Předměty:
- Určete a nainstalujte ovladače pro systém řízení motoru
- Vstřikovače paliva
- Výběr vhodných vstřikovačů
- Instalace vstřikovačů do sacího potrubí
- Zánět
- Příprava s konvenčním zapalováním
- Zapalovací cívka pro systém řízení motoru
- Nárůst proudu v primární cívce
- Předstih zapalování
- těleso škrticí klapky
- Testovací nastavení krokového motoru se simulátorem
- Nastavení krokového motoru
- Okruh palivového čerpadla
- Dokončení mechanických prací
Určení a instalace ovladačů pro systém řízení motoru:
Akční členy, které budou ovládány pomocí MegaSquirt, jsou vstřikovače, zapalovací cívka, palivové čerpadlo a krokový motor pro volnoběžné otáčky. Tato kapitola popisuje proces, ve kterém byly aktuátory testovány a instalovány na blok motoru, a jak byl proveden výběr.
Vstřikovače paliva:
MegaSquirt ovládá vstřikovače. Vstřikovače jsou připojeny k zemi. U uzemněné součásti je přítomno napájecí napětí, ale proud teče pouze při zapnutém uzemnění. V tomto případě bude vstřikovač vstřikovat pouze tehdy, když se ECU MegaSquirt přepne na zem. Jakmile je aktivace zastavena, injektor přestane vstřikovat. Množství paliva, které má být vstřikováno, je určeno na základě tabulky VE a tabulky AFR.
MOS FET zapíná a vypíná vstřikovač, což způsobuje vstřikování paliva. Množství paliva určené MegaSquirt závisí na několika faktorech:
- Zákon ideálního plynu, který dává do souvislosti množství vzduchu s jeho tlakem, objemem a teplotou;
- Hodnoty naměřené snímači v bloku motoru: tlak v sacím potrubí (snímač MAP), teplota chladicí kapaliny a nasávaného vzduchu, otáčky klikového hřídele a údaje ze snímače polohy škrticí klapky;
• Parametry nastavení: požadované množství paliva, stupeň naplnění (VE), doba otevření vstřikovače a obohacení za určitých podmínek.
Doba vstřikování by měla být co nejdelší, když motor běží na volnoběh, aby bylo dosaženo dobrého dávkování paliva. Na motoru tedy nelze použít ledajaký vstřikovač. Vlastnosti různých typů vstřikovačů musí být porovnány a výpočty musí poskytnout náhled na požadované množství paliva pro daný motor. Na výběr bylo také mezi vysoko- a nízkoimpedančními vstřikovači. Nízkoimpedanční vstřikovače jsou vhodné pro motory, kde je vyžadováno velmi rychlé otevření jehly vstřikovače. Typický odpor je 4 ohmy. Nevýhodou těchto vstřikovačů je vysoký proud. Vývoj tepla, který to vytváří v MegaSquirt, je nežádoucí. Je možné použít nízkoimpedanční vstřikovače namontováním speciálních IGBT na tepelně vodivou desku na pouzdru MegaSquirt. Bylo rozhodnuto použít vysokoimpedanční vstřikovače. Dochází k menšímu vývinu tepla a tyto IGBT se nepoužívají.
Velikost průchodu (průtok) je velmi důležitá pro stanovení správného vstřikovaného množství, a tedy i kontroly. Pokud zvolíte příliš velké vstřikovače, bude doba vstřikování při volnoběžných otáčkách tak krátká, že motor může běžet nepravidelně. Vstřikované množství musí být dostatečné pro vstříknutí veškerého paliva v dostupném čase. Vstřikované množství je indikováno jako doba vstřiku v milisekundách. Vysoké zatížení se předpokládá při vysokých otáčkách motoru. To je při MAP 100 kPa. Požadovaný průtok vstřikovačem lze vypočítat na základě vlastností motoru. Průtok vstřikovačem udává, kolik mililitrů paliva je vstříknuto za minutu.
Výběr vhodných vstřikovačů:
Pro projekt byly k dispozici vstřikovače tří různých typů. Výzkum ukázal, který typ injektoru byl pro použití v tomto projektu nejvhodnější.
Každý typ vstřikovače má jiný průtok; výtěžnost po jedné minutě injekce se liší podle typu. Před testováním vstřikovačů prošly čištěním v ultrazvukové lázni. Při této metodě čištění je vstřikovač vyčištěn zevnitř i zvenčí pomocí ultrazvukových vibrací a speciální testovací kapaliny, takže zbytky starých nečistot nemohou ovlivnit měření průtoku ani vzor vstřikování. Během ultrazvukového čištění byly vstřikovače nepřetržitě otevírány a zavírány a byl zkoumán vzor vstřikování každého vstřikovače; tohle byla krásná mlha. Při zavírání nebyly vidět žádné abnormality, jako je tvorba kapek nebo vychylující se proud. Po čištění a testování ultrazvukem byly O-kroužky vyměněny, aby bylo zajištěno dobré utěsnění při montáži do sacího potrubí.
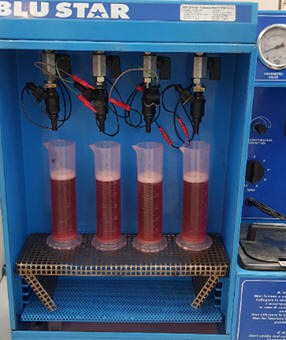
Pomocí testovacího nastavení (viz obrázek výše) mohou vstřikovače vstřikovat do více odměrek, takže po určité době lze odečíst vstřikované množství paliva. Ovládáním vstřikovačů při pracovním tlaku 3 bary lze řídit množství vstřikovaného paliva. Tlak paliva v přívodním potrubí (rail) musí být 3 bary a jehla vstřikovače musí být aktivována po dobu 30 nebo 60 sekund při pracovním cyklu 100 %. Po aktivaci vstřikovačů po dobu 30 sekund bylo možné zadat následující údaje:
Typ 1: 120 ml
Typ 2: 200 ml
Typ 3: 250 ml
Bude použit pouze jeden typ vstřikovače. Velikost vstřikovače se určuje pomocí vzorce níže:

Velikost vstřikovačů se určuje na základě efektivního výkonu (Pe) dodávaného při určité rychlosti, specifické spotřeby paliva při přestávce (BSFC), počtu vstřikovačů (n vstřikovačů) a maximálního pracovního cyklu, kterým jsou vstřikovače řízeny. Celek se vynásobí 10.5, aby se převedl z liber za hodinu (lb/h) na ml/min.
