Asignaturas:
- Determinar e instalar actuadores para el sistema de gestión del motor.
- Inyectores de combustible
- Elegir inyectores adecuados
- Instalación de los inyectores en el colector de admisión.
- La inflamación
- Preparando con el encendido convencional
- Bobina de encendido para el sistema de gestión del motor.
- Acumulación de corriente en la bobina primaria.
- Avance de encendido
- cuerpo del acelerador
- Configuración de prueba del motor paso a paso con simulador.
- Configuración del motor paso a paso
- Circuito de la bomba de combustible
- Finalización del trabajo mecánico.
Determinación e instalación de actuadores para el sistema de gestión del motor:
Los actuadores que serán controlados con el MegaSquirt son los inyectores, la bobina de encendido, la bomba de combustible y el motor paso a paso para el ralentí. Este capítulo describe el proceso en el que se probaron e instalaron los actuadores en el bloque del motor, y la selección realizada.
Inyectores de combustible:
El MegaSquirt controla los inyectores. Los inyectores están conectados a tierra. Con un componente conectado a tierra, hay tensión de alimentación, pero la corriente sólo fluye cuando la tierra está conectada. En este caso, el inyector sólo inyectará cuando la ECU MegaSquirt cambie a tierra. Tan pronto como se detiene la activación, el inyector deja de inyectar. La cantidad de combustible a inyectar se determina con base en la tabla VE y la tabla AFR.
Un MOS FET enciende y apaga el inyector, lo que provoca que se inyecte el combustible. La cantidad de combustible determinada por el MegaSquirt depende de varios factores:
- La ley de los gases ideales que relaciona la cantidad de aire con su presión, volumen y temperatura;
- Valores medidos por los sensores en el bloque motor: presión en el colector de admisión (sensor MAP), temperatura del refrigerante y del aire de admisión, velocidad del cigüeñal y datos del sensor de posición del acelerador;
• Parámetros de ajuste: cantidad de combustible requerida, grado de llenado (VE), tiempo de apertura del inyector y enriquecimiento en determinadas condiciones.
El tiempo de inyección debe ser el mayor posible con el motor al ralentí para obtener una buena dosificación de combustible. Por tanto, no se puede utilizar cualquier inyector en el motor. Se deben comparar las propiedades de los diferentes tipos de inyectores y los cálculos deben proporcionar información sobre la cantidad de combustible necesaria para el motor en cuestión. También se podía elegir entre inyectores de alta y baja impedancia. Los inyectores de baja impedancia son adecuados para motores donde se requiere una apertura muy rápida de la aguja del inyector. La resistencia típica es de 4 ohmios. La desventaja de estos inyectores es la alta corriente. El desarrollo de calor que esto genera en el MegaSquirt no es deseable. Es posible utilizar inyectores de baja impedancia montando IGBT especiales en una placa conductora de calor en la carcasa del MegaSquirt. Se decidió utilizar inyectores de alta impedancia. Hay menos desarrollo de calor y estos IGBT no se utilizan.
El tamaño del conducto (flujo) es muy importante para determinar la cantidad de inyección correcta y, por tanto, el control. Si elige inyectores demasiado grandes, el tiempo de inyección al ralentí será tan corto que el motor puede funcionar de forma irregular. La cantidad de inyección debe ser suficiente para inyectar todo el combustible en el tiempo disponible. La cantidad de inyección se indica como tiempo de inyección en milisegundos. Se supone una carga elevada a un régimen del motor elevado. Esto es a un MAP de 100 kPa. El flujo del inyector requerido se puede calcular en función de las propiedades del motor. El flujo del inyector indica cuántos mililitros de combustible se inyectan por minuto.
Elección de los inyectores adecuados:
Para el proyecto se han puesto a disposición inyectores de tres tipos diferentes. La investigación mostró qué tipo de inyector era el más adecuado para su uso en este proyecto.
Cada tipo de inyector tiene un caudal diferente; el rendimiento después de un minuto de inyección varía según el tipo. Antes de probar los inyectores, se limpiaron en un baño de ultrasonidos. Con este método de limpieza, el inyector se limpia por dentro y por fuera mediante vibraciones ultrasónicas y un líquido de prueba especial, de modo que los restos de suciedad antiguos no puedan influir en la medición del caudal ni en el patrón de inyección. Durante la limpieza ultrasónica, los inyectores se abrieron y cerraron continuamente y se examinó el patrón de inyección de cada inyector; Esta era una hermosa niebla. Al cerrar no se observaron anomalías como, por ejemplo, la formación de gotas o un chorro desviado. Después de la limpieza y pruebas ultrasónicas, se reemplazaron las juntas tóricas para garantizar un buen sellado cuando se montaron en el colector de admisión.
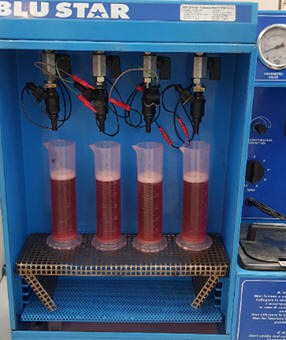
Usando una configuración de prueba (ver imagen arriba), los inyectores pueden inyectar en múltiples tazas medidoras, de modo que la cantidad de combustible inyectada se pueda leer después de un tiempo determinado. Controlando los inyectores a una presión de trabajo de 3 bar, se puede controlar la cantidad de combustible inyectado. La presión del combustible en la línea de suministro (el riel) debe ser de 3 bar y la aguja del inyector debe estar activada durante 30 o 60 segundos con un ciclo de trabajo del 100%. Después de 30 segundos de activación de los inyectores, se pudieron introducir los siguientes datos:
Tipo 1: 120ml
Tipo 2: 200ml
Tipo 3: 250ml
Sólo se utilizará un tipo de inyector. El tamaño del inyector se determina mediante la siguiente fórmula:

El tamaño del inyector se determina en función de la potencia efectiva (Pe) entregada a una determinada velocidad, el consumo específico de combustible en pausa (BSFC), el número de inyectores (n inyectores) y el ciclo de trabajo máximo con el que se controlan los inyectores. El total se multiplica por 10.5 para convertir de libras por hora (lb/hr) a ml/min.
