Thèmes:
- Injection indirecte et directe
- Contrôle de la pression du carburant avec injection indirecte
- Stratégie d'injection injection multipoint
- Injecteur électromagnétique (MPI)
- Injecteur piézo (DI)
- Stratégies d'injection injection directe
- Double injection
- Mesure des caractéristiques de tension et de courant sur un injecteur multipoint
- Calage de l'injection par rapport à la position du vilebrequin
- Limitation de courant du calculateur
- Détermination de la quantité de carburant requise
- Tableau VE
- Tableau AFR
Injection indirecte et directe :
Les types de systèmes d'injection d'un moteur à essence sont divisés en injection indirecte pour le papillon des gaz, injection indirecte par cylindre et injection directe haute pression. Les paragraphes de cette page expliquent ces différents systèmes d'injection.
Injection indirecte :
Il y a un injecteur devant le papillon des gaz. Le carburant est pulvérisé contre le papillon des gaz, où il se mélange à l'air qui passe. L’inconvénient majeur est qu’il n’y a pas de dosage précis de carburant par cylindre ; un cylindre reçoit toujours un peu plus ou moins que l'autre. Le système n'est donc pas réglable et n'est donc plus utilisé au regard des exigences environnementales. Ce système est aussi appelé injection centrale (Monopoint).
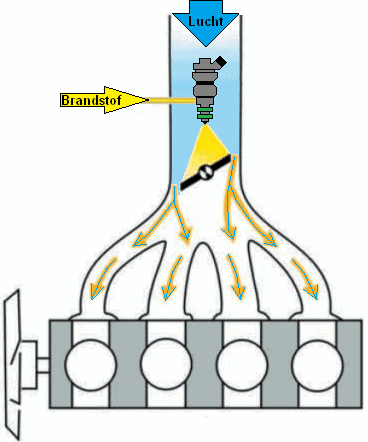
Injection indirecte :
Chaque cylindre possède son propre injecteur. L'injecteur injecte du carburant dans la soupape d'admission. L'air qui circule assure également le mélange dans ce système avant que le mélange air-carburant n'entre dans la chambre de combustion. L'avantage par rapport à l'injection indirecte est que la quantité de carburant peut être contrôlée avec beaucoup plus de précision. Ce système est également appelé MPI (MultiPoint Injection) ou PFI (Port Fuel Injection).
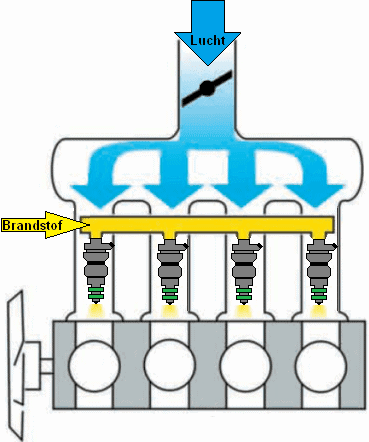
Injection directe:
Les injecteurs pour DI (Direct Injection) ou DISI (Direct Injection Spark Ignition) sont situés à côté de la bougie, en haut de la chambre de combustion. Le carburant est injecté par cet injecteur à une haute pression d'environ 200 bars pendant la course d'admission. Les principaux avantages de ce système sont que la quantité de carburant peut être réglée avec encore plus de précision, que les injections peuvent être effectuées plusieurs fois pendant la course d'admission et que le mélange air-carburant est plus frais. Cela permet aux constructeurs d’augmenter le taux de compression du moteur. L'injecteur peut être conçu comme un injecteur piézoélectrique ou à bobine magnétique.
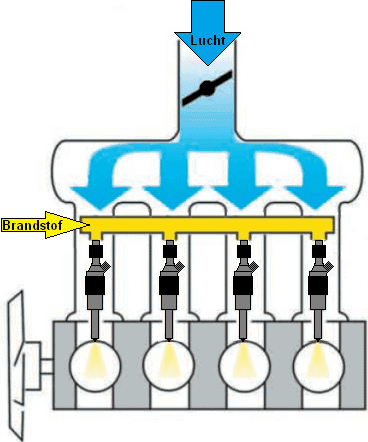
DI nécessite des pressions d'injection plus élevées que MPI/PFI, car l'injection a lieu pendant la course de compression ; le carburant doit être suffisamment atomisé pendant que l'air dans le cylindre est comprimé. C'est pourquoi DI dispose d'une pompe haute pression séparée. La pompe haute pression crée une pression de carburant dans la galerie de carburant. Les injecteurs sont fixés à cette galerie de carburant par des tuyaux. Dès que la gestion moteur envoie un signal à l'injecteur, celui-ci s'ouvrira et se fermera à l'heure souhaitée.
Les avantages du DI par rapport au PFI incluent :
- Injection plus précise ;
- Plusieurs injections possibles ;
- Le temps d'injection peut être ajusté ;
- Pression effective plus élevée possible au-dessus du piston (permettant ainsi une réduction de taille avec un taux de compression plus élevé) ;
- Consommation de carburant réduite, émissions de CO2 réduites.
Les inconvénients comprennent :
- Coûts du système plus élevés en raison d'une pompe à carburant haute pression, d'injecteurs avancés et d'une culasse plus complexe ;
- Les émissions de suie ont augmenté (émissions de particules) ;
- L'injection directe dans la chambre de combustion assure le refroidissement au lieu de la chaleur nécessaire à l'évaporation du carburant.
Un moteur à double injection profite des avantages des deux systèmes. L'injection directe et indirecte peut être commutée en fonction des conditions de fonctionnement. Le fonctionnement et l'application de la double injection sont décrits dans le paragraphe du même nom sur cette page.
Contrôle de la pression du carburant avec injection indirecte :
Une pression de carburant constante est une condition préalable au contrôle précis de l’injection de carburant. La pression du carburant (pression de la rampe) est en haut de l'injecteur et la pression du collecteur d'admission est en bas. La pression dans le collecteur d'admission varie en fonction de la charge du moteur et, sans régulateur de pression, influencera la différence de pression du carburant et donc la quantité injectée. C'est pour cette raison que nous utilisons un régulateur de pression de carburant. Dans cette section, nous approfondirons le fonctionnement et l’objectif de ce contrôleur.
L'image ci-dessous montre les composants d'un moteur essence à injection indirecte avec injection multipoint. Nous examinons le débit de carburant de la pompe dans le réservoir jusqu'à l'injecteur.
Lorsque l'ECU contrôle le relais de la pompe à carburant, la pompe fonctionne. La pompe aspire le carburant de la partie la plus basse possible du réservoir de carburant et force le flux de carburant vers le filtre à carburant. Les particules de saleté présentes dans le carburant restent dans le matériau filtrant. Le carburant filtré arrive ensuite dans la galerie à carburant. Dans la plupart des cas, la galerie de carburant est montée directement sur l'entrée de l'injecteur.
Il y a une pression constante dans la galerie de carburant : ce n'est que lorsque l'injecteur est commandé électriquement par l'ECU (voir le fil bleu) que l'injecteur s'ouvre et que le carburant est injecté dans le collecteur d'admission sur la soupape d'admission ouverte. La quantité de carburant injectée dépend :
- le temps d'injection (déterminé par le calculateur en allongeant ou en raccourcissant le signal d'injection) ;
- la pression du carburant (avec un temps d'injection de 2 millisecondes, l'injecteur injectera plus que ce que le calculateur a calculé si la pression du carburant est trop élevée).
La pression du carburant dans la galerie de carburant (également appelée pression du rail) est ajustée en fonction de la charge du moteur. Nous en discuterons plus en détail dans la section suivante.
