emner:
- introduktion
- Intelligent batterisensor
- Batterisensorens komponenter og måleprincipper
- Opladning og udskiftning af batteri
Forord:
I moderne køretøjer tilpasses generatorens ladestatus efter omstændighederne. Generatoren styres fra motorens ECU og modtager signaler om at lade mere eller mindre. Generatoren genererer energi, da der skabes et magnetfelt mellem rotoren og statoren. Jo større magnetfelt, jo mere kraft kræves der for at dreje rotoren. At generere en stor mængde ladestrøm koster derfor energi og brændstof.
- Tomgangshastigheden kan øges, når batteriet er næsten tomt, når der ikke er tilstrækkelig genopladning mulig;
- Under maksimal acceleration styres generatoren midlertidigt ikke for at bruge hele det genererede drejningsmoment til fremdrift;
- Ved deceleration (motorbremsning) styrer ECU'en generatoren til maksimal effekt, således at køretøjets kinetiske energi bruges til at generere energi i generatoren. Figuren viser indikationen af den maksimale batteriopladning (12 volt system).
Signalet fra den intelligente batterisensor bruges til at bestemme batteriets ladestatus. Dette er en af de vigtigste data til at bestemme, i hvilket omfang generatoren skal kontrolleres.
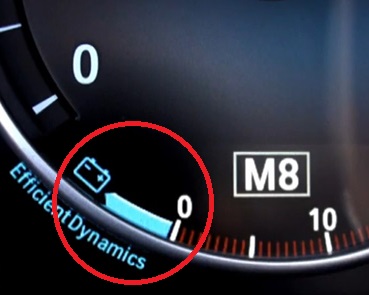
Intelligent batterisensor:
Moderne køretøjer er næsten alle udstyret med en batterisensor, ofte kendt som en IBS (Intelligent Battery Sensor), strømsensor eller batterimonitor. I denne artikel vil vi referere til udtrykket "batterisensor". Batterisensoren arbejder tæt sammen med Battery Monitor System (BMS) i køretøjet. Dette gælder især for køretøjer med et start- og stopsystem. I disse køretøjer udsættes batteriet gentagne gange for kraftig belastning, da startmotoren aktiveres flere gange pr. tur for at starte motoren. Derfor vælger man ofte et AGM-batteri i sådanne køretøjer i stedet for en traditionel blycelle. Et AGM-batteri er mere modstandsdygtigt over for gentagen afladning og opladning.
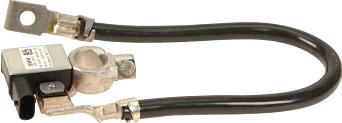
Batterisensoren er integreret i jordkablet, som er fastgjort mellem batteriets minuspol og et jordpunkt på karrosseriet eller chassiset. På batterisensoren finder du et stik med to eller flere ledninger. En ledning fører direkte til batteriets positive pol, og en anden ledning er til kommunikation.
Inde i batterisensorhuset er et printkort med en mikroprocessor og en controller, der måler spænding, strøm, temperatur og tid. Dataene fra denne elektroniske kontrolenhed (ECU) overføres ofte via en LIN-bus til generatoren og komfortstyringsenheden (BCM) eller motorstyringsenheden. Gatewayen er ofte placeret mellem batterisensoren og BCM eller motorstyringsenheden for at oversætte LIN-busmeddelelsen til en CAN-busmeddelelse. Dette diskuteres yderligere i afsnittet "diagnose på den intelligente batterisensor".
Batterisensoren overvåger batteriets tilstand og måler følgende parametre:
- Batterispændingen.
- Den strøm, som batteriet oplades og aflades med.
- Batteriets temperatur.
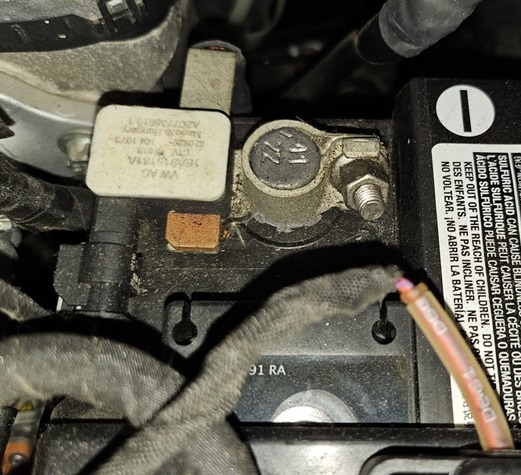
Batterisensoren sender disse data til motorstyreenheden eller BCM. Ved hjælp af disse data beregner ECU'en (elektronisk kontrolenhed) følgende:
Batteriets ladetilstand (SOC). Ved at måle den udgående strøm til forbrugerne og den indgående strøm til batteriet kan det bestemmes, hvor meget energi der stadig er til rådighed i batteriet.
