Asignaturas:
- El comienzo del proyecto.
- Motor
- Caja de cambios
- Inspeccionar, reemplazar y ajustar piezas del motor.
- Montar el motor en un bastidor móvil.
- Enfriamiento
- Cuadro de mandos e instalación eléctrica.
- Bomba de combustible y tanque
- Opere el motor en una configuración clásica.
El comienzo del proyecto:
Después de que se decidió equipar un motor con un sistema de gestión de motor MegaSquirt, se consideró un tipo de motor adecuado. Los paquetes de conversión estándar con manuales no eran interesantes. El objetivo era utilizar un motor que cumpliera las siguientes condiciones:
- no se deben conocer proyectos de conversión anteriores de este motor;
- motor de gasolina de cuatro cilindros;
- aún no equipado con un sistema de inyección y encendido electrónico;
- la capacidad de cargar el motor.
Motor:
La búsqueda dio como resultado un motor de un Land Rover (serie 2A) de principios de los años 70. Este motor de gasolina de cuatro cilindros y 2,25 litros con tres cojinetes principales estaba originalmente equipado con carburador y encendido por distribuidor mecánico. La combinación de este motor Land Rover y la caja de cambios original fue decisiva para la elección; Un freno de transmisión está conectado al eje de salida de la caja de cambios. El freno de la transmisión, que en realidad sirve como freno de estacionamiento, permite cargar el motor en marcha aplicando este freno.
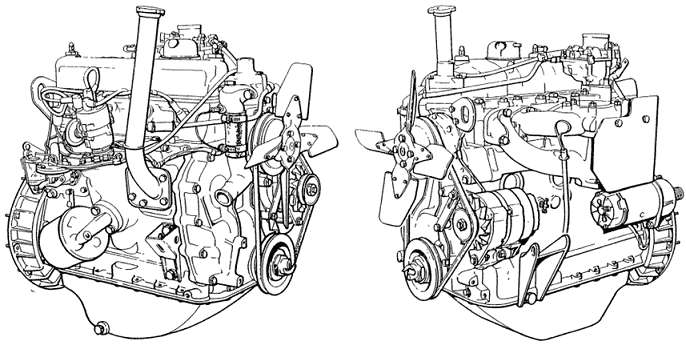
Probablemente el motor llevaba décadas sin funcionar. Naturalmente, debe ser lo suficientemente fiable como para funcionar con el sistema de gestión del motor. Por lo tanto, primero fue necesario inspeccionar y probar minuciosamente el motor. Se establecieron los siguientes objetivos:
- Inspeccionar, reemplazar y ajustar piezas del motor;
- Montar el motor sobre un bastidor móvil;
- Permitir que el motor funcione en la configuración clásica;
- Instalación de componentes para el sistema de gestión del motor;
- Ensamble y prepare la ECU MegaSquirt;
- Permita que el motor funcione en el sistema de gestión del motor.
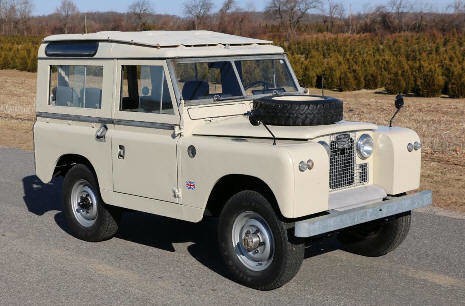
Caja de cambios:
La caja de cambios procede de un Land Rover militar. El color verde lo delata: para poder formar un conjunto lo más original posible con el motor en un futuro, se ha quitado la pintura verde. El freno de la transmisión aún no está presente en la foto; Posteriormente se montó en el eje de salida de acuerdo con las instrucciones de fábrica.
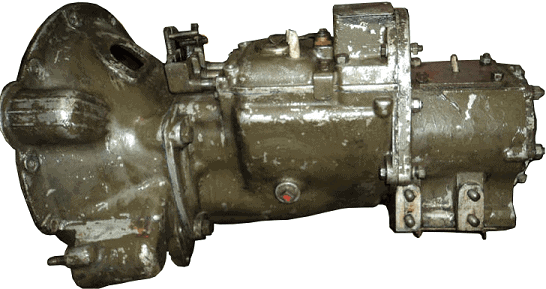
Inspeccionar, reemplazar y ajustar piezas del motor:
Al principio del proyecto no estaba claro si el motor disponible era adecuado para su uso. Poco se sabía sobre el bloque del motor, sólo que el motor había estado parado durante años. No estaba claro si alguna pieza interna estaba dañada o incluso, posiblemente irreparablemente, defectuosa. En este último caso, sustituir el motor por otro era la única opción para retomar el proyecto.
Para no llegar a la conclusión posterior de que el motor quedaría inutilizable, se decidió desmontarlo y revisarlo. Se comprobaron los patrones de desgaste de las piezas y se compararon con las especificaciones de fábrica. Se han sustituido las piezas cuyas medidas estaban dentro de estas tolerancias. Las piezas que fueron rechazadas han sido reemplazadas. Se ha tenido en cuenta la finalidad para la que se utilizará el motor; el motor debe construirse con el menor costo posible para que sea lo suficientemente confiable para la implementación del proyecto y su uso como herramienta de enseñanza-aprendizaje.
El motor está sujeto al soporte de montaje en los puntos de montaje de la carcasa de la caja de cambios. El motor se puede girar en diferentes posiciones. Esto hace que tanto la culata como el cárter de aceite sean perfectamente accesibles para los trabajos de desmontaje. Para el correcto funcionamiento del motor es importante tomar precauciones para asegurar una buena presión final de compresión. Si la presión en uno o más cilindros es demasiado baja, el resultado es un motor que funciona mal y falla. En ese caso, el ajuste con el encendido recién instalado y el sistema de inyección será difícil, si no imposible.
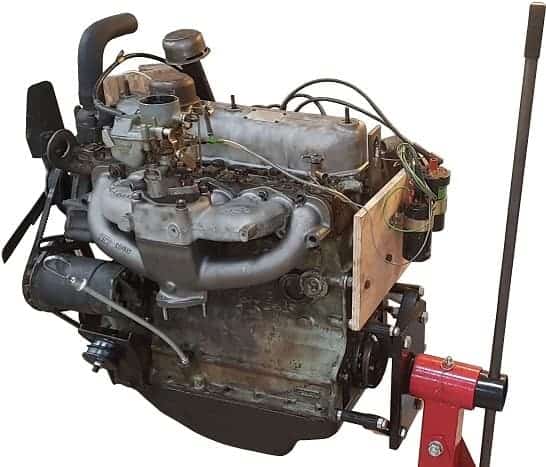
Uno de los primeros puntos de control son los pistones y las paredes del cilindro. Para ejercer un control adecuado, era necesario retirar los pistones del bloque del motor. Después de desmontar la culata y el cárter de aceite, se pudieron quitar los pistones. Los pistones han sido revisados para detectar ovalidades y signos visibles de desgaste. También se ha comprobado el desgaste de los aros del pistón. Los aros de pistón desgastados pueden provocar pérdida de compresión y consumo de aceite; Ambas consecuencias deben evitarse mediante este control. Además de la comprobación óptica, también se midió el juego entre las ranuras de los segmentos del pistón y el segmento del pistón.
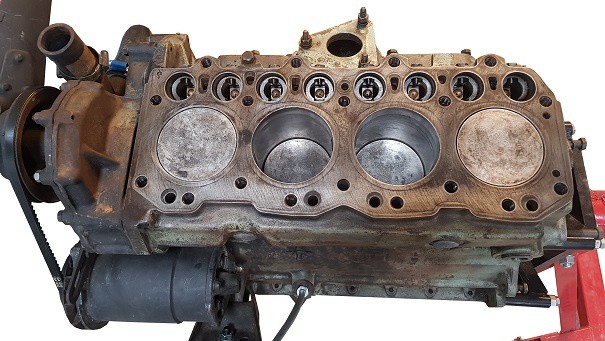
La siguiente imagen muestra una medición donde el pistón se mide con un calibre de tornillo. Además de la ovalidad, también se puede determinar la distancia entre el pistón y la pared del cilindro. Una distancia demasiado grande significa un desgaste excesivo. Para el proyecto, esto significaría que es posible que sea necesario instalar otros pistones sobrantes. Después de evaluar visual y geométricamente los cuatro pistones, se determinó que no había desgaste excesivo.
Después de sustituir los aros de pistón, se debe medir el juego final y, si es necesario, ajustarlo para evitar que el aro se rompa (debido a un juego demasiado pequeño o demasiado grande) y para evitar la pérdida de compresión (pérdidas por fugas debido a un juego demasiado grande). ). El segmento del pistón se coloca en el cilindro cuyo diámetro es menor. La holgura de la cerradura se mide con una galga de espesores. Esta medida se muestra en la figura. Los aros del pistón del cilindro 1 fueron reemplazados por su mal estado y debieron limarse un milímetro más pequeños; Cuando se ensamblaron, los extremos se tocaron entre sí.
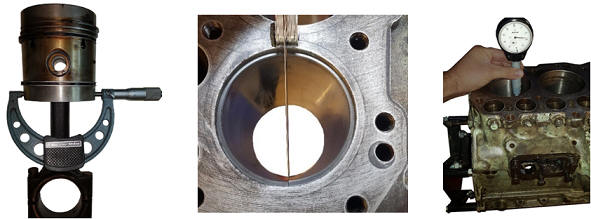
La medición del desgaste de las camisas de los cilindros se realiza con un objeto de medición adecuado. La desviación del puntero muestra el grado de desgaste. La imagen muestra la medida del cilindro 4. El diámetro del cilindro habrá aumentado, especialmente en el lado donde se produce la fuerza de deslizamiento. Las paredes del cilindro pueden mostrar algo de desgaste, pero el desgaste debe estar dentro de las tolerancias. Los resultados de las mediciones mostraron que había un desgaste aceptable en las paredes del cilindro. Una inspección óptica de las camisas de los cilindros mostró que algunas partes de las paredes estaban lisas. Las ranuras de bruñido ya casi no estaban presentes.
Las ranuras de bruñido, una especie de pequeños rasguños, consiguen que en todo momento haya una pequeña película de aceite entre el segmento del pistón y la pared del cilindro. La función principal de esta película de aceite es la lubricación, pero también sirve como sello y, por lo tanto, ayuda a alcanzar la presión de compresión final. Se hicieron nuevas ranuras de bruñido en las cuatro camisas de cilindro utilizando una piedra de bruñido adecuada. La imagen muestra esta operación. Se ha intentado aplicar las ranuras de bruñido lo más transversalmente posible, en un ángulo de 45 grados.
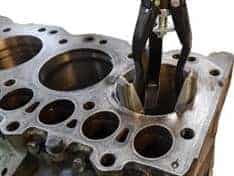
Las válvulas sellan el espacio de combustión encima del pistón. Las fugas a lo largo del asiento de la válvula provocan una pérdida de compresión; algo que debería prevenirse. Para comprobar el estado de las válvulas y del asiento de válvulas, primero se deben retirar todas las válvulas de la culata. La imagen muestra un resorte de válvula desmontado de la válvula de admisión del cilindro 1. Los discos de las válvulas del cilindro 1 estaban tan dañados que se decidió reemplazar ambos.
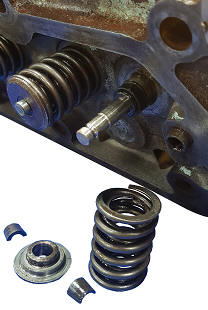
Después del desmontaje, varios asientos de válvulas parecían estar comidos o afectados. La siguiente imagen muestra los asientos de válvulas del cilindro 1. Es muy probable que el motor no hubiera funcionado correctamente si no se hubiera revisado. Simplemente volver a lijar las válvulas nuevas no sería suficiente, por lo que se decidió fresar los asientos de las válvulas.
Con un cortador de asientos de válvula se retira una pequeña cantidad de material para que el asiento de la válvula vuelva a quedar liso. El vástago del cortador se desliza dentro de la guía de la válvula (vea la imagen a continuación). Esto garantiza que la cortadora se pueda colocar recta sobre el asiento. Durante el proceso de mecanizado se tuvieron en cuenta dos ángulos diferentes en los que se debe realizar el fresado. Las válvulas de los cilindros 1 y 2 fueron las más afectadas. Para que esté completo, los ocho asientos de válvula han sido mecanizados. Después del fresado, las válvulas se lijan con un abrasivo especial para garantizar el mejor sellado posible.
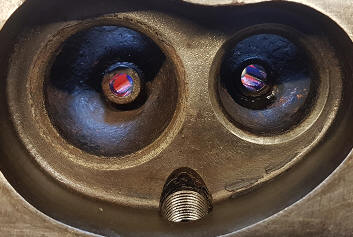
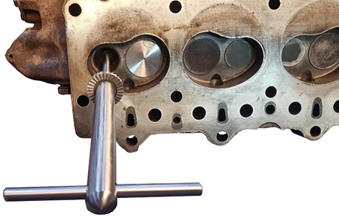
El juego axial del cigüeñal con tres cojinetes principales y dos cojinetes axiales se mide con un comparador. Si hay demasiado juego axial, se puede instalar un rodamiento axial más grande si no hay ningún defecto mecánico. La medición que se muestra en la imagen mostró que el juego axial estaba bien.
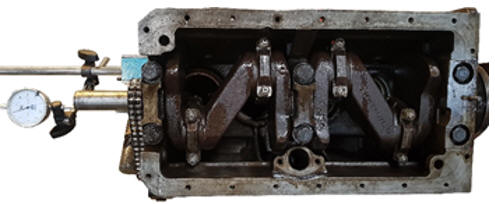
El espacio entre los cojinetes de deslizamiento del cigüeñal y la biela, es decir, el juego radial del cigüeñal, se mide con plastigage (ver figura). Plastigage es un alambre de plástico especial que se deforma permanentemente después de la compresión. Después de montar la tapa del cojinete o la biela, el plastigage dejará una huella. El ancho de la impresión indica cuánto juego hay entre el cojinete deslizante y el cigüeñal.
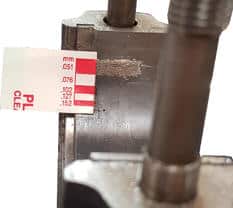
La cadena de distribución transmite el movimiento del cigüeñal al árbol de levas. Después de instalar los pistones, el cigüeñal y la culata, se debe reajustar la cadena de distribución después de la instalación. Debido a la falta de ajuste y de marcas, el ajuste tuvo que determinarse basándose en el diagrama de válvula asimétrico. Usando un disco graduado en el cigüeñal, se puede determinar el ángulo en el que se abren y cierran las válvulas de admisión y escape (ver imagen). Se ha comprobado el desgaste óptico de los elementos de distribución como piñones, cadena, guía y tensor. Esto estuvo bien.
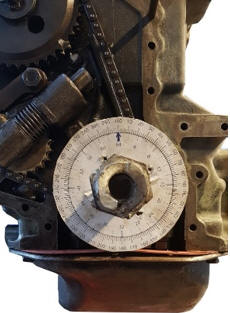
Todas las piezas se aprietan según los pares de apriete prescritos. Como el motor está desmontado, es necesario realizar controles después de varios kilómetros recorridos. Sin embargo, esto no es posible porque el motor no está instalado en un vehículo. Por ello se ha decidido realizar los controles prescritos por Land Rover después de 24 horas de funcionamiento.
Montaje del motor en el bastidor móvil:
El objetivo era utilizar el motor como herramienta de enseñanza, ejecutándolo en un sistema de gestión del motor. El motor no se coloca en un coche. Para garantizar una configuración segura y fiable, se decidió colocar el motor en un bastidor adecuado. La intención es que el motor esté sujeto al bastidor del motor en las ubicaciones originales de los soportes del motor. Como no existen kits de conversión ya preparados, los soportes tuvieron que fabricarse a medida.
En la fase de construcción, hubo que elegir cómo se construiría el motor. El sistema de gestión del motor debe ajustarse cuando la carga del motor aumenta. Debido a que la caja de cambios original tiene un freno de transmisión, se decidió montar también la caja de cambios en el bastidor del motor. Al accionar este freno de transmisión es posible hacer funcionar el motor bajo carga durante un breve periodo de tiempo.
La edición y adaptación de los soportes del motor existentes ha hecho posible conectar el motor al bastidor de forma fiable. El bastidor del motor también ofrece la posibilidad de colocar un tablero de instrumentos en el que, entre otras cosas, se pueden realizar los controles. La imagen muestra el momento en que el motor está colgado sobre el marco y listo para ser acoplado.
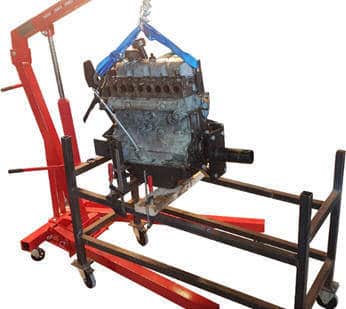
Los soportes del motor en el lado de distribución están fabricados con tubos de acero y perfiles en U. Una goma de motocicleta proporciona la amortiguación. Se montan dos tubos uno encima del otro en la parte inferior para montar la combinación del bloque del motor y la caja de cambios lo más horizontalmente posible en el bastidor. Los soportes se fijan al bloque del motor y al bastidor mediante varillas roscadas, pernos y tuercas M8 y M12.
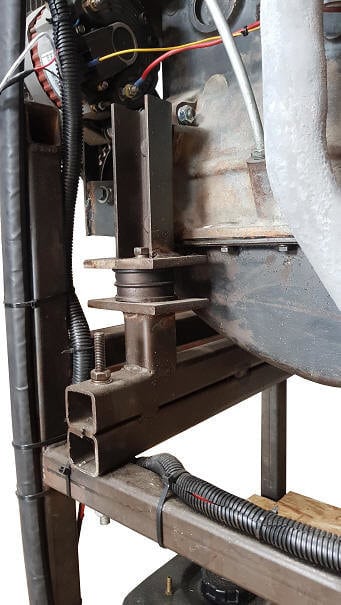
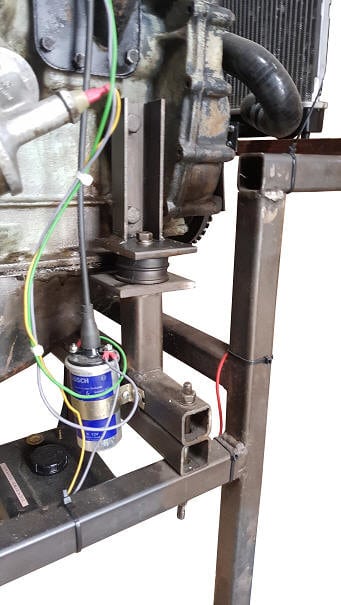
Se ha realizado un soporte de caja de cambios de este tipo a ambos lados de la caja de cambios con el que se apoya sobre el bastidor.
Una vez montados el motor y la caja de cambios en el bastidor de forma segura y fiable, se pudo reanudar el montaje del motor. Luego de instalar piezas ajustables y regulables, como el carburador y el encendido, estas fueron ajustadas según los valores de fábrica.
Otros componentes que permiten el funcionamiento del motor también están montados en el bastidor, como el radiador, el tablero con controles y el tanque de combustible. Estos componentes se describen en los siguientes párrafos.
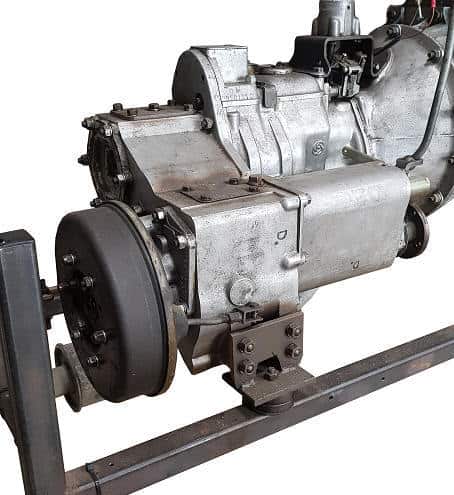
Enfriamiento:
En su estado original, la refrigeración se logra mediante un radiador grande y un ventilador de refrigeración metálico montado en la bomba de agua. Dado que el motor no está instalado en un vehículo, sino en un bastidor móvil, es importante utilizar componentes de posventa adecuados. El ventilador de enfriamiento de metal fue reemplazado por un ventilador de enfriamiento eléctrico con aspas de plástico. La versión de plástico no sólo es mucho más segura, ya que el motor está diseñado para fines educativos (tenga en cuenta la seguridad personal al tomar medidas), sino que también es más adecuada para calentar más rápidamente el radiador y el bloque del motor. El ventilador de refrigeración eléctrico se puede encender y apagar con un botón en el tablero. Esto permite calentar el motor rápidamente, porque hay pocas posibilidades de someterlo a una carga mecánica. Cuando el motor se calienta, es más probable que se produzca un "circuito cerrado" en el que los datos del sensor lambda se utilizan para controlar la inyección de combustible. Por ejemplo, cuando el motor está frío – en “circuito abierto” – se produce un enriquecimiento adicional: al inyectar una cantidad mayor de combustible (λ < 1), la corrección del combustible mediante la sonda lambda no es deseable.
La figura muestra una descripción general de los componentes del sistema de refrigeración instalado. El radiador original no estaba presente. Debido a que su tamaño y peso no eran adecuados para montarlo en el chasis de la motocicleta, se eligió un radiador de posventa más pequeño. Los diámetros de las conexiones de los manguitos superior e inferior del radiador corresponden a los originales.
Las mangueras superior e inferior del radiador están hechas a medida con mangueras y conectores de silicona. El ventilador de refrigeración eléctrico está asegurado a un soporte de montaje. La manguera superior del radiador protege el radiador contra vuelcos. Una tapa de sobrepresión (0,9 bar) protege el sistema de refrigeración contra una presión excesiva. Cuando la presión aumenta demasiado, la válvula en la tapa del radiador se abre contra la fuerza y el refrigerante fluye a través del rebosadero hacia un recipiente colector.
Hubo que determinar experimentalmente si el radiador tenía un caudal suficientemente alto y si el ventilador de refrigeración tenía suficiente capacidad para disipar el calor. Durante la primera fase de prueba se comprobó que el sistema estaba en orden.
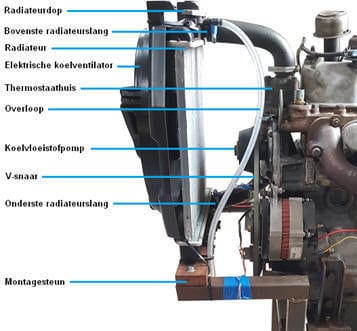
Cuadro de mandos e instalación eléctrica:
Se adjunta un tablero al marco en el que se encuentran las luces indicadoras, los interruptores, la ECU MegaSquirt, varios relés y haces de cables. El tablero se utiliza para monitorear y controlar las funciones del motor.
La imagen muestra el tablero. El número 1 en la figura indica la ubicación del seccionador de tierra; una llave desconecta la batería de tierra. Dado que no es necesario aplicar energía al motor apagado, es más seguro desconectar la tierra cuando el motor se deja desatendido. El número 2 indica el interruptor del ventilador de refrigeración. Los números 3 y 4 son las luces indicadoras del alternador (D+), el número 5 es el botón de arranque y el número 6 es el interruptor de encendido (terminal 15). Hay una caja de fusibles en la parte trasera del tablero. El MegaSquirt está montado en el panel inferior y está indicado con el número 7. El número 8 indica el relé de la bomba de combustible. El tablero también ofrece la opción de montar una caja de conexiones en la que los estudiantes pueden tomar medidas. Esto permite medir los valores del sensor y los controles del actuador con el osciloscopio.
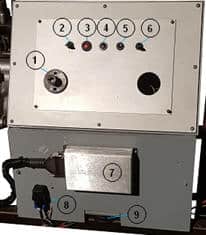
El relé de arranque original controla el motor de arranque; Con un pequeño botón de inicio, el pin 86 se conecta a tierra, lo que provoca que fluya una corriente de control. La corriente de control proporciona un campo magnético, lo que hace que fluya una corriente principal entre los terminales 30 y 87; el motor de arranque recibe esta corriente principal hasta que se suelta el botón de arranque.
El alternador reequipado proporciona la tensión y la corriente de carga a la batería. Una luz indicadora indica si el alternador se está cargando correctamente. La sonda lambda, los inyectores y la bobina de encendido reciben tensión de alimentación de la caja de fusibles. La transferencia de información y los comandos de encendido y apagado del MegaSquirt se realizan a través de otros cables de señal y de tierra.
Bomba y tanque de combustible.
La bomba de combustible mecánica en la configuración clásica ya no se utiliza al instalar los componentes del sistema de gestión del motor porque la presión de funcionamiento es demasiado baja (200 mbar). La presión de combustible requerida para los inyectores MPI controlados por la ECU MegaSquirt es de 3 bar. Basta con una bomba de combustible electrónica estándar de un turismo. Debido al espacio limitado, se eligió una unidad compacta, en la que el tanque de combustible, la bomba y el filtro están en una sola carcasa. Un marco de metal permite montar la unidad en el marco del motor. En una etapa posterior del proyecto, se instalarán las mangueras de combustible que forman la conexión entre la bomba de combustible y los inyectores en el colector de admisión.
Los cables de alimentación de la bomba de combustible discurren a través de un conducto para cables hasta el panel de instrumentos, cuya instalación ya se ha descrito. El MegaSquirt energiza el cable positivo de la bomba a través de un relé.
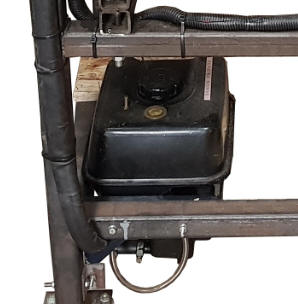
Opere el motor en una configuración clásica.
Antes de instalar los componentes del sistema de gestión del motor, el motor se puso inicialmente en funcionamiento con la configuración clásica, es decir, con carburador y encendido por distribuidor. El Capítulo 5.2 describe el trabajo que se llevó a cabo para montar el motor y los componentes auxiliares en el bastidor del motor. En la primera fase de prueba, en la que se arrancó el motor en la configuración clásica, las comprobaciones se pudieron realizar en las siguientes condiciones:
- Inicio fresco;
- De marcha en vacío;
- Mayor velocidad, mayor carga;
- Funcionamiento a largo plazo a temperatura de funcionamiento.
Durante las comprobaciones anteriores resultó que todavía era necesario realizar una serie de reparaciones antes de que el motor fuera lo suficientemente fiable para la conversión.
- Después del primer arranque del motor, resultó que la junta de la bomba de refrigerante ya no estaba en orden; el refrigerante se fugó del bloque del motor a lo largo del cojinete. Reemplazar la bomba de refrigerante fue suficiente para resolver el problema.
- El siguiente problema fue el calado cuando el motor alcanzó la temperatura de funcionamiento. El encendido falló, lo que hizo imposible arrancar el motor. El problema estaba en el distribuidor y se resolvió fácilmente.
- Con el tiempo, se formó una fuga de aceite entre el motor y la caja de cambios. La fuga probablemente proviene del sello del cigüeñal. Esta fuga se resolverá una vez finalizado el proyecto.
Una vez que se comprobó que el motor estaba en orden en la configuración clásica, pudimos continuar con la electrónica.
Siguiente: Sensores.