La respuesta al cálculo indica qué inyector es adecuado para esta configuración de motor. No hay problema si hay una desviación inferior a 20 ml del valor calculado. Esta diferencia se compensa ajustando el software del MegaSquirt. La siguiente tabla proporciona una descripción general de los datos utilizados en las fórmulas:
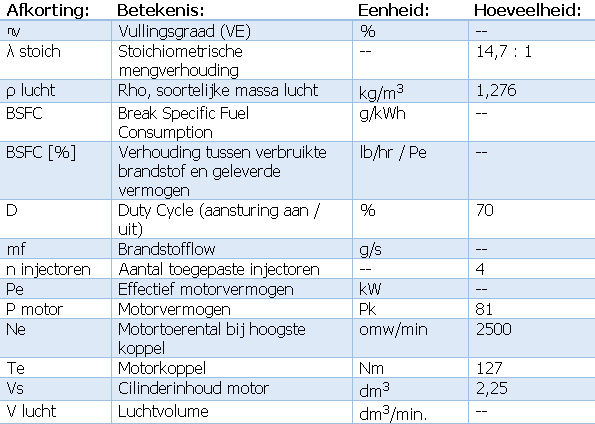
El primer paso es determinar el combustible inyectado a la velocidad del par. Por cada dos revoluciones del cigüeñal se aspira una determinada cantidad de aire. El grado de llenado es máximo a la velocidad del par. Debido a las propiedades del motor (incluida la superposición de válvulas), el motor se llena mejor a esta velocidad y la eficiencia es máxima. Se estima que la tasa de ocupación rondará el 70%. La fórmula 4 calcula el volumen de aire que hay presente en el motor en ese momento.
En la fórmula 5, la cantidad de combustible inyectado se calcula en función del volumen de aire presente. La potencia del motor alcanzada a la velocidad del par se calcula en la fórmula 6. La relación entre la cantidad de combustible inyectado y la potencia la indica el BSFC en las fórmulas 7 y 8.
El BSFC real se multiplica por 6 en la fórmula 3600 para convertirlo a kWh. El BSFC de un motor de gasolina suele estar entre 250 y 345 g/kWh. Cuanto menor sea el valor, más eficiente será el motor. La Fórmula 8 indica la relación entre el flujo de combustible en libras/hora y la potencia efectiva del motor. Este porcentaje está incluido en la fórmula 9.



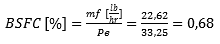

La respuesta a la fórmula 9 ha dejado claro que los inyectores con un caudal de 200 ml/min son adecuados para su uso en el motor. La diferencia de 7 ml es insignificante porque se compensa en el software al rellenar la tabla VE.
Instalación de los inyectores en el colector de admisión:
El sistema de inyección controlado electrónicamente permite desmontar el carburador, que forma parte de la configuración clásica. Por tanto, el carburador se sustituye por un cuerpo de mariposa (para el suministro de aire) y cuatro inyectores de combustible separados. El colector de admisión se conservó y se modificó para permitir la conversión al sistema de gestión del motor. La inyección de combustible se realiza en el colector de admisión. Se tomó la decisión de montar los inyectores lo más cerca posible de la válvula de admisión. En la mayoría de los casos, los fabricantes de motores de automóviles optan por montar la válvula de admisión en ángulo en el colector de admisión. El combustible se rocía contra la válvula de entrada. Sin embargo, para el proyecto actual, se eligió una configuración en la que los inyectores se colocan en un ángulo de 45 grados con respecto a los conductos de aire en el colector.
El colector de admisión está fabricado en fundición de aluminio. Se decidió colocar casquillos de aluminio en el colector. Mecanizar manualmente hasta obtener un buen tamaño no era una opción, porque los casquillos debían tener dimensiones diferentes a las de un tamaño de broca estándar. Esto significó que la subcontratación de las furgonetas tuvo que subcontratarse a una empresa con el equipamiento adecuado. Luego, los casquillos podrían unirse al colector mediante soldadura TIG. La elección de montar los inyectores en posición vertical en lugar de en ángulo se tomó por el siguiente motivo:
- El proceso de montaje: Es más fácil montar las furgonetas en una disposición recta y horizontal. Soldar las furgonetas al colector es más fácil porque ahora es más fácil soldar todo alrededor que en la situación en la que la furgoneta está en ángulo.
- Postprocesamiento: Durante la soldadura, los casquillos se vuelven un poco ovalados. La deformación es causada por el calor liberado durante el proceso de soldadura. Esto se ha tenido en cuenta haciendo que el diámetro interior de los casquillos sea menor que el diámetro exterior de los inyectores. El acabado (escariado) es menos riesgoso: cuando los manguitos han sido redondeados por dentro, el diámetro es óptimo para los inyectores y la estanqueidad mediante las juntas tóricas está garantizada. La altura de las furgonetas es importante; El inyector no debe colocarse demasiado dentro del colector. El extremo del inyector no debe obstruir el flujo de aire. A partir de la información de la fuente: (Banish, Engine Management, advanced tuning, 2007) se decidió montar los inyectores tan profundamente en el colector que los extremos queden exactamente en los orificios del colector; el flujo de aire no se ve obstaculizado.
- Inyección de combustible: debido a que la mezcla de la niebla de combustible con el aire es óptima antes de que se abra la válvula de admisión, no importa mucho si el inyector inyecta exactamente en la válvula de admisión o justo antes en el colector de admisión.
En la inyección simultánea, la inyección se realiza con cada rotación del cigüeñal (360°). Los cuatro inyectores inyectan simultáneamente. Esto significa que también se inyecta combustible en el tracto de admisión cuando la válvula de admisión no está abierta. Algún tiempo después, la válvula de entrada se abre y el combustible todavía ingresa al cilindro.
Los casquillos se cortan especialmente a medida en un torno. El diámetro interior es ligeramente menor que el diámetro exterior del inyector; Debido a que la deformación tiene lugar durante el proceso de soldadura, debe existir la oportunidad de eliminar material durante el posprocesamiento mediante escariado. Esto significa que el diámetro aumenta ligeramente porque el material se elimina. El diámetro no debe ser demasiado grande, porque entonces existe la posibilidad de que la junta tórica de goma del inyector ya no pueda sellar lo suficientemente bien. Un buen sello es muy importante; La fuga de aire que pasa por el inyector da como resultado un vacío más bajo en el colector de admisión.
La presión negativa medida ya no corresponde a la presión negativa calculada. Esto afecta a la inyección, que se determina basándose en la tabla VE. La presión negativa juega un papel importante en esto. Las características y configuraciones de la mesa VE se describen en el siguiente capítulo.
