Asignaturas:
- Introducción
- Medición sin interferencias
- Fallo 1: cable de señal interrumpido
- Fallo 2: cable de alimentación interrumpido
- Fallo 3: cable de tierra interrumpido
- Fallo 4 – Resistencia de transición
- Fallo 5: cortocircuito entre el cable de alimentación y de señal
- Fallo 6: cortocircuito entre el cable de alimentación y de tierra
- Fallo 7 – Cortocircuito en el sensor C
- Fallo 8: no hay voltaje de suministro debido a una ECU defectuosa
- Fallo 9: cable de señal PWM interrumpido
- Reparación de un cable positivo interrumpido.
Introducción:
Si sospechamos que hay una avería, primero escaneamos el coche. El código de error nos da una dirección para continuar nuestra búsqueda. Si no hay códigos de error guardados en la memoria de fallos, comprobamos si podemos reconocer desviaciones en los datos en tiempo real. ver la pagina Diagnóstico a bordo.
Si el código de error se relaciona con un sensor, esto no significa que el sensor esté defectuoso. Para descartar si hay algún problema en el cableado y/o conexiones de enchufes utilice: diagramas electricos y los equipos de medición excluyen ciertas cosas. Esta página describe una serie de situaciones posibles y muestra que la descripción del código de error puede diferir de la causa real.
Medición sin interferencias:
La siguiente figura muestra la medición de la tensión de alimentación y tierra de un sensor activo.
El sensor activo recibe un plus (5 voltios) y una tierra a través de él. dispositivo de control. En este caso la fuente de alimentación está bien. Podemos realizar una segunda medición en el cable de tierra (pin 3 del sensor, y/o pin 4 de la ECU). La señal debe estar entre 0,5 y 4,5 voltios.
Además de los sensores activos, también nos ocupamos de sensores pasivos e inteligentes. Lea más sobre esto en la página: tipos de sensores y señales.
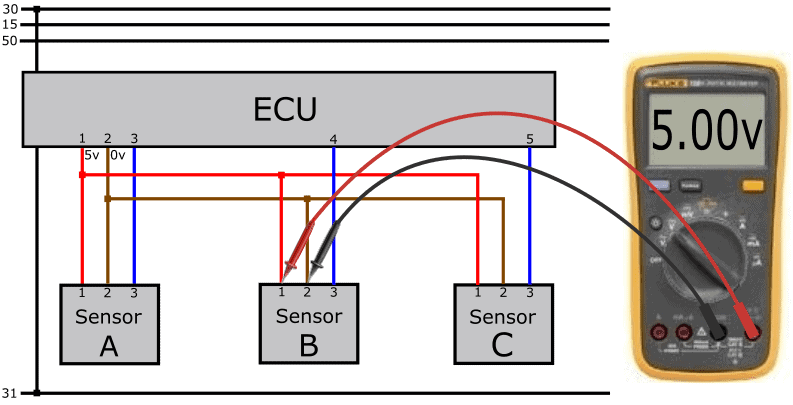
El sensor utiliza la tensión de alimentación de 5 voltios para generar la señal. La señal debe estar entre 0,5 y 4,5 voltios. La ECU lee el nivel de voltaje (o en otros casos la frecuencia) y lo traduce en un valor. Por ejemplo, este podría ser el valor de la sensor de presión de carga son: a una presión del turbo de 1,5 bar, el sensor envía una tensión de 3,25 voltios a la ECU.
Con esta medición, el voltaje de la señal se mide contra tierra y está bien.
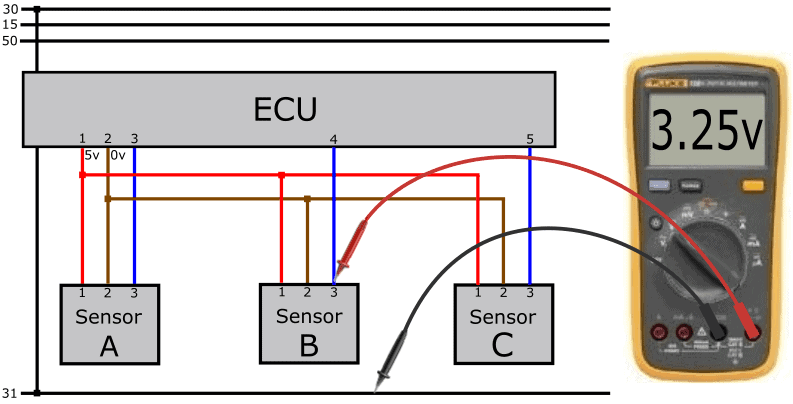
Utilizando un caja de ruptura Podemos medir en el enchufe de la ECU. Entonces sabemos qué voltajes envía y recibe la ECU.
En la siguiente medición volvemos a medir 3,25 voltios, pero luego en la entrada de la ECU. Esto significa que el cable de señal está bien: el voltaje se transmite 1:1 desde el sensor a la ECU.
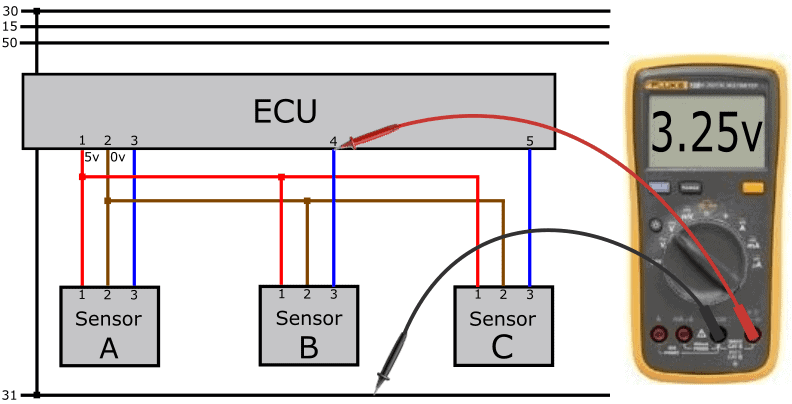
La señal del sensor nunca será de 0,0 o 5,0 voltios. Siempre se mantiene un cierto rango. Suele estar entre 0,5 y 4,5 voltios. El sensor no emitirá voltajes inferiores a 0,5 ni superiores a 4,5 voltios. En caso de defectos en los sensores o en el cableado, la ECU puede reconocer por el nivel de tensión si el valor está dentro o fuera del rango de medición:
- voltajes inferiores a 0,5 voltios: la ECU genera un código de error con la descripción: “sensor
- para voltajes superiores a 4,5 voltios, se indica "circuito positivo" en la descripción del código de error.