Batteriets tilstand (Sundhedstilstand, SOH). Batterispændingen og afladningsstrømmen sammenlignes for at vurdere batteriets kvalitet. Under start kan der trækkes op til 60 A strøm fra batteriet med en lille benzinmotor eller op til 120 A med en tungere dieselmotor. Hvorvidt batterispændingen falder angiver niveauet af intern modstand i batteriet. Hvis spændingen falder fra 11,5 til 10 volt ved en strøm på 60 A, er dette acceptabelt. Hvis spændingen falder fra 11,5 til 8 volt med samme startstrøm, indikerer det for høj intern modstand i batteriet og kræver udskiftning.
Stillestrøm under stilstand. Denne registrerer en forstyrrelse af hvilestrømmen, f.eks. fra en uautoriseret forbruger. Chaufføren vil modtage en meddelelse under den næste tur, hvis der registreres en øget hvilestrøm.
Batterisensorens komponenter og måleprincipper:
Batterisensorens hus og jordterminalen er ofte integreret i en helhed. Jordkablet kan også danne en helhed med batterisensoren eller fastgøres med en skrueforbindelse. Inde i batterisensoren er der en shuntmodstand med en meget lav modstandsværdi. Ved at måle spændingsforskellen over denne shunt kan strømmen beregnes. I kombination med batterispændingen kan den effekt, som batteriet oplades eller aflades med, beregnes.
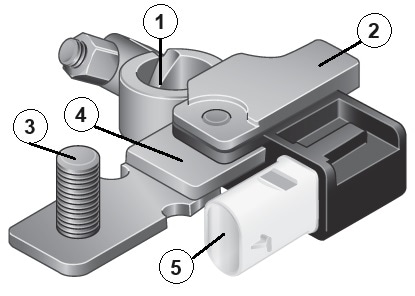
1. Polklemme jordstang;
2. Batterisensor;
3. Køretøjets jordforbindelse;
4. Shunt;
5. Stikforbindelse til B+ og LIN bus.
Shuntmodstanden er placeret i serie mellem køretøjets jordforbindelse og batteriets minuspol. Al strøm til og fra batteriet passerer gennem denne shunt. På grund af den lave modstandsværdi forbruges lille spænding i shunten.
Niveauet af denne spænding konverteres til en strøm i mikroprocessoren sammen med den kendte modstandsværdi af shunten:
- Et stort spændingsfald over shunten indikerer en stor strøm.
- Et lavt spændingsfald indikerer en lav strøm.
På det vedhæftede billede ser vi et diagram, hvor modstanden R repræsenterer shunten og strømmen I repræsenterer afladningsstrømmen under afladningen af batteriet. Voltmeteret, som er placeret parallelt over shuntmodstanden, illustrerer, hvordan måleelektronikken i batterisensoren måler spændingsforskellen over denne shunt.
Billedet nedenfor giver et overblik over de steder, hvor temperatur-, spændings- og strømmålinger finder sted.
Shuntmodstanden er angivet med nummer 5. Spændingsforskellen (V) over shunten aflæses som strøm (A). Disse data sendes via LIN-bussen til DME/DDE, som er betegnelserne for BMW's benzinmotor (DME) og dieselmotor (DDE).
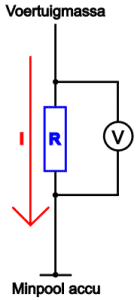
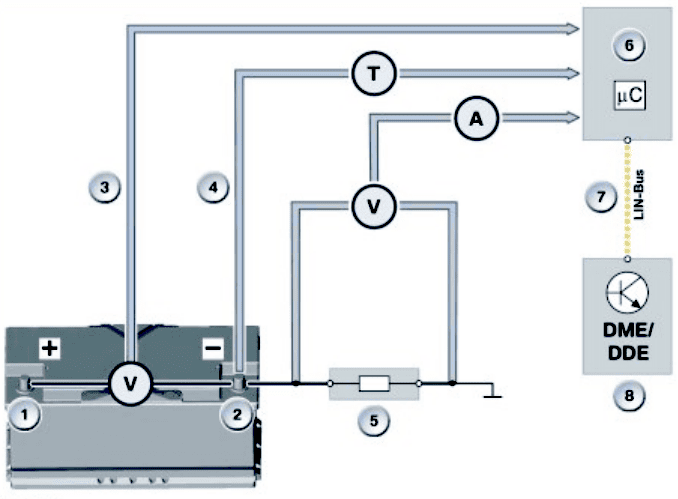
1. Batteriets positive terminal;
2. Batteriets jordterminal;
3. Måling af batterispænding;
4. Måling af batteritemperatur;
5. Måling af strømmen ved hjælp af en shuntmodstand;
6. Mikroprocessor i den intelligente batterisensor;
7. LIN bus kommunikationsledning
8. Motorstyringsenhed
Opladning og udskiftning af batteriet:
Batteristyringssystemet bruger batterisensoren til at måle strømmen, der flyder til og fra batteriet og gemme denne information i hukommelsen. Når batteriet skal oplades, eller hvis der anvendes starthjælp, er det vigtigt, at batteriopladeren ikke tilsluttes direkte til batteripolerne, men til ladepunkterne. Batterisensoren er placeret mellem disse ladepunkter og batteripolerne og kan kun måle energiflowet, når batteriopladeren er tilsluttet ladepunkterne. Hvis batteriopladeren tilsluttes direkte til batteripolerne, vil BMS-hukommelsen indikere, at batteriet er (næsten) tomt, mens det i virkeligheden er fuldt opladet. Generatoren vil herefter overoplade batteriet, hvorefter systemet fejler. Billederne nedenfor viser en batterioplader tilsluttet direkte til batteriet og til ladepunkterne under emhætten.