Se ha limado un borde biselado en la parte inferior de los casquillos para que las formas coincidan con las del colector de admisión. Entonces la furgoneta debe estar lo más vertical posible. La siguiente imagen muestra el colector de admisión con un recipiente durante el proceso de montaje. El manguito está pegado por un lado, de modo que se puede ver claramente cómo influye la soldadura en el material. No estaba claro si el aluminio del colector contenía demasiada contaminación, lo que dificultaría la soldadura. Esto resultó estar bien. Para evitar que los casquillos se desplacen de su posición durante la soldadura, se perforaron orificios en el colector con antelación y los casquillos se mantuvieron en la posición correcta con una plantilla especialmente hecha a medida. De esta forma los cuatro casquillos quedan soldados por todos lados. Una verificación final mostró que las conexiones entre los casquillos y el colector eran herméticas.
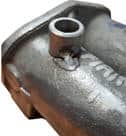
La conexión entre los inyectores normalmente está formada por un carril de inyectores macizo. Este tubo con conexiones, a menudo de aleación de aluminio, lo fabrica a medida el fabricante. El motor Land Rover utilizado para el proyecto tiene dos inyectores uno al lado del otro, pero el espacio entre los pares de inyectores es bastante grande. Las dimensiones del riel de combustible y el espacio entre los conductos de aire del colector de admisión no coincidían. Por lo tanto, fue necesario ajustar el carril.
Acortar algunas piezas y alargar otras mediante soldadura es muy difícil; la contaminación por combustible viejo, muy difícil de eliminar del interior del carril, puede provocar un deterioro de la adherencia. Por tratarse de combustible, se eligió el método más seguro; Las piezas a las que se fijan los inyectores están conectadas mediante una manguera de combustible de alta calidad. Se han colocado bordes cosidos en todos los extremos y se han utilizado abrazaderas de manguera resistentes para evitar que las mangueras se deslicen sobre los bordes cosidos.
La siguiente imagen muestra el colector de admisión en el momento del mecanizado. La línea de suministro (marcada con el número 1) está conectada a la salida de la bomba de combustible. El combustible se suministra a la entrada de los cuatro inyectores bajo una presión de 3 bares. El regulador de presión (3) regula la presión en función de la presión del colector de admisión, ya que la diferencia de presión entre la presión del combustible y el vacío en el colector de admisión debe permanecer en 3 bar. El combustible regresa al depósito a través del tubo de retorno (2). Hay una circulación continua de combustible. La inyección sólo se produce cuando los inyectores están controlados por la ECU MegaSquirt.
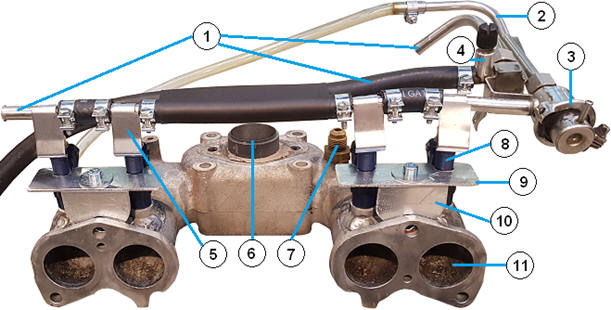
- línea de suministro
- Linea de retorno
- Regulador de presión
- Control de presion
- escudo térmico
- Conexión de válvula de gas
- Conexión de presión negativa
- Cilindro inyector 1
- Soporte del inyector A
- Soporte del inyector B
- Cilindro del conducto de admisión 1
En los turismos existentes, el carril de inyección se fija al colector de admisión mediante abrazaderas u ojales. El riel de inyectores sujeta los inyectores en el colector. Debido a que se eligió una manguera de combustible flexible como riel de inyección para este proyecto, lo mencionado anteriormente no es posible. Por ello se decidió sujetar los inyectores en el colector de admisión con un soporte hecho a medida. Los soportes constan de dos partes: la parte superior (soporte A) y la parte inferior (soporte B).
El soporte A contiene dos muescas que se pueden deslizar sobre los inyectores. Esto permite presionar los inyectores en el colector por medio de los lados planos. Ambos soportes A tienen orificios ranurados para poder ajustar la distancia entre los inyectores y los orificios ranurados. Los soportes A y B están atornillados entre sí: el soporte B está sujeto al mismo perno que sujeta el colector al motor. Un orificio ranurado permite ajustar el soporte en dirección vertical. Cuanto más se mueve el soporte hacia abajo, más firmemente se sujeta el inyector.
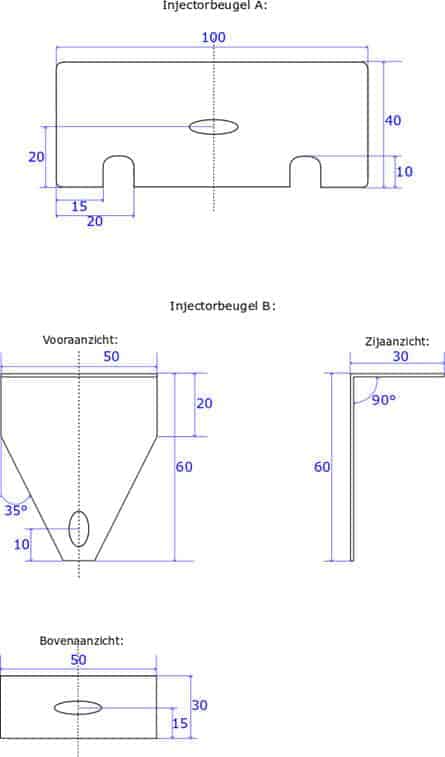
Encendido
El encendido convencional ha sido reemplazado por un sistema de encendido controlado electrónicamente con una bobina de encendido controlada por el MegaSquirt. Para que el motor funcione plenamente con las técnicas originales, inicialmente se debe conectar el sistema convencional con puntos de contacto. Sólo después de varias horas de funcionamiento se puede determinar que el motor funciona correctamente, después de lo cual se puede comenzar con el montaje y ajuste, entre otras cosas, del encendido controlado electrónicamente.
Preparando con el encendido convencional:
El motor Land Rover estaba originalmente equipado con un sistema de encendido con puntos de contacto, que ahora también se denomina sistema de encendido convencional. La imagen muestra este tipo de sistema de encendido.