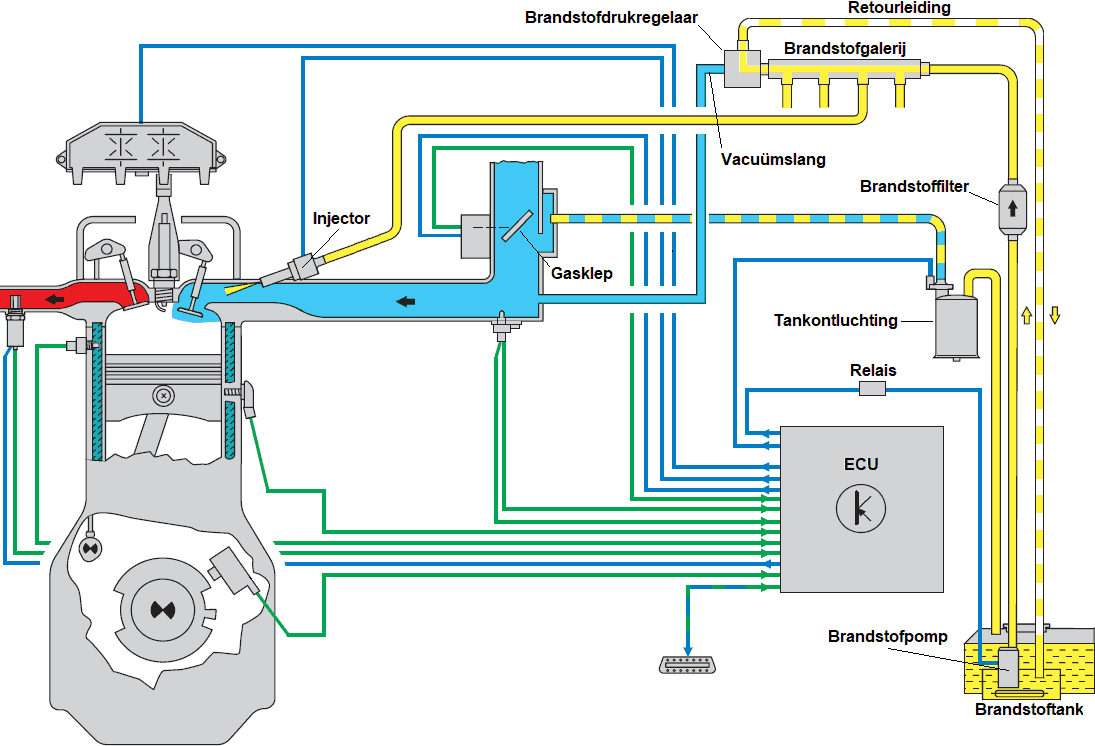
Sans utiliser de régulateur de pression, les situations suivantes se présentent :
- Au ralenti, le vide plus élevé (c'est-à-dire la faible pression d'air) dans le collecteur d'admission produirait une pression de carburant indésirablement plus élevée ;
- Lors de l'accélération, il y a moins, voire presque pas de vide (pleine charge) et la pression du carburant chuterait, alors qu'une pression de carburant plus élevée est souhaitée.
Le régulateur de pression de carburant augmente ou diminue la pression de l'essence dans la galerie de carburant en fonction de la pression de l'air dans le collecteur d'admission. On peut considérer le régulateur de pression de carburant comme une vanne dynamique, qui permet une ouverture entre la conduite d'alimentation de la pompe à carburant et la conduite de retour.
A droite on voit un diagramme de pression de carburant où la différence de pression relative dans toutes les conditions (ralenti, charge partielle et pleine charge) est de 4 bars grâce au régulateur de pression.
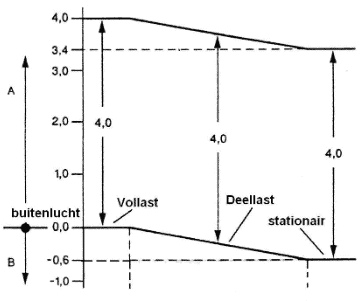
L'explication ci-dessous se réfère aux images montrant le régulateur de pression en situation sans et avec vide. À droite se trouve un régulateur de pression de carburant de Bosch, utilisé par plusieurs constructeurs automobiles.
Sans vide (à gauche) :
Le régulateur de pression est fermé au repos : le ressort presse la membrane pour la fermer, empêchant le carburant fourni d'atteindre la conduite de retour.
Avec vide (milieu) :
Lorsque la pression au-dessus du diaphragme diminue, la pression du carburant du côté alimentation pousse le diaphragme vers le haut contre la force du ressort. Une ouverture est créée à travers laquelle le carburant fourni est évacué par la conduite de retour vers le réservoir de carburant.
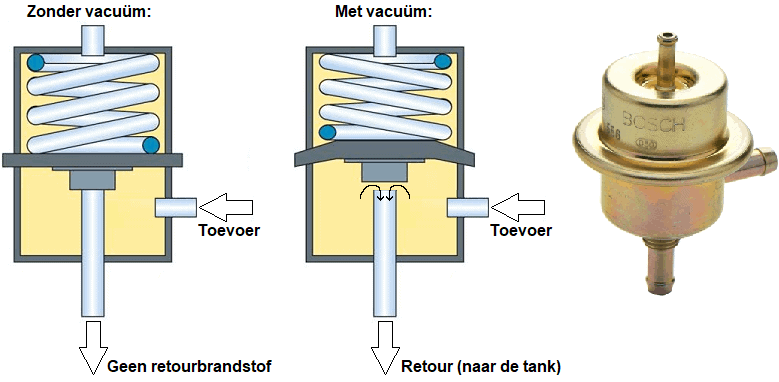
Stratégie d'injection injection multipoint :
Avec l’injection multipoint (indirecte), trois méthodes d’injection différentes sont utilisées :
- Simultanée : l'injection s'effectue en même temps sur tous les cylindres.
- Groupe : l'injection s'effectue par groupe ; il existe une distinction entre un ou plusieurs groupes.
- Séquentiel : chaque injecteur est piloté séparément et possède donc son propre moment d'injection.
Le système de gestion moteur dans la figure ci-dessous illustre une injection groupée. Les injecteurs des cylindres 1 et 2 ont une alimentation commune (rouge) et sont tous deux reliés à la masse en même temps (vert). Les injecteurs des cylindres 3 et 4 sont les mêmes, mais sont commandés séparément des cylindres 1 et 2.
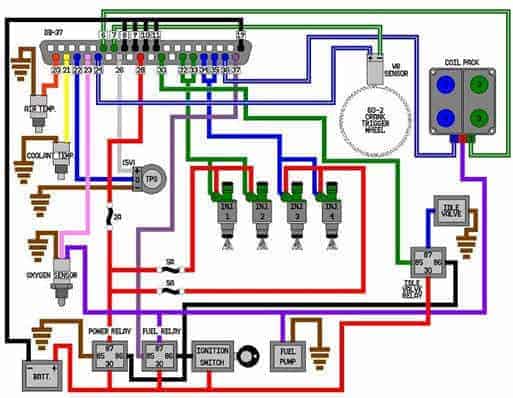
Injecteur électromagnétique (MPI) :
L'injecteur électromagnétique est utilisé sur de nombreux moteurs à essence qui n'utilisent pas d'injection haute pression (directe) avec une pompe haute pression séparée. Le carburant est sous une pression constante de 1 bar à l'entrée de l'injecteur. La pression du carburant est fournie par la pompe à carburant dans le réservoir. Avec l'injection multipoint (ceci est décrit plus loin sur la page), chaque cylindre possède son propre injecteur. Cet injecteur est monté dans le collecteur d'admission et injecte du carburant avec une pression allant jusqu'à 6 bars avant l'ouverture de la soupape. Le carburant a alors suffisamment de temps, lorsque la soupape d'admission commence à s'ouvrir, pour se mélanger à tout l'oxygène (indiqué sur la figure par la flèche bleu foncé) circulant dans le cylindre.