Los sensores activos también pueden enviar una señal digital. Estos sensores a menudo no son alimentados por la ECU, sino a través del terminal 15. En la mayoría de los casos estamos ante una señal PWM.
La siguiente imagen muestra parte del esquema donde un sensor activo tiene una fuente de alimentación externa y el cable de señal está conectado a través del pin 3 del sensor al pin 4 de la ECU. Con el osciloscopio se mide el perfil de tensión del sensor en comparación con la conexión a tierra.
El alcance está establecido en 2 voltios y 5 milisegundos por división. El ciclo de trabajo es del 50%.
En el párrafo: Fallo 9: cable de señal PWM interrumpido Te comentamos los pasos para realizar un diagnóstico adecuado.
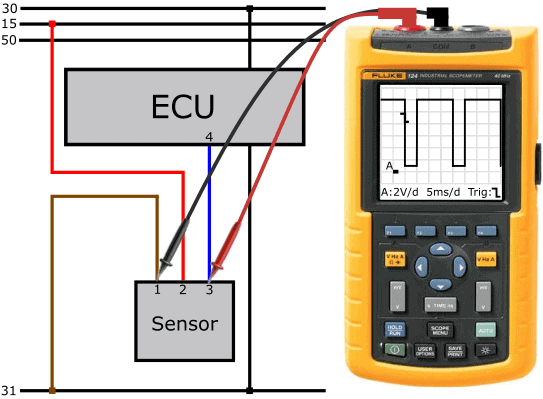
Diagnóstico del cableado del sensor:
Antes de diagnosticar sensores, debemos conocer el tipo de sensor (pasivo, activo, inteligente) y la forma en que el sensor envía su señal al dispositivo de control (analógico o digital, en forma de AM (Modulación de Amplitud) o FM (Modulación de Frecuencia): Después de consultar el esquema eléctrico, podemos estimar qué tensiones mediremos en el cableado.
Los siguientes párrafos describen posibles fallos de funcionamiento que pueden ocurrir en la práctica. En lugar de empezar con “la queja del cliente”, se menciona inmediatamente la causa; por ejemplo: un cable interrumpido, un cortocircuito, etc. Se trata de conocer mejor las técnicas de medición. Porque, ¿cómo actuar en caso de avería? ¿Y qué medidas utilizas para descubrir la causa?
¿Domina las técnicas de medición y tiene curiosidad por un caso? Entonces visita la página: Caso: mal funcionamiento del sensor de presión de combustible, cortocircuito con positivo.
Fallo 1 – Cable de señal interrumpido:
Si el cable de señal se interrumpe, el voltaje de la señal del sensor no puede llegar a la ECU. En este apartado podrás leer lo que mides en esta situación en las conexiones tanto del sensor como de la ECU.
Realizamos las siguientes mediciones en el sensor activo y obtenemos las siguientes lecturas:
- cable de alimentación (pin 1) en relación con la tierra del sensor (pin 2). 5 voltios;
- tensión de señal a tierra 2,9 voltios.
La fuente de alimentación y la señal del sensor generada están bien. Sin embargo, la señal del sensor no llega a la ECU debido a la interrupción.
Para medir el voltaje en la entrada de la ECU, utilizamos una caja de conexiones.
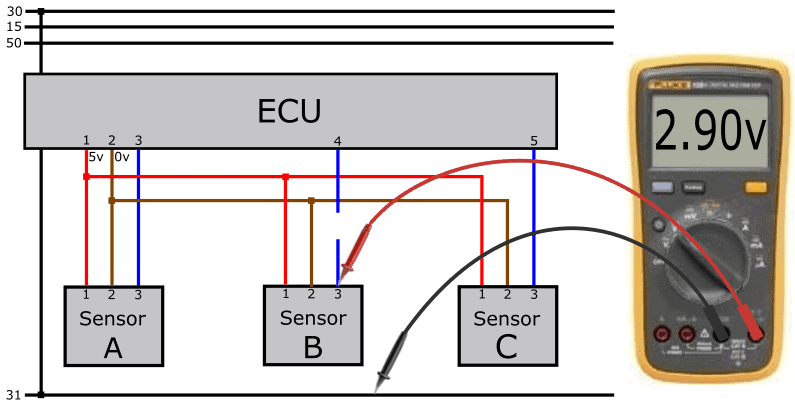
Usando una caja de conexiones, realizamos una medición en el pin 4 de la ECU en comparación con tierra (o pin 2 del sensor). Medimos un voltaje de 4,98 voltios.
Por lo tanto, el voltaje en el lado de la ECU es mayor que el voltaje enviado por el sensor. Un circuito en la ECU es responsable del voltaje de salida de 4,98 voltios. Esto tiene que ver, por un lado, con el método de procesamiento de señales, pero también con el reconocimiento de interrupciones.
La ECU mide ahora su propia tensión de salida y la reconoce como un circuito positivo debido a la tensión de alimentación de 4,98 voltios.