Con los puntos de contacto cerrados comienza la formación de la corriente primaria. La corriente está limitada a 3 o 4 amperios por la resistencia del devanado primario. Cuando una corriente fluye a través de la bobina primaria de la bobina de encendido, se forma un campo magnético. Tanto la bobina primaria (3) como la secundaria (4) se encuentran en este campo magnético. Cuando la corriente a través de los puntos de contacto (10) es interrumpida por la leva disyuntor (9) en el eje distribuidor, se induce un voltaje en ambas bobinas. En la bobina primaria se producen aproximadamente 250 voltios. La diferencia en los devanados creará un voltaje de inducción de 10 a 15 kV en la bobina secundaria. La chispa de la bujía se crea cuando se abren las puntas.
El voltaje de inducción se puede limitar permitiendo que la corriente primaria fluya durante un tiempo después de abrir los puntos de contacto. Esto se consigue con un condensador conectado en paralelo entre los puntos de contacto. El condensador es un elemento determinante del tiempo que, dependiendo de la capacitancia, en realidad ajusta el nivel de la tensión de inducción. También se evita que se quemen los puntos de contacto.
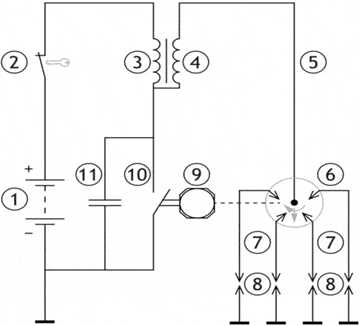
Bobina de encendido para el sistema de gestión del motor:
El sistema de gestión del motor controlará la bobina de encendido. La clásica bobina de encendido con distribuidor permanece en el motor como dispositivo de prueba, pero ya no forma parte del funcionamiento del motor de combustión. Se eligió un sistema de encendido sin distribuidor (bobina de encendido DIS), que se traduce libremente como: “sistema de encendido sin distribuidor”. Este tipo de sistema de encendido no utiliza distribuidor. Otra opción era elegir una bobina de encendido Coil on plug (COP). Se conecta una bobina de encendido separada a cada bujía. Una bobina de encendido COP también se llama bobina de encendido de pasador. La desventaja de una bobina de encendido COP es que la disipación de calor es peor que la de una bobina de encendido DIS. Cuando se utilizan bobinas de encendido COP, también se requiere una señal del sensor del árbol de levas, que no está presente en el motor actual.
El diente que falta en la polea del cigüeñal sirve como punto de referencia para determinar el tiempo de encendido. Con la bobina de encendido DIS, se activarán dos bujías simultáneamente en un momento de encendido. La bobina de encendido DIS es en realidad una unidad en la que están montadas dos bobinas de encendido. Cuando los pistones de los cilindros 1 y 4 se mueven hacia arriba, uno estará ocupado con la carrera de compresión y el otro con la carrera de escape. Aún así, ambas bujías generarán una chispa. La chispa creada por el cilindro que participa en la carrera de compresión provocará una mezcla inflamable. La otra chispa, la llamada “chispa desperdiciada”, se produce cuando los gases de escape salen de la cámara de combustión. La chispa desperdiciada es una chispa que se forma cuando no se enciende ninguna mezcla. La energía de ignición es baja; A pesar de la chispa, hay poca pérdida de energía. Tampoco es perjudicial.
La figura muestra el esquema de funcionamiento de un motor de gasolina de cuatro cilindros con bobina de encendido DIS. Este diagrama de trabajo muestra dos marcas de ignición por momento de ignición; 1 de ellos genera la chispa para encender la mezcla, el otro es la chispa desperdiciada. El MegaSquirt puede controlar una bobina de encendido DIS con solo dos pulsos.
Cuando la carrera de compresión tiene lugar en el cilindro 1 y la carrera de escape en el cilindro 4, el MegaSquirt controla la bobina primaria A a través del pasador 36 en DB37 (ver imagen a continuación). Este control se realiza en función del punto de referencia del cigüeñal (entre 90 y 120 grados antes del PMS). El MegaSquirt controla la bobina primaria B, que es responsable de la formación de chispas de los cilindros 2 y 3, y se gira 180 grados después de la bobina A. No existe un punto de referencia para la bobina B, pero el tiempo de encendido se puede determinar simplemente contando los dientes de la rueda de impulsos 36-1.
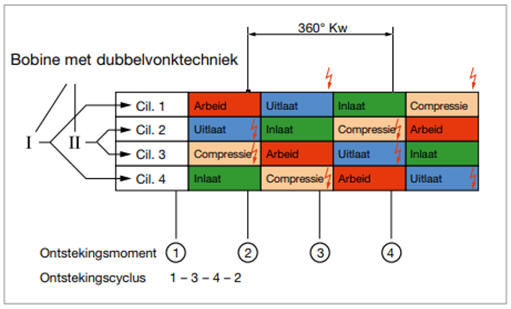
Se muestra una resistencia de 7 ohmios entre la bobina A de la bobina de encendido y el pin 330 del procesador. Esta resistencia limita la corriente y el voltaje de inducción del pulso de conducción. Debido a que esta resistencia no es estándar en la placa de circuito MegaSquirt, se debe actualizar. A la izquierda de la línea discontinua vertical en la imagen de abajo, se muestra el circuito interno del MegaSquirt. Los componentes mostrados (las dos resistencias de 330 ohmios y los LED) tuvieron que soldarse posteriormente a la placa de circuito impreso.
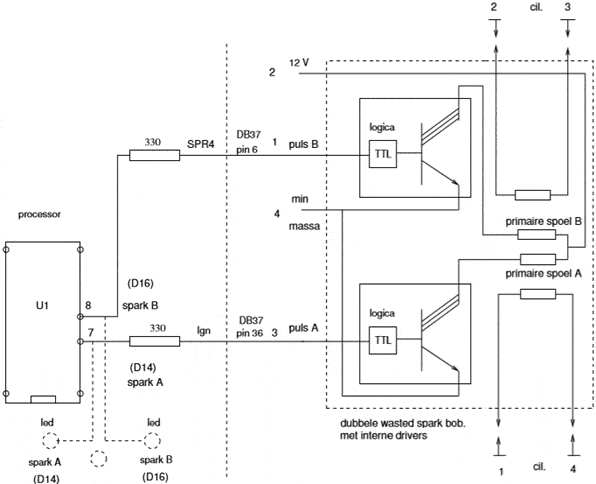
Acumulación de corriente en la bobina primaria:
Es importante conocer la acumulación de corriente en la bobina primaria. Con esto se puede determinar no sólo el amperaje, sino también el tiempo de carga de la bobina de encendido. El tiempo de carga depende de una serie de factores que el MegaSquirt debe tener en cuenta.