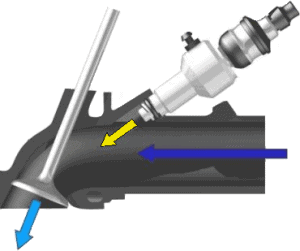
L'unité de commande du moteur examine la position du vilebrequin pour réguler le calage de l'injection et le calage de l'allumage. En fonction de plusieurs facteurs (température moteur et ambiante, charge, vitesse, etc., il donnera un signal à l'injecteur au bon moment pour s'ouvrir. La fiche de cet injecteur contient deux fils. Un fil a un plus constant d'environ 14 Volts. L'autre fil est connecté à la masse par l'ECU pour permettre au courant de circuler à travers la bobine de l'injecteur. Lorsque la bobine est suffisamment chargée, l'aiguille de l'injecteur s'ouvre contre la force du ressort. Lorsque la commande s'arrête, un ressort comprime l'aiguille de l'injecteur vers l'arrière. " L'alimentation en carburant est alors coupée. Lorsque la commande s'arrête, la bobine est encore chargée électriquement. L'énergie dans la bobine forme un pic d'induction, qui peut être observé sur l'oscilloscope. La tension d'induction se situe brièvement autour de 60 volts.
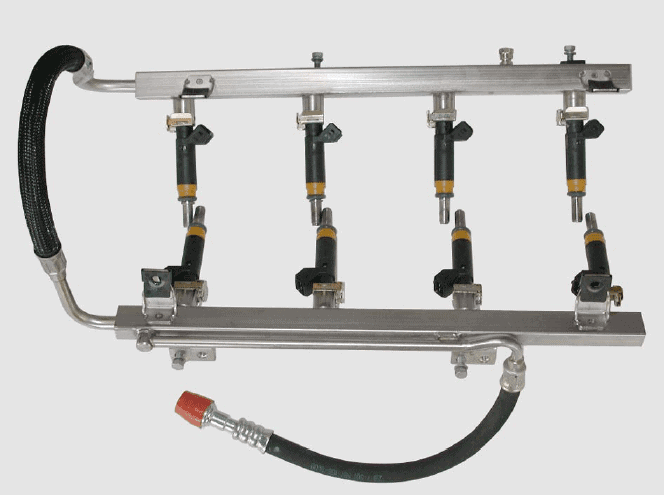
Ces injecteurs sont alimentés en carburant par la rampe d'injection (également appelée galerie de carburant). La pompe de suralimentation située dans le réservoir de carburant fournit la pression dans la rampe d'injection. La pression du carburant dans le rail est constante (environ 4 bars). La pression étant si faible, les injecteurs sont fixés à l'aide d'un clip de verrouillage et d'un joint torique pour l'étanchéité. Surtout dans les voitures plus anciennes où le système est démonté, il est judicieux de remplacer les joints toriques avant l'installation.
Le boîtier d'un injecteur est généralement en plastique. Au sommet du boîtier se trouve le connecteur qui est connecté en interne à la bobine. Il y a un joint torique en caoutchouc en haut sur lequel glisse la galerie de carburant. Des joints toriques ou des bagues d'étanchéité en téflon se trouvent en bas. Un joint torique est principalement utilisé dans les injecteurs MPI à injection basse pression, tandis que les anneaux en téflon peuvent être trouvés dans les moteurs à injection haute pression, comme un moteur FSI.
La bobine est enroulée autour du noyau de l'injecteur. Dans l'image ci-jointe, la bobine est surlignée en rouge. Au centre de l’injecteur, également interne à la bobine, se trouve un piston. Ce piston possède un couplage mécanique avec l'aiguille. Au-dessus du piston se trouve un ressort qui maintient le piston et donc l'aiguille dans son siège, fermant ainsi l'ouverture d'injection.
Au repos, la tension aux deux bornes de la bobine est d'environ 14 volts par rapport à la masse. Pour amorcer l'injecteur, l'ECU du moteur alimente un côté de la bobine en masse, tandis que l'autre côté reçoit une tension positive. À ce stade, le courant commence à circuler dans la bobine, entraînant la formation d’un champ magnétique. Ce champ magnétique tire le piston et donc l'aiguille d'injection vers le haut.
Lorsqu'il faut arrêter l'injection, le calculateur déconnecte la masse, provoquant la disparition du champ magnétique. Le ressort repousse le piston vers le bas, ce qui amène l'aiguille à couper l'alimentation en carburant de la chambre de combustion.
L'injecteur a généralement plusieurs ouvertures. Ces ouvertures sont très petites, de sorte que le carburant est injecté depuis l'injecteur dans la chambre de combustion sous forme de brouillard. Plus la brume est fine, plus elle s’évapore facilement.
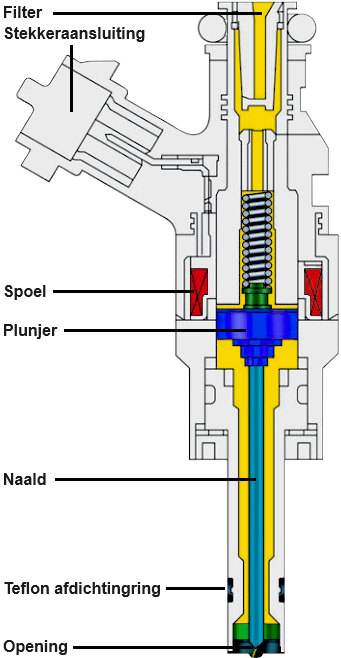
Injecteur piézo (DI) :
Les injecteurs piézoélectriques peuvent être utilisés aussi bien dans les moteurs essence que diesel. BMW a été la première marque à utiliser la technologie piézoélectrique dans les moteurs à essence, mais elle a arrêté de le faire avec les moteurs les plus récents.
Un injecteur piézo fait partie de l’injection haute pression. Une pompe haute pression séparée fournit une pression sur la rampe d'injection. Cette rampe d'injection distribue le carburant à tous les injecteurs (voir image). En raison des pressions très élevées, des tuyaux en aluminium avec presse-étoupes sont utilisés. Les presse-étoupes (qui sont vissés sur le tuyau et les injecteurs) doivent toujours être serrés avec la force correcte. Ceci est indiqué dans le manuel de réparation du moteur concerné.
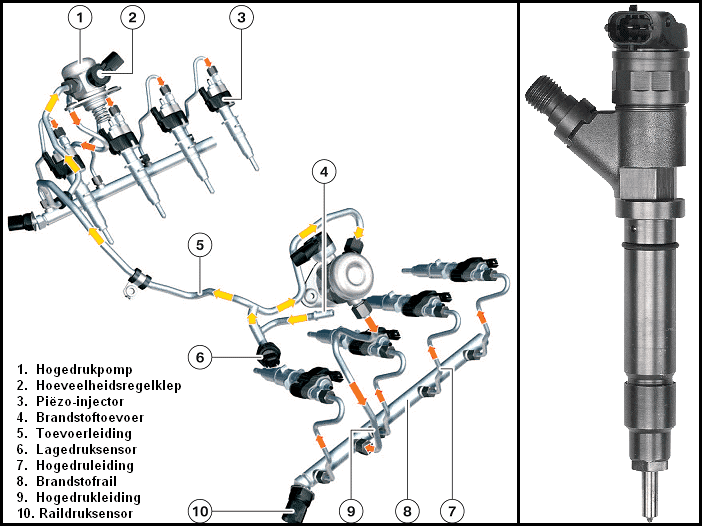
L'élément piézo de l'injecteur a la propriété de changer de longueur lorsqu'une tension positive ou négative y est connectée. Ceci est utilisé avec l'injecteur. Dès que le calculateur du moteur fournit une tension de commande d'environ 100 à 150 volts, l'élément piézo se dilate d'environ 0,03 mm. Ce changement de longueur suffit à établir une connexion entre la chambre haute et basse pression. L'injection commence immédiatement. L'élément piézoélectrique peut s'allumer et s'éteindre en un millième de seconde. Associé à une pression d'injection très élevée pouvant atteindre 2000 XNUMX bars, cela permet d'obtenir des injections très rapides et précises. Ces vitesses permettent également d'effectuer plusieurs injections les unes après les autres.
Les injections multiples pendant la course d'admission présentent l'avantage que le mélange air-carburant est optimal. La haute pression provoque une atomisation ultra fine des gouttelettes de carburant, afin qu'elles soient encore mieux mélangées à l'air. Jusqu'à 8 injections peuvent avoir lieu pendant la course d'admission. Cela a des conséquences positives sur la consommation de carburant, la puissance et les émissions de gaz d’échappement.
Stratégies d'injection injection directe :
La stratégie d'injection par injection directe présente différentes variantes : guidée par la paroi, guidée par air et guidée par jet (voir les images ci-dessous). Dans ces situations, il existe un processus de combustion en couches. Ceci ne s'applique pas à toutes les conditions de fonctionnement.
- Guidage mural : Le piston guide le nuage de carburant jusqu'à la bougie d'allumage. La distance entre la bougie d'allumage et l'injecteur est grande. Appliqué aux moteurs GDI et HPI.
- Guidé par air : Le mouvement de l’air amène le nuage de carburant jusqu’à la bougie d’allumage. La distance entre la bougie d'allumage et l'injecteur est grande. Appliqué aux moteurs FSI et JTS.
- Jet guidé : La bougie d'allumage est située au bord du nuage de carburant. La distance entre l'injecteur et la bougie d'allumage est petite. Appliqué aux moteurs BMW.
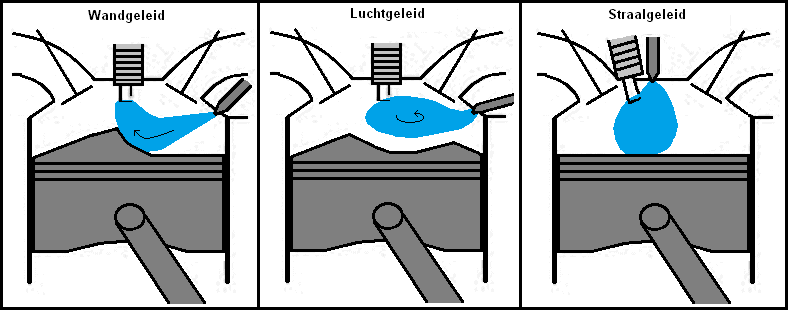
Comme déjà indiqué, les moteurs essence à injection directe ne disposent pas d'une combustion stratifiée dans toutes les conditions de fonctionnement. Les moteurs à injection directe guidée par jet peuvent fonctionner par phases à charge partielle. Un processus de combustion en couches signifie qu'il y a plusieurs couches d'air dans l'espace de combustion. Près de la bougie, la valeur lambda est de 1. Plus loin, la valeur lambda devient plus élevée (plus pauvre, donc plus d'air). Cet air constitue une couche d’air isolante. Dans un procédé en couches, le temps d'injection est plus long que dans un procédé homogène. À l'aide d'une injection en couches, le papillon des gaz peut être complètement ouvert, de sorte qu'il étouffe moins l'air. L'air aspiré étant étouffé, il rencontre moins de résistance et peut donc être aspiré plus facilement. Étant donné que la valeur lambda dans l'espace de combustion avec injection en couches est inférieure à 1 en raison de la couche d'air isolante, cela ne pose aucun problème de combustion. Pendant le processus de stratification, la consommation de carburant diminue.
Avec un mélange homogène, la valeur lambda est partout de 1. Cela signifie que dans un moteur à essence, le rapport air/carburant est de 14,7:1 (14,7 kg d'air pour 1 kg de carburant). Chaque moteur peut fonctionner de manière homogène. Si un enrichissement a lieu, la valeur lambda diminuera et si le mélange est appauvri, la valeur lambda augmentera :
<1 = Riche
>1 = Mauvais
Un moteur oscillera toujours entre riche et pauvre pour que le convertisseur catalytique continue de fonctionner correctement. Le sonde lambda envoie les données au système de gestion du moteur.
À pleine charge, le moteur fonctionne toujours de manière homogène. Cela donne un couple plus élevé qu'avec un processus en couches. Si le moteur tourne de manière homogène, le carburant est injecté précocement. Le moteur tourne également de manière homogène même après un arrêt. Le couple de démarrage est alors plus élevé que si le moteur fonctionnait en couches.
La courbe caractéristique ci-dessous représente les situations de fonctionnement à différentes vitesses par rapport au pression de combustion, avec et sans utilisation de l'EGR.
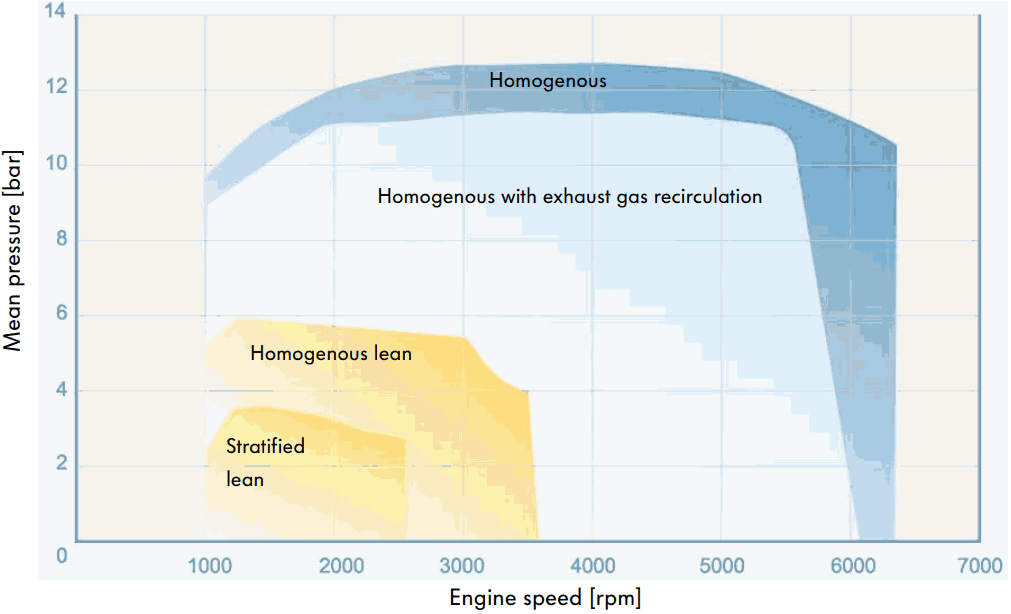
Double injection :
Le groupe VAG utilise des moteurs essence à double injection pour répondre aux normes d'émissions en vigueur. Dans les moteurs à double injection, il existe deux systèmes d’injection de carburant : un système basse pression et un système haute pression.
- Le système basse pression contient des injecteurs MPI utilisés depuis des décennies. Les injecteurs MPI sont montés dans le collecteur d'admission et injectent dans la soupape d'admission à une pression de 4 à 5 bars ;
- Le système haute pression contient des injecteurs haute pression qui injectent directement dans la chambre de combustion avec une pression d'injection maximale de 150 à 200 bars.
Le système de gestion du moteur détermine quel injecteur est contrôlé.
L'image suivante montre une coupe transversale de la culasse avec les deux systèmes de carburant.