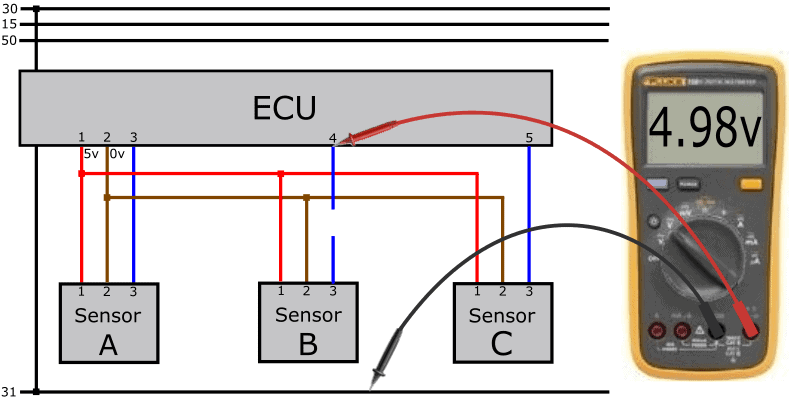
Luego medimos la diferencia de voltaje a través del cable entre la ECU y el sensor. La diferencia de voltaje debe ser de casi 0 voltios en una situación sin problemas.
En este caso medimos una diferencia de voltaje de 2,08 voltios; es decir, 2,9 voltios (sensor) en comparación con 4,98 voltios (ECU).
Las tensiones pueden llevarte por el camino equivocado.
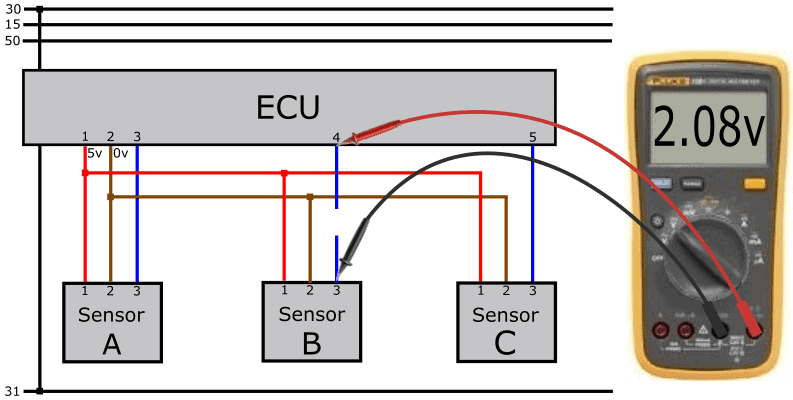
Retire el enchufe del sensor. Si no hubiera rotura del cable, mediríamos 4,98 voltios de la ECU en el enchufe retirado. Ahora medimos 4 voltios en el pin 4,98 de la ECU, pero 0 voltios en el enchufe quitado.
En este caso ya podemos concluir que el cable de señal está interrumpido.
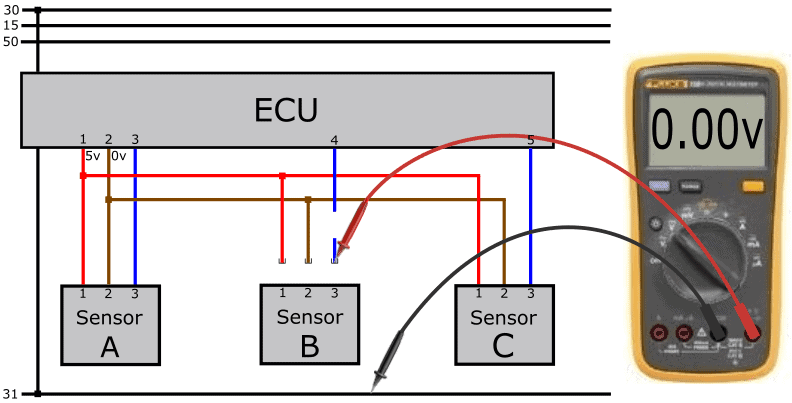
Con un cable de señal interrumpido, el voltaje en la entrada de señal de la ECU es de aproximadamente 5.0 voltios. En la pagina: tipos de sensores y señales, en el apartado: “suministro de tensión y procesamiento de señales” puedes leer cómo la ECU procesa la señal del sensor activo. Con este conocimiento podrá comprender mejor cómo podemos lidiar con interrupciones como la interrupción del cable de señal.
En la ECU se genera un voltaje de 4,98 voltios. Entre el cable positivo (del 78L05) y el ADC hay una serie de resistencias que elevan el voltaje de la señal a 5 voltios cuando no entra voltaje a través de la conexión de señal. El ADC mide este voltaje y lo procesa en una señal digital. Por lo tanto, la ECU recibe una señal sobre un voltaje que está fuera de rango y genera un código de error.
Tenga en cuenta: en caso de un fallo similar, el voltaje no siempre es exactamente de 4,98 o 5,0 voltios.
En la pagina: Caso: mal funcionamiento del sensor de presión de combustible - cortocircuito con positivo Se describe un fallo cuando este valor de tensión se desvía.
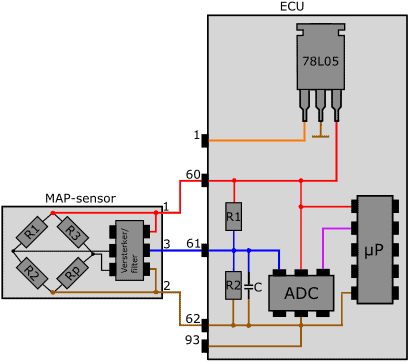
Fallo 2 – Cable de alimentación interrumpido:
Hay una interrupción entre la unión del cable positivo entre los tres sensores y el enchufe del sensor. La tensión de alimentación de 5 voltios no puede llegar al sensor ahora. El sensor no puede funcionar sin tensión de alimentación y tierra.