El coeficiente de autoinducción (valor L) de la bobina de encendido seleccionada es 3,7 mH. Junto con la resistencia óhmica R se determinan la corriente primaria máxima y el tiempo de subida de la curva. Un pequeño valor L y una resistencia garantizan que la corriente aumente rápidamente después del encendido. A partir de los datos conocidos de la bobina de encendido se puede calcular cómo se genera la corriente primaria.
La siguiente fórmula muestra la solución general de la ecuación diferencial de primer orden, que calcula las corrientes, los tiempos de carga y descarga para mostrar el fenómeno de conmutación como una curva.
La ecuación es:

donde la constante de tiempo (Tau) se calcula de la siguiente manera:

La corriente máxima sería de 28 amperios según la Ley de Ohm:
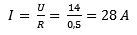
En realidad, este amperaje no se alcanzará.
La bobina se apaga antes. El motivo se explica más adelante. Al ingresar esta información en la fórmula general se obtiene:
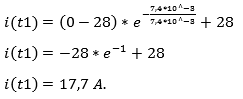
La figura muestra la curva de carga de la bobina primaria. Desde el momento T0 hasta 1 Tau, la bobina se carga al 63,2%. Se trata de un porcentaje fijo del tiempo de carga de una bobina. El resultado de la fórmula 13 muestra que la bobina está cargada con 1 amperios a 17,7 Tau. En t = 5 Tau prácticamente se ha alcanzado el valor final.
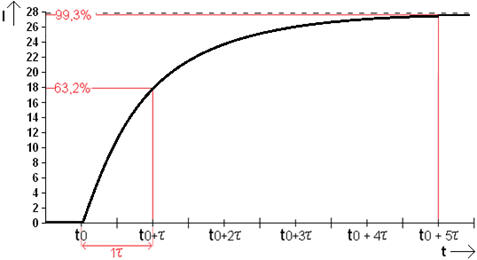
Según las especificaciones de la bobina de encendido, la corriente primaria de la bobina de encendido después de la carga es de 7,5 A. La corriente no aumenta. El tiempo que tarda en alcanzar 7,5 A se llama tiempo de permanencia. El tiempo de permanencia depende del voltaje de la batería, que en este caso es de 14 voltios. Si no se ajusta el proceso de carga, la corriente a través de la bobina es de un máximo de 12 amperios según la fórmula 28.
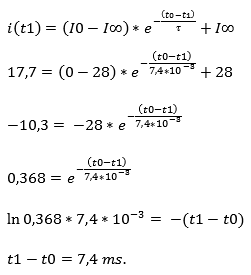
La bobina según la fórmula 14 se carga a 7,4 A en t = 17,7 ms. El tiempo de carga real es más corto porque la bobina se carga hasta un máximo de 7,5 A. El tiempo requerido se puede calcular ingresando los datos conocidos en la fórmula 15.
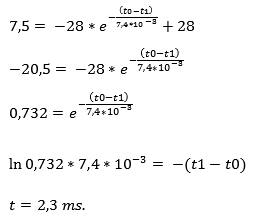
La acumulación de corriente primaria se detiene en 7,5 A. Esto evita que la bobina de encendido se caliente excesiva e innecesariamente. Lo más importante es que la bobina se cargue de forma óptima en el menor tiempo posible. La figura muestra la curva de carga hasta t = 2,3 ms.
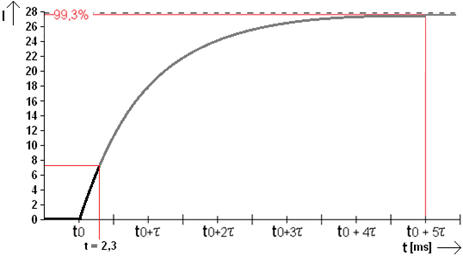
Cuando el voltaje de la batería cae, por ejemplo al arrancar el motor, esto afecta el tiempo de permanencia. Luego se necesitan más de 2,3 ms para alcanzar los 7,5 A. El nuevo tiempo de carga se determina mediante la ya conocida fórmula. La corriente máxima se determina en función del voltaje de la batería:
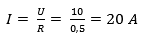
El tiempo de carga hasta 7,5 A con un máximo de 20 A se calcula en la fórmula 17:
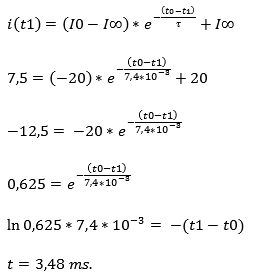
En la figura, el tiempo de carga a 14 voltios se muestra con la línea negra y el tiempo de carga a 10 voltios se muestra con la línea verde. Las líneas bajan a 0 al mismo tiempo; este es el momento del encendido. Debido a que un voltaje de batería más bajo requiere más tiempo para cargar la bobina primaria, el MegaSquirt debe encender la energía primaria antes.
Las líneas negras (ascendentes y descendentes) indican el tiempo de permanencia con una tensión de batería de 14 voltios. La línea verde indica el tiempo de carga avanzado a un voltaje más bajo: esto da Δt. El tiempo de carga real en ese caso es Δt + 100%.
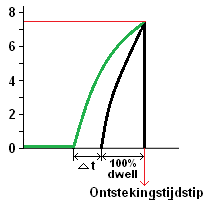
Esto se aclarará más adelante en esta sección con un ejemplo y la figura 36. El tiempo de carga se amplía y el tiempo de encendido sigue siendo el mismo. Si esto no sucede o no sucede lo suficiente, tendrá consecuencias para la energía liberada durante la ignición. En este caso se desconecta la corriente primaria demasiado pronto, de modo que no se alcanza la corriente de 7,5 A. La extensión del tiempo de carga de la bobina primaria (tiempo de permanencia) es, en forma de fórmula, una función del voltaje de la batería. Calcular el tiempo de permanencia a diferentes voltajes da una corriente máxima diferente en la bobina.
