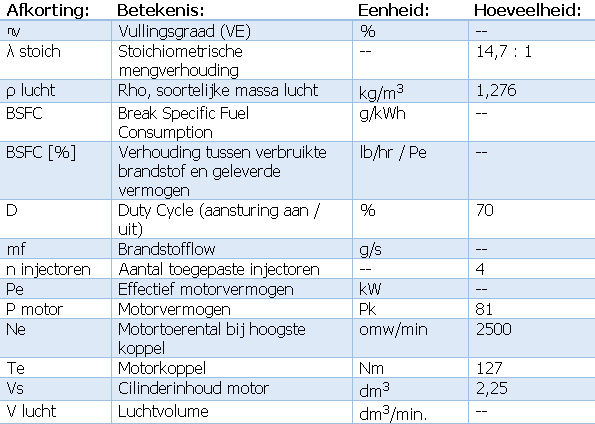
La première étape consiste à déterminer le carburant injecté au régime de couple. Une certaine quantité d'air est aspirée tous les deux tours du vilebrequin. Le degré de remplissage est le plus élevé à la vitesse de couple. En raison des propriétés du moteur (y compris le chevauchement des soupapes), le moteur se remplit mieux à ce régime et le rendement est le plus élevé. On estime que le taux de remplissage sera d'environ 70 %. La Formule 4 calcule le volume d'air présent dans le moteur à ce moment-là.
Dans la formule 5, la quantité de carburant injectée est calculée en fonction du volume d'air présent. La puissance moteur atteinte au régime de couple est calculée dans la formule 6. Le rapport entre la quantité de carburant injectée et la puissance indique le BSFC dans les formules 7 et 8.
Le BSFC réel est multiplié par 6 dans la formule 3600 pour être converti en kWh. Le BSFC d'un moteur essence est souvent compris entre 250 et 345 g/kWh. Plus la valeur est faible, plus le moteur est efficace. La formule 8 indique la relation entre le débit de carburant en livres/heure et la puissance effective du moteur. Ce pourcentage est inclus dans la formule 9.



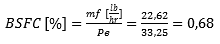

La réponse à la formule 9 a clairement indiqué que les injecteurs avec un débit de 200 ml/min sont adaptés à une utilisation dans le moteur. La différence de 7 ml est négligeable car elle est compensée dans le logiciel lors du remplissage du tableau VE.
Installation des injecteurs dans le collecteur d'admission :
Le système d'injection à commande électronique permet de retirer le carburateur, qui fait partie de la configuration classique. Le carburateur est donc remplacé par un corps de papillon (pour l'alimentation en air) et quatre injecteurs de carburant séparés. Le collecteur d'admission a été conservé et modifié pour permettre la conversion vers le système de gestion moteur. L'injection de carburant a lieu dans le collecteur d'admission. La décision a été prise de monter les injecteurs le plus près possible de la soupape d'admission. Dans la plupart des cas, les constructeurs de moteurs automobiles choisissent de monter la soupape d'admission en biais dans le collecteur d'admission. Le carburant est projeté contre la soupape d'admission. Cependant, pour le projet actuel, une configuration a été choisie dans laquelle les injecteurs sont placés à un angle de 45 degrés par rapport aux conduits d'air du collecteur.
Le collecteur d'admission est en fonte d'aluminium. Il a été décidé de fixer des bagues en aluminium au collecteur. L'usinage manuel à une bonne taille n'était pas une option, car les douilles devaient avoir des dimensions différentes de celles d'une taille de foret standard. Cela signifiait que la sous-traitance des fourgons devait être confiée à une entreprise disposant de l'équipement approprié. Les bagues pourraient ensuite être fixées au collecteur par soudage TIG. Le choix de monter les injecteurs à la verticale plutôt qu'en angle a été fait pour la raison suivante :
- Le processus d’assemblage : Il est plus facile d’installer les fourgons dans une disposition droite et horizontale. Le soudage des fourgons au collecteur est plus facile car il est désormais plus facile de souder tout autour que dans la situation où le fourgon est incliné.
- Post-traitement : Pendant le soudage, les douilles deviennent un peu ovales. La déformation est causée par la chaleur dégagée lors du processus de soudage. Ceci a été pris en compte en rendant le diamètre intérieur des bagues plus petit que le diamètre extérieur des injecteurs. La finition (alésage) est moins risquée : lorsque les manchons ont été arrondis vers l'intérieur, le diamètre est optimal pour les injecteurs, et l'étanchéité par les joints toriques est garantie. La hauteur des fourgons est importante ; l'injecteur ne doit pas être placé trop loin dans le collecteur. L'extrémité de l'injecteur ne doit pas obstruer le flux d'air. D'après les informations de la source : (Banish, Engine Management, advanced tuning, 2007), il a été décidé de monter les injecteurs si profondément dans le collecteur que les extrémités se trouvent exactement dans les trous du collecteur ; le flux d'air n'est pas entravé.
- Injection de carburant : étant donné que le mélange du brouillard de carburant avec l'air est optimal avant l'ouverture de la soupape d'admission, peu importe que l'injecteur injecte exactement au niveau de la soupape d'admission ou juste avant dans le collecteur d'admission.
En cas d'injection simultanée, l'injection a lieu à chaque rotation du vilebrequin (360°). Les quatre injecteurs injectent simultanément. Cela signifie que le carburant est également injecté dans le conduit d'admission lorsque la soupape d'admission n'est pas ouverte. Quelque temps plus tard, la soupape d'admission s'ouvre et le carburant pénètre toujours dans le cylindre.