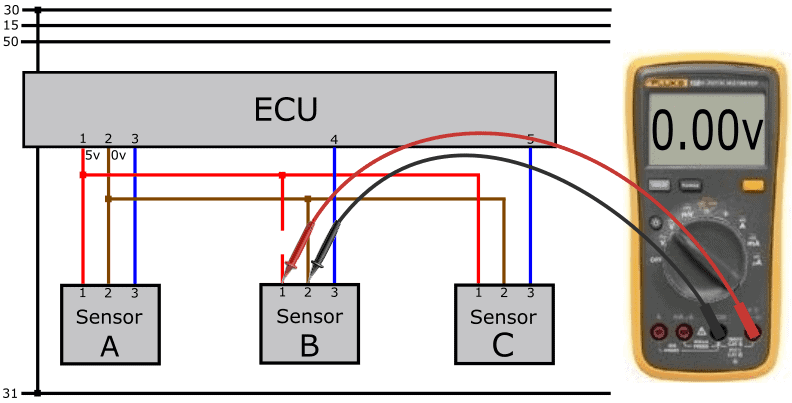
Debido a que medimos la fuente de alimentación y la tierra en el enchufe en la medición anterior, todavía tenemos que descartar cuál de los dos cables tiene un problema. Por tanto, medimos el positivo en otro sensor en el mismo circuito positivo. Por supuesto, esto también se puede hacer en la ECU, si hay una caja de conexiones disponible.
Medimos 1 voltios en el pin 5 del sensor A en comparación con la tierra del sensor B. Esto significa que la tierra del sensor B está bien.
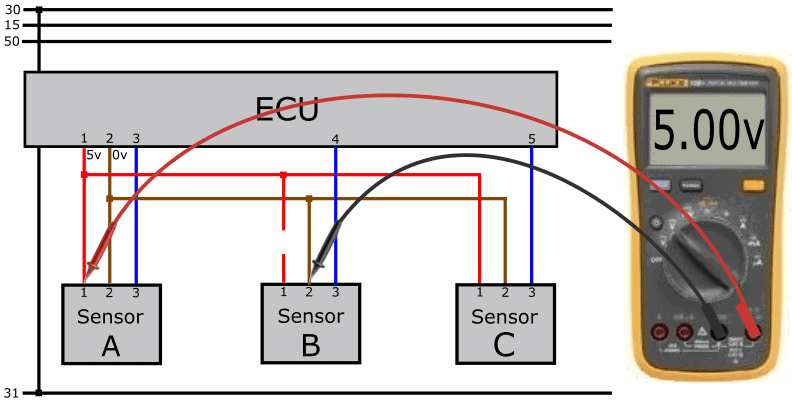
Cuando no fluye corriente a través de la electrónica del sensor activo debido a un cable de alimentación interrumpido, medimos un voltaje de 4,98 voltios en la entrada de señal de la ECU. Tenemos una situación similar a la del cable de señal interrumpido: las resistencias internas de la ECU elevan el voltaje de la señal: a 4,98 voltios. Como en este caso el cable de señal está bien, también medimos el voltaje de 4,98 voltios en el enchufe del sensor.
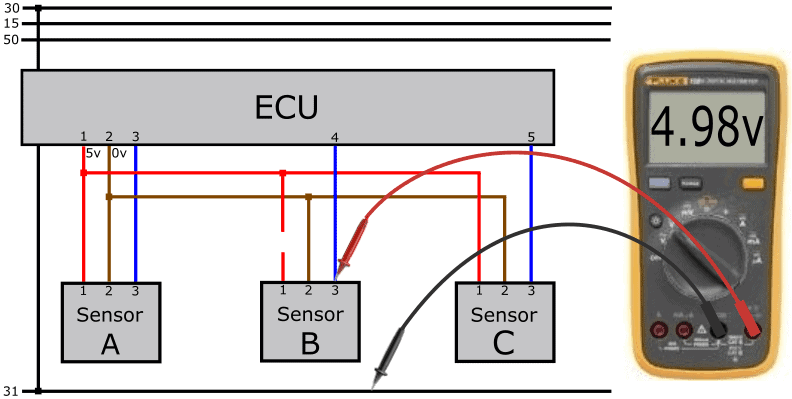
En los casos en que el voltaje esté justo por encima de 5,0 voltios, es posible que el voltaje del estabilizador de voltaje haya aumentado. Ver el párrafo: “suministro de tensión y procesamiento de señales” en la página: “tipos de sensores y señales".
Fallo 3 – Cable de tierra interrumpido:
En este caso, no se interrumpe el cable positivo, sino el cable de tierra. Se suministra un voltaje de alimentación de 5 voltios al sensor, pero debido a que estamos midiendo contra un cable interrumpido, el voltímetro no tiene voltaje de referencia e indica 0 voltios.
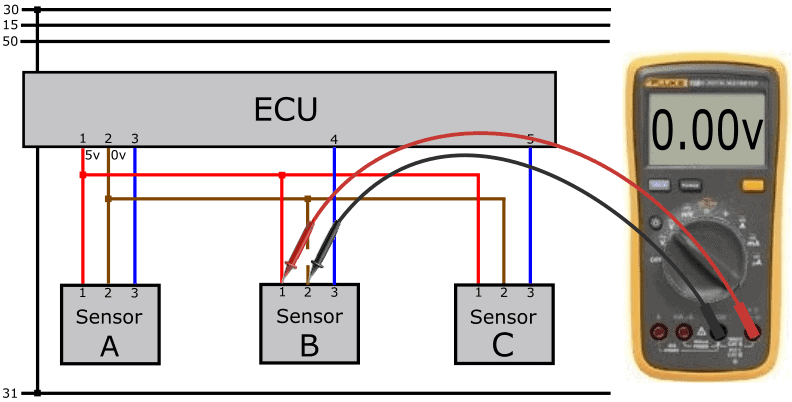
Al acercar la clavija de medición negativa al suelo de la carrocería o de la batería, el voltímetro sí indica 5 voltios.
