Asignaturas:
- Inyección indirecta y directa.
- Control de presión de combustible con inyección indirecta.
- Estrategia de inyección inyección multipunto
- Inyector electromagnético (MPI)
- Inyector piezoeléctrico (DI)
- Estrategias de inyección inyección directa
- Doble inyección
- Medición de características de voltaje y corriente en un inyector multipunto.
- Sincronización de la inyección en relación con la posición del cigüeñal.
- Limitación de corriente de la ECU
- Determinación de la cantidad requerida de combustible.
- mesa VE
- tabla AFR
Inyección indirecta y directa:
Los tipos de sistemas de inyección de un motor de gasolina se dividen en inyección indirecta por la válvula de mariposa, inyección indirecta por cilindro e inyección directa de alta presión. Los párrafos de esta página explican estos diferentes sistemas de inyección.
Inyección indirecta:
Hay un inyector delante de la válvula de mariposa. El combustible se rocía contra la válvula de mariposa, donde se mezcla con el aire que pasa. La principal desventaja es que no existe una dosificación precisa de combustible por cilindro; un cilindro siempre recibe un poco más o menos que el otro. Por lo tanto, el sistema no es ajustable y, por lo tanto, ya no se utiliza teniendo en cuenta los requisitos medioambientales. Este sistema también se llama inyección central (Monopoint).
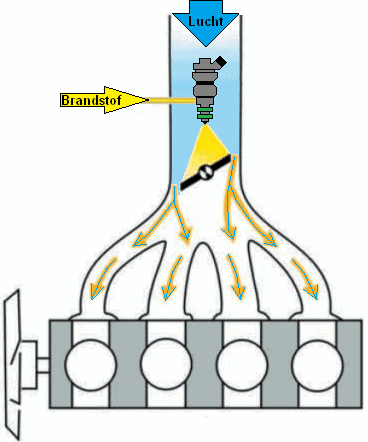
Inyección indirecta:
Cada cilindro tiene su propio inyector. El inyector inyecta combustible en la válvula de admisión. El aire que pasa también asegura la mezcla en este sistema antes de que la mezcla de aire y combustible ingrese a la cámara de combustión. La ventaja sobre la inyección indirecta es que la cantidad de combustible se puede controlar con mucha más precisión. Este sistema también se llama MPI (Inyección multipunto) o PFI (Inyección de combustible por puerto).
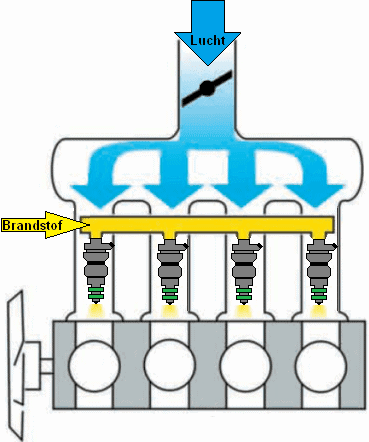
Inyección directa:
Los inyectores para DI (Inyección Directa) o DISI (Inyección Directa de Encendido por Chispa) están ubicados al lado de la bujía, en la parte superior de la cámara de combustión. El combustible se inyecta a través de este inyector a una alta presión de aproximadamente 200 bar durante la carrera de admisión. Las principales ventajas de este sistema son que la cantidad de combustible se puede ajustar con mayor precisión, que las inyecciones se pueden realizar varias veces durante la carrera de admisión y que la mezcla de aire y combustible es más fría. Esto permite a los fabricantes aumentar la relación de compresión del motor. El inyector puede estar diseñado como inyector piezoeléctrico o de bobina magnética.
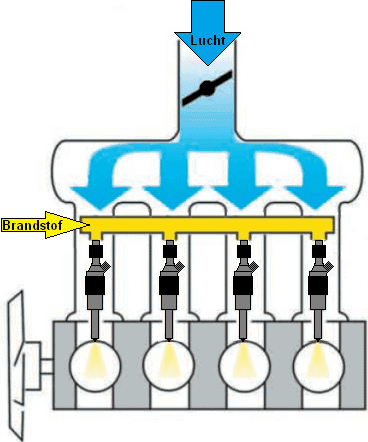
DI requiere presiones de inyección más altas que MPI / PFI, porque la inyección tiene lugar durante la carrera de compresión; el combustible debe atomizarse suficientemente mientras se comprime el aire del cilindro. Por eso DI tiene una bomba de alta presión independiente. La bomba de alta presión aumenta la presión del combustible en el conducto de combustible. A esta galería de combustible se unen los inyectores mediante tuberías. Tan pronto como la gestión del motor envía una señal al inyector, este se abrirá y cerrará en el momento deseado.
Las ventajas de DI en comparación con PFI incluyen:
- Inyección más precisa;
- Posibilidad de múltiples inyecciones;
- El tiempo de inyección se puede ajustar;
- Es posible una presión efectiva más alta sobre el pistón (permitiendo así una reducción de tamaño con una relación de compresión más alta);
- Menor consumo de combustible, menores emisiones de CO2.
Las desventajas incluyen:
- Mayores costos del sistema debido a una bomba de combustible de alta presión, inyectores avanzados y una culata más compleja;
- Aumentaron las emisiones de hollín (emisiones de PM);
- La inyección directa en la cámara de combustión proporciona enfriamiento en lugar del calor necesario para la evaporación del combustible.
Un motor de doble inyección aprovecha las ventajas de ambos sistemas. La inyección directa e indirecta se puede cambiar según las condiciones de funcionamiento. El funcionamiento y aplicación de la doble inyección se describe en el párrafo del mismo nombre en esta página.
Control de presión de combustible con inyección indirecta:
La presión constante del combustible es un requisito previo para controlar con precisión la inyección de combustible. La presión del combustible (presión del riel) está en la parte superior del inyector y la presión del colector de admisión está en la parte inferior. La presión en el colector de admisión varía según la carga del motor y, sin un regulador de presión, influirá en la diferencia de presión del combustible y, por tanto, en la cantidad inyectada. Por ese motivo utilizamos un regulador de presión de combustible. En este apartado profundizaremos en el funcionamiento y finalidad de este controlador.
La siguiente imagen muestra los componentes de un motor de gasolina de inyección indirecta con inyección multipunto. Observamos el flujo de combustible desde la bomba en el tanque hasta el inyector.
Cuando la ECU controla el relé de la bomba de combustible, la bomba funciona. La bomba aspira el combustible desde la parte más baja posible del tanque de combustible y fuerza el flujo de combustible hacia el filtro de combustible. Las partículas de suciedad del combustible permanecen en el material del filtro. El combustible filtrado llega luego a la galería de combustible. En la mayoría de los casos la galería de combustible se monta directamente en la entrada del inyector.
Hay una presión constante en la galería de combustible: sólo cuando el inyector está controlado eléctricamente por la ECU (ver el cable azul), el inyector se abre y el combustible se inyecta en el colector de admisión en la válvula de admisión abierta. La cantidad de combustible inyectado depende de:
- el tiempo de inyección (determinado por la ECU alargando o acortando la señal de inyección);
- la presión del combustible (con un tiempo de inyección de 2 milisegundos, el inyector inyectará más de lo que la ECU ha calculado si la presión del combustible es demasiado alta).
La presión del combustible en la galería de combustible (también llamada presión del riel) se ajusta en función de la carga del motor. Discutiremos esto con más detalle en la siguiente sección.