Les buissons sont spécialement découpés sur mesure sur un tour. Le diamètre intérieur est légèrement plus petit que le diamètre extérieur de l'injecteur ; Étant donné que la déformation se produit pendant le processus de soudage, il doit être possible d'enlever de la matière pendant le post-traitement au moyen d'un alésage. Cela signifie que le diamètre augmente légèrement car le matériau est broyé. Le diamètre ne doit pas être trop grand, car il se peut alors que le joint torique en caoutchouc de l'injecteur ne soit plus suffisamment étanche. Une bonne étanchéité est très importante ; Une fuite d'air au-delà de l'injecteur entraîne une dépression plus faible dans le collecteur d'admission.
La dépression mesurée ne correspond alors plus à la dépression calculée. Cela affecte l'injection, qui est déterminée sur la base du tableau VE. La pression négative joue à cet égard un rôle majeur. Les fonctionnalités et paramètres de la table VE sont décrits dans un chapitre suivant.
Un bord biseauté a été limé au bas des bagues afin que les formes correspondent à celles du collecteur d'admission. Le fourgon doit alors être le plus droit possible. L'image ci-dessous montre le collecteur d'admission avec un bidon pendant le processus d'assemblage. Le manchon est collé sur un côté, de sorte que l'on puisse clairement voir l'impact du soudage sur le matériau. Il n’était pas clair si l’aluminium du collecteur contenait trop de contamination, ce qui rendrait le soudage difficile. Cela s'est avéré bien. Pour éviter que les bagues ne bougent de leur position pendant le soudage, des trous ont été percés à l'avance dans le collecteur et les bagues ont été maintenues dans la position correcte à l'aide d'un gabarit spécialement conçu sur mesure. De cette façon, les quatre bagues sont soudées tout autour. Un dernier contrôle a montré que les connexions entre les bagues et le collecteur étaient étanches.
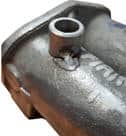
La connexion entre les injecteurs est normalement constituée par une rampe d'injecteur solide. Ce tuyau avec raccords, souvent en alliage d'aluminium, est réalisé sur mesure par un fabricant. Le moteur Land Rover utilisé pour le projet comporte deux injecteurs côte à côte, mais l'espace entre les paires d'injecteurs est assez grand. Les dimensions de la rampe d'injection et l'espace entre les conduits d'air du collecteur d'admission ne correspondaient pas. Le rail a donc dû être ajusté.
Raccourcir certaines pièces et allonger d’autres pièces par soudure est très difficile ; la contamination par le vieux carburant, très difficile à éliminer de l'intérieur du rail, peut provoquer une détérioration de l'adhérence. Puisqu'il s'agit de carburant, la méthode la plus sûre a été choisie ; les pièces sur lesquelles sont fixés les injecteurs sont reliées par un tuyau de carburant de haute qualité. Des bords cousus ont été installés à toutes les extrémités et des colliers de serrage robustes ont été utilisés pour empêcher les tuyaux de glisser sur les bords cousus.
L'image ci-dessous montre le collecteur d'admission au moment de l'usinage. La conduite d'alimentation (marquée numéro 1) est connectée à la sortie de la pompe à carburant. Le carburant est amené à l'entrée des quatre injecteurs sous une pression de 3 bars. Le régulateur de pression (3) régule la pression en fonction de la pression du collecteur d'admission, car la différence de pression entre la pression du carburant et la dépression dans le collecteur d'admission doit rester de 3 bars. Le carburant retourne au réservoir via la conduite de retour (2). Il y a une circulation continue de carburant. L'injection n'a lieu que lorsque les injecteurs sont contrôlés par le calculateur MegaSquirt.
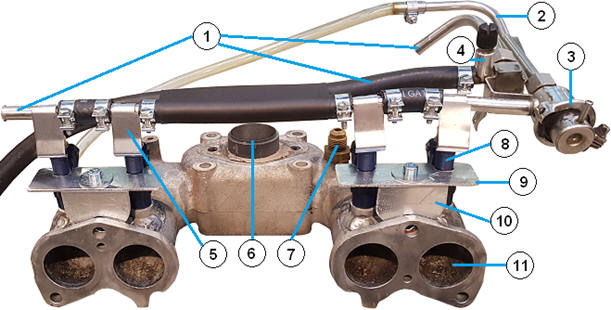
- ligne d'alimentation
- La ligne de retour
- Régulateur de pression
- Controle de la pression
- bouclier thermique
- Raccordement de la vanne à gaz
- Raccordement à pression négative
- Cylindre d'injecteur 1
- Support d'injecteur A
- Support d'injecteur B
- Cylindre de conduit d'admission 1
Dans les voitures particulières existantes, le rail d'injecteur est fixé au collecteur d'admission à l'aide de colliers ou d'œillets. Le rail d'injecteur serre les injecteurs dans le collecteur. Étant donné qu'un tuyau de carburant flexible a été choisi comme rampe d'injection pour ce projet, ce qui précède n'est pas possible. Il a donc été décidé de fixer les injecteurs dans le collecteur d'admission avec un support sur mesure. Les supports se composent de deux parties : la partie supérieure (support A) et la partie inférieure (support B).
Le support A contient deux encoches qui peuvent être glissées sur les injecteurs. Cela permet aux injecteurs d'être enfoncés dans le collecteur au moyen des côtés plats. Les deux supports A sont dotés de trous oblongs afin que la distance entre les injecteurs et les trous oblongs puisse être ajustée. Les supports A et B sont vissés ensemble : le support B est fixé au même goujon qui fixe le collecteur au moteur. Un trou oblong permet d'ajuster le support dans le sens vertical. Plus le support est déplacé vers le bas, plus l'injecteur est fermement serré.