Cuando conectamos el pin de medición negativo a la conexión a tierra de los sensores A y C, también debemos medir una diferencia de 5 voltios. Si medimos 2 voltios en el pin 5 del sensor A, pero no 5 voltios en el sensor C, entonces la interrupción estaría en el cable entre el sensor A y B, es decir, entre los dos primeros nodos.
Al igual que con la señal interrumpida y el cable positivo, ahora medimos un voltaje de 4,98 voltios en el cable de señal.
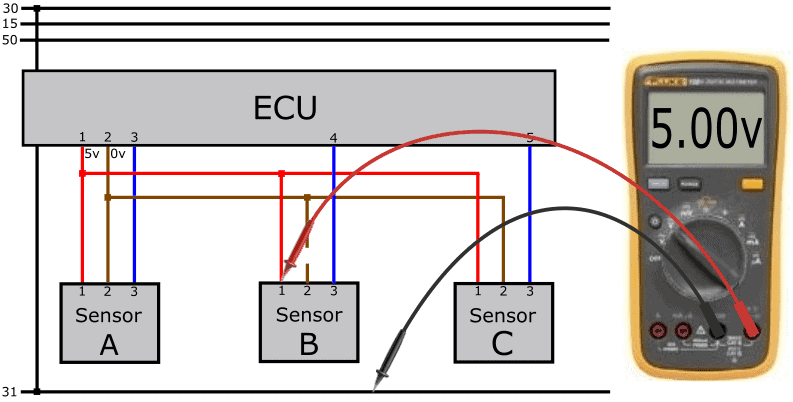
Fallo 4 – Resistencia de transición:
En el párrafo anterior ya se discutió la pérdida de voltaje debido a una resistencia de transición. En el siguiente diagrama vemos una resistencia en el cable de alimentación. Cuando la corriente fluye a través del cable de alimentación, la resistencia de transición asegura un voltaje (presumiblemente) demasiado bajo en el pin 1 del enchufe B. Medimos 4 voltios en lugar de los 5 voltios que esperábamos medir.
La descripción del DTC almacenado en este caso puede ser: “valor límite inferior de señal no alcanzado”.
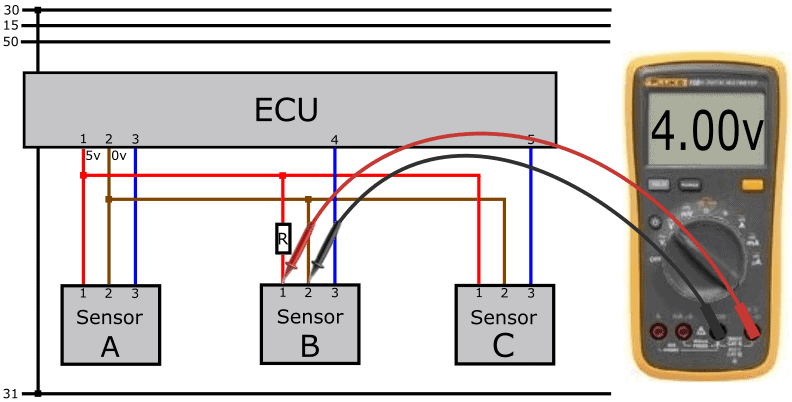
Si medimos el pin 1 del conector B versus el pin 1 del conector C, deberíamos tener una diferencia de (5-5) = 0 voltios. Ahora vemos una diferencia de 1 voltio.
Debido a que la pérdida de voltaje solo está presente en el cable del sensor B y no en el sensor C, podemos suponer que el cable entre la unión del cable horizontal en el diagrama y el enchufe no está bien.
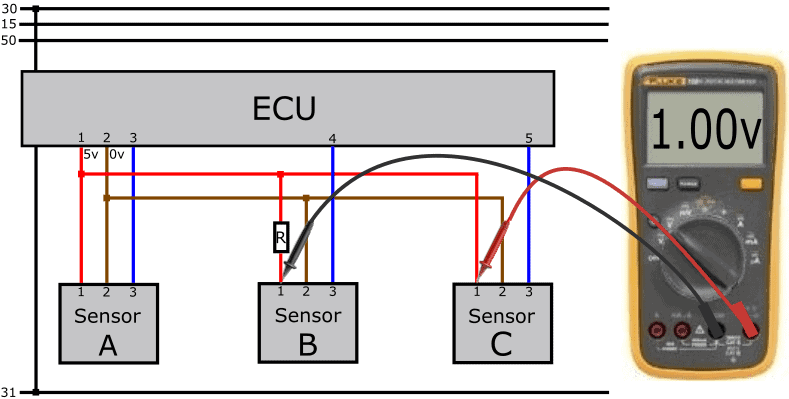
Fallo 5 – Cortocircuito entre el cable de alimentación y de señal:
Un posible fallo en el cableado es un cortocircuito. Nos encontramos con cortocircuitos en las siguientes situaciones:
- entre el cable de alimentación y el cable de señal (cierre positivo);
- entre el cable de tierra y el cable de señal (cortocircuito a tierra);
- entre uno de los tres cables entre sí y/o con la carrocería (conexión a tierra);
En este diagrama vemos un cortocircuito entre el cable de señal y el cable positivo (circuito positivo). Medimos un voltaje de señal igual al voltaje de suministro de 5 voltios.
