Thèmes:
- Préface
- Capteur de batterie intelligent
- Composants et principes de mesure du capteur de batterie
- Chargement et remplacement de la batterie
Préface:
Dans les véhicules modernes, l'état de charge de l'alternateur est adapté aux circonstances. L'alternateur est contrôlé depuis l'ECU du moteur et reçoit des signaux pour charger plus ou moins. L'alternateur génère de l'énergie lorsqu'un champ magnétique est créé entre le rotor et le stator. Plus le champ magnétique est grand, plus la force nécessaire pour faire tourner le rotor est importante. Générer une grande quantité de courant de charge coûte donc de l’énergie et du carburant.
- Le régime de ralenti peut être augmenté lorsque la batterie est presque vide lorsqu'il n'y a pas suffisamment de recharge possible ;
- Lors de l'accélération maximale, l'alternateur n'est temporairement pas piloté afin d'utiliser tout le couple généré pour la propulsion ;
- Lors de la décélération (freinage moteur), l'ECU contrôle l'alternateur au maximum, de sorte que l'énergie cinétique du véhicule soit utilisée pour générer de l'énergie dans l'alternateur. La figure montre l'indication de la charge maximale de la batterie (système 12 volts).
Le signal du capteur de batterie intelligent est utilisé pour déterminer l'état de charge de la batterie. C'est l'une des données les plus importantes pour déterminer dans quelle mesure l'alternateur doit être contrôlé.
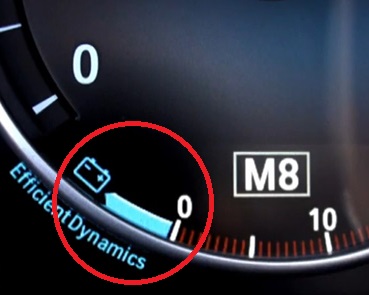
Capteur de batterie intelligent :
Les véhicules modernes sont presque tous équipés d'un capteur de batterie, souvent appelé IBS (Intelligent Battery Sensor), capteur de courant ou moniteur de batterie. Dans cet article, nous ferons référence au terme « capteur de batterie ». Le capteur de batterie fonctionne en étroite coopération avec le système de surveillance de la batterie (BMS) du véhicule. Cela est particulièrement vrai pour les véhicules équipés d'un système de démarrage et d'arrêt. Dans ces véhicules, la batterie est soumise à de fortes contraintes à plusieurs reprises, car le démarreur est activé plusieurs fois par trajet pour démarrer le moteur. C'est pourquoi une batterie AGM est souvent choisie dans ces véhicules au lieu d'une cellule au plomb traditionnelle. Une batterie AGM est plus résistante aux décharges et charges répétées.
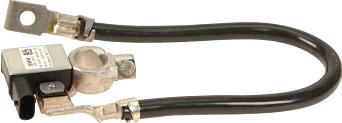
Le capteur de batterie est intégré au câble de masse, qui est fixé entre la borne négative de la batterie et un point de masse sur la carrosserie ou le châssis. Sur le capteur de batterie, vous trouverez une fiche avec deux fils ou plus. Un fil mène directement à la borne positive de la batterie et un deuxième fil sert à la communication.
À l'intérieur du boîtier du capteur de batterie se trouve un circuit imprimé avec un microprocesseur et un contrôleur qui mesure la tension, le courant, la température et le temps. Les données de cette unité de commande électronique (ECU) sont souvent transmises via un bus LIN à l'alternateur et à l'unité de commande de confort (BCM) ou à l'unité de commande du moteur. La passerelle est souvent située entre le capteur de batterie et le BCM ou l'unité de commande du moteur pour traduire le message du bus LIN en message de bus CAN. Ce point est abordé plus en détail dans la section « Diagnostic du capteur de batterie intelligent ».
Le capteur de batterie surveille l'état de la batterie et mesure les paramètres suivants :
- La tension de la batterie.
- Le courant avec lequel la batterie est chargée et déchargée.
- La température de la batterie.
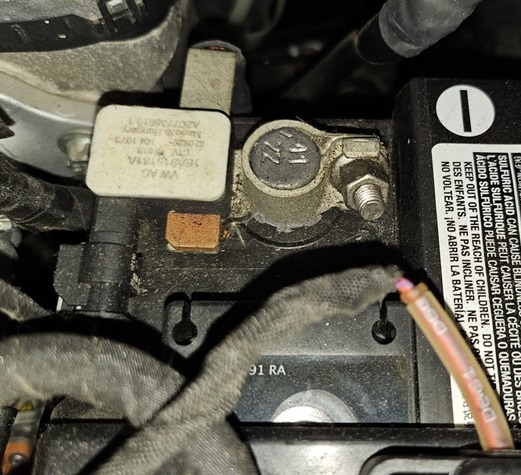
Le capteur de batterie envoie ces données à l'unité de commande du moteur ou BCM. À l'aide de ces données, l'ECU (Electronic Control Unit) calcule les éléments suivants :
État de charge (SOC) de la batterie. En mesurant le courant sortant vers les consommateurs et le courant entrant vers la batterie, il est possible de déterminer la quantité d'énergie encore disponible dans la batterie.
État (State Of Health, SOH) de la batterie. La tension de la batterie et le courant de décharge sont comparés pour évaluer la qualité de la batterie. Lors du démarrage, jusqu'à 60 A de courant peuvent être tirés de la batterie avec un petit moteur essence ou jusqu'à 120 A avec un moteur diesel plus lourd. La mesure dans laquelle la tension de la batterie chute indique le niveau de résistance interne de la batterie. Si la tension chute de 11,5 à 10 volts pour un courant de 60 A, cela est acceptable. Si la tension chute de 11,5 à 8 volts avec le même courant de démarrage, cela indique une résistance interne trop élevée dans la batterie et nécessite un remplacement.
Courant de repos à l'arrêt. Celui-ci détecte une perturbation du courant de repos, par exemple par un consommateur non autorisé. Le conducteur recevra une notification lors du prochain trajet si un courant de repos accru est détecté.
Composants et principes de mesure du capteur de batterie :
Le boîtier du capteur de batterie et la borne de terre sont souvent intégrés en un tout. Le câble de masse peut également former un tout avec le capteur de batterie ou être fixé à l'aide d'un raccord à vis. À l’intérieur du capteur de batterie se trouve une résistance shunt avec une valeur de résistance très faible. En mesurant la différence de tension aux bornes de ce shunt, le courant peut être calculé. En combinaison avec la tension de la batterie, il est possible de calculer la puissance avec laquelle la batterie est chargée ou déchargée.
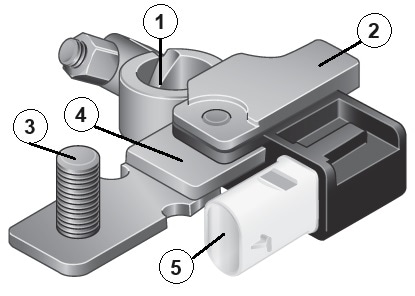
1. Poteau de masse de pince de poteau ;
2. Capteur de batterie ;
3. Connexion à la terre du véhicule ;
4.Shunt ;
5. Connexion enfichable pour bus B+ et LIN.
La résistance shunt est placée en série entre la connexion à la masse du véhicule et la borne négative de la batterie. Tout le courant entrant et sortant de la batterie passe par ce shunt. En raison de la faible valeur de résistance, peu de tension est consommée dans le shunt.
Le niveau de cette tension est converti en courant dans le microprocesseur, ainsi que la valeur connue de la résistance du shunt :
- Une chute de tension importante aux bornes du shunt indique un courant important.
- Une faible chute de tension indique un faible courant.
Dans l'image ci-jointe nous voyons un schéma dans lequel la résistance R représente le shunt et le courant I représente le courant de décharge lors de la décharge de la batterie. Le voltmètre, placé en parallèle aux bornes de la résistance shunt, illustre comment l'électronique de mesure du capteur de batterie mesure la différence de tension aux bornes de ce shunt.