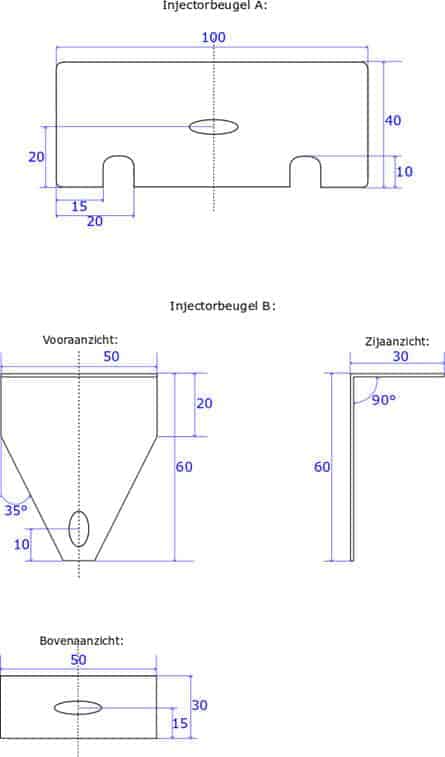
Allumage:
L'allumage conventionnel a été remplacé par un système d'allumage à commande électronique avec une bobine d'allumage contrôlée par le MegaSquirt. Pour que le moteur fonctionne pleinement avec les techniques d'origine, il faut d'abord connecter le système conventionnel avec points de contact. Ce n'est qu'après quelques heures de fonctionnement que l'on peut déterminer que le moteur fonctionne correctement, après quoi l'installation et le réglage, entre autres, de l'allumage à commande électronique peuvent commencer.
Préparation avec l'allumage classique:
Le moteur Land Rover était à l'origine équipé d'un système d'allumage avec points de contact, désormais également appelé système d'allumage conventionnel. L'image montre ce type de système d'allumage.
Avec des points de contact fermés, l'accumulation du courant primaire commence. Le courant est limité à 3 à 4 ampères par la résistance de l'enroulement primaire. Lorsqu’un courant traverse la bobine primaire de la bobine d’allumage, un champ magnétique se crée. Les bobines primaire (3) et secondaire (4) sont toutes deux dans ce champ magnétique. Lorsque le courant traversant les points de contact (10) est interrompu par la came du disjoncteur (9) sur l'arbre du distributeur, une tension est induite dans les deux bobines. Environ 250 volts sont produits dans la bobine primaire. La différence entre les enroulements créera une tension d'induction de 10 à 15 kV dans la bobine secondaire. L'étincelle de la bougie d'allumage est créée lorsque les pointes sont ouvertes.
La tension d'induction peut être limitée en permettant au courant primaire de circuler pendant un certain temps après l'ouverture des points de contact. Ceci est réalisé grâce à un condensateur connecté en parallèle entre les points de contact. Le condensateur est un élément déterminant le temps qui, en fonction de la capacité, ajuste réellement le niveau de la tension d'induction. Les points de contact sont également empêchés de brûler.
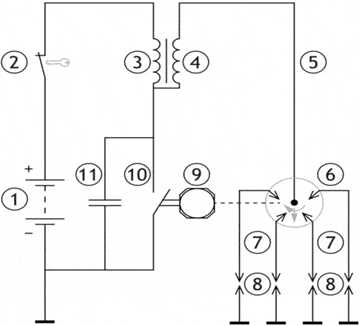
Bobine d'allumage pour le système de gestion moteur :
Le système de gestion du moteur contrôlera la bobine d’allumage. La bobine d'allumage classique avec distributeur reste sur le moteur pour servir de dispositif de test, mais ne fait plus partie du fonctionnement du moteur thermique. Un système d'allumage sans distributeur (bobine d'allumage DIS) a été choisi, vaguement traduit par : « système d'allumage sans distributeur ». Ce type de système d'allumage n'utilise pas de distributeur. Une autre option consistait à choisir une bobine d'allumage à bobine sur bougie (COP). Une bobine d'allumage séparée est connectée à chaque bougie d'allumage. Une bobine d'allumage COP est également appelée bobine d'allumage à broches. L'inconvénient d'une bobine d'allumage COP est que la dissipation thermique est moins bonne que celle d'une bobine d'allumage DIS. Lors de l'utilisation de bobines d'allumage COP, un signal provenant d'un capteur d'arbre à cames est également requis, qui n'est pas présent sur le moteur actuel.
La dent manquante dans la poulie de vilebrequin sert de point de référence par lequel le calage de l'allumage est déterminé. Avec la bobine d'allumage DIS, deux bougies d'allumage seront activées simultanément au moment de l'allumage. La bobine d'allumage DIS est en fait une unité dans laquelle sont montées deux bobines d'allumage. Lorsque les pistons des cylindres 1 et 4 montent, l’un sera occupé par la course de compression et l’autre par la course d’échappement. Pourtant, les deux bougies génèrent une étincelle. L'étincelle créée par le cylindre engagé dans la course de compression provoquera un mélange inflammable. L’autre étincelle, appelée « étincelle perdue », se produit lorsque les gaz d’échappement quittent la chambre de combustion. L’étincelle perdue est une étincelle qui se forme lorsqu’aucun mélange n’est enflammé. L'énergie d'inflammation est faible ; malgré l'étincelle, il y a peu de perte d'énergie. Ce n’est pas non plus nocif.
La figure montre le schéma de fonctionnement d'un moteur essence quatre cylindres avec une bobine d'allumage DIS. Ce diagramme de travail montre deux marques d'allumage par moment d'allumage ; L’un d’eux génère l’étincelle qui enflamme le mélange, l’autre est l’étincelle gaspillée. Une bobine d'allumage DIS peut être contrôlée par le MegaSquirt avec seulement deux impulsions.
Lorsque la course de compression a lieu dans le cylindre 1 et la course d'échappement dans le cylindre 4, le MegaSquirt contrôle la bobine primaire A via la broche 36 sur DB37 (voir image ci-dessous). Ce contrôle s'effectue en fonction du point de référence vilebrequin (entre 90 et 120 degrés avant PMH). Le MegaSquirt contrôle la bobine primaire B, qui est responsable de la formation d'étincelles des cylindres 2 et 3, et est allumée à 180 degrés après la bobine A. Il n'y a pas de point de référence pour la bobine B, mais le calage de l'allumage peut être déterminé simplement en comptant les dents de la roue d'impulsions 36-1.
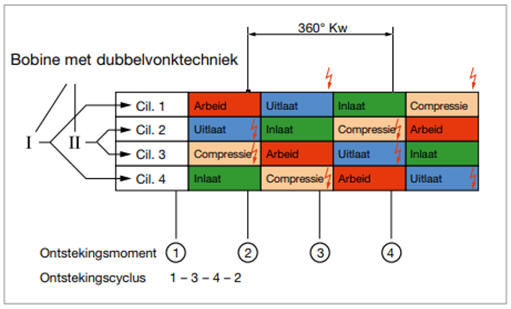
Une résistance de 7 ohms est affichée entre la bobine A de la bobine d'allumage et la broche 330 du processeur. Cette résistance limite le courant et la tension d'induction de l'impulsion motrice. Cette résistance n'étant pas standard sur le circuit imprimé MegaSquirt, elle doit être installée ultérieurement. À gauche de la ligne pointillée verticale dans l'image ci-dessous, les circuits internes du MegaSquirt sont affichés. Les composants représentés (les deux résistances de 330 Ohm et les LED) ont ensuite dû être soudés au circuit imprimé.
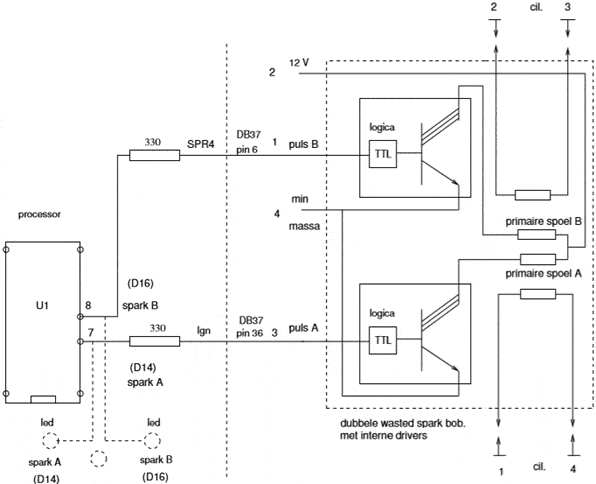
Accumulation de courant dans la bobine primaire :
Il est important d’avoir un aperçu de l’accumulation de courant dans la bobine primaire. Cela permet de déterminer non seulement l'ampérage, mais aussi le temps de charge de la bobine d'allumage. Le temps de chargement dépend d'un certain nombre de facteurs que MegaSquirt doit prendre en compte.
Le coefficient d'auto-induction (valeur L) de la bobine d'allumage sélectionnée est de 3,7 mH. Avec la résistance ohmique R, le courant primaire maximum et le temps de montée de la courbe sont déterminés. Une petite valeur L et une résistance garantissent que le courant augmente rapidement après la mise sous tension. Les données connues de la bobine d'allumage peuvent être utilisées pour calculer la manière dont le courant primaire est créé.
La formule suivante montre la solution générale de l'équation différentielle du 1er ordre, qui calcule les courants, les temps de charge et de décharge pour montrer le phénomène de commutation sous forme de courbe.
L'équation est :

où la constante de temps (Tau) est calculée comme suit :

Le courant maximum serait de 28 ampères selon la loi d'Ohm :
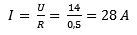
En réalité, cet ampérage ne sera pas atteint.
La bobine est éteinte plus tôt. La raison est expliquée plus tard. La saisie de ces informations dans la formule générale donne :
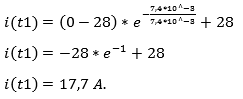
La figure montre la courbe de charge de la bobine primaire. Du temps T0 à 1 Tau, la bobine est chargée à 63,2%. Il s'agit d'un pourcentage fixe pour le temps de charge d'une bobine. Le résultat de la formule 13 montre que la bobine est chargée de 1 ampères à 17,7 Tau. A t = 5 Tau, la valeur finale est pratiquement atteinte.
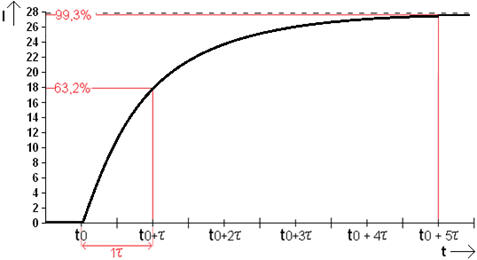
Selon les spécifications de la bobine d'allumage, le courant primaire de la bobine d'allumage après charge est de 7,5 A. Le courant n'augmente pas. Le temps nécessaire pour atteindre 7,5 A est appelé temps de maintien. Le temps de maintien dépend de la tension de la batterie, qui est dans ce cas de 14 volts. Si le processus de charge n'est pas ajusté, le courant traversant la bobine est au maximum de 12 ampères selon la formule 28.
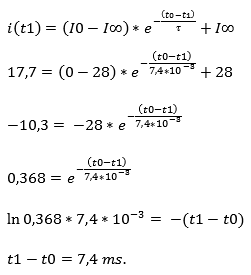
La bobine selon la formule 14 est chargée à 7,4 A à t = 17,7 ms. Le temps de charge réel est plus court, car la bobine est chargée jusqu'à un maximum de 7,5 A. Le temps requis peut être calculé en entrant les données connues dans la formule 15.