Suponiendo que el voltaje de la batería puede caer a 6 voltios durante el arranque y aumentar a 14,7 voltios durante la carga, se puede trazar una curva calculando una serie de valores intermedios. La siguiente imagen muestra la corrección del tiempo de permanencia para la bobina de encendido DIS utilizada. Se coloca un punto (rojo) en el gráfico por cada aumento de 2 voltios. Dado que en el programa TunerStudio se introdujo un tiempo de permanencia previamente introducido de 2,3 ms con una tensión de 14 voltios, a partir de esta tensión se forma un factor de corrección. Por tanto, una tensión de 14 voltios es del 100% (sin corrección).
Ahora quedó claro que el tiempo de carga aumenta hasta un 315% con una tensión de batería de 6 voltios.
El voltaje de la batería puede caer hasta 6 voltios en condiciones desfavorables. Esto significa un debilitamiento de la chispa de encendido. Esto se compensa ampliando el tiempo de permanencia (el tiempo durante el cual fluye la corriente primaria), de modo que se obtiene suficiente energía de ignición incluso con esta baja tensión. Esto significa que Δt de la Figura 36 se triplica (2,3 ms * 315 % = 7,26 ms) en comparación con el tiempo de permanencia del 100 % (2,3 ms) indicado en negro.
Los coeficientes indicados en rojo en la imagen de arriba se pueden copiar directamente al programa TunerStudio.
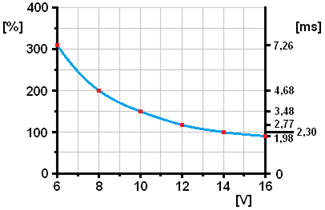
Algún tiempo después de que se haya descargado la bobina primaria, comienza la preparación para el siguiente encendido. Cuanto mayor sea la velocidad del motor, más rápido se recarga la bobina. La Figura 37 muestra dos curvas donde la corriente primaria aumenta a 8,85 A. El tiempo de encendido es en el punto donde la línea cae a 0 A.
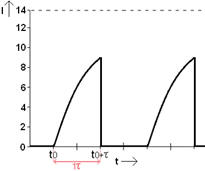
Determinación del momento de encendido:
La señal de encendido se determina a partir del punto de referencia del cigüeñal.
En la corona dentada de la polea del cigüeñal, 36 diente de los 1 dientes ha sido fresado a 100 grados delante del punto muerto superior del pistón del cilindro 1. Entre 100 y 0 grados, por lo que durante la carrera de compresión, el microprocesador de El MegaSquirt puede determinar el momento del encendido. Esto tiene en cuenta el anticipo.
La imagen muestra la imagen del osciloscopio de dos canales en la que la imagen superior muestra el punto de referencia del cigüeñal y la imagen inferior muestra la señal de control del MegaSquirt a la bobina de encendido DIS. La señal de control tiene un voltaje de 5 voltios (un 1 lógico) y dura aproximadamente 1,5 ms.
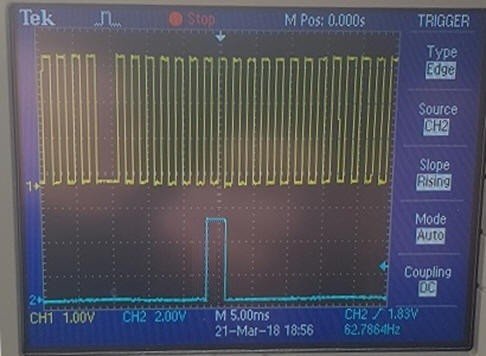
Avance de encendido:
En este proyecto no se utilizan sensores de detonación. Es posible procesar información procedente de sensores de detonación, pero no basta con instalar un sensor de detonación. El procesamiento de las señales es complejo. La señal de detonación primero debe convertirse en una señal de sí/no o en una señal analógica que indique la fuerza de la detonación.
La conversión de las vibraciones del motor en una señal de detonación se realiza mediante un circuito de interfaz. Este circuito no está presente en el MegaSquirt II. Por eso se decidió ajustar de forma segura el avance a plena carga y a carga parcial, para que el motor no pueda acabar en la zona de golpeteo. La curva de avance a plena carga que se va a establecer debe determinarse dentro de los límites de detonación. Los datos de avance centrífugo y de vacío del encendido convencional se determinan con base en los datos de fábrica del manual del motor. Los puntos se pueden trazar en un gráfico (ejemplo en la imagen a continuación).
La línea rosa indica el avance mecánico original. Esto es parcialmente lineal debido a la construcción mecánica de las pesas centrífugas. La línea negra muestra el control del mapa en MegaSquirt; esta línea sigue una curva. Es importante mantenerse alejado de las áreas de impacto de carga parcial y carga completa; por lo tanto, el control del mapa está limitado en carga parcial (línea roja) y el avance en carga completa no aumenta más que en la situación con avance mecánico (línea roja). La disposición real del mapa sigue la línea azul.
Primero, se tuvo que ingresar la curva de avance a plena carga en la tabla de avance de chispa. A velocidades más altas y cargas más bajas, se requerirá más avance. En carga parcial, el avance se suma al avance de carga completa. La tabla completa de avance del encendido y los ajustes de avance cuando el motor está frío se muestran en la página 7.
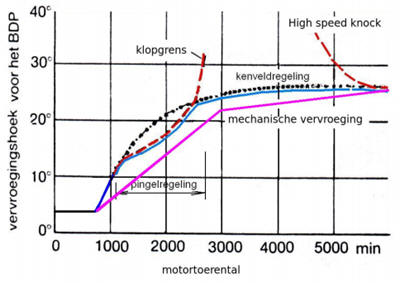
Cuerpo del acelerador:
El suministro de aire/combustible estaba controlado por el carburador en su estado original. Para el sistema de gestión del motor, el carburador se sustituye por un cuerpo del acelerador y cuatro inyectores montados en el colector de admisión. Esto proporciona una inyección más precisa y controlada que con el carburador, donde se forma una mezcla de aire/combustible centralmente en el colector y se divide en cuatro canales. El acelerador se abre mediante un cable Bowden que se acciona manualmente desde el panel de instrumentos.
Después de todo, el MegaSquirt II no admite un cuerpo de aceleración operado electrónicamente. Es por eso que el control por cable Bowden es la única opción a utilizar.
La posición del acelerador se transmite al MegaSquirt mediante una tensión. La magnitud del voltaje depende del ángulo de apertura de la válvula de mariposa. El sensor de posición del acelerador es un potenciómetro con una tensión de alimentación de 5 voltios (ver imagen). Son necesarias la conexión 3 y una conexión a tierra 1. El patín (pin 2) asume una posición en la resistencia que depende de la posición del acelerador. Por lo tanto, el corredor está conectado a la válvula de mariposa. Cuando el corredor tiene que superar una pequeña distancia por encima de la resistencia (el corredor apunta hacia la izquierda), la resistencia es baja. En la imagen, el corredor está colocado a la derecha (el lado de tierra), lo que significa que hay una alta resistencia y por lo tanto un voltaje de señal bajo.
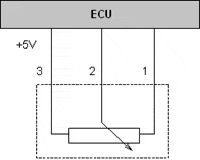
Cuando se utiliza el cuerpo del acelerador, hay un voltaje de 600 mV en el corredor cuando el acelerador está cerrado y un voltaje de 3,9 V cuando la válvula está completamente abierta. La ECU recibe el voltaje y lo utiliza para calcular el ángulo de apertura de la válvula del acelerador. Un aumento rápido en el ángulo de apertura significa que se está produciendo una aceleración; el ECU responde a esto enriqueciéndose brevemente. Esto se llama enriquecimiento por aceleración. El sensor de posición del acelerador no se utiliza para determinar el enriquecimiento de la mezcla en diferentes condiciones de funcionamiento; Para ello se utiliza el sensor MAP.
Configuración de prueba del motor paso a paso con simulador:
Una vez ajustado el hardware del MegaSquirt, se podía utilizar la caja de conexiones para comprobar si se estaba recibiendo el control del motor paso a paso. La iluminación de LED de dos colores indica que se está realizando el control. Los pasos en los que se controla el motor paso a paso se pueden seguir observando el cambio de colores. Los colores alternan entre rojo y amarillo. Los datos del motor paso a paso se pueden ingresar en el menú "Control de ralentí" en el programa TunerStudio. Además del tipo (4 hilos), también se puede configurar el número de pasos. Esto también incluye la posición inicial en la que debe estar el motor paso a paso cuando se arranca el motor. Además, se puede establecer el tiempo que lleva ajustar un paso.
El número de pasos depende, entre otras cosas, de la temperatura del refrigerante; una temperatura más baja requiere una mayor apertura del motor paso a paso. Los pasos relativos a la temperatura se pueden establecer en un gráfico. Con el simulador se puede comprobar si el motor paso a paso está realmente controlado correctamente. Debido a que se verifica primero en el simulador en lugar de en el motor, se pueden evitar problemas durante el arranque o el funcionamiento del motor debido a un posible problema de hardware o software. Debido a que la temperatura del refrigerante y la velocidad del motor influyen principalmente en el ángulo de apertura del motor paso a paso, puedes comprobar si el control es correcto girando estos potenciómetros. El medidor en el tablero de TunerStudio mostrará el ajuste en el número de pasos ajustados.
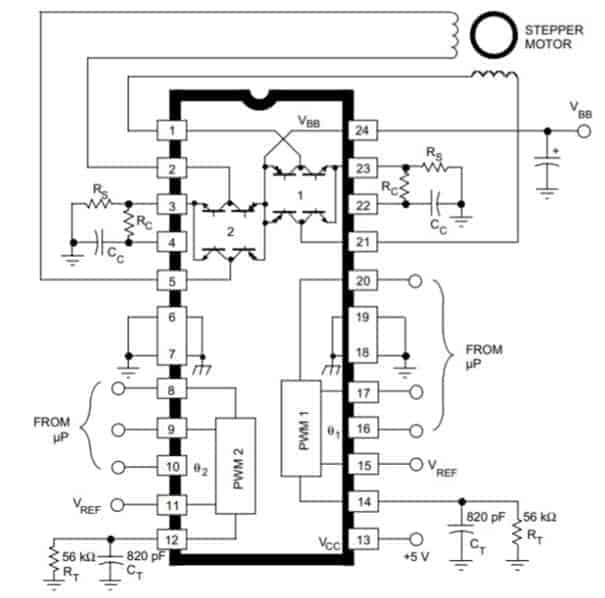
Configuración del motor paso a paso:
La figura muestra la pantalla de configuración del motor paso a paso utilizado para la velocidad de ralentí (control de ralentí).
Los pasos en los que se ajusta el motor se determinan de antemano mediante un Arduino. También se debe introducir el número de pasos para desplazarse a su posición básica (pasos de inicio). El motor paso a paso está activo en la fase de calentamiento (algoritmo) y energiza las bobinas en reposo (mantiene la corriente entre pasos).
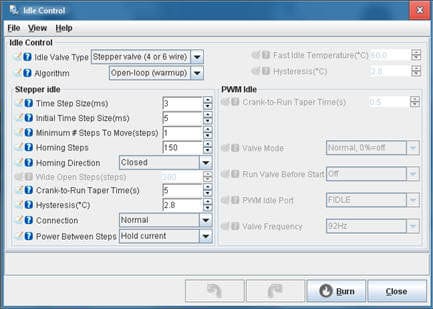
La posición del motor paso a paso depende de la temperatura del refrigerante. Al arrancar un motor frío, la válvula debe estar abierta un poco más que al arrancar un motor calentado. La siguiente imagen muestra la pantalla de configuración para configurar los pasos (Steps) en relación con la temperatura del refrigerante (Coolant). Cuando el motor está frío, el motor paso a paso se abre completamente mientras el motor está en ralentí. Durante la fase de calentamiento el motor paso a paso se cierra ligeramente.
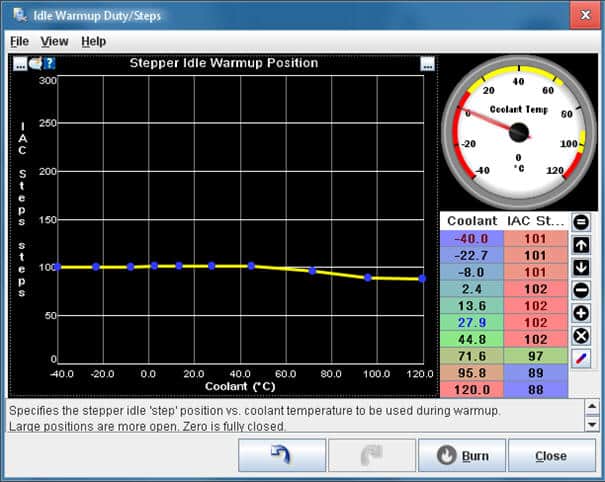
También es posible ajustar la posición del motor paso a paso según la temperatura del refrigerante al arrancar el motor. Esto se denomina “Pasos/servicios de arranque en ralentí”. La siguiente imagen muestra la pantalla de configuración.