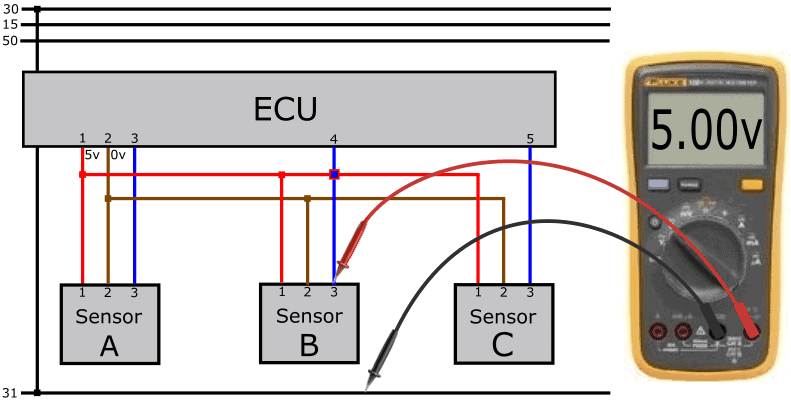
Al medir 5 voltios en el pin 3 del sensor y el pin 4 de la ECU, el problema puede ser interno al sensor. Para descartarlo, comprobamos que no haya cortocircuito en el cableado con un ohmímetro. Para obtener una medida segura y correcta apagamos la ECU, desmontamos el enchufe de la ECU y desmontamos los enchufes de los sensores que están conectados a los nodos. Debido a que hay un cortocircuito, medimos una conexión con el ohmímetro.
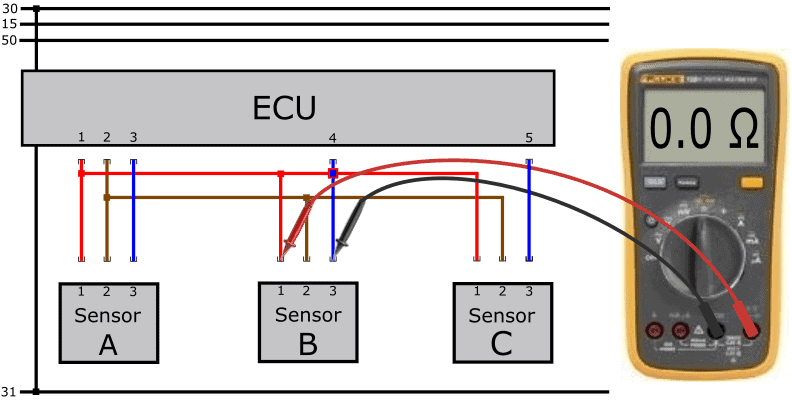
En este caso es 0,0 ohmios porque los cables se conectan entre sí. En realidad, este valor puede ser unos ohmios mayor. Cuando no hay ningún cortocircuito, el óhmetro indica OL o 1. (resistencia infinitamente alta) porque no hay conexión eléctrica entre los cables y las puntas de prueba.
Fallo 6 – Cortocircuito entre el cable de alimentación y de tierra:
En caso de un cortocircuito entre el cable de alimentación y el de tierra, la ECU corta la alimentación al pin 1. Todos los sensores alimentados por el pin 1 ya no funcionarán. Por lo tanto, los códigos de error se almacenarán en varios sensores.
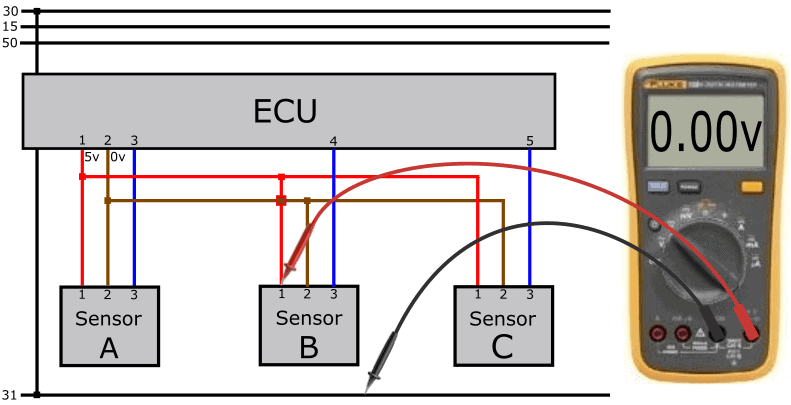
En este caso también medimos un voltaje de 5,0 en el cable de señal, que viene de la ECU.
Para descartar si estamos ante un cortocircuito, desmontamos los conectores tanto de la ECU como de todos los sensores del circuito en cuestión, como en el párrafo anterior. Utilice un óhmetro para medir la resistencia entre los cables rojo y marrón.
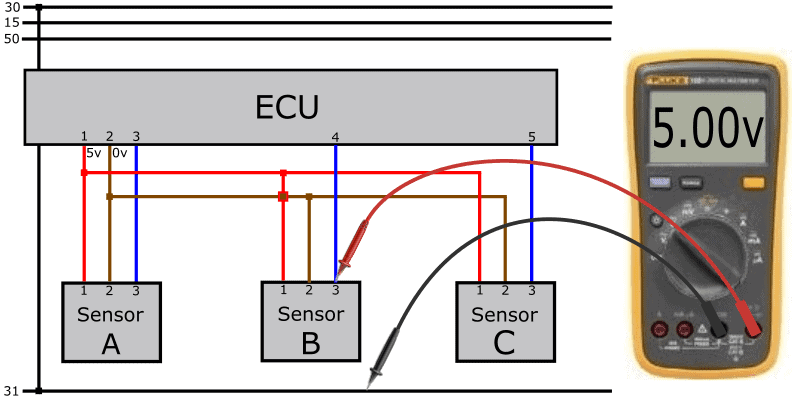
Fallo 7 – Cortocircuito en el sensor C:
Al medir el voltaje de suministro con respecto a tierra, medimos nuevamente 0 voltios. En la avería anterior tuvimos un cortocircuito en el cableado. En este caso el cortocircuito es interno a un sensor.