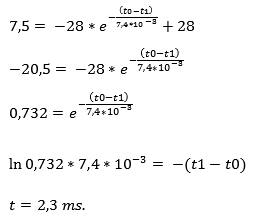
L'accumulation de courant primaire est arrêtée à 7,5 A. Cela évite que la bobine d'allumage ne chauffe excessivement et inutilement. Le plus important est que la bobine soit chargée de manière optimale, autant que possible, dans les plus brefs délais. La figure montre la courbe de charge jusqu'à t = 2,3 ms.
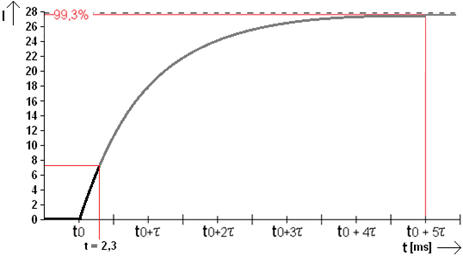
Lorsque la tension de la batterie chute, par exemple lors du démarrage du moteur, cela affecte le temps de maintien. Il faut alors plus de 2,3 ms avant que 7,5 A soit atteint. Le nouveau temps de chargement est déterminé à l'aide de la formule désormais bien connue. Le courant maximum est déterminé en fonction de la tension de la batterie :
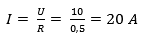
Le temps de charge jusqu'à 7,5 A avec un maximum de 20 A est calculé selon la formule 17 :
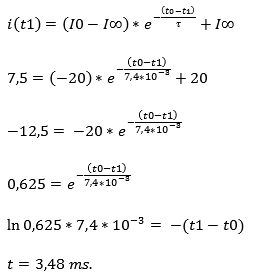
Sur la figure, le temps de charge à 14 volts est indiqué par la ligne noire et le temps de charge à 10 volts est indiqué par la ligne verte. Les lignes tombent à 0 en même temps ; c'est le calage de l'allumage. Étant donné qu'une tension de batterie inférieure nécessite plus de temps pour charger la bobine principale, le MegaSquirt doit allumer l'alimentation principale plus tôt.
Les lignes noires (montantes et descendantes) indiquent le temps de maintien à une tension de batterie de 14 volts. La ligne verte indique le temps de charge avancé à une tension inférieure : cela donne Δt. Le temps de charge réel est dans ce cas Δt + 100 %.
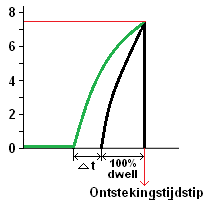
Ceci sera clarifié plus loin dans cette section avec un exemple et la figure 36. Le temps de charge est prolongé et le calage de l'allumage reste le même. Si cela ne se produit pas ou pas suffisamment, cela aura des conséquences sur l’énergie libérée lors de l’allumage. Dans ce cas, le courant primaire est coupé trop tôt, de sorte que le courant de 7,5 A n'est pas atteint. L'allongement du temps de charge de la bobine primaire (temps de maintien) est sous forme de formule fonction de la tension de la batterie. Le calcul du temps de séjour à différentes tensions donne un courant maximum différent dans la bobine.
En supposant que la tension de la batterie peut descendre jusqu'à 6 volts au démarrage et remonter jusqu'à 14,7 volts pendant la charge, une courbe peut être tracée en calculant un certain nombre de valeurs intermédiaires. L'image ci-dessous montre la correction du temps de séjour pour la bobine d'allumage DIS utilisée. Un point (rouge) est placé sur le graphique pour chaque augmentation de 2 volts. Étant donné qu'un temps d'arrêt préalablement saisi de 2,3 ms à une tension de 14 volts a été saisi dans le programme TunerStudio, un facteur de correction est formé à partir de cette tension. Une tension de 14 volts vaut donc 100% (pas de correction).
Il est désormais clair que le temps de charge augmente jusqu'à 315 % avec une tension de batterie de 6 volts.
La tension de la batterie peut chuter jusqu'à 6 volts dans des conditions défavorables. Cela signifie un affaiblissement de l'étincelle d'allumage. L'allongement du temps de maintien (le temps pendant lequel le courant primaire circule) compense cela, de sorte qu'une énergie d'allumage suffisante soit obtenue même à cette basse tension. Cela signifie que Δt de la figure 36 est triplé (2,3 ms * 315 % = 7,26 ms) par rapport au temps de séjour de 100 % (2,3 ms) indiqué en noir.
Les coefficients indiqués en rouge dans l'image ci-dessus peuvent être copiés directement dans le programme TunerStudio.
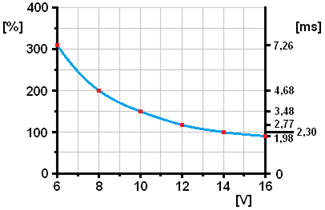
Quelque temps après la décharge de la bobine primaire, la préparation pour le prochain allumage commence. Plus le régime moteur est élevé, plus la bobine se recharge rapidement. La figure 37 montre deux courbes où le courant primaire augmente jusqu'à 8,85 A. Le calage de l'allumage se situe au point où la ligne chute à 0 A.
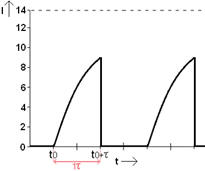
Détermination du calage de l'allumage :
Le signal d'allumage est déterminé à partir du point de référence du vilebrequin.
Dans la couronne dentée de la poulie de vilebrequin, 36 dent sur 1 a été fraisée à 100 degrés devant le point mort haut du piston du cylindre 1. Entre 100 et 0 degrés, donc pendant la course de compression, le microprocesseur de le MegaSquirt peut déterminer le calage de l'allumage. . Celui-ci tient compte de l'avance.
L'image montre l'image de l'oscilloscope à deux canaux dans laquelle l'image supérieure montre le point de référence du vilebrequin et l'image inférieure montre le signal de commande du MegaSquirt à la bobine d'allumage DIS. Le signal de commande a une tension de 5 volts (un 1 logique) et dure environ 1,5 ms.