Odpověď na výpočet udává, který vstřikovač je vhodný pro tuto konfiguraci motoru. Není problém, pokud je odchylka menší než 20 ml od vypočtené hodnoty. Tento rozdíl je kompenzován úpravou softwaru v MegaSquirt. Následující tabulka poskytuje přehled údajů použitých ve vzorcích:
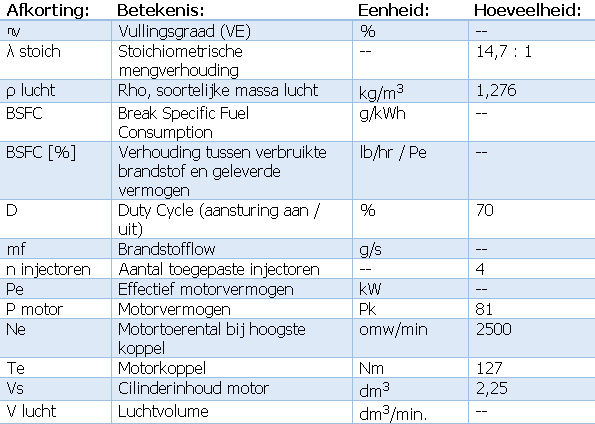
Prvním krokem je určení vstřikovaného paliva při otáčkách točivého momentu. Na každé dvě otáčky klikového hřídele je nasáváno určité množství vzduchu. Stupeň plnění je nejvyšší při otáčkách točivého momentu. Vzhledem k vlastnostem motoru (včetně překrytí ventilů) se motor nejlépe plní v těchto otáčkách a účinnost je nejvyšší. Odhaduje se, že míra naplnění bude kolem 70 %. Vzorec 4 vypočítá objem vzduchu, který je v tu chvíli přítomen v motoru.
Ve vzorci 5 se množství vstřikovaného paliva vypočítá na základě objemu přítomného vzduchu. Výkon motoru dosažený při otáčkách točivého momentu se vypočítá podle vzorce 6. Poměr mezi množstvím vstřikovaného paliva a výkonem udává BSFC ve vzorcích 7 a 8.
Skutečný BSFC se ve vzorci 6 vynásobí 3600, aby se převedl na kWh. BSFC zážehového motoru se často pohybuje mezi 250 a 345 g/kWh. Čím nižší je hodnota, tím je motor účinnější. Vzorec 8 udává vztah mezi průtokem paliva v librách/hodinu a efektivním výkonem motoru. Toto procento je zahrnuto ve vzorci 9.



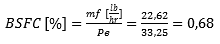

Odpověď na vzorec 9 jasně ukázala, že vstřikovače s průtokem 200 ml/min jsou vhodné pro použití v motoru. Rozdíl 7 ml je zanedbatelný, protože je kompenzován v softwaru při vyplňování tabulky VE.
Instalace vstřikovačů do sacího potrubí:
Elektronicky řízený systém vstřikování umožňuje vyjmutí karburátoru, který je součástí klasického nastavení. Karburátor je tedy nahrazen tělesem škrticí klapky (pro přívod vzduchu) a čtyřmi samostatnými vstřikovači paliva. Sací potrubí bylo zachováno a bylo upraveno tak, aby umožňovalo přestavbu na systém řízení motoru. Vstřikování paliva probíhá v sacím potrubí. Padlo rozhodnutí namontovat vstřikovače co nejblíže sacímu ventilu. Ve většině případů se výrobci automobilových motorů rozhodnou namontovat sací ventil pod úhlem do sacího potrubí. Palivo je stříkáno proti sacímu ventilu. Pro současný projekt však bylo zvoleno uspořádání, ve kterém jsou vstřikovače umístěny pod úhlem 45 stupňů vůči vzduchovým kanálům v rozdělovači.
Sací potrubí je vyrobeno z litého hliníku. Bylo rozhodnuto připevnit k rozdělovači hliníková pouzdra. Ruční opracování na dobrou velikost nepřicházelo v úvahu, protože pouzdra musela mít jiné rozměry než standardní velikost vrtáku. To znamenalo, že outsourcing dodávek musel být zadán společnosti s vhodným vybavením. Pouzdra pak mohla být připevněna k rozdělovači pomocí TIG svařování. Volba namontovat vstřikovače svisle namísto šikmo byla učiněna z následujícího důvodu:
- Proces montáže: Je snazší postavit dodávky v rovném vodorovném uspořádání. Svařování dodávek k rozdělovači je jednodušší, protože je nyní jednodušší svařovat kolem dokola než v situaci, kdy je dodávka pod úhlem.
- Následné zpracování: Během svařování se pouzdra stávají trochu oválnými. Deformace je způsobena teplem uvolněným během procesu svařování. To bylo vzato v úvahu tím, že vnitřní průměr pouzder byl menší než vnější průměr vstřikovačů. Dokončení (vystružování) je méně riskantní: když jsou pouzdra zevnitř zaoblená, je průměr pro vstřikovače optimální a je zaručeno utěsnění pomocí O-kroužků. Důležitá je výška dodávek; vstřikovač nesmí být umístěn příliš hluboko v potrubí. Konec vstřikovače nesmí bránit proudění vzduchu. Z informací ze zdroje: (Banish, Engine Management, advanced tuning, 2007) bylo rozhodnuto namontovat vstřikovače tak hluboko do rozdělovače, aby konce byly přesně v otvorech v rozdělovači; proudění vzduchu není bráněno.
- Vstřikování paliva: Protože promíchání palivové mlhy se vzduchem je optimální před otevřením sacího ventilu, nezáleží příliš na tom, zda vstřikovač vstřikuje přesně u sacího ventilu nebo těsně před tím do sacího potrubí.
Při současném vstřikování probíhá vstřikování při každém otočení klikového hřídele (360°). Čtyři vstřikovače vstřikují současně. To znamená, že palivo je také vstřikováno do sacího traktu, když není sací ventil otevřený. Po nějaké době se otevře sací ventil a palivo stále vstupuje do válce.
Keře jsou speciálně nařezány na soustruh. Vnitřní průměr je o něco menší než vnější průměr vstřikovače; Protože k deformaci dochází během procesu svařování, musí existovat možnost odstranit materiál během následného zpracování pomocí vystružování. To znamená, že se průměr mírně zvětší, protože materiál je odbroušen. Průměr by neměl být příliš velký, protože pak je šance, že gumový O-kroužek na vstřikovači již nebude moci dostatečně dobře těsnit. Dobré těsnění je velmi důležité; únik vzduchu kolem vstřikovače má za následek nižší podtlak v sacím potrubí.
Naměřený podtlak pak již neodpovídá vypočtenému podtlaku. To ovlivňuje vstřik, který se určuje na základě tabulky VE. Velkou roli v tom hraje podtlak. Funkce a nastavení tabulky VE jsou popsány v další kapitole.
Na spodní straně pouzder byla vypilována zkosená hrana tak, aby tvary odpovídaly tvaru sacího potrubí. Dodávka pak musí být co nejvíce vzpřímená. Obrázek níže ukazuje sací potrubí s kanystrem během procesu montáže. Pouzdro je nalepeno na jedné straně, takže je jasně vidět, jak svařování ovlivňuje materiál. Nebylo jasné, zda hliník potrubí obsahoval příliš mnoho nečistot, což by znesnadnilo svařování. To se ukázalo být v pořádku. Aby se zabránilo posunutí pouzder ze své polohy při svařování, byly v rozdělovači předem vyvrtány otvory a pouzdra byla držena ve správné poloze speciálně vyrobeným přípravkem. Tímto způsobem jsou čtyři pouzdra kolem dokola svařena. Konečná kontrola ukázala, že spojení mezi průchodkami a potrubím jsou vzduchotěsná.
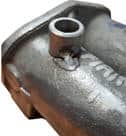
Spojení mezi vstřikovači je normálně tvořeno pevnou vstřikovací lištou. Tuto trubku s přípojkami, často z hliníkové slitiny, vyrábí na míru výrobce. Motor Land Rover použitý pro projekt má dva vstřikovače těsně vedle sebe, ale prostor mezi dvojicemi vstřikovačů je poměrně velký. Rozměry palivové lišty a prostoru mezi vzduchovými kanály sacího potrubí neodpovídaly. Kolejnice proto musela být upravena.
Zkracování některých dílů a prodlužování jiných dílů pájením je velmi obtížné; znečištění starým palivem, které se velmi obtížně odstraňuje z vnitřku kolejnice, může způsobit zhoršenou adhezi. Protože jde o palivo, byla zvolena nejbezpečnější metoda; díly, na kterých jsou uchyceny vstřikovače, jsou spojeny kvalitní palivovou hadicí. Na všech koncích byly osazeny švy a byly použity robustní hadicové svorky, aby se zabránilo klouzání hadic přes švy.
Obrázek níže ukazuje sací potrubí v době obrábění. Přívodní potrubí (označené číslem 1) je připojeno k výstupu palivového čerpadla. Palivo je přiváděno ke vstupu čtyř vstřikovačů pod tlakem 3 bar. Regulátor tlaku (3) reguluje tlak v závislosti na tlaku v sacím potrubí, protože tlakový rozdíl mezi tlakem paliva a podtlakem v sacím potrubí musí zůstat 3 bary. Palivo proudí zpět do nádrže zpětným potrubím (2). Dochází k nepřetržitému oběhu paliva. Vstřikování probíhá pouze tehdy, když jsou vstřikovače ovládány ECU MegaSquirt.
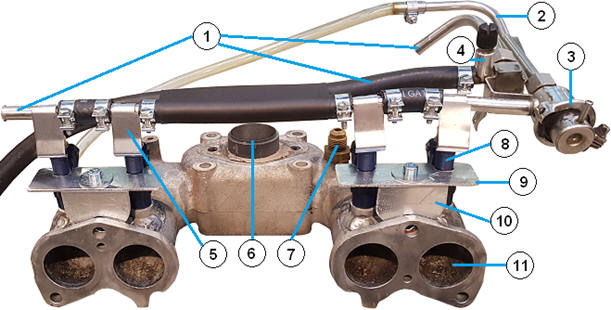
- Přívodní potrubí
- Zpětná linka
- regulátor tlaku
- Regulace tlaku
- tepelný štít
- Připojení plynového ventilu
- Podtlakové připojení
- Válec vstřikovače 1
- Držák vstřikovače A
- Držák vstřikovače B
- Válec sacího potrubí 1
U stávajících osobních automobilů je lišta vstřikovače připevněna k sacímu potrubí pomocí svorek nebo ok. Lišta vstřikovačů upíná vstřikovače v rozdělovači. Vzhledem k tomu, že pro tento projekt byla jako kolejnice vstřikovače zvolena flexibilní palivová hadice, výše uvedené není možné. Bylo proto rozhodnuto upnout vstřikovače v sacím potrubí pomocí na míru vyrobeného držáku. Držáky se skládají ze dvou částí: horní část (držák A) a spodní část (držák B).
Držák A obsahuje dva zářezy, které lze nasunout přes vstřikovače. To umožňuje vtlačování vstřikovačů do rozdělovače pomocí plochých stran. Oba držáky A mají štěrbinové otvory, takže lze nastavit vzdálenost mezi vstřikovači a štěrbinovými otvory. Konzoly A a B jsou sešroubovány dohromady: držák B je připevněn ke stejnému čepu, který připevňuje potrubí k motoru. Drážkovaný otvor umožňuje nastavení držáku ve vertikálním směru. Čím více je držák posunut směrem dolů, tím pevněji je vstřikovač upnut.
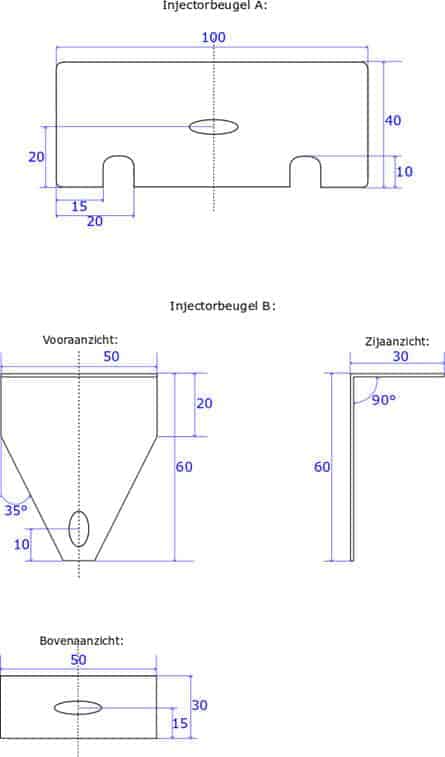
Zapalování:
Konvenční zapalování bylo nahrazeno elektronicky řízeným zapalovacím systémem se zapalovací cívkou, kterou ovládá MegaSquirt. Aby motor mohl plně fungovat s původními technikami, musí být nejprve připojen konvenční systém s kontaktními body. Správnou funkci motoru lze zjistit až po několika hodinách provozu, poté může začít montáž a seřízení mimo jiné elektronicky řízeného zapalování.
Příprava s konvenčním zapalováním:
Motor Land Rover byl původně vybaven zapalovacím systémem s kontaktními body, kterému se dnes také říká konvenční zapalovací systém. Obrázek ukazuje tento typ zapalovacího systému.
U uzavřených kontaktních bodů začíná narůstání primárního proudu. Proud je omezen na 3 až 4 ampéry odporem primárního vinutí. Když primární cívkou zapalovací cívky protéká proud, vytvoří se magnetické pole. Primární (3) i sekundární cívka (4) jsou v tomto magnetickém poli. Když je proud přes kontaktní body (10) přerušen vačkou přerušovače (9) na hřídeli rozdělovače, indukuje se napětí v obou cívkách. V primární cívce se vyrábí přibližně 250 voltů. Rozdíl vinutí vytvoří v sekundární cívce indukční napětí 10 až 15 kV. Jiskra zapalovací svíčky vzniká při otevření hrotů.
Indukční napětí lze omezit tím, že po otevření kontaktních bodů necháme chvíli protékat primární proud. Toho je dosaženo pomocí kondenzátoru, který je zapojen paralelně přes kontaktní body. Kondenzátor je prvek určující čas, který v závislosti na kapacitě vlastně upravuje úroveň indukčního napětí. Kontaktní body jsou také chráněny před spálením.
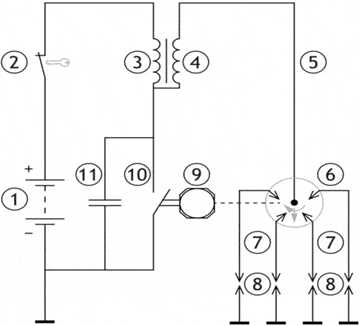
Zapalovací cívka pro systém řízení motoru:
Systém řízení motoru bude ovládat zapalovací cívku. Klasická zapalovací cívka s rozdělovačem zůstává na motoru, aby sloužila jako testovací nastavení, ale již není součástí fungování spalovacího motoru. Byl zvolen Distributorless Ignition System (DIS zapalovací cívka), volně přeloženo jako: „systém zapalování bez rozdělovače“. Tento typ zapalovacího systému nepoužívá rozdělovač. Další možností bylo zvolit zapalovací cívku Coil on plug (COP). Ke každé zapalovací svíčce je připojena samostatná zapalovací cívka. COP zapalovací cívka se také nazývá kolíková zapalovací cívka. Nevýhodou zapalovací cívky COP je, že odvod tepla je méně dobrý než u zapalovací cívky DIS. Při použití zapalovacích cívek COP je nutný i signál ze snímače vačkového hřídele, který u současného motoru není.
Chybějící zub v řemenici klikového hřídele slouží jako referenční bod, podle kterého se určuje časování zapalování. Se zapalovací cívkou DIS se v okamžiku zapálení aktivují dvě zapalovací svíčky současně. Zapalovací cívka DIS je ve skutečnosti jednotka, ve které jsou namontovány dvě zapalovací cívky. Když se písty válců 1 a 4 pohybují nahoru, jeden bude zaneprázdněn kompresním zdvihem a druhý výfukovým zdvihem. Přesto obě zapalovací svíčky vygenerují jiskru. Jiskra vytvořená válcem, který je zapojen do kompresního zdvihu, způsobí vznícení směsi. Druhá jiskra, takzvaná „zbytečná jiskra“, jiskří, když výfukové plyny opouštějí spalovací komoru. Zbytečná jiskra je jiskra, která se vytvoří, když není zapálena žádná směs. Energie vznícení je nízká; i přes jiskru dochází k malým ztrátám energie. To také není škodlivé.
Na obrázku je schéma činnosti zážehového čtyřválcového motoru se zapalovací cívkou DIS. Tento pracovní diagram ukazuje dvě značky zážehu na okamžik zážehu; Jeden z nich generuje jiskru k zapálení směsi, druhý je zbytečná jiskra. Zapalovací cívku DIS lze ovládat pomocí MegaSquirt pouhými dvěma impulsy.
Když kompresní zdvih probíhá ve válci 1 a výfukový zdvih ve válci 4, MegaSquirt ovládá primární cívku A přes kolík 36 na DB37 (viz obrázek níže). Tato regulace probíhá na základě referenčního bodu klikového hřídele (mezi 90 a 120 stupni před TDC). MegaSquirt ovládá primární cívku B, která je zodpovědná za tvorbu jisker válců 2 a 3, a je zapnutá o 180 stupňů za cívkou A. Neexistuje žádný referenční bod pro cívku B, ale časování zapalování lze určit jednoduše spočítáním zubů na 36-1 pulzním kole.
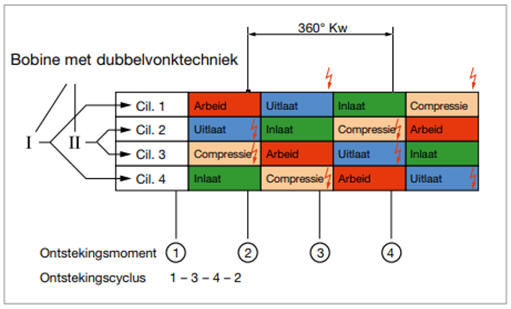
Mezi cívkou A zapalovací cívky a kolíkem 7 procesoru je zobrazen odpor 330 ohmů. Tento odpor omezuje proud a indukční napětí budícího impulsu. Protože tento rezistor není standardní na desce s obvody MegaSquirt, je nutné jej dodatečně namontovat. Vlevo od svislé přerušované čáry na obrázku níže jsou zobrazeny vnitřní obvody MegaSquirt. Zobrazené součástky (dva 330 Ohmové rezistory a LED diody) musely být následně připájeny k desce plošných spojů.
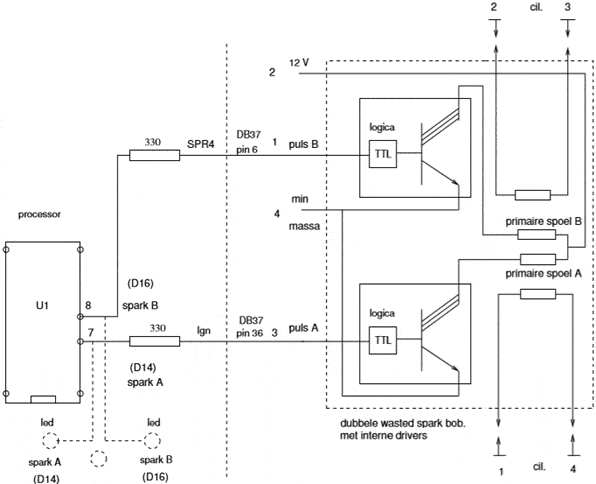
Nárůst proudu v primární cívce:
Je důležité získat vhled do nahromadění proudu v primární cívce. Tím lze určit nejen proud, ale také dobu nabíjení zapalovací cívky. Doba načítání závisí na řadě faktorů, které musí MegaSquirt vzít v úvahu.
Koeficient samoindukce (hodnota L) zvolené zapalovací cívky je 3,7 mH. Společně s ohmickým odporem R se určí maximální primární proud a doba náběhu křivky. Malá hodnota L a odpor zajišťují rychlý nárůst proudu po zapnutí. Ze známých dat zapalovací cívky lze vypočítat, jak se vytváří primární proud.
Následující vzorec ukazuje obecné řešení diferenciální rovnice 1. řádu, která vypočítává proudy, doby nabíjení a vybíjení, aby se spínací jev zobrazil jako křivka.
Rovnice je:

kde časová konstanta (Tau) se vypočítá takto:

Maximální proud by byl 28 ampér podle Ohmova zákona:
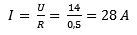
Ve skutečnosti nebude tohoto proudu dosaženo.
Cívka se vypne dříve. Důvod je vysvětlen později. Zadáním těchto informací do obecného vzorce získáte:
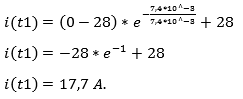
Obrázek ukazuje nabíjecí křivku primární cívky. Od času T0 do 1 Tau se cívka nabije na 63,2 %. Jedná se o fixní procento doby nabíjení cívky. Výsledek vzorce 13 ukazuje, že cívka je nabitá 1 A při 17,7 Tau. Při t = 5 Tau bylo prakticky dosaženo konečné hodnoty.
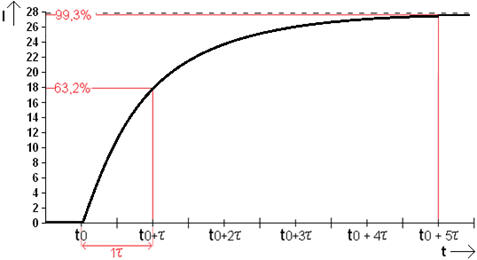
Podle specifikací zapalovací cívky je primární proud zapalovací cívky po nabití 7,5 A. Proud se nezvyšuje. Doba potřebná k dosažení 7,5 A se nazývá doba prodlevy. Doba prodlevy závisí na napětí baterie, které je v tomto případě 14 voltů. Pokud není nabíjecí proces upraven, je proud procházející cívkou maximálně 12 ampérů podle vzorce 28.
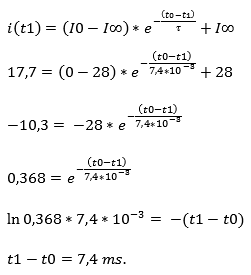
Cívka podle vzorce 14 se nabije na 7,4 A při t = 17,7 ms. Skutečná doba nabíjení je kratší, protože cívka se nabíjí maximálně 7,5 A. Požadovaný čas lze vypočítat zadáním známých údajů do vzorce 15.
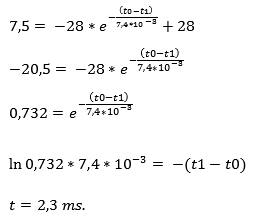
Primární nárůst proudu je zastaven na 7,5 A. Tím se zabrání nadměrnému a zbytečnému zahřívání zapalovací cívky. Nejdůležitější je, aby se cívka optimálně nabila co nejvíce v co nejkratším čase. Na obrázku je nabíjecí křivka do t = 2,3 ms.
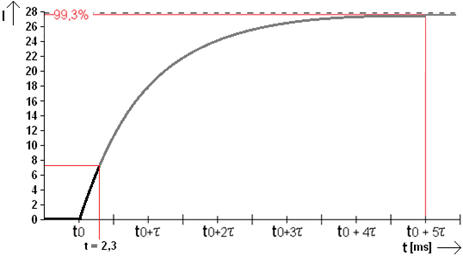
Když napětí baterie klesne, například při startování motoru, ovlivní to dobu prodlevy. Dosažení 2,3 A pak trvá déle než 7,5 ms. Nová doba načítání se určuje pomocí dnes již dobře známého vzorce. Maximální proud je určen na základě napětí baterie:
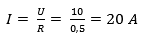
Doba nabíjení do 7,5 A s maximem 20 A se vypočítá podle vzorce 17:
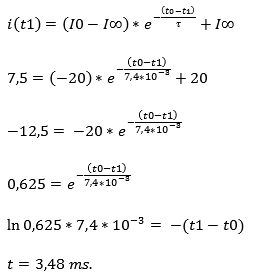
Na obrázku je doba nabíjení při 14 voltech zobrazena černou čarou a doba nabíjení při 10 voltech je zobrazena zeleně. Řádky současně klesnou na 0; toto je časování zapalování. Protože nižší napětí baterie vyžaduje více času k nabití primární cívky, musí MegaSquirt zapnout primární napájení dříve.
Černé čáry (stoupající a klesající) indikují dobu prodlevy při napětí baterie 14 voltů. Zelená čára označuje pokročilou dobu nabíjení při nižším napětí: to dává Δt. Skutečná doba nabíjení je v tomto případě Δt + 100 %.
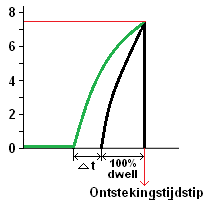
To bude vysvětleno později v této části s příkladem a obrázkem 36. Doba nabíjení se prodlouží a čas zapálení zůstává stejný. Pokud k tomu nedojde nebo nedojde dostatečně, bude to mít důsledky pro energii uvolněnou při zapalování. V tomto případě je primární proud vypnut příliš brzy, takže není dosaženo proudu 7,5 A. Prodloužení doby nabíjení primární cívky (doba prodlevy) je ve vzorci funkcí napětí baterie. Výpočet doby prodlevy při různých napětích dává různý maximální proud v cívce.
Za předpokladu, že napětí baterie může během startování klesnout na 6 voltů a během nabíjení stoupnout na 14,7 voltů, lze načrtnout křivku výpočtem řady mezilehlých hodnot. Obrázek níže ukazuje korekci doby prodlevy pro použitou zapalovací cívku DIS. Pro každé zvýšení o 2 volty je v grafu umístěn (červený) bod. Protože byla v programu TunerStudio zadána dříve zadaná doba prodlevy 2,3 ms při napětí 14 voltů, je z tohoto napětí vytvořen korekční faktor. Napětí 14 voltů je tedy 100 % (bez korekce).
Nyní bylo objasněno, že při napětí baterie 315 voltů se doba nabíjení prodlužuje až o 6 %.
Napětí baterie může za nepříznivých podmínek klesnout až o 6 voltů. To znamená oslabení zapalovací jiskry. Prodloužení doby prodlevy (doba, po kterou teče primární proud) to kompenzuje, takže i při tomto nízkém napětí se získá dostatečná zapalovací energie. To znamená, že Δt z obrázku 36 je trojnásobný (2,3 ms * 315 % = 7,26 ms) ve srovnání s dobou prodlevy 100 % (2,3 ms) vyznačenou černě.
Koeficienty označené červeně na obrázku výše lze zkopírovat přímo do programu TunerStudio.
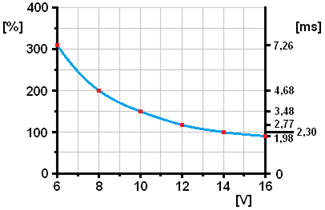
Po určité době po vybití primární cívky začne příprava na další zapálení. Čím vyšší jsou otáčky motoru, tím rychleji se cívka dobíjí. Obrázek 37 ukazuje dvě křivky, kde primární proud vzroste na 8,85 A. Časování zapalování je v bodě, kdy čára klesne na 0 A.
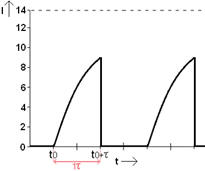
Určení časování zapalování:
Signál zapalování je určen z referenčního bodu klikového hřídele.
V ozubeném věnce řemenice klikového hřídele je vyfrézován 36 zub z 1 zubů pod úhlem 100 stupňů před horní úvratí pístu válce 1. Mezi 100 a 0 stupni, takže během kompresního zdvihu mikroprocesor MegaSquirt dokáže určit načasování zapalování. Toto bere v úvahu zálohu.
Obrázek ukazuje obrázek dvoukanálového osciloskopu, na kterém horní obrázek ukazuje referenční bod klikového hřídele a spodní obrázek ukazuje řídicí signál z MegaSquirt do zapalovací cívky DIS. Řídicí signál má napětí 5 voltů (logická 1) a trvá přibližně 1,5 ms.
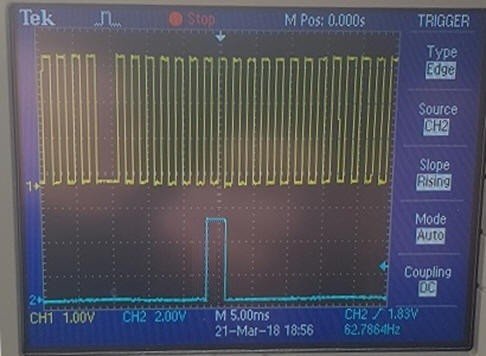
Předstih zapalování:
V tomto projektu nejsou použity snímače klepání. Je možné zpracovávat informace ze snímačů klepání, ale pouhá instalace snímače klepání nestačí. Zpracování signálů je složité. Signál klepání musí být nejprve převeden na signál ano/ne nebo na analogový signál, který indikuje sílu detonace.
Přeměna vibrací motoru na signál klepání se provádí obvodem rozhraní. Tento obvod není v MegaSquirt II přítomen. Proto bylo rozhodnuto bezpečně nastavit předstih plného a částečného zatížení, aby motor nemohl skončit v oblasti klepání. Křivka posunu plného zatížení, která má být nastavena, musí být stanovena v mezích klepání. Údaje o odstředivém a vakuovém předstihu konvenčního zapalování jsou určeny na základě továrních údajů z příručky motoru. Body lze vynést do grafu (příklad na obrázku níže).
Růžová čára označuje původní, mechanický posun. To je částečně lineární díky mechanické konstrukci odstředivých závaží. Černá čára ukazuje ovládání mapy v MegaSquirt; tato čára sleduje křivku. Je důležité zůstat mimo oblasti klepání při částečném a plném zatížení; proto je ovládání mapy omezeno při částečném zatížení (červená čára) a předstih při plném zatížení se nezvyšuje dále než v situaci s mechanickým předstihem (červená čára). Vlastní uspořádání mapy sleduje modrou čáru.
Nejprve bylo nutné zadat křivku předstihu plného zatížení do tabulky předstihu jiskry. Při vyšších rychlostech a nižším zatížení bude zapotřebí větší předstih. Při částečném zatížení se předstih přičte k předstihu plného zatížení. Kompletní tabulka předstihu zapalování a nastavení předstihu při studeném motoru jsou uvedeny na straně 7.
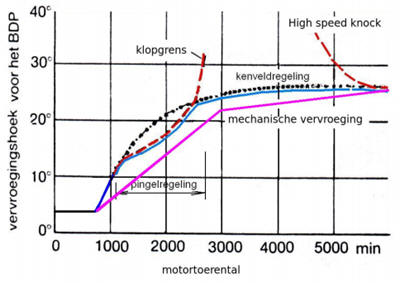
Tělo škrticí klapky:
Přívod vzduchu/paliva byl řízen karburátorem v původním stavu. U systému řízení motoru je karburátor nahrazen tělesem škrticí klapky a čtyřmi vstřikovači, které jsou namontovány v sacím potrubí. To poskytuje přesnější a kontrolovanější vstřikování než u karburátoru, kde se směs vzduchu a paliva tvoří centrálně v potrubí a je rozdělena do čtyř kanálů. Plyn se otevírá bowdenem, který se ovládá ručně z přístrojové desky.
Ostatně MegaSquirt II nepodporuje elektronicky ovládané těleso škrticí klapky. Proto je ovládání bowdenem jedinou možností použití.
Poloha škrticí klapky je přenášena na MegaSquirt pomocí napětí. Velikost napětí závisí na úhlu otevření škrticí klapky. Snímač polohy škrticí klapky je potenciometr s napájecím napětím 5 voltů (viz obrázek). Připojení 3 a uzemnění 1 jsou nezbytné. Běžec (pin 2) zaujme polohu na odporu, který závisí na poloze škrticí klapky. Běžec je tedy spojen se škrticí klapkou. Když musí běžec překonat malou vzdálenost přes odpor (běžec ukazuje doleva), odpor je nízký. Na obrázku je běžec umístěn vpravo (strana země), což znamená, že je zde vysoký odpor a tedy nízké napětí signálu.
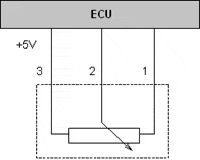
S použitým tělesem škrticí klapky je na běžci při zavřené škrticí klapce napětí 600mV a při plně otevřeném ventilu napětí 3,9V. ECU přijímá napětí a používá jej k výpočtu úhlu otevření škrticí klapky. Rychlé zvýšení úhlu otevření znamená zrychlení; ECU na to reaguje krátkým obohacením. Tomu se říká akcelerační obohacení. Snímač polohy škrticí klapky se nepoužívá k určení obohacení směsi při různých provozních podmínkách; K tomuto účelu slouží snímač MAP.
Testovací nastavení krokového motoru se simulátorem:
Poté, co byl MegaSquirt hardwarově upraven, bylo možné použít breakout box ke kontrole, zda bylo přijímáno ovládání krokového motoru. Rozsvícení dvoubarevných LED signalizuje, že probíhá ovládání. Kroky, ve kterých je krokový motor řízen, lze sledovat při pohledu na změnu barev. Barvy se střídají mezi červenou a žlutou. Data krokového motoru lze zadat v menu „Idle control“ v programu TunerStudio. Kromě typu (4 dráty) lze nastavit i počet kroků. To také zahrnuje výchozí polohu, ve které musí být krokový motor při spuštění motoru. Dále lze nastavit čas, jak dlouho trvá úprava jednoho kroku.
Počet kroků závisí mimo jiné na teplotě chladicí kapaliny; nižší teplota vyžaduje větší otevření krokového motoru. Kroky vzhledem k teplotě lze nastavit v grafu. Simulátor lze použít ke kontrole, zda je krokový motor skutečně správně řízen. Protože se kontroluje nejprve na simulátoru místo na motoru, lze předejít problémům při startování nebo chodu motoru kvůli možnému hardwarovému nebo softwarovému problému. Protože teplota chladicí kapaliny a otáčky motoru ovlivňují především úhel otevření krokového motoru, můžete otáčením těchto potenciometrů zkontrolovat správnost ovládání. Měřič na přístrojové desce v TunerStudio zobrazí úpravu v počtu upravených kroků.
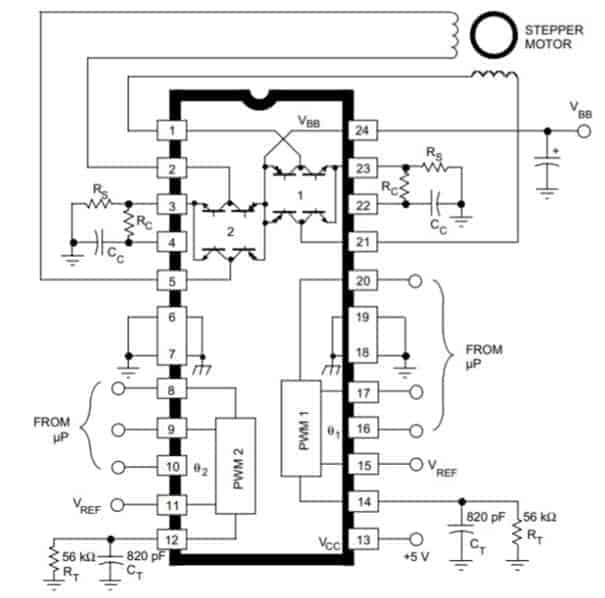
Nastavení krokového motoru:
Obrázek ukazuje obrazovku nastavení pro krokový motor používaný pro volnoběh (regulace volnoběhu).
Kroky, ve kterých se motor nastavuje, jsou určeny předem pomocí Arduina. Počet kroků musí být také zadán pro přesun do základní polohy (nájezdové kroky). Krokový motor je aktivní ve fázi zahřívání (algoritmus) a napájí cívky v klidu (přídržný proud mezi kroky).
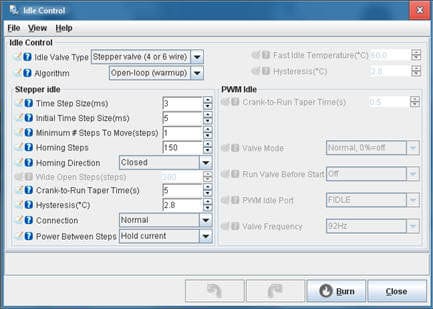
Poloha krokového motoru závisí na teplotě chladicí kapaliny. Při startování studeného motoru by měl být ventil otevřen o něco více než při startování zahřátého motoru. Obrázek níže ukazuje obrazovku nastavení pro nastavení kroků (Kroky) ve vztahu k teplotě chladicí kapaliny (Chladicí kapalina). Když je motor studený, je krokový motor plně otevřen, zatímco motor běží na volnoběh. Během zahřívací fáze se krokový motor mírně zavírá.
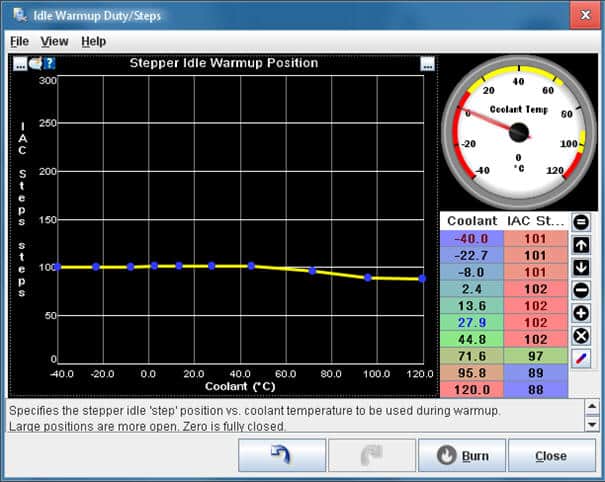
Je také možné upravit polohu krokového motoru na základě teploty chladicí kapaliny při startování motoru. Toto se nazývá „Povinnost/kroky při roztáčení naprázdno“. Obrázek níže ukazuje obrazovku nastavení.
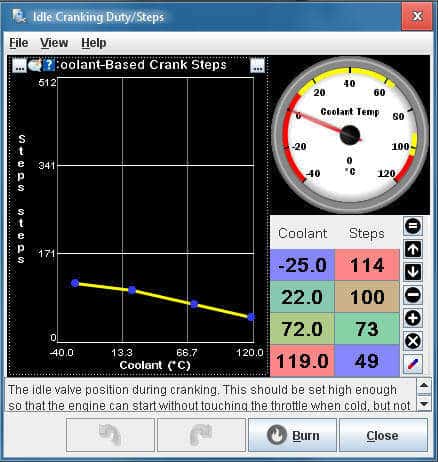
Okruh palivového čerpadla:
MegaSquirt zajišťuje zapínání a vypínání palivového čerpadla. Tranzistor Q19 na obrázku níže chrání tranzistor Q2 před nadměrným proudem. Pokud je proud příliš vysoký, tranzistor se může spálit. Když se proud procházející částí kolektor-emitor Q2 a R40 zvýší, dosáhne se saturačního napětí na bázi Q19. Tranzistor Q19 se zapne, což způsobí snížení napětí báze-emitor na Q2.
Připojení FP-1 PTA0 je řízeno interně pomocí MegaSquirt. K ovládání tranzistorového obvodu je nutný vstupní signál ze snímače polohy klikového hřídele (snímač Hall nebo indukční snímač). Při ztrátě signálu, například při nechtěném zhasnutí motoru, je okamžitě ukončeno napájení palivového čerpadla.
Výstup tranzistorového obvodu (FP1 OUT) je připojen k relé palivového čerpadla. Pin 85 relé je výstupem řídicího proudu. Při aktivovaném relé se přepne hlavní výkonová část (pin 30 a 87), takže palivové čerpadlo obdrží napájecí napětí pro provoz.
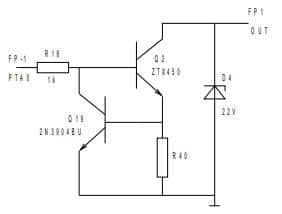
Je použito elektronické palivové čerpadlo s provozním tlakem 3 bar. Palivo je vedeno přes palivový filtr do palivové lišty, kde je tlak na vstupu vstřikovačů. Vstřikovač vstříkne předem vypočítané množství paliva do sacího potrubí, když přijde signál z MegaSquirt. Nejen ovládání MegaSquirt určuje množství vstřikovaného paliva, ale také tlak paliva v railu.
Při vyšším tlaku v railu bude při stejném ovládání vstřikováno větší množství paliva. Tlak v railu proto musí být nastaven na základě podtlaku v sacím potrubí. Tlakový rozdíl (∆P) musí vždy zůstat 3 bary. Obrázek ukazuje schéma palivového systému. Růžové, žluté, oranžové a černé čáry ukazují elektrické připojení. Červená čára označuje přívod paliva a modrá čára zpětné vedení paliva.
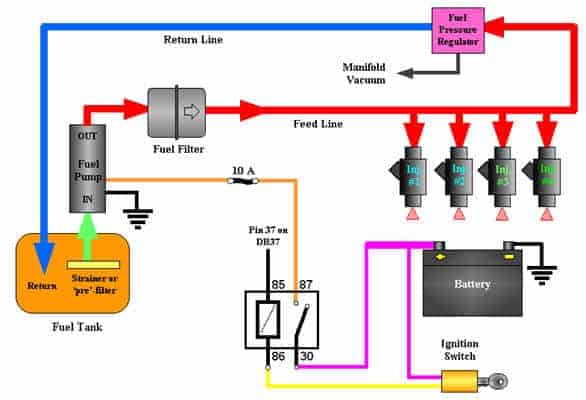
Dokončení mechanických prací:
Na dalších třech fotografiích je motor ve finální fázi mechanických úprav.
Foto 1:
Toto je strana, kde je vidět většina aplikovaných částí. Je zde také umístěna přístrojová deska pro ovládací prvky a ECU MegaSquirt. Pod fotkou je legenda s popisem čísel dílů. Fotografie můžete otevřít ve větší velikosti kliknutím na ně.
- Škrticí klapka;
- Palivové potrubí pro vstřikovače;
- Spojovací trubka pro škrticí klapku na sacím potrubí;
- Tlakoměr paliva;
- Sací a výfukové potrubí;
- Palubní deska se spínačem chladicího ventilátoru, kontrolkami alternátoru a tlaku oleje, spínačem zapalování a uzemňovacím spínačem;
- Vakuová hadice pro senzor MAP;
- Lambda sonda;
- Palivové hadice (přívodní a vratné) společně ve smršťovací krabičce;
- Jednotka palivového čerpadla/nádrže;
- Relé palivového čerpadla;
- MegaSquirt;
- Tlumič výfuku.
Foto 2:
Tato fotografie ukazuje druhou stranu motoru. Zde vidíte karburátor (15) a klasické zapalování (17). Účelem tohoto klasického zapalování je vyvolat jiskření zapalovacích svíček v testovací sestavě (14). To samozřejmě nemá pro motor žádnou funkci, ale poskytuje pohled na fungování zapalování, jak to fungovalo v klasických autech.
Číslo 20 označuje mechanismus brzdy převodovky. Tyč brzdového bubnu lze dotáhnout pomocí bowdenu, takže je zabrzděna výstupní hřídel převodovky. Brzda převodovky se použije ke krátkému zatížení motoru při zařazení rychlostního stupně.
Foto 3:
Zde je dobře vidět pohled shora na motor s testovacím nastavením zapalování a rozdělovače paliva.
Mechanické úpravy byly dokončeny. Motor zatím nelze nastartovat, protože do MegaSquirt je třeba nejprve zadat některá data.
Další: Nastavení ECU MegaSquirt II.