Sacamos uno a uno los enchufes de los sensores que vemos en el esquema. Cuando desconectamos el enchufe del sensor C, ya no tenemos cortocircuito y la ECU volverá a suministrar 5 voltios al cable positivo. En algunas versiones esto ocurre automáticamente, en otros tipos es necesario un cambio de abrazadera.

Fallo 8: No hay voltaje de suministro debido a una ECU defectuosa:
En algunos casos puede suceder que la ECU sea la culpable de la falta de tensión de alimentación. Internamente, un circuito está dañado y no salen 5 voltios.
A menudo se informa erróneamente que la ECU está defectuosa. En la mayoría de los casos hay otra causa. Por ello, compruebe en primer lugar posibles interrupciones y cortocircuitos en el cableado y los sensores conectados. Para descartar si la causa es un defecto interno en la ECU, verificamos todas las conexiones a tierra de la ECU.
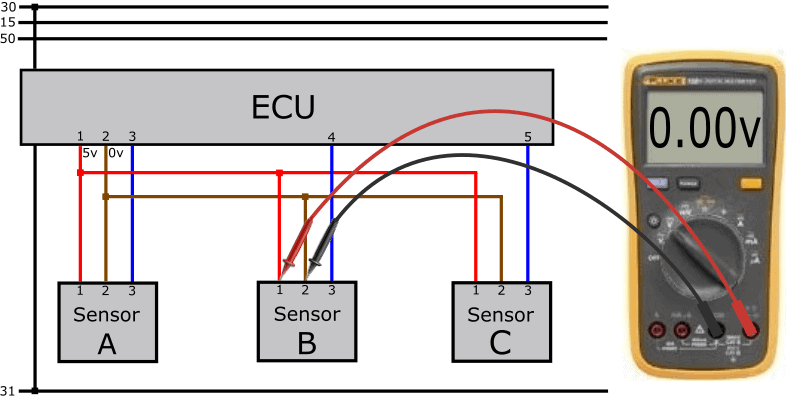
Con un extenso sistema de gestión del motor, vemos múltiples circuitos en una ECU, cada uno con su propio cable de tierra. A veces encontramos hasta ocho cables de tierra en un enchufe. En el momento en que una clavija del enchufe hace mal contacto o un cable de tierra en el mazo de cables se interrumpe, ese circuito falla. Por lo tanto, preferiblemente bajo carga, mida con una lámpara de prueba (positivo en la batería, negativo en cada conexión a tierra en el enchufe de la ECU) si la tierra está bien. La lámpara de prueba debe brillar con el mismo brillo en cada cable de tierra. ¿La lámpara no enciende con una conexión a tierra? Entonces es posible que haya identificado la causa y que la ECU no esté defectuosa.
Fallo 9 – Cable de señal PWM interrumpido:
Hasta ahora hemos hablado de tensiones analógicas que se pueden medir con un multímetro. Si se trata de una señal digital, un multímetro ya no es suficiente. Luego usamos el osciloscopio. El siguiente texto trata sobre el osciloscopio en las imágenes siguientes. Aquí vemos el Fluke 124 con una pantalla modificada.
El motivo para realizar esta medición es la descripción de la falla que se puede traducir del código de falla. La descripción dice: “señal del sensor interrumpida”.
La imagen del osciloscopio muestra una línea de voltaje constante de 0 voltios. Esto significa que no hay diferencia de voltaje entre las sondas de medición. ¿Has medido que los cables positivo y de tierra del sensor están bien (pin 2 comparado con 1), en este caso alrededor de 13 voltios, hay algún problema con el cable de señal? Tenga en cuenta que el sensor puede transmitir la información de dos maneras:
- El sensor envía un voltaje positivo a la ECU (generalmente un voltaje analógico;
- La ECU envía un voltaje, que el sensor aplica a tierra periódicamente (mediante PWM; una señal digital).
En el ejemplo, el voltaje de la señal en el lado del sensor es 0 voltios, por lo que asumimos el método 2.
Debido a que el cable de señal está interrumpido, el sensor no recibe energía de la ECU.
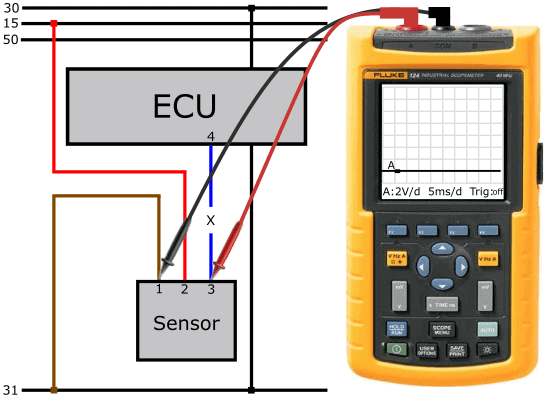
Medimos el pin 4 de la ECU contra el pin 1 del enchufe. El voltaje es 12 voltio. Con estas medidas hemos determinado que la entrada del sensor de la ECU está bien.
La ECU aparentemente envía un voltaje constante, pero no llega al sensor. Por lo tanto, el sensor no tiene voltaje para conectarse a tierra.