L'image ci-dessous donne un aperçu des emplacements où les mesures de température, de tension et de courant ont lieu.
La résistance du shunt est indiquée par le numéro 5. La différence de tension (V) aux bornes du shunt est lue comme courant (A). Ces données sont envoyées via le bus LIN aux DME/DDE, qui sont les désignations du moteur essence (DME) et du moteur diesel (DDE) de BMW.
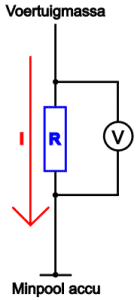
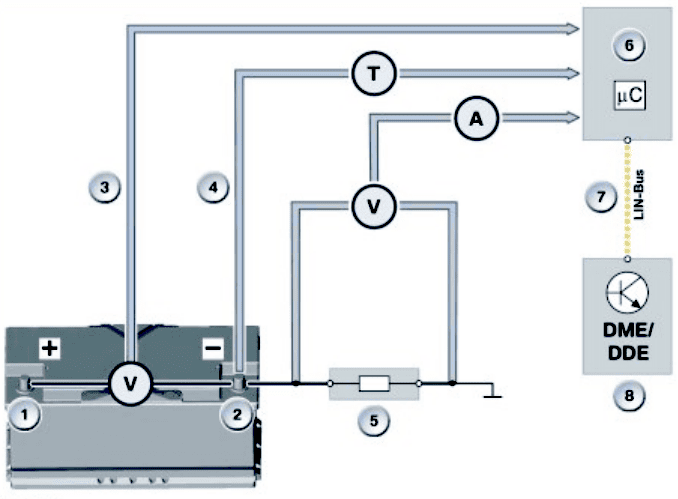
1. Pôle positif de la batterie ;
2. Borne de masse de la batterie ;
3. Mesurer la tension de la batterie ;
4. Mesure de la température de la batterie ;
5. Mesure du courant à l'aide d'une résistance shunt ;
6. Microprocesseur dans le capteur de batterie intelligent ;
7. Fil de communication du bus LIN
8. Unité de commande du moteur
Chargement et remplacement de la batterie :
Le système de gestion de la batterie utilise le capteur de batterie pour mesurer le courant circulant vers et depuis la batterie et stocke ces informations en mémoire. Lorsque la batterie doit être chargée ou si une aide au démarrage est utilisée, il est important que le chargeur de batterie ne soit pas connecté directement aux bornes de la batterie, mais aux points de charge. Le capteur de batterie est situé entre ces points de charge et les bornes de la batterie et ne peut mesurer le flux d'énergie que lorsque le chargeur de batterie est connecté aux points de charge. Si le chargeur de batterie est connecté directement aux bornes de la batterie, la mémoire du BMS indiquera que la batterie est (presque) vide, alors qu'en réalité elle est complètement chargée. L'alternateur surchargera alors la batterie, après quoi le système fonctionnera mal. Les images ci-dessous montrent un chargeur de batterie connecté directement à la batterie et aux points de recharge sous le capot.
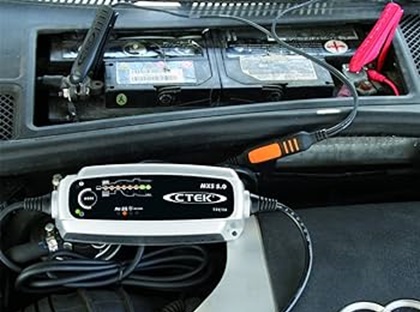
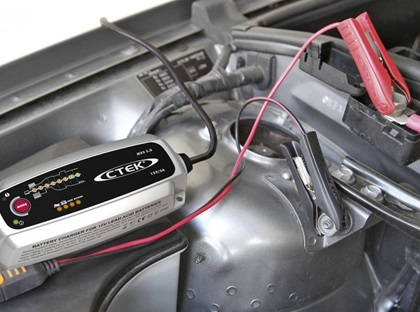
Après avoir remplacé la batterie, celle-ci doit être enregistrée sur un véhicule équipé d'un capteur de batterie. En atelier, cela est aussi appelé « apprentissage » ou « codage ». La gestion de la batterie prend en compte :
- vieillissement de la batterie. Le courant de charge d'une batterie plus ancienne avec une résistance interne accrue peut être augmenté ;
- la capacité et le courant de démarrage à froid de la batterie.