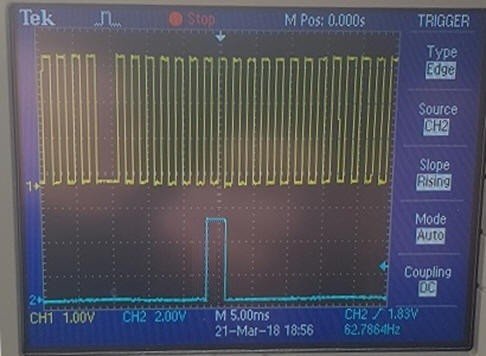
Avance à l'allumage :
Les capteurs de cliquetis ne sont pas utilisés dans ce projet. Il est possible de traiter les informations provenant des capteurs de cliquetis, mais la simple installation d'un capteur de cliquetis n'est pas suffisante. Le traitement des signaux est complexe. Le signal de détonation doit d’abord être converti en un signal oui/non ou en un signal analogique indiquant la force de la détonation.
La conversion des vibrations du moteur en signal de cognement se fait par un circuit d'interface. Ce circuit n'est pas présent dans le MegaSquirt II. C'est pourquoi il a été décidé de régler en toute sécurité l'avance à pleine charge et à charge partielle, afin que le moteur ne puisse pas se retrouver dans la zone de cognement. La courbe d'avance à pleine charge à régler doit être déterminée dans les limites de détonation. Les données d'avance centrifuge et sous vide de l'allumage conventionnel sont déterminées sur la base des données d'usine du manuel du moteur. Les points peuvent être tracés sur un graphique (exemple dans l'image ci-dessous).
La ligne rose indique l’avance mécanique originale. Ceci est en partie linéaire en raison de la construction mécanique des poids centrifuges. La ligne noire montre le contrôle de carte dans MegaSquirt ; cette ligne suit une courbe. Il est important de rester en dehors des zones de cognement à charge partielle et à pleine charge ; par conséquent, le contrôle cartographique est limité à charge partielle (ligne rouge) et l'avance à pleine charge n'augmente pas plus que dans la situation avec avance mécanique (ligne rouge). La disposition réelle de la carte suit la ligne bleue.
Tout d'abord, la courbe d'avance à pleine charge devait être inscrite dans le tableau d'avance à l'allumage. À des vitesses plus élevées et des charges plus faibles, une plus grande avance sera nécessaire. A charge partielle, l’avance s’ajoute à l’avance à pleine charge. Le tableau d'avance à l'allumage complété ainsi que les réglages d'avance moteur froid sont présentés page 7.
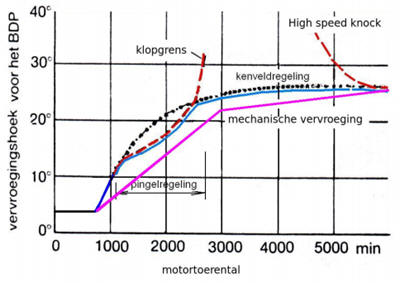
Corps de papillon :
L'alimentation air/carburant était contrôlée par le carburateur dans son état d'origine. Pour le système de gestion moteur, le carburateur est remplacé par un corps de papillon et quatre injecteurs montés dans le collecteur d'admission. Cela permet une injection plus précise et contrôlée qu'avec le carburateur, où un mélange air/carburant est formé au centre du collecteur et est divisé en quatre canaux. L'accélérateur est ouvert par un câble Bowden qui est actionné manuellement depuis le tableau de bord.
Après tout, le MegaSquirt II ne prend pas en charge un corps de papillon à commande électronique. C'est pourquoi la commande par câble Bowden est la seule option à utiliser.
La position du papillon est transmise au MegaSquirt au moyen d'une tension. L'amplitude de la tension dépend de l'angle d'ouverture du papillon des gaz. Le capteur de position du papillon est un potentiomètre avec une tension d'alimentation de 5 volts (voir image). La connexion 3 et une connexion à la terre 1 sont nécessaires. Le curseur (broche 2) prend une position sur la résistance qui dépend de la position du papillon. Le coureur est donc relié au papillon des gaz. Lorsque le coureur doit franchir une petite distance au-dessus de la résistance (le coureur pointe vers la gauche), la résistance est faible. Sur l'image, le coureur est positionné à droite (côté masse), ce qui signifie qu'il y a une résistance élevée et donc une faible tension de signal.
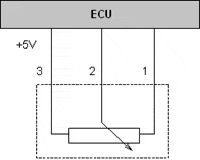
Avec le corps de papillon utilisé, il y a une tension de 600 mV sur le coureur lorsque le papillon est fermé et une tension de 3,9 V lorsque la vanne est complètement ouverte. L'ECU reçoit la tension et l'utilise pour calculer l'angle d'ouverture du papillon des gaz. Une augmentation rapide de l’angle d’ouverture signifie qu’une accélération se produit ; l'ECU répond à cela en enrichissant brièvement. C’est ce qu’on appelle l’enrichissement par accélération. Le capteur de position du papillon n'est pas utilisé pour déterminer l'enrichissement du mélange dans différentes conditions de fonctionnement ; Le capteur MAP est utilisé à cet effet.
Configuration de test du moteur pas à pas avec simulateur :
Une fois le MegaSquirt ajusté matériellement, le boîtier de dérivation pouvait être utilisé pour vérifier si la commande du moteur pas à pas était reçue. L'allumage de LED bicolores indique que le contrôle est en cours. Les étapes dans lesquelles le moteur pas à pas est contrôlé peuvent être suivies en observant le changement de couleurs. Les couleurs alternent entre le rouge et le jaune. Les données du moteur pas à pas peuvent être saisies dans le menu « Contrôle du ralenti » du programme TunerStudio. En plus du type (4 fils), le nombre de pas peut également être réglé. Cela inclut également la position de départ dans laquelle le moteur pas à pas doit se trouver lors du démarrage du moteur. De plus, le temps nécessaire pour ajuster une étape peut être réglé.