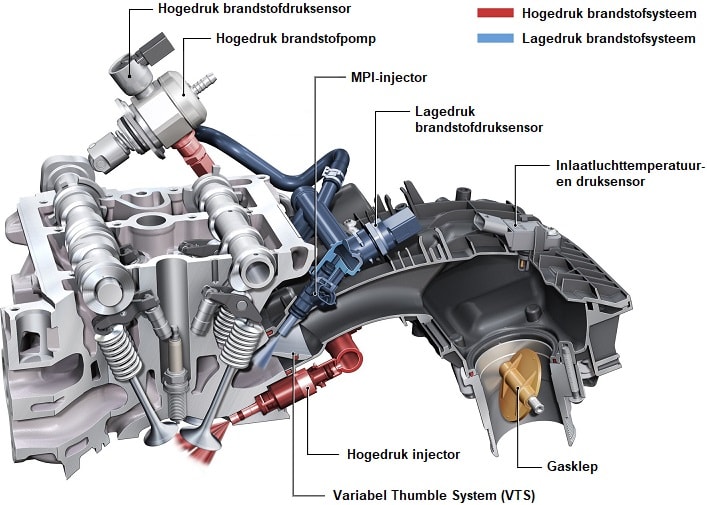
L'injection MPI offre un meilleur mélange entre l'air et le carburant. Les injecteurs directs sont utilisés au ralenti et à pleine charge. Avec l'injection directe, un meilleur refroidissement est obtenu, ce qui permet un taux de compression plus élevé. Cependant, le mélange de l’air et du carburant n’est pas optimal. Cela provoque davantage d’émissions de suie. C’est pour cette raison que les moteurs à injection directe sont aujourd’hui équipés d’un filtre à particules. Ce n'est pas un problème avec la double injection. Le « système de pouce variable », en abrégé VTS, est une version d'un collecteur d'admission variable qui offre un meilleur débit d'air. Le « pouce » est un flux d’air qui se transforme en vortex lorsqu’il entre dans le cylindre. Le tourbillon d'air est nécessaire pour mélanger correctement le carburant de l'injecteur MPI avec l'air.
La double injection associée au VTS garantit de meilleures émissions d’échappement. Un avantage supplémentaire est que la soupape d'admission est nettoyée par l'injecteur MPI. Les moteurs à injection directe souffrent souvent d'un conduit d'admission sale (collecteur d'admission et soupapes d'admission), ce qui entraîne des problèmes tels qu'une alimentation en air limitée. Dans le cas extrême, l'admission devient tellement bouchée que la soupape d'admission ne peut plus se fermer correctement sur la culasse et finit par brûler parce qu'elle ne peut pas dissiper suffisamment la chaleur.
On sait qu'aux Etats-Unis, les mêmes moteurs sont équipés uniquement d'injection directe pour les moteurs VAG à double injection. Le collecteur d'admission est bouché. En effet, au moment de la rédaction de cet article, les exigences environnementales sont plus strictes en Europe qu'aux États-Unis, et le constructeur ne propose pas de moteurs pour les marchés où les normes d'émission sont moins strictes avec des systèmes aussi coûteux pour des raisons de coût.
Mesure des caractéristiques de tension et de courant sur un injecteur multipoint :
L'oscilloscope ne peut mesurer que la tension. Les câbles de mesure peuvent être connectés en parallèle entre les composants électriques. La mesure du courant en série n'est pas possible. Le courant peut être mesuré à l'aide d'une pince ampèremétrique inductive. Les capteurs Hall de la pince ampèremétrique mesurent le champ magnétique et le convertissent en tension. La tension peut être mesurée avec l'oscilloscope. Dans ce cas, il existe un facteur de conversion de 10 mv par ampère ; Pour chaque 0,010 volt transmis par la pince ampèremétrique, cela peut être converti en 1 A.
L'image d'oscilloscope suivante montre le profil de tension et de courant d'un injecteur électromagnétique.
- Rouge : gradient de tension ;
- Jaune : flux de courant.
Au repos la tension est de 14 volts. Il n’y a plus de différence de tension au niveau de la fiche, donc aucun courant ne circule. L'ECU connecte un fil à la terre pour contrôler l'injecteur. La différence de tension fait circuler le courant à travers la bobine de l’injecteur.
La ligne jaune indique le flux de courant : dès que la tension chute à 0 volt, l'accumulation de courant commence. Le chargement de la bobine prend du temps. Le courant n'augmente pas au-delà d'environ 0,9 A. À mi-chemin de l'accumulation de courant, nous voyons un coude dans la ligne : c'est le moment où suffisamment de magnétisme s'est accumulé pour soulever l'aiguille de son siège. L'injecteur commence à injecter.
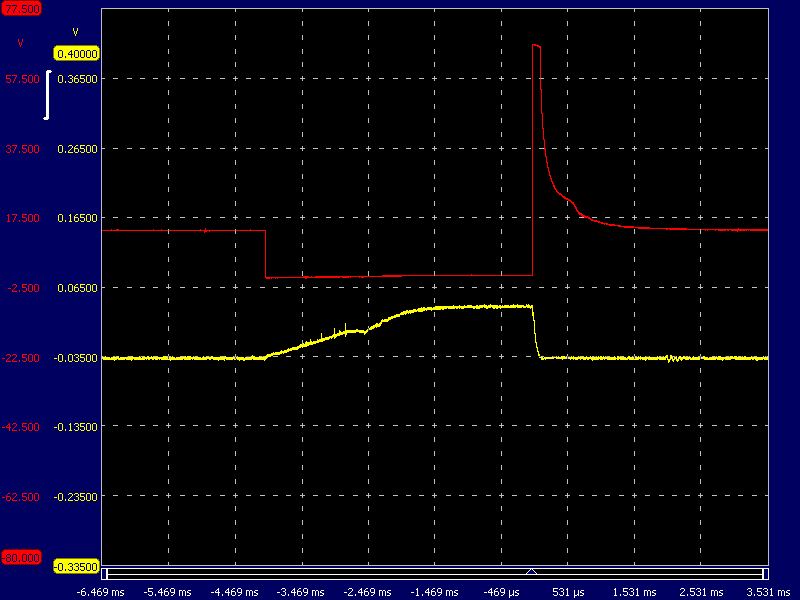
L'ECU coupe la connexion à la terre pour arrêter le contrôle. L'énergie résiduelle dans la bobine fournit une tension d'induction d'environ 60 volts. L'injecteur arrête d'injecter car le ressort repousse l'aiguille dans son siège. Cela peut être vu sur l'image de l'oscilloscope par la bosse du signal de tension.
Si le moteur tourne de manière irrégulière et que des ratés d'allumage des cylindres se produisent, cela peut être dû à plusieurs causes :
- Pas d'étincelle ou mauvaise étincelle en raison d'une bougie d'allumage, d'un câble de bougie ou d'une bobine d'allumage défectueux ;
- Restriction de l'alimentation en carburant due à un filtre à carburant obstrué, un régulateur de pression défectueux, un problème avec la pompe à carburant ou l'injecteur ;
- Perte de compression due à un problème au niveau des segments de piston, d'un joint de culasse ou de joints de soupape défectueux.
Lors d'un diagnostic, un oscilloscope peut être utilisé pour vérifier si les injecteurs fonctionnent toujours correctement. Au début de cette section, des mesures ont été présentées sans aucun dysfonctionnement. Les lignes bleues montrent à titre d'exemple à quoi ressemblerait le profil de tension et de courant d'un injecteur défectueux.
Dans le cas où le contrôle de l'injecteur est correct, mais qu'aucun pli n'est visible dans l'image de tension et de courant, on peut en conclure que l'aiguille de l'injecteur ne bouge pas. Étant donné que l'injecteur d'un cylindre ne fonctionne pas correctement et que les autres injecteurs fonctionnent correctement, les images des différents injecteurs peuvent être facilement comparées entre elles.
Si vous tapotez doucement l’injecteur, l’aiguille de l’injecteur risque de se détacher. Dans ce cas, le moteur fonctionnera immédiatement plus silencieusement et les plis seront à nouveau visibles sur les images du télescope. Toutefois, cela ne garantit pas une solution permanente ; il y a de fortes chances que le problème réapparaisse dans un court laps de temps. Le remplacement de l'injecteur concerné est nécessaire.