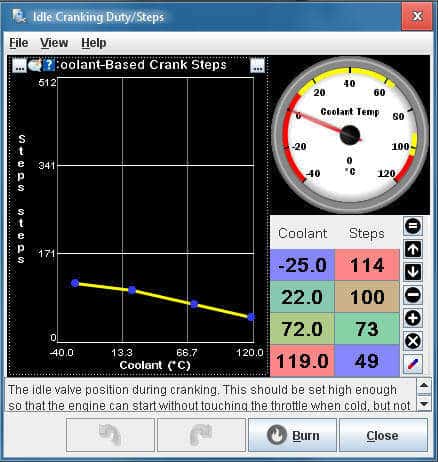
Circuito de la bomba de combustible:
El MegaSquirt garantiza que la bomba de combustible esté encendida y apagada. El transistor Q19 en la figura siguiente protege el transistor Q2 contra una corriente excesiva. Si la corriente es demasiado alta, el transistor puede quemarse. Cuando aumenta la corriente a través de la porción colector-emisor de Q2 y R40, se alcanza el voltaje de saturación en la base de Q19. El transistor Q19 se activa, lo que hace que disminuya el voltaje base-emisor en Q2.
La conexión FP-1 PTA0 está controlada internamente por el MegaSquirt. Se requiere una señal de entrada del sensor de posición del cigüeñal (un sensor Hall o sensor inductivo) para controlar el circuito del transistor. Si se pierde la señal, por ejemplo si el motor se cala involuntariamente, se interrumpe inmediatamente el suministro de energía a la bomba de combustible.
La salida del circuito del transistor (FP1 OUT) está conectada al relé de la bomba de combustible. El pin 85 del relé es la salida de la corriente de control. Con un relé energizado, la sección de alimentación principal (pin 30 y 87) se conmuta, de modo que la bomba de combustible recibe un voltaje de suministro para funcionar.
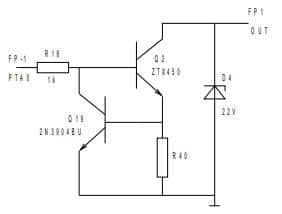
Se utiliza una bomba de combustible electrónica con una presión de funcionamiento de 3 bar. El combustible pasa a través del filtro de combustible hasta la rampa de combustible, donde la presión se encuentra en la entrada de los inyectores. El inyector inyectará una cantidad precalculada de combustible en el colector de admisión cuando llegue una señal del MegaSquirt. El control del MegaSquirt no sólo determina la cantidad de combustible inyectado, sino también la presión del combustible en el riel.
A mayor presión del riel, se inyectará una mayor cantidad de combustible con el mismo control. Por lo tanto, la presión del raíl debe ajustarse en función de la presión negativa en el colector de admisión. La diferencia de presión (∆P) debe permanecer en todo momento en 3 bar. La figura muestra el esquema del sistema de combustible. Las líneas rosa, amarilla, naranja y negra muestran las conexiones eléctricas. La línea roja indica el suministro de combustible y la línea azul el retorno de combustible.
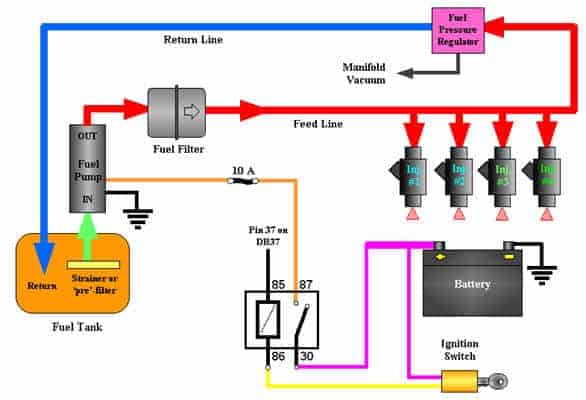
Finalización del trabajo mecánico:
Las siguientes tres fotografías muestran el motor en las etapas finales de modificaciones mecánicas.
Foto 1:
Este es el lado donde son visibles la mayoría de las piezas aplicadas. El tablero para los controles y la ECU MegaSquirt también se encuentran aquí. Debajo de la foto hay una leyenda con la descripción de los números de las piezas. Puedes abrir las fotos en un tamaño mayor haciendo clic sobre ellas.
- La válvula del acelerador;
- Línea de combustible para los inyectores;
- Tubo de conexión para válvula de mariposa en el colector de admisión;
- Manómetro de combustible;
- Colector de admisión y escape;
- Tablero de instrumentos con interruptor del ventilador de refrigeración, luces para alternador y presión de aceite, interruptor de encendido e interruptor de tierra;
- Manguera de vacío para sensor MAP;
- sonda lambda;
- Mangueras de combustible (suministro y retorno) juntas en una caja retráctil;
- Unidad de bomba/depósito de combustible;
- Relé de la bomba de combustible;
- megachorro;
- Silenciador de escape.
Foto 2:
Esta foto muestra el otro lado del motor. Aquí se puede ver el carburador (15) y el encendido convencional (17). El propósito de este encendido clásico es hacer que las bujías en la configuración de prueba (14) chispeen. Por supuesto, esto no tiene ninguna función para el motor, pero proporciona información sobre el funcionamiento del encendido tal como funcionaba en los coches clásicos.
El número 20 indica el mecanismo de freno de la transmisión. La varilla del tambor de freno se puede apretar con un cable Bowden, de modo que se frene el eje de salida de la caja de cambios. El freno de la transmisión se aplica para cargar brevemente el motor cuando se engrana una marcha.
Foto 3:
Aquí se puede ver claramente la vista superior del motor con el dispositivo de prueba para el encendido y el conducto de combustible.
Se han completado los ajustes mecánicos. El motor aún no se puede arrancar porque primero se deben ingresar algunos datos en el MegaSquirt.
Siguiente: Ajuste de la ECU del MegaSquirt II.