Lors de l'enregistrement, les valeurs stockées de la batterie qui se sont détériorées avec le temps sont supprimées. Ainsi, même si une batterie identique de la même marque, de même capacité et courant de démarrage à froid est installée, le remplacement doit être enregistré. Bien entendu, les données relatives à une batterie présentant des propriétés différentes doivent être connues. Cela peut être fait en saisissant manuellement la capacité [Ah] et le courant de démarrage à froid [A], ou en saisissant les numéros de pièce ou les numéros de série. Avec un équipement de diagnostic moderne, le code QR indiqué sur l'autocollant de la batterie peut être scanné.
Les captures d'écran ci-dessous montrent l'enregistrement d'une batterie avec un programme BMW (à gauche) et VCDS (à droite).
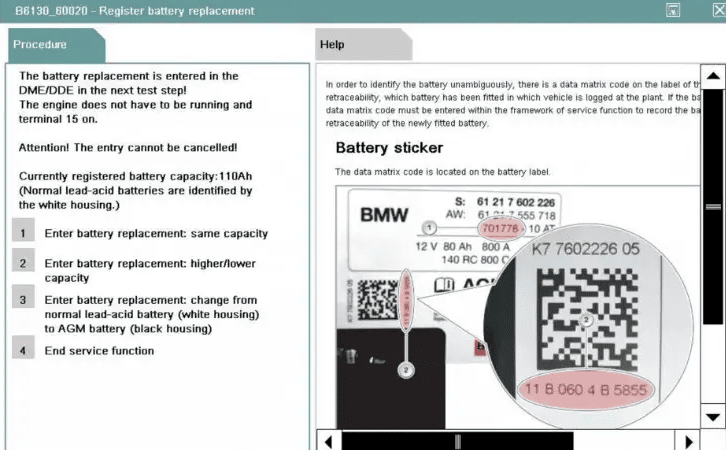
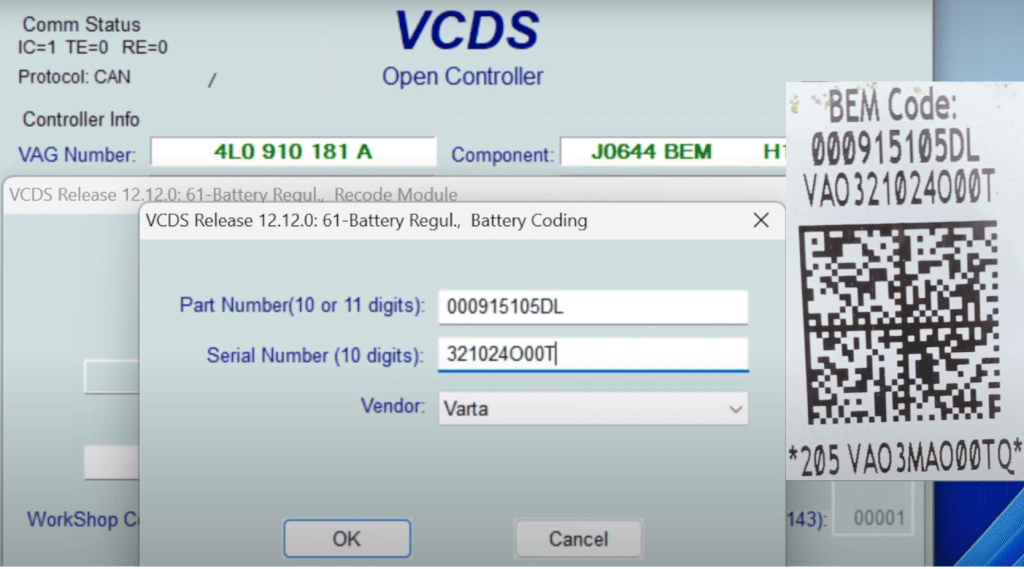
Diagnostic sur le capteur de batterie intelligent :
Le capteur de batterie intelligent communique avec l'alternateur et le BCM ou l'unité de commande du moteur. Cette section explique comment lire le schéma et comment établir un diagnostic.
Dans le schéma suivant, nous voyons le capteur de batterie (A85) qui est alimenté en tension d'alimentation de 2 volts par un fusible sur la broche 12. La broche 1 est destinée à la communication : à partir de là, un message est envoyé via le bus LIN à la passerelle (A25di) et à l'alternateur (O01). Les broches 1 et 2 sont situées dans la fiche à deux broches visible sur les images précédentes.
Les deux fils noirs du bas du capteur de batterie n'ont pas de numéro de broche : il s'agit d'une connexion directe à la borne négative de la batterie.
Le capteur de batterie intelligent envoie un message sur le bus LIN à la passerelle et à l'alternateur. La passerelle est la jonction entre des réseaux aux protocoles différents (tensions et débits). Dans la passerelle, le message du bus LIN est envoyé via le bus CAN au BCM et/ou au calculateur moteur. A l'inverse, l'un de ces deux organes de commande pilote l'alternateur via la passerelle et le bus LIN.
Un défaut dans la communication du bus LIN peut signifier que les données du capteur de batterie ne peuvent pas être utilisées ou que l'alternateur n'est pas correctement contrôlé. Dans ce dernier cas, l'alternateur passe à un programme d'urgence dans lequel la commande D+ conventionnelle est utilisée pour créer une tension et un courant de charge suffisants.
Le parcours tendu du Signal du bus LIN peut avec un oscilloscope sont mesurés pour l’évaluation.
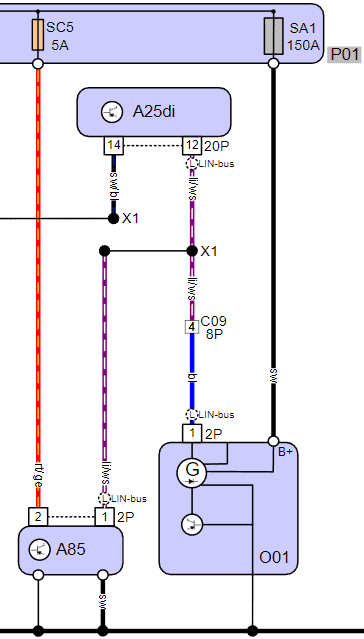
Légende:
P01: boîte à fusibles compartiment moteur
A25di: interface de diagnostic (passerelle)
A85: capteur de batterie du calculateur
O01: dynamo
Lorsqu'il y a un défaut et que la communication sur le bus LIN est OK, nous savons que la tension d'alimentation et la masse du capteur sont bonnes. Le défaut est provoqué par l'un des composants de ce schéma. Les mesures suivantes peuvent être prises :
- vérifier les mises à jour logicielles des dispositifs de contrôle ;
- Testez la batterie 12 volts (de préférence sous charge) ;
- vérifiez si les données correctes de la batterie ont été enregistrées. La batterie a peut-être été remplacée dans le passé, mais l'enregistrement n'a jamais été effectué ;
- réinitialiser les données du capteur de batterie ;
- vérifier que la référence de l'alternateur est correcte : un alternateur incorrect qui ne correspond pas au capteur finira par causer des problèmes ;
- Si ce qui précède a été vérifié et jugé correct, il peut être possible de conclure que le capteur de batterie est défectueux. Cela se produit parfois lors de démarrages fréquents (incorrects) via des câbles de démarrage ou un booster de batterie.
Pages connexes :