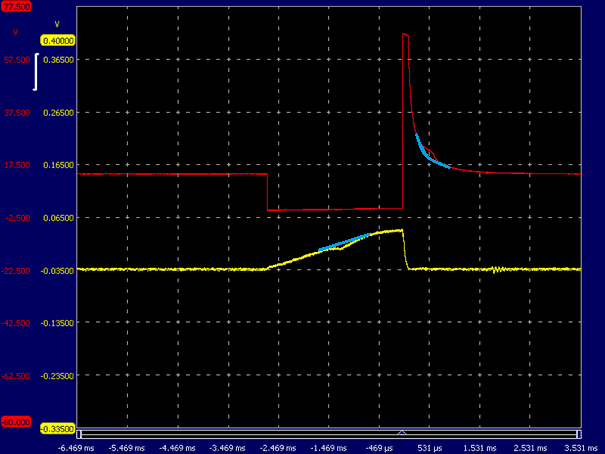
L'aiguille de l'injecteur ne s'ouvre qu'une fois que la bobine a été suffisamment chargée. En conséquence, l'injecteur n'injecte pas immédiatement le carburant lorsque l'ECU commence à le contrôler. Une fois l'actionnement terminé, le ressort presse l'aiguille de l'injecteur sur son siège. Cela prend également du temps. Le temps de contrôle n'est généralement pas égal au temps d'injection. L'image suivante montre la courbe de tension et de courant du même injecteur que ci-dessus, mais avec une vitesse accrue.
- Début du contrôle : l'ECU met le fil de commande à la masse. Le courant circule à travers la bobine de l’injecteur pour l’ouvrir. Le coude dans le schéma d'écoulement indique le moment où l'aiguille de l'injecteur s'ouvre. Le courant augmente alors un peu et reste donc constant. L'aiguille de l'injecteur reste ouverte.
- Fin du contrôle : comme déjà décrit, on reconnaît le moment où l'aiguille de l'injecteur se ferme par la bosse dans l'image de tension.
Le contrôle prend 4 ms, mais le temps d'injection réel est de 3 ms. Nous appelons la différence entre ceux-ci le « retard », traduit en néerlandais par « retard ». Le calculateur contrôle donc l'injecteur pendant 4 ms pour lui permettre d'injecter pendant 3 ms.
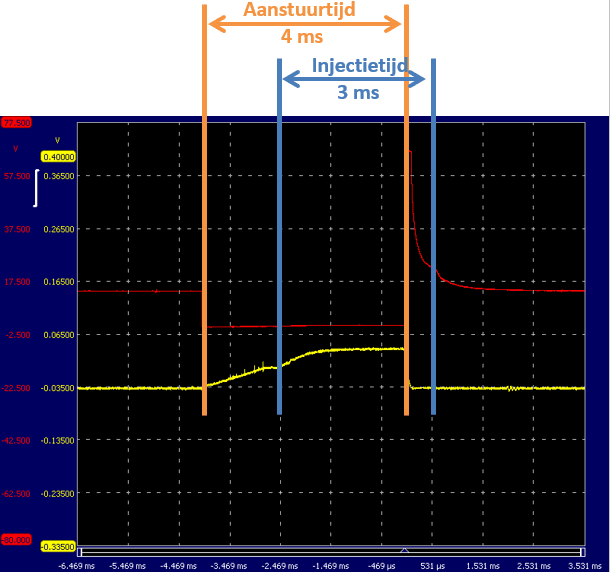
Calage de l’injection par rapport à la position du vilebrequin :
Le moment d'injection peut être visualisé à l'aide d'un oscilloscope. Le canal A (rouge) est sur le fil de terre de l'injecteur et le canal B (jaune) est sur le fil de l'injecteur. Capteur de position de vilebrequin connecté. Pendant que le moteur tourne, nous pouvons utiliser cette image d'oscilloscope pour déterminer le calage de l'injection et le temps d'injection.
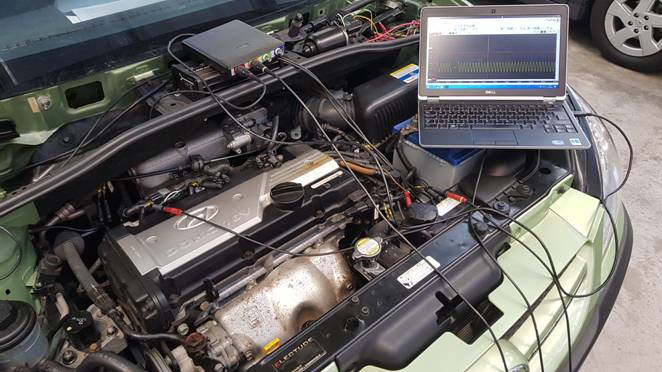
L’image de l’oscilloscope a été prise au ralenti. L'image de tension rouge montre l'ouverture et la fermeture de l'injecteur (voir la section : Mesure des caractéristiques de tension et de courant sur un injecteur multipoint). Le contrôle démarre au temps -2,860 ms ; la tension de 12 volts chute à 0 volt. C'est le point auquel la bobine de l'injecteur est mise à la terre et où le courant circule. Le contrôle des injecteurs se termine lorsque la ligne rouge remonte. En raison de l'énergie accumulée dans la bobine, une tension d'induction de plus de 60 volts apparaît. Ensuite, la tension chute progressivement jusqu'à 12 volts ; ici, l'injecteur est à nouveau éteint.
La tension alternative rouge provient de l'inductance Capteur de position de vilebrequin. Chaque fois que les dents de la roue d'impulsion passent devant le capteur de vilebrequin, une tension alternative sinusoïdale est créée. La roue d'impulsion contient 60 dents, dont 2 meulées. Les deux dents rectifiées constituent le point de référence auquel le système de gestion moteur reconnaît que les pistons des cylindres 1 et 4 se trouvent entre 90⁰ et 120⁰ avant le PMH (point mort haut). Une fois la dent manquante reconnue, le système de gestion du moteur a le temps (éventuellement en combinaison avec le capteur d'arbre à cames) pour déterminer le moment d'injection et d'allumage correct et pour activer l'injecteur et la bobine d'allumage avant que le piston ne soit au PMH.
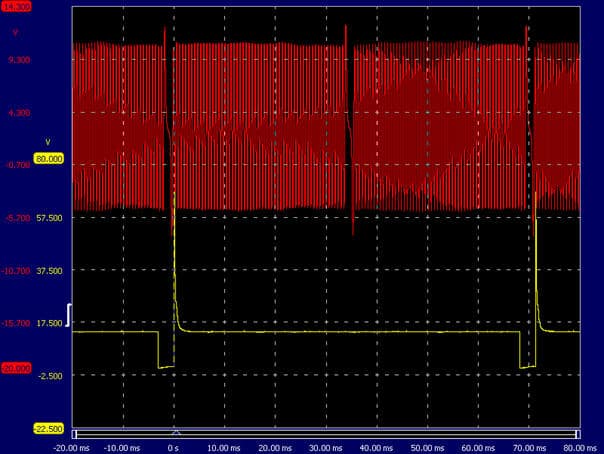
L'image de l'oscilloscope montre l'heure à laquelle l'injection commence ; l'injection démarre à la quatrième impulsion du capteur de vilebrequin. En supposant qu'il y ait 60 - 2 dents, après chaque rotation de 6⁰ du vilebrequin (360⁰ pour 1 tour / 60 dents) l'injection a lieu 24 degrés après le point de référence. La dent manquante est à 90⁰ avant le PMH, donc l'injection commence (90⁰ – 24⁰) = 66⁰ avant le PMH.
Avec une vitesse accrue de 2000 XNUMX tr/min, les impulsions du capteur inductif de vilebrequin sont plus rapprochées. La fréquence de ce signal est traduite en régime par le système de gestion moteur. En fonction de la vitesse, la charge (mesurée par le Capteur de carte) et le températures de l'air d'admission et du liquide de refroidissement, le temps d'injection nécessaire est déterminé. Le temps d'injection a lieu plus tôt et l'injecteur reste plus longtemps au sol : l'injecteur injecte plus tôt et plus longtemps.
Du début de l'activation jusqu'au point de déclenchement (flèche au niveau de l'arrêt de l'injecteur), le temps d'activation est d'environ 5,2 ms. Le temps d'activation de l'injecteur n'est pas égal à l'injection réelle (voir paragraphe précédent).
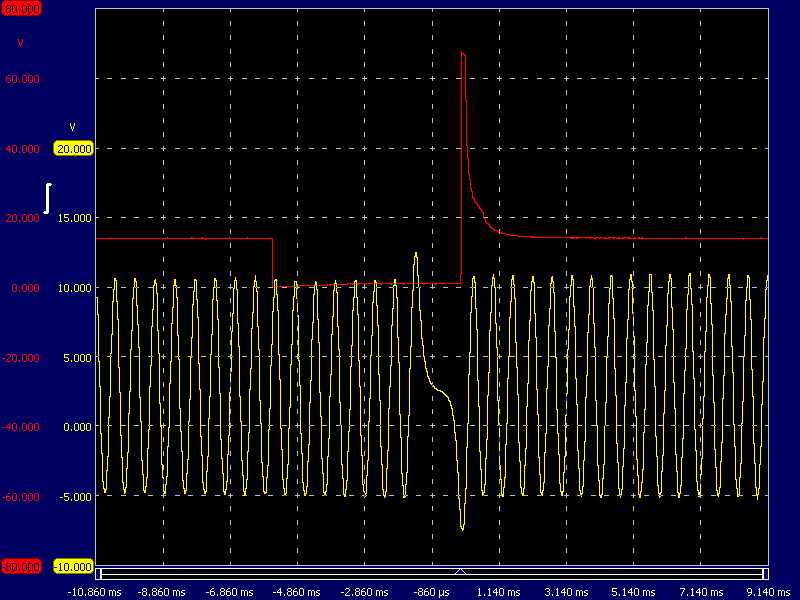
Dans l'image d'oscilloscope suivante, le signal inductif du vilebrequin est affiché en rouge et le signal de l'injecteur est affiché en jaune. En augmentant la vitesse jusqu'à environ 3000 tr/min, deux commandes d'injecteurs sont visibles. Il est clairement visible que l'injection de carburant du cylindre 1 a lieu à chaque seconde rotation du vilebrequin.
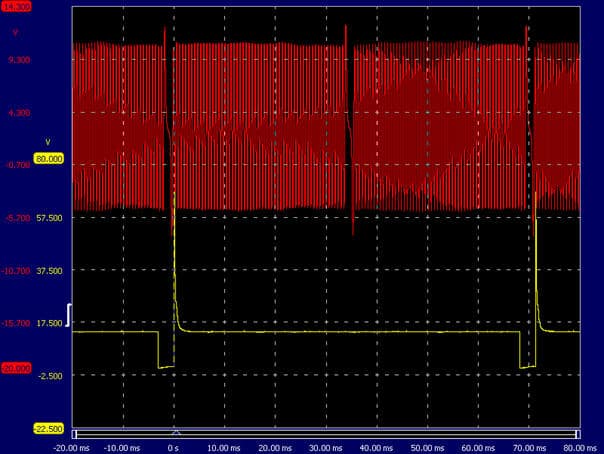
Limitation actuelle dans l'ECU :
Comme l'ont montré les mesures dans la section « Mesure de tension et de courant sur un injecteur multipoint », il existe un délai entre l'actionnement et l'ouverture effective de l'aiguille de l'injecteur. Dans ce cas, l'ouverture prend 1,5 ms.
L'aiguille de l'injecteur s'ouvrirait plus rapidement si le courant traversant la bobine augmentait plus rapidement. Le courant dépend de la résistance de la bobine : plus la résistance est faible, plus l'accumulation de courant est rapide. Les injecteurs à haute impédance utilisés dans le moteur des mesures ont une résistance de 16 Ohm. À une tension de bord de 14 volts, un petit courant circulera :
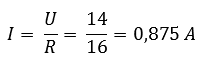
Le courant est suffisant pour ouvrir l'aiguille de l'injecteur, mais pas trop élevé pour qu'elle devienne trop chaude en raison d'une puissance trop élevée :

Comme seule une faible puissance est générée, il n’est pas nécessaire d’utiliser un contrôle de courant. Cela serait nécessaire avec des injecteurs à faible impédance.
- Les injecteurs à faible impédance présentent l'avantage que l'accumulation de courant augmente rapidement dès le départ. Il en résulte une ouverture rapide de l'aiguille de l'injecteur, donc peu de retard.
- Les injecteurs à faible ohm ont une résistance d'environ 2,8 ohms. La faible résistance provoque la circulation d’un courant élevé :
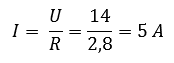
La puissance augmente également fortement :

La consommation électrique est presque sept fois supérieure à celle des injecteurs à haute impédance. Si le courant augmente trop, de la chaleur se développe dans les injecteurs et dans l'étage de sortie du dispositif de commande. Pour limiter le courant, la tension est activée et désactivée plusieurs fois sur une courte période de temps. Une fois l’aiguille de l’injecteur ouverte, il faut peu d’énergie pour la maintenir ouverte. Le courant diminue lors de la mise sous et hors tension. Cette progression est visible sur l’image de la lunette.
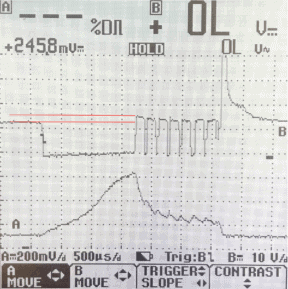
Détermination de la quantité de carburant requise :
Le constructeur a déterminé la quantité de carburant requise dans divers champs caractéristiques stockés dans la mémoire ROM de l'ECU. Il système de gestion du moteur lit à partir de ces graphiques la quantité de carburant nécessaire sans corrections. Cela dépend bien entendu du régime moteur, de la température et de la charge. Les paramètres les plus importants pour déterminer la quantité correcte de carburant sont expliqués dans cette section sous les noms de tableau VE et tableau AFR.
Tableau VÉ :
Le tableau VE représente l'efficacité volumétrique et le rapport air/carburant à chaque régime moteur et pression du collecteur d'admission. L'efficacité volumétrique est le rapport entre la quantité d'air mesurée remplissant les cylindres et la quantité d'air qui remplirait le cylindre dans une situation statique, en fonction du régime moteur et de la pression du collecteur d'admission. Les valeurs du tableau sont utilisées par l'ECU pour déterminer la masse d'air actuelle et donc le niveau de remplissage. Ces données sont utilisées pour calculer la quantité de carburant à injecter.
Cette approche théorique diffère de la réalité. Les spécifications du moteur n'ont pas encore été prises en compte ici. Considérez le diagramme des soupapes (chevauchement des soupapes, ou éventuellement calage variable des soupapes), la résistance de l'air dans le conduit d'admission, etc. C'est pourquoi un facteur de correction est appliqué qui donne un écart par rapport à la relation linéaire. Le facteur de correction est indiqué dans l'image ci-dessus par la ligne pointillée. La courbe indique dans quelle mesure la relation linéaire est correcte. À une pression de 60 kPa, l'écart est d'environ 50 % par rapport à la ligne représentant la relation linéaire. Le facteur de correction peut être exprimé en pourcentage.
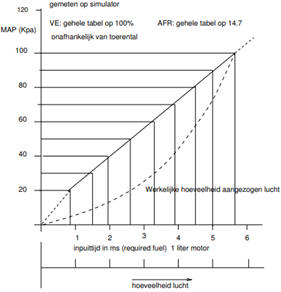
Dans un tableau VE, chaque cellule indique le pourcentage associé à la pression négative par rapport à la vitesse. Ce pourcentage sera le plus élevé à la vitesse à laquelle le couple est le plus élevé. Après tout, c'est là que le moteur est le plus efficace car c'est le moteur qui se remplit le mieux.
Les valeurs des tableaux VE et AFR plus loin dans cette section sont dérivées de la courbe de couple et de puissance d'un moteur 1.8 20v d'une VW Golf.
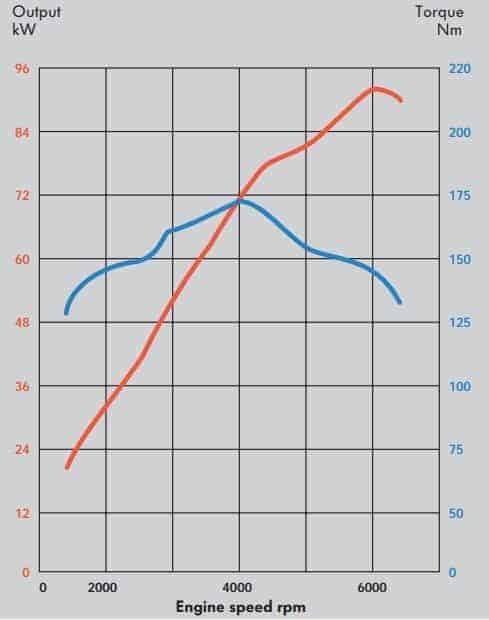
Les images ci-dessous montrent le tableau VE sous forme de tableau à remplir et la représentation tridimensionnelle créée à l'aide de la courbe de couple et de puissance dans le programme « TunerStudio ». Ce programme est principalement utilisé pour fournir un logiciel pour un calculateur programmable tel que le MegaSquirt ou le Speeduino. Pour plus d'informations : voir les pages à ce sujet Projet MegaSquirt.
L'axe vertical montre la MAP (Manifold Air Pressure) de 15 kPa (beaucoup de pression négative) à 100 kPa (la pression de l'air extérieur). La MAP indique la charge du moteur. L'axe horizontal indique le régime moteur entre le ralenti et le régime moteur maximum.
Les cellules du tableau VE indiquent le niveau de remplissage du moteur. Autrement dit; l'efficacité du moteur à une certaine vitesse et charge. Le moteur est le plus efficace autour du régime où le couple est le plus élevé (environ 4200 XNUMX tr/min) ; les pourcentages sont ici les plus élevés. C'est là que le moteur se « remplit » le mieux. L'application de techniques qui augmentent le niveau de remplissage, telles que le calage variable des soupapes, le réglage du collecteur d'admission ou l'utilisation d'un turbo, bénéficieront aux pourcentages.
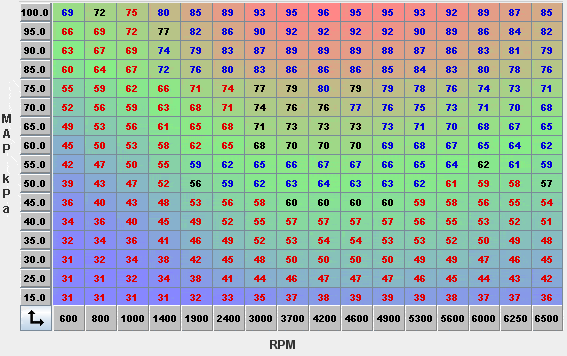
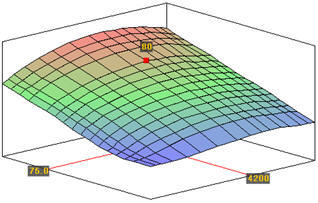
Tableau AFR :
La composition air/carburant requise est enregistrée dans un tableau AFR. AFR est l'abréviation de « Air Fuel Ratio ». Avec un rapport de mélange stoechiométrique (lambda = 1), 14,7 kg d'air sont nécessaires pour brûler 1 kg d'essence. Un mélange stœchiométrique n’est pas souhaitable dans toutes les situations.
- Un mélange pauvre profite à la consommation de carburant ;
- Un mélange riche permet une puissance plus élevée.
Lorsque le moteur doit fournir plus de puissance (P), un enrichissement a lieu. Un mélange plus riche assure également le refroidissement. L'enrichissement à λ = 0,8 signifie qu'un rapport de mélange (AFR) de 11,76 kg d'air pour 1 kg d'essence s'applique. Il y a donc moins d'air disponible pour brûler 1 kg de carburant qu'avec un mélange stœchiométrique. Un mélange pauvre, en revanche, donne une meilleure consommation de carburant (be), mais donne plus de chances de cogner. L'enrichissement ou l'appauvrissement du mélange doit toujours rester dans les limites de la combustion.
Au ralenti, le régime est compris entre 600 et 900 tr/min. Le robinet de gaz est presque complètement fermé et la dépression est importante : elle est comprise entre 25 et 40 kPa. Le mélange est stoechiométrique (14,7:1) dans cette plage de vitesse.
En charge partielle, le régime moteur aura augmenté jusqu'à 4200 40 tr/min. Le papillon des gaz est ouvert davantage, de sorte que la dépression dans le collecteur d'admission tombe à 75 – 13 kPa. À mesure que la charge du moteur augmente, la pression négative diminue ; l'enrichissement a lieu (AFR de 1:100). Un mélange pauvre est possible à faible charge moteur. À pleine charge, le papillon est complètement ouvert. La pression négative chute à 12,5 kPa (la pression de l'air extérieur) et un enrichissement maximal a lieu (1:XNUMX).
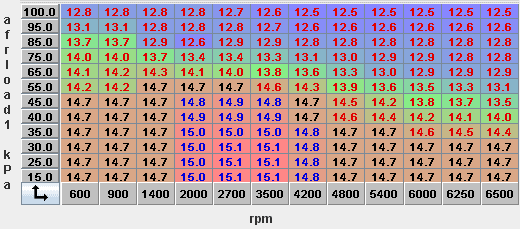
La valeur lambda affecte non seulement la puissance et la consommation de carburant, mais également les émissions de gaz d'échappement. Un mélange plus riche garantit une teneur en NOx plus faible, mais également des émissions de CO et de HC plus élevées. Avec un mélange plus pauvre, les particules de carburant sont plus éloignées les unes des autres, de sorte que la combustion n'est plus optimale ; avec pour conséquence que les émissions de HC augmentent également.
Lors de l'utilisation d'un catalyseur, il est souhaitable de s'assurer que l'injection alterne constamment entre riche et pauvre. Dans un mélange riche, du CO se forme en raison d'un manque d'oxygène, le catalyseur réduisant ainsi les NOx. Un mélange pauvre contient un surplus d’oxygène, qui oxyde le CO et les HC.
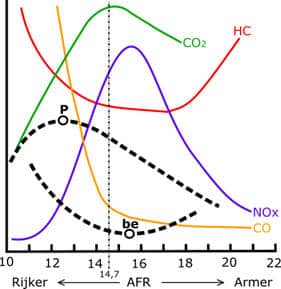
L'unité de commande détermine la quantité de carburant à injecter. Tout d'abord, les données d'injection de base sont lues à partir des champs caractéristiques. Les valeurs des tableaux VE et AFR, entre autres, sont incluses dans le calcul de la quantité injectée. Sont également prises en compte les valeurs suivantes déterminées par le constructeur :
- enrichissement en fonction de la température du liquide de refroidissement et de l'air d'admission ;
- enrichissement de l'accélération à court terme lors de l'ouverture (rapide) du papillon ;
- correction due à la variation de la tension de bord.
En plus de ces valeurs déterminées, les tensions que la sonde lambda envoie à l'unité de commande sont soigneusement prises en compte. Ces tensions dépendent de la teneur en oxygène des gaz d'échappement. Il s’agit d’un facteur variable qui change continuellement. L'entrée de ces tensions de capteur est appelée «garnitures de carburant" incorporé.
La façon dont les valeurs des tableaux VE et AFR et les autres paramètres mentionnés sont déterminées sont décrites sur les pages des Projet MegaSquirt.