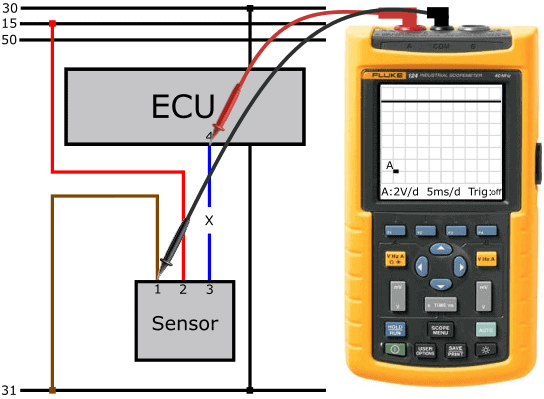
Durante la siguiente medición conectamos las clavijas de medición a ambos lados del cable de señal. Con esto determinamos la diferencia de voltaje en el estado activo a través del cable. La tensión debe ser de 0 voltios en una situación sin problemas. Sin embargo, en la parte activa del voltaje del bloque vemos un voltaje de 12 voltios. Cuando conseguimos el lleno Si mide el voltaje de suministro en la parte positiva máxima del voltaje del bloque, en la mayoría de los casos estamos ante un cable interrumpido. Ahora también es así: la tensión de salida de la ECU (pin 4 comparado con masa) es de 12 voltios.
Además, vemos en la parte inferior del tensión de bloqueo una desviación: dLa línea de voltaje cae a aproximadamente 5 voltios, permanece constante durante 10 milisegundos con una onda y luego vuelve a subir a 12 voltios. Debido a que el osciloscopio ahora está en serie entre la resistencia pull-up de la ECU y la resistencia pull-down del sensor, se crea una conexión en serie. El alcance tiene una alta resistencia interna, lo que afecta la señal. Por este motivo la señal no es utilizable.
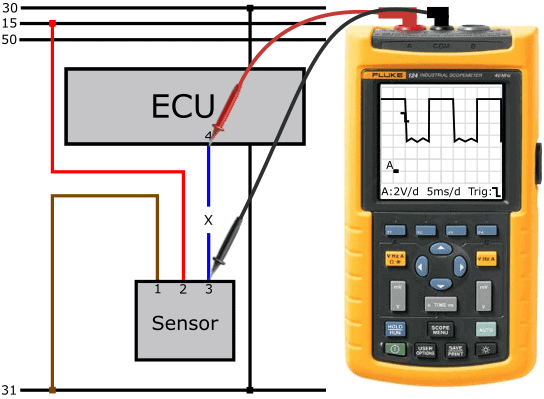
Aunque la medición del voltaje cargado es suficiente para un buen diagnóstico, no está de más utilizar una medición de resistencia para demostrar que realmente hay una conexión rota en el cable. En este caso medimos una resistencia infinitamente alta (OL o 1).
Después de reparar el cable de señal, medimos nuevamente el voltaje de la señal contra tierra. Tenga en cuenta: aquí estamos midiendo en relación con el suelo, por lo que la parte "activa" del sensor en la señal PWM ahora está invertida...
Vemos en esta imagen de alcance que:
- el voltaje es de un máximo de 12 voltios. Aquí el sensor no está activo: el voltaje en el cable de señal no llega a tierra.
- el voltaje cae a 1 voltio. Aquí el sensor está activo: el sensor aplica el voltaje de la ECU a tierra a través de la electrónica del sensor.
El sensor contiene un circuito electrónico que todavía usa 1 voltio. Este voltaje también permite que la ECU reconozca que el sensor se está activando correctamente. La ECU puede determinar a partir de los niveles de voltaje si el sensor está funcionando correctamente:
- La tensión durante un período de tiempo más largo es igual o superior a 12 voltios:
La ECU reconoce una interrupción o un circuito positivo; - voltaje inferior a 1 voltio: la ECU reconoce un cortocircuito a tierra.
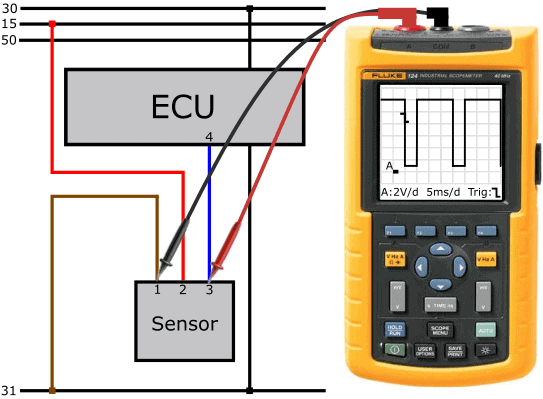
Reparación de un cable positivo interrumpido:
De los cinco fallos descritos en los párrafos anteriores, en la mayoría de los casos se pueden solucionar con bastante facilidad.
Corte el cable del cable con la resistencia de interrupción o transición lo más corto posible en el mazo de cables.
Aplique aislamiento si es necesario. Encuentre el sensor más cercano conectado al mismo circuito. Con sensores activos puedes encontrar esto fácilmente en un diagrama eléctrico. En el diagrama, el sensor más cercano es el C. Suelde cuidadosamente un cable nuevo al cable positivo.
Trabaje siempre con tubo retráctil para evitar problemas futuros debido a la penetración de humedad. ¡Si lo cierras con cinta aislante, en un futuro próximo surgirán nuevos problemas!
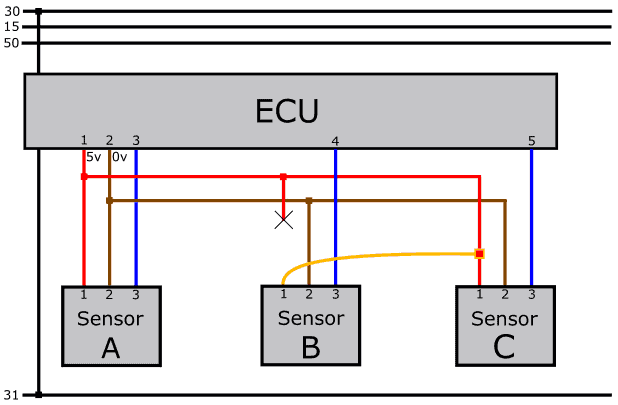