Le nombre d'étapes dépend, entre autres, de la température du liquide de refroidissement ; une température plus basse nécessite une plus grande ouverture du moteur pas à pas. Les pas relatifs à la température peuvent être paramétrés dans un graphique. Le simulateur peut être utilisé pour vérifier si le moteur pas à pas est réellement contrôlé correctement. Comme il est vérifié d'abord sur le simulateur plutôt que sur le moteur, les problèmes peuvent être évités lors du démarrage ou du fonctionnement du moteur en raison d'un éventuel problème matériel ou logiciel. Étant donné que la température du liquide de refroidissement et le régime moteur influencent principalement l'angle d'ouverture du moteur pas à pas, vous pouvez vérifier si la commande est correcte en tournant ces potentiomètres. Le compteur sur le tableau de bord de TunerStudio affichera l'ajustement du nombre d'étapes ajustées.
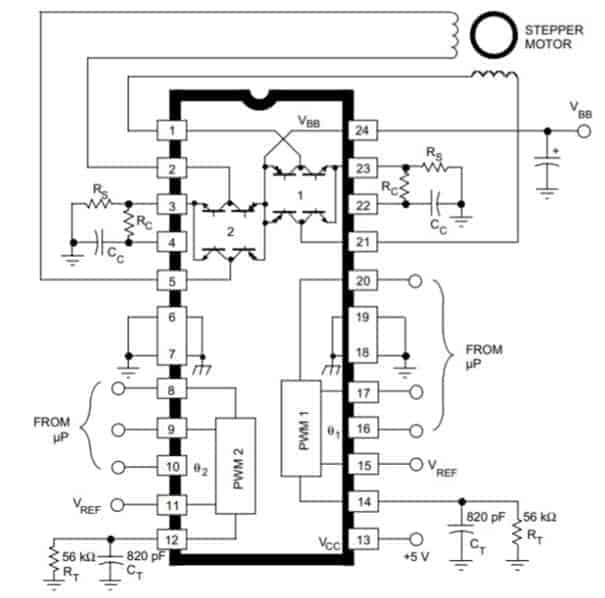
Paramètres du moteur pas à pas :
La figure montre l'écran de paramètres du moteur pas à pas utilisé pour le régime de ralenti (contrôle du ralenti).
Les étapes de réglage du moteur sont déterminées à l'avance à l'aide d'un Arduino. Le nombre de pas doit également être saisi pour se déplacer vers sa position de base (pas de référence). Le moteur pas à pas est actif en phase de préchauffage (algorithme) et alimente les bobines à l'arrêt (maintien du courant entre les étapes).
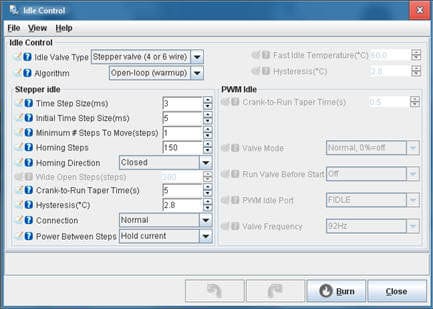
La position du moteur pas à pas dépend de la température du liquide de refroidissement. Lors du démarrage d'un moteur froid, la soupape doit être légèrement plus ouverte que lors du démarrage d'un moteur réchauffé. L'image ci-dessous montre l'écran de paramètres permettant de définir les étapes (Steps) en relation avec la température du liquide de refroidissement (Coolant). Lorsque le moteur est froid, le moteur pas à pas est complètement ouvert pendant que le moteur tourne au ralenti. Pendant la phase de préchauffage, le moteur pas à pas se ferme légèrement.
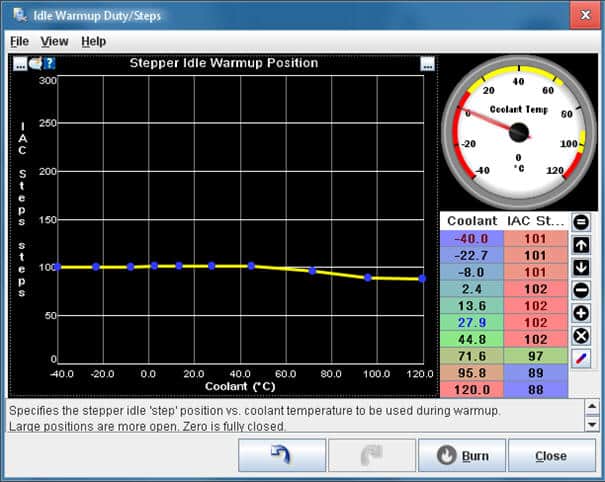
Il est également possible d'ajuster la position du moteur pas à pas en fonction de la température du liquide de refroidissement lors du démarrage du moteur. C'est ce qu'on appelle le « devoir/étapes de démarrage au ralenti ». L'image ci-dessous montre l'écran des paramètres.
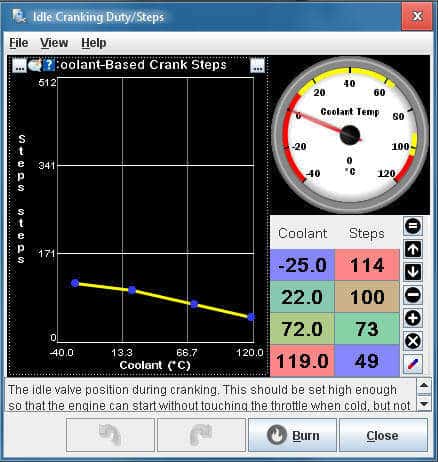
Circuit de pompe à essence :
Le MegaSquirt garantit que la pompe à carburant est allumée et éteinte. Le transistor Q19 dans la figure ci-dessous protège le transistor Q2 contre un courant excessif. Si le courant est trop élevé, le transistor peut griller. Lorsque le courant traversant la partie collecteur-émetteur de Q2 et R40 augmente, la tension de saturation à la base de Q19 est atteinte. Le transistor Q19 s'allume, provoquant une diminution de la tension base-émetteur en Q2.
La connexion FP-1 PTA0 est contrôlée en interne par le MegaSquirt. Un signal d'entrée provenant du capteur de position du vilebrequin (un capteur Hall ou un capteur inductif) est nécessaire pour contrôler le circuit à transistors. Si le signal est perdu, par exemple si le moteur cale involontairement, l'alimentation électrique de la pompe à carburant est immédiatement interrompue.
La sortie du circuit transistor (FP1 OUT) est connectée au relais de la pompe à carburant. La broche 85 du relais est la sortie du courant de commande. Avec un relais sous tension, la section d'alimentation principale (broches 30 et 87) est commutée, de sorte que la pompe à carburant reçoive une tension d'alimentation pour fonctionner.
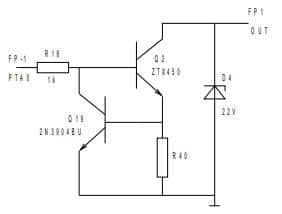
Une pompe à carburant électronique avec une pression de fonctionnement de 3 bars est utilisée. Le carburant est guidé à travers le filtre à carburant jusqu'à la rampe d'injection, où la pression est à l'entrée des injecteurs. L'injecteur injectera une quantité pré-calculée de carburant dans le collecteur d'admission lorsqu'un signal provient du MegaSquirt. Le contrôle du MegaSquirt détermine non seulement la quantité de carburant injectée, mais également la pression du carburant dans le rail.
À une pression de rail plus élevée, une plus grande quantité de carburant sera injectée avec le même contrôle. La pression de la rampe doit donc être ajustée en fonction de la dépression dans le collecteur d'admission. La différence de pression (∆P) doit toujours rester à 3 bars. La figure montre le schéma du système de carburant. Les lignes roses, jaunes, orange et noires montrent les connexions électriques. La ligne rouge indique l'alimentation en carburant et la ligne bleue le retour de carburant.
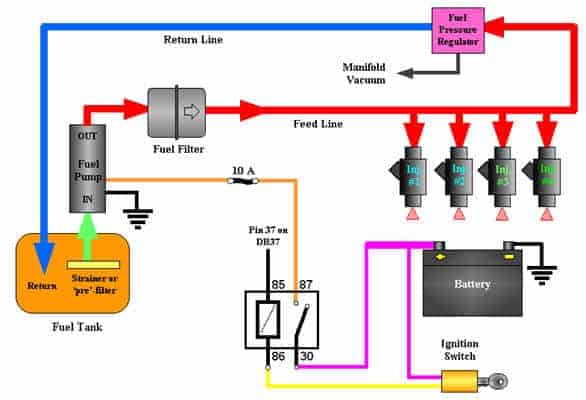
Réalisation des travaux mécaniques :
Les trois photos suivantes montrent le moteur dans les dernières étapes des modifications mécaniques.
Photo 1:
C'est le côté où la plupart des pièces appliquées sont visibles. Le tableau de bord des commandes et l'ECU MegaSquirt se trouvent également ici. Sous la photo se trouve une légende avec la description des numéros des pièces. Vous pouvez ouvrir les photos en plus grand en cliquant dessus.
- La soupape d'étranglement;
- Conduite de carburant pour les injecteurs ;
- Tube de raccordement pour papillon des gaz sur collecteur d'admission ;
- Manomètre de pression de carburant ;
- Collecteur d'admission et d'échappement ;
- Tableau de bord avec interrupteur du ventilateur de refroidissement, voyants de l'alternateur et de la pression d'huile, interrupteur d'allumage et interrupteur de terre ;
- Tuyau à dépression pour capteur MAP ;
- Sonde lambda ;
- Durites de carburant (arrivée et retour) réunies dans une boîte thermorétractable ;
- Unité pompe à carburant/réservoir ;
- Relais de pompe à carburant ;
- Mégagicler ;
- Silencieux d'échappement.
Photo 2:
Cette photo montre l'autre côté du moteur. Ici vous pouvez voir le carburateur (15) et l'allumage conventionnel (17). Le but de cet allumage classique est de faire étinceller les bougies d'allumage du montage d'essai (14). Cela n'a bien sûr aucune fonction pour le moteur, mais cela donne un aperçu du fonctionnement de l'allumage tel qu'il fonctionnait dans les voitures classiques.
Le numéro 20 indique le mécanisme de freinage de la transmission. La tige du tambour de frein peut être tendue à l'aide d'un câble Bowden, afin que l'arbre de sortie de la boîte de vitesses soit freiné. Le frein de transmission est appliqué pour charger brièvement le moteur lorsqu'un rapport est engagé.
14. Test de configuration de l'allumage du distributeur mécanique ;
15. Carburateur ;
16. Bobine d'allumage DIS ;
17. Allumage du distributeur mécanique avec avance à vide ;
18. Tableau de bord arrière ;
19. Pompe à carburant mécanique ;
20. Mécanisme de frein de transmission ;
21. Bobine d'allumage classique.
Photo 3:
La vue de dessus du moteur avec le dispositif de test pour l'allumage et la rampe d'injection est clairement visible ici.
Les réglages mécaniques sont terminés. Le moteur ne peut pas encore démarrer car certaines données doivent d'abord être saisies dans le MegaSquirt.
suivant: Réglage de l'ECU MegaSquirt II.