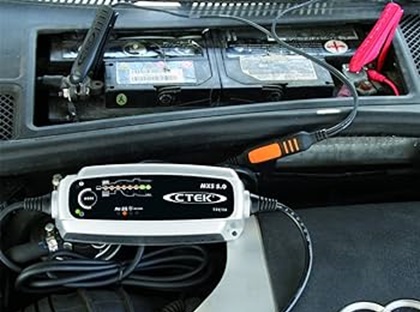
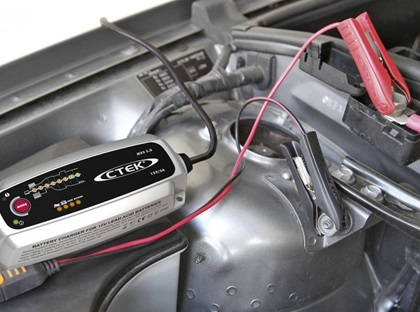
Efter udskiftning af batteriet skal batteriet registreres på et køretøj udstyret med batterisensor. På værkstedet kaldes det også "læring" eller "kodning". Batteristyring tager højde for:
- ældning af batteriet. Ladestrømmen af et ældre batteri med en øget indre modstand kan øges;
- batteriets kapacitet og koldstartstrøm.
Under optagelse slettes de lagrede værdier for batteriet, som er blevet forringet over tid. Så selvom der er installeret et identisk batteri af samme mærke og samme kapacitet og koldstartstrøm, skal udskiftningen registreres. Data for et batteri med forskellige egenskaber skal naturligvis gøres kendt. Dette kan gøres ved at indtaste kapaciteten [Ah] og koldstartstrømmen [A] manuelt eller ved at indtaste varenumre eller serienumre. Med moderne diagnoseudstyr kan QR-koden vist på batteriets mærkat scannes.
Skærmbillederne nedenfor viser registrering af et batteri med et BMW-program (venstre) og VCDS (højre).
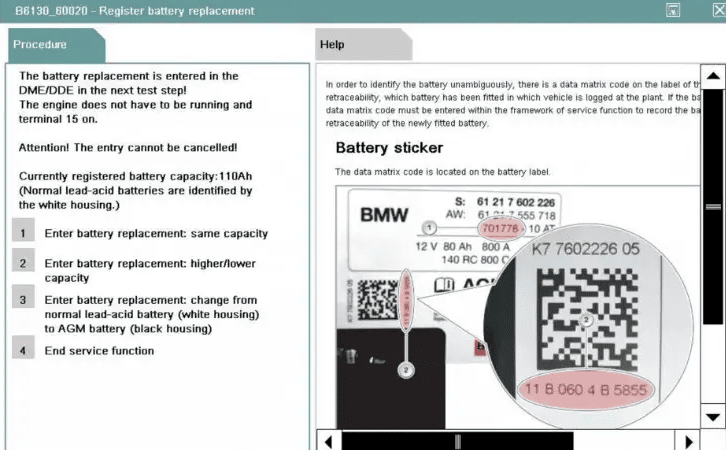
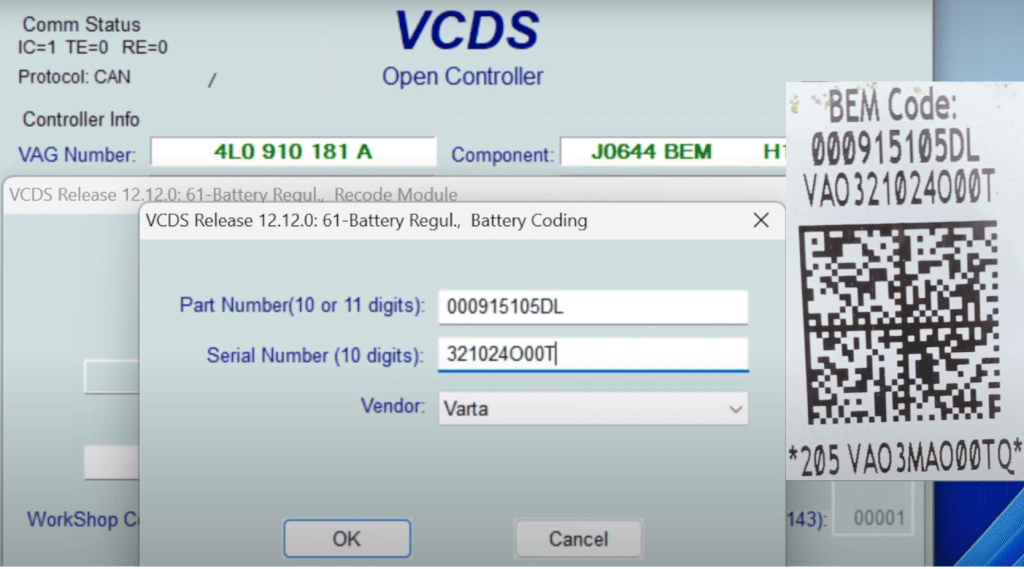
Diagnose på den intelligente batterisensor:
Den intelligente batterisensor kommunikerer med generatoren og BCM eller motorstyringsenheden. Dette afsnit forklarer, hvordan man læser diagrammet, og hvordan en diagnose kan stilles.
I det følgende diagram ser vi batterisensoren (A85), som forsynes med en forsyningsspænding på 2 volt af en sikring på ben 12. Pin 1 er til kommunikation: Herfra sendes en besked via LIN-bus til gatewayen (A25di) og generatoren (O01). Ben 1 og 2 er placeret i det to-benede stik, der er synligt på tidligere billeder.
De to nederste sorte ledninger på batterisensoren har ikke et pin-nummer: dette er en direkte forbindelse til batteriets negative pol.