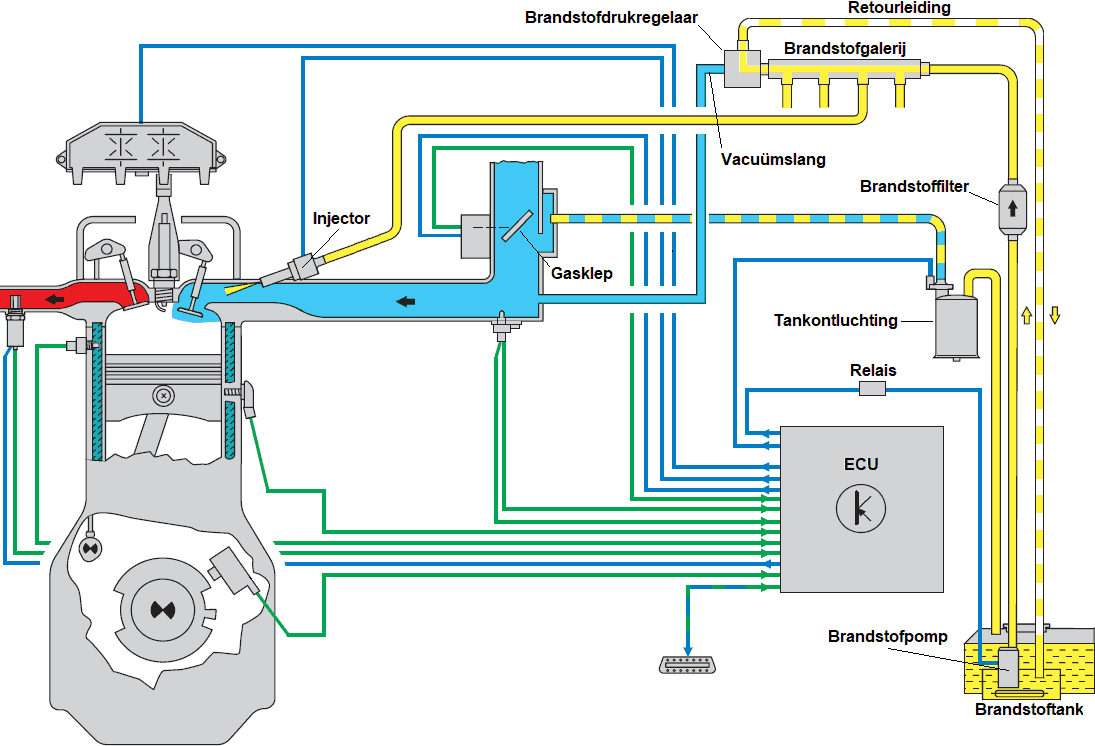
Sin utilizar un regulador de presión, surgen las siguientes situaciones:
- Al ralentí, el mayor vacío (es decir, baja presión de aire) en el colector de admisión produciría una presión de combustible indeseablemente más alta;
- Al acelerar, el vacío es menor o incluso casi nulo (carga completa) y la presión del combustible bajaría, mientras que se desea una presión de combustible más alta.
El regulador de presión de combustible aumenta o disminuye la presión de la gasolina en la galería de combustible en función de la presión del aire en el colector de admisión. Podemos considerar el regulador de presión de combustible como una válvula dinámica, que permite una apertura entre la línea de suministro de la bomba de combustible y la línea de retorno.
A la derecha vemos un diagrama de presión de combustible donde la diferencia de presión relativa en todas las condiciones (ralentí, carga parcial y carga completa) es de 4 bar gracias al regulador de presión.
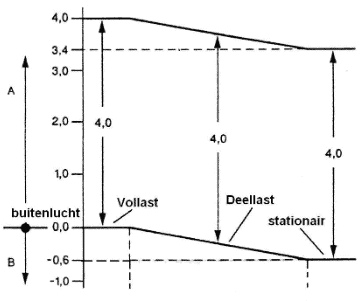
La explicación siguiente se refiere a las imágenes que muestran el regulador de presión en situación sin y con vacío. A la derecha se encuentra un regulador de presión de combustible de Bosch, que utilizan varios fabricantes de automóviles.
Sin vacío (izquierda):
El regulador de presión está cerrado en reposo: el resorte presiona la membrana para cerrarla, impidiendo que el combustible suministrado llegue a la línea de retorno.
Con vacío (medio):
Cuando se reduce la presión sobre el diafragma, la presión del combustible en el lado de suministro empuja el diafragma hacia arriba contra la fuerza del resorte. Se crea una abertura a través de la cual se drena el combustible suministrado a través de la línea de retorno al tanque de combustible.
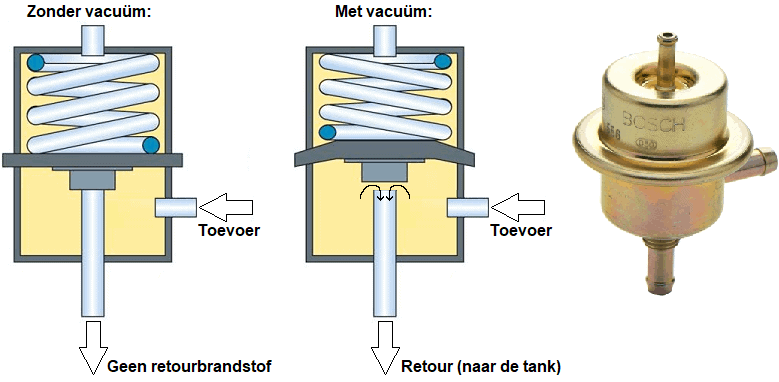
Estrategia de inyección inyección multipunto:
En la inyección multipunto (indirecta) se utilizan tres métodos de inyección diferentes:
- Simultánea: la inyección se realiza al mismo tiempo en todos los cilindros.
- Grupo: la inyección se realiza por grupo; hay una distinción entre uno o más grupos.
- Secuencial: cada inyector se controla por separado y por tanto tiene su propio momento de inyección.
El sistema de gestión del motor en la siguiente figura ilustra una inyección grupal. Los inyectores de los cilindros 1 y 2 tienen alimentación común (rojo) y ambos están conectados a masa al mismo tiempo (verde). Los inyectores de los cilindros 3 y 4 son iguales, pero se controlan por separado de los cilindros 1 y 2.
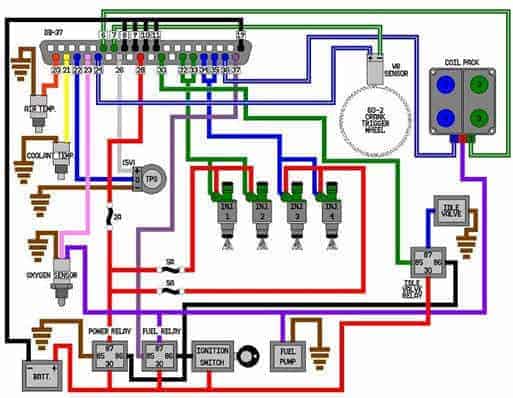
Inyector electromagnético (MPI):
El inyector electromagnético se utiliza en muchos motores de gasolina que no utilizan inyección (directa) de alta presión con una bomba de alta presión independiente. El combustible está bajo una presión constante de 1 bar en la entrada del inyector. La presión del combustible la proporciona la bomba de combustible en el tanque. Con la inyección multipunto (esto se describe más adelante en la página), cada cilindro tiene su propio inyector. Este inyector está montado en el colector de admisión e inyecta combustible con una presión de hasta 6 bar antes de que se abra la válvula. El combustible tiene entonces tiempo suficiente, cuando la válvula de admisión comienza a abrirse, para mezclarse con todo el oxígeno (indicado en la figura como una flecha azul oscuro) que fluye hacia el cilindro.
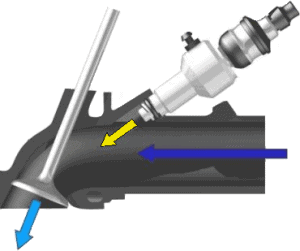
La unidad de control del motor observa la posición del cigüeñal para regular el tiempo de inyección y el tiempo de encendido. En función de varios factores (motor y temperatura ambiente, carga, velocidad, etc.), dará una señal al inyector en el momento adecuado para abrir. El enchufe de este inyector contiene dos cables. Un cable tiene un plus constante de alrededor de 14 voltios. El otro cable está conectado a tierra por la ECU para permitir que la corriente fluya a través de la bobina del inyector. Cuando la bobina está suficientemente cargada, la aguja del inyector se abre contra la fuerza del resorte. Cuando el control se detiene, un resorte comprime la aguja del inyector hacia atrás. Luego se corta el suministro de combustible. Cuando se detiene el control, la bobina todavía está cargada eléctricamente. La energía en la bobina forma un pico de inducción, que se puede observar en el osciloscopio. La tensión de inducción ronda brevemente los 60 voltios.
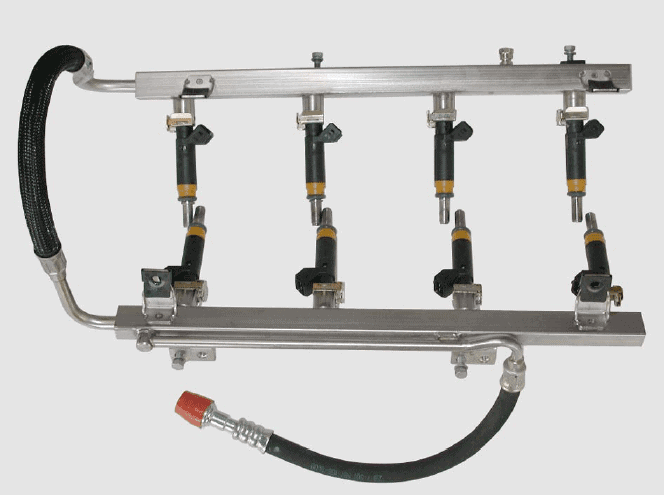
Estos inyectores reciben combustible a través del riel de combustible (también llamado galería de combustible). La bomba de refuerzo en el tanque de combustible proporciona la presión en el riel de combustible. La presión del combustible en la rampa es constante (aprox. 4 bar). Debido a que la presión es tan baja, los inyectores están sujetos con un clip de bloqueo y una junta tórica para sellar. Especialmente en coches más antiguos en los que el sistema está desmontado, es aconsejable sustituir las juntas tóricas antes de la instalación.
La carcasa de un inyector suele estar hecha de plástico. En la parte superior de la carcasa encontramos la conexión de enchufe, que está conectada internamente a la bobina. Hay una junta tórica de goma en la parte superior sobre la cual se desliza la galería de combustible. En la parte inferior se encuentran juntas tóricas o juntas de teflón. Una junta tórica se utiliza principalmente en inyectores MPI con inyección de baja presión, mientras que los anillos de teflón se pueden encontrar en motores con inyección de alta presión, como un motor FSI.
La bobina se enrolla alrededor del núcleo del inyector. En la imagen adjunta la bobina está resaltada en rojo. En el centro del inyector, también interno a la bobina, hay un émbolo. Este émbolo tiene un acoplamiento mecánico con la aguja. Encima del émbolo hay un resorte que sujeta el émbolo y, por tanto, la aguja en su asiento, cerrando la abertura de inyección.
En reposo, el voltaje en ambos terminales de la bobina es de aproximadamente 14 voltios con respecto a tierra. Para cebar el inyector, la ECU del motor suministra tierra a un lado de la bobina, mientras que el otro lado recibe voltaje positivo. En ese momento, la corriente comienza a fluir a través de la bobina, lo que da como resultado la formación de un campo magnético. Este campo magnético empuja el émbolo y, por tanto, la aguja de inyección hacia arriba.
Cuando es necesario detener la inyección, la ECU desconecta la masa, provocando la desaparición del campo magnético. El resorte empuja el émbolo hacia abajo, lo que hace que la aguja corte el suministro de combustible a la cámara de combustión.
El inyector suele tener múltiples aberturas. Estas aberturas son muy pequeñas, de modo que el combustible se inyecta desde el inyector a la cámara de combustión en forma de niebla. Cuanto más fina es la niebla, más fácil se evapora.
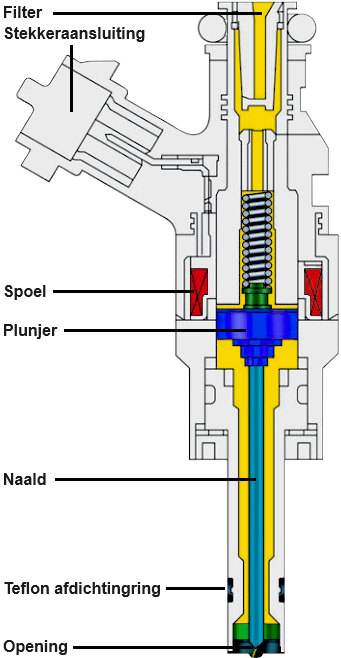
Inyector piezoeléctrico (DI):
Los inyectores piezoeléctricos se pueden utilizar tanto en motores de gasolina como diésel. BMW fue la primera marca en utilizar la tecnología piezoeléctrica en los motores de gasolina, pero dejó de hacerlo con los motores más nuevos.
Un inyector piezoeléctrico forma parte de la inyección de alta presión. Una bomba de alta presión separada proporciona presión al riel de combustible. Este riel de combustible distribuye el combustible a todos los inyectores (ver imagen). Debido a las altísimas presiones se utilizan tubos de aluminio con prensaestopas. Los prensaestopas (que se atornillan al tubo y a los inyectores) deben apretarse siempre con la fuerza correcta. Esto se indica en el manual de reparación del motor correspondiente.
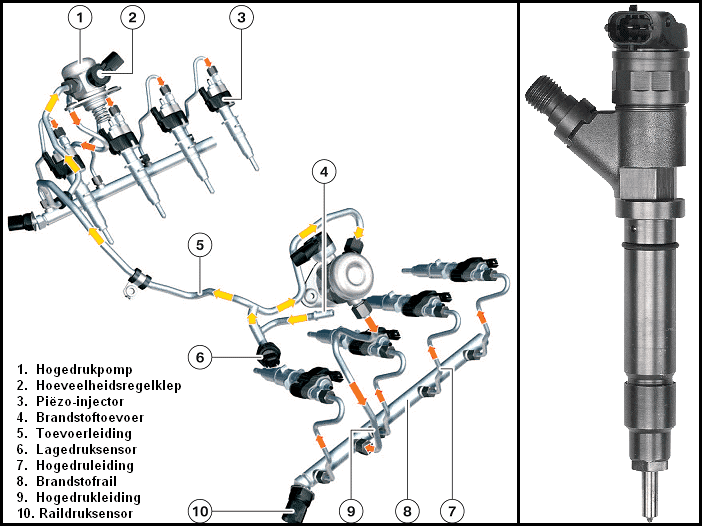
El elemento piezoeléctrico en el inyector tiene la propiedad de cambiar de longitud cuando se le conecta un voltaje positivo o negativo. Esto se usa con el inyector. En cuanto la unidad de control del motor suministra una tensión de control de aproximadamente 100 a 150 voltios, el elemento piezoeléctrico se expande aproximadamente 0,03 mm. Este cambio de longitud es suficiente para establecer una conexión entre la cámara de alta y baja presión. La inyección comienza inmediatamente. El elemento piezoeléctrico puede encenderse y apagarse en una milésima de segundo. Junto con la altísima presión de inyección de hasta 2000 bar, esto proporciona inyecciones muy rápidas y precisas. Estas velocidades también permiten realizar múltiples inyecciones una tras otra.
Las inyecciones múltiples durante la carrera de admisión tienen la ventaja de que la mezcla de aire y combustible es óptima. La alta presión hace que las gotas de combustible se atomicen muy finamente, de modo que se mezclan aún mejor con el aire. Durante la carrera de admisión pueden realizarse hasta 8 inyecciones. Esto tiene consecuencias positivas para el consumo de combustible, la potencia y las emisiones de escape.
Estrategias de inyección inyección directa:
La estrategia de inyección directa tiene diferentes variantes: guiada por pared, guiada por aire y guiada por chorro (ver las imágenes a continuación). En estas situaciones se produce un proceso de combustión por capas. Esto no se aplica en todas las condiciones de funcionamiento.
- Guiado por la pared: el pistón guía la nube de combustible hasta la bujía. La distancia entre la bujía y el inyector es grande. Aplicado a motores GDI y HPI.
- Guiado por aire: el movimiento del aire lleva la nube de combustible a la bujía. La distancia entre la bujía y el inyector es grande. Aplicado a motores FSI y JTS.
- Guiado por chorro: la bujía se encuentra en el borde de la nube de combustible. La distancia entre el inyector y la bujía es pequeña. Aplicado a motores BMW.
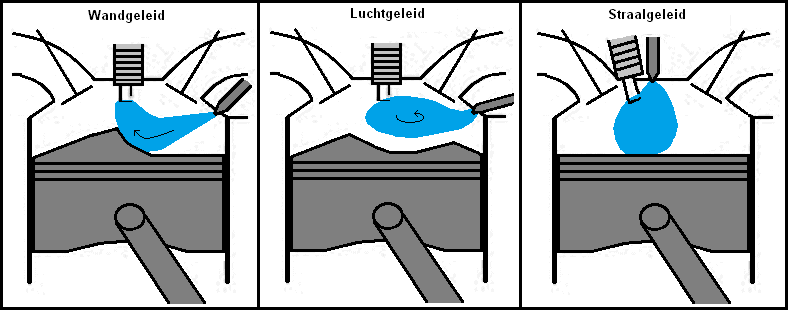
Como ya se ha indicado, los motores de gasolina de inyección directa no presentan combustión estratificada en todas las condiciones de funcionamiento. Los motores con inyección directa guiada por chorro pueden funcionar por fases con carga parcial. Un proceso de combustión por capas significa que en el espacio de combustión hay varias capas de aire. Cerca de la bujía, el valor lambda es 1. Más lejos, el valor lambda aumenta (más pobre, por lo que hay más aire). Este aire proporciona una capa de aire aislante. En un proceso por capas el tiempo de inyección es posterior que en el proceso homogéneo. Con la ayuda de una inyección en capas, la válvula de mariposa se puede abrir completamente, de modo que ahoga menos el aire. Al ser desasfixiado, el aire aspirado encuentra menos resistencia y, por tanto, puede aspirarse más fácilmente. Debido a que el valor lambda en la cámara de combustión con inyección por capas es inferior a 1 debido a la capa de aire aislante, no se producen problemas de combustión. Durante el proceso de estratificación, el consumo de combustible disminuye.
En una mezcla homogénea, el valor lambda en todas partes es 1. Esto significa que en un motor de gasolina la proporción de aire y combustible es de 14,7:1 (14,7 kg de aire por 1 kg de combustible). Cada motor puede funcionar de forma homogénea. Si se produce un enriquecimiento, el valor lambda disminuirá y si la mezcla se adelgaza, el valor lambda aumentará:
<1 = Rico
>1 = Pobre
Un motor siempre fluctuará entre rico y pobre para mantener el convertidor catalítico funcionando correctamente. El sonda lambda envía los datos al sistema de gestión del motor.
A plena carga el motor siempre funciona de forma homogénea. Esto proporciona un par mayor que con un proceso en capas. Si el motor funciona de forma homogénea, el combustible se inyecta antes. El motor también funciona de forma homogénea al salir de parado. Se produce entonces un par de arranque mayor que si el motor funcionara por capas.
La siguiente curva característica muestra las situaciones de funcionamiento a diferentes velocidades en comparación con el presión de combustión, con y sin uso de EGR.
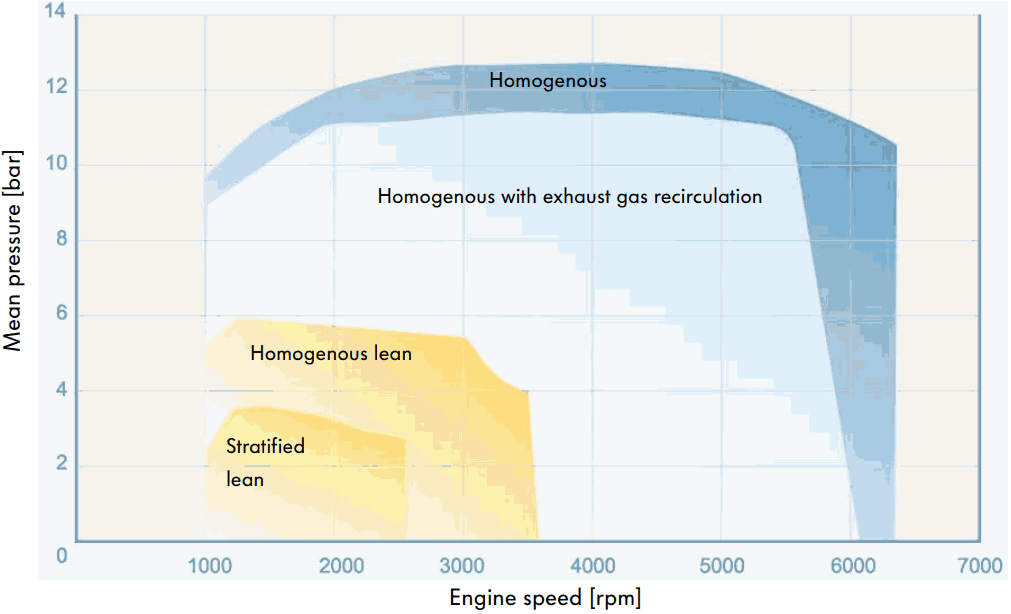
Doble inyección:
El grupo VAG utiliza motores de gasolina de doble inyección para cumplir con las normas de emisiones actuales. En los motores de doble inyección, hay dos sistemas de inyección de combustible: un sistema de baja presión y un sistema de alta presión.
- El sistema de baja presión contiene inyectores MPI que se utilizan desde hace décadas. Los inyectores MPI se montan en el colector de admisión e inyectan en la válvula de admisión a una presión de 4 a 5 bar;
- El sistema de alta presión contiene inyectores de alta presión que inyectan directamente en la cámara de combustión con una presión de inyección de un máximo de 150 a 200 bar.
El sistema de gestión del motor determina qué inyector está controlado.
La siguiente imagen muestra una sección transversal de la culata con los dos sistemas de combustible.
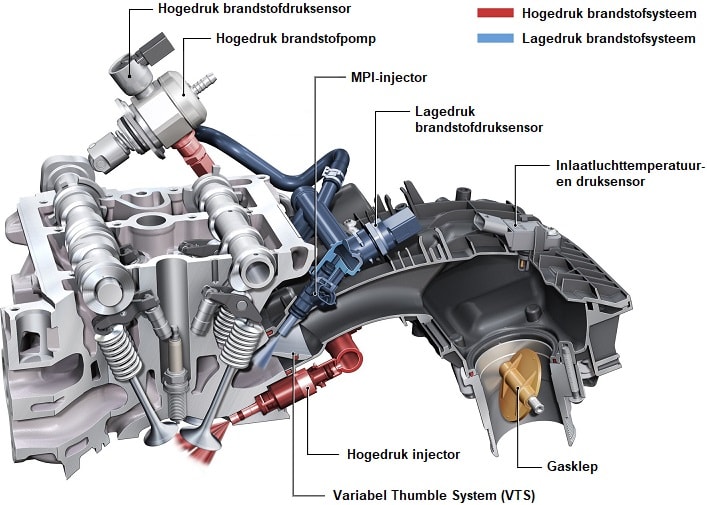
La inyección MPI ofrece una mejor mezcla entre aire y combustible. Los inyectores directos se utilizan al ralentí y a plena carga. Con la inyección directa se consigue una mejor refrigeración, lo que posibilita una mayor relación de compresión. Sin embargo, la mezcla de aire y combustible no es óptima. Esto provoca más emisiones de hollín. Por este motivo, los motores con inyección directa hoy en día están equipados con un filtro de partículas. Esto no es un problema con la doble inyección. El "sistema de pulgar variable", abreviado VTS, es una versión de un colector de admisión variable que proporciona un mejor flujo de aire. El "pulgar" es un flujo de aire que se crea en un vórtice cuando ingresa al cilindro. El remolino de aire es necesario para mezclar adecuadamente el combustible del inyector MPI con el aire.
La doble inyección en combinación con el VTS garantiza mejores emisiones de escape. Una ventaja adicional es que la válvula de admisión se limpia mediante el inyector MPI. Los motores con inyección directa a menudo sufren de un tracto de admisión sucio (colector de admisión y válvulas de admisión), lo que causa problemas como un suministro de aire limitado. En el caso extremo, la admisión se obstruye tanto que la válvula de admisión ya no puede cerrar correctamente en la culata y finalmente se quema porque no puede disipar el calor lo suficiente.
Se sabe que los mismos motores en Estados Unidos están equipados únicamente con inyección directa para los motores VAG de doble inyección. El colector de admisión está tapado. Esto se debe a que, en el momento de escribir este artículo, los requisitos medioambientales son más estrictos en Europa que en los EE. UU., y el fabricante no proporciona motores con sistemas tan caros para mercados donde las normas de emisiones son menos estrictas por razones de coste.
Medición de características de voltaje y corriente en un inyector multipunto:
El osciloscopio sólo puede medir voltaje. Los cables de medición se pueden conectar en paralelo a través de los componentes eléctricos. No es posible medir la corriente en serie. La corriente se puede medir utilizando una pinza amperimétrica inductiva. Los sensores Hall de la pinza amperimétrica miden el campo magnético y lo convierten en tensión. El voltaje se puede medir con el osciloscopio. En este caso existe un factor de conversión de 10 mv por amperio; Por cada 0,010 voltios que transmite la pinza amperimétrica, este se puede convertir a 1 A.
La siguiente imagen de alcance muestra el perfil de voltaje y corriente de un inyector electromagnético.
- Rojo: gradiente de voltaje;
- Amarillo: flujo de corriente.
En reposo el voltaje es de 14 voltios. Ahora no hay diferencia de voltaje en el enchufe, por lo que no fluye corriente. La ECU conecta un cable a tierra para controlar el inyector. La diferencia de voltaje hace que la corriente fluya a través de la bobina del inyector.
La línea amarilla indica el flujo de corriente: en el momento en que el voltaje cae a 0 voltios, comienza la acumulación de corriente. Cargar la bobina lleva tiempo. La corriente no aumenta más allá de aproximadamente 0,9 A. A mitad de la acumulación de corriente vemos una curva en la línea: este es el momento en que se ha acumulado suficiente magnetismo para levantar la aguja de su asiento. El inyector comienza a inyectar.
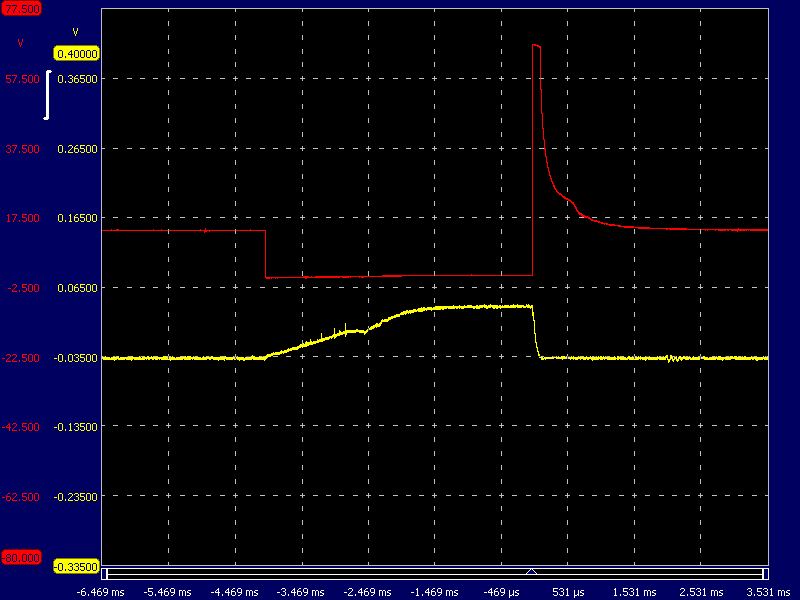
La ECU rompe la conexión a tierra para detener el control. La energía residual en la bobina proporciona un voltaje de inducción de aproximadamente 60 voltios. El inyector deja de inyectar porque el resorte empuja la aguja hacia su asiento. Esto se puede ver en la imagen del osciloscopio por el aumento en la señal de voltaje.
Si el motor funciona de forma irregular y se produce un fallo de encendido del cilindro, esto puede deberse a varias causas:
- Falta de chispa o chispa deficiente debido a una bujía, un cable de bujía o una bobina de encendido defectuosos;
- Restricción del suministro de combustible debido a un filtro de combustible obstruido, regulador de presión defectuoso, problema con la bomba de combustible o el inyector;
- Pérdida de compresión debido a un problema con los anillos del pistón, junta de culata o sellos de válvula defectuosos.
Durante un diagnóstico, se puede utilizar un osciloscopio para comprobar si los inyectores siguen funcionando correctamente. Al principio de esta sección se mostraron mediciones en las que no hubo ningún mal funcionamiento. Las líneas azules muestran como ejemplo cómo se vería el perfil de voltaje y corriente de un inyector defectuoso.
En el caso de que el control del inyector sea correcto, pero no se vean torceduras en la imagen de voltaje y corriente, se puede concluir que la aguja del inyector no se mueve. Debido a que el inyector de un cilindro no funciona correctamente y los otros inyectores sí funcionan correctamente, las imágenes de diferentes inyectores se pueden comparar fácilmente entre sí.
Si golpea suavemente el inyector, la aguja del inyector puede soltarse. En ese caso, el motor funcionará inmediatamente de forma más silenciosa y las torceduras volverán a ser visibles en las imágenes del visor. Sin embargo, esto no garantiza una solución permanente; Es muy probable que el problema vuelva a aparecer en poco tiempo. Es necesario sustituir el inyector correspondiente.
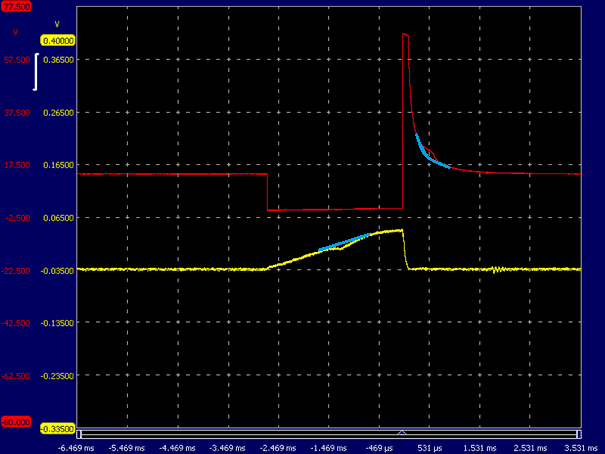
La aguja del inyector no se abre hasta que la bobina esté suficientemente cargada. Como resultado, el inyector no inyecta combustible inmediatamente cuando la ECU comienza a controlarlo. Una vez finalizado el accionamiento, el resorte presiona la aguja del inyector sobre su asiento. Esto también lleva tiempo. El tiempo de control no suele ser igual al tiempo de inyección. La siguiente imagen muestra la curva de voltaje y corriente del mismo inyector que el anterior, pero con mayor velocidad.
- Inicio del control: la ECU conecta el cable de control a masa. La corriente fluye a través de la bobina del inyector para abrirla. La torsión en el patrón de flujo indica el momento en que se abre la aguja del inyector. Entonces la corriente aumenta un poco y por tanto permanece constante. La aguja del inyector permanece abierta.
- Fin del control: como ya se ha descrito, reconocemos en la imagen de tensión el momento en que la aguja del inyector se cierra por el golpe.
El control tarda 4 ms, pero el tiempo de inyección real es de 3 ms. A la diferencia entre estos la llamamos “retraso”, traducido al holandés como “retraso”. Por tanto, la ECU controla el inyector durante 4 ms para permitirle inyectar durante 3 ms.
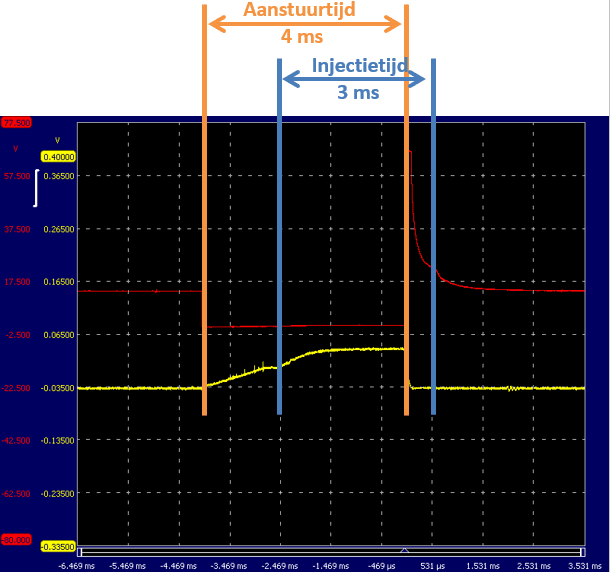
Sincronización de la inyección en relación con la posición del cigüeñal:
El momento de inyección se puede ver con un osciloscopio. El canal A (rojo) está en el cable de tierra del inyector y el canal B (amarillo) está en el cable del inyector sensor de posición del cigüeñal conectado. Mientras el motor está en marcha, podemos usar esta imagen de alcance para determinar el momento y el tiempo de inyección.
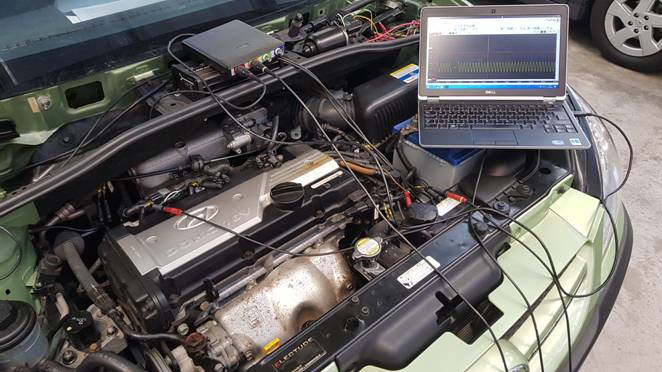
La imagen del visor se tomó al ralentí. La imagen de voltaje roja muestra la apertura y cierre del inyector (ver la sección: Medición de las características de voltaje y corriente en un inyector multipunto). En el tiempo -2,860 ms se inicia el control; el voltaje de 12 voltios cae a 0 voltios. Este es el punto en el que la bobina del inyector está conectada a tierra y fluye la corriente. El control del inyector finaliza cuando la línea roja vuelve a subir. Debido a la energía acumulada en la bobina, se produce una tensión de inducción de más de 60 voltios. Luego, el voltaje cae gradualmente a 12 voltios; aquí se vuelve a desconectar el inyector.
La tensión alterna roja proviene del inductivo. sensor de posición del cigüeñal. Cada vez que los dientes de la rueda de impulso pasan por el sensor del cigüeñal, se crea una tensión alterna sinusoidal. La rueda de impulso contiene 60 dientes, 2 de los cuales están pulidos. Los dos dientes rectificados constituyen el punto de referencia en el que el sistema de gestión del motor reconoce que los pistones de los cilindros 1 y 4 se encuentran entre 90⁰ y 120⁰ antes del PMS (punto muerto superior). Una vez detectado el diente faltante, el sistema de gestión del motor tiene tiempo (posiblemente en combinación con el sensor del árbol de levas) para determinar el momento correcto de inyección y encendido y para activar el inyector y la bobina de encendido antes de que el pistón esté en el PMS.
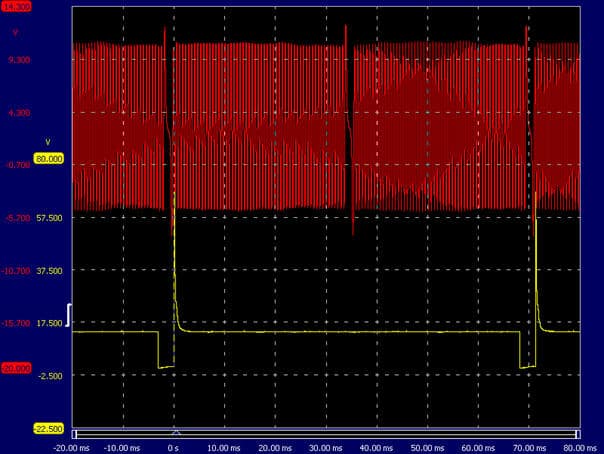
La imagen del osciloscopio muestra el momento en que comienza la inyección; La inyección comienza con el cuarto pulso del sensor del cigüeñal. Suponiendo que hay 60 - 2 dientes, después de cada 6⁰ de rotación del cigüeñal (360⁰ para 1 revolución / 60 dientes) la inyección se produce 24 grados después del punto de referencia. El diente que falta está 90⁰ antes del PMS, por lo que la inyección comienza (90⁰ – 24⁰) = 66⁰ antes del PMS.
Con un aumento de velocidad de 2000 rpm, los pulsos del sensor inductivo del cigüeñal están más juntos. La frecuencia de esta señal se traduce en velocidad mediante el sistema de gestión del motor. Dependiendo de la velocidad, la carga (medida por el Sensor de mapa) y el temperaturas del aire de admisión y del refrigerante se determina el tiempo de inyección necesario. El tiempo de inyección se adelanta y el inyector permanece en el suelo durante más tiempo: el inyector inyecta antes y durante más tiempo.
Desde el inicio de la activación hasta el punto de activación (flecha al nivel del apagado del inyector), el tiempo de activación es de aproximadamente 5,2 ms. El tiempo de activación del inyector no es igual a la inyección real (ver párrafo anterior).
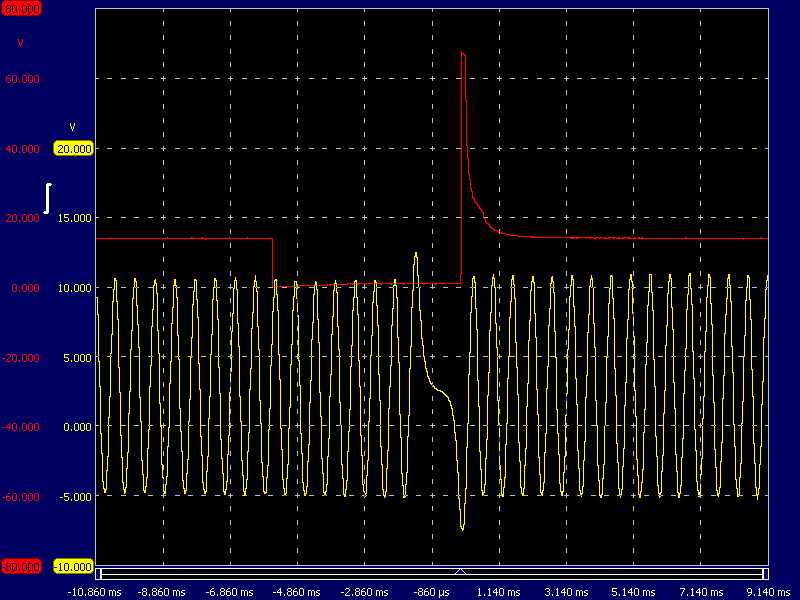
En la siguiente imagen de alcance, la señal inductiva del cigüeñal se muestra en rojo y la señal del inyector se muestra en amarillo. Al aumentar la velocidad a aproximadamente 3000 rpm, se pueden ver dos controles de inyector. Se ve claramente que la inyección de combustible en el cilindro 1 se produce cada dos vueltas del cigüeñal.
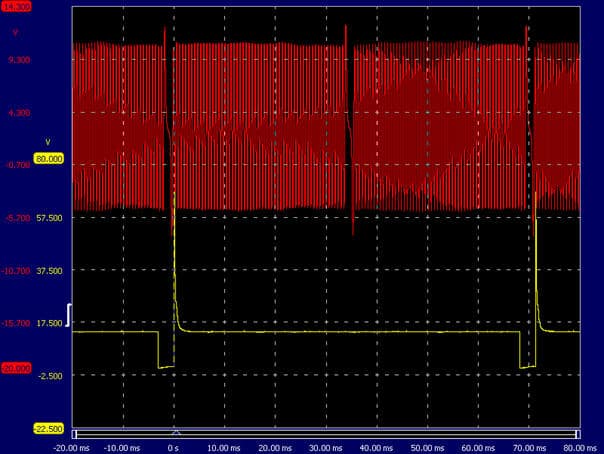
Limitación actual en la ECU:
Como mostraron las mediciones en la sección "Medición de voltaje y corriente en un inyector multipunto", hay un retraso entre el accionamiento y la apertura real de la aguja del inyector. En este caso tarda 1,5 ms en abrirse.
La aguja del inyector se abriría más rápido si la corriente a través de la bobina aumentara más rápido. La corriente depende de la resistencia de la bobina: cuanto menor sea la resistencia, más rápida será la acumulación de corriente. Los inyectores de alta impedancia utilizados en el motor de las mediciones tienen una resistencia de 16 Ohm. Con una tensión de a bordo de 14 voltios, fluirá una pequeña corriente:
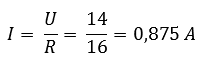
La corriente es suficiente para abrir la aguja del inyector, pero no demasiado alta para que se caliente demasiado debido a una potencia demasiado alta:

Debido a que sólo se genera una potencia baja, no es necesario utilizar un control de corriente. Esto sería necesario con inyectores de baja impedancia.
- Los inyectores de baja impedancia tienen la ventaja de que la corriente generada aumenta rápidamente desde el principio. Esto da como resultado una apertura rápida de la aguja del inyector, por lo que hay poco retraso.
- Los inyectores de bajos ohmios tienen una resistencia de aproximadamente 2,8 ohmios. La baja resistencia hace que fluya una alta corriente:
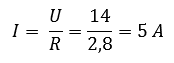
El poder también aumenta drásticamente:

El consumo de energía es casi siete veces mayor que con los inyectores de alta impedancia. Si la corriente aumenta demasiado, se genera calor en los inyectores y en la etapa de salida del dispositivo de control. Para limitar la corriente, la tensión se enciende y apaga varias veces en un corto período de tiempo. Una vez abierta la aguja del inyector, se necesita poca energía para mantenerla abierta. La corriente disminuye durante el encendido y apagado. Esta progresión se puede ver en la imagen del alcance.
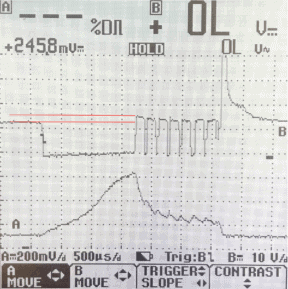
Determinación de la cantidad requerida de combustible:
El fabricante ha determinado la cantidad de combustible necesaria en varios campos característicos que se almacenan en la memoria ROM de la ECU. Él sistema de gestión del motor lee en estas tablas cuánto combustible se necesita sin correcciones. Por supuesto, esto depende del régimen del motor, la temperatura y la carga. Los parámetros más importantes para determinar la cantidad correcta de combustible se explican en esta sección como tabla VE y tabla AFR.
Tabla VE:
La tabla VE representa la eficiencia volumétrica y la relación aire/combustible en cada velocidad del motor y presión del colector de admisión. La eficiencia volumétrica es la relación entre la cantidad medida de aire que llena los cilindros y la cantidad de aire que llenaría el cilindro en una situación estática, dependiendo de la velocidad del motor y la presión del colector de admisión. La ECU utiliza los valores de la tabla para determinar la masa de aire actual y, por tanto, el nivel de llenado. Estos datos se utilizan para calcular la cantidad de combustible a inyectar.
Este enfoque teórico difiere de la realidad. Aquí todavía no se han tenido en cuenta las especificaciones del motor. Considere el diagrama de válvulas (superposición de válvulas o posiblemente sincronización variable de válvulas), la resistencia del aire en el tracto de admisión, etc. Es por eso que se aplica un factor de corrección que da una desviación de la relación lineal. El factor de corrección se muestra en la imagen de arriba mediante la línea discontinua. La curva indica hasta qué punto la relación lineal es correcta. A una presión de 60 kPa, la desviación es aproximadamente del 50 % de la línea que muestra la relación lineal. El factor de corrección se puede formar en porcentaje.
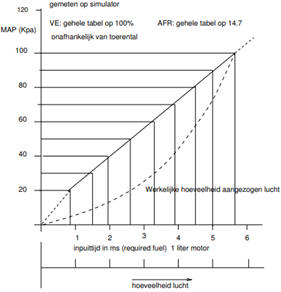
En una tabla VE, cada celda indica el porcentaje asociado a la presión negativa en relación a la velocidad. Este porcentaje será mayor a la velocidad a la que el par sea mayor. Después de todo, el motor es más eficiente allí porque es el que llena mejor.
Los valores de las tablas VE y AFR que aparecen más adelante en esta sección se derivan de la curva de par y potencia de un motor 1.8 20v de un VW Golf.
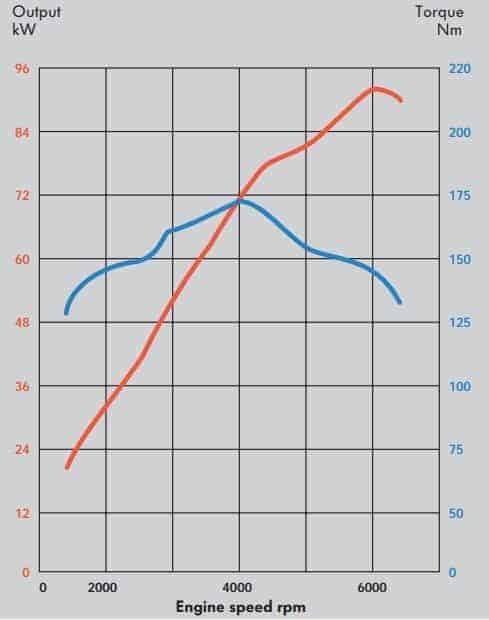
Las imágenes siguientes muestran la tabla VE como una tabla de relleno y la representación tridimensional creada utilizando la curva de par y potencia en el programa “TunerStudio”. Este programa se utiliza principalmente para proporcionar software para una ECU programable como MegaSquirt o Speeduino. Para más información: ver las páginas al respecto Proyecto MegaSquirt.
El eje vertical muestra la MAP (presión de aire del colector) desde 15 kPa (mucha presión negativa) hasta 100 kPa (la presión del aire exterior). El MAP indica la carga del motor. El eje horizontal indica la velocidad del motor entre ralentí y velocidad máxima del motor.
Las celdas de la tabla VE muestran el nivel de llenado del motor. En otras palabras; qué tan eficiente es el motor a una determinada velocidad y carga. El motor es más eficiente a la velocidad en la que el par es mayor (alrededor de 4200 rpm); Los porcentajes son los más altos aquí. Aquí es donde el motor se “llena” mejor. Aplicar técnicas que aumenten el nivel de llenado, como la sincronización variable de válvulas, el ajuste del colector de admisión o el uso de un turbo, beneficiará los porcentajes.
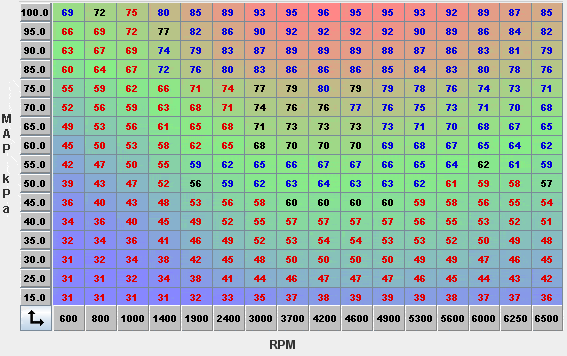
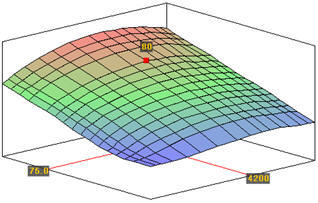
Tabla AFR:
La composición de aire/combustible requerida se registra en una tabla AFR. AFR es la abreviatura de “Air Fuel Ratio”. Con una relación de mezcla estequiométrica (lambda = 1), se necesitan 14,7 kg de aire para quemar 1 kg de gasolina. Una mezcla estequiométrica no es deseable en todas las situaciones.
- Una mezcla pobre beneficia el consumo de combustible;
- Una mezcla rica permite una mayor potencia.
Cuando el motor tiene que entregar más potencia (P), se produce el enriquecimiento. Una mezcla más rica también proporciona enfriamiento. Enriquecer a λ = 0,8 significa que se aplica una proporción de mezcla (AFR) de 11,76 kg de aire por 1 kg de gasolina. Por tanto, hay menos aire disponible para quemar 1 kg de combustible que con una mezcla estequiométrica. Una mezcla pobre, por el contrario, proporciona un mejor consumo de combustible (be), pero ofrece más posibilidades de detonación. El enriquecimiento o empobrecimiento de la mezcla debe mantenerse siempre dentro de los límites de combustión.
En ralentí, la velocidad está entre 600 y 900 rpm. La válvula de gas está casi completamente cerrada y la presión negativa es alta: está entre 25 y 40 kPa. En este rango de velocidades la mezcla es estequiométrica (14,7:1).
Cuando hay carga parcial, la velocidad del motor habrá aumentado a 4200 rpm. La válvula de mariposa se abre más, por lo que el vacío en el colector de admisión cae a 40 – 75 kPa. A medida que aumenta la carga del motor, la presión negativa disminuye; tiene lugar el enriquecimiento (AFR de 13:1). Es posible obtener una mezcla pobre con una carga baja del motor. A plena carga, el acelerador está completamente abierto. La presión negativa cae a 100 kPa (la presión del aire exterior) y se produce un enriquecimiento máximo (12,5:1).
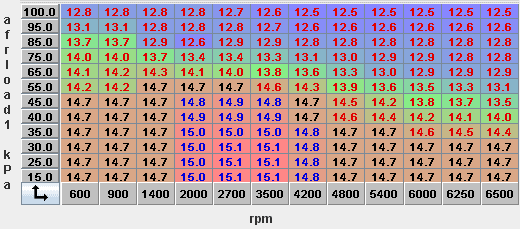
El valor lambda no sólo influye en el consumo de potencia y combustible, sino también en las emisiones de escape. Una mezcla más rica garantiza un menor contenido de NOx, pero también mayores emisiones de CO y HC. En una mezcla más pobre, las partículas de combustible están más separadas, por lo que la combustión ya no es óptima; con el resultado de que las emisiones de HC también aumentan.
Cuando se utiliza un catalizador, es deseable asegurarse de que la inyección alterne constantemente entre rica y pobre. En una mezcla rica se forma CO debido a una deficiencia de oxígeno, con lo que el catalizador reduce los NOx. Una mezcla pobre contiene un excedente de oxígeno, que oxida CO y HC.
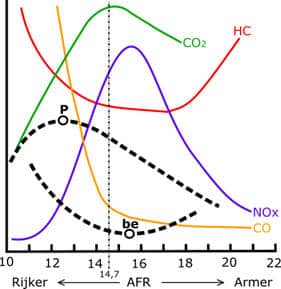
La unidad de control determina cuánto combustible se debe inyectar. En primer lugar se leen los datos básicos de inyección de los campos característicos. En el cálculo de la cantidad inyectada se incluyen, entre otras, los valores de las tablas VE y AFR. También se tienen en cuenta los siguientes valores determinados por el fabricante:
- enriquecimiento dependiendo de la temperatura del refrigerante y del aire de admisión;
- enriquecimiento de aceleración a corto plazo al abrir (rápidamente) el acelerador;
- Corrección por variación de la tensión de abordo.
Además de estos valores determinados, se tienen en cuenta cuidadosamente las tensiones que la sonda lambda envía a la unidad de control. Estos voltajes dependen del contenido de oxígeno en los gases de escape. Este es un factor variable que cambia continuamente. La entrada de voltajes de estos sensores se denomina "ajustes de combustible" incorporado.
Cómo se determinan los valores de la tabla VE y AFR y las otras configuraciones mencionadas se describen en las páginas del realizado Proyecto MegaSquirt.