Den intelligente batterisensor sender en LIN-busmeddelelse til gatewayen og generatoren. Gatewayen er knudepunktet mellem netværk med forskellige protokoller (spændinger og hastigheder). I gatewayen sendes LIN-busmeddelelsen via CAN-bus til BCM og/eller motorstyringsenheden. Omvendt styrer en af disse to styreenheder generatoren via gatewayen og LIN-bussen.
En fejl i LIN-buskommunikationen kan betyde, at batterisensordata ikke kan bruges, eller at generatoren ikke styres korrekt. I sidstnævnte tilfælde skifter generatoren til et nødprogram, hvor den konventionelle D+ styring bruges til at skabe tilstrækkelig ladespænding og ladestrøm.
Spændingsforløbet af LIN bus signal kan med en oscilloskop måles til vurdering.
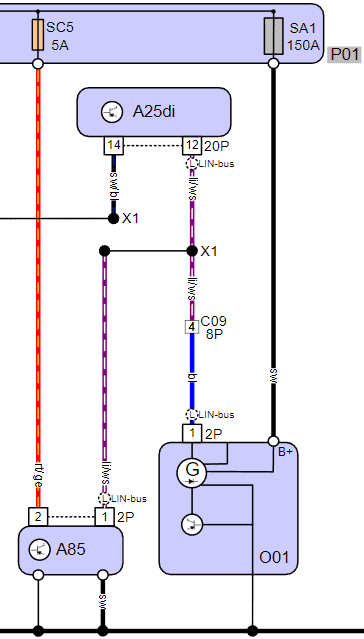
Undertekst:
P01: sikringsboks i motorrum
A25di: diagnostisk interface (gateway)
A85: ECU batteri sensor
O01: dynamo
Når der er en fejl, og LIN-bus-kommunikationen er OK, ved vi, at forsyningsspændingen og jord på sensoren er god. Fejlen skyldes en af komponenterne i dette diagram. Følgende trin kan tages:
- kontrollere for softwareopdateringer af kontrolenhederne;
- Test 12 volt batteri (helst under belastning);
- kontrollere, om de korrekte batteridata er blevet registreret. Batteriet kan være blevet udskiftet tidligere, men registreringen blev aldrig gennemført;
- nulstil batterisensordataene;
- kontroller, at generatorens varenummer er korrekt: en forkert generator, der ikke passer til sensoren, vil i sidste ende forårsage problemer;
- Hvis ovenstående er blevet kontrolleret og fundet korrekt, kan det være muligt at konkludere, at batterisensoren er defekt. Dette sker nogle gange ved hyppig (forkert) start via startkabler eller en batteriforstærker.
